3D printing has revolutionized manufacturing, enabling new possibilities in design and production across industries. Among the most sophisticated technologies is Selective Laser Sintering (SLS), which uses lasers to fuse powdered materials into solid objects layer by layer. What makes SLS stand out? Its ability to print with a variety of materials offering exceptional strength, flexibility, and durability.
Choosing the right material for your application can be challenging. Whether you’re prototyping, manufacturing end-use parts, or working in the medical or aerospace industries, the material you select is crucial for the success of your project. Do you need a material that withstands high temperatures? or balances flexibility with strength?
This guide will explore the essential SLS 3D printing materials, detailing their properties, benefits, and ideal use cases. From nylon to metal powders, we’ll provide insights into how each material is transforming industries worldwide. By the end, you’ll have the knowledge to select the best SLS material for your next project.
What is SLS 3D Printing?
Selective Laser Sintering (SLS) is a leading 3D printing technology that uses lasers to fuse powdered materials into solid objects layer by layer. This process enables the creation of durable and complex parts. Here’s a breakdown of how it works:
The SLS Process
- Powder Bed Preparation: A thin layer of powder is spread on the build platform, typically nylon, metal, or a composite.
- Laser Sintering: A laser scans and sinters the powder particles according to the design.
- Layer-by-Layer Construction: Each layer is sintered and consolidated, building the part in 3D.
- Cooling and Removal: After printing, the part cools and is removed from the powder bed. Unused powder is recycled.
- Post-Processing: Includes cleaning, support removal, or surface finishing.
Key Features
- No Support Structures: Unlike other methods, SLS doesn’t require support structures for complex geometries.
- High-Resolution Prints: Offers excellent detail and surface finish.
- Material Versatility: Supports plastics, metals, and composites.
- Strength and Durability: Produces strong, durable parts ideal for industrial applications.
SLS vs Other 3D Printing Technologies
Feature | SLS | FDM | SLA |
---|---|---|---|
Material Range | Broad | Limited | Limited |
Support Structures | None Required | Required | Required |
Strength | High | Low | Moderate |
Print Resolution | High | Medium | Very High |
Cost | Higher | Lower | High |
Ideal Use Cases | Functional Parts | Prototypes | Intricate Models |
Why Choose SLS?
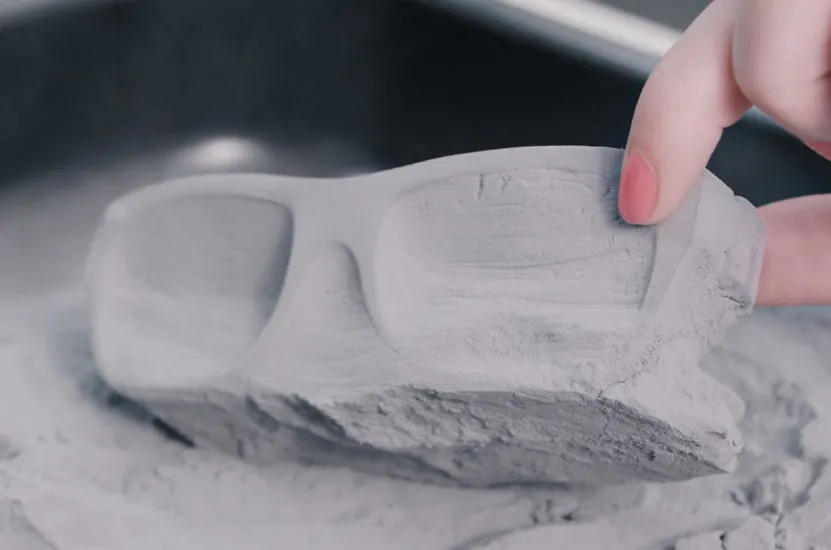
- Complex Geometries: Excels at printing intricate designs without support structures.
- Functional Prototyping: Produces durable, high-performance parts.
- Material Recycling: Reduces waste by reusing unsintered powder.
