The footwear industry is a dynamic and ever-evolving sector, constantly driven by innovation and the pursuit of perfection. From the earliest leather sandals to today’s technologically advanced sneakers, the quest to create the perfect shoe has been relentless. However, despite significant advancements, traditional shoe manufacturing still faces challenges such as inefficiency, high costs, and limited customization. Enter the game-changer: Digital Light Processing (DLP) 3D printing.
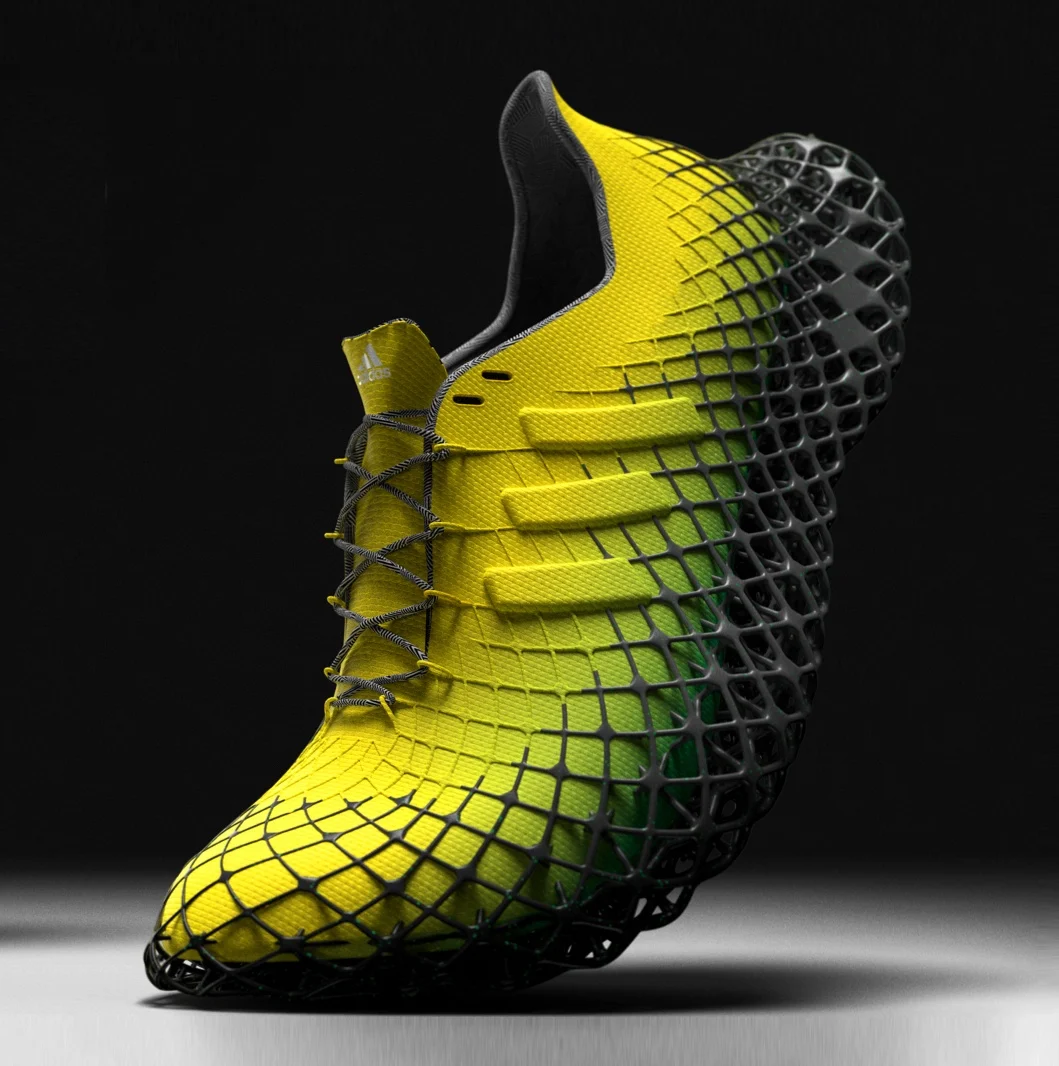
Imagine a world where shoes are not only custom-fitted to your feet but also produced quickly and sustainably. This is no longer a distant dream but a burgeoning reality, thanks to the revolutionary impact of DLP 3D printing on flexible shoe molds. This groundbreaking technology is poised to transform the footwear industry, offering unprecedented levels of design flexibility, efficiency, and sustainability.
