What is Selective Laser Sintering?
Selective Laser Sintering (SLS) is an additive manufacturing process. It commences with a bed of powdered materials such as nylon, polyamide, or other specialized polymers. A high-powered laser selectively fuses the powder particles layer by layer based on a 3D model. For instance, when creating a small, intricate figurine, the laser traces and fills each slice in the powder bed. The unfused powder acts as a support for overhanging parts, reducing the need for additional support structures and minimizing material waste and post-processing time.
Common materials used in SLS include nylon and polyamide. Nylon is popular for its durability and flexibility, suitable for applications like automotive and consumer goods prototypes and end products. Polyamide offers similar properties and is used when specific strength and heat resistance are required, such as in engineering components and housings.
Material | Properties | Typical Applications |
Nylon | Durable, flexible | Prototypes, automotive parts, consumer goods |
Polyamide | Good strength, heat resistance | Engineering components, housings |
SLS is well-suited for products with complex geometries, low-volume production runs, and functional prototypes. It can produce objects with intricate internal structures or shapes that are difficult to manufacture using traditional methods, like custom medical implants with porous structures. For low-volume production, it avoids the high costs of tooling setups associated with mass-production techniques. Engineers and designers also favor it for creating functional prototypes that closely mimic the final product’s properties.
Initial Investment Costs
Understanding the initial investment costs is crucial when considering SLS. The price range of SLS machines varies widely. Entry-level models start around $50,000, suitable for small-scale or hobbyist use. Mid-range industrial machines, offering better build volumes and advanced features, cost between $150,000 and $300,000. High-end, large-format, and highly precise systems can exceed $500,000. The cost depends on factors such as build volume, laser power and precision, and machine build quality and durability.
SLS requires specialized software for 3D model preparation. Basic software packages for single-user licenses may start at around $2,000 per year. More advanced software with features like advanced material simulation and multi-material support can cost upwards of $10,000 per year. Some manufacturers offer software bundles with their machines, which can be a more cost-effective option in the long term.
SLS machines need a dedicated space with specific environmental conditions. A typical machine requires a room of at least 10 feet by 10 feet, plus space for operator access and material storage. If suitable space is not available, the cost of renting or building an addition must be considered. Renting a small industrial space can cost between $500 and $2,000 per month, depending on the location. Additionally, environmental controls such as air conditioning and filtration systems may need to be installed and maintained, costing an additional $5,000 to $10,000 annually.
Operator training is essential for the proper use of SLS machines. Training programs vary in cost and duration. A basic one-day course provided by the machine manufacturer may cost around $1,000 per operator. More comprehensive programs covering advanced techniques, maintenance, and troubleshooting can cost upwards of $5,000 per operator and may span several days or weeks.
Initial Investment Component | Cost Range | Key Considerations |
SLS Machine | $$50,000 -$$800,000+ | Build volume, laser specifications, quality |
Software | $$2,000 -$$10,000+ per year | Features, license type |
Space | $$500 -$$2,000 per month (rent) + $5,000 – $10,000 annual (environmental controls) | Size, location, environmental needs |
Training | $$1,000 -$$5,000+ per operator | Duration, comprehensiveness |
Material Costs
Material costs play a vital role in SLS. Nylon, a commonly used material, typically costs between $30 and $80 per kilogram. Specialty nylons with enhanced properties, such as increased strength or heat resistance, can cost over $100 per kilogram. Polyamide materials usually fall within a similar price range, with standard powders costing between $40 and $90 per kilogram, and specialized ones commanding higher prices depending on properties like chemical resistance.
Material | Price per Kilogram Range | Special Considerations |
Nylon | $$30 -$$120+ | Enhanced strength or heat resistance variants |
Polyamide | $$40 -$$110+ | Chemical resistance and other specialty types |
Compared to other additive manufacturing methods like Fused Deposition Modeling (FDM), SLS materials are generally more expensive per unit. However, SLS offers the ability to produce more complex geometries and parts with better mechanical properties.
