3D printing has come a long way from an expensive, niche technology of industrial giants. In 2025, it’s reshaping industries, empowering creators, and has made manufacturing more approachable than ever. Among the many 3D printing technologies today, SLS stands out as a real game changer to produce quality, tough, yet detailed parts at scale. Whether you’re a hobbyist, professional, or business owner, SLS 3D printing sets itself apart owing to its utmost versatility and precision.
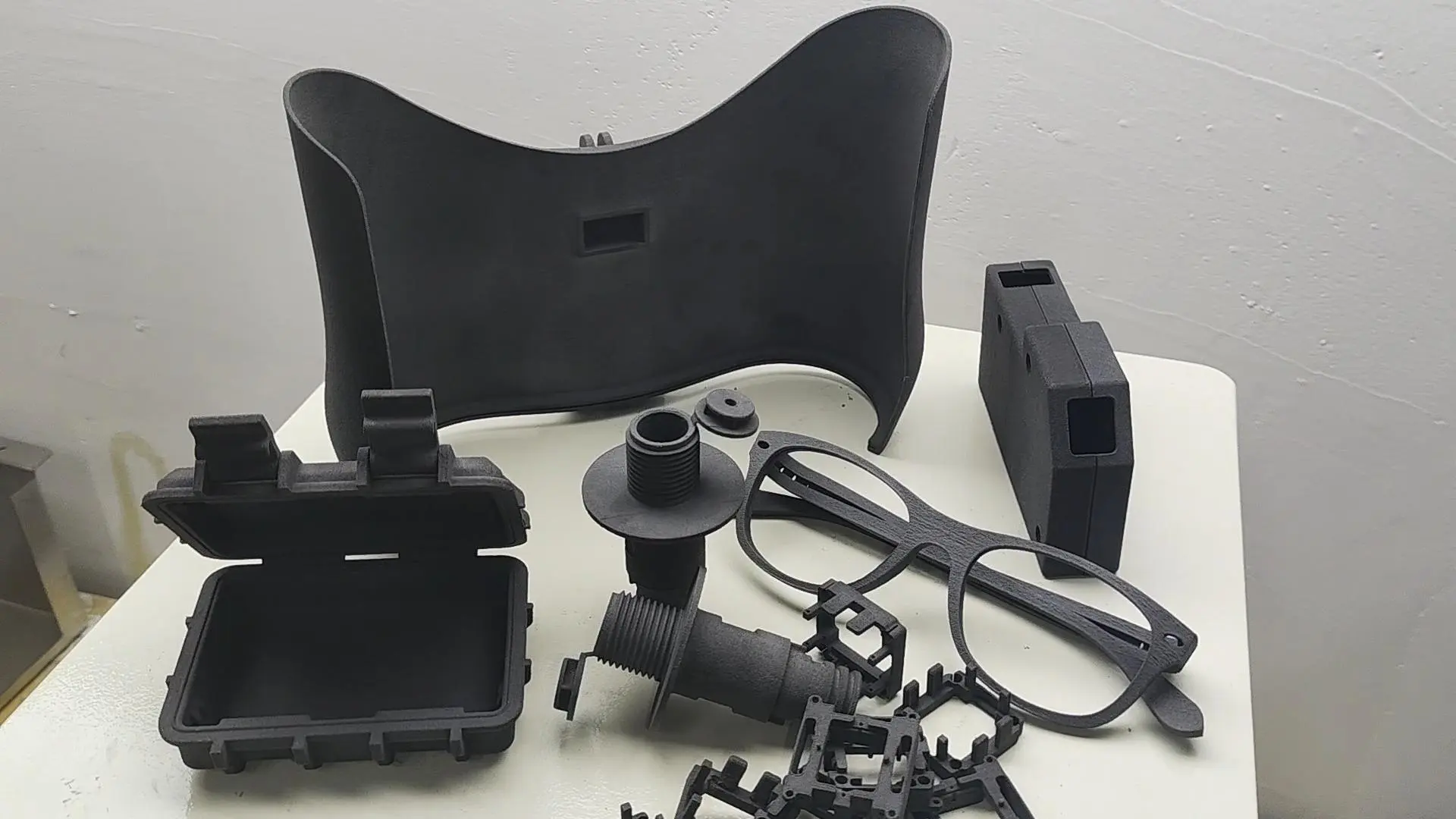
However, with all the advances coming to the market and newer models coming up, how do you distinguish the right SLS 3D printer for your needs? Is it print speed, material compatibility, or cost? And what advances coming in 2025 should you be aware of before you buy?
This guide will answer these and more. We are going to cover what makes SLS technology unique, the major factors for consideration when selecting a printer, and follow this with a set of recommendations for the best SLS 3D printers for every budget and use case. By doing so, we will cover the latest trends, answer common questions, and give you helpful suggestions for extracting the most value from your investment.
Whatever your purpose is- prototype, manufacture end-use parts, or elevate your business with additive manufacturing, you will equip yourself with valuable knowledge throughout this article to make an informed choice. Let’s dive into the world of SLS 3D printing and find the right one for you.
What Is SLS 3D Printing?
3D printing has revolutionized the way we design, prototype, and manufacture products, but not all 3D printing technologies are created equal. Among the various methods available, Selective Laser Sintering (SLS) stands out as one of the most advanced and versatile options. Known for its ability to create highly detailed, durable, and functional parts, SLS is a go-to choice for industries ranging from aerospace to healthcare. But what exactly is SLS 3D printing, and why is it so popular?
In this article, we’ll unpack everything you need to know about SLS 3D printing, including how it works, the materials it uses, its benefits, and the industries that rely on it. By the end, you’ll have a solid understanding of why SLS is one of the most important technologies in the world of additive manufacturing.
How Does SLS 3D Printing Work?
Selective Laser Sintering, orSLS, is a powder-based 3D printing process which employs a powerful laser to fuse together extremely fine particles of material, usually plastic powders, into a solid three-dimensional object. The important processes are as follows:
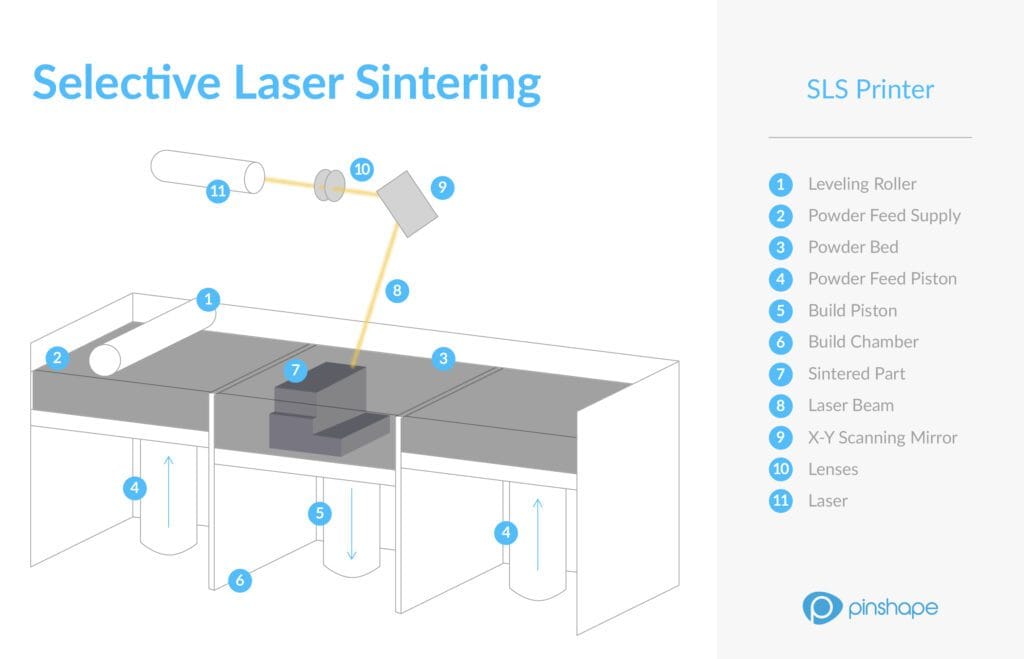
- Preparation:
- A thin layer of powdered material (e.g., nylon or TPU) is spread across the build platform.
- The printer’s software slices the 3D model into thin layers, which the laser will sinter one at a time.
- Laser Sintering:
- A laser selectively heats and fuses the powder particles in the areas defined by the digital model.
- The unfused powder remains in place, providing support for the part as it is built.
- Layer-by-Layer Construction:
- The build platform lowers slightly, and a new layer of powder is spread over the previous one.
- The laser repeats the sintering process for the next layer.
- Cooling and Post-Processing:
- Once the object is fully printed, the build chamber is allowed to cool to avoid warping.
- The part is removed from the surrounding loose powder, which can often be recycled for future prints.
This layer-by-layer approach enables SLS printers to create complex geometries and detailed designs with no need for support structures, unlike other 3D printing methods such as Fused Deposition Modeling (FDM).