In this comprehensive article, we will delve into the intricacies of DLP 3D printing, explore its role in creating flexible shoe molds, and examine how it stands to revolutionize the footwear industry. From understanding the basic principles of DLP technology to analyzing real-world applications and future trends, we aim to answer every question you might have about this exciting development. So, lace up your curiosity and step into the future of footwear with us.
Understanding DLP 3D Printing
Digital Light Processing (DLP) 3D printing is at the forefront of additive manufacturing technology, offering remarkable precision and efficiency. Whether you’re an industry veteran or a curious newcomer, understanding DLP’s inner workings is essential to appreciating its impact on modern manufacturing.
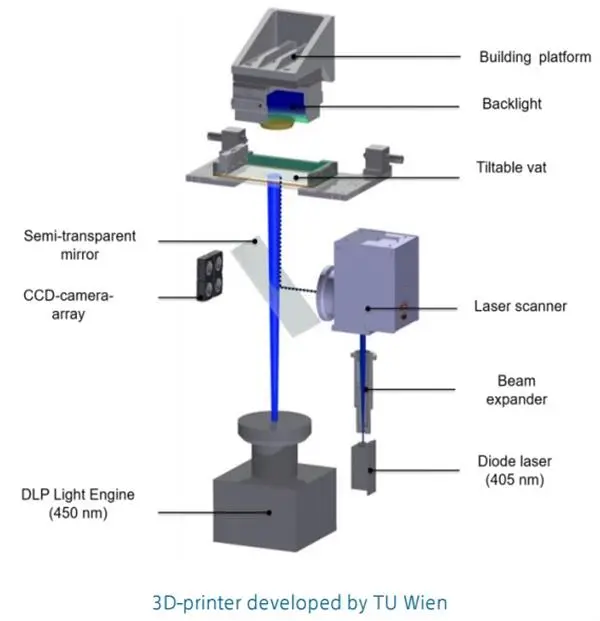
How DLP 3D Printing Works
At its core, DLP 3D printing uses a digital light projector to cure photopolymer resin layer by layer, creating highly detailed and accurate objects. Here’s a step-by-step breakdown of the process:
- Design Creation: The process begins with a digital 3D model, typically crafted using CAD software.
- Layer Slicing: The model is sliced into thin layers, which the printer will build sequentially.
- Projection and Curing: A digital light source projects an image of each layer onto the resin. The light cures the resin, solidifying it in the desired shape.
- Layer Building: The build platform moves, allowing a new layer of resin to be cured on top of the previous one.
- Post-Processing: Once printing is complete, the object is cleaned and may undergo additional curing to enhance its properties.
Materials Used in DLP 3D Printing
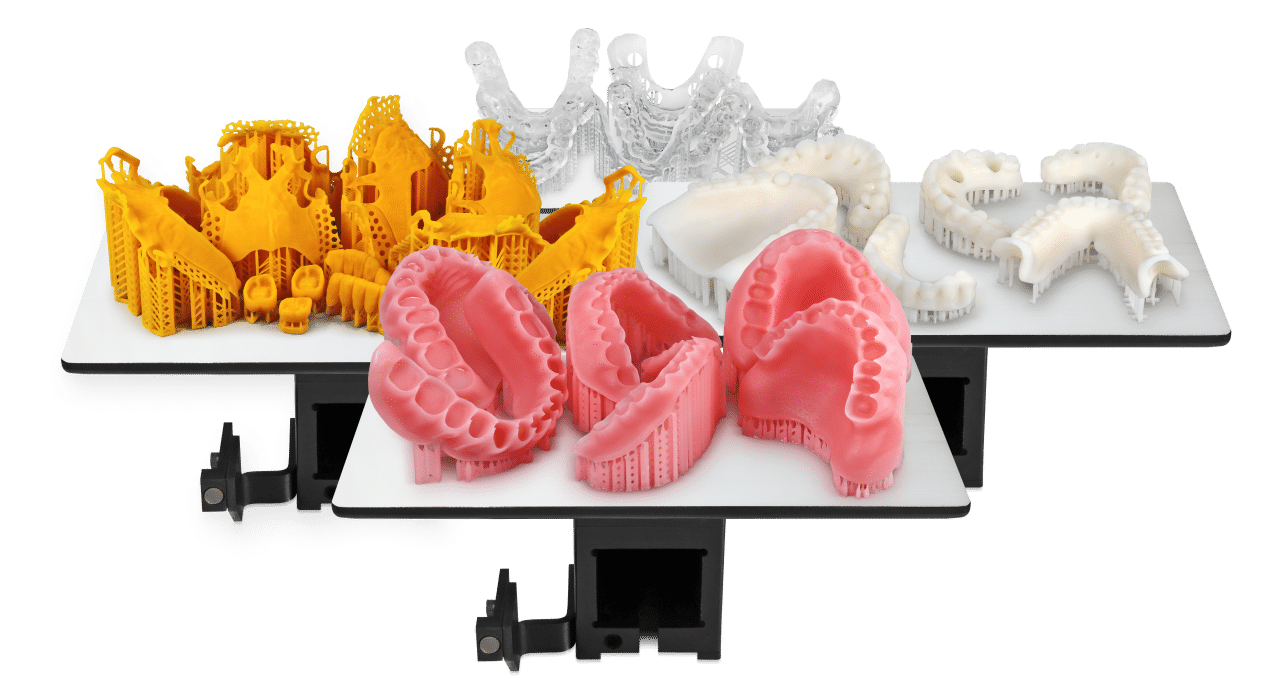
DLP printers use **photopolymer resins**, which are liquid plastics that harden under specific light wavelengths. These resins come in various formulations, each tailored for different applications:
- Standard Resins: Ideal for prototypes, offering good detail and smooth surfaces.
- Flexible Resins: Used for creating flexible parts like shoe molds.
- High-Temperature Resins: Suitable for parts that need to withstand higher temperatures.
- Biocompatible Resins: Used in medical applications, safe for human contact.
Resin Type | Characteristics | Applications |
Standard | Smooth finish, good detail | Prototypes, models |
Flexible | Elastic, durable | Shoe molds, wearable parts |
High-Temperature | Heat resistant, strong | Engine parts, industrial use |
Biocompatible | Safe for skin, medical-grade | Dental, medical devices |
Advantages of DLP Over Traditional Methods
DLP 3D printing stands out for several reasons:
