Imagine being in front of two canvases, where your imagination is going to come alive in 3D-one with a fine beam of laser light to do the drawing and the other with the broad stroke of projected light. Such is the sight that presents itself to the creators in the world of 3D resin printing, as one is faced with the decision between Stereolithography and Digital Light Processing.
Over the recent years, resin 3D printing has taken off like a fire and is now one of the major technologies for industries ranging from dentistry to jewelry, prototyping, and custom manufacturing. But with growing popularity comes that pivotal question: which resin printing technology will be best for your needs?
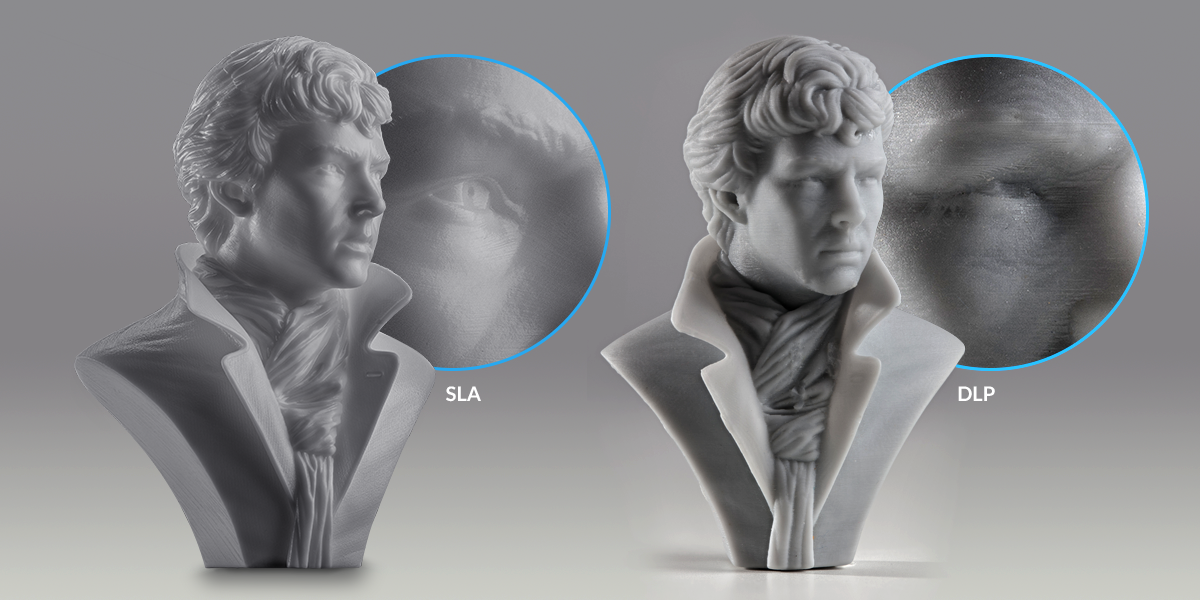
Every nuance of SLA and DLP is investigated in-depth in the following insider glance into the very heart of resin 3D printing. We are going to break down exactly how they work, what makes each different, strengths and weaknesses, and at what each shines. Be it a hobbyist looking to make intricate models or a pro looking to perfect production, the differences between these are important to take full advantage of resin printing. Let’s dive in and see which of these powerhouse technologies will be the right tool for your next project.
Fundamentals of Resin 3D Printing
The first time one steps into the amazing world of 3D printing, resin printing might come into view due to its promise of fine details and smooth surfaces. But what is resin 3D printing, and why is this technology becoming so important in different fields? Let’s see in detail.
What is Resin 3D Printing?
Resin 3D printing, often referred to as vat photopolymerization, involves curing liquid photopolymer resins with light. Here’s how it generally works:
- The Setup: Imagine a tank or ‘vat’ filled with liquid resin. This resin isn’t your average liquid; it’s photopolymer, meaning it solidifies when exposed to certain wavelengths of light.
- The Process:
- A build platform lowers into the resin, just barely submerged.
- Light, whether from a laser or a projector, then selectively illuminates the resin, layer by layer. Where the light hits, the resin cures or hardens, creating a solid object.
- Layer by Layer: After each layer is cured, the platform moves slightly (up for bottom-up printers, down for top-down systems), and the process repeats until the object is fully formed.
Why Resin Printing?
Precision and Detail
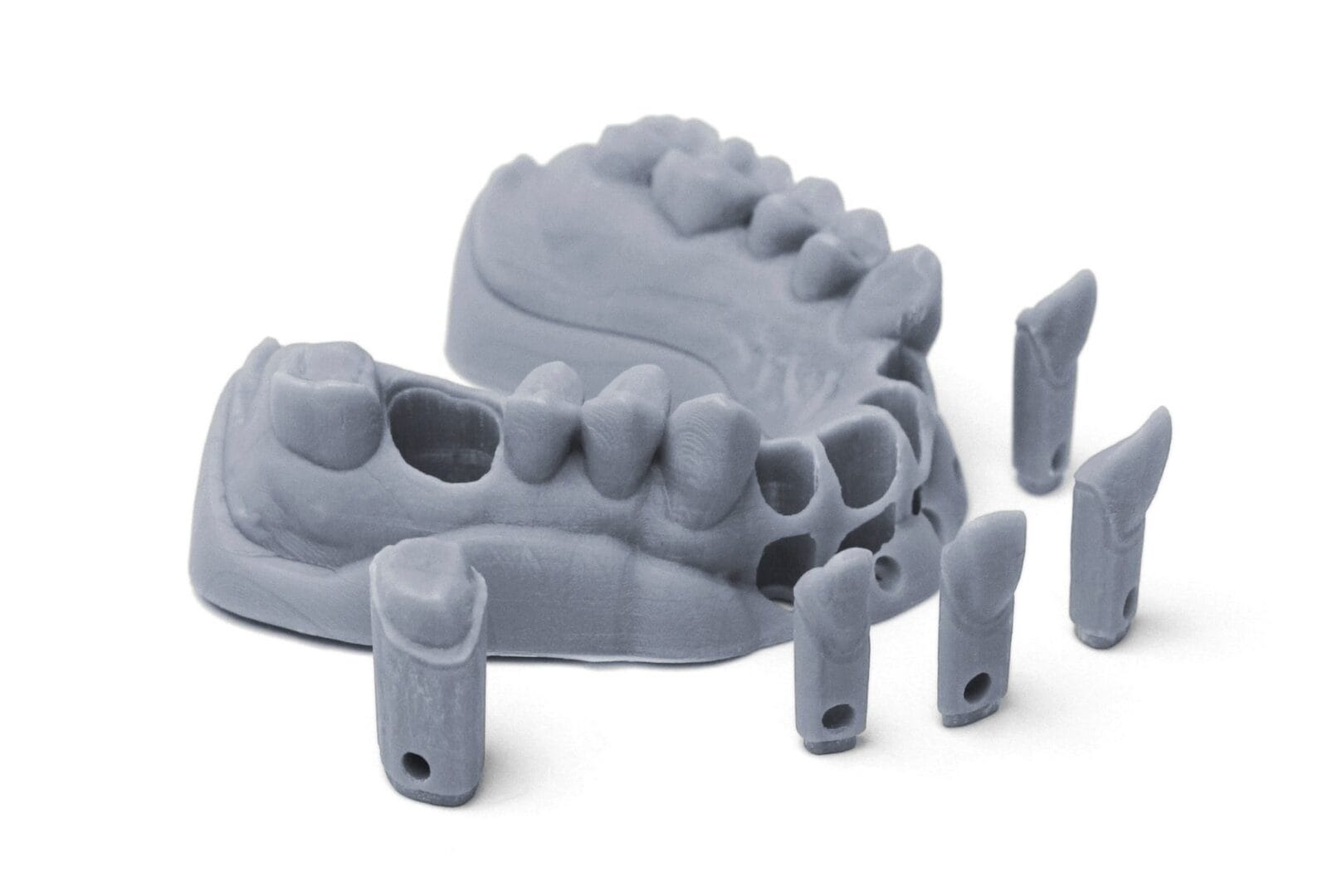
- Resin printers can achieve layers as thin as 25 microns or even less, which means:
- High resolution – Great for intricate designs like jewelry or dental implants.
