Welcome to a comprehensive guide that demystifies the complex realm of SLS 3D printing. As you journey through this insightful article, prepare to uncover the intricate layers masking the art and science of this innovative technology. You’ll whimsically traverse through the very essence of SLS 3D printing—beginning with its fundamentals, meandering through its beneficial applications, and landing at predictions for its exciting future trajectory.
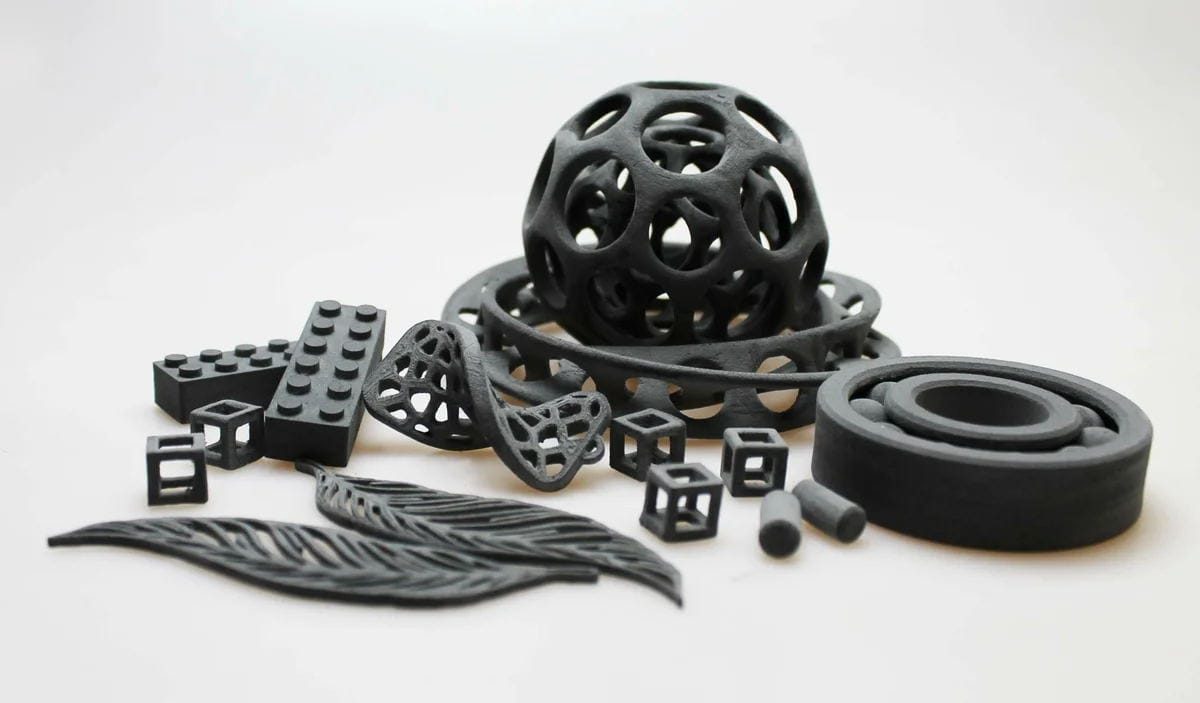
Above all, our goal is clear—we’re here to get you fully initiated into the world of SLS 3D Printing. By the end of this riveting exploration, you’ll not only be well-versed with the ins and outs of SLS 3D printing, but also be armed with the knowledge to leverage this cutting-edge technology to its fullest potential in your unique context.
Whether you’re a seasoned 3D printing enthusiast aiming to delve deeper into advanced processes, or an inquisitive beginner seeking to unravel the fascinating domain of additive manufacturing—there’s truly something to glean for everyone.
What is SLS 3D Printing?”
Imagine yourself sculpting a statue, but instead of chipping away at marble to reveal your masterpiece, you’re building it up layer by layer, gradually shaping your creation bit by bit. That’s the art of 3D printing. But let’s go further, imagine you’re using a high-power laser to fuse small particles of polymer powder together to shape each layer of your model. This, my reader, is Selective Laser Sintering (SLS).
The ABCs of SLS
SLS is a cutting-edge 3D printing or additive manufacturing process that uses a laser to sinter powdered material, binding it together to create a solid structure. Born from a 1980s’ invention by Carl Deckard, an undergrad at the University of Texas, SLS has now been adopted in a variety industries ranging from aerospace to fashion, proving its unrivaled versatility and flexibility.
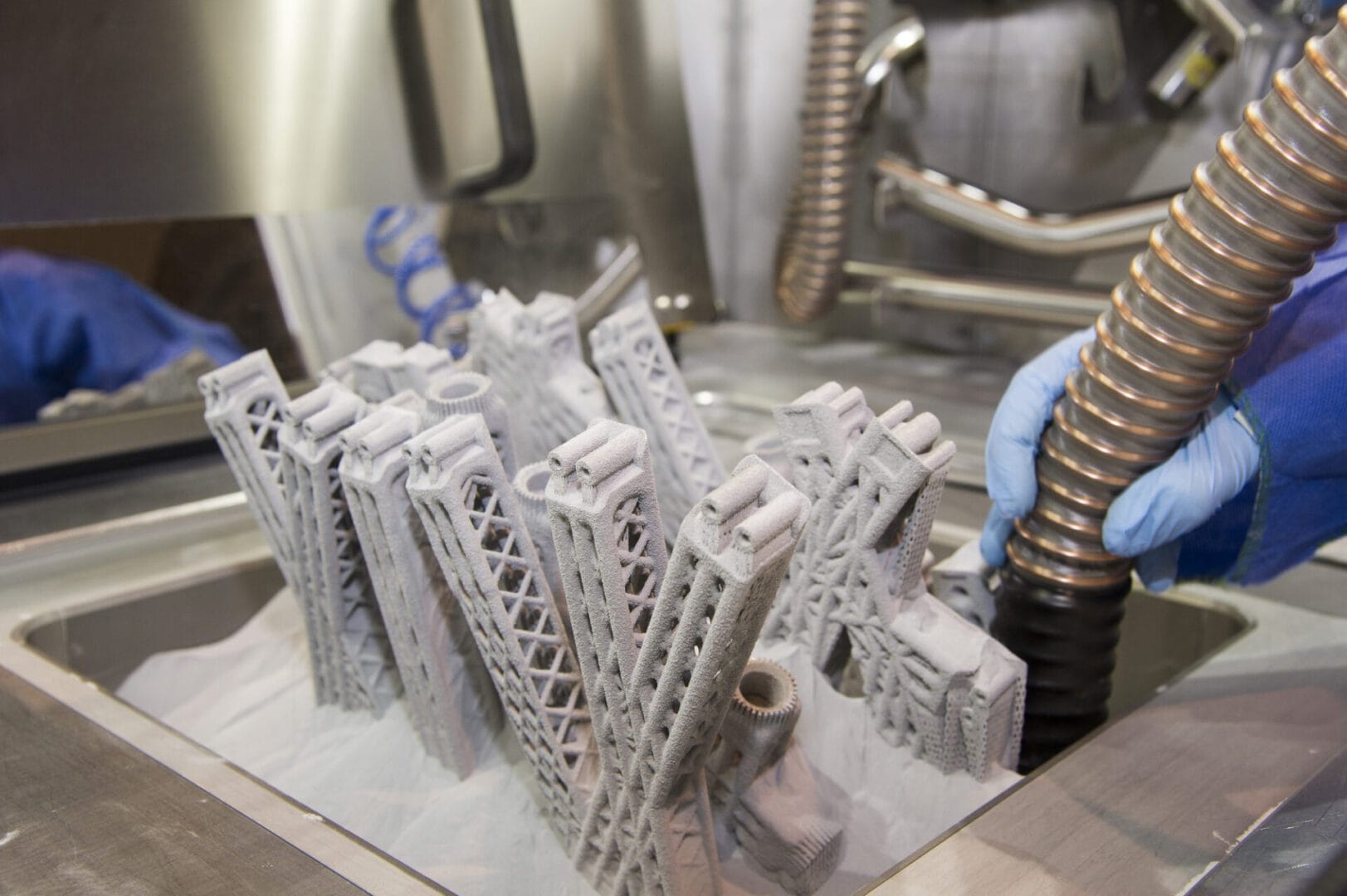
What sets SLS apart from other 3D printing techniques like FDM (Fused Deposition Modeling) or SLA (Stereolithography)? No need for support structures! As your object comes to life, unsintered powder surrounds each completed layer, holding your design in place. This distinctive characteristic makes SLS a preferred choice when printing designs of high complexity.