- Speed: DLP can produce parts faster than other traditional methods, making it ideal for rapid prototyping.
- Precision: With high resolution and accuracy, DLP creates intricate designs effortlessly.
- Cost-Effectiveness: Reduced material waste and lower labor costs make DLP an economical choice.
- Versatility: Suitable for a wide range of materials and applications.
Comparison with Other 3D Printing Technologies
While DLP shares similarities with other 3D printing methods, it boasts unique advantages:
- SLA (Stereolithography): Similar to DLP but uses a laser to cure resin, generally slower and less efficient.
- FDM (Fused Deposition Modeling): Uses thermoplastic filaments, less precise, but more accessible.
Technology | Speed | Precision | Cost | Material Options |
DLP | Fast | High | Medium | Wide range |
SLA | Medium | High | Medium | Limited to resins |
FDM | Slow | Medium | Low | Wide range |
DLP 3D printing is a transformative technology, offering unmatched speed, precision, and versatility. Its ability to create detailed and flexible parts opens new possibilities across various industries, particularly in footwear manufacturing. By understanding its workings and benefits, businesses can harness its potential to innovate and lead in their respective fields. Whether you’re looking to streamline production or explore creative design, DLP 3D printing offers a promising path forward.
Flexible Shoe Molds: A Game Changer
In the world of footwear manufacturing, the pursuit of innovation is relentless. Traditional shoe molds, often rigid and time-consuming to produce, have long been a bottleneck in the design and production process. Enter **flexible shoe molds**, a revolutionary advancement powered by DLP 3D printing that is transforming how shoes are crafted.
What are Flexible Shoe Molds?
Flexible shoe molds are adaptive molds used to create footwear with enhanced comfort, fit, and style. Unlike traditional molds, which are typically made from metal or hard plastic, flexible molds are crafted from elastic materials that allow for greater adaptability and customization.
Key Characteristics
- Elasticity: Made from flexible resins, these molds can bend and stretch without losing shape.
- Customization: Easily adjusted to accommodate various designs and sizes.
- Durability: Resilient materials ensure long-lasting use.
Benefits Over Rigid Molds
The advantages of flexible shoe molds extend far beyond mere flexibility. Here are some of the core benefits:
- Improved Fit and Comfort: Molds can be tailored to individual foot shapes, enhancing comfort and reducing the risk of blisters or discomfort.
