Exploring the Costs of 3D Printing Technologies
3D printing has transformed various industries in the past decade. Selective Laser Sintering (SLS) is a prominent 3D printing technology known for creating durable, complex parts. This article compares SLS with other methods like FDM, SLA, and MJF in terms of cost, to help users make informed decisions based on their specific needs. now we are going to see cost comparison of 3d printing methods with others.
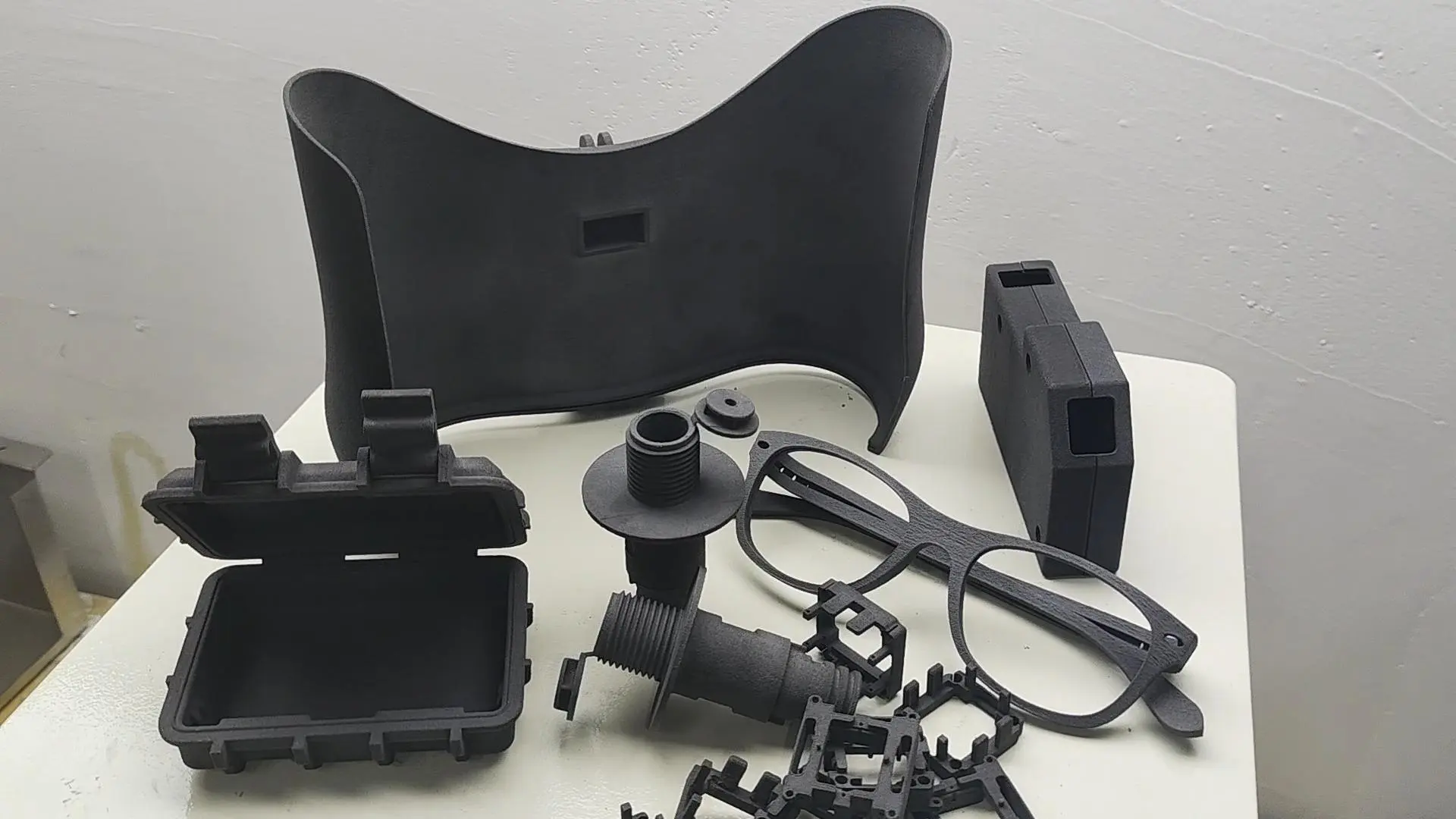
What is SLS (Selective Laser Sintering)?
How SLS Works
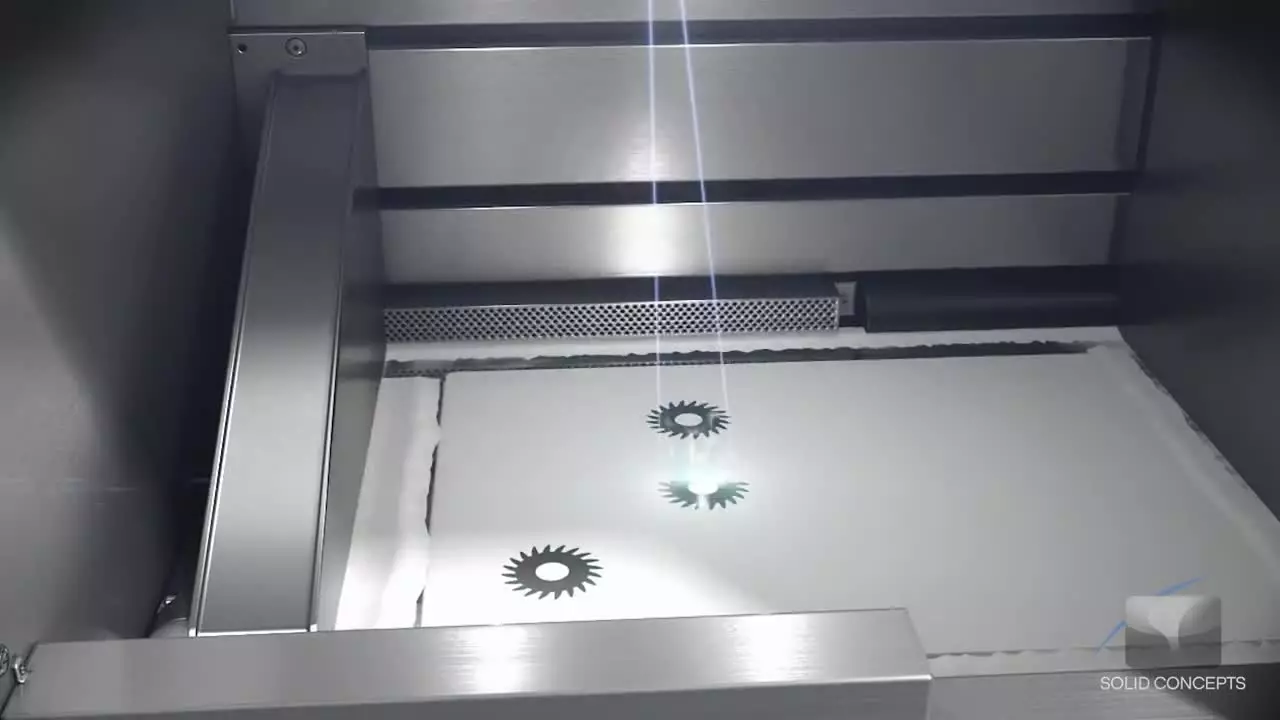
SLS is an additive manufacturing process. It starts with spreading a thin layer of powdered material (e.g., nylon) on the build platform. A high-powered laser selectively fuses the powder particles following the 3D model design, heating them just below the melting point. After each layer is sintered, the platform lowers, and a new layer of powder is added. Once printing finishes, the chamber cools, and the unfused powder is removed, leaving the final part.