Now let’s break it down into a step-by-step process:
- Layer Application: A thin layer of printing material (usually nylon or polyamide) is applied onto the build platform.
- Laser Sintering: The printer’s laser selectively fuses the powder according to the 3D model’s cross-sectional geometry.
- Platform Lowering: Once a layer is complete, the build platform lowers, and a fresh layer of powder is applied.
- Repeat: The laser sintering process repeats, building successive layers until your entire 3D object is complete.
- Cool Down: After the printing is finished, the object needs to cool down before it can be removed.
- Post-Processing: The unsintered powder is brushed off, revealing the finished product, ready for any necessary finishing touches.
Fun Fact: The term ‘sintering’ originates from the world of ceramics, where it describes the process of making objects from powdery material by heating it until the particles stick together!
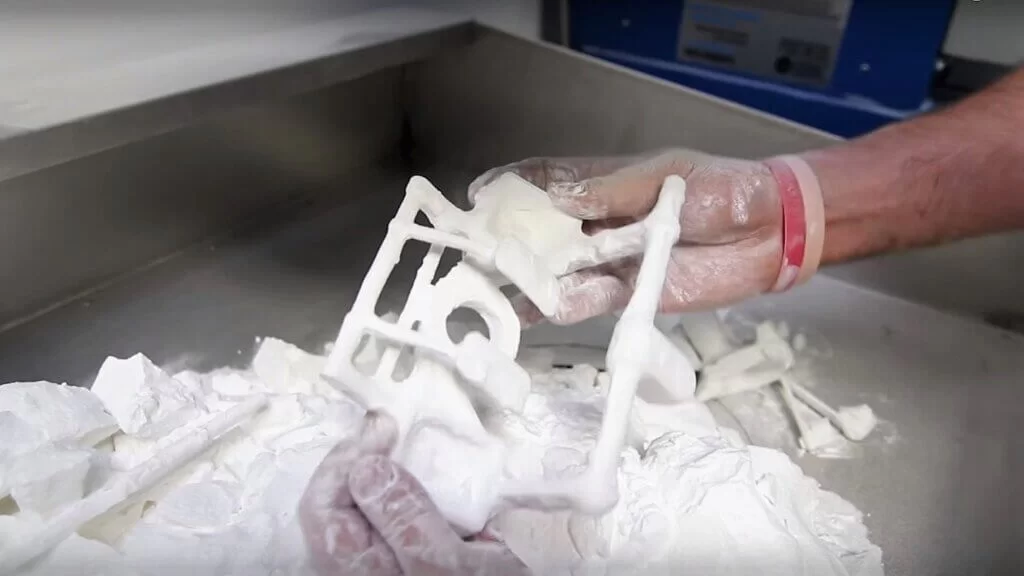
Types of SLS 3D Printers
Desktop SLS 3D Printers
Desktop SLS 3D printers ushered in the democratization of 3D Printing. Bridging the gap between the hobbyist and professional world, these compact powerhouses are pushing boundaries from your tabletop. Here are few standout models to consider:
This user-friendly printer can handle both small and large prints, perfect for entrepreneurs and educational institutions.
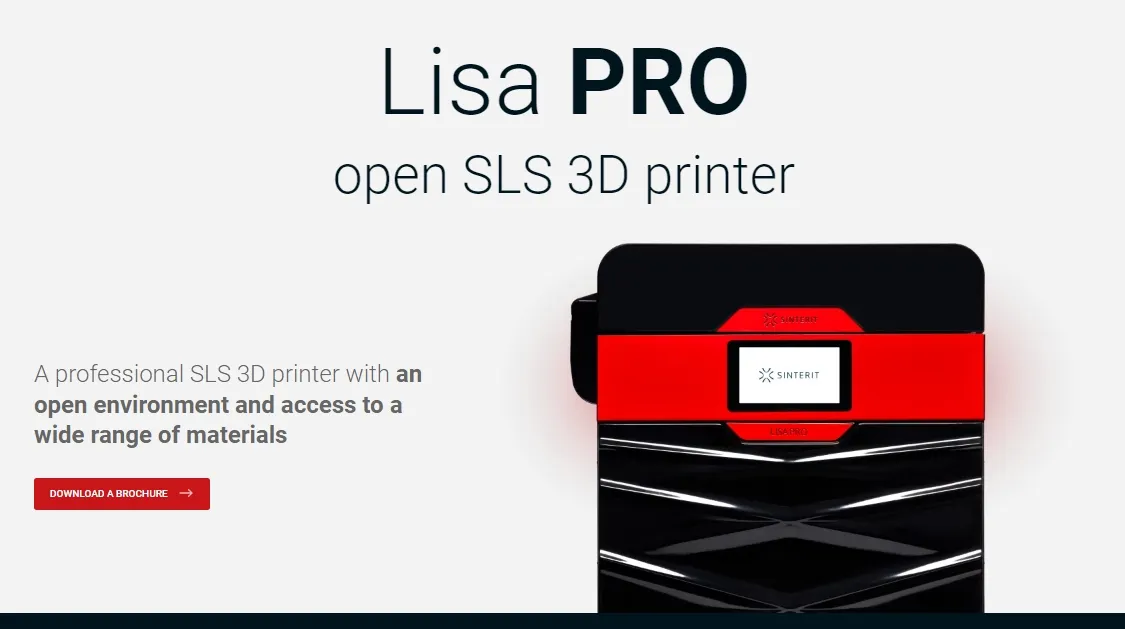
Brought by the pioneers of desktop SLA, Fuse 1 is designed for versatile applications with its wide range of printable materials.