- Smooth surfaces – Reduces the visibility of layer lines, often requiring less post-processing.
Material Variety
- From standard resins for general use, to castable resins for jewelry making, and even biocompatible resins for medical applications, the options are vast.
Applications Galore
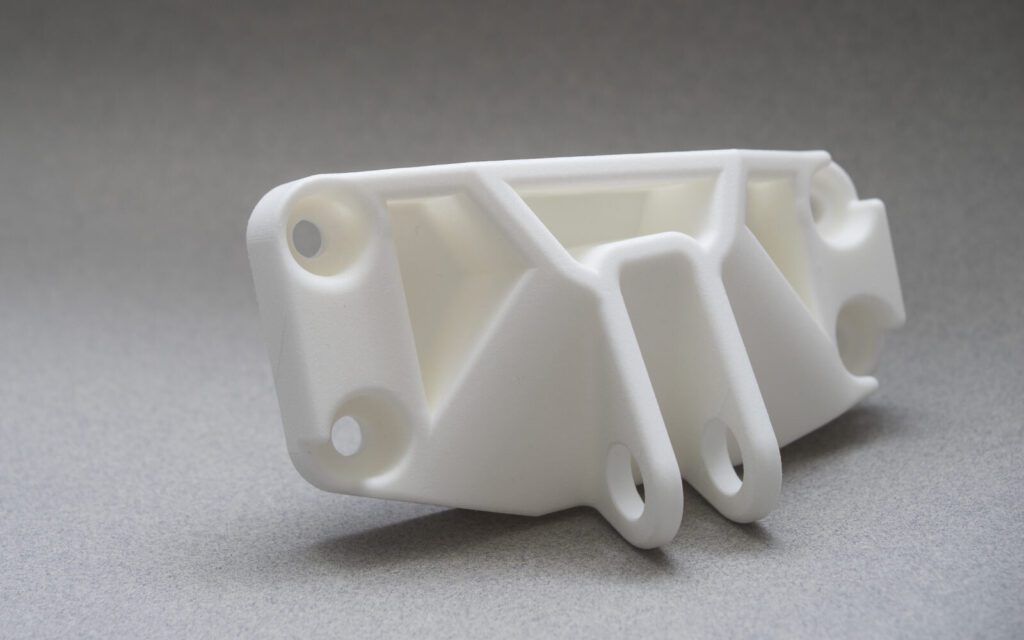
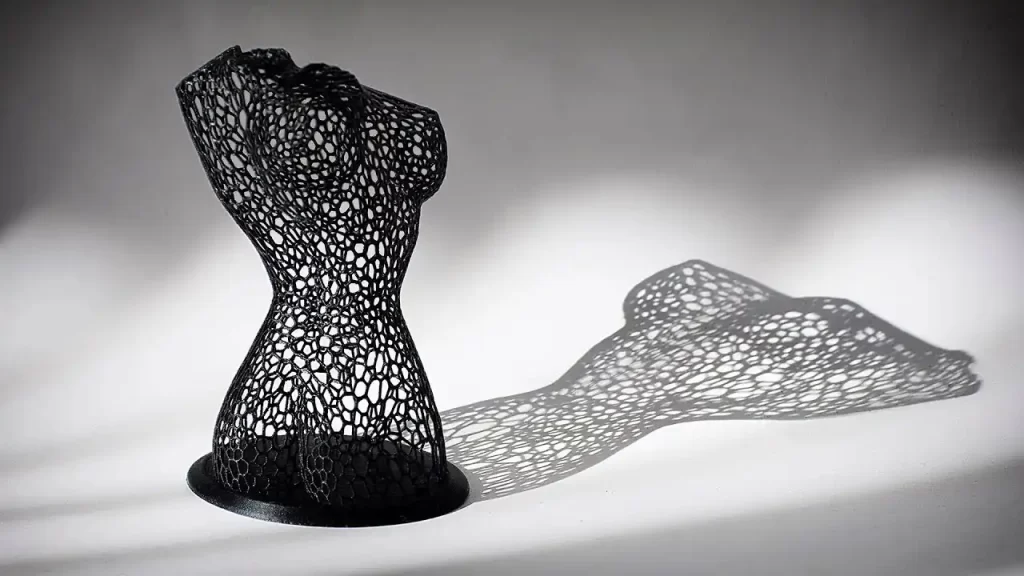
- Dental industry: For crowns, bridges, and surgical guides.
- Jewelry: For creating molds or even direct casting.
- Engineering: Prototyping parts that require fine detail.
- Art and Miniatures: For gamers, collectors, or artists seeking high detail.
The Workflow
- Design: Using CAD software, you design your 3D model.
- Slicing: Software slices your model into thin layers and generates the light patterns needed.
- Printing: The actual printing where magic happens, turning liquid into solid.
- Post-Processing:
- Cleaning: Resin parts typically need to be washed in isopropyl alcohol (IPA) to remove uncured resin.
- Curing: Further curing under UV light to harden the piece fully.
- Finishing: Sanding, painting, or other finishes as required.
Challenges to Consider
- Resin Handling: The resins can be toxic and require careful handling. Gloves, masks, and good ventilation are a must.
- Cost: While the printers themselves have become more affordable, the resin can be pricey, and there’s waste to consider.
- Time: Despite advances, resin printing can be slower than filament-based methods like FDM, especially for larger objects.
3D printing using resin allows one to make highly detailed, smooth models possible. Be it creating the next big thing in tech gadgets, bespoke jewelry, or simply a desire to bring your digital art into the real world, an essential understanding of resin printing is the first step into vibrant series. So power up with knowledge, prepare the workspace, and let the curing light guide your creations from liquid dreams into tangible reality.