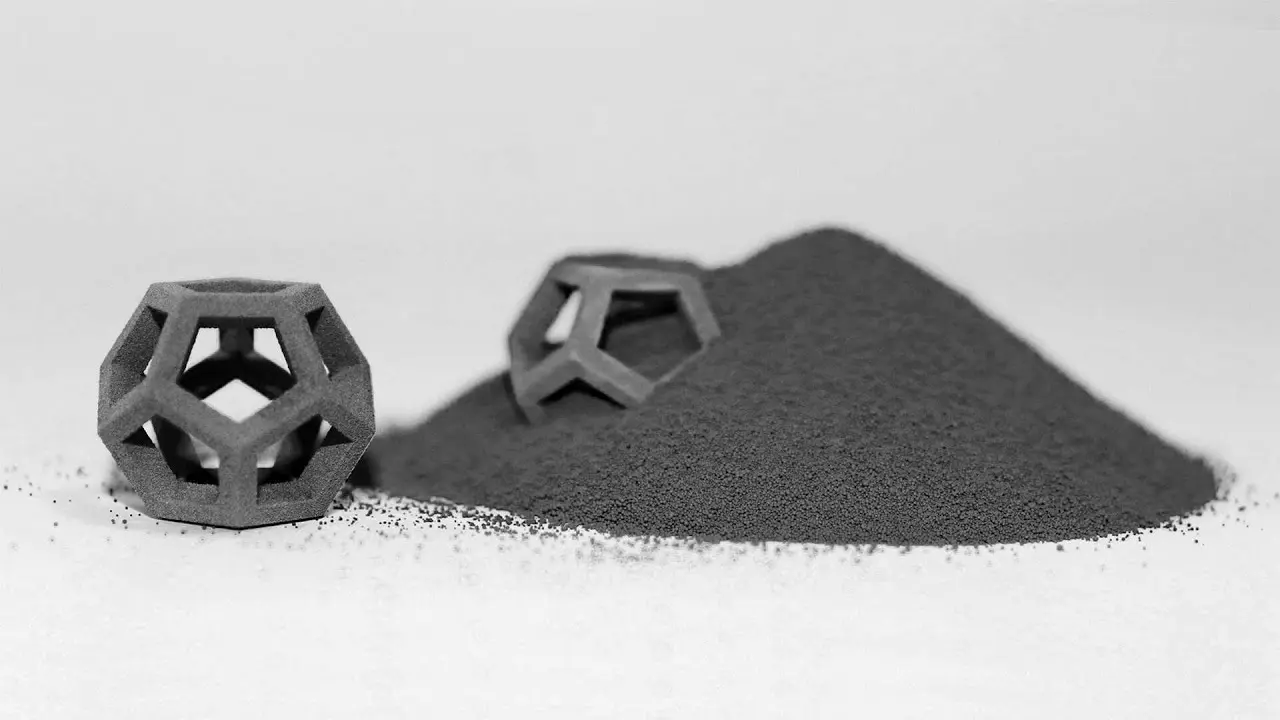
Part design and build orientation significantly affect material consumption. Parts with hollow interiors or lattice structures use less material than solid blocks of the same external dimensions. By optimizing part geometries, material usage can potentially be reduced by up to 30% or more. Build orientation also impacts consumption; improper orientation may require more support structures and thus more material.
SLS typically has lower material waste compared to some other manufacturing methods. The unfused powder can be recycled and reused in subsequent builds. However, to minimize waste further, proper powder handling and recycling processes are necessary. Using a closed-loop powder recycling system can recover up to 90% of the unused powder, reducing the need for new material purchases and waste disposal costs.
Operational Costs
Operational costs are an important factor in determining the viability and cost-effectiveness of SLS. SLS machines consume a significant amount of energy, typically ranging from 3 to 10 kilowatts per hour, depending on machine size, laser power, and build complexity. For example, a mid-sized machine running an 8-hour print job at 5 kilowatts per hour would consume 40 kilowatt-hours of electricity. At an electricity cost of $0.15 per kilowatt-hour, the energy cost for this single print job would be $6. Regular use can lead to substantial energy costs over time.
Regular maintenance is crucial for the smooth operation of SLS machines and to ensure print quality. Maintenance tasks include cleaning the build chamber, replacing filters, and calibrating the laser. The cost of routine maintenance can range from $2,000 to $5,000 per year. However, unexpected breakdowns and repairs can occur. Major repairs, such as replacing a faulty laser or damaged build platform, can cost between $5,000 and $20,000 or more, depending on the component and machine model. Some manufacturers offer maintenance contracts to cover routine servicing and certain repair work.
Consumables in SLS also contribute to operational costs. Build plates need to be replaced periodically, typically costing between $500 and $2,000 each, with replacement intervals ranging from 6 months to 2 years. Support structures, although required less frequently in SLS than in other methods, can add $100 to $500 to the cost of each build, depending on part complexity.
