In the 3D printing domain, precision is a necessity, not a luxury. As industries innovate, the demand for parts and prototypes with micron – level accuracy has surged. Among additive manufacturing technologies, Stereolithography (SLA) stands out for its ability to create highly detailed printed objects. Whether for intricate dental models, complex aerospace components, or bringing creative ideas to life, understanding SLA’s resolution limits is crucial.
Imagine producing a miniature car engine with moving parts, all within a fraction of a millimeter—this is the potential of SLA technology. But what does “micron precision” mean, and how can it be achieved? This article will explore the intricacies of SLA, its resolution limits, and the influencing factors. From the technology’s fundamentals to practical tips for fine – detail printing, it will cover all aspects.
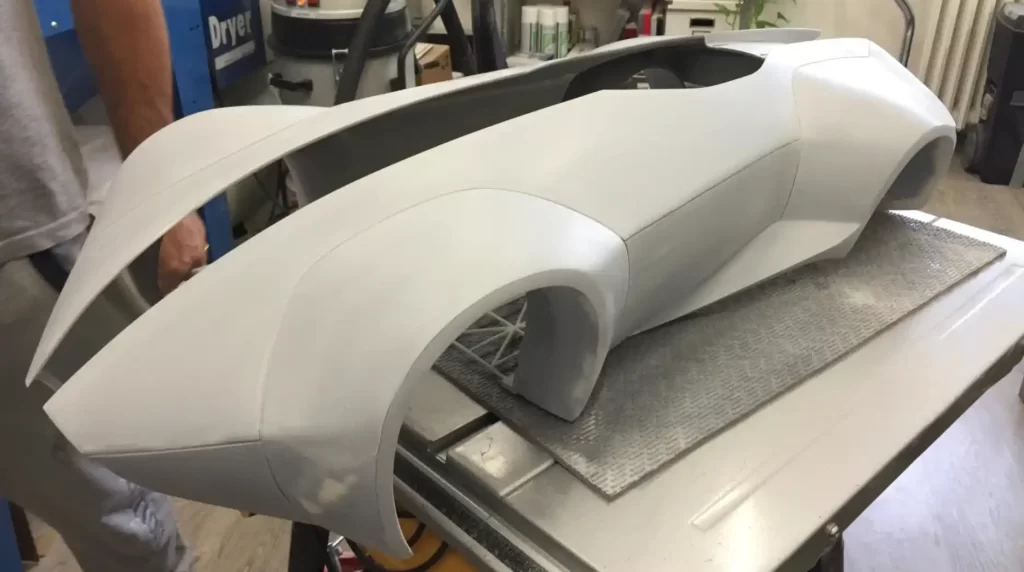
Let’s dive into the world of SLA, uncover the secrets of achieving micron precision, and explore its impact on various industries. This guide is for both seasoned professionals and curious beginners, aiming to provide the knowledge needed to leverage SLA technology effectively in projects.
1. Understanding SLA Technology
Stereolithography (SLA) is a pioneering 3D printing technology. Developed in the 1980s, it was a significant breakthrough in additive manufacturing, enabling the creation of complex geometries with high detail. This section will explore SLA’s definition, key components, and its differences from other 3D printing methods.
1.1 What is SLA?
SLA is a 3D printing process that uses a laser to cure liquid resin into solid parts layer by layer. Here’s how it works:

- Start with a 3D digital model created in Computer – Aided Design (CAD) software.
- Use slicing software to slice the model into thin horizontal layers.
- A UV laser selectively cures the resin in a vat, following the shape of each layer.
- As each layer is completed, the build platform lowers, and the next layer is cured. This continues until the entire object is formed.
The Evolution of SLA
Invented by Chuck Hull in 1983, SLA has evolved significantly. Early systems produced rough parts, while modern SLA printers can create high – resolution, polished components suitable for diverse applications.
1.2 Key Components of SLA
To understand SLA better, it’s essential to look at its key components. Each part plays a crucial role in the printing process, affecting the final product’s quality and precision.
Component | Function |
Resin Vat | Holds the liquid resin that is cured layer by layer. |
UV Laser/Projector | Cures the resin with ultraviolet light, determining print accuracy and detail. |
Build Platform | The surface where the object is printed; it moves down incrementally as layers are added. |
Control Software | Manages the printing process, including laser movement, exposure time, and layer thickness. |
Types of Resins
The resin type used can greatly impact the SLA print outcome. Common resin types include:
- Standard Resins: Suitable for general – purpose applications and prototyping.