Stereolithography: Where Precision in 3D Printing Was First Achieved
Welcome to the wonderful world of Stereolithography-or, as most people refer to it, SLA-the grandsire of resin 3D printing technologies. The brainchild of Chuck Hull back in 1986, SLA was more than just another print technology; it was a sea change in manufacturing and prototyping. Here is everything one could want to know about this most venerable technology.
Historical Context: The Birth of SLA
- Invented by: Chuck Hull, who also co-founded 3D Systems.
- Patent Year: 1986, marking the inception of 3D printing as we know it.
- Why It Matters: SLA set the stage for rapid prototyping, allowing for quicker and more cost-effective development cycles across industries.
How SLA Works
The Core Mechanism

- Vat of Resin: Starts with a tank filled with liquid photopolymer resin.
- Laser: A UV laser traces a cross-section of the object onto the surface of the resin.
- Galvanometers: These are mirrors that direct the laser beam with high precision across the resin surface.
- Curing Process:
- Where the laser hits, the resin cures or hardens.
- This process is known as photopolymerization.
- Build Platform: After a layer is cured, the platform moves (usually down in top-down systems, up in bottom-up setups), and the process repeats.
Layer by Layer Building
- Layer Thickness: Typically ranges from 25 to 100 microns, offering a good balance between speed and detail.
Advantages of SLA
- Superb Detail and Precision:
- Laser Spot Size: The smaller the spot size, the finer the details. SLA can achieve very small, focused points.
- Ideal for jewelry, dental applications, and any model requiring high detail.
- Surface Finish:
- SLA parts have a very smooth surface finish right out of the printer, minimizing post-processing.
- Material Versatility:
- From standard to engineering-grade resins like tough or flexible, SLA can handle a wide variety.
Limitations of SLA
- Print Speed:
- Although precise, curing with a laser point by point can be slower than technologies that cure an entire layer at once.
- Maintenance:
- Lasers can degrade over time, requiring replacement.
- The system needs regular calibration for optimal performance.
- Size Limitations:
- Large objects take longer and might be less cost-effective due to the time and resin used.
The SLA Workflow
- Design: Your model in CAD software.
- Slicing: Software prepares the model by slicing it into layers and planning the laser’s path.
- Printing:
- Laser Calibration: Ensure the laser is focused for optimal results.
- Resin Selection: Choose the right resin for your project’s needs.
- Post-Processing:
- Washing: Use solvents like IPA to clean off excess resin.
- Post-Curing: UV light exposure to achieve maximum material properties.
- Support Removal: Carefully remove supports, which can be more intricate due to the high detail.
Choosing SLA: When Does It Make Sense?
- High Detail Required: If your project demands intricate details or smooth surfaces.
- Small to Medium Objects: Best for objects where detail outweighs the build volume.
- Professional Applications: Dentistry, jewelry, engineering prototypes where precision is non-negotiable.
SLA is still one of the best options for anyone who wants literally the best detail and quality in 3D printing. While not the fastest or the cheapest, precision has kept SLA relevant in a constantly evolving field. Whether it be a custom design for jewelry, prototyping the latest and greatest in tech gadgets that are sure to change the world, or dental implants, the careful process of SLA will make sure your creations turn out both stunningly beautiful and functional. Avail of the service offerings SLA when your work demands the best for 3D resin printing.
Digital Light Processing-When Speed Marries Precision in 3D Printing
Welcome to fast-moving DLP, a resin 3D printing technology that is all about bringing your designs to life with speed without giving away too much in detail. While SLA might be the meticulous artist, DLP is the efficient craftsman-ready for volume production. Here’s the full scoop on DLP:
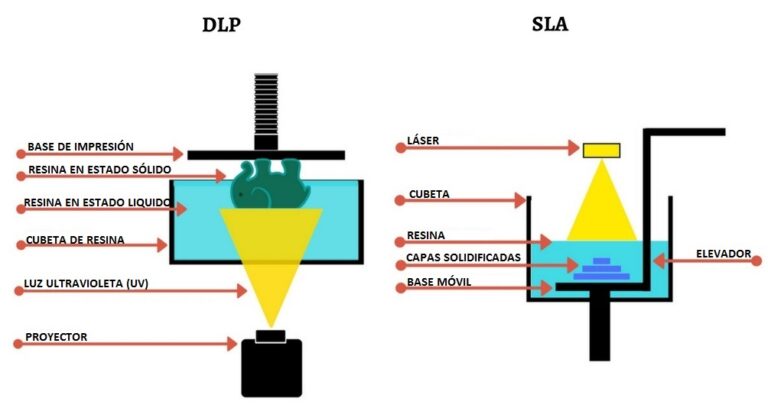
Introduction to DLP Technology
- Developed by: Larry Hornbeck of Texas Instruments in 1987, primarily for projectors, but its application in 3D printing has revolutionized the speed at which detailed models can be produced.
- Why DLP?: It offers a unique approach to curing resin that balances speed with detail, making it particularly appealing for certain applications where time is of the essence.
The Mechanism of DLP
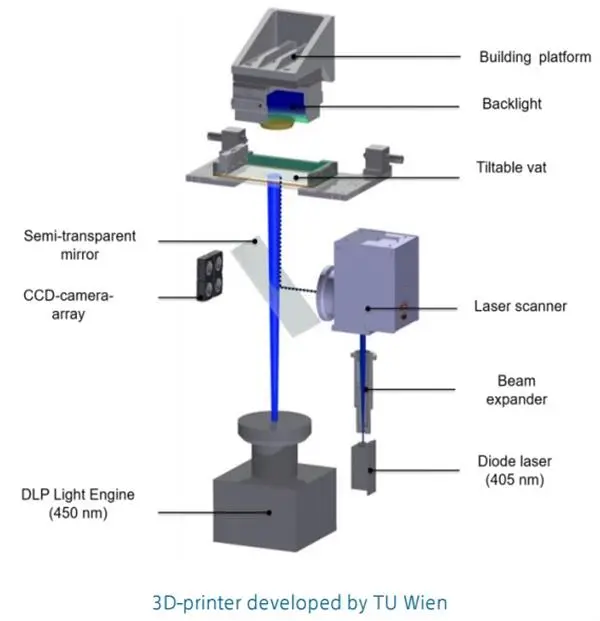
Core Components
- Digital Light Projector:
- Instead of a laser, DLP uses a digital projector to flash an entire layer at once onto the resin.
- Digital Micromirror Device (DMD):
- The heart of DLP technology, the DMD is an array of tiny mirrors. Each mirror corresponds to a pixel in the image projected.
- These mirrors tilt rapidly to either reflect light through the lens (on) or away from it (off), creating the light pattern needed to cure the resin.
