Both DLP and LCD 3D printing have paved their own paths into the 3D printing hemisphere, each with unique features, capabilities, and intricacies. Whether you’re a novice curious about this illuminating field, an experienced 3D artist looking to harness new techniques, or a professional aiming for optimization, understanding the key differences and applications of DLP and LCD is crucial.
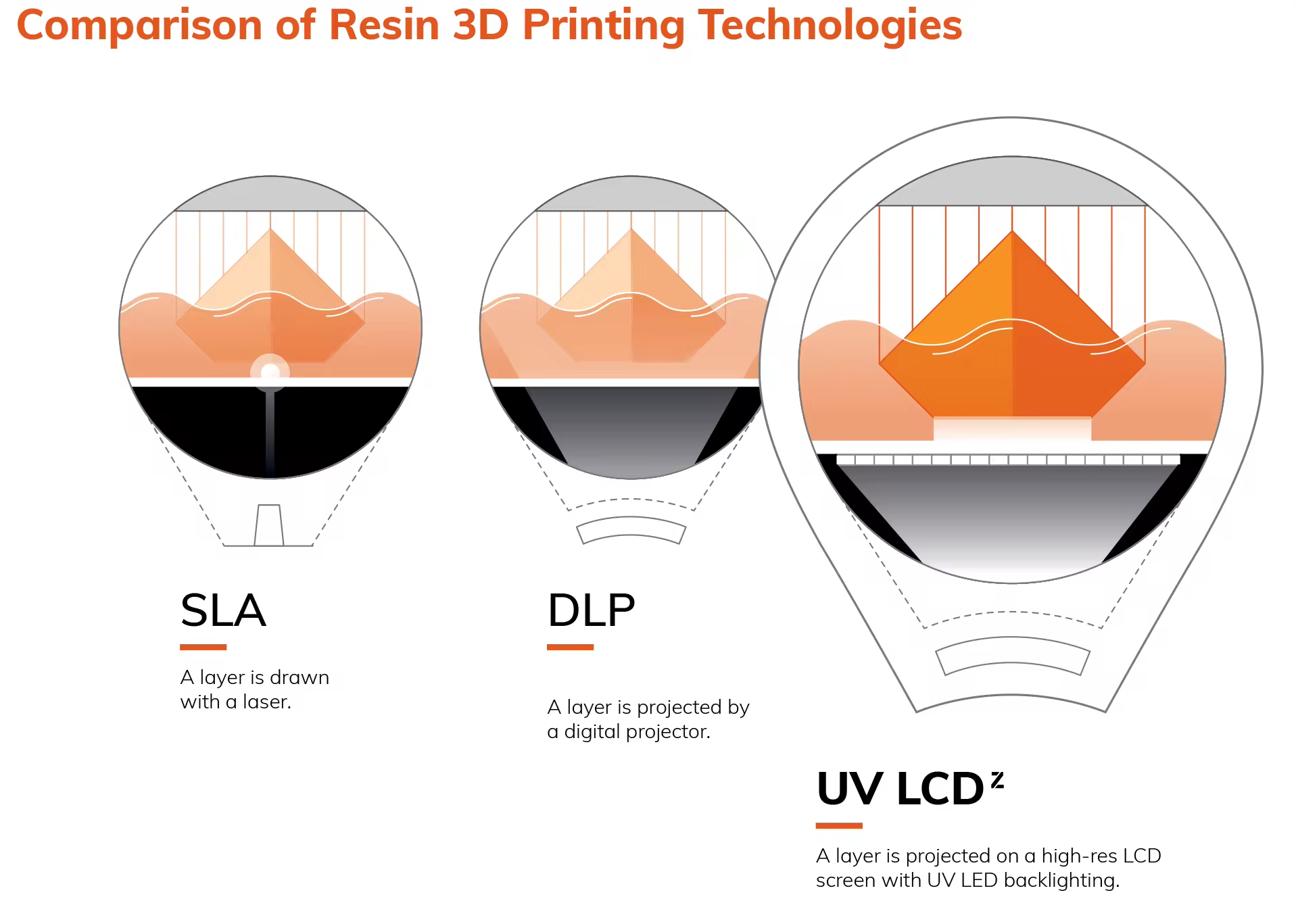
As we delve deeper into the strengths, weaknesses, and idiosyncrasies of these two technologies, we’ll equip you with the necessary knowledge to illuminate your 3D printing journey. So whether you’re choosing a 3D printing method for your next project or simply exploring the fascinating landscape of technological evolution – this comprehensive guide will brighten your understanding of DLP and LCD 3D printing. Let’s step into the light, and embark on this enlightening journey together.
The History of 3D Printing: DLP and LCD
As we turn the pages back, we delve into the fascinating history of our two guiding lights – DLP and LCD. Understanding the genesis, evolution of, and influencers behind these technologies provide valuable insights into their capabilities and where they’re headed.