Materials Used in SLS 3D Printing
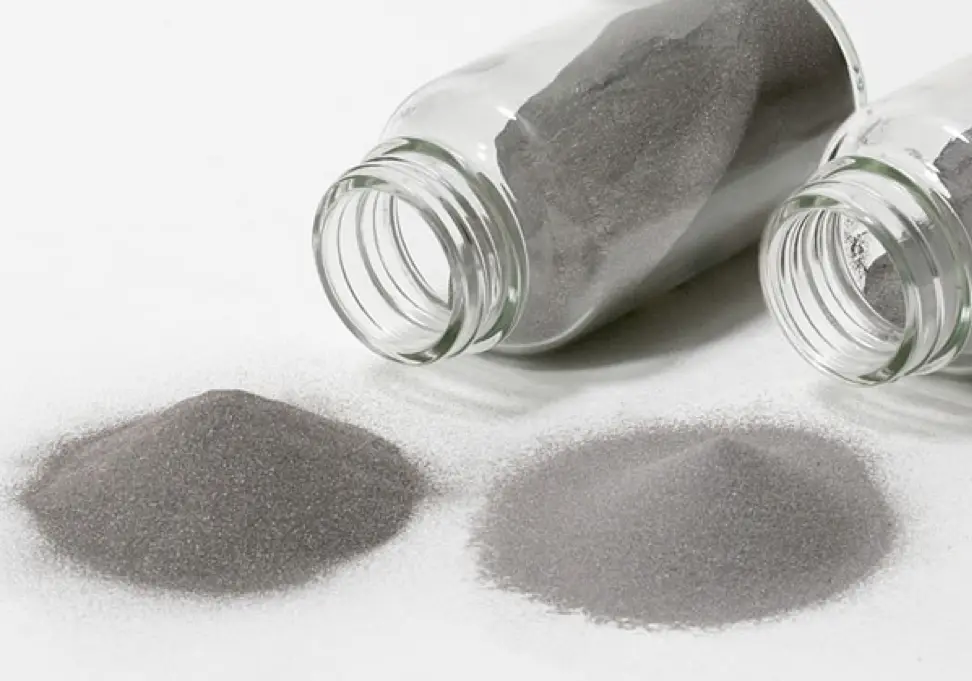
One of the key strengths of SLS 3D printing is its compatibility with a wide range of materials. The most common materials used in SLS printing include:
Material | Description | Applications |
Nylon (PA 12) | A versatile, durable, and lightweight thermoplastic. | Functional prototypes, end-use parts, automotive components, consumer goods. |
Nylon (PA 11) | Similar to PA 12 but offers higher flexibility and impact resistance. | Medical devices, sports equipment, flexible parts. |
TPU (Thermoplastic Polyurethane) | A flexible, rubber-like material with excellent elasticity and durability. | Footwear, gaskets, seals, wearable devices. |
Glass-Filled Nylon | Nylon mixed with glass fibers for added strength and stiffness. | Aerospace and automotive parts, structural components. |
Alumide | Nylon powder blended with aluminum particles for a metallic finish. | Decorative items, lightweight metal-like parts. |
In 2025, advancements in SLS materials have introduced biodegradable options and advanced composites, making the technology even more versatile and sustainable.
What Makes SLS 3D Printing Unique?
SLS stands out from other 3D printing technologies for several reasons. Here are the key features that make SLS a favorite among professionals:
1. No Need for Support Structures
In most 3D printing methods, such as FDM or SLA, support structures are required to hold overhanging parts during the printing process. With SLS, the unused powder acts as a natural support, allowing for the creation of complex geometries without additional material waste.
2. Durable and Functional Parts
SLS-printed parts are strong and durable, with mechanical properties comparable to those of injection-molded parts. This makes SLS ideal for functional prototypes and end-use components that can withstand real-world conditions.
3. High Design Freedom
SLS enables the creation of intricate designs that would be impossible with traditional manufacturing methods. From internal channels to organic shapes, the possibilities are virtually limitless.
4. Efficient Material Usage
Unfused powder can often be reused in subsequent prints, significantly reducing material waste and lowering operational costs.
5. Scalability
SLS is well-suited for both prototyping and small-scale production runs, making it a versatile option for businesses looking to scale up manufacturing.
Benefits of SLS 3D Printing
Here’s a quick breakdown of the benefits you can expect from SLS:
- High Strength and Durability: Perfect for functional parts and prototypes.
- Complex Geometry: Create intricate designs with no need for supports.
- Material Versatility: Print with a wide range of materials, including flexible and composite options.
- Cost-Effectiveness: Efficient powder recycling reduces material costs.
- Scalable Production: Suitable for one-off prototypes or small-batch manufacturing.
Why Is SLS 3D Printing So Popular in 2025?
By 2025, SLS is more accessible than ever before, with affordable desktop versions sold to small businesses and hobbyists, as well as industrial-grade machines for large manufacturing needs. Advances in materials science and software have increased the speed, accuracy, and sustainability of the technology, helping it to emerge as a preferred choice for professionals around the globe.
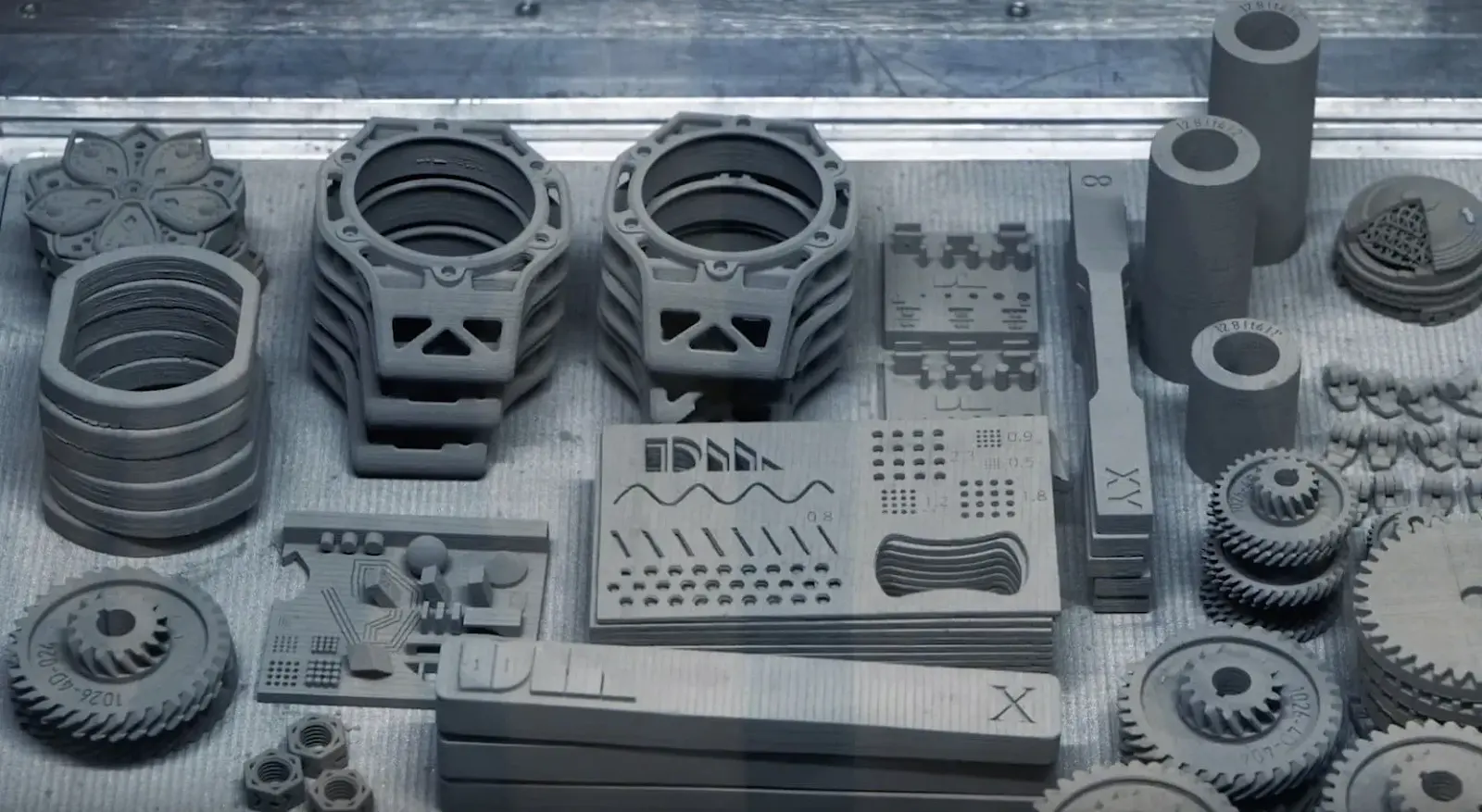
Be it an engineer making prototypes, a business owner making custom products, or an innovator looking into new manufacturing possibilities, SLS 3D printing provides an unparalleled combination of quality, versatility, and efficiency.
How to Choose the Best SLS 3D Printer in 2025
Selective Laser Sintering (SLS) 3D printers are in broad demand in 2025 due to their professionalism, robustness, and high precision in manufacture. With many of them on the market- all with unique features and price tags- your choice for the SLS 3D printer may be perplexed.
Choosing the right SLS printer requires commercial and industrial investigation and serious considerations of individual needs, budget, and long-term goals-since it may represent a major capital investment. Therefore, this guide deconstructs everything there is to know about improving your making the right choice-from how to weigh your options, through key factors you need to consider, to tips on-avoid making a costly mistake.