- ResinVat:
- Similar to SLA, but the interaction with light here involves a broad area exposure rather than point-by-point curing.
The Printing Process
- Layer Exposure: The projector exposes an entire layer of resin at once, curing it in a single flash. This significantly reduces printing time compared to SLA.
- Resolution: Determined by the resolution of the projector; higher resolution projectors can lead to finer details but at the cost of potentially smaller build areas.
Benefits of DLP
- Speed:
- Entire layers are cured at once, making DLP generally faster than SLA for models with similar levels of detail.
- Consistency:
- The light intensity is uniform across the layer, leading to consistent curing and potentially fewer failures.
- Good for Prototyping:
- Ideal for applications where you need multiple iterations or many parts in a short amount of time.
Drawbacks of DLP
- Resolution Limitations:
- The resolution is tied to the projector’s capabilities. While high, it might not match the fine point detail of SLA’s laser.
- PixelDistortion:
- At the edges of the build area, pixels can become elongated or distorted, which might affect part quality.
- Light Bleed:
- There can be some light bleed or scatter, which might slightly reduce the crispness of edges.
DLP in Action: When to Use It?
- Rapid Prototyping:
- When you need to iterate designs quickly, DLP’s speed is invaluable.
- Figurines and Miniatures:
- Hobbyists love DLP for creating detailed models where speed helps in producing multiple pieces or sets.
- Dental and Medical Models:
- For applications where speed and a good level of detail are required, but not necessarily the ultra-fine detail of SLA.
The DLP Workflow
- Model Preparation: Similar CAD design process as with other 3D printing methods.
- Slicing:
- Software prepares the model, but here, it’s optimizing for full layer projections.
- Printing:
- Projector Calibration: Ensuring the projector accurately reflects the desired image is key for quality prints.
- Post-Processing:
- Cleaning: Washing off uncured resin.
- Curing: Post-cure under UV light for full material strength.
- Support Removal: Often easier than with SLA due to potentially less intricate support structures.
Since DLP could work out a way to balance the speed with the detail to a good enough level, it became a game-changer in resin printing and turned into a weapon for hobbyists and pros alike. Not as capable of capturing each micro-detail as SLA, DLP can produce great quality prints at relatively fast speeds and finds its necessary place in the toolkit of a 3D printer. Whether someone is printing off a set of miniatures for the next gaming session or prototyping the next hot product, DLP delivers with swift precision.
Comparative Analysis: DLP vs. SLA in Resin 3D Printing
When choosing between Digital Light Processing (DLP) and Stereolithography (SLA), it’s not just about picking a printing method; it’s about aligning your project needs with the technology that best serves them. Here’s an in-depth comparison to guide you through this decision.
Print Quality
Resolution
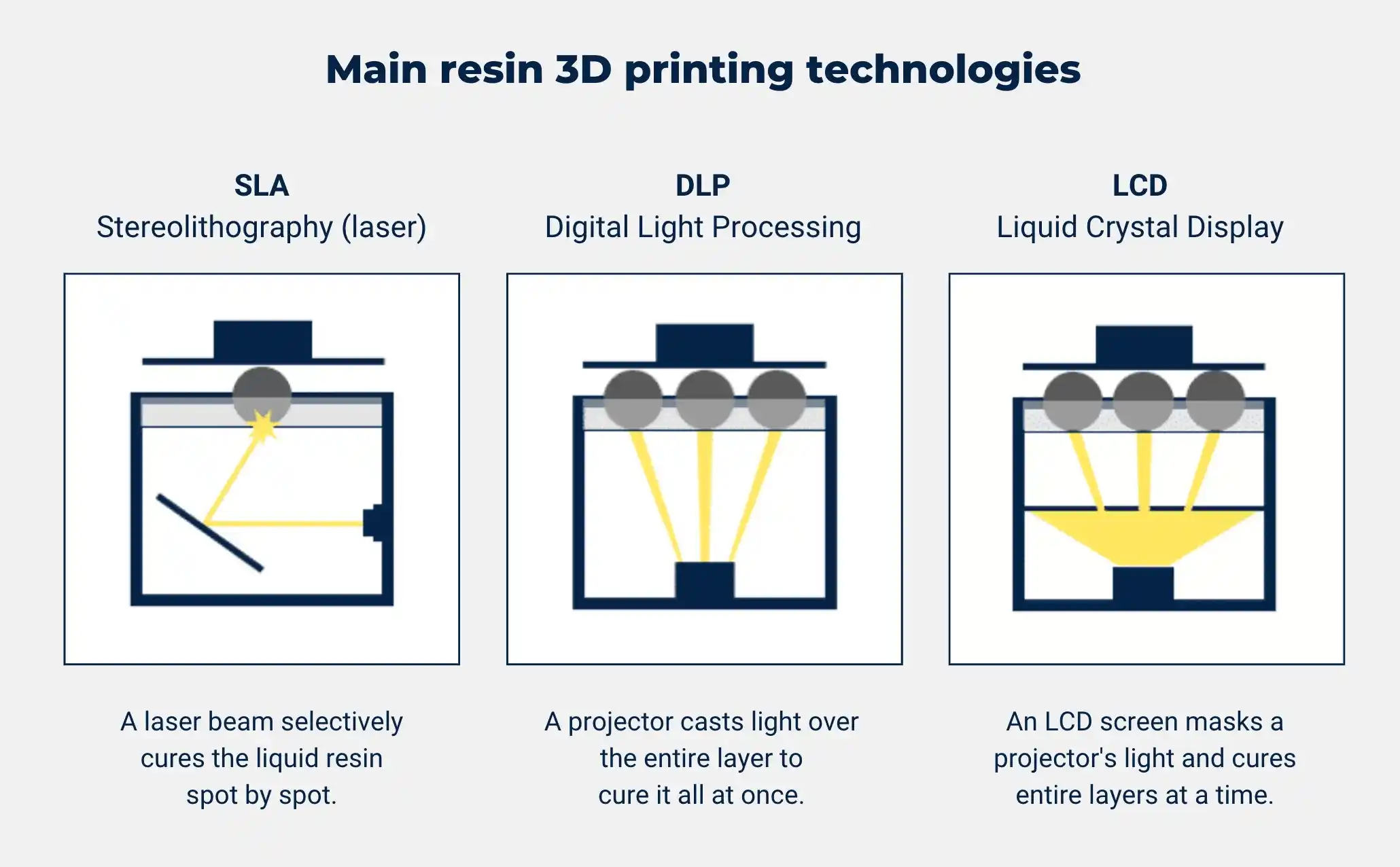
- SLA:
- Laser Spot Size: Typically can achieve a smaller spot size, leading to very fine details.
- Best for: Ultra-high resolution prints where every micron counts, like intricate jewelry or dental work.
- DLP:
- Pixel Size: Resolution is dependent on the projector’s resolution. While very good, it might not reach the peak detail of SLA due to the fixed pixel size.