The SLS process requires skilled operators. The labor cost varies depending on location and expertise. Entry-level operators may earn an annual salary of around $30,000 to $40,000, while more experienced technicians with advanced skills in SLS and post-processing can command a salary of $50,000 to $80,000 or more. Additionally, tasks such as loading and unloading the build chamber add to the overall labor cost.
Operational Cost Component | Cost Range | Frequency/Details |
Energy Consumption | $$0.15 -$$X per kWh (varies by region) * 3 – 10 kWh per hour | Hourly consumption during operation |
Maintenance | $$2,000 -$$5,000 per year (routine), $5,000 – $20,000+ (major repairs) | Annual routine, as-needed major repairs |
Build Plates | $$500 -$$2,000 | Every 6 months – 2 years |
Support Structures | $$100 -$$500 per build | Varies per part complexity |
Scalability and Cost
Scalability is a key consideration when evaluating the cost-effectiveness of SLS compared to other manufacturing processes. As the production volume of SLS parts increases, the cost per part generally follows a specific pattern. At low volumes (1 – 10 parts), the cost per part is relatively high due to significant fixed costs associated with the initial investment in the machine, software, and operator training. For example, if the total setup and overhead costs amount to $50,000 and only 10 parts are produced, the cost per part could be as high as $5,000. However, as volume increases, the fixed costs are spread over more parts, reducing the cost per part. When producing 1,000 parts, the fixed cost contribution per part might drop to $50.
Production Volume | Approximate Cost per Part | Explanation |
Low (1 – 10 parts) | High, e.g., $5,000 | High fixed cost impact |
Medium (100 – 500 parts) | Moderate, e.g., $500 – $1,000 | Fixed cost spread |
High (1,000+ parts) | Low, e.g., $50 – $200 | Economies of scale |
SLS offers several advantages in scalability. It allows for quick production of small to medium batches without extensive tooling changes or setup times, enabling businesses to respond rapidly to market demands and make design modifications easily. Additionally, it provides design freedom to create complex geometries without incurring additional costs as volume increases. However, SLS also has limitations. The selection of materials is somewhat limited compared to traditional manufacturing processes like injection molding. As production volume grows, larger parts or higher quantities may require multiple build runs or larger, more expensive machines due to build volume constraints.
Case studies illustrate the impact of scalability on SLS production. Company A, a small medical device manufacturer, initially produced small batches (20 – 50 instruments per month) of custom surgical instruments using SLS. The cost per instrument was around $800 due to low volume. As production increased to 500 instruments per month, the cost per instrument dropped to $200. Company B, a consumer electronics company, started with 100 unique phone cases per week. The cost per case was $50. But when scaling up to 1,000 cases per week, they faced challenges with the build volume of their SLS machine, leading to increased labor and energy costs and the need to consider a hybrid manufacturing approach.
Quality and Cost Relationship
The relationship between quality and cost in SLS is complex and significant. SLS generally provides good dimensional accuracy, typically within ± 0.1 – 0.3 mm, depending on the machine and process parameters. This level of accuracy suffices for many applications such as prototyping and the production of functional parts where tight tolerances are not critical. However, achieving higher accuracy, such as within ± 0.05 mm, may require additional calibration and optimization of the SLS process, involving more precise laser control, advanced software settings, and potentially more expensive machine components.
The surface finish of SLS parts is often relatively rough compared to some other manufacturing methods, typically having a matte or granular appearance with a roughness value (Ra) ranging from 10 – 20 μm. For products with visible surfaces or those requiring a smooth feel, additional post-processing is necessary. Processes like bead blasting, tumbling, or coating can improve the surface finish, but these steps add to the cost. For example, a simple bead blasting operation might cost $50 – $100 per batch of parts, depending on size and quantity.
Quality requirements have a direct impact on the overall cost. In industries where extremely tight tolerances are essential, such as aerospace or medical implants, the SLS process may need to be fine-tuned. This can involve using higher-resolution lasers, advanced scanning systems, and extensive quality control checks. The cost of upgrading the machine or implementing these additional quality measures can be significant. For a high-precision SLS machine with enhanced tolerance capabilities, the price could be 50% – 100% higher than a standard machine. Additionally, calibration and quality inspection time increase labor costs.
