In the world of 3D printing, the choice between SLS and SLA technologies is a crucial one for many enthusiasts and professionals. Let’s explore in detail which of these, SLS or SLA, is the right fit for your projects. This article will cover every aspect, from their basic principles, strengths and weaknesses, materials, applications, costs, to emerging trends. By the end, you’ll be well – informed to make the best decision.
Understanding the Basics: A Glimpse into SLS and SLA
Before we compare SLS and SLA in depth, let’s first understand what each technology is all about.
What is Selective Laser Sintering (SLS)?
Imagine building with powdered materials like nylon or metal, similar to constructing with sand, but for 3D printing. That’s how SLS works. A laser selectively sinters (melts) layers of powder, and the unmelted powder supports parts during printing. As a result, parts are fully enclosed without needing additional support structures.
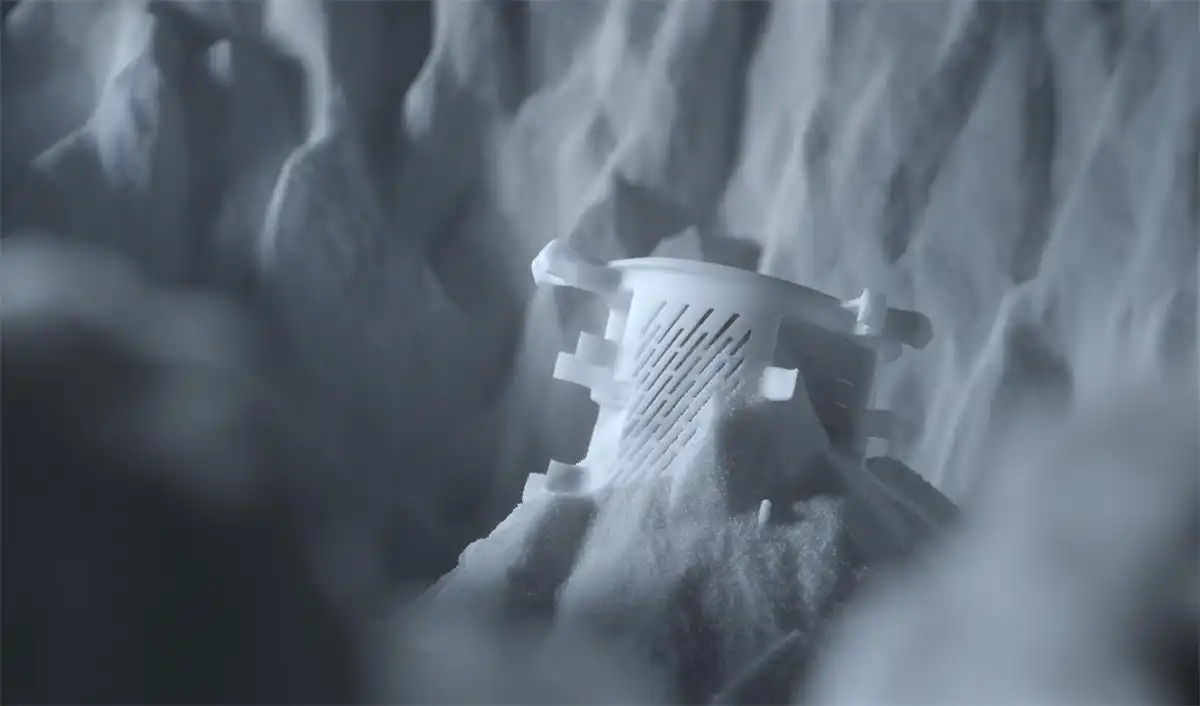
- Key Features:
- No need for support structures.
- High mechanical strength.
- Ideal for functional prototypes.
What is Stereo Lithography Apparatus (SLA)?
In SLA printing, a laser cures liquid resin layer by layer. Each layer hardens as it’s exposed to light, resulting in smooth surfaces with high detail.