- Design Flexibility: Designers can experiment with complex shapes and patterns that were previously impossible with rigid molds.
- Efficient Production: Faster mold creation and easy modifications reduce production time and costs.
- Sustainability: Less waste generated during production, aligning with eco-friendly initiatives.
Role of DLP in Creating Flexible Molds
DLP 3D printing plays a pivotal role in the creation of flexible shoe molds. Here’s how:
- Precision: The high resolution of DLP printers allows for meticulous detail in mold creation, ensuring a perfect fit.
- Speed: Rapid curing times mean molds can be produced quickly, accelerating the design-to-production timeline.
- Material Versatility: DLP’s ability to work with various flexible resins makes it ideal for creating adaptive molds.
Feature | Traditional Molds | Flexible Molds (DLP) |
Material Flexibility | Low | High |
Customization | Limited | Extensive |
Production Speed | Slow | Fast |
Waste | High | Low |
Impact on Design Flexibility
Flexible molds open up a world of possibilities for designers, enabling them to push the boundaries of creativity:
- Complex Patterns: Intricate designs and textures become feasible, allowing for unique and personalized footwear.
- Adaptive Features: Elements like adjustable arch support or custom cushioning can be integrated directly into the mold.
Real-World Applications and Success Stories
Several leading footwear brands have already embraced flexible molds, demonstrating their potential:
- Nike’s Customizable Sneakers: Utilizing flexible molds to offer personalized fit and style.
- Adidas’ Eco-Friendly Line: Reducing waste and improving efficiency with DLP-produced molds.
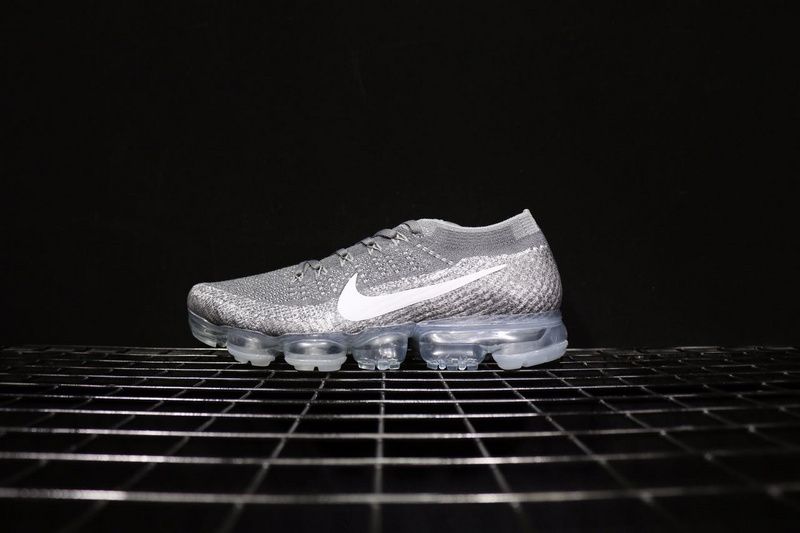
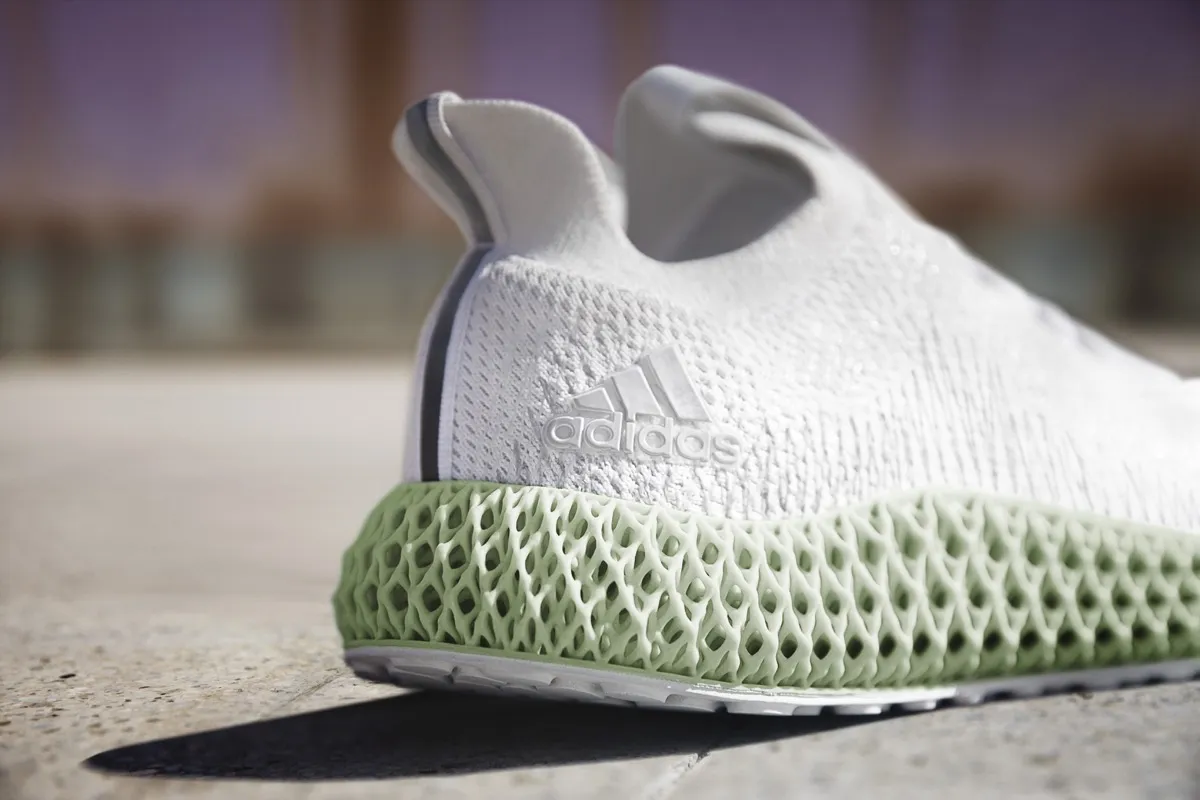
Flexible shoe molds represent a significant leap forward in footwear manufacturing, combining the adaptability of modern materials with the precision of DLP 3D printing. By embracing this technology, manufacturers can offer unparalleled customization, comfort, and efficiency, making it a true game-changer in the industry. As the demand for personalized and sustainable products grows, flexible molds stand poised to lead the charge into a new era of footwear innovation.
Benefits for the Footwear Industry