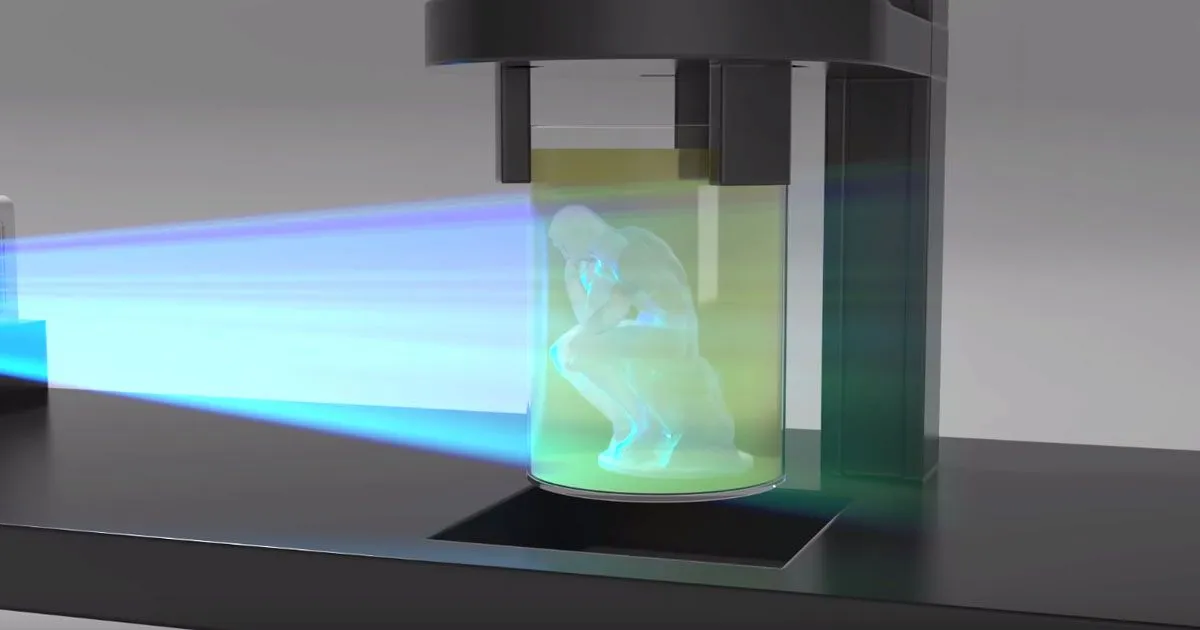
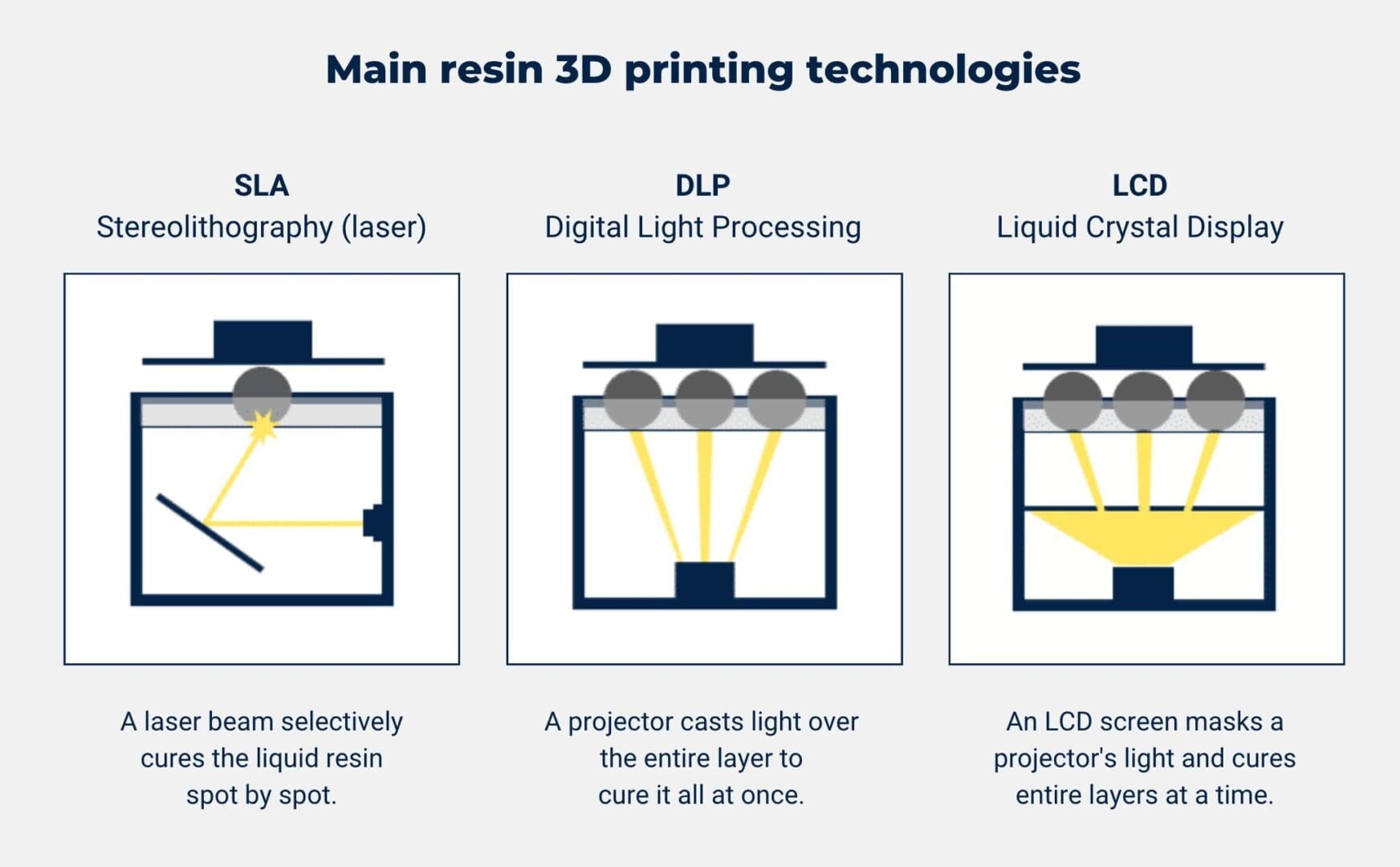
A. DLP – The Magic of Mirrors
Born out of a laboratory experiment at Texas Instruments in 1987, Digital Light Processing, more popularly known as DLP, has evolved from a simple idea to a revolutionary 3D printing technology. Larry Hornbeck, the inventor of the DMD (Digital Micromirror Device), kindled the first spark of this powerful technology. By bouncing light off strategically-arranged microscopic mirrors, Hornbeck created the foundation for DLP.
DLP 3D printing made its commercial debut in the early 2000s. The DLP technology provided a plethora of benefits, including precision, speed, and efficient use of materials. Over the years, the technology has continuously refined and expanded its scope, with applications ranging from dental prosthetics to jewelry creation to architecture.