Key Factors to Consider When Choosing an SLS 3D Printer
When evaluating SLS 3D printers, there are several critical factors to keep in mind. Let’s explore these in detail:
1. Print Volume (Build Size)
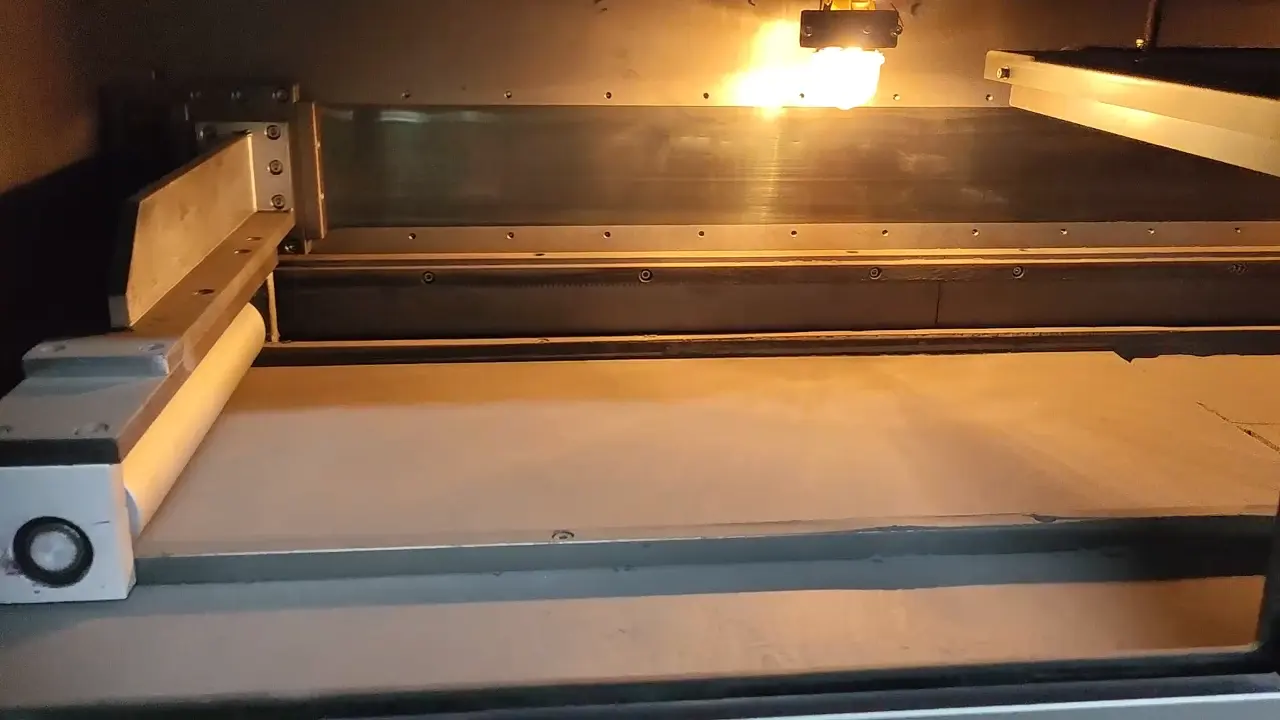
The build size determines the maximum dimensions of the parts you can create in a single print.
- Small Printers: Ideal for prototyping smaller parts or items like jewelry and medical devices.
- Example: Build volume of around 150 x 150 x 150 mm.
- Mid-Sized Printers: Great for professionals and small businesses needing versatility in part sizes.
- Example: Build volume between 250 x 250 x 300 mm.
- Large Printers: Suitable for industrial applications and printing larger parts or multiple parts simultaneously.
- Example: Build volume exceeding 500 x 500 x 500 mm.
Ask Yourself:
- What is the maximum size of the parts you plan to print?
- Will you need to print multiple parts at once for batch production?
2. Resolution and Precision
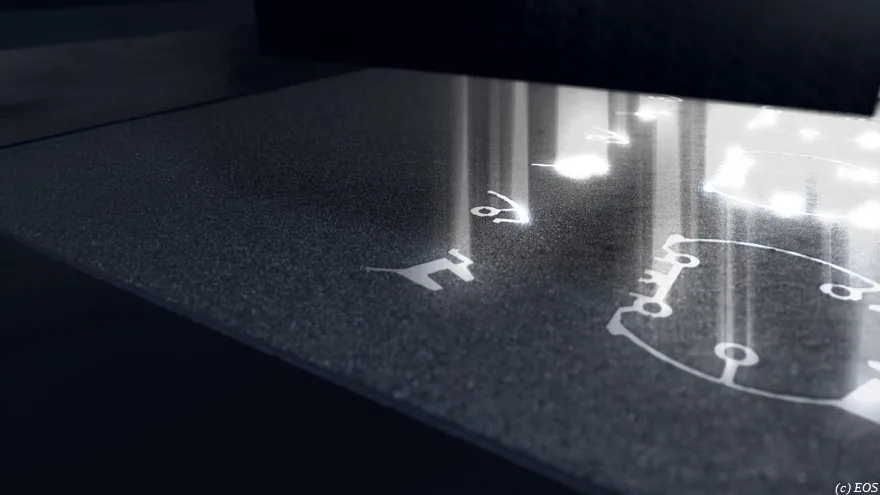
One of the standout features of SLS 3D printing is its ability to produce high-resolution, highly detailed parts, but resolution can vary between printers.
- High-Resolution Printers:
- Layer thickness as low as **50 microns**.
- Ideal for applications requiring fine details, such as medical or aerospace components.
- Standard-Resolution Printers:
- Layer thickness around **100 microns**.
- Suitable for most functional prototypes and general use.
Pro Tip: If your parts need tight tolerances or intricate geometries, prioritize printers with higher resolution.
3. Material Compatibility
Not all SLS printers can handle every material type. Consider the materials you need for your application:
Material | Applications | SLS Printer Requirements |
Nylon (PA 12) | General-purpose, durable parts. | Most SLS printers are compatible. |
TPU (Flexible Material) | Wearables, gaskets, seals. | Requires a printer optimized for flexibility. |
Glass-Filled Nylon | Stiff, strong parts for industrial use. | Requires higher-temperature settings. |
Alumide | Lightweight, metallic-looking parts. | Printer must support composite powders. |
Ask Yourself:
- Does the printer support the materials you need?
- Are additional material options (e.g., flexible or composite powders) important to you?
4. Ease of Use
The usability of an SLS printer can make or break your experience, especially if you’re new to the technology. Look for features that simplify the printing process:
- Intuitive Software: Easy-to-use slicing and preparation tools save time and reduce errors.
- Automation Features: Self-leveling build platforms, automated powder handling, and material recycling systems are game-changers.
- User-Friendly Interface: Touchscreen controls and guided workflows improve accessibility.
Pro Tip: If you’re new to SLS printing, prioritize printers with beginner-friendly features to reduce the learning curve.
5. Speed and Throughput
In 2025, SLS printers are faster than ever, but print speed can still vary widely.
- Print Speed: Measured in layers per hour or build time per part. Faster printers are ideal for time-sensitive projects or production runs.
- Post-Processing Speed: Consider how quickly powder can be removed and recycled after a print.
Ask Yourself:
- Do you need a printer for rapid prototyping or high-volume production?
- Can the printer’s speed meet your project deadlines?
6. Cost and Budget
SLS 3D printers vary greatly in price, from affordable desktop models to industrial giants.
- Entry-Level Printers:
- Cost: **$5,000 – $****20,000**.
- Ideal for small businesses, hobbyists, or limited prototyping.
- Mid-Range Printers:
- Cost: **$20,000 – $****75,000**.
- Suitable for professionals and small-to-medium businesses.
- Industrial-Grade Printers:
- Cost: **$100,000+**.
- Designed for large-scale production and industrial use.
Keep in mind **long-term costs**, such as:
- Material costs (powder prices can vary).
- Maintenance and replacement parts.
- Post-processing equipment.
7. Customer Support and Warranty
SLS printers are complex machines, so the quality of customer support and warranty policies can make a huge difference.
- Customer Support:
- Look for manufacturers with a reputation for responsive and helpful support teams.
- Warranty:
- Ensure the printer includes a solid warranty that covers major parts and components.
Pro Tip: Read reviews or testimonials to gauge how well the manufacturer handles technical issues.
8. Scalability
If you plan to grow your business or increase production in the future, consider whether the printer can scale with you.
- Modular Designs: Some printers offer modular upgrades for larger build volumes or improved capabilities.
- Network Integration: Industrial-grade printers often allow for integration into larger production workflows.
Key Features to Look For
Feature | Entry-Level | Mid-Range | Industrial-Grade |
Build Volume | Small (150 x 150 x 150 mm) | Medium (250 x 250 x 300 mm) | Large (500 x 500 x 500 mm or more) |
Resolution | 100 microns | 50-100 microns | 50 microns or better |
Material Options | Limited | Moderate | Broad (including composites) |
Automation Features | Basic | Advanced (e.g., powder recycling) | Fully automated |
Cost | $$5,000 -$$20,000 | $$20,000 -$$75,000 | $100,000+ |
Target Audience | Hobbyists, small businesses | Professionals, SMEs | Industrial manufacturers |
Tips for Narrowing Down Your Options
- Define Your Goals:
- Do you need a printer for rapid prototyping, functional parts, or production?
- Set a Budget:
- Understand the upfront and long-term costs.
- Research Use Cases:
- Look into case studies or examples of businesses using specific printers for similar applications.
- Ask for Demos or Samples:
- Many manufacturers offer sample prints or live demos to showcase their printer’s capabilities.
- Prioritize Critical Features:
- Focus on the features that align most with your needs, whether it’s build volume, material compatibility, or ease of use.
Effectively choosing the right SLS 3D printer in the year 2025 isn’t a daunting task. Clear comprehension of the application, budget, and unique features of each machine should make it fairly simple. This would allow for appropriate decisions concerning the right 3D printer that fits your needs of creating functional prototypes, scaling production, or innovating in your sector.
Top SLS 3D Printers to Buy in 2025
As the demand for high-quality, precise 3D printing continues to grow, Selective Laser Sintering (SLS) technology has emerged as a leading choice for many applications. In 2025, several SLS printers stand out for their performance, reliability, and value. This article provides a comprehensive comparison of the best SLS 3D printers available, categorized into entry-level, mid-range, and industrial-grade options.