- Best for: High detail but where slight compromises on the smallest features are acceptable for faster production.
Surface Finish
- Both technologies offer excellent surface finishes right out of the printer, but SLA might have a slight edge due to the precision of the laser. However, DLP‘s uniform light exposure often results in very smooth surfaces with less noticeable layer lines.
Speed
- DLP:
- Layer Exposure: Cures an entire layer at once, significantly reducing print times, especially beneficial for larger objects or when printing multiple items simultaneously.
- SLA:
- Point-by-Point Curing: Generally slower as it traces each part of the model with a laser, though advancements in laser technology are closing this gap.
Material Use
- ResinCompatibility:
- SLA might have a slight advantage with a broader range of specialized resins due to its longer history and widespread use.
- DLP works well with most resins but might have limitations with very specialized or highly viscous resins due to the nature of its curing process.
- Waste: Both produce waste in the form of supports and uncured resin, but SLA might waste less resin in some scenarios due to its precision.
Cost Implications
- Initial Investment:
- SLA Printers: Often come with a higher initial cost due to the precision engineering of lasers and galvanometers.
- DLP Printers: Generally more affordable upfront, with the cost largely in the projector, which can also be upgraded or replaced more economically.
- Operational Costs:
- SLA: Laser replacements can be costly, and the system might require more maintenance.
- DLP: Projector bulbs or LEDs will need replacing, but typically this is less frequent and cheaper than laser maintenance.
Scalability and Size
- Build Volume:
- DLP might offer larger build volumes at a lower cost per cubic centimeter of print volume, beneficial for producing bigger parts or batch printing.
- Detail on Large Prints:
- SLA maintains high detail across all sizes, whereas DLP might lose some detail on very large prints due to pixel size.
Choosing Based on Application
- For High Detail, Small Items:
- SLA is often the go-to for jewelry, dental, and micro-engineering parts.
- For Speed or Larger Items:
- DLP shines in producing miniatures, prototyping where speed is crucial, or when printing multiple items at once.
Environmental and Handling Considerations
- Resin Handling: Both require careful handling, but SLA systems might be slightly more complex due to laser safety considerations.
- Environmental Impact:
- DLP might consume less power per print due to faster printing times, potentially reducing the environmental footprint for large volumes.
Matching Technology to Need
Choosing between DLP and SLA depends heavily on your project’s requirements:
- Choose SLA if your work demands the absolute highest detail, or you’re working with very specialized resins where precision is non-negotiable.
- Opt for DLP when speed, cost-effectiveness for larger prints, or batch production are your priorities, and you can accept very good, but not necessarily the finest, detail.
In the dynamic field of 3D printing, both technologies have their place. By understanding these differences, you can make an informed choice that maximizes efficiency, quality, and cost-effectiveness for your specific needs.
Applications: Where SLA and DLP Shine in 3D Printing
Each 3D printing technology brings its unique strengths to the table, making Stereolithography (SLA) and Digital Light Processing (DLP) suited for different applications. Here’s how these technologies are applied across various industries, showcasing their practical uses.
SLA Specific Applications
Jewelry Casting
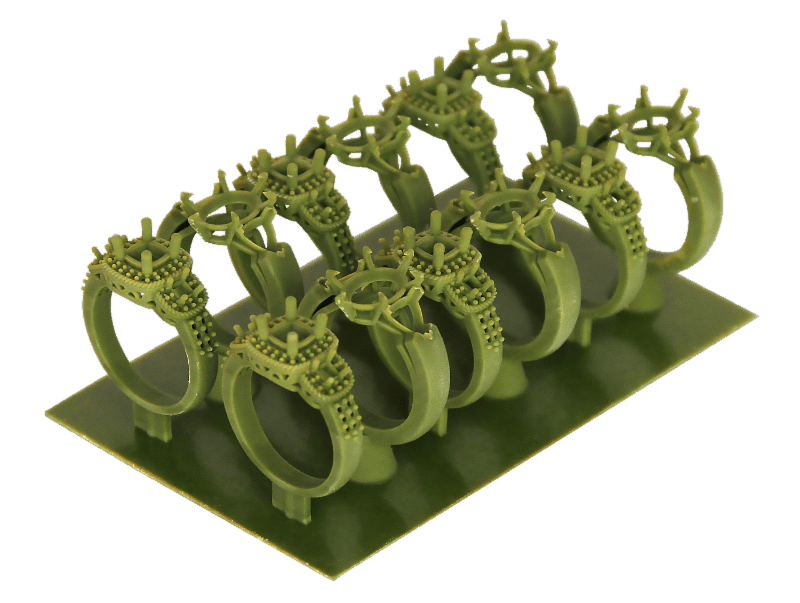
- High Precision: SLA printers are ideal for jewelry due to their ability to capture the minutest details, which is crucial for intricate designs that require casting patterns with smooth surfaces for direct casting processes.
- Material Use: Castable resins designed for SLA produce burnout with little to no ash, ensuring clean molds for casting precious metals.
Dental Models
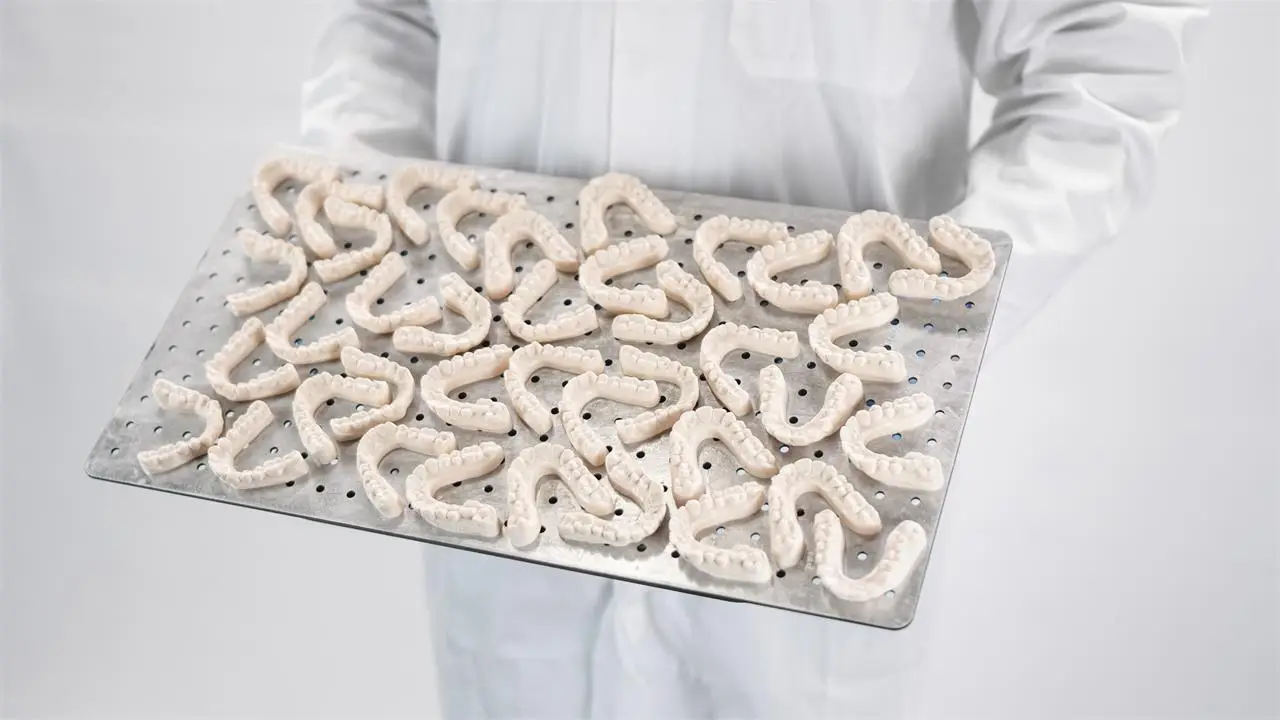
- Detail and Accuracy: The dental industry demands high precision for crowns, bridges, and aligners. SLA’s fine resolution ensures that each dental model matches the patient’s anatomy perfectly.