B. LCD – Lighting the Pixel Pathway
With roots in the television and monitor industry, LCD 3D printing technology leverages the power of liquid crystals to manipulate light. Contrary to the projection method in DLP, LCD utilizes photomasks for each layer, harnessing UV light to harden the resin precisely.
LCD 3D printing, particularly the subtype called MSLA (Masked Stereolithography), climbed the popularity ladder quickly due to its cost-efficiency and simplicity. Moreover, it is an extraordinarily scalable technology, allowing both smaller desktop models and larger industrial-sized printers.
With the constant evolution of LCD technology, it continues to be a strong contender in the world of resin 3D printing.
A Side-by-Side Timeline:
Year | DLP | LCD |
1987 | Inception of DLP through Larry Hornbeck’s invention of the Digital Micromirror Device at Texas Instruments. | – |
Early 2000s | DLP makes its foray into the commercial world of 3D printing. | – |
Late 2000s | – | LCD technology begins to be adapted for 3D printing. |
Early 2010s | DLP technology expands and refines for various applications. | LCD (especially MSLA) gains ground due to scalability and affordability. |
Today | Various applications from dental prosthetics to jewelry making. | Commonly used in both desktop and industrial 3D printing. |
As we voyage through the intricate landscape of DLP and LCD technologies’ history, we set the stage for a closer look at their functionality, advantages, and challenges.
A Closer Look at DLP 3D Printing
As we leap from our historical overview, we now land on the integral mechanics and application of Digital Light Processing (DLP) in 3D printing, a phenomenon whose roots are deeply entangled with light and mirrors.
- DLP – The Science and The Process
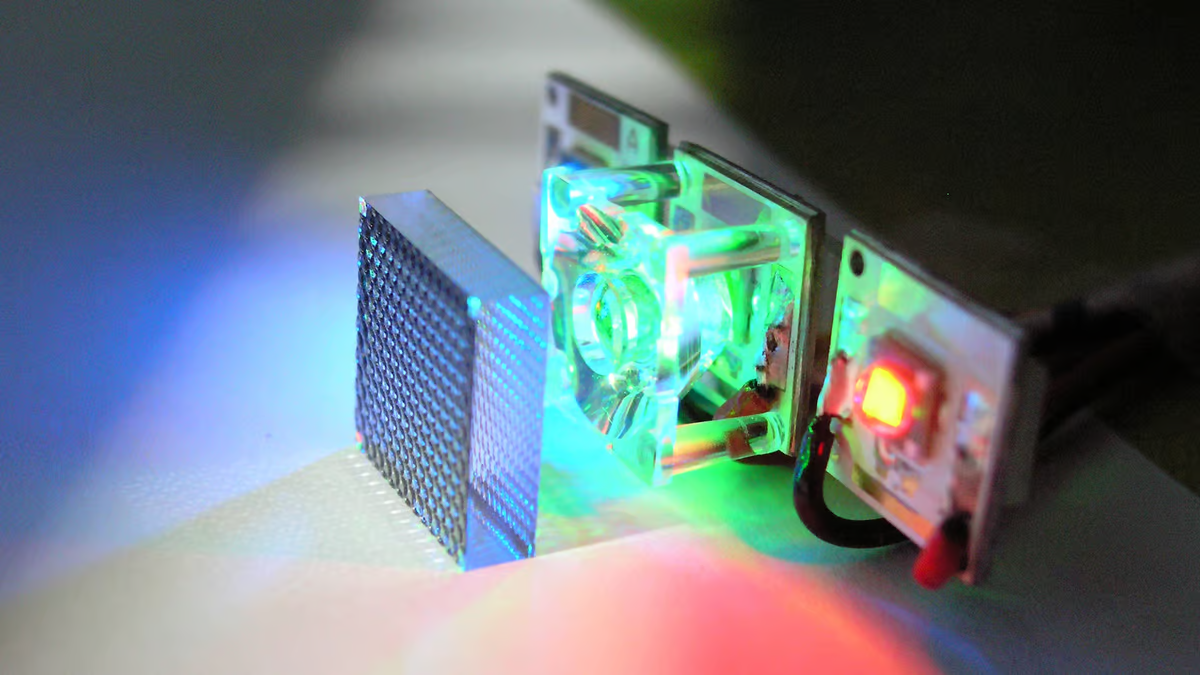
DLP revolves around a Digital Micromirror Device (DMD), a chip with millions of tiny mirrors. Each mirror corresponds to a pixel and can tilt to either reflect light towards the resin or away. Here’s how the magic happens:
- A projective light shines on the DMD chip.
- Based on the 3D model’s layers, the mirrors tilt, guiding the light to harden the resin accurately.
- The build platform lifts, the next layer adheres and the process repeats until the whole model is printed.
Key Takeaway:DLP’s accuracy lies in the choreography of micro mirrors, each dancing in tune with the model’s design.
- Advantages of DLP 3D Printing
Understanding the inherent benefits of DLP technology can help guide you on when to use this method:
a. High Precision: DLP ensures incredible detail quality, both for intricate designs and smooth surfaces, due to its high-resolution light source.