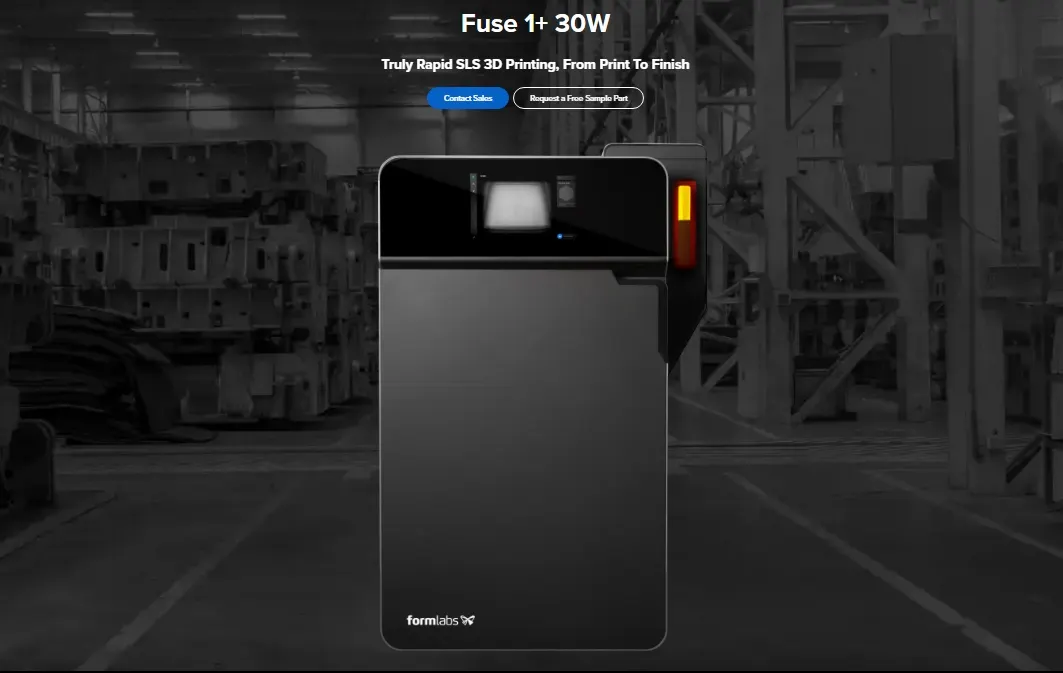
If you’re interested in getting hands-on with SLS technology, this do-it-yourself kit might be just right for you.
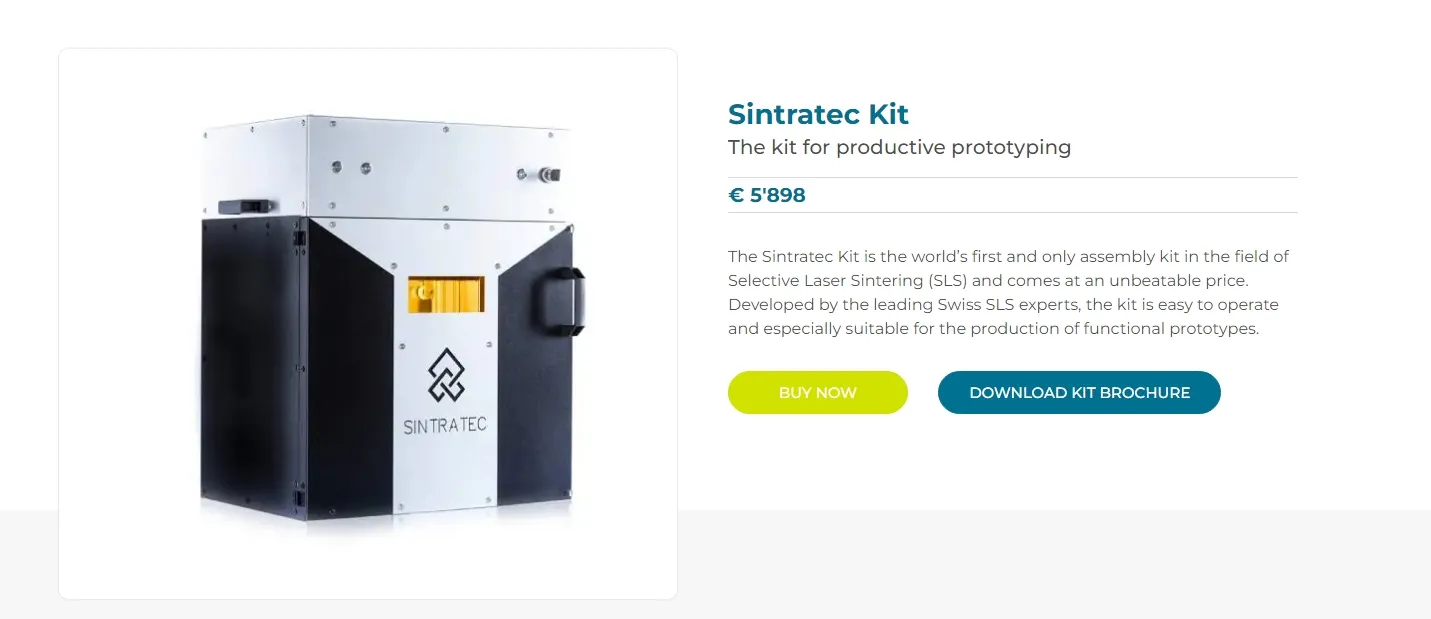
Industrial SLS 3D Printers
Industrial SLS 3D printers are the workhorses of additive manufacturing, known for their impressive build volumes, high-speed production, and exceptional part quality. Notable players in the industry include:
A cost-effective entry-level model favored for its precision and reproducibility.