- Engineering Resins: Designed for durability and heat resistance, ideal for functional testing.
- Dental Resins: Formulated for dental applications, ensuring biocompatibility.
- Flexible Resins: Enable the creation of rubber – like parts, useful for applications requiring elasticity.
How SLA Differs from Other 3D Printing Technologies
SLA differs from other 3D printing methods like Fused Deposition Modeling (FDM) and Selective Laser Sintering (SLS) in several ways:
Aspect | SLA | FDM | SLS |
Material | Liquid photopolymer resin | Thermoplastic filament | Powdered materials |
Detail & Finish | High resolution and smooth surface finish | Moderate detail, rougher finish | Good detail with a grainy texture |
Speed | Slower, due to layer – by – layer curing | Faster for larger parts | Moderate, depending on layer thickness |
Cost | Higher initial cost because of resin and equipment | Generally lower cost | Higher operational costs |
SLA technology has revolutionized the creation and prototyping of intricate designs. Its ability to produce high – resolution parts with excellent surface finish makes it a popular choice across industries. Understanding SLA’s fundamentals sets the stage for exploring its resolution limits and achieving micron precision.
2. The Concept of Resolution in 3D Printing
In 3D printing, resolution is a critical factor that directly affects the quality, detail, and accuracy of printed objects. For those aiming for high – quality SLA prints, understanding resolution, its measurement, and its significance in the SLA process is essential. This section will explore these aspects.