Key Advantages of SLS
- No Support Structures Required: Unlike some other methods, SLS uses the surrounding unfused powder for support, enabling the creation of complex geometries like interlocking parts.
- High-Quality and Durable Parts: SLS parts, such as those made from nylon 12, have excellent mechanical strength and durability, suitable for functional prototypes and end-use components.
- Efficient Material Usage: The unused powder in SLS can often be recycled for future prints, reducing waste and material costs.
- Scalability for Batch Production: SLS can print multiple parts simultaneously, making it efficient for small- to medium-scale production runs.
Materials Used in SLS
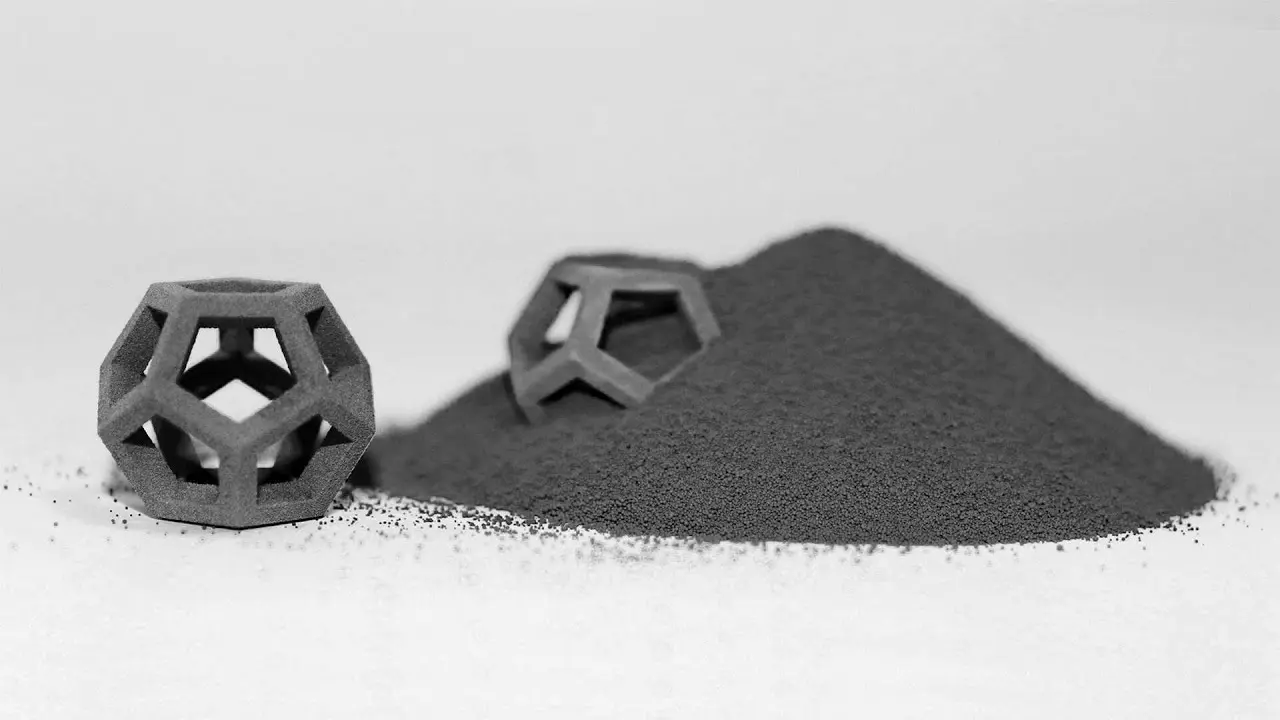
SLS is compatible with various thermoplastic polymers. Commonly used materials include nylon (PA12 and PA11), glass-filled nylon, TPU, and composite powders. Each material has unique properties and applications, such as nylon being suitable for functional parts and TPU for flexible components.
Material | Description | Applications |
Nylon (PA12) | Strong, lightweight, and resistant to wear. Excellent for functional parts. | Prototypes, tools, housings, and enclosures. |
Nylon (PA11) | More flexible and impact-resistant than PA12. Bio-based and sustainable. | Automotive, sports equipment, and medical devices. |
Glass-Filled Nylon | Reinforced with glass fibers for enhanced stiffness and strength. | Structural components and parts under heavy loads. |
TPU (Thermoplastic Polyurethane) | Elastic, rubber-like material with excellent flexibility. | Gaskets, seals, and wearable products. |
Composite Powders | Blends of polymers and other materials like aluminum for specialized properties. | Aerospace and high-performance applications. |
Applications of SLS
SLS is widely used in prototyping, end-use part manufacturing (e.g., in automotive and aerospace), medical applications (like custom prosthetics), and consumer product production (e.g., eyewear frames).