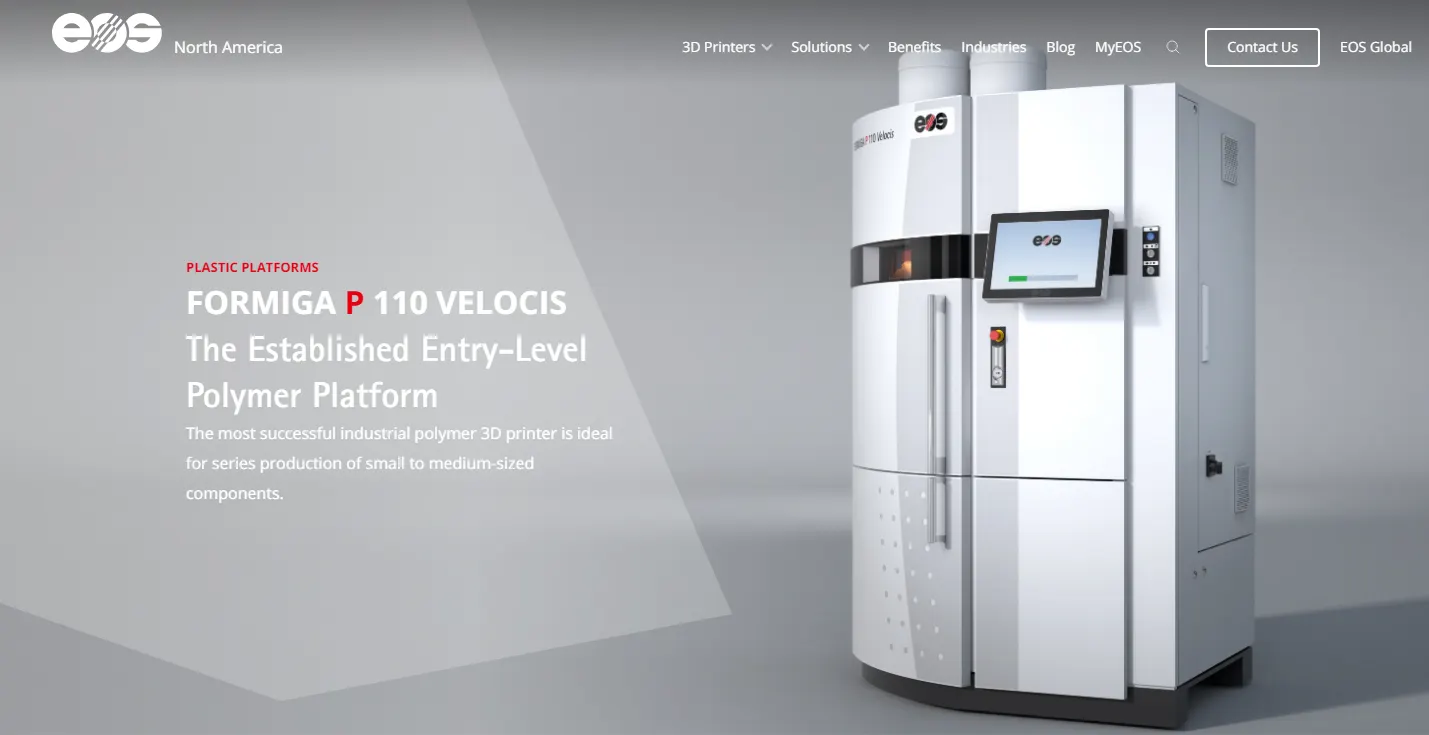
This robust machine excels in producing durable, heat-resistant parts, ideal for aerospace and automotive industries.
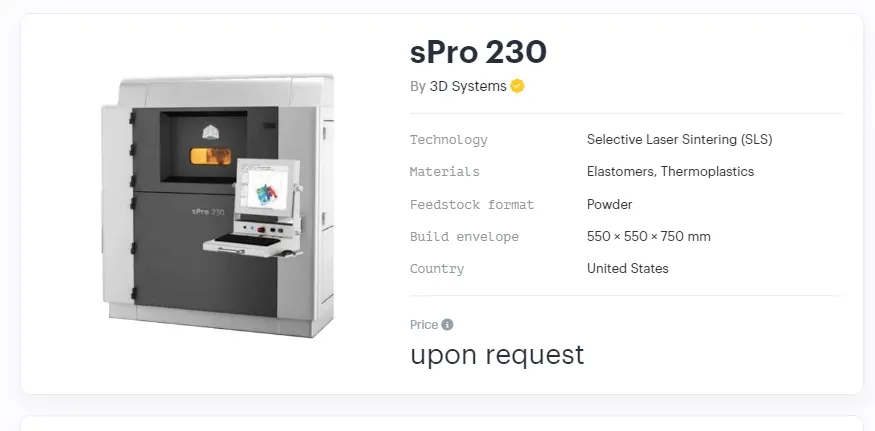
Specifically designed for metal applications, the Farsoon FS422M offers high flexibility and user safety.
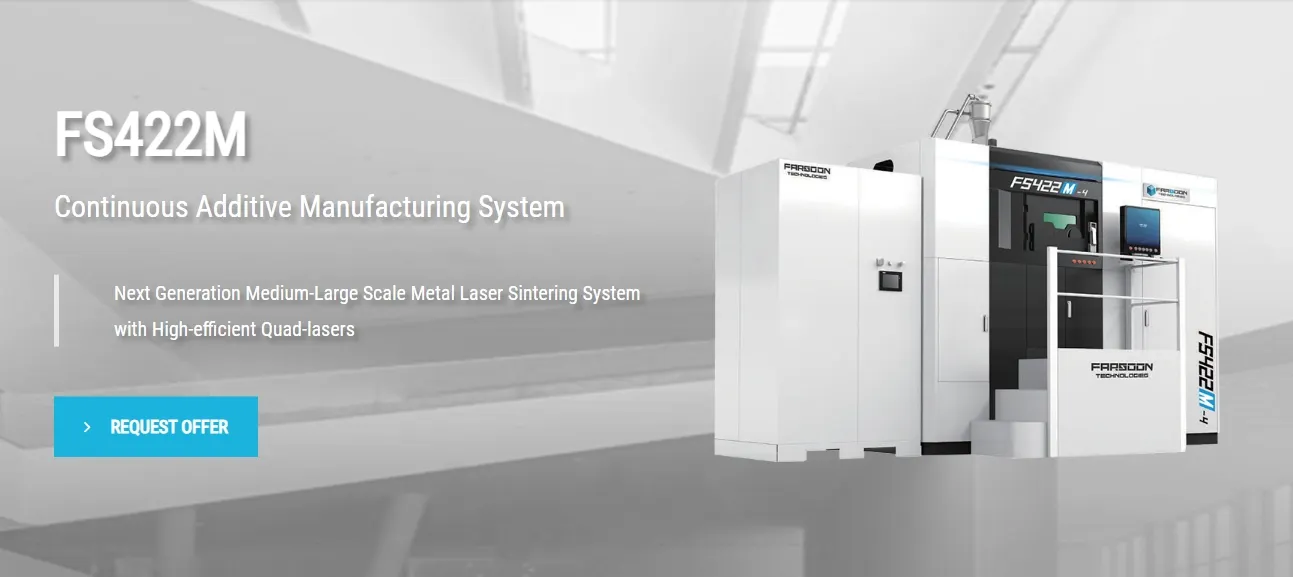
For the best solutions tailored from industrial manufacturing to commercial applications, ultimate performance and outstanding stability are also solutions worth considering.