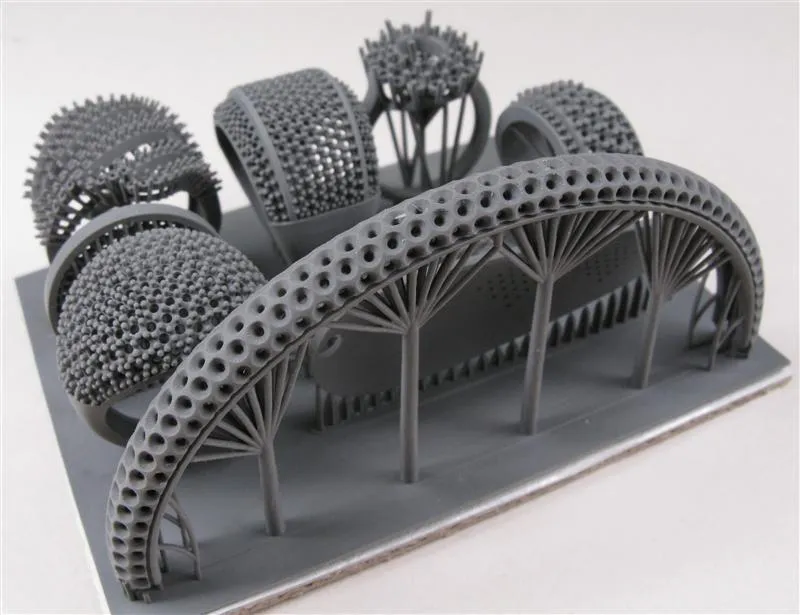
b. Speed: As entire layers are cured simultaneously instead of point-by-point, DLP can be faster than some other forms of resin printing.
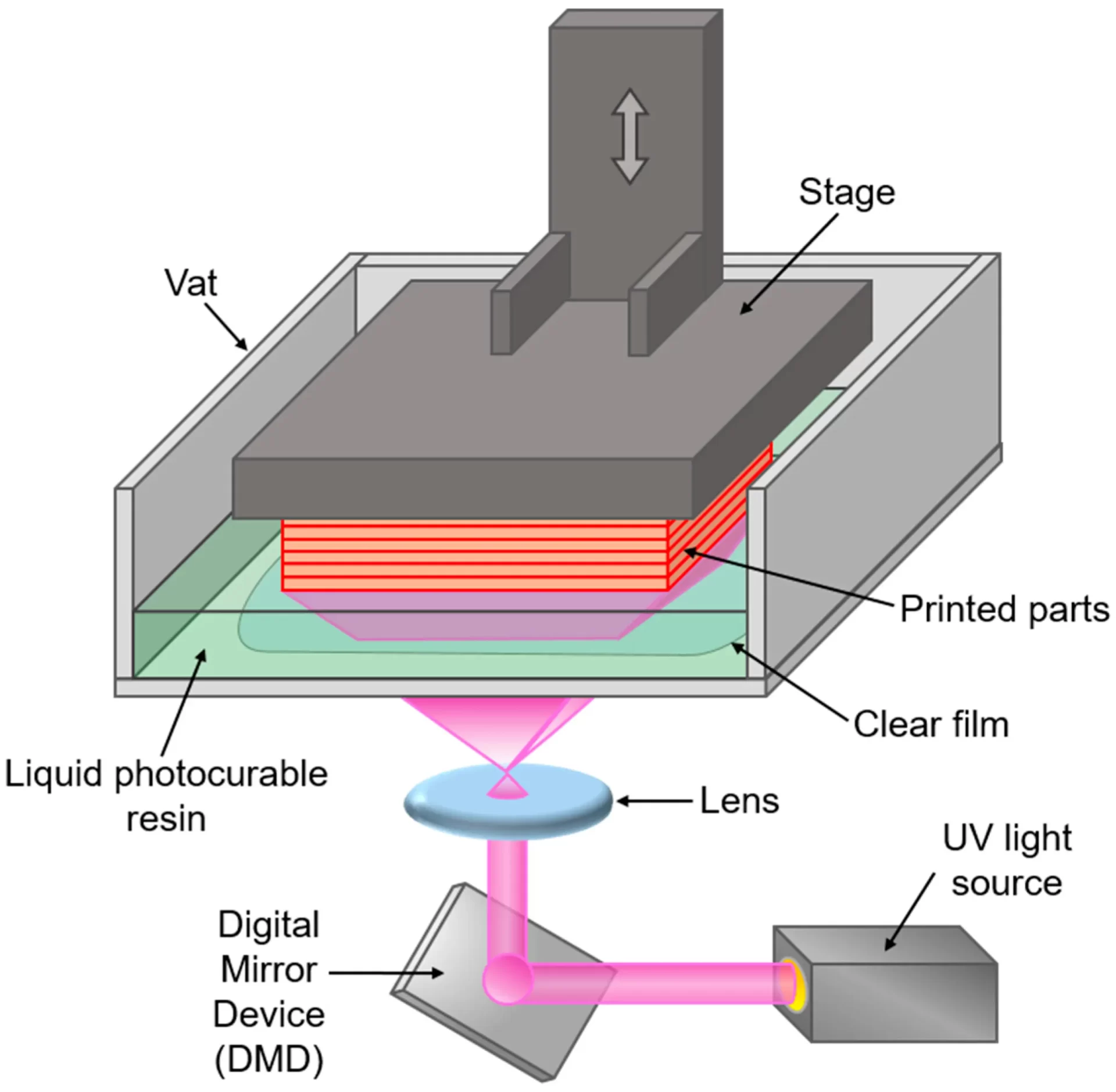
c. Material Versatility: DLP printers can handle a wide array of materials, from standard resins to flexible, castable, or even ceramic-filled resins.
d. Longevity: The absence of mechanical movement in the light source contributes to extended printer lifespan.
- Challenges of DLP 3D Printing
Before you set out with DLP, it’s essential to know the potential roadblocks you might encounter:
a. Cost: DLP printers, especially high-resolution ones, can be pricey. The resins used are also more expensive than filament used in FDM printers.
b. Post-Processing: Printed parts require washing and post-curing, adding time to the overall process.
c. Safety and Handling: Resins can be messy and require careful handling, both for user safety and maintaining the print quality.
d. Limited Build Size: DLP printers often have a smaller build size compared to other types of 3D printers.