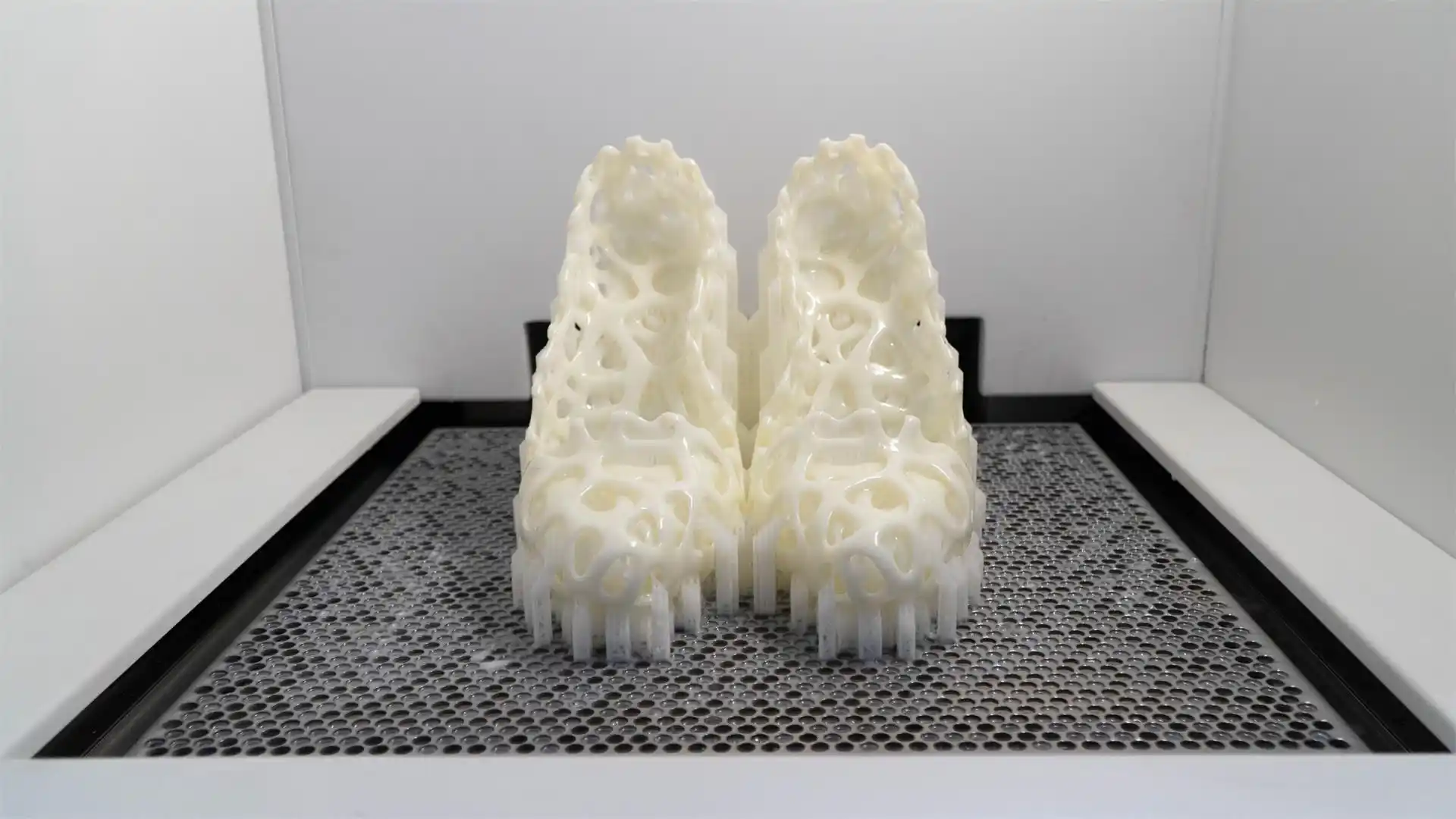
2.1 What is Resolution?
Resolution in 3D printing refers to the level of detail a printer can achieve in the final product. It’s often expressed in microns (µm), with smaller micron values indicating higher resolution and more detailed prints.
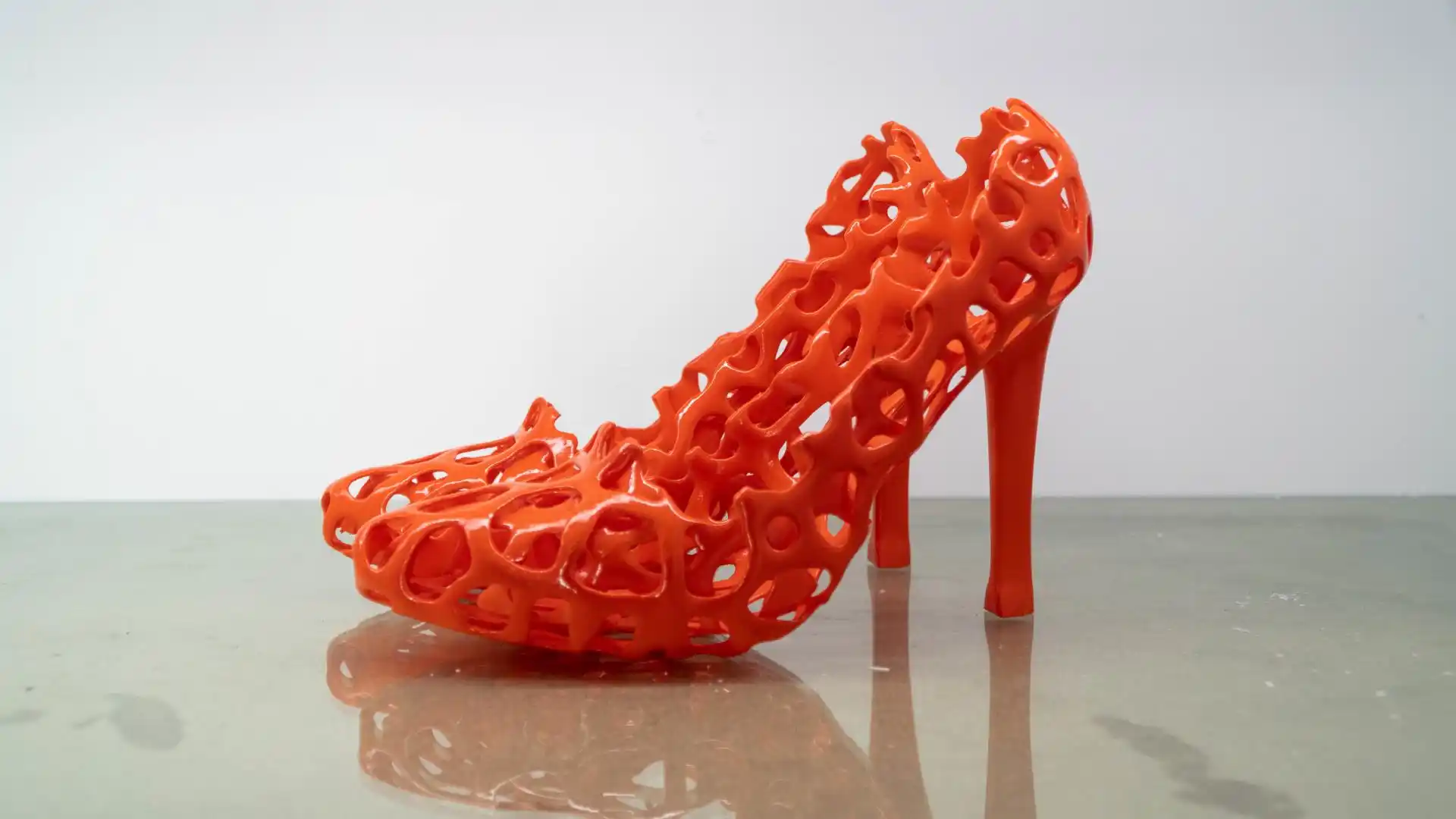
- Spatial Resolution: This is the smallest feature size a printer can produce. In SLA, it’s determined by the laser spot size and the resin – curing accuracy.