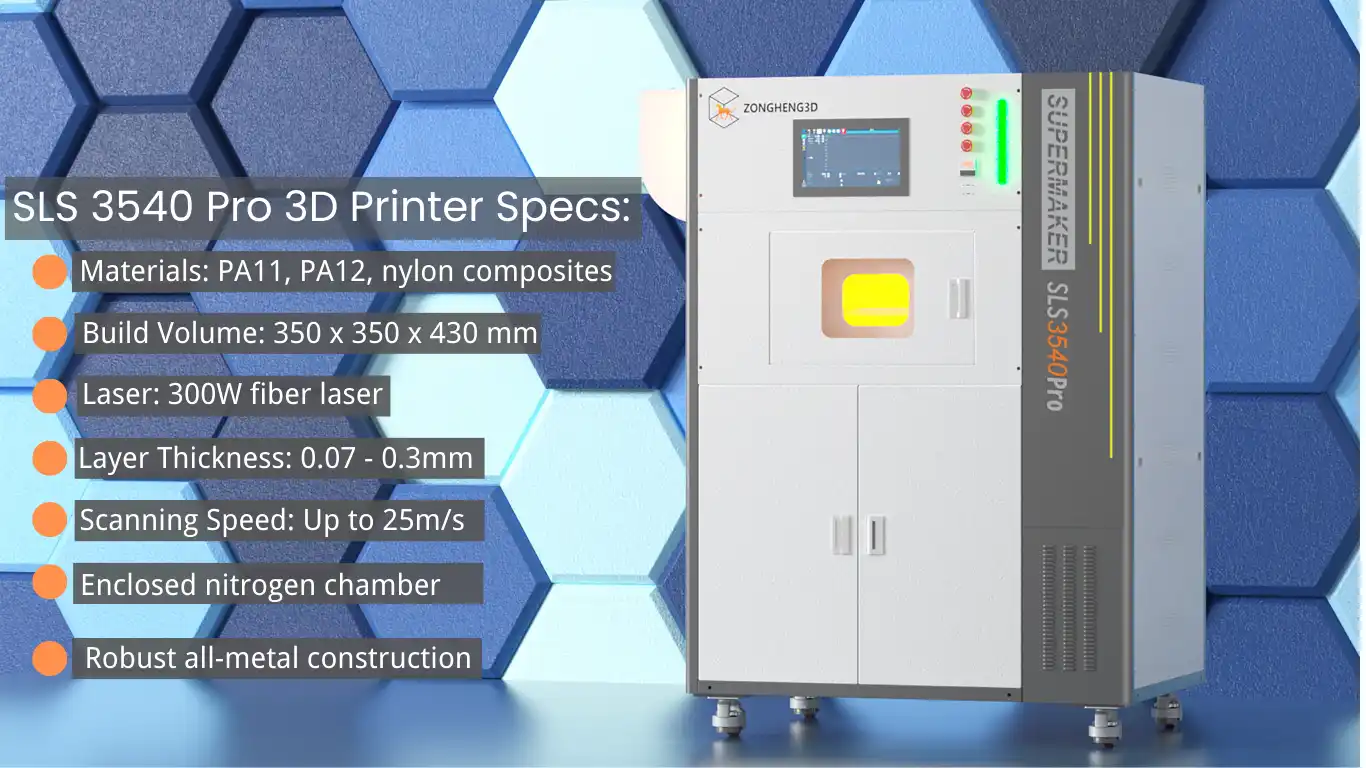
Pros and Cons
Industrial SLS Printers
Renowned for their high precision and vast material compatibility, industrial SLS printers are the juggernauts of the SLS world. They offer incredible accuracy, large build volumes, and high-quality finishes, making them an ideal choice for professional applications.
Pros
- High-quality prints
- Large build volume
- Broad material compatibility
Cons
- Expensive
- Requires trained personnel
- Significant operational and maintenance needs
Desktop SLS Printers
Brought into prominence by the rise of compact, affordable technology, desktop SLS printers have revolutionized the accessibility of SLS technology. Though they may lack the build volume and material versatility of their industrial counterparts, desktop printers like the Sinterit Lisa Pro and Formlabs Fuse 1 punches way above its weight in delivering quality prints.
Pros
- More affordable
- Compact and user-friendly
- Lower maintenance
Cons
- Limited build volume
- Limited material options
- Might not offer the same print quality as industrial printers
Materials in SLS 3D Printing: Know Your Medium
In the captivating realm of 3D printing, it’s not only about the technique or the equipment. An essential piece of the puzzle lies in the printing material or the medium. Just like a sculptor, to mold your masterpiece in Selective Laser Sintering (SLS) 3D printing, it’s paramount to understand and choose your material wisely.