Overview of Other 3D Printing Technologies
FDM (Fused Deposition Modeling)
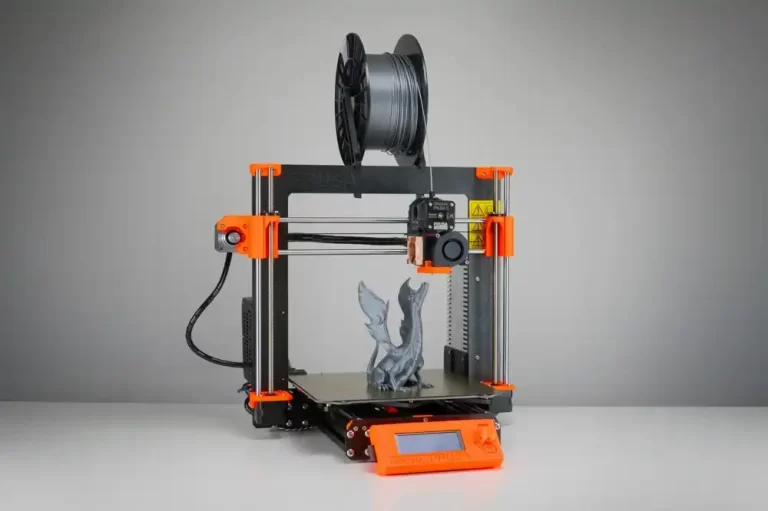
- How It Works: FDM extrudes a thermoplastic filament through a heated nozzle, laying down material layer by layer.
- Advantages: Affordable printers, beginner-friendly, and a wide selection of materials like PLA, ABS, PETG, and TPU.
- Disadvantages: Low surface quality, weaker mechanical properties compared to SLS, and limited design freedom due to the need for support structures.
SLA (Stereolithography)
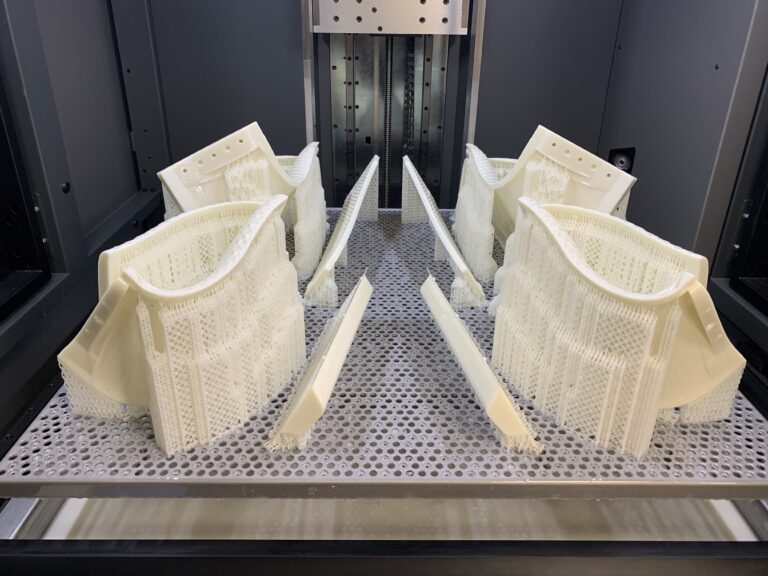
- How It Works: SLA cures liquid resin with a UV laser or light source, creating detailed parts layer by layer.
- Advantages: High precision, ideal for small and intricate parts, and versatile resins.
- Disadvantages: Expensive resins, post-processing required (washing and curing), and brittle parts.
MJF (Multi Jet Fusion)
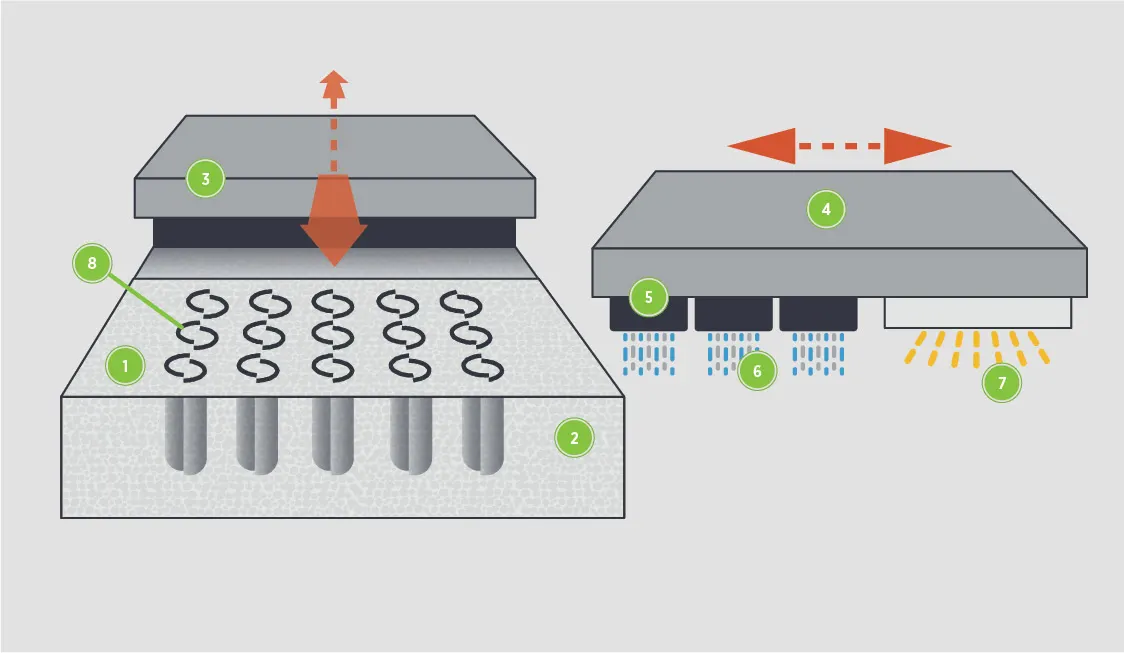
- How It Works: MJF deposits a fusing agent onto powder using inkjet arrays and then heats it to fuse the material.