Comprehensive Comparison of the Best SLS 3D Printers
Printer Model | Price | Build Volume | Key Features | Target Audience |
Formlabs Fuse 1 | ~$18,499 | 165 x 165 x 300 mm | Reliable, precise; great for prototypes | Hobbyists & SMEs |
Sinterit Lisa X | ~$15,490 | Larger than standard | Enhanced capabilities for larger prints | Professionals |
Zongheng3D SuperMaker SLS2030 | ~$39,800 | 200 x 200 x 300 mm | Advanced features for rapid prototyping | Small businesses |
Zongheng3D SuperMaker SLS 3540 PRO | ~$69,800 | 350 x 350 x 430 mm | High precision; supports multiple materials | Industrial users |
Entry-Level SLS Printers
Entry-level SLS printers are perfect for hobbyists or small businesses looking to explore the technology without a hefty investment.
Formlabs Fuse 1
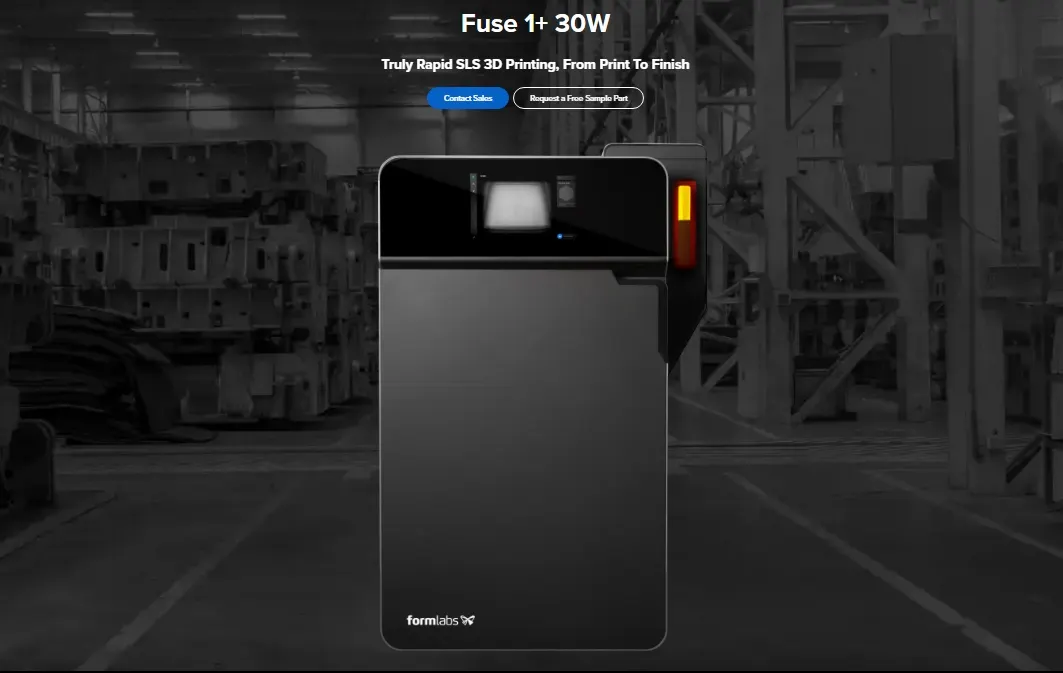
- Price: Approximately $18,499
- Build Volume: 165 x 165 x 300 mm
- Materials: Nylon 12, Nylon 11
- Key Features:
- Reliable and precise printing.
- Suitable for functional prototypes and small-scale production.
- Pros:
- Excellent print quality.
- User-friendly interface.
- Cons:
- Higher price point compared to other entry-level options.
Mid-Range SLS Printers
Mid-range printers offer high-performance features suitable for professionals and small to medium enterprises (SMEs).
Sinterit Lisa X
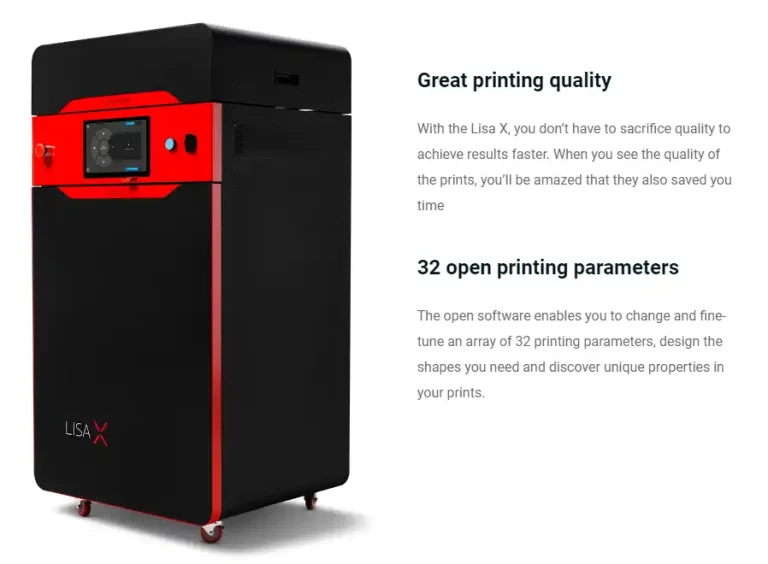
- Price: Approximately $15,490
- Build Volume: Larger than the standard Lisa model.
- Materials: Nylon PA12, TPU
- Key Features:
- Enhanced capabilities for larger prints while maintaining ease of use.
- Pros:
- Compact design with good print quality.
- Versatile material compatibility.
- Cons:
- Limited build volume compared to industrial models.
Industrial-Grade SLS Printers
Industrial-grade printers are designed for mass production and high-volume applications.
Zongheng3D SuperMaker SLS2030
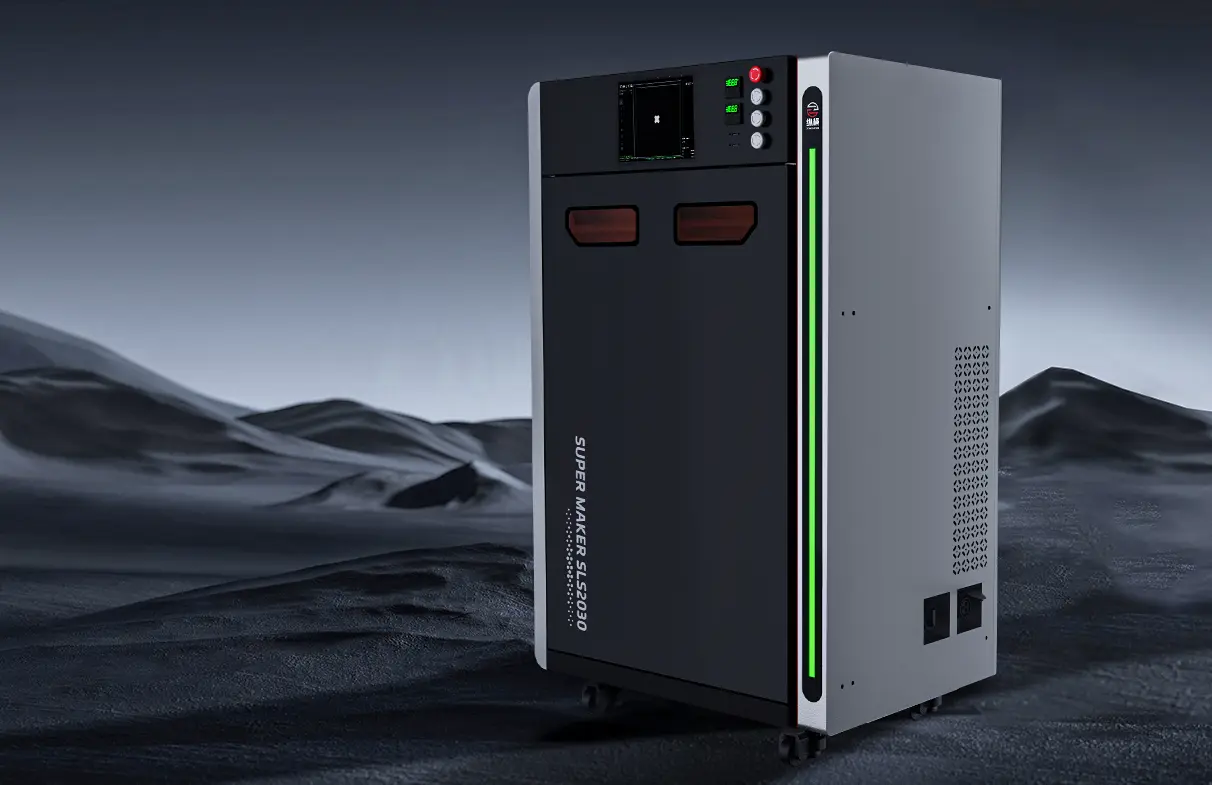
- Price: Approximately $39,800
- Build Volume: 200 x 200 x 300 mm
- Materials: PA11, PA12, TPU
- Key Features:
- Advanced features suited for rapid prototyping.
- Pros:
- High precision and efficiency.
- Good material versatility.
- Cons:
- Higher initial investment compared to entry-level options.