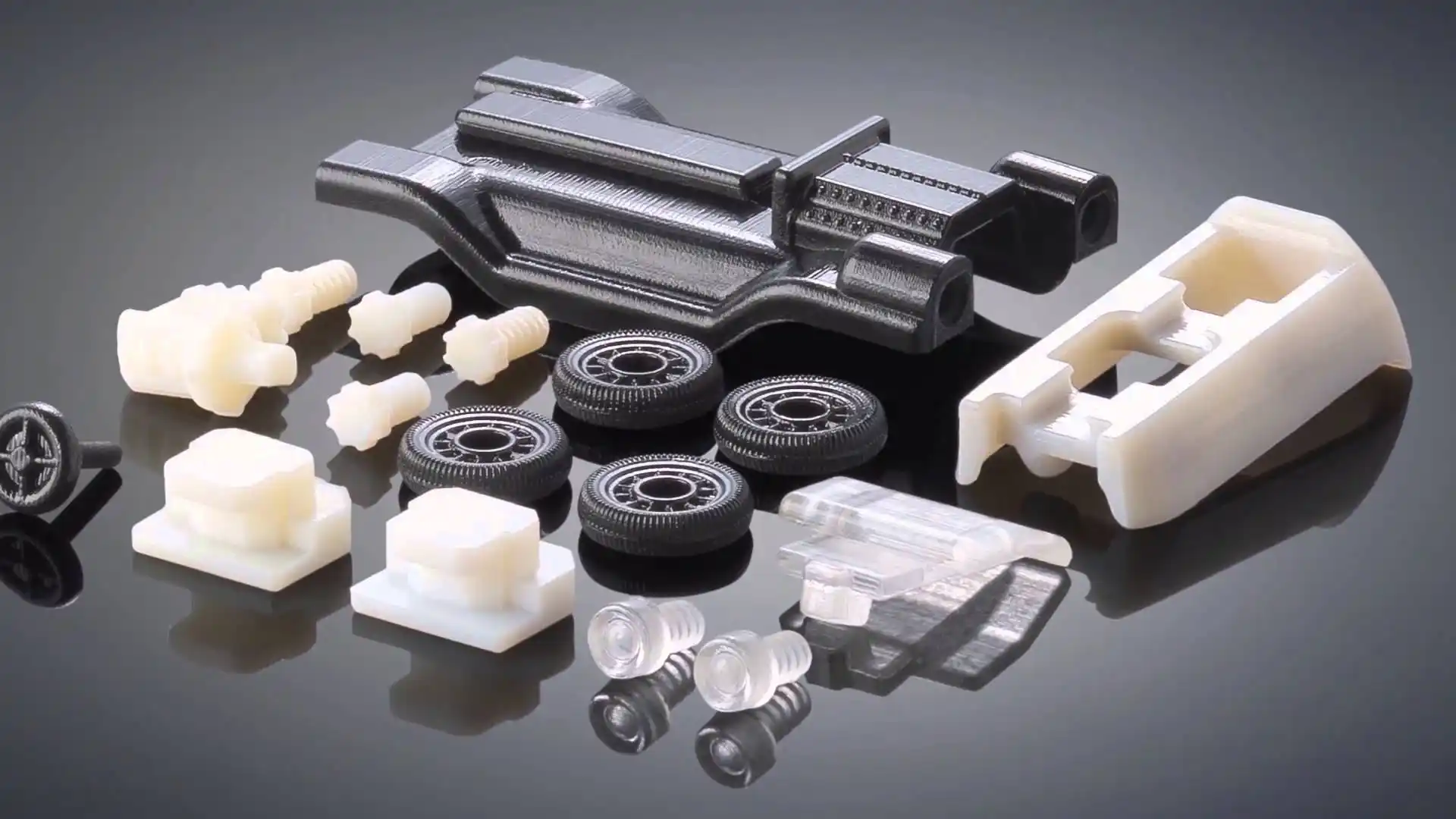
SLS technology is revered for its material versatility. This powder-based technology is compatible with a wide range of materials from plastic, ceramic, to even metal. Each of these materials brings unique properties to your 3D printed part. Let’s explore the most commonly used materials in SLS 3D Printing.
Nylon (Polyamide)
Arguably the most popular choice, Nylon, particularly PA 11 and PA 12, is durable, flexible, and resistant to many chemicals and high temperatures. It’s exceptional for making functional parts and prototypes.
- PA 12 (Nylon 12) With its excellent material properties, such as low weight, high strength, and superior durability, it’s no wonder PA 12 is the favorite child of the SLS world.
- PA 11 (Nylon 11) Jealously holding up to its cousin PA 12, PA 11 provides even better flexibility and impact resistance, prominently used for snap fit assemblies and living hinges.
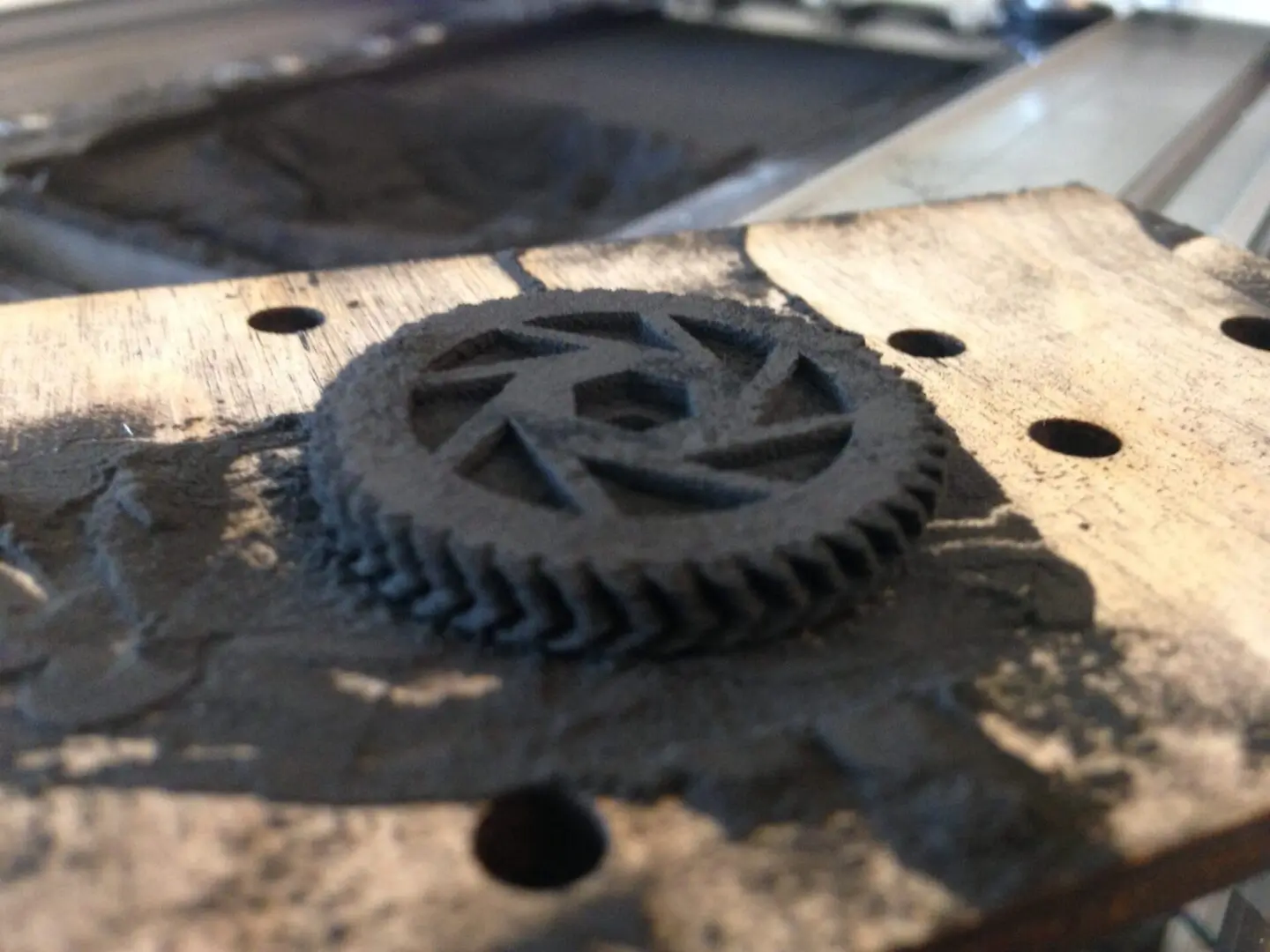
Key Applications:
- Functional prototypes and end parts
- Mechanical parts
- Automotive components
Glass-Filled Nylon
A blend of nylon and glass offer increased rigidity and thermal resistance, although this does compromise the flexibility somewhat. It’s excellent for mechanical parts that require high rigidity or temperature resistance.