The integration of DLP 3D printing and flexible shoe molds is reshaping the footwear industry, offering numerous advantages that cater to both manufacturers and consumers. This technological advancement is not just a trend but a significant leap towards a more efficient, sustainable, and personalized footwear experience.
Customization and Personalization
One of the most compelling benefits of DLP 3D printing in footwear is the ability to offer **mass customization**. This means creating shoes tailored to individual preferences and needs, without the constraints of traditional manufacturing.
Key Benefits
- Personalized Fit: Custom molds ensure a perfect fit for every foot, enhancing comfort and performance.
- Unique Designs: Consumers can select colors, patterns, and features, creating truly one-of-a-kind footwear.
- Adaptive Features: Incorporate personalized arch support or specific cushioning preferences.
Sustainability and Waste Reduction
In an age where sustainability is paramount, DLP 3D printing offers a greener alternative to conventional manufacturing processes:
- Reduced Material Waste: Precision printing minimizes excess material usage.
- Eco-Friendly Materials: Use of recyclable and biodegradable resins.
- Energy Efficiency: Lower energy consumption compared to traditional manufacturing methods.
Environmental Impact
Aspect | Traditional Methods | DLP 3D Printing |
Material Waste | High | Low |
Energy Use | High | Moderate |
Emissions | Significant | Reduced |
Efficiency and Speed
Speed and efficiency are crucial in the competitive footwear market, and DLP 3D printing delivers on both fronts:
- Rapid Prototyping: Quickly test and iterate designs without lengthy delays.
- Shortened Production Cycles: Faster mold creation leads to quicker product launches.
- Reduced Time-to-Market: Stay ahead of trends by swiftly responding to consumer demands.
Efficiency Gains
- Faster Turnaround: Significantly reduce the time from design to finished product.
- On-Demand Production: Manufacture only what is needed, reducing overproduction and inventory costs.
Industry Success Stories
Several brands have already leveraged these benefits to gain a competitive edge:
- Under Armour’s SpeedForm Line: Utilizing DLP technology for rapid product development and customized fit.
- New Balance’s 3D-Printed Insoles: Offering personalized comfort and performance enhancements.