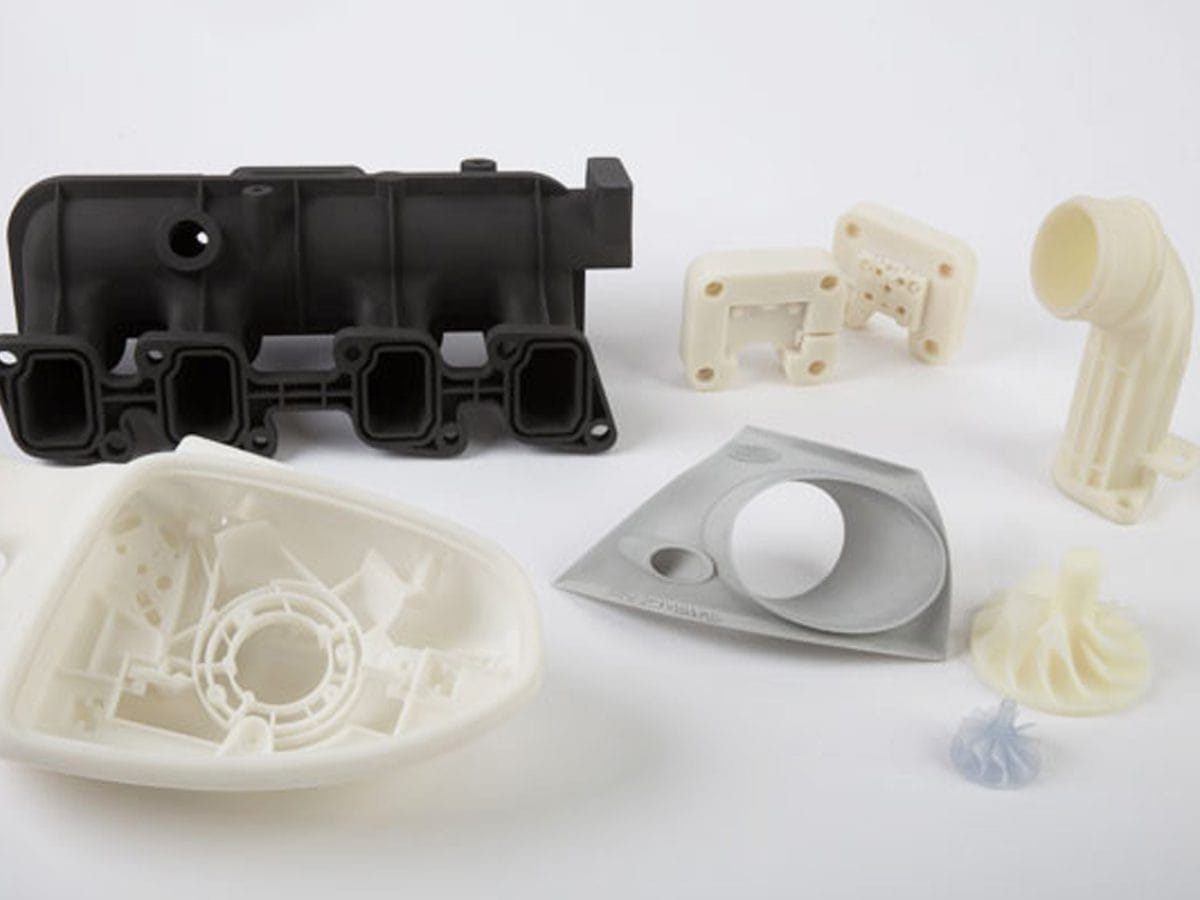
This exploration into DLP 3D printing’s ins and outs should equip you with a deeper understanding of its mechanism, advantages, and constraints. As we shift focus onto the LCD’s world in the following chapter, retain this knowledge to ultimately help you choose the right light to guide your 3D printing journey.
An In-Depth Dive into LCD 3D Printing
Having unraveled the secrets of DLP 3D printing, our narrative leads us into the realm of another guiding luminary in the 3D printing universe – LCD (Liquid Crystal Display) technology.
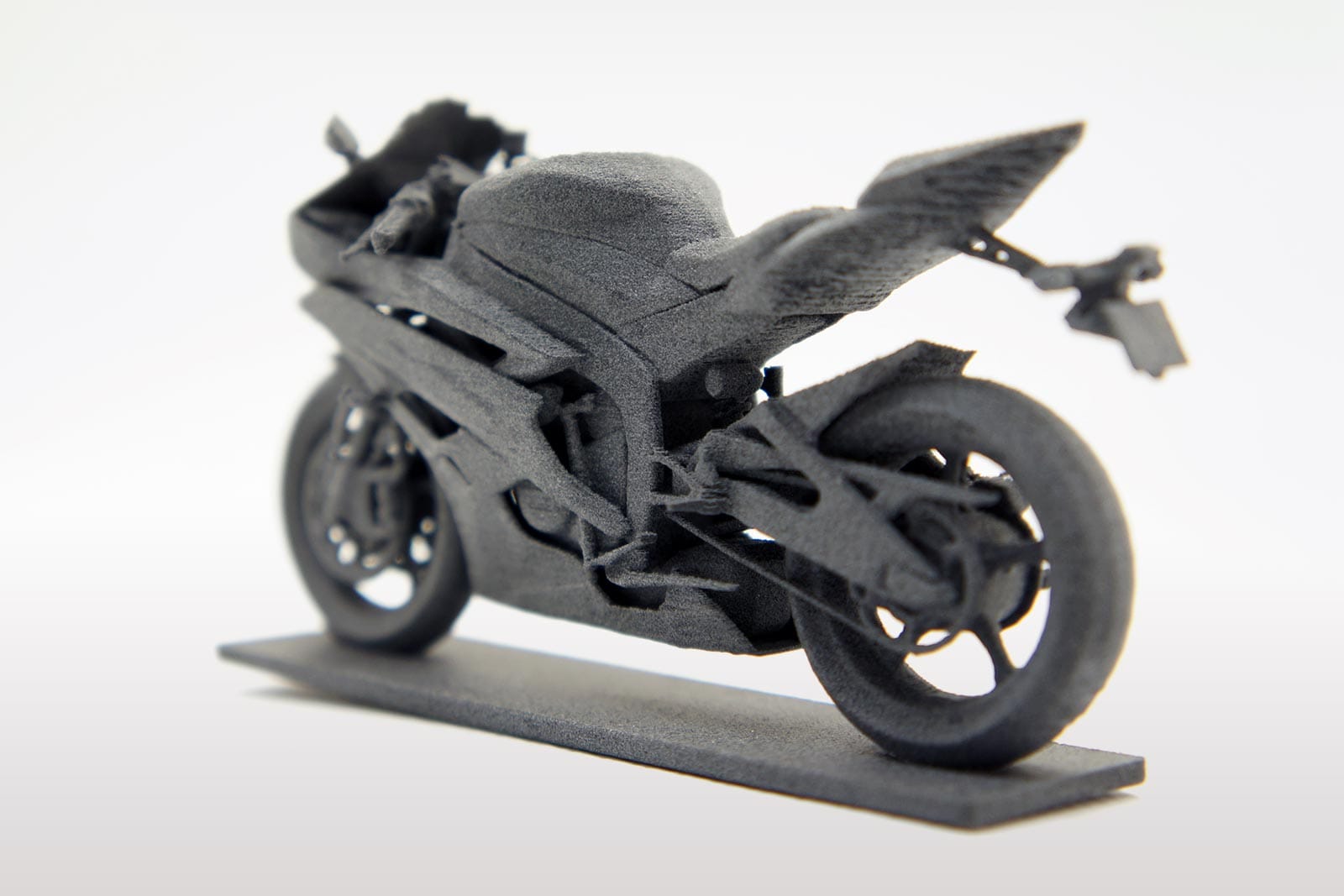
- LCD – The Technology Underneath
At the core of LCD 3D printing is an array of liquid crystals. Unlike DLP, which uses mirrors to direct light, LCD employs a UV LCD panel, which serves as a photomask to allow precise UV light passage, hardening the resin selectively per layer. The snippets of this process are:
- An LCD screen projects the UV light.
- Each pixel on the LCD screen either allows or blocks the light per layer design.
- The resin that gets exposed to light hardens, fusing layer upon layer until the model is complete.
Key Takeaway:LCD’s precision is attributed to the individual control of light passage at each pixel.
- Advantages of LCD 3D Printing
LCD 3D printing offers tangible benefits that might urge you to choose it for your next 3D printing project:
a. Price: Due to relatively simpler technology, LCD printers are generally more affordable.
b. Even Illumination: LCD offers uniform light distribution leading to consistent curing across the entire build plate.
c. Accuracy: As with DLP, LCD can achieve high resolution resulting in detailed and accurate models.
d. Long Lifespan: LCD screens are durable and don’t degrade quickly, ensuring a longer printer lifespan.
- Challenges of LCD 3D Printing
However, every silver lining might have a cloud. Here are some constraints to be aware of with LCD 3D printing:
a. Limited Materials: Not all resins are compatible with all LCD printers, limiting your choices.
b. Durability of Parts: While the printer itself is durable, the parts printed with LCD may not be as strong as those created by other technologies.
c. Post-Processing: Similar to DLP, LCD printed parts require thorough washing and additional post-curing.
d. Screen Replacement: Despite the durability, the LCD screen will eventually need replacement after extensive use.
With this comprehensive understanding of LCD 3D printing, including its process, benefits, and challenges, we hope you’re better equipped to make an informed choice on your 3D printing journey. As we close this chapter, we look forward to illuminating further intriguing aspects of these incredible technologies in the upcoming sections.
Comparing DLP and LCD Printing: When to Use What?