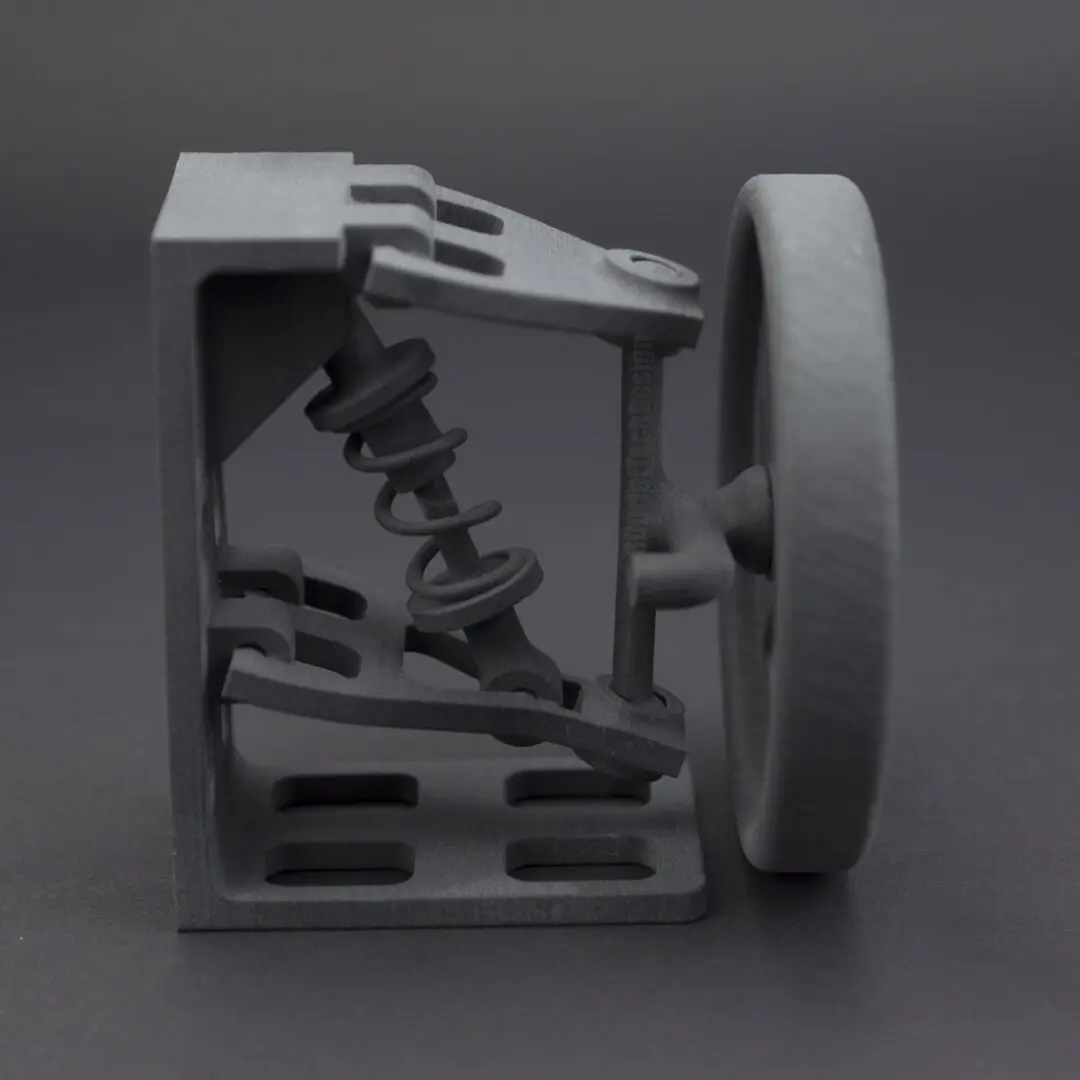
- PA GF (Glass-Filled Nylon) Ever needed the strength of a superhero in your parts? PA GF achieves precisely that by combining Nylon with small glass particles, resulting in improved rigidity and thermal resistance.
Key Applications:
- Aerospace components
- Industrial machinery
- High precision tools
Alumide
This is a blend of nylon and aluminum powder, creating parts with a metallic visual effect, and slightly higher stiffness and thermal resistance than standard nylon.
Key Applications:
- Decorative models
- Experimental design pieces
- Parts requiring metallic aesthetic without actual metal strength
(TPU)Thermoplastic Polyurethane
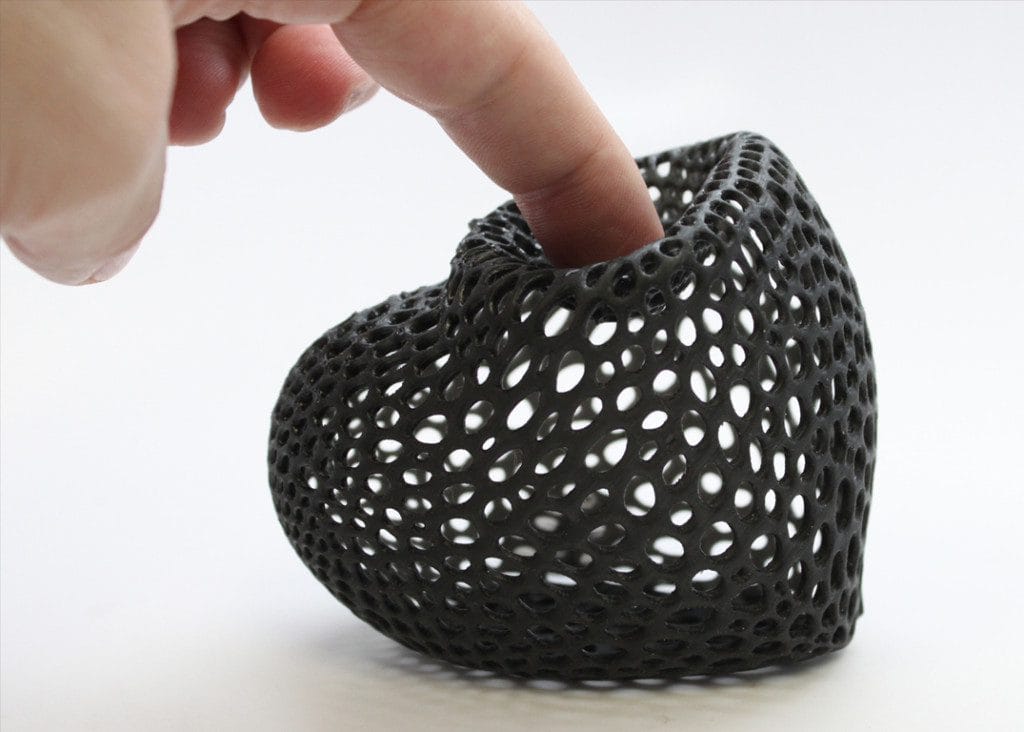
TPUis a rubber-like material that’s flexible and stretchable while also boasting the benefits of durability and strength. Ideal for prototypes and parts that require high elasticity.