The benefits of integrating DLP 3D printing and flexible shoe molds into footwear manufacturing are profound. From enabling unprecedented levels of customization and sustainability to enhancing efficiency and speed, this technology is transforming the industry landscape. By embracing these innovations, brands can meet the evolving demands of consumers while maintaining a commitment to environmental responsibility. As the footwear industry continues to evolve, those who adopt these technologies will undoubtedly lead the way in creating the shoes of tomorrow.
Challenges and Considerations
While the integration of DLP 3D printing and flexible shoe molds offers numerous advantages, it’s not without its challenges. As with any groundbreaking technology, there are hurdles to overcome and factors to consider to ensure successful implementation in the footwear industry.
Technical Challenges
The technical complexities of DLP 3D printing can pose significant challenges:
- Material Limitations: While flexible resins are available, they may not yet match the durability and performance of traditional materials.
- Post-Processing: Printed molds often require additional curing and finishing, which can add time and complexity.
- Printer Maintenance: DLP printers require regular maintenance and calibration to ensure consistent quality.
Overcoming Technical Hurdles
- Continuous Research and Development: Investing in R&D to improve material properties and printing processes.
- Advanced Post-Processing: Developing efficient post-processing techniques to streamline production.
- Regular Maintenance Protocols: Implementing rigorous maintenance schedules to keep printers in optimal condition.
Cost Considerations
Despite the potential for cost savings in the long run, the initial investment in DLP 3D printing technology can be substantial:
- High Initial Investment: Purchasing DLP printers and setting up the required infrastructure can be expensive.
- Material Costs: High-quality resins suitable for footwear molds can be costlier than traditional materials.
- Training and Expertise: Skilled personnel are required to operate and maintain the technology, adding to labor costs.
Mitigating Cost Impacts
- Gradual Integration: Phasing the adoption of DLP technology to spread out costs over time.
- Bulk Material Purchases: Buying resins in bulk to reduce per-unit costs.
- Training Programs: Investing in comprehensive training programs to build in-house expertise.
Design and Implementation
Transitioning from traditional manufacturing to DLP 3D printing requires careful planning and execution:
- Design Adaptation: Existing designs may need to be reworked to be compatible with 3D printing.
- Quality Control: Ensuring consistent quality across printed molds can be challenging.
- Scalability: Scaling up production while maintaining efficiency and quality is crucial.
Strategic Planning for Implementation
- Pilot Projects: Starting with pilot projects to refine processes and address potential issues.
- Quality Assurance Protocols: Implementing robust quality control measures to maintain high standards.
- Scalable Solutions: Developing scalable production strategies to facilitate growth.
Regulatory and Compliance Issues
Navigating the regulatory landscape is essential for successful implementation:
- Material Safety: Ensuring that all materials used are compliant with safety regulations.
- Product Standards: Meeting industry standards for quality and performance.
- Environmental Regulations: Adhering to environmental regulations regarding waste disposal and emissions.
Ensuring Compliance
- Regular Audits: Conducting regular audits to ensure compliance with all relevant regulations.
- Certification Programs: Obtaining certifications to demonstrate adherence to industry standards.
- Sustainable Practices: Implementing sustainable practices to meet environmental regulations.
Market Acceptance
Gaining market acceptance for 3D-printed footwear can be a gradual process:
- Consumer Perception: Educating consumers about the benefits of 3D-printed footwear to overcome skepticism.
- Market Positioning: Positioning 3D-printed footwear as a premium, customizable option.
- Competitive Landscape: Competing with established brands that use traditional manufacturing methods.
Building Market Acceptance
- Marketing Campaigns: Running campaigns to highlight the unique benefits of 3D-printed footwear.
- Consumer Education: Providing information and demonstrations to educate consumers.
- Strategic Partnerships: Partnering with influencers and athletes to build credibility.
While the integration of DLP 3D printing and flexible shoe molds presents numerous opportunities, it’s essential to navigate the associated challenges thoughtfully. By addressing technical, cost, design, regulatory, and market considerations, the footwear industry can harness the full potential of this transformative technology. With strategic planning and continuous innovation, the path to revolutionizing footwear manufacturing is both achievable and promising.
Future Trends in Footwear Manufacturing
As the footwear industry continues to evolve, the integration of DLP 3D printing and flexible shoe molds is poised to lead a wave of innovation. Exploring future trends provides insight into how these technologies will shape the industry landscape.