- Layer Resolution: It pertains to the thickness of each printed layer. Thinner layers usually result in better detail and smoother surfaces.
- Temporal Resolution: Although less discussed, it involves the speed of curing each layer, which impacts the overall print time.
2.2 How is Resolution Measured?
Measuring resolution in SLA involves understanding several key metrics:
Metric | Description |
Minimum Feature Size | The smallest detail that can be accurately reproduced. |
Layer Thickness | The height of each layer, typically ranging from 25 – 100 microns. |
XY Resolution | The accuracy of movement in the horizontal plane, related to the laser or projector’s dot size. |
Z Resolution | The precision of layer height, determining vertical detail. |
Minimum Feature Size
The minimum feature size is a crucial resolution measure in SLA. It defines the smallest printable detail without loss of fidelity. Modern SLA printers can achieve feature sizes as small as 50 microns or even lower, depending on technology and settings.
Layer Thickness
Layer thickness significantly impacts the overall resolution of an SLA print. Common layer thickness settings range from 25 microns (high resolution) to 100 microns (standard resolution), with different effects on the print:
Layer Thickness | Impact on Print |
25 Microns | High – detail, smooth surfaces, but longer print times. |
50 Microns | A balance between detail and speed, suitable for most applications. |
100 Microns | Faster prints, but less detail; good for rough prototypes. |
Importance of Resolution in SLA
Achieving the right resolution is crucial for several reasons:
- Quality of Final Product: Higher resolution leads to finer details and a smoother finish, essential for applications like dental models and intricate prototypes.
- Functional Testing: For engineering and mechanical parts, precision affects component fit and functionality.
- Aesthetic Appeal: In industries such as jewelry and art, resolution impacts the printed piece’s visual quality.
Resolution is a fundamental concept in 3D printing, directly influencing the final product’s quality, detail, and functionality. In SLA, understanding resolution measurement and its influencing factors, like minimum feature size and layer thickness, is vital for achieving micron precision. This knowledge helps users make informed decisions when configuring SLA printers for optimal results.
3. SLA Resolution Limits
Achieving high precision in SLA printing isn’t just about setting a high – resolution option. Understanding SLA’s resolution limits is crucial for maximizing its capabilities. This section will explore the factors affecting resolution, the concept of minimum feature size, and the impact of layer thickness on print quality.
3.1 Factors Affecting Resolution
Several factors influence SLA printing’s resolution limits. Understanding these can help users optimize prints for the desired detail level.
- Resin Characteristics
- Viscosity: Resin thickness affects its flow and curing. High – viscosity resins may not fill fine features, limiting detail.
- Curing Time: The time for resin to cure under UV light impacts feature accuracy. Insufficient curing can cause detail loss or blurring.
- Light Source Specifications
- Wavelength: The UV light wavelength in SLA printers affects cure depth and resolution. Shorter wavelengths generally enable finer details.
- Laser Spot Size: In laser – based SLA systems, the laser spot diameter directly impacts the minimum feature size. Smaller spots create more precise details.
- Build Platform Mechanics
- Platform Stability: A stable build platform during printing is crucial. Vibrations or movements can lead to print inaccuracies.
- Layer Registration: Accurate layer alignment is essential for maintaining resolution. Misalignment can cause visible seams and detail loss.
3.2 Minimum Feature Size
The minimum feature size is a critical metric for determining SLA’s resolution limits. It refers to the smallest physical dimensions printable without quality compromise.
- Understanding Minimum Feature Size
- Theoretical vs. Practical Limits: While SLA can theoretically achieve very small feature sizes, practical limitations arise from resin type, printer capabilities, and the curing process. Modern SLA printers can typically produce features as small as 50 microns, but optimal conditions are required.