After a detailed exploration into both DLP and LCD, it’s clear that these technologies possess unique strengths that make them ideal for different applications. Now we’ll delve into these scenarios and decipher when you might consider DLP over LCD, and vice versa.
- Speed Games: Large Designs with Homogeneous Details
When it comes to extensive designs with homogeneous details – think big chess pieces or simple geometric shapes – you’d want a method that could render the whole layer simultaneously, which both DLP and LCD can accomplish. However, LCD often edges out DLP in these situations due to its even light distribution, rendering an entire layer uniformly in one single exposure.
Verdict: For large, single-piece models where detail differentiation across the object isn’t paramount, LCD holds the reins.
- Battle of Details: Curves, Corners, and Crevices
Envision a model with intricate details, complex undercuts, and tight crevices. In this scenario, precision and detail resolution are critical, making DLP a solid choice. DLP’s superior control with the micromirrors can render extremely precise details, along with sharper edges, which are crucial for detailed professional applications like jewelry or dental model prototyping.
Verdict: For complex, detailed, and professional-grade models, DLP might be your champion.
- Auto vs. Manual: Ease of Use and Post-Processing
The simplicity of LCD, coupled with its affordability and durability, make it an attractive option for hobbyists and beginners. Moreover, LCD printers require less tinkering, calibration, and maintenance, offering a smoother printing journey.
In contrast, DLP printers, with their superior resolution and print quality, require a slightly steeper learning curve. Post-processing of DLP prints also demand careful washing and post-curing to ensure model stability.
Verdict: For beginners and hobbyists seeking easy operation and minimal tinkering, LCD fits the bill. For more advanced users who can navigate post-processing procedures for higher quality prints, DLP could be the pick.
- Price Tag Woes: Affordability
In terms of equipment cost, LCD printers generally fare better than DLP printers. The simpler technology and components make LCD a more affordable option. However, it’s essential to consider the total cost of ownership, including resin cost, spare parts, and maintenance.
Verdict: For tight budgets and cost-effective printing, LCD would get your vote.
Expanding Horizons: Exploring Other 3D Printing Technologies
We have unveiled the intricacies of DLP and LCD 3D printing technologies, examining their functional principles, the pros, and cons, and their ideal applications. However, the world of 3D printing is not confined to these two! Let’s embark on a brief journey to discover a few other stars that adorn the vast universe of 3D printing.