Zongheng3D SuperMaker SLS 3540 PRO
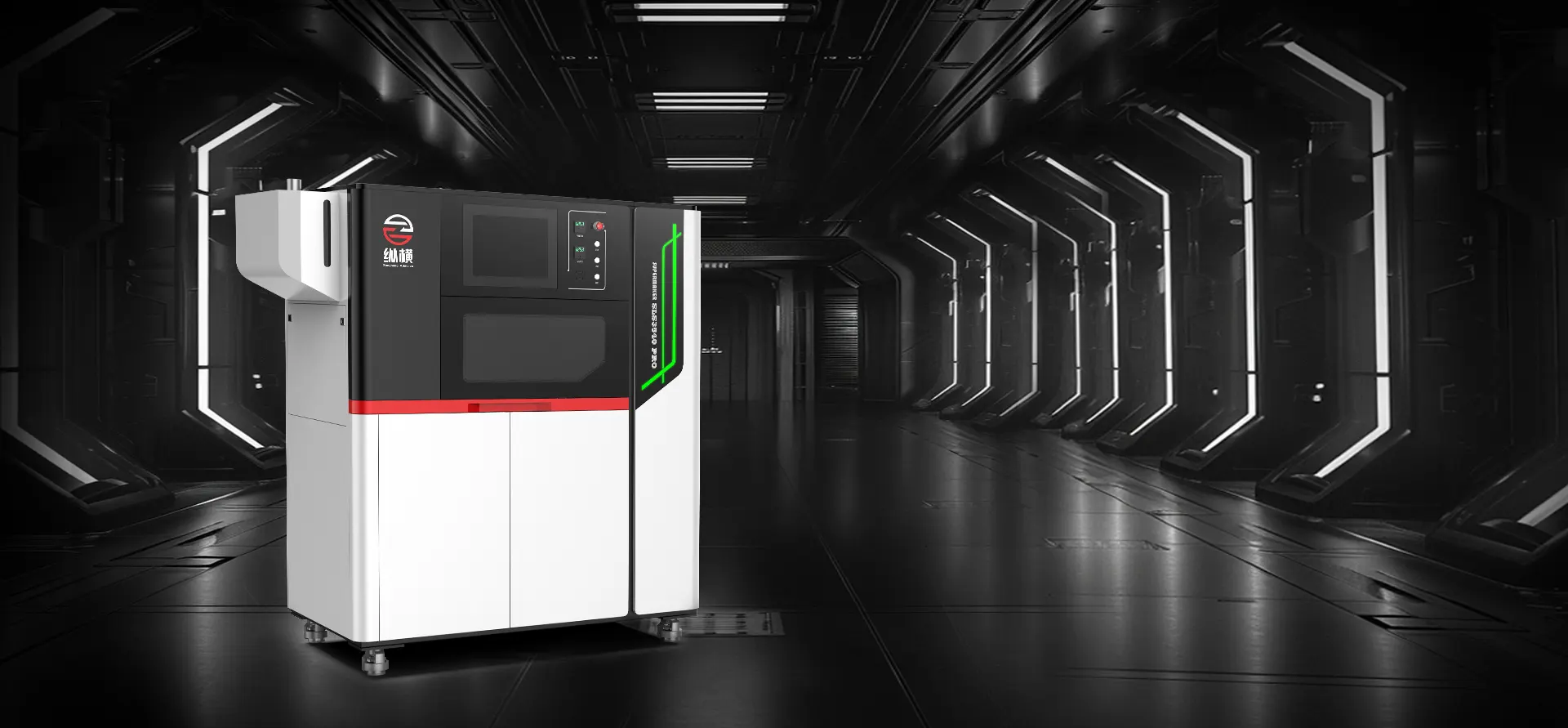
- Price: Approximately $69,800
- Build Volume: 350 x 350 x 430 mm
- Laser Type: Fiber Laser (1 x 300W)
- Layer Thickness: Adjustable between 0.1 to 0.3 mm
- Maximum Cabin Temperature: Up to 190ºC
- Materials Supported: PA11, PA12, TPU, Nylon with glass fiber
- Key Features:
- Real-time online temperature compensation for consistent results.
- Inert gas protection to maintain material integrity during printing.
- Pros:
- Large build size allows for significant production capabilities.
- High-quality prints suitable for industrial applications.
- Cons:
- Price may be prohibitive for smaller operations.
the landscape of SLS printers in 2025 offers a variety of options tailored to different user needs. From entry-level models like the Formlabs Fuse 1 that provide excellent quality at a reasonable price to industrial-grade machines like the Zongheng3D SuperMaker SLS models that cater to large-scale production demands, there is an ideal printer for every type of user. When selecting an SLS printer, consider your specific requirements regarding budget, intended use, and desired print quality to make an informed decision.
What’s New in SLS 3D Printing Technology in 2025?
As we step into 2025, the world of Selective Laser Sintering (SLS) 3D printing is evolving rapidly, driven by innovations that enhance speed, efficiency, and sustainability. This section revisits recent advances in SLS tech, including improvements in printing speed, material recycling, new materials, and integration with next-generation technologies.
Innovations in SLS Printers
- Faster Print Speeds
One of the most significant trends in SLS technology is the improvement in print speeds. Manufacturers are continually optimizing laser scanning and recoating processes to reduce production times. For instance:
- Advanced Scanning Algorithms: New algorithms enable faster laser movements and more efficient sintering processes.
- Improved Recoater Speed: Upgrades to recoater mechanisms allow for quicker layer application, significantly boosting overall throughput.
- Improved Material Recycling and Waste Reduction
Sustainability is a growing concern in manufacturing, and SLS technology is adapting accordingly. Innovations include:
- Automated Post-Processing Solutions: The introduction of systems like UNPIT automates post-processing steps such as unpacking and depowdering, allowing for up to 100% recovery of unused powder. This reduces waste and operational costs for users, particularly small and medium enterprises (SMEs)
- Enhanced Material Recovery Techniques: New methods are being developed to reclaim and reuse materials efficiently, minimizing environmental impact.
- Enhanced Software for Print Optimization
Software advancements are crucial for maximizing the capabilities of SLS printers:
- Open Architecture Systems: New software solutions provide users with complete control over slicing parameters and laser settings, allowing for tailored print jobs that optimize material usage and print quality
- AI-Driven Optimization: AI technologies are being integrated to analyze print data in real-time, enabling smarter adjustments during the printing process for improved accuracy and efficiency.
New Materials in 2025
The material landscape for SLS printing is expanding with innovative options that cater to diverse applications:
Biodegradable and Sustainable Materials
There is a notable shift towards environmentally friendly materials:
- Biodegradable Polymers: New formulations of biodegradable materials are being introduced, allowing for sustainable production without compromising performance.
- Recyclable Materials: Advances in material science are leading to the development of recyclable SLS powders that can be reused multiple times without significant degradation.
- Advanced Composites for Specific Industries
The demand for specialized materials in sectors like aerospace and automotive is driving innovation:
- High-Performance Composites: New composite materials that combine strength with lightweight properties are being developed specifically for high-stress applications.
- Conductive Materials: Innovations in conductive polymers enable the creation of parts with integrated electronic functionalities, paving the way for advanced applications in electronics and wearables.
Integration with Other Technologies
The integration of SLS printing with other technologies is enhancing its capabilities:
AI-Driven Print Optimization
Artificial Intelligence is playing a pivotal role in refining the SLS printing process:
- Predictive Analytics: AI algorithms analyze historical data to predict potential issues during printing, allowing for proactive adjustments.
- Design Optimization: AI tools assist designers by providing insights into optimal geometries and material choices based on specific application requirements
IoT-Enabled Printers for Remote Monitoring
The Internet of Things (IoT) is transforming how printers operate:
- Remote Monitoring Capabilities: IoT-enabled printers allow users to monitor print jobs remotely, ensuring real-time oversight and reducing downtime.
- Data Collection: IoT devices collect data from various stages of the printing process, providing valuable insights that can be used to enhance future production runs
What’s the Difference Between SLS, SLA, and FDM?
SLS, SLA (Stereolithography), and FDM (Fused Deposition Modeling) are three prominent 3D printing technologies, each with distinct characteristics:
Feature | SLS | SLA | FDM |
Process | Uses a laser to sinter powdered material into solid parts. | Uses a UV light to cure liquid resin layer by layer. | Extrudes thermoplastic filament through a heated nozzle. |
Material Types | Primarily powders (e.g., nylon, metals). | Liquid resins. | Thermoplastic filaments (e.g., PLA, ABS). |
Print Quality | High detail and mechanical properties; suitable for functional parts. | Excellent surface finish and detail; ideal for prototypes. | Good for functional parts but may require post-processing for smooth finishes. |
Speed | Generally faster for larger parts due to layer sintering. | Slower due to curing time of resin. | Varies based on complexity but generally slower than SLS for larger parts. |
Cost | More expensive due to equipment and material costs. | Moderate initial cost; resin can be expensive. | Generally more affordable with lower material costs. |
How Much Does an SLS 3D Printer Cost in 2025?
In 2025, the cost of SLS 3D printers varies widely based on features and capabilities:
- Entry-Level Models: Approximately $15,000 – $20,000.
- Mid-Range Models: Around $25,000 – $40,000.
- Industrial Models: Starting from $40,000 and can exceed $100,000 depending on specifications and capabilities (e.g., Zongheng3D SuperMaker SLS 3540 PRO).
These prices reflect the growing accessibility of SLS technology as more manufacturers enter the market.
What Are the Maintenance Requirements for an SLS Printer?
Maintaining an SLS printer is crucial for optimal performance and longevity. Key maintenance tasks include:
- Regular Cleaning:
- Clean the build chamber and powder handling systems after each print.
- Use compressed air to remove powder residue from components.
- Lubrication:
- Lubricate moving parts regularly to ensure smooth operation.
- Follow manufacturer guidelines for specific lubrication intervals.
- Inspection:
- Regularly inspect optical components for dust or debris.
- Check all cables and connections for wear or damage.