- Biocompatibility: Specialized dental resins that are biocompatible can be used, which is essential for surgical guides and orthodontic devices.
Engineering Prototypes
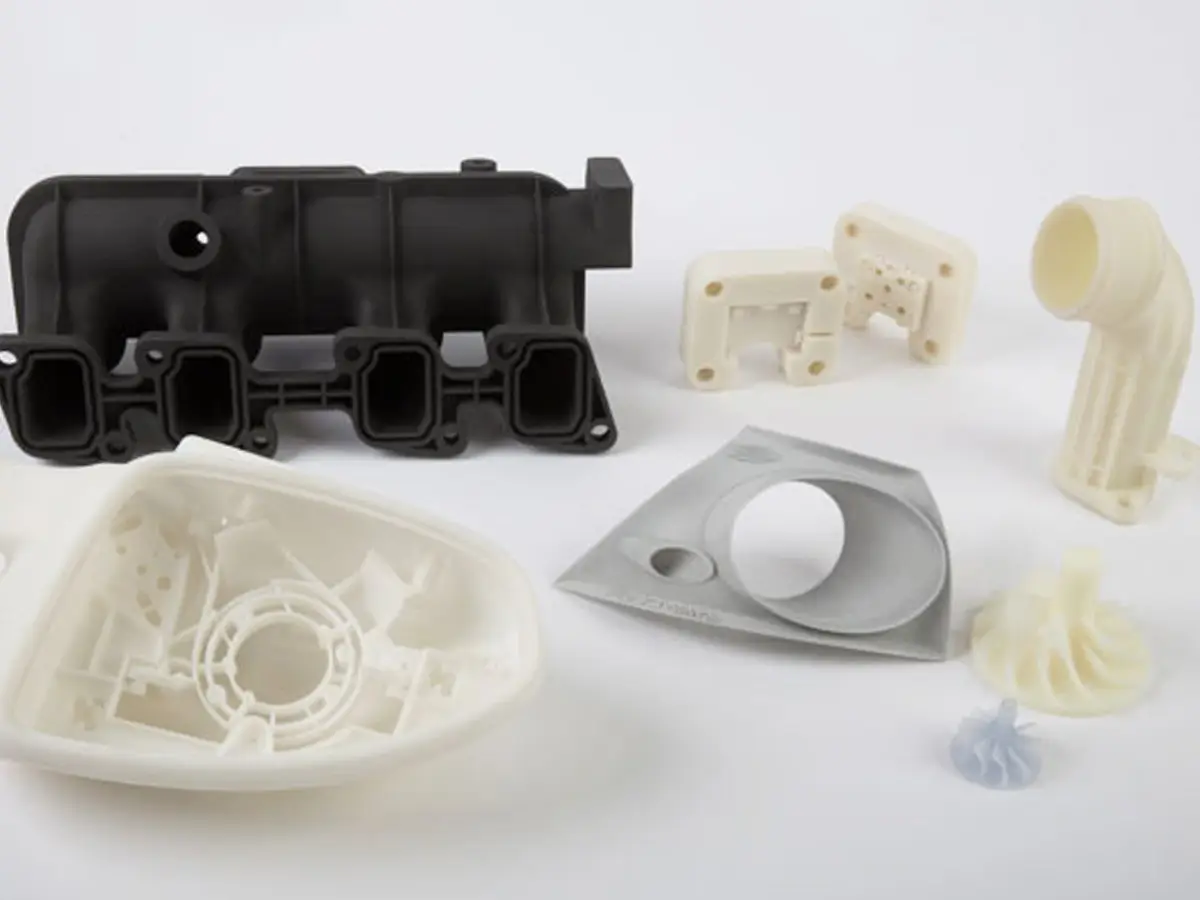
- Functional Testing: Engineers use SLA for parts that need to fit within assemblies or undergo stress testing. The high detail and surface finish allow for functional prototypes that closely mimic final products.
- Aerospace and Automotive: For components where every gram and every curve matters, SLA’s precision helps in creating lightweight, optimized parts.
DLP Preferred Uses
Rapid Prototyping
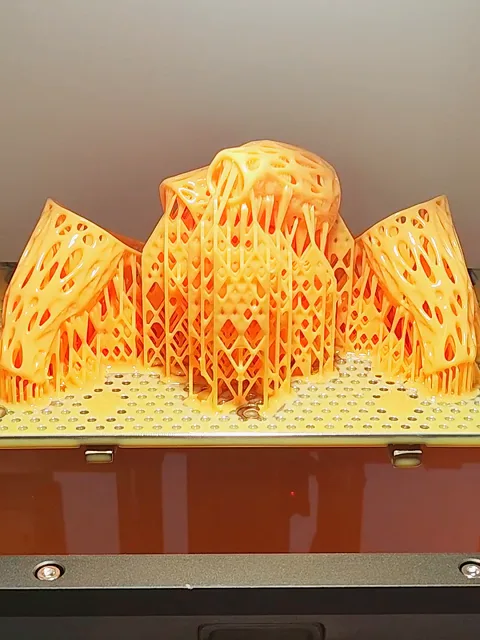
- Speed: DLP’s ability to cure entire layers at once makes it invaluable for rapid prototyping where multiple iterations might be needed in a short time frame.
- Cost Efficiency: For businesses where time-to-market is critical, DLP reduces the development cycle, allowing for quicker design validations.