- Examples of Minimum Feature Sizes by Application
Application | Typical Minimum Feature Size |
Dental Models | 50 microns |
Jewelry Design | 30 – 50 microns |
Prototyping Functional Parts | 100 microns |
Architectural Models | 100 – 200 microns |
3.3 Layer Thickness and Its Impact
Layer thickness is another key factor affecting SLA resolution. It influences both print quality and speed.
- The Trade – offs of Layer Thickness
- Thinner Layers (25 microns): Offer higher detail, smoother surfaces, and better representation of intricate designs but result in longer printing times due to more layers.
- Standard Layers (50 microns): Provide a balance between detail and speed, suitable for most applications, though with slightly less detail than thinner layers.
- Thicker Layers (100 microns): Enable faster printing, making them suitable for rough prototypes and larger models, but with reduced detail and visible layer lines, which may not be acceptable for high – quality prints.
- Layer Thickness vs. Print Speed
Layer Thickness | Print Speed | Detail Quality |
25 microns | Slow | High |
50 microns | Moderate | Moderate |
100 microns | Fast | Low |
SLA technology’s resolution limits are determined by resin properties, light source specifications, and mechanical factors. Understanding these limits, especially minimum feature size and layer thickness, is essential for achieving the desired print detail. Optimizing these parameters can push the boundaries of SLA printing precision.
4. Achieving Micron Precision
Achieving micron precision in SLA printing is essential for applications demanding high detail and accuracy. Whether creating intricate prototypes or functional parts, optimizing SLA settings and materials is key. This section will explore practical tips for optimizing settings, selecting the right resin, and using effective post – processing techniques.
4.1 Optimizing SLA Settings
Fine – tuning SLA printer settings can significantly improve print precision. Consider these factors:
- Layer Thickness: For high – detail prints, use a layer thickness between 25 – 50 microns. Thinner layers result in better quality, especially for intricate designs, although they increase print time.
- Exposure Time: Adjust exposure time based on the resin type and layer thickness. A typical range is 5 – 15 seconds per layer. Too short an exposure may lead to incomplete curing, while too long can cause over – curing and detail loss.
- Lift Speed and Retract Speed: Optimize the lift speed (how quickly the build platform moves up after each layer) and retract speed (how fast it moves down). Slower speeds can minimize suction forces that may distort the print, reducing layer separation and improving accuracy.
- Anti – aliasing Settings: If available in slicer software, use anti – aliasing features. This smooths the edges of printed features, enhancing visual quality and reducing jagged edges.
4.2 Choosing the Right Resin
The resin choice is crucial for achieving micron precision. Here’s how to select the right one:
- High – Resolution Resins: These are formulated for fine detail and smooth finishes. They often have lower viscosity and better flow properties. Standard resins are good for general prototyping, while engineering resins are suitable for functional parts, offering durability and heat resistance.
- Specialty Resins: Dental and medical resins are designed for biocompatibility and fine detail, ideal for dental models and surgical guides. Flexible resins provide rubber – like properties without sacrificing detail, useful for applications requiring elasticity.
- Testing and Calibration: Before using a resin for a project, conduct test prints to evaluate detail and accuracy. This ensures the resin meets the specific application’s requirements.
4.3 Post – Processing Techniques
Post – processing is vital for enhancing SLA print precision and finish. Consider these techniques:
- Cleaning: Properly clean the printed part to remove uncured resin. Use isopropyl alcohol (IPA) and an ultrasonic cleaner for thorough cleaning. This ensures a smooth finish without residual material.
- Curing: After cleaning, fully cure the part under UV light according to the resin manufacturer’s guidelines. This solidifies the part, enhances its mechanical properties, and improves surface finish and detail retention.
- Sanding and Finishing: For surfaces needing extra smoothness, lightly sand with fine – grit sandpaper, especially for visible surfaces. Consider painting or applying a clear coat for better aesthetics and protection.
Achieving micron precision in SLA printing requires optimizing printer settings, choosing the right resin, and using effective post – processing techniques. Paying attention to these factors can enhance print quality and detail, making the prints suitable for various applications. The next section will discuss common challenges in SLA precision and their solutions.
5. Common Challenges and Solutions
Although SLA offers high precision and detail, achieving micron – level accuracy can be challenging. Understanding and addressing these challenges is crucial for optimizing the SLA printing experience. This section will discuss common SLA printing issues and their solutions.