The Importance of Material Selection in SLS
Material selection significantly impacts the quality, durability, and functionality of SLS prints. Here’s why it matters:
- Material Properties:
- Mechanical Strength: Nylon offers flexibility and impact resistance, while stainless steel provides high tensile strength.
- Temperature Resistance: PEEK tolerates extreme heat.
- Flexibility vs. Rigidity: TPU for flexibility; glass-filled nylon for rigidity.
- Application-Specific Performance:
- Prototyping: Nylon for speed and affordability.
- High-Performance Parts: Aluminum or titanium for demanding environments.
- Medical: Titanium for biocompatible implants.
- Cost Considerations:
- Metal powders are expensive, while nylon is cost-effective.
- Surface Finish:
- Compare materials like nylon (smooth finish) with stainless steel (rough texture).
- Environmental Considerations:
- SLS reduces waste by reusing powder and provides sustainable bio-based materials.
Types of Materials Used in SLS
Thermoplastics
- Nylon (PA12):
- Strength, flexibility, and chemical resistance.
- Ideal for functional prototypes.
- Nylon 11 (PA11):
- Flexible, biodegradable, derived from castor oil.
- Suitable for environmental applications.
Metal Powders
- Stainless Steel:
- Corrosion resistance and high strength.
- Ideal for industrial and aerospace parts.
- Titanium:
- Lightweight, biocompatible.
- Used in aerospace and medical devices.
- Aluminum:
- Lightweight, cost-effective.
- Used in automotive and prototyping.
Composite Materials
- Glass-Filled Nylon:
- Enhanced stiffness and strength.
- Ideal for structural components.
- Carbon-Fiber Reinforced Nylon:
- High strength-to-weight ratio.
- Suitable for aerospace and automotive parts.
Key Considerations for Material Selection
- Strength and Durability.
- Heat Resistance.
- Flexibility.
- Surface Finish.
- Cost.
- Environmental Impact.
The Best SLS Materials for Specific Applications
Prototyping
- Nylon (PA12): Cost-effective, strong.
- Glass-Filled Nylon: Rigid and durable.
Aerospace and Automotive
- Carbon-Fiber Reinforced Nylon: Lightweight, high strength.
- Titanium: High performance and durability.
Medical and Healthcare
- Titanium: Biocompatible and corrosion-resistant.
- Nylon 12: Strength and flexibility.
Manufacturing and End-Use Parts
- Stainless Steel: Corrosion resistance, high strength.
- Nylon 12: Chemical resistance.
Consumer Products
- Nylon 12: Smooth finish for aesthetic appeal.
- Polycarbonate (PC): Impact resistance.
Advances in SLS Material Technology
- High-Performance Polymers:
- PEEK for extreme conditions.
- Metal-Based Composites:
- Carbon-fiber reinforced metals for lightweight strength.
- Sustainable Materials:
- Bio-based polymers and recycled plastics.
- Hybrid Materials:
- Combining properties for tailored solutions.
- Multimaterial Printing:
- Printing with multiple materials for complex designs.
Post-Processing of SLS Materials
- Cleaning:
- Air blasting, vibration tumblers, manual brushing.
- Surface Finishing:
- Sanding, polishing, media blasting.
- Heat Treatment:
- Annealing for strength.
- Coating:
- Painting, powder coating for aesthetics.
Sustainability in SLS
- Recyclable Materials:
- nylon reuse.
- Energy Efficiency:
- Reduced material waste.
- End-of-Life Considerations:
- Recycling and biodegradability.
The Future of SLS Materials
- Novel Materials:
- High-performance polymers, nanomaterials.
- Multi-Material Printing:
- Printing with multiple materials.
- Sustainable Developments:
- Bio-based and recycled materials.
- Customized Solutions:
- Tailored materials for specific applications.
This comprehensive guide provides a clear, concise, and SEO-friendly exploration of SLS 3D printing materials. It has been optimized for readability, keyword integration, and logical flow to enhance search engine performance while maintaining the depth and technical accuracy essential for professionals in the field.