- Advantages: Efficient production, excellent surface finish, and high material reusability.
- Disadvantages: High initial investment and a relatively limited range of materials.
DLP (Digital Light Processing)
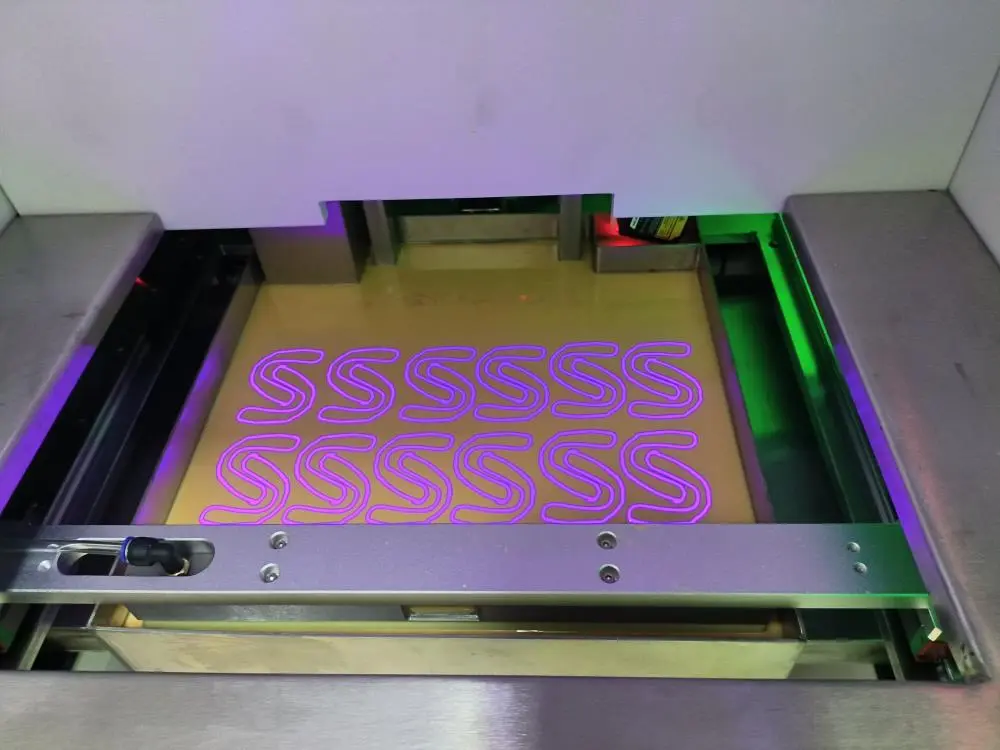
- How It Works: DLP cures resin using a digital light projector, similar to SLA but curing entire layers at once.
- Advantages: Fast printing speeds and fine details.
- Disadvantages: Limited build volume and high resin costs.
Comparison Table
Technology | Cost | Precision | Material Types | Best For |
SLS | High | High | Nylon, composites | Functional parts, batch production |
FDM | Low | Moderate | PLA, ABS, PETG, TPU | Prototyping, hobby projects |
SLA | Moderate | Very High | Photopolymer resins | Jewelry, dental, intricate designs |
MJF | Moderate to High | High | Nylon, glass-filled powders | Functional prototypes, small-batch runs |
DLP | Moderate | Very High | Photopolymer resins | Small, detailed parts |
Factors Influencing 3D Printing Costs
Material Costs
- FDM: Uses thermoplastic filaments (e.g., PLA at $20–$50/kg). Minimal waste as most material is used in the final print.
- SLA: Liquid resins cost $50–$150 per liter. Some leftover resin may be unusable.
- SLS: Nylon powders cost $60–$200/kg. High recyclability with 50%–80% of unused powder reusable.
- MJF: Similar to SLS in cost ($70–$150/kg) with high material efficiency.
Printer Costs
Technology | Price Range | Typical Use Case |
FDM | $$200$$10,000+ | Hobbyists, small businesses, prototyping |
SLA | $$500$$6,000+ | Professionals, jewelry, dental, design |
SLS | $$10,000$$500,000+ | Industrial production, functional parts |
MJF | $$50,000$$500,000+ | Batch production, high-end applications |
Operating Costs
- Electricity Costs: FDM is low, SLA is moderate, and SLS/MJF are high due to their power requirements.
- Maintenance Costs: FDM requires regular nozzle and bed cleaning. SLA needs resin tank cleaning and light source replacement. SLS/MJF have high maintenance costs due to machine complexity.
Labor Costs
FDM may require significant labor for post-processing if support removal and sanding are needed. SLA is labor-intensive for washing and curing. SLS and MJF have low labor requirements as no support structures are needed.
Post-Processing Costs
FDM may need support removal and sanding. SLA requires washing and curing. SLS and MJF mainly involve powder removal, with MJF having an optional coloring step.
Build Speed and Cost Implications
FDM is slow for large parts. SLA is faster for small, detailed parts but slower for larger objects. SLS/MJF are among the fastest, especially for batch production.
Scalability and Cost Per Part in Batch Production
SLS and MJF are highly scalable, reducing cost per part in batch production. FDM is limited in scalability, and SLA is less efficient for large-scale production.