- Software Updates:
- Keep firmware up-to-date to benefit from improvements and new features.
- Filter Replacement:
- Replace exhaust filters periodically to maintain air quality during operation.
Are There Any Safety Concerns with SLS Printing?
While SLS printing is generally safe, certain precautions should be taken:
- Powder Handling: Fine powders can pose inhalation risks; use appropriate personal protective equipment (PPE) such as masks and gloves when handling materials.
- Fire Hazards: Some powders are flammable; ensure proper ventilation and avoid ignition sources near the printer.
- Skin Irritation: Direct contact with powders can cause skin irritation; always wear gloves during maintenance.
- Post-Processing Risks: The depowdering process can expose operators to hot surfaces; allow prints to cool before handling.
Can SLS Printers Handle Multiple Materials in One Print?
Yes, many modern SLS printers can handle multiple materials in a single print job:
- Multi-Material Capabilities: Some printers allow users to mix different polymer powders during printing, enabling the creation of complex parts with varying properties (e.g., rigid structures with flexible hinges).
- Customization Opportunities: This capability is particularly valuable in industries like consumer products and fashion where aesthetics and functionality are crucial.
What Is the Lifespan of an SLS Printer?
The lifespan of an SLS printer can vary significantly based on usage and maintenance:
- General Lifespan: Most well-maintained printers last between 3 to 10 years.
- Industrial Models: High-quality industrial-grade printers can last several decades if properly cared for.
- Factors Influencing Lifespan:
- Frequency of use
- Quality of components
- Level of maintenance performed
Regular upkeep is essential to maximizing the operational life of your printer.
Grasping some of the technicalities of SLS 3D printing is of prime importance to everyone considering their integration into their workflow process or business. From differentiated technologies to defining what upkeep means, this FAQ section will serve as a strong grounding for the world of SLS printing in 2025. Whatever position you’re in-hobbyist furthering the horizons of creativity, or business seeking to augment production capabilities-knowledge will allow you to make the best possible decision for your needs.
Case Studies and Use Cases of SLS 3D Printing in 2025
Selective laser sintering(SLS) has steadily captured a free niche is of merit and can produce worthy parts in many industries, ranging from aerospace to health care, because SLS 3D printing in 2025 is currently in use in several applications. Here we provide some real-life applications of SLS while showcasing some success stories of companies adopting this exquisite technology.
Real-World Applications of SLS 3D Printing
- Aerospace Industry: Lightweight and Durable Parts
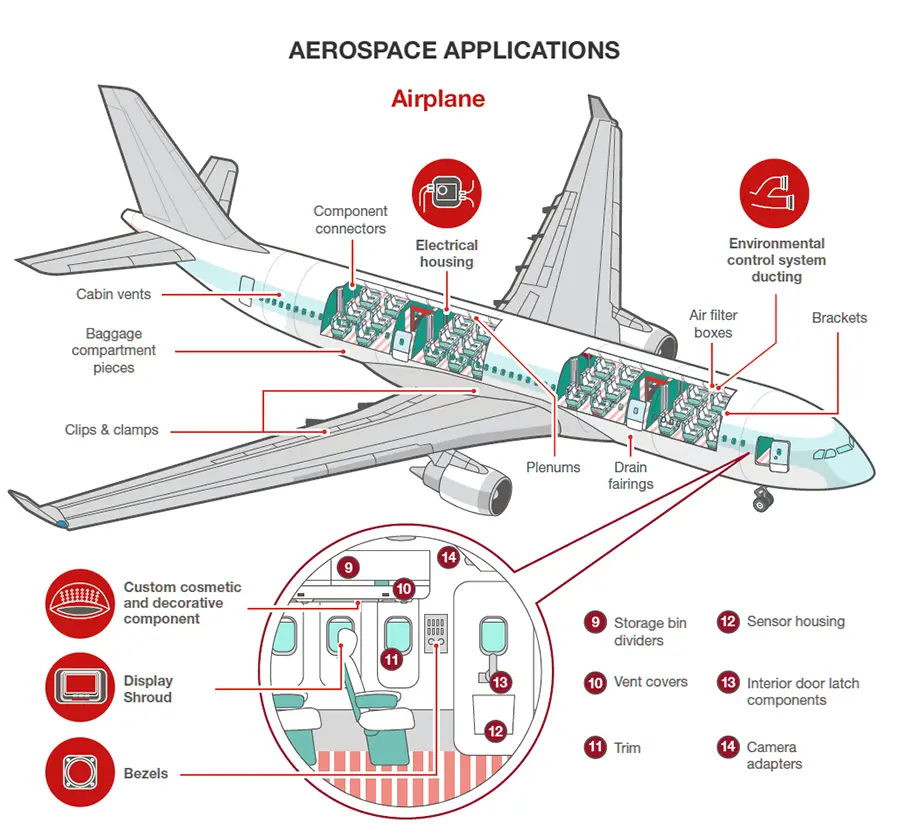
The aerospace sector is one of the leading adopters of SLS technology, primarily due to its ability to produce lightweight and complex geometries that traditional manufacturing methods struggle with.
- Key Benefits:
- Weight Reduction: Parts produced using SLS can be up to 70% lighter than those made through conventional methods, enhancing fuel efficiency.
- Complex Geometries: SLS allows for intricate designs that improve aerodynamics and functionality.
- Example:
- Airbus has successfully integrated 3D-printed spacer panels into its A320 aircraft. These components were produced using SLS to meet the low-volume production needs without the high costs associated with injection molding.
- Healthcare: Custom Prosthetics and Medical Devices
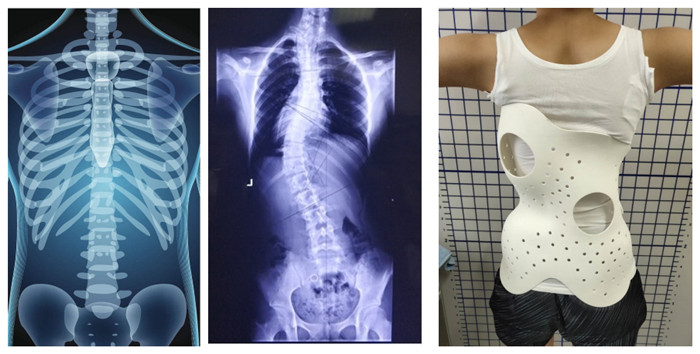
SLS technology is revolutionizing the healthcare industry by enabling the production of highly customized medical devices tailored to individual patient needs.
- Key Benefits:
- Personalization: Each device can be designed based on a patient’s specific anatomy, improving fit and comfort.
- Rapid Prototyping: Quick iterations allow for faster development cycles in medical device design.
- Example:
- Companies like Xometry have utilized SLS to create custom prosthetics and surgical tools that are patient-specific, significantly enhancing patient care and outcomes. This includes spinal implants and orthopedic devices tailored to individual patients based on their imaging data.
- Automotive: Functional Prototypes and Spare Parts
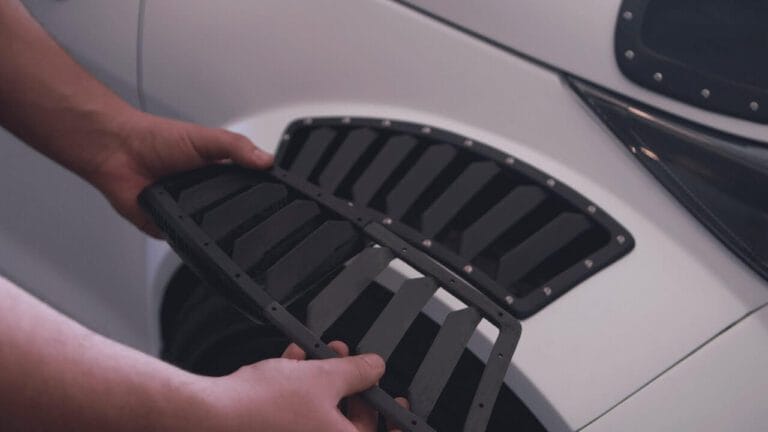
In the automotive industry, SLS is used for both prototyping and producing functional parts that meet stringent performance standards.
- Key Benefits:
- Rapid Prototyping: Allows for quick testing of designs before full-scale production.
- On-Demand Spare Parts: Reduces inventory costs by enabling manufacturers to produce parts as needed.
- Example:
- Automotive manufacturers are using SLS to create custom tooling and fixtures that streamline assembly processes. For instance, a company might use SLS to produce lightweight jigs that enhance precision during manufacturing.