- Fused Deposition Modeling (FDM)
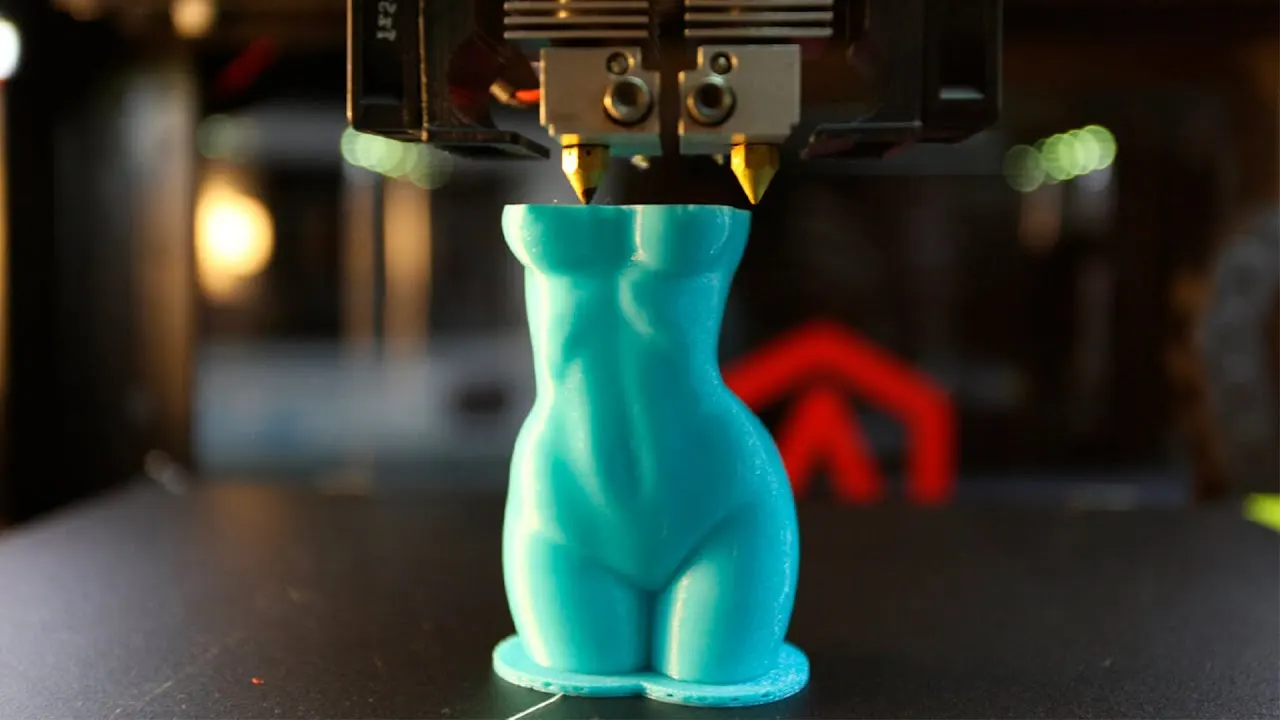
Perhaps the most common and accessible form of 3D printing is Fused Deposition Modeling (FDM). Working on the principle of extrusion, an FDM printer heats a thermoplastic filament and deposits it layer by layer, creating a 3D object. FDM is beloved for its affordability and ease of use, making it popular among hobbyists, educators, and even some commercial users.
- Stereolithography (SLA)
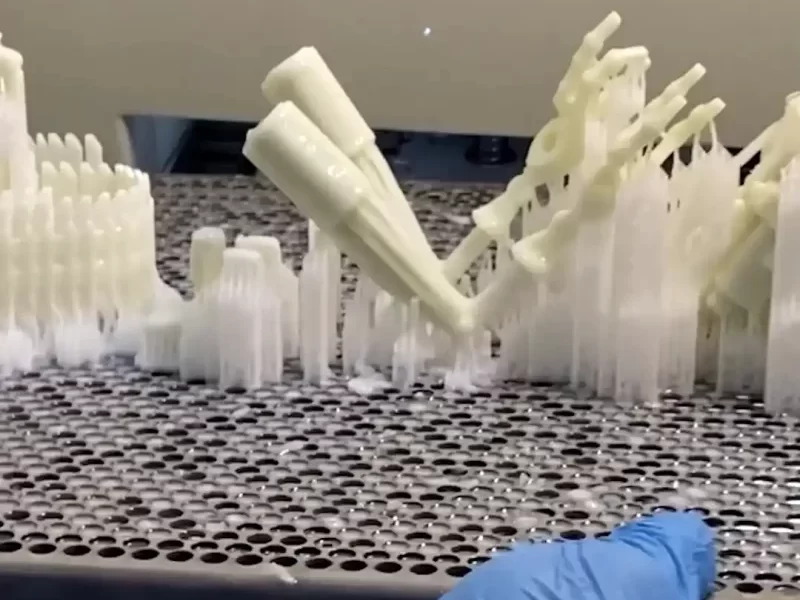
Stereolithography (SLA) is another resin-based 3D printing technology, considered the pioneer in the field. An SLA printer employs a laser to selectively cure a vat of photopolymer resin, creating high-precision, high-detail prints. Ideal for professional applications requiring a superior finish, SLA is commonly used in dental, jewelry, and prototype modeling.