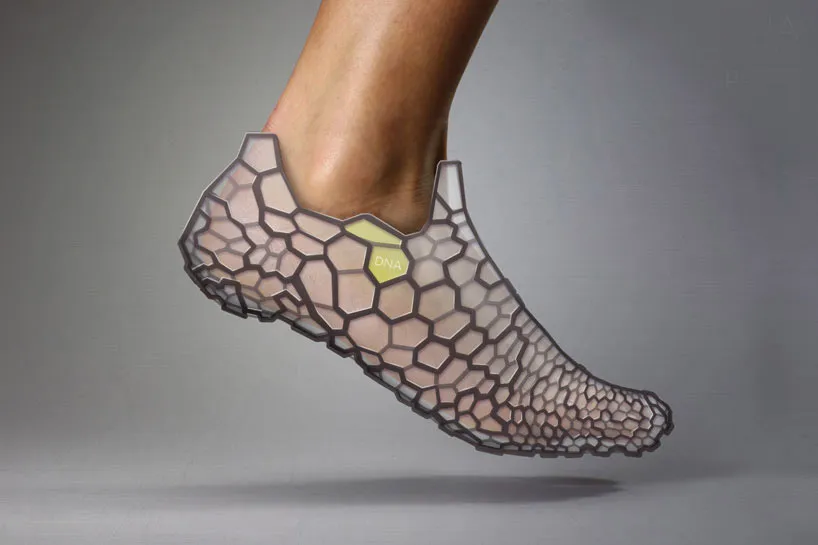
Advanced Customization
The future of footwear lies in hyper-personalization, where consumers can design every aspect of their shoes:
- 3D Scanning: Using advanced scanning technology to capture precise foot measurements.
- AI-Driven Design: Leveraging AI to suggest design options based on personal preferences and past purchases.
- Interactive Design Platforms: Offering consumers intuitive tools to create their own designs.
Potential Developments
- Virtual Fitting Rooms: Allowing consumers to visualize and adjust designs in real-time.
- Customization APIs: Integrating with e-commerce platforms for seamless design experiences.
Sustainable Innovations
Sustainability will continue to drive innovation in footwear manufacturing:
- Biodegradable Materials: Development of new resins that decompose naturally without harming the environment.
- Closed-Loop Systems: Implementing systems that recycle used shoes into new products.
- Energy-Efficient Printing: Enhancing printer designs to further reduce energy consumption.
Environmental Initiatives
- Carbon Neutral Goals: Brands aiming for carbon neutrality in their production processes.
- Green Certifications: Pursuing certifications to validate sustainable practices.
Integration with Smart Technology
The merging of footwear with smart technology offers exciting possibilities:
- Smart Insoles: Embedding sensors to track movement and provide real-time feedback.
- Health Monitoring: Using data to monitor foot health and recommend corrective measures.
- Connectivity: Integrating with smartphones for a connected experience.
Upcoming Innovations
- Augmented Reality Features: Using AR to customize and enhance the user experience.
- IoT Integration: Connecting shoes to the Internet of Things for advanced functionalities.
Expansion into New Markets
The adoption of innovative technologies can open doors to new markets:
- Sports and Performance: Creating specialized footwear for athletes with enhanced performance features.
- Medical Applications: Developing orthopedic and therapeutic shoes tailored to individual health needs.
- Fashion Forward Designs: Collaborating with fashion designers for avant-garde creations.
Market Opportunities
- Elderly and Disabled: Designing shoes that address specific mobility challenges.
- Youth Markets: Creating trend-driven designs for younger consumers.
Collaborative Ecosystems
Collaboration will be key to driving innovation in the footwear industry:
- Cross-Industry Partnerships: Partnering with tech companies, material scientists, and environmental organizations.
- Open Innovation Platforms: Encouraging co-creation with consumers and designers.
- Shared Resources: Pooling resources for research and development to reduce costs and accelerate innovation.
Collaborative Models
- Innovation Hubs: Establishing centers focused on developing cutting-edge technologies.
- Crowdsourcing Initiatives: Engaging consumers in the design and development process.
Conclusion
The future of footwear manufacturing is bright, driven by technological advancements and a commitment to sustainability and personalization. As DLP 3D printing and flexible shoe molds continue to evolve, they will enable unprecedented levels of customization, efficiency, and connectivity. By embracing these trends, the footwear industry can not only meet the demands of today’s consumers but also lead the charge into a more innovative and sustainable future.