- Consumer Goods: Customized Products like Eyewear and Footwear
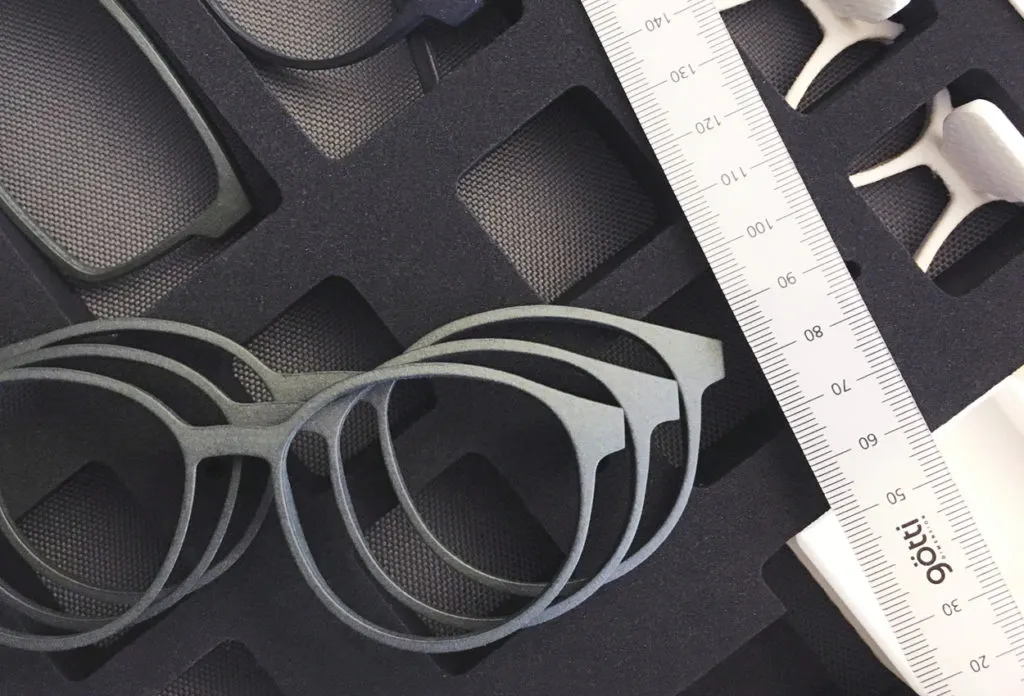
SLS technology is making waves in the consumer goods sector by enabling mass customization of products such as eyewear and footwear.
- Key Benefits:
- Customization at Scale: Brands can offer personalized products without significant increases in production costs.
- Design Freedom: Designers can create intricate designs that would be impossible with traditional manufacturing methods.
- Example:
- Brands like Adidas are exploring SLS for producing customized footwear that fits individual consumers perfectly, enhancing both comfort and performance.
Success Stories from Businesses Using SLS Printers
Success Story 1: Airbus
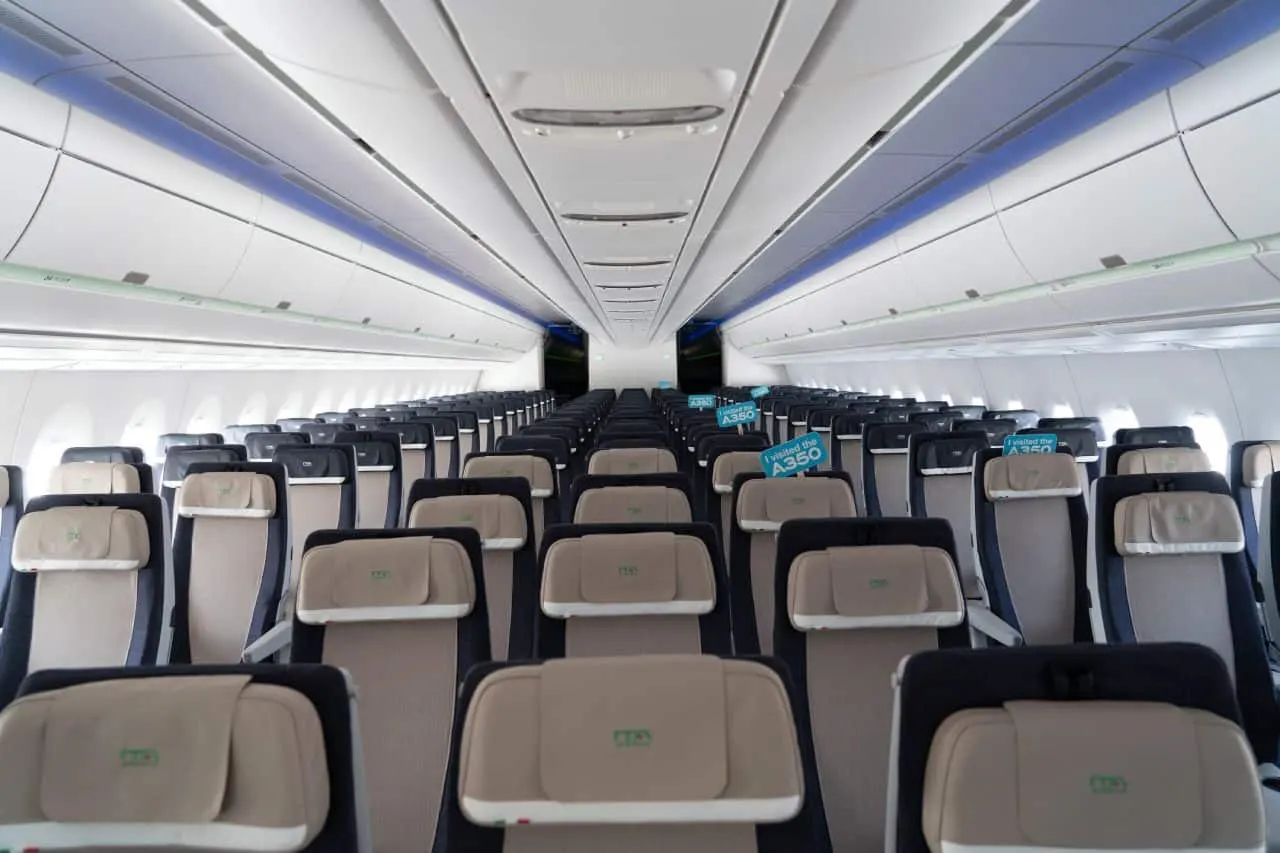
Airbus has leveraged SLS technology to produce lightweight components for its aircraft interiors. This initiative not only reduces weight but also shortens lead times for part production. By integrating SLS into their manufacturing processes, Airbus can respond more quickly to design changes and customer demands while maintaining high standards of quality.
Success Story 2: Xometry
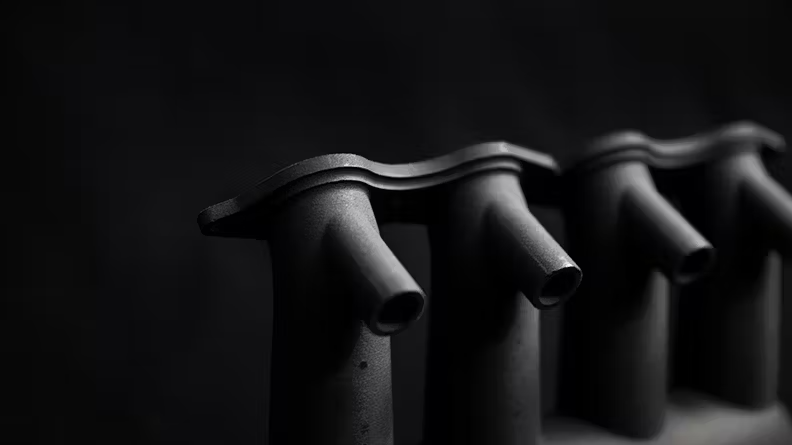
Xometry has become a leader in providing custom manufacturing solutions, utilizing SLS for creating specialized medical devices. Their ability to produce patient-specific prosthetics has set them apart in the healthcare market, demonstrating how SLS can enhance patient care through customization.
Success Story 3: Adidas
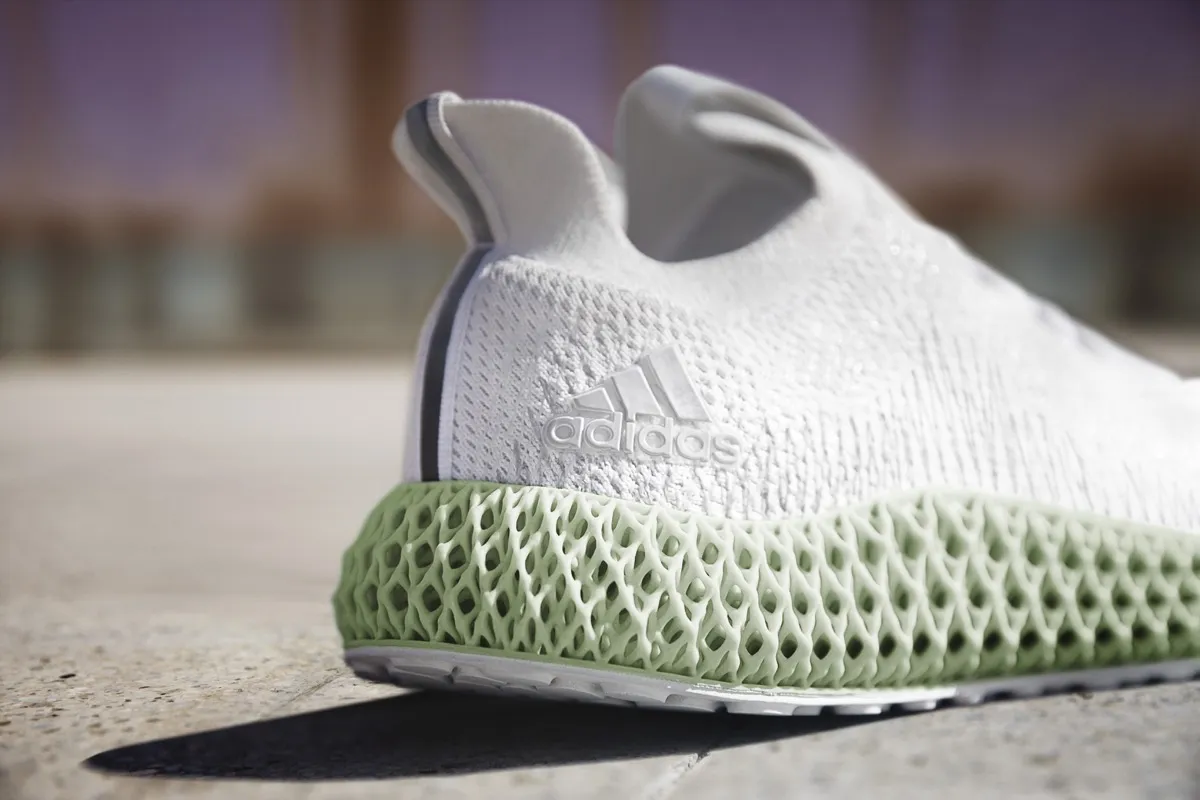
Adidas has embraced SLS technology in their quest for innovation in footwear design. By using SLS printers, they can create bespoke shoe components tailored to the individual needs of athletes, thus improving performance and comfort while reducing waste through efficient material use.