- Selective Laser Sintering (SLS)
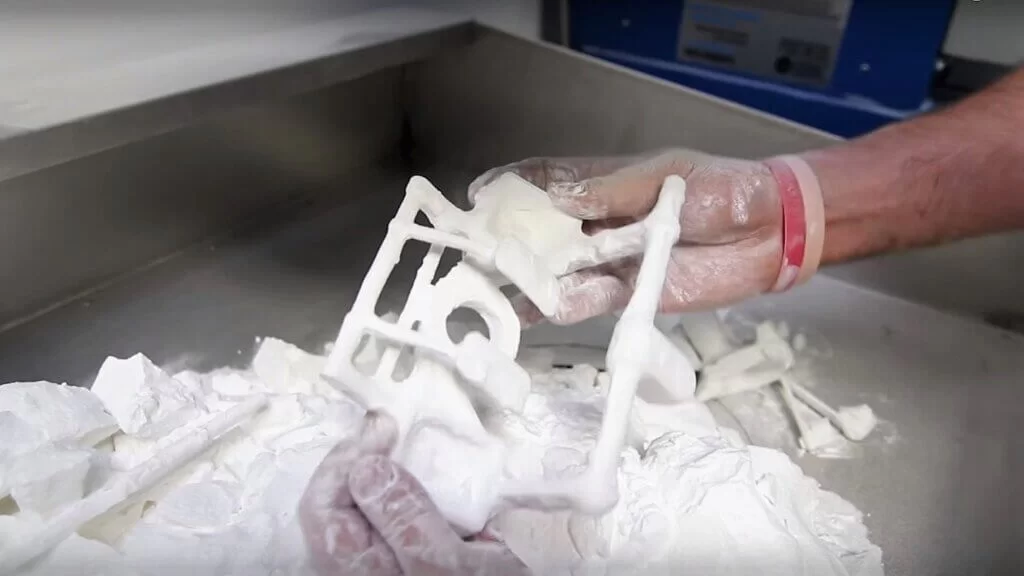
Departing from resin and filament, we find Selective Laser Sintering (SLS), where a high-power laser sinters powdered material, be it plastic, metal, or even glass, layer by layer to form a solid object. Known for its ability to create strong, functional parts without the need for supports, SLS is widely used in the aerospace, automotive, and medical industries.
- MultiJet Fusion (MJF)
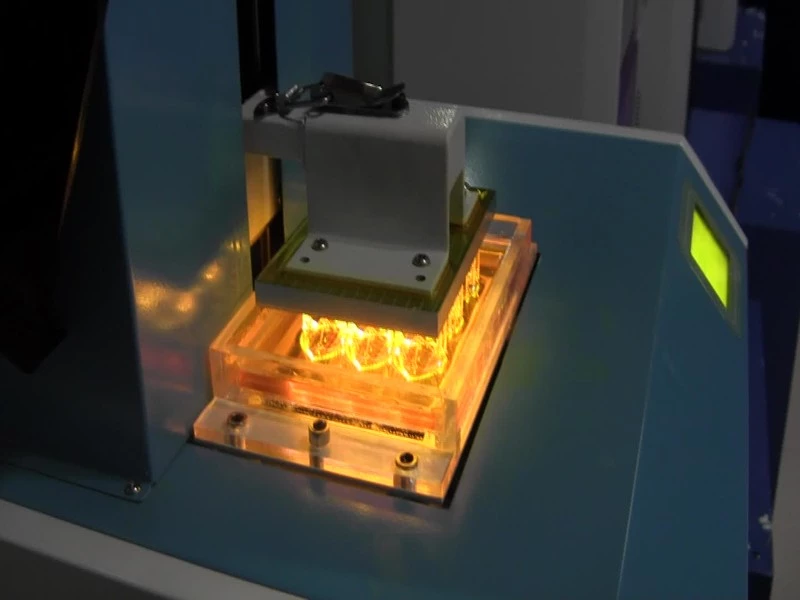
Lastly, MultiJet Fusion (MJF) developed by HP, brings together the principles of SLS and inkjet 2D printing. In MJF, a fusing agent is jetted onto a bed of powder material, which is then activated by heat, producing robust and detailed components. When it comes to producing robust, complex parts in a relatively short timeframe, MJF stands its ground.
3D printing technologies are multifarious and vibrant, each with its unique qualities, advantages, and challenges. At this point, you’ve not only penetrated the depths of DLP and LCD but also brushed the surface of FDM, SLA, SLS, and MJF. As we chart our course to visit more wonders of this universe in upcoming sections, remember, every storyteller’s tale is shaped by their audience. Tailor this learning to suit your specific requirements and keep exploring new horizons in the impressive world of 3D printing.
Making the Right Choice: Tips for Selecting Your 3D Printing Technology
As we’ve navigated through the cosmos of 3D printing technologies, we’re now ready to address the pivotal question: how do I choose the right one? Just as a compass guides a traveler, certain factors can steer you towards the best 3D printing technology for your unique requirements. Let’s throw some light on these pathfinders:
- Assessing Your Design
The complexity, size, and purpose of your model are critical pointers. For large, homogeneous models, LCD may be ideal. However, if your design harbors intricate details and zoetic curves, technologies like DLP or SLA may shine. Remember, compatibility with your model’s intricacies is crucial.
- Material Matters
Consider the type of material your design requires. FDM enables printing with various thermoplastics, while resin printers, such as DLP, LCD, or SLA, deliver models with superior finish. For specialized materials like metals or ceramics, SLS or Direct Metal Laser Sintering (DMLS) might prove worthy.
- Quality vs. Quantity
In terms of precision and finish, DLP, SLA, and MJF dominate. However, for rapid production of simpler models, LCD might suffice. Thus, weigh your need for detailing and refinement against the volume you wish to produce.
- Budget Boundaries
Your budget also plays a significant role. An LCD printer may suffice if affordability is a priority. In contrast, if resources are aplenty, then technologies like SLA, DLP, or even SLS, may afford you superior functionalities.
- Post-Production Lookout
Don’t forget the journey post-printing. Each technology calls for different post-processing procedures, affecting your model’s finish and your project’s lifespan. Therefore, account for your willingness and resources to engage in these processes.
Throughout this section, if there’s one key point you should engrave in your mind, it’s this: Align your 3D printing technology choice with your design requirements, materials, quality and quantity needs, budgetary boundaries, and post-processing capabilities. While each technology we’ve reviewed holds its unique charm, your project goals should determine your ultimate choice. As we journey deeper into the 3D printing algorithm in the chapters to come, may you find your bearings and steer towards enriched 3D printing experiences.