Cost Breakdown of SLS Technology
Material Costs in SLS
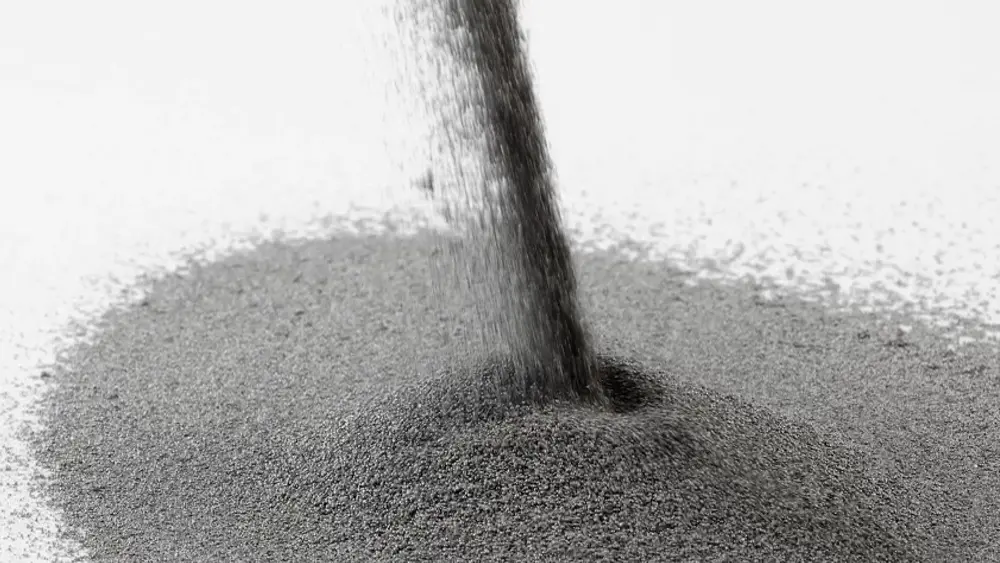
Common SLS materials like nylon (PA12, PA11), glass-filled nylon, TPU, and carbon-filled nylon vary in cost from $60–$200/kg. The high recyclability of unused powder (50%–80%) reduces long-term material costs.
Equipment and Setup Costs for SLS

Desktop SLS printers cost $10,000–$20,000, while industrial ones can exceed $500,000. Their high cost is due to precision technology, large build volume, and advanced software.
Operational Costs of SLS
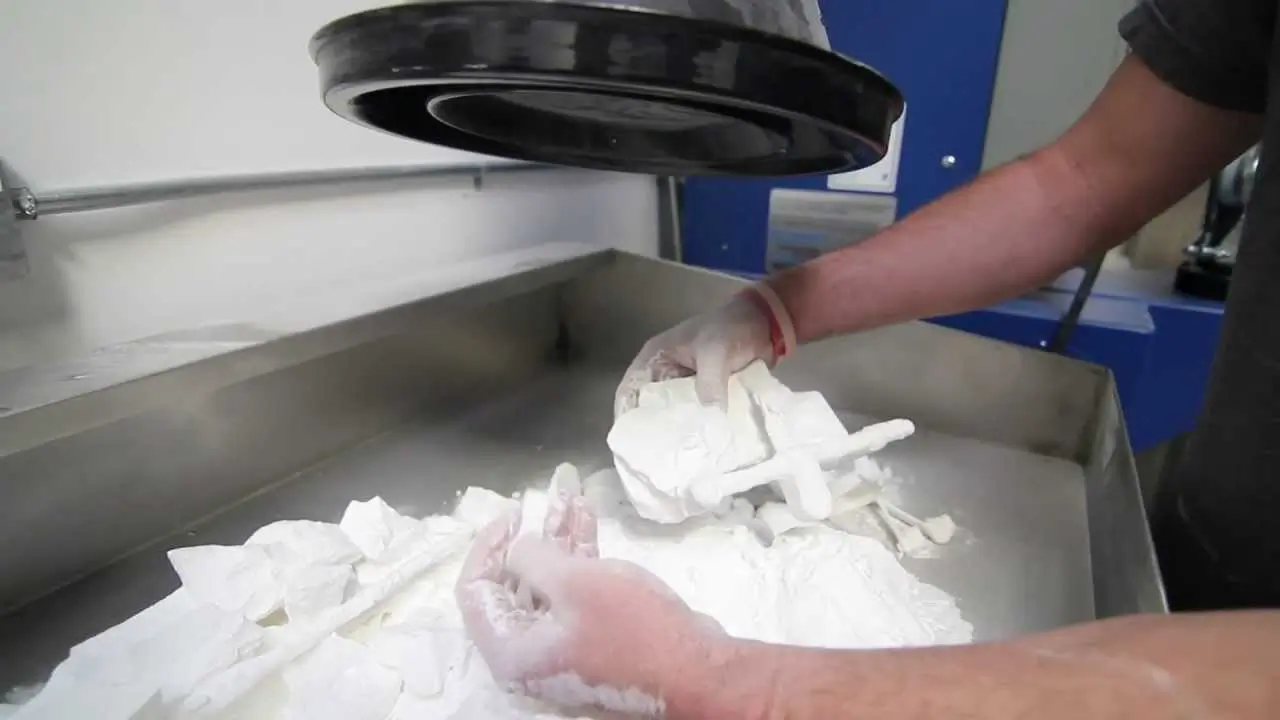
SLS machines consume significant power. Maintenance includes filter replacement and laser servicing. However, the labor efficiency in SLS reduces post-processing labor costs.
Post-Processing Costs for SLS
Post-processing mainly involves powder removal, which has minimal cost and time requirements. Optional surface finishing steps like painting or dyeing may be done for aesthetic or functional purposes.
Cost Efficiency of SLS in Batch Production
In batch production, SLS can print multiple parts simultaneously, reducing the cost per part. For example, an industrial SLS printer with a build chamber for 100 parts may have a cost per part as low as $7 when producing a batch.
Long-Term Cost Considerations
SLS offers advantages like material efficiency, batch production savings, and durable parts. However, the high initial investment and the need for specialized operators and maintenance are potential drawbacks.
Cost Breakdown of Other 3D Printing Methods
FDM (Fused Deposition Modeling)
- Material Costs: Affordable filaments like PLA, ABS, PETG, and TPU range from $20–$60/kg.