SLS 3D printing is reshaping industrial landscapes by giving new innovative solutions to allow flexibility of design, reduce production timing, and enable customization but at a greater scale. SLS has subsumed numerous sectors, ranging from aerospace to medical to consumer products; real-life applications of SLS showcase the technology’s diversity and effectiveness to be adopted in manufacturing. As more companies start to adopt this technology, more advancements will come, along with success stories that further illuminate SLS’s profound potential in this space to shape the future of manufacturing across sectors.
Future Trends in SLS 3D Printing Beyond 2025
Going forward beyond 2025, the SLS landscape will see notable changes. With advances in technology, more businesses jumping into various industries for adoption, competition, and pressure from what may lie ahead in heightened challenges, the prospects will be ever-changing and influential. This article explores predictions on improvement in technology, adoption growth trends, and challenges to come in this near future.
Predictions for SLS Technology Advancements
The future of SLS technology is characterized by several key advancements that are expected to revolutionize its application:
- Expansion into Final Part Production:
- SLS is transitioning from primarily prototyping to producing end-use parts. This shift is facilitated by improvements in accuracy and surface finishes, enabling manufacturers to produce high-quality components suitable for various industries.
- Larger Build Volumes: New machines with increased build sizes will allow for mass production of lightweight assemblies, streamlining manufacturing processes.
- Faster Print Speeds:
- The introduction of dual laser systems is expected to significantly reduce cycle times, enhancing throughput and making SLS more competitive with traditional manufacturing methods.
- Increased Efficiency: Faster printing capabilities will enable companies to meet tight deadlines and respond quickly to market demands.
- Expanded Material Options:
- The development of over 60 production-grade materials will enhance the versatility of SLS printers. This includes composites and reactive metals that can cater to specific industry needs.
- New Geometries: Innovations such as periodic cellular structures and metamaterials will enable the creation of complex designs that were previously unattainable.
- Integration with Industry 4.0:
- SLS systems will increasingly integrate with smart factory technologies, utilizing AI and IoT for real-time monitoring and optimization.
- Automated Quality Control: In-line inspection systems will ensure part integrity during production, reducing waste and improving reliability.
Growth in Adoption Across Industries
The adoption of SLS technology is expected to grow significantly across various sectors:
- Aerospace and Defense: The need for lightweight, durable components will drive continued investment in SLS printing for aircraft and spacecraft manufacturing.
- Healthcare: Custom medical devices and prosthetics tailored to individual patient needs will see increased use of SLS technology.
- Automotive: The automotive industry will leverage SLS for rapid prototyping and production of functional parts, particularly as electric vehicles gain traction.
- Consumer Goods: The trend towards customization in consumer products such as footwear and eyewear will further propel the adoption of SLS printing.
Potential Challenges
Despite the promising future of SLS technology, several challenges may impact its growth:
- Material Shortages:
- As demand for advanced materials increases, supply chain disruptions could lead to shortages or increased costs for essential powders used in SLS printing.
- Sustainability Concerns: The environmental impact of sourcing raw materials may also become a pressing issue as industries strive for greener practices.
- Pricing Pressures:
- The cost of high-quality SLS printers and materials may pose a barrier to entry for smaller businesses or startups looking to adopt this technology.
- Market Competition: As more players enter the market, pricing strategies may fluctuate, impacting profitability for manufacturers.
- Technological Adaptation:
- Companies may face challenges in integrating new technologies into existing workflows. Training staff and adapting processes can require significant investment and time.
- Keeping Pace with Innovation: Businesses must stay updated with rapid technological advancements to remain competitive.
The future of SLS 3D printing will see immense growth from 2025 onward, driven by advancements in technology, increased penetration of applications across industries, and enhanced focus on sustainability. While challenges like a shortage of materials and cost pressures may occur now and then, it is the promising benefits of increased efficiency, personalization, and innovation that will excite manufacturers. As organizations continue to explore the capabilities of SLS technology to meet new market demands, they will be well-positioned to redefine their manufacturing processes in customer-centric ways.
Conclusion
At the end of our discourse concerning SLS 3D printing, by the year 2025, it is clear that this piece of technology is not just evolving but diversifying into different industries. From aerospace to the healthcare industry, SLS printers have become an integral part of modern manufacturing. Here’s brief coverage of the best SLS printer recommendations for 2025, alongside some final thoughts worth noting before purchase and on how this technology will be in years to come.
Recap of the Best SLS 3D Printer Recommendations for 2025
In 2025, several SLS printers stand out for their performance, versatility, and value. Here’s a summary of the top recommendations:
Printer Model | Price | Build Volume | Key Features | Target Audience |
Formlabs Fuse 1 | ~$18,499 | 165 x 165 x 300 mm | Reliable, precise; great for prototypes | Hobbyists & SMEs |
Sinterit Lisa X | ~$15,490 | Larger than standard | Enhanced capabilities for larger prints | Professionals |
Zongheng3D SuperMaker SLS2030 | ~$39,800 | 200 x 200 x 300 mm | Advanced features for rapid prototyping | Small businesses |
Zongheng3D SuperMaker SLS 3540 PRO | ~$69,800 | 350 x 350 x 430 mm | High precision; supports multiple materials | Industrial users |
These printers cater to a range of needs from entry-level hobbyists to industrial applications, ensuring that there is an option suitable for every budget and requirement.
Consider Your Specific Needs and Budget
Before purchasing an SLS printer, it’s essential to evaluate your specific needs and budget:
- Application Requirements: Consider what you will be printing. Are you focused on prototyping, or do you need production-grade parts?
- Material Compatibility: Different printers support various materials; ensure the printer you choose can handle the materials you intend to use.
- Budget Constraints: While some printers offer advanced features, they may come at a higher price. Determine what fits within your budget while still meeting your requirements.
Taking the time to assess these factors will help you make an informed decision that aligns with your goals.
Final Thoughts on the Future of SLS 3D Printing Technology
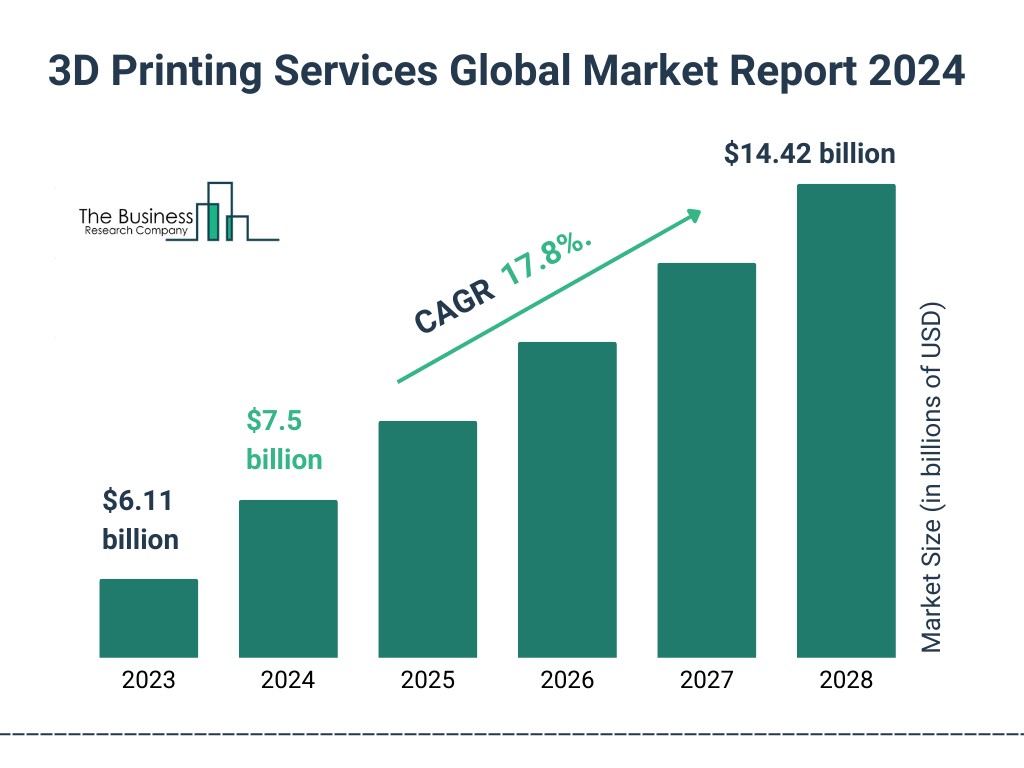
The near future appears bright for SLS technology, as developments continue to materialize. With anticipated print speeds doubling, greater material selection possibilities, and more extensive acceptance in the industrial field, SLS printing may soon redefine the manufacturing horizon. However, materials shortages and pricing pressures may occur with the rise of demand. As organizations increasingly recognize the benefit of SLS technology- increased design flexibility and shortened lead timelines-it is likely that the technology will be integrated quickly into mainstream production. The industry can be further aided by organizations that open themselves to the growth trends today. Additive manufacturing offers excellent opportunities moving forward, whether for the hobbyist looking to experiment or types in production for businesses.