3D printing, particularly Stereolithography (SLA) technology, has been making significant strides in various industries. SLA is renowned for its ability to fabricate highly precise and detailed parts. However, when it comes to applications demanding flexibility and elasticity, flexible resins for SLA 3D printing come into play. These resins offer a unique combination of properties, enabling the creation of parts that can bend, stretch, and adapt, thereby opening up new possibilities in design and manufacturing.
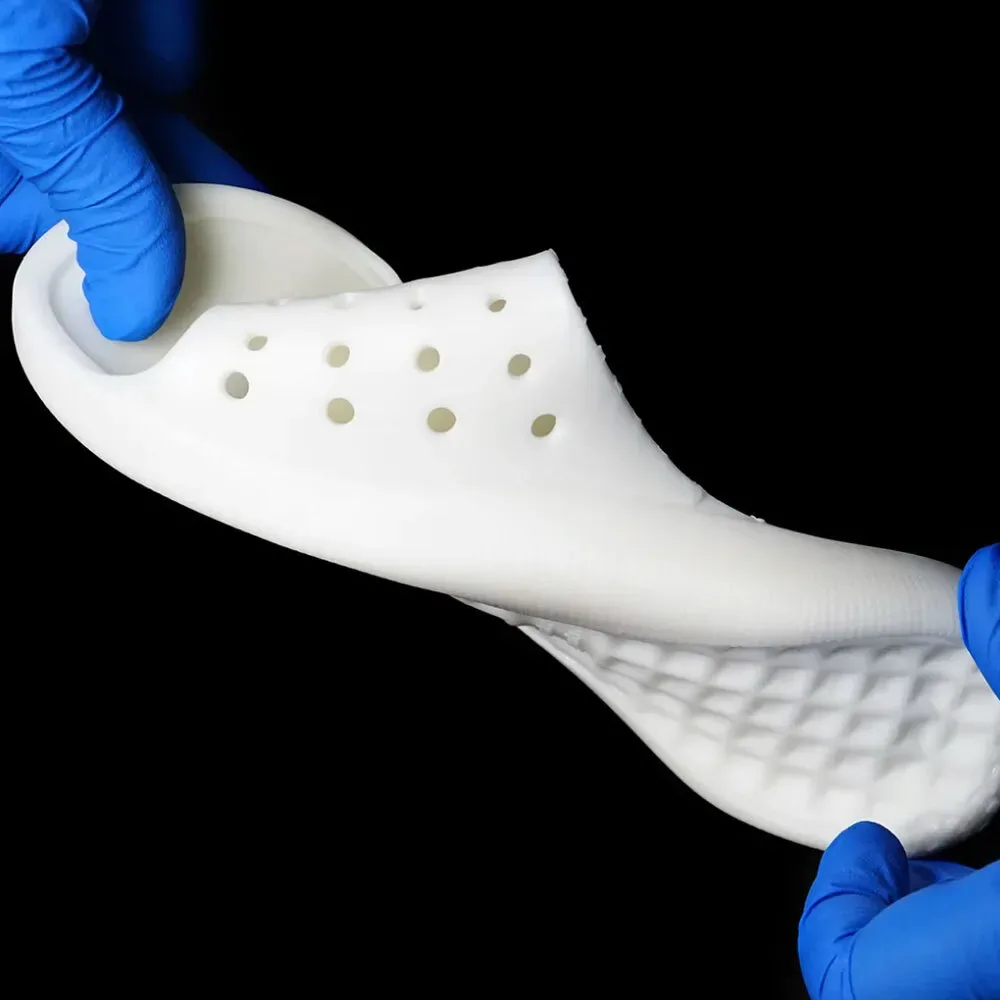
This guide aims to provide a detailed understanding of flexible resins for SLA 3D printing. It will cover their characteristics, applications, advantages, challenges, and how to effectively utilize them in the printing process. By the end, readers will be equipped with the knowledge necessary to incorporate these materials into their 3D printing workflows.
What Are Flexible Resins?
Definition and Characteristics
Flexible resins are photopolymer materials specifically formulated for SLA and other resin-based 3D printing technologies. Unlike standard resins that cure into rigid and brittle structures, flexible resins cure to exhibit rubber-like properties. Key characteristics include elasticity, allowing them to bend, stretch, and compress without fracturing; high tear resistance, enabling them to withstand mechanical stress; and a soft, rubber-like texture, making them suitable for ergonomic designs.
Comparison with Other 3D Printing Resins
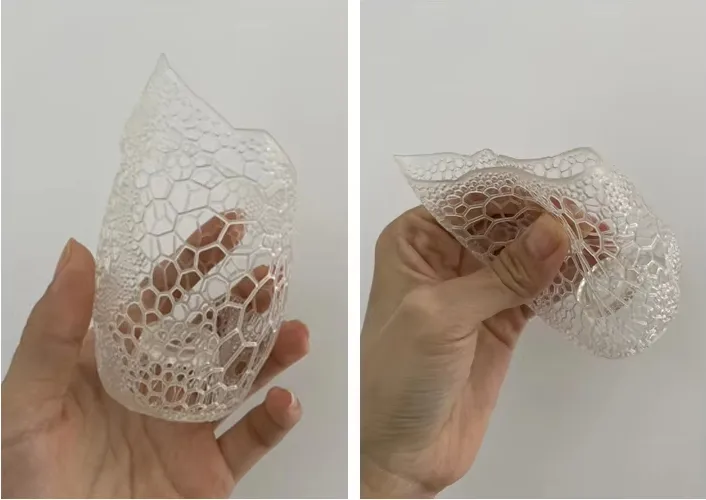
To better understand flexible resins, a comparison with other common SLA resins is instructive. The following table summarizes the differences:
Property | Standard Resin | Tough Resin | Flexible Resin |
Texture | Hard and brittle | Firm but slightly pliable | Soft and rubber-like |
Elasticity | None | Moderate | High |
Durability | Prone to cracking | Good for functional parts | Excellent for strain and impact |
Applications | Visual prototypes | Functional prototypes | Wearables, gaskets, seals |
Cost | Affordable | Moderate | Slightly higher |
As shown, flexible resins stand out with their soft and rubber-like texture, high elasticity, and excellent durability under strain and impact. They are commonly used in applications such as wearables, gaskets, and seals, while standard resins are preferred for visual prototypes and tough resins for more durable functional parts.
Unique Properties
Flexible resins possess several unique properties. They are rated on the Shore hardness scale, which indicates their resistance to indentation. Lower Shore values correspond to softer materials, while higher values denote firmer yet elastic substances. Elongation at break measures their stretchability before rupture, typically ranging from 50% to over 200%. Their tear strength allows them to endure repeated mechanical stresses, making them ideal for functional parts subject to bending or stretching. Additionally, their rubber-like feel provides a natural grip and comfort in wearable or ergonomic products.
Applications of Flexible Resins
Consumer Products