- Equipment Costs: Entry-level printers start at $200, mid-level at $500–$2,000, and industrial-grade at $5,000–$10,000+.
- Operating Costs: Low electricity usage and regular maintenance of nozzles and print bed.
- Post-Processing Costs: Can be time-consuming if support removal and advanced finishing are required.
- Cost Efficiency: Suitable for hobbyists and low-budget prototyping. Cost per part varies from $2–$5 for small parts to $20–$40 for large parts.
SLA (Stereolithography)
- Material Costs: Liquid photopolymer resins cost $50–$200 per liter.
- Equipment Costs: Entry-level printers are $500–$1,500, professional ones $2,000–$6,000, and industrial ones over $10,000.
- Operating Costs: Moderate electricity usage and maintenance of resin tanks and light sources.
- Post-Processing Costs: Includes washing, curing, and potentially sanding/polishing, adding significant cost and time.
- Cost Efficiency: Best for high-detail prototypes and small parts. Cost per part ranges from $8–$15 for small parts to $50–$100 for large parts.
MJF (Multi Jet Fusion)
- Material Costs: Similar to SLS, with powders like nylon (PA12, PA11) costing $70–$200/kg and high recyclability.
- Equipment Costs: Industrial printers cost $50,000–$500,000+.
- Operating Costs: High electricity usage and maintenance of printheads and powder recycling systems.
- Post-Processing Costs: Minimal, mainly powder removal with optional coloring.
- Cost Efficiency: Ideal for batch production. Cost per part is $7–$12 for small parts and $40–$80 for large parts.
When Should You Choose SLS Over Other Methods?
Scenarios Where SLS Excels
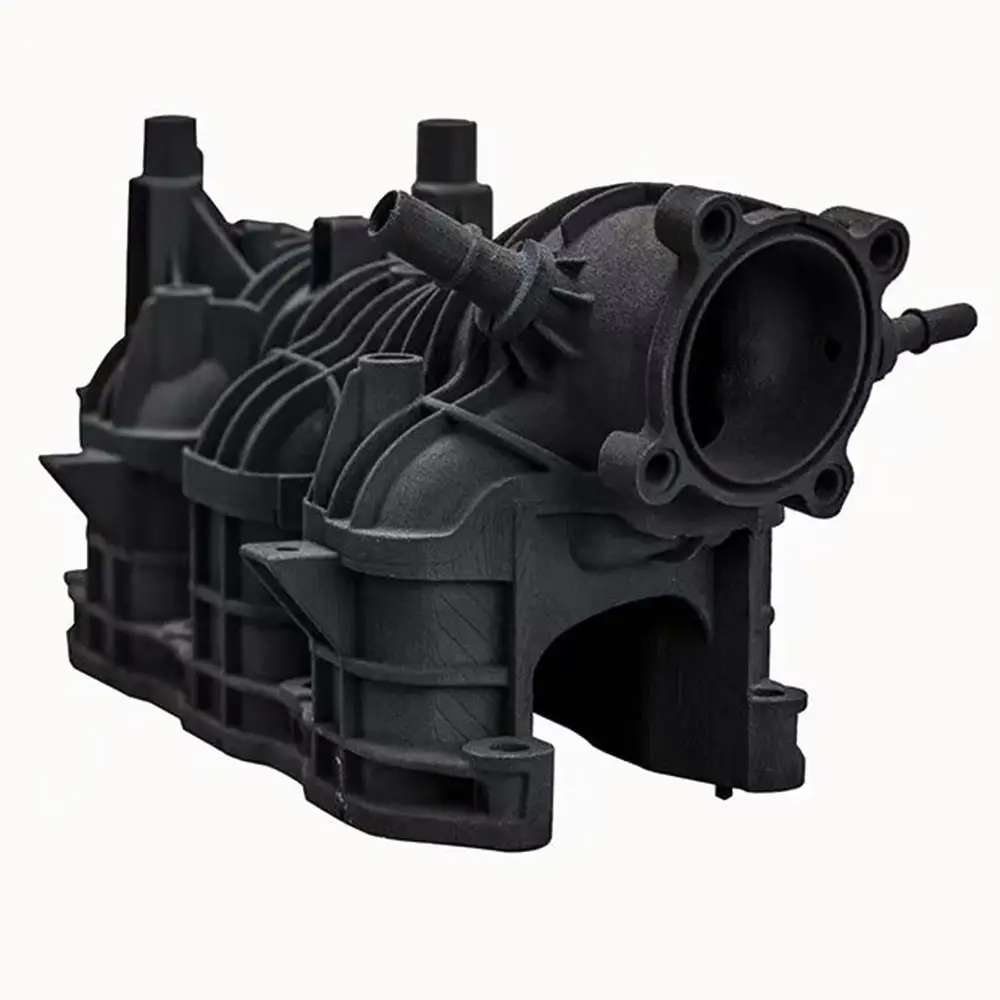
- Complex Geometries: SLS can create intricate designs without support structures, such as lattice structures for aerospace components.
- Durable Prototypes: SLS parts have high mechanical strength and durability, suitable for testing in real-world conditions.
- Small-Batch Production: Efficient batch printing reduces cost per unit for custom or low-volume end-use parts.
- High-Performance Materials: Offers a wide range of materials like reinforced nylons for demanding applications.
Situations Where Other Methods Are Better
- Budget Constraints: FDM is the cheapest option for simple prototypes or non-functional parts.
- Aesthetic Prototypes: SLA is better for parts requiring smooth surfaces and high detail, like jewelry models.
- Highly Detailed Small Parts: SLA or DLP are more suitable for tiny, intricate components.
- Extremely Large or Simple Parts: FDM is cost-effective for very large or simple parts.
Comparing Long-Term Costs: SLS vs Others
Upfront Costs and ROI
SLS has a high upfront cost but can offer significant savings in the long run for businesses producing durable, functional parts or engaging in batch production. The return on investment is strong due to reduced reprints and lower cost per part in batch production.
Material Reuse and Efficiency
SLS has minimal material waste with 50%–80% powder recyclability. In contrast, FDM and SLA generate more waste. Over time, the recyclability of SLS powder offsets its higher initial cost per kilogram.