- Key Features:
- Exceptional detail accuracy.
- Smooth surface finish.
- Great for visual prototypes.
SLS vs SLA: Comparing Strengths and Weaknesses
Strengths & Weaknesses at a Glance
When Does SLA Shine?
If you’re looking for high – detail and a great – looking finish, SLA might be the right choice.
- Detail Accuracy: SLA offers exceptional detail accuracy, comparable to the precision of a microscope.
- Smooth Surface Finish: It provides a smooth surface without rough edges, making it perfect for showpieces.
- Weaknesses: However, SLA – printed parts are brittle and need to be handled with care. Also, layer lines can sometimes be visible.
When Does SLS Excel?
SLS has its own set of advantages. It doesn’t require support structures, has high mechanical strength, and is great for creating parts that need to withstand stress and strain. But the surface finish of SLS – printed parts is not as smooth as SLA’s, and post – printing processing like sanding is often needed.
Material Considerations: Choosing Your Medium
The right material is crucial for 3D printing. Let’s look at the materials used in SLS and SLA.
Types Of Resins In SLA
Resin is the main material for SLAs.
- Standard Resin: A general – purpose option.
- Castable Resin: Ideal for jewelry making or applications that require casting processes.
- Durable Resin: Designed to last longer.
Types Of Powders In SLS
Powders are where SLS shines.
- Nylon (PA): Flexible and strong, suitable for functional parts.
- Aluminum – Filled Nylon: Adds conductivity and a touch of shine.
- TPU (Thermoplastic Polyurethane): Extremely flexible, great for items that need to bend.
Material Availability And Cost
SLS has a wide range of powders available, but they’re not cheap. However, if handled carefully, the powders can be reused. SLA resins are diverse too, but they tend to be pricier per unit volume compared to SLS powders.
Surface Finish And Post Processing Requirements
Typical Surface Finish Achievable By Each Technology
In terms of surface finish, SLA takes the lead with its ultra – smooth surfaces, suitable for museum – worthy pieces. SLS, on the other hand, needs some post – printing treatment like sanding to achieve a smooth finish.
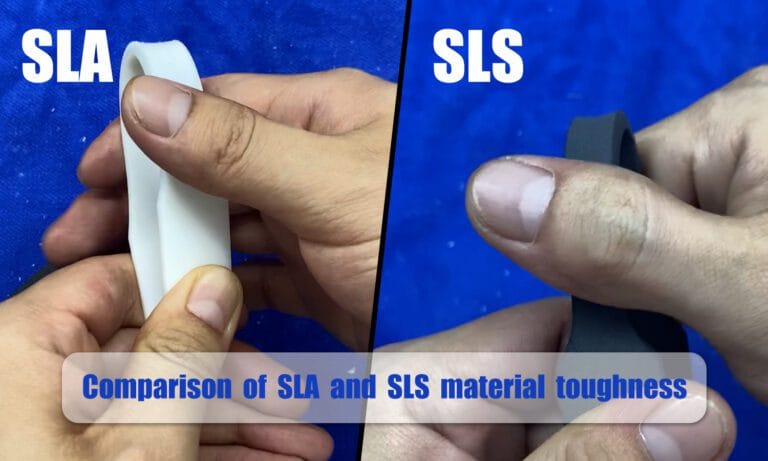
Common Post Processing Steps For Both Methods
For SLS Printing
After printing, you need to brush off excess powder and may need to do some filing or sanding to get the final product ready.
For SLA Printing
Don’t skip the washing and curing steps if you want your SLA – printed parts to have long – term durability.
Speed And Throughput Comparisons
Print Time Expectations For Similarly Complex Parts
The print speed of both SLS and SLA depends on part size and complexity. Generally, intricate geometries slow down both processes. However, in some cases, if speed is more important than detail precision, SLS might be a better choice. But it’s not a straightforward answer, as both technologies have their optimal scenarios for print speed. (Click the image to view the complete spreadsheet, which shows the comparison data of printing times for different complex parts under SLS and SLA technologies.)