5.1 Issues in Achieving Precision
- Layer Separation
- Description: Layer separation occurs when printed layers don’t adhere well, resulting in weak or incomplete prints.
- Causes: Inadequate exposure time and rapid lift speeds that stress the layers.
- Solution: Increase exposure time to ensure proper layer adhesion. Adjust the exposure time according to the resin used. Also, optimize the lift speed to minimize forces on the layers during printing.
- Print Distortion
- Description: Print distortion, such as warping or bending, can be caused by uneven curing or temperature fluctuations.
- Causes: Uneven UV exposure and variations in resin temperature.
- Solution: Maintain a stable ambient temperature during printing to prevent thermal expansion and contraction. Use proper support structures to stabilize the print and reduce distortion risk.
- Surface Imperfections
- Description: Surface imperfections like pitting, roughness, or visible layer lines can reduce print quality.
- Causes: Incorrect layer thickness, inadequate cleaning, or improper curing.
- Solution: Adjust layer thickness for high – detail prints to achieve smoother surfaces. Thoroughly clean the print to remove all uncured resin, preferably using an ultrasonic cleaner. Follow the manufacturer’s guidelines for curing times and conditions to ensure maximum detail and finish.
5.2 Troubleshooting Print Failures
Even with careful preparation, print failures can occur. Here are common failures and troubleshooting methods:
- Incomplete Prints
- Description: Parts of the print may be missing or not fully formed.
- Causes: Insufficient resin in the vat or incorrect printer settings.
- Solution: Check the resin level before starting a print. Verify all printer settings, including exposure time, layer thickness, and lift speed, to ensure they match the print requirements.
- Bubbles or Voids in the Print
- Description: Bubbles or voids in the print can weaken its structure.
- Causes: Air trapped in the resin or rapid build – platform movement.
- Solution: Degas the resin before printing to remove trapped air bubbles. Adjust the lift and retract speeds to allow the resin to flow freely and minimize bubble formation.
Challenges in achieving SLA printing precision are common but can be overcome. Understanding potential issues and implementing effective solutions can improve print quality and achieve the desired micron precision. The next section will explore the applications of micron – precision SLA, its impact on industries, and future trends.
6. Applications of Micron Precision in SLA
Achieving micron precision in SLA printing opens up numerous possibilities across industries. The ability to produce detailed and accurate parts has transformed product design, testing, and manufacturing. This section will explore SLA technology’s applications, showcase case studies, and discuss future trends.
6.1 Industries Utilizing SLA Precision
SLA technology is used in various industries, each benefiting from its ability to create intricate and precise components.
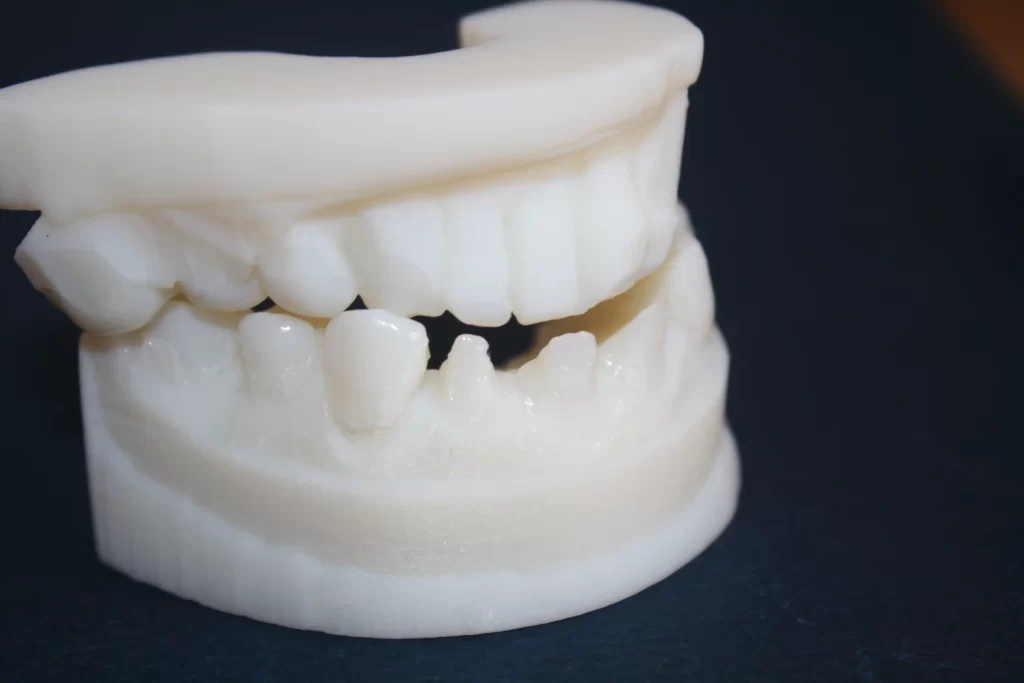
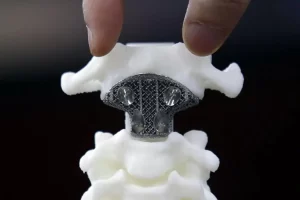
- Dental Industry: SLA is widely used for creating dental models, crowns, bridges, and surgical guides. It offers high – detail reproduction of complex dental anatomies and enables custom – fit solutions for patients.