Figurines and Miniatures
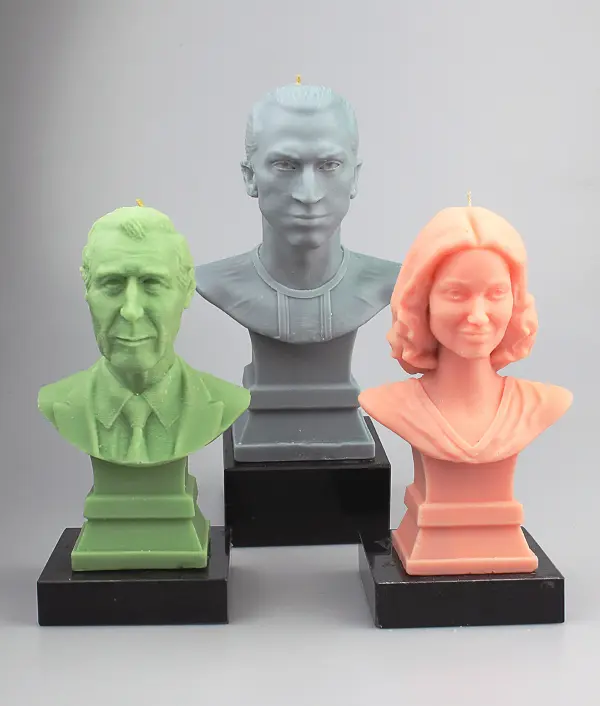
- Batch Production: Hobbyists and companies producing gaming miniatures or collectibles prefer DLP for its ability to print multiple figures at once without a significant drop in detail quality.
- Customization: The speed of DLP printing supports customization at scale, where each miniature can be slightly different, catering to personalized gaming experiences or bespoke collections.
Medical Models for Education
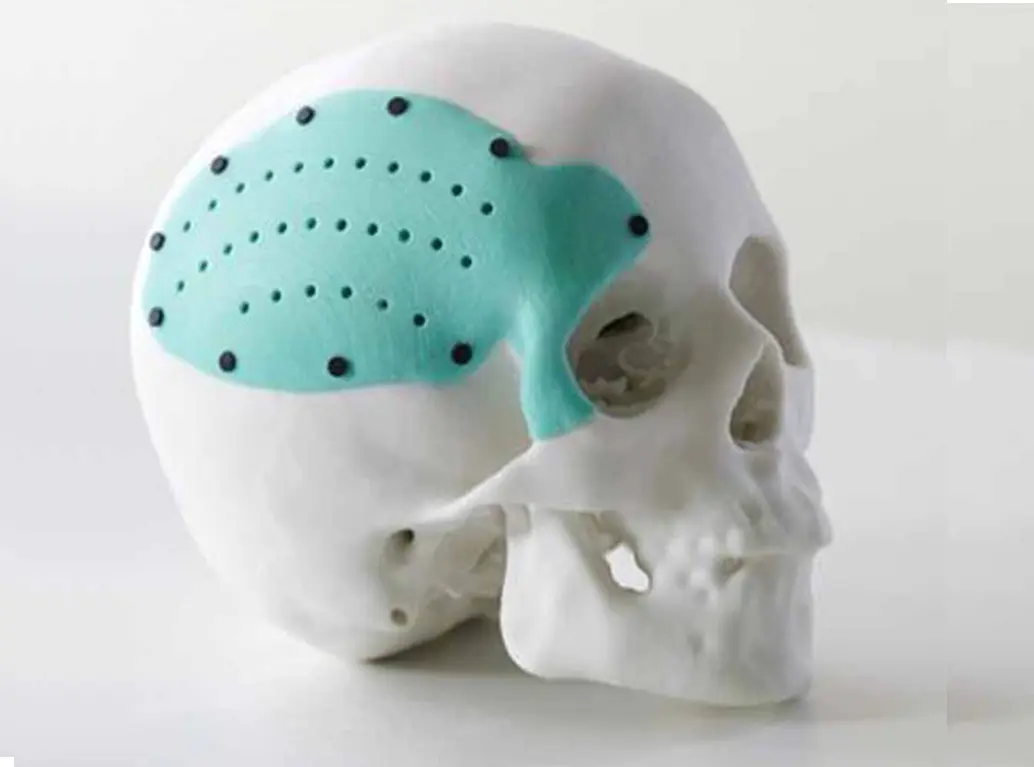
- Anatomical Models: DLP printers are often used to produce detailed anatomical models for educational purposes where speed and volume are more critical than the ultra-fine detail of SLA.
- Speed Over Ultra Detail: While still providing good detail, DLP’s faster print times are beneficial for producing multiple models for classrooms or training sessions.
Art and Sculpture
- Creative Flexibility: Artists might opt for DLP when creating larger pieces or when they need to produce multiple iterations of an art piece quickly for exhibitions or client reviews.
Shared Applications
- Product Development: Both technologies are used for concept models where the physical form needs to be reviewed, though the choice might depend on the level of detail required versus the need for speed.
- Mold Making: While SLA might be preferred for direct casting, DLP is excellent for creating master patterns for silicone molds due to its speed and good surface finish, which is adequate for many mold-making applications.
Tailoring Technology to Task
The choice between SLA and DLP in these applications comes down to the specific requirements of the project:
- SLA is your go-to when every detail counts, and you need the highest possible resolution, particularly for applications where the end product’s quality depends on microscopic accuracy.
- DLP steps in when speed, volume, and cost-effectiveness are paramount, and while detail is still important, there’s room for slight trade-offs for the sake of efficiency.
By matching the technology to the task, users can optimize both the creative and manufacturing processes, ensuring that whether it’s a piece of jewelry, a dental implant, or a custom miniature, the result meets or exceeds expectations.
Technological Advancements in SLA and DLP
As 3D printing evolves, both Stereolithography (SLA) and Digital Light Processing (DLP) are not standing still. Innovations in these technologies are pushing the boundaries of what’s possible in resin-based printing. Here’s a look at the recent advancements and how they’re shaping the future of 3D printing.
Recent Innovations in SLA
Advanced Laser Systems
- Higher Power Lasers: Newer SLA printers are equipped with more powerful lasers that can cure resins faster, reducing print times without sacrificing detail.
- Multiple Laser Sources: Some high-end SLA machines now employ multiple lasers, allowing for simultaneous curing of different parts of a layer, significantly speeding up the process.
Improved Motion Systems
- Dynamic Beam Control: The development of more sophisticated galvanometers allows for quicker and more precise laser movement, improving both speed and the ability to create intricate details.
- Reduced Vibration: Enhanced build platforms and motion systems reduce vibrations, leading to even smoother surfaces and higher precision.
Smart Resin Handling
- Automated Resin Systems: Innovations like auto-refilling resin tanks and integrated resin management systems minimize user intervention, optimize resin use, and maintain consistency in prints.
- Resin Development: New formulations of resins are being developed to work with these advanced systems, offering properties like increased toughness, flexibility, or even conductivity.
DLP Developments
Higher Resolution Projectors
- 4K and Beyond: The adoption of 4K and even higher resolution projectors in DLP systems means finer details can be achieved, closing the gap with SLA in terms of resolution.