Quality control and inspection are crucial in SLS to ensure parts meet the required standards. This involves using tools such as coordinate measuring machines (CMMs), optical scanners, and manual inspection. The cost of quality control includes the purchase or rental of inspection equipment, operator training, and inspection time. A basic CMM can cost around $20,000 – $50,000, and an optical scanner might range from $10,000 – $30,000. Operator training for these devices can cost $1,000 – $5,000 per person. Inspection time can add several minutes to each part, increasing labor costs. For example, if it takes 5 minutes per part for inspection and an operator’s hourly rate is $30, the inspection cost per part would be $2.50. For a production run of 1,000 parts, the total inspection cost would be $2,500.
Quality Aspect | SLS Quality Level | Cost Implications |
Dimensional Accuracy | ± 0.1 – 0.3 mm (standard), ± 0.05 mm (high precision) | Higher precision requires upgraded machine and more calibration time |
Surface Finish | Ra 10 – 20 μm (as-is), improved with post-processing | Post-processing costs vary depending on method and part complexity |
Quality Control | Use of CMMs, optical scanners, manual inspection | Equipment cost, operator training, and inspection time add to overall cost |
Comparison with Other Manufacturing Processes
When evaluating SLS, it is essential to compare it with other manufacturing processes to understand its cost advantages and disadvantages.
Compared to traditional subtractive manufacturing like CNC machining, SLS has relatively lower setup costs. In CNC machining, creating custom tooling, fixtures, and programming for complex parts can cost several thousand to tens of thousands of dollars. For example, machining a custom aluminum part with intricate features might require a specialized cutting tool costing $5,000 and several hours of programming time. In contrast, SLS only requires a 3D model and minimal physical setup, with the main setup cost related to machine and software preparation, typically ranging from a few hundred to a couple of thousand dollars.
SLS also has lower material waste. CNC machining often results in 60% – 80% material waste due to its subtractive nature, while SLS typically has 5% – 15% waste, depending on part design and build process.
For small to medium batch sizes, SLS can be faster. A simple CNC-machined part might take 30 minutes to an hour per piece including setup, while SLS can produce multiple parts simultaneously in a single build. For example, a batch of 20 small plastic parts might take 6 – 8 hours in SLS, which is faster than machining each part individually. However, for large production runs of simple parts, CNC machining is more efficient due to its high-speed cutting capabilities.
Comparison Factor | SLS | CNC Machining |
Setup Cost | Low ($few hundred – $couple thousand) | High ($few thousand – $tens of thousand) |
Material Waste | Low (5% – 15%) | High (60% – 80%) |
Production Time (small – medium batch) | Faster | Slower |
Production Time (large batch simple parts) | Slower | Faster |
Compared to other additive manufacturing techniques like Fused Deposition Modeling (FDM), SLS has higher material costs. FDM uses thermoplastic filaments that are generally cheaper, with a kilogram of PLA filament costing $20 – $30, while SLS powders like nylon can range from $30 – $120 per kilogram. However, SLS offers better material properties and can produce parts with higher strength and heat resistance.
SLS provides better dimensional accuracy and surface finish than FDM. FDM parts have visible layer lines and a rougher surface finish with a typical Ra value of 20 – 50 μm, while SLS has an Ra of 10 – 20 μm. Achieving a similar quality in FDM would require additional post-processing steps like sanding and coating, which add to the cost.
SLS is more suitable for highly complex geometries and parts with internal structures. FDM has limitations in creating overhangs and complex internal cavities without significant support structures, and removing these supports adds to production time and material waste. SLS can handle such complex designs more easily, potentially reducing overall cost for complex parts.
Comparison Factor | SLS | FDM |
Material Cost | Higher ($30 – $120/kg) | Lower ($20 – $30/kg) |
Build Quality | Better (Ra 10 – 20 μm) | Poorer (Ra 20 – 50 μm) |
Complexity of Parts | High suitability | Limited by support structures |
SLS is cost-effective for low to medium volume production of complex, custom parts with specific material requirements, such as custom orthopedic implants. It is also advantageous when rapid prototyping is required. However, for large volume production of simple, standardized parts, injection molding or CNC machining may be more economical. SLS may not be suitable when the required material is not available or not well-suited for the process.
Long-Term Cost Considerations
Long-term cost considerations are important when adopting SLS. SLS machines depreciate over their useful lifespan. The rate of depreciation can vary depending on factors such as brand, model, technological advancements, and usage intensity. Typically, an SLS machine may lose 10% – 20% of its value in the first year. For a machine purchased at $300,000, this means a depreciation of $30,000 – $60,000 in the initial year. Over a five-year period, the total depreciation could amount to 40% – 60% of the original cost. Depreciation affects the decision of when to upgrade or