Labor and Operational Costs
SLS has low labor requirements and is highly automated. Its operational costs are offset by batch production efficiency. FDM is labor-intensive for post-processing, while SLA has high labor and material costs for post-processing.
Scalability and Cost Per Part
SLS and MJF are highly scalable, with the cost per part decreasing significantly as batch size increases. FDM is cheaper for one-off prototypes but becomes less cost-effective for larger batches.
Long-Term Maintenance Costs
SLS requires regular laser calibration and filter replacement. FDM needs frequent nozzle cleaning. SLA requires resin tank cleaning and light source replacement. MJF has high initial maintenance costs but is efficient for scaling.
Real-World Examples and Case Studies
SLS in Key Industries
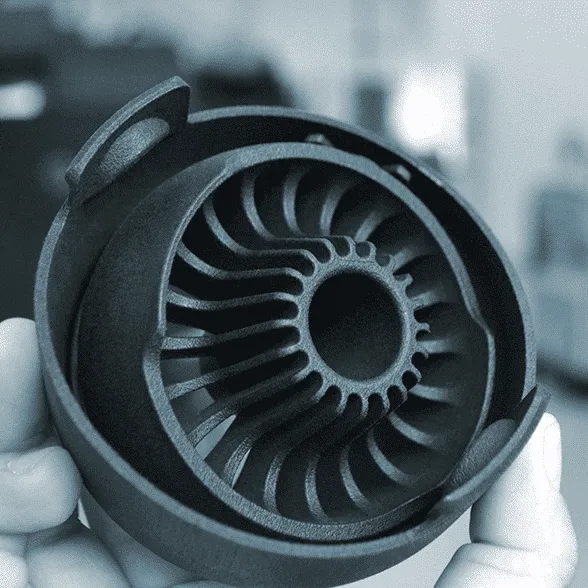

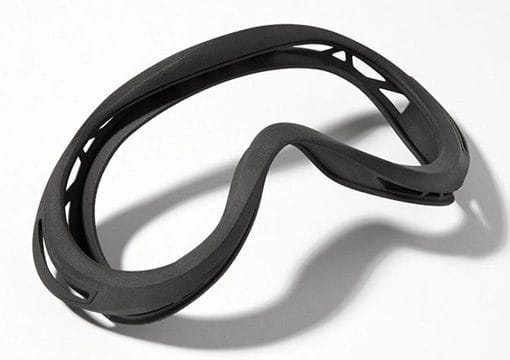
- Aerospace: Used to produce lightweight, durable brackets with complex geometries, reducing weight and improving fuel efficiency.
- Healthcare: Manufactures custom prosthetics that are lightweight, durable, and personalized.
- Consumer Products: Creates custom eyewear frames with high-quality finishes and flexible designs.
- Industrial Manufacturing: Produces functional prototypes like engine components for automotive testing.
When Other Technologies Are Preferred
- SLA for High Aesthetic Needs: Jewelry manufacturers may choose SLA for prototypes with extremely smooth finishes.
- FDM for Low-Cost Prototypes: Startups may opt for FDM for quick, low-budget basic product prototypes.
- MJF for Faster Batch Production: Some companies may select MJF for faster production of small plastic casings.
Cost Impact in Real-World Applications
In various applications, SLS shows cost competitiveness compared to other technologies. For example, in producing lightweight brackets, SLS costs $8–$12 per unit compared to $5–$8 for FDM (less durable) and $15–$20 for SLA (brittle).
Common Misconceptions About SLS and Costs
SLS Is Too Expensive
While SLS has a high upfront cost, it can be more economical in the long term for functional parts, complex designs, and batch production due to material recyclability and reduced cost per part with scale.
SLS Is Only for Large Companies
Desktop SLS printers are now available at lower prices, making SLS accessible to small businesses and even hobbyists. Additionally, the availability of third-party powders has reduced material costs.
SLS Parts Are Overkill
SLS is ideal for functional prototypes, end-use parts, and complex designs where its unique capabilities like creating intricate geometries and durable parts are required.
SLS Materials Are Too Expensive
Although SLS powders are initially more costly than FDM filaments or SLA resins, their high recyclability makes the actual cost per print competitive, especially for batch production.
SLS Is Only for High-Volume Production
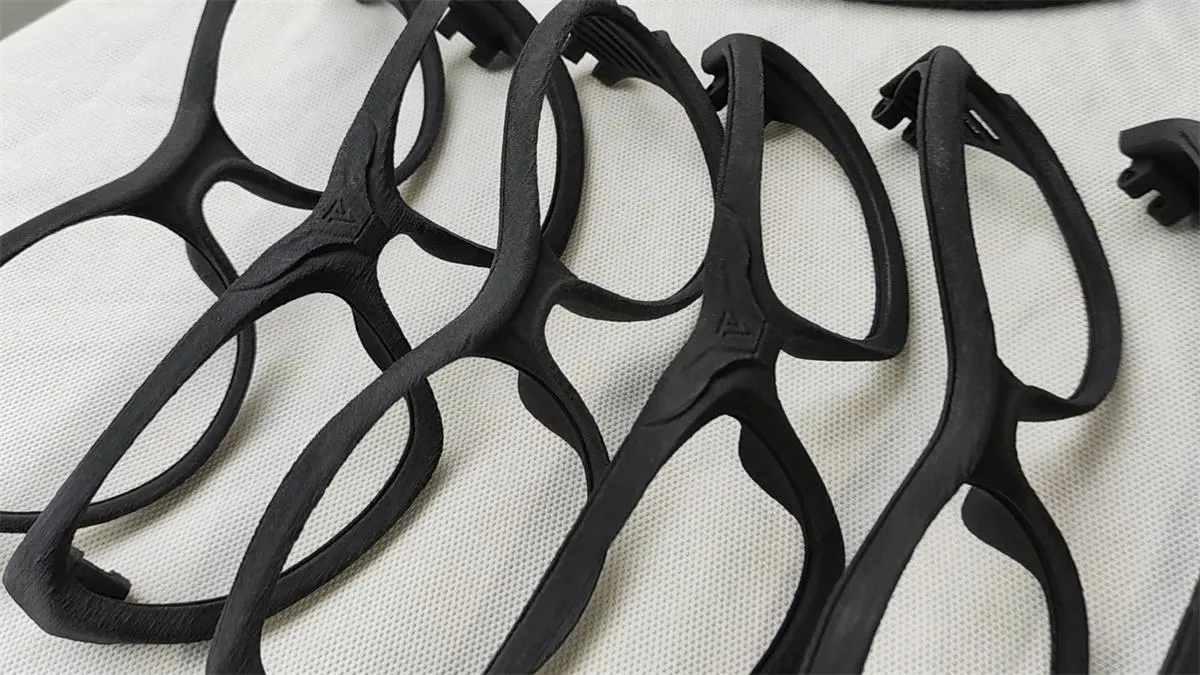
SLS is cost-effective for low-volume and customized production as it eliminates tooling costs and allows batch printing of multiple parts simultaneously.
SLS Requires Too Much Post-Processing
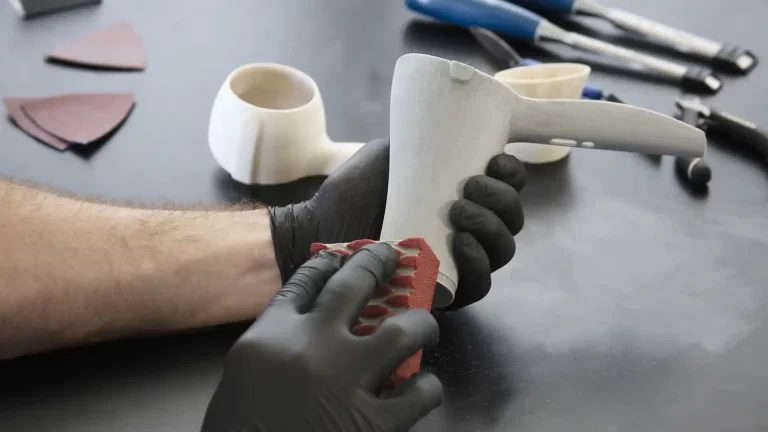
SLS requires less post-processing compared to FDM and SLA as it has no support structures to remove and powder removal is relatively quick and can be automated.
Strategies for Reducing SLS Costs
Optimize Part Design
- Use Lightweight Structures: Replace solid designs with lattice or hollow geometries to reduce material usage and print time.
- Reduce Wall Thickness: Opt for thinner walls where possible without sacrificing mechanical strength.
- Combine Components: Integrate multiple parts into one design to simplify production.
Leverage Efficient Build Packing
- Optimize Build Volume: Arrange parts densely in the build chamber using 3D nesting software.
- Group Similar Parts: Print similar-sized parts together to ensure consistent quality and reduce errors.
Reuse Unused Powder
Understand the powder reusability of SLS materials (50%–80%) and mix reclaimed powder with fresh powder. Invest in high-quality powders for better recyclability.
Select the Right SLS Material
Choose the appropriate material based on the application. For example, nylon PA12 is a versatile and affordable option for general-purpose parts.
Plan for Batch Production
Batch production reduces the cost per part by sharing build costs and increasing material efficiency. Group print jobs into larger batches if possible.
Use External SLS Printing Services
Outsourcing can be a cost-effective alternative, especially when purchasing a printer is not feasible. Compare quotes from different providers.
Minimize Post-Processing Requirements
Reduce surface finishing steps if aesthetics are not critical. Invest in automated powder removal systems for larger operations.
Maintain Your Printer
Regularly replace filters, calibrate the laser system, and clean powder handling systems to prevent costly repairs and ensure print quality.
Compare In-House vs Outsourced Printing
Consider both short-term and long-term costs when deciding between in-house and outsourced SLS printing. In-house is better for frequent or large-scale production, while outsourcing is suitable for occasional use.
Future Trends in SLS and Cost Reduction
Advances in SLS Materials
- Lower-Cost Powders: Manufacturers are developing more affordable powders, like nylon PA12, reducing material expenses.
- Expanded Material Options: New materials like biodegradable powders and conductive materials are being developed, expanding applications.
- Improved Recyclability: Efforts to increase powder reuse rates will further reduce waste and costs.
Smaller and More Affordable SLS Printers
- Desktop SLS Printers: Compact and affordable desktop printers are becoming available, lowering the entry barrier.
- Modular and Open-Source Hardware: Open-source and modular printers allow customization and gradual scaling of operations.
Faster Printing Speeds
- Multi-Laser Systems: New printers with multiple lasers can significantly reduce print times.
- Enhanced Powder Spreading: Advances in powder distribution systems improve layering speed and precision.
Automation in Post-Processing
- Automated Powder Removal: Automated systems are becoming common, reducing labor costs.
- Streamlined Finishing Processes: New equipment simplifies tasks like smoothing and dyeing.
AI-Driven Design and Workflow Optimization
- AI for Design Optimization: Software can generate lightweight, material-efficient designs.
- Predictive Maintenance and Quality Control: AI helps monitor print quality and predict maintenance needs.
Sustainability as a Cost-Reduction Driver
- Energy-Efficient Printers: Printers with improved energy efficiency reduce operating costs.
- Powder Recycling Programs: Recycling used powder can save costs.
Integration with Other Technologies
- Hybrid Manufacturing: Combining SLS with other manufacturing methods like CNC machining expands capabilities.
- Digital Twins and IoTConnectivity: IoT-enabled printers can simulate and optimize production processes.
In conclusion, SLS is a powerful 3D printing technology with unique advantages in creating durable and complex parts. Despite the initial perception of high costs, various strategies and future trends indicate that its cost can be effectively reduced. As the technology continues to evolve, SLS is expected to become more accessible and widely used across different industries. By understanding its capabilities, costs, and potential for improvement, businesses and individuals can make more informed decisions when choosing 3D printing technologies for their specific needs.