- LED Technology: Transition to LED light sources from traditional bulbs has increased the lifespan of projectors, reduced heat generation, and improved color accuracy for curing different resins.
Enhanced DMD Technology
- Increased Mirror Density: Digital Micromirror Devices with higher mirror counts enhance resolution and reduce pixelation effects, allowing for smoother surfaces.
- Faster Switching Mirrors: Newer DMDs can switch states faster, which not only speeds up printing but also allows for grayscale curing, providing better control over material properties.
Layerless Printing
- Continuous DLP: Innovations like Continuous Liquid Interface Production (CLIP) technology, though different from traditional DLP, showcase the potential for ‘layerless’ printing where resin is continuously drawn and cured, dramatically increasing speed.
Improved Software and Algorithms
- Optimized Light Exposure: Advanced algorithms now optimize how light is used to cure resin, reducing over-curing and improving the mechanical properties of the final print.
- Adaptive Layer Thickness: Software that dynamically adjusts layer thickness based on the complexity of the current cross-section, balancing speed and detail more effectively.
The Future of Resin Printing
Hybrid Systems
- Combining Technologies: Future printers might combine elements of SLA, DLP, and even other technologies like jetting to leverage the strengths of each, potentially offering unparalleled versatility in a single machine.
Material Science Breakthroughs
- Functional Resins: Development in resin materials could lead to prints with embedded functionalities, like electrical conductivity, thermal properties, or even biological compatibility for direct medical use.
Automation and Integration
- Factory Integration: Both SLA and DLP are moving towards greater integration into automated production lines, with robotic arms for post-processing, inline quality checks, and more seamless workflows.
Environmental Considerations
- Eco-friendly Resins: As environmental concerns grow, there’s a push towards biodegradable resins and systems designed for less waste, making 3D printing more sustainable.
These improvements in SLA and DLP are not only extending what these systems do today but are building the bridge to the future of manufacturing. From the creation of complex, highly detailed models at unprecedented speeds to the integration of 3D printing into fully automated production environments, both SLA and DLP technologies represent leading-edge industrial innovation. And with these on, we will see a further seamless integration in industries and the lines that separate prototyping from production continually blur, bringing us closer to the world of scale custom manufacturing, if not a banal one.
More You Like
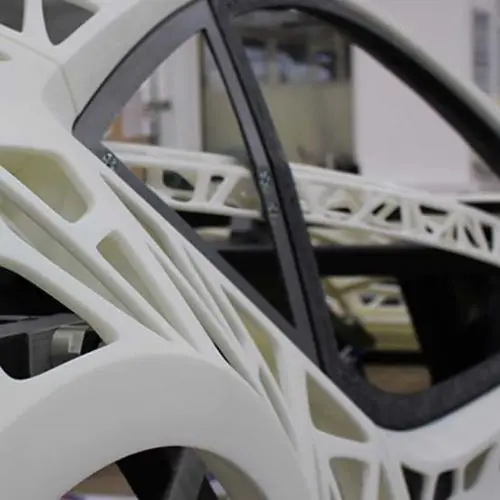
355nm SLA Standard Resin
Standard resins are the most commonly used and provide a good balance of cost and performance for general prototyping and production applications. They create rigid plastic parts with properties similar to injection-molded plastics.
355nm SLA High Temperature Resin
The 355nm High Temperature Resin is designed to withstand extreme temperatures, making it ideal for applications that involve prolonged exposure to heat.
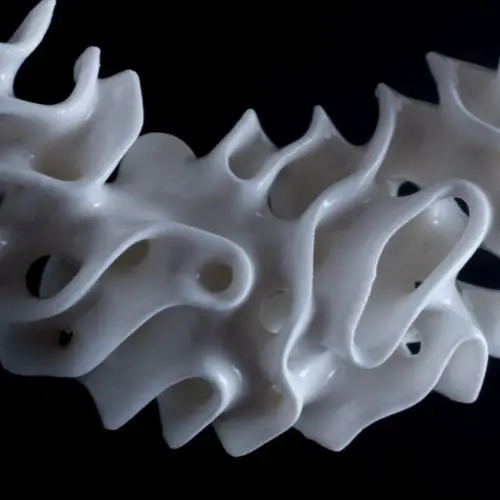
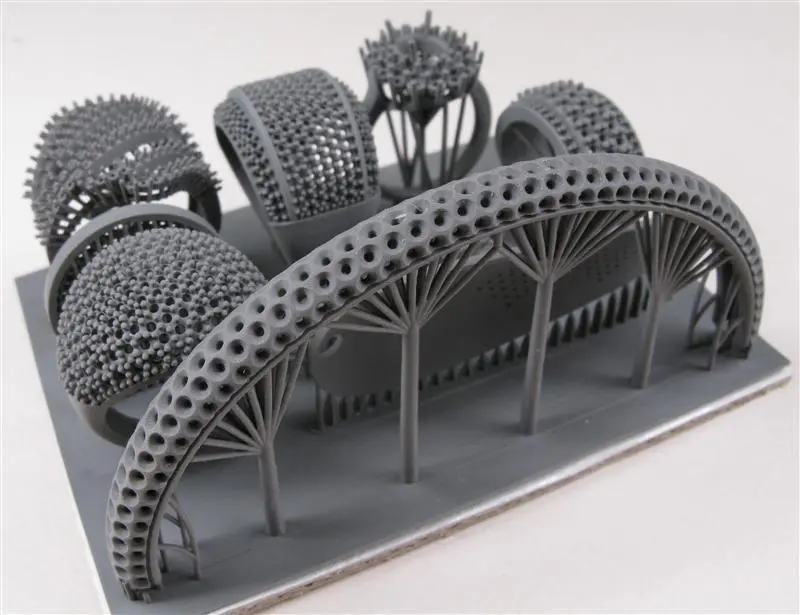
405nm DLP Standard Resin
405nm standard resin is specially formulated for DLP printers that use 405nm wavelength light sources, enabling exceptional detail and surface finish.
405nm Transparent Resin
This specialized photopolymer resin cures under 405nm wavelength light, enabling the creation of highly detailed 3D prints with brilliant clarity.
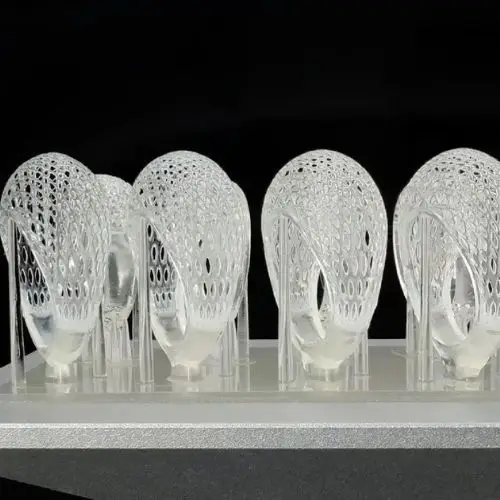