Applications Where One Technology Excels Over The Other
Manufacturing & Prototyping Use Cases
When To Choose SLS
- Functional Prototypes Requiring Mechanical Testing: SLS parts are tough and can withstand real – world testing, making them suitable for parts in machinery or automotive components.
- End – Use Parts That Need High Durability: If you’re producing long – term use parts, like gears in gadgets, SLS is a great option.
When To Choose SLA
- Detailed Visual Prototypes Needed For Presentation Or Fit/Check Purposes: SLA’s smooth surfaces and intricate details make it perfect for creating product models for catalogs or trade shows.
- Jewelry Casting Patterns Due To High Detail Capability: Jewelers love SLA for its ability to capture every detail in casting rings, pendants, and other delicate pieces.
Industry – Specific Applications
Automotive Industry
- Why SLS?: It’s great for producing durable parts that can handle the harsh conditions under a car’s hood.
- Why SLA?: Ideal for creating detailed prototypes or custom interior components where appearance is as important as functionality.
Aerospace Industry
- Why SLS?: Aerospace requires materials that can withstand extreme conditions, and many SLS powders fit the bill.
- Why SLA?: Perfect for lightweight components with complex geometries without sacrificing detail quality.
Medical Devices
- Why SLS?: Good for creating durable prosthetics or surgical tools that can endure repeated use.
- Why SLA?: Ideal for highly detailed anatomical models used in pre – surgical planning or educational tools.
Consumer Goods
- Why SLS?: Allows for mass customization, producing strong and affordable end – use products.
- Why SLA?: Great for items with eye – catching designs and smooth finishes, like luxury accessories or unique home accents.
Economic Considerations For Choosing Between The Two Technologies
Capital Expenditure (CapEx)
- SLS Printers: These are high – end and expensive, often starting in the tens of thousands of dollars, similar to luxury cars.
- SLA Printers: More affordable, with prices ranging from a few hundred to a few thousand dollars, comparable to economy cars. So, if you’re on a tight budget, SLA might be more accessible.
Operational Expenditure (OpEx)
- Material Costs: SLS powders can be pricey but are reusable. SLA resins are also costly but offer great detail.
- Energy Consumption: SLS generally consumes more energy due to its higher operating temperatures. So, while SLA printers may have lower initial costs, ongoing expenses could add up over time.
Return On Investment (ROI)
- For SLS: If you’re producing long – lasting functional parts, the durability can lead to reduced maintenance and replacement costs in the long run.
- For SLA: If your focus is on detailed prototypes or custom products where appearance matters, the investment can translate into higher customer satisfaction and potential sales.
Emerging Trends In Additive Manufacturing Impacting The Choice Between These Technologies
Advances In Desktop Printers Offering Higher Quality Output At Lower Costs
Desktop printers are improving rapidly. Now, high – quality 3D printing that used to require industrial – grade equipment can be done on a desktop without a huge cost, making both SLS and SLA more accessible.
Development Of New Materials Expanding Application Possibilities
Materials science is evolving, with new materials like biodegradable plastics and high – performance alloys being used in 3D printing. This opens up new application areas that were previously unimaginable.
Adoption Of Multi – Material Printing Capabilities
Multi – material printing allows manufacturers to create objects with multiple materials in a single print job, making products more intelligent and versatile.
Conclusion & Recommendations
Based on your priorities, such as cost, speed, detail, and application, you can now make an informed decision between SLS and SLA 3D printing. (Click the image to view the complete spreadsheet for a more detailed comparison based on different criteria.)
Final Thoughts On The Future Of These Technologies
The future of additive manufacturing looks bright. Both SLS and SLA will likely continue to evolve, and we may even see hybrid systems that combine the best of both worlds, such as high detail and exceptional durability. This could revolutionize industries once again.