- Aerospace and Automotive: In these sectors, SLA is used for prototyping parts, tooling, and even end – use components. It can produce lightweight components with intricate geometries, reducing weight without sacrificing strength, and accelerates the design process through rapid prototyping.
- Medical Devices: SLA is employed to produce medical devices, prosthetics, and anatomical models for surgical planning. It allows for customization, improving patient outcomes, and ensures the high accuracy required for functional medical devices.
- Jewelry and Fashion: SLA is increasingly used for creating intricate jewelry designs and fashion accessories. Designers can create unique, detailed pieces that are difficult to achieve with traditional methods, and it speeds up the prototyping process for faster market entry.
- Consumer Products: Companies use SLA for prototyping consumer goods like electronics, toys, and household items. It enables market testing through rapid prototyping and offers customization based on consumer preferences.
6.2 Case Studies of Successful Implementations
- Case Study 2: Aerospace Component Prototyping
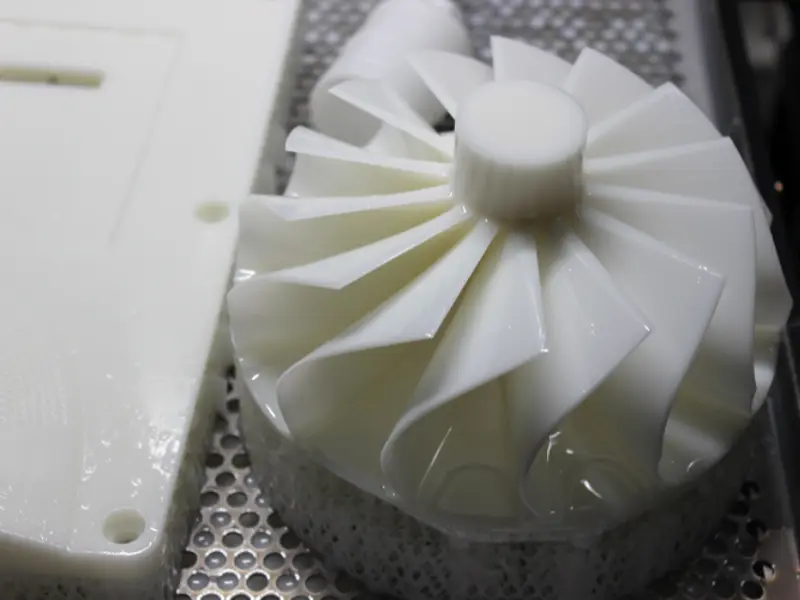
An aerospace manufacturer utilized SLA for prototyping complex engine components. The technology allowed the company to produce lightweight and intricate designs, reducing material costs and improving fuel efficiency. Thanks to the rapid prototyping capabilities of SLA, the company could validate designs more quickly, significantly shortening the time it took for new components to reach the market.
- Case Study 3: Jewelry Design
A jewelry designer embraced SLA technology to create elaborate patterns and details in their pieces. With SLA, the designer was able to craft complex shapes that were previously difficult to achieve. This led to an expansion of the product line, with unique, customizable pieces that attracted a broader customer base.
6.3 Future Trends in SLA Technology
The SLA technology landscape is constantly evolving, with several trends shaping its future:
- Material Advancements
- Biocompatible Resins: The development of new biocompatible materials will expand the applications of SLA in the medical and dental fields. These resins will enable the creation of even more complex and personalized medical devices and dental products.
- High – Strength Resins: Innovations in resin formulations will result in stronger, more durable prints. This will make SLA – printed parts suitable for a wider range of functional applications, such as in high – stress mechanical components.
- Speed and Efficiency Improvements
- Multi – Laser Systems: The introduction of multi – laser SLA printers will substantially increase print speeds. Multiple lasers can work simultaneously, allowing for larger parts to be produced in less time and improving overall productivity.
- Automated Post – Processing: Advances in automated cleaning and curing solutions will simplify the post – processing workflow. Automated systems can ensure consistent results, reduce labor costs, and enhance the overall efficiency of the SLA printing process.
- Integration with Other Technologies
- Hybrid Manufacturing: Integrating SLA with other manufacturing technologies, like CNC machining or injection molding, will create new opportunities. This combination can leverage the strengths of different processes to produce complex parts with enhanced characteristics, such as improved surface finish and mechanical properties.
- Software Innovations: Improvements in slicing software will enable better optimization of print settings. This will further enhance resolution, reduce print times, and make the SLA printing process more user – friendly.
Micron – precision SLA technology is revolutionizing various industries by enabling the production of highly detailed and functional parts. From dental applications to aerospace components, this precision unlocks new paths for innovation and customization. As the technology continues to evolve, the future of SLA holds great promise, with more applications and advancements on the horizon.
7. Conclusion
As we conclude our exploration of achieving micron precision in Stereolithography (SLA), it’s evident that this technology has transformative potential across numerous industries. The high – level of detail and accuracy offered by SLA is not just an advantage; it’s essential for meeting the exacting specifications of modern applications.
Recap of the Importance of Achieving Micron Precision in SLA
Achieving micron precision in SLA printing is crucial for several reasons:
- Quality and Detail: High – resolution prints ensure that intricate designs are accurately reproduced. This is of utmost importance in industries such as dental, aerospace, and jewelry, where the level of detail can determine the success or failure of a product.
- Functional Integrity: For functional parts used in engineering and medical applications, precision is directly related to how well components fit together and perform. Precise parts also tend to have enhanced durability.
- Rapid Prototyping: The ability to quickly produce accurate prototypes allows companies to iterate on their designs faster. This reduces the time to market and cuts down on development costs.
- Customization: Micron precision enables the customization of products to meet individual user needs and preferences. This is a significant advantage in fields ranging from consumer goods to healthcare.
Key Takeaways
Throughout this discussion, several key aspects for achieving micron precision in SLA have been highlighted:
- Understanding Resolution: Knowledge of resolution metrics, including minimum feature size and layer thickness, is fundamental to maximizing the capabilities of SLA technology.
- Optimization of Settings: Fine – tuning printer settings such as exposure time and lift speed is essential for enhancing print quality and achieving the desired level of detail.
- Material Selection: The choice of resin has a significant impact on the print outcome. High – resolution and specialty resins play a crucial role in achieving precision.
- Post – Processing: Proper cleaning, curing, and finishing techniques are vital for enhancing the quality of SLA prints and ensuring they meet the required specifications.
- Overcoming Challenges: Being aware of common challenges like layer separation and print distortion, and applying effective solutions, can greatly improve printing results.
Looking Ahead: The Future of SLA Technology
The future of SLA technology looks promising, with ongoing advancements set to further enhance its capabilities:
- Innovative Materials: Continued research into new resin formulations will lead to even greater precision and functionality. This will expand the applications of SLA in various industries, opening up new opportunities for product development.
- Faster Printing Processes: Developments in multi – laser systems and automated post – processing will make SLA printing faster and more efficient. This will make it a more viable option for large – scale production, increasing its competitiveness in the manufacturing industry.
- Integration with New Technologies: As SLA integrates with emerging technologies such as artificial intelligence and machine learning, we can expect smarter printing solutions. These will optimize the printing process and improve the final product quality.
- Sustainability Initiatives: Future innovations may focus on developing eco – friendly resins and reducing waste in the SLA process. This will help the technology align with global sustainability goals, making it more environmentally friendly.
Final Thoughts
Achieving micron precision in SLA printing is not just about the technology itself; it’s about pushing the boundaries of what can be created and how these creations can be utilized across industries. Whether you’re an engineer, designer, or manufacturer, understanding and harnessing the power of SLA is essential for creating products that meet the highest standards of quality and performance. As we look to the future, SLA technology will continue to play a pivotal role in innovation, shaping the way we design, prototype, and produce in an increasingly complex world.