Key Applications:
- Flexible and elastic prototypes
- Seals and gaskets
- Wearable items
Metals
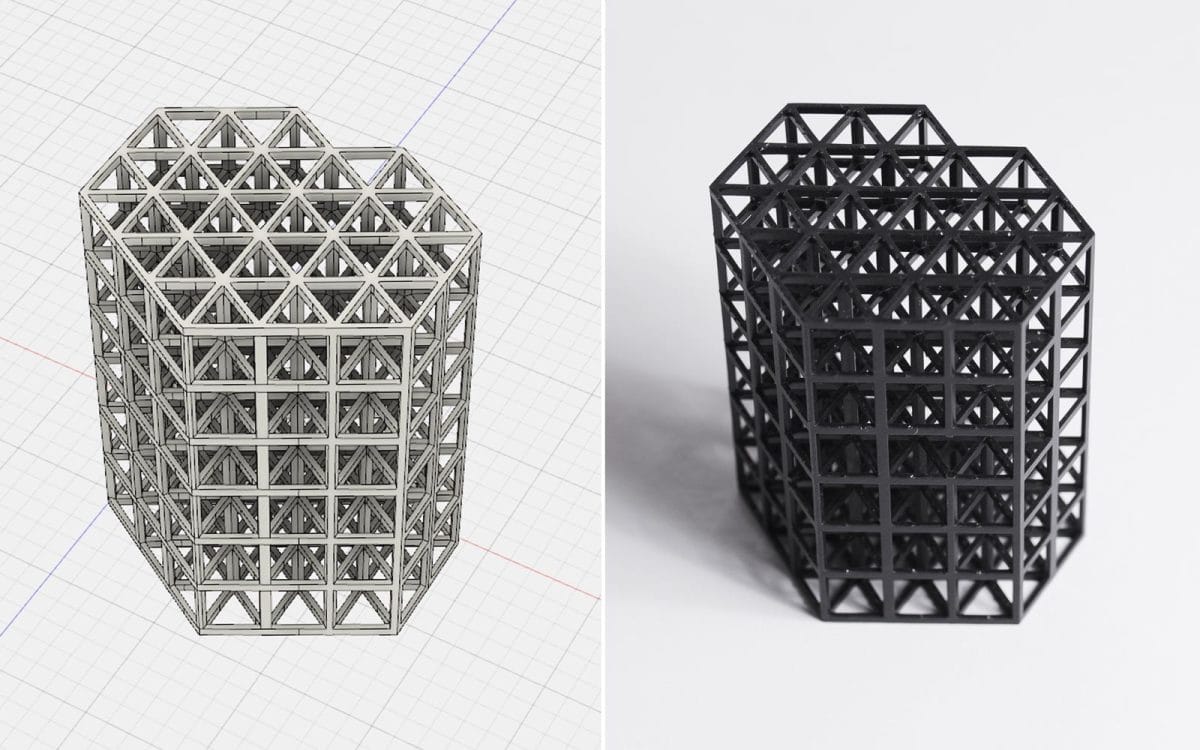
Though not as common as in Direct Metal Laser Sintering (DMLS), some SLS printers also work with metal powders like stainless steel, and titanium, creating robust, high-strength parts.
Key Applications:
- High-strength mechanical components
- Aerospace-parts
- Advanced prototypes
Choosing the right material for your SLS print can make or break the efficiency and purpose of your final part. Carefully consider the mechanical and visual properties needed for your design.
Exploring the SLS 3D Printing Process: Every Detail Matters
3D printing is not just a technology. It narrates a story of transformation — from a digital file into a tangible object. This mesmerizing journey led by Selective Laser Sintering (SLS) technology is packed with exactitude, understanding of materials, and mastery of the process.
1.Creating a 3D Model
The inception of any 3D-printed object is in its digital design. This blueprint is predominantly formed using CAD (Computer-Aided Design) software, focusing on the immense level of detail and precision required for the final output.
2.Converting CAD to STL
Once the 3D design is finalized, it’s converted into an STL (STereoLithography) file format – the standard for all 3D printing technologies, breaking down the design into layers ready for printing.
3.Preprocess Printing
The STL file is sent to the SLS printer, where the system warms up to the optimal temperature just below the melting point of the material’s powder form, ensuring it is adequately sintered when lasers pass over it.
4.Printing Process
In its heart, lays a high-power laser, capable of sintering (fusing) the powder layer by layer according to the design. As each layer is completed, the build platform lowers, and a fresh layer of powder is evenly spread across the surface, ready for the next round of sintering.
5.Cooling and Powder Removal
After the printing process, patience is key. The finished part must cool down before the excess powder is removed. This cooling process is crucial, as rapid temperature changes could result in deformations or cracks in the part.
6.Post-Processing
The last stage in our journey, post-processing, involves the removal of any unsintered powder, smoothing out the surface, and if required, coloring or varnishing for the final finish.
Conclusion: The Future of SLS in Polymer Parts Manufacturing
Despite the challenges, Selective Laser Sintering (SLS) technology has already proven its potential in shaping the future of polymer parts manufacturing. Expanding on its real-world applications, let’s envisage the future path of SLS.
Sustainability Efforts
As sustainability becomes a pressing concern, SLS technology may very well be a part of the solution. With its ability to virtually eliminate waste by reusing unsintered powder, SLS stands as an eco-friendly 3D printing alternative.
Material Innovations
The constant advancements in material science could lead to a broadened array of materials suitable for SLS. This expansion of material options will further widen the scope of its applications.
Advancements in Efficiency
Ongoing research and technological enhancements are progressively making SLS machines more energy-efficient and thereby more cost-effective. This paves the way for SLS to becoming a standard in various industries.
Diverse Applications
As more industries recognize the potential of SLS, its adoption rate is bound to surge. From automotive to aerospace, and healthcare to fashion, the use of SLS in creating intricate and durable components is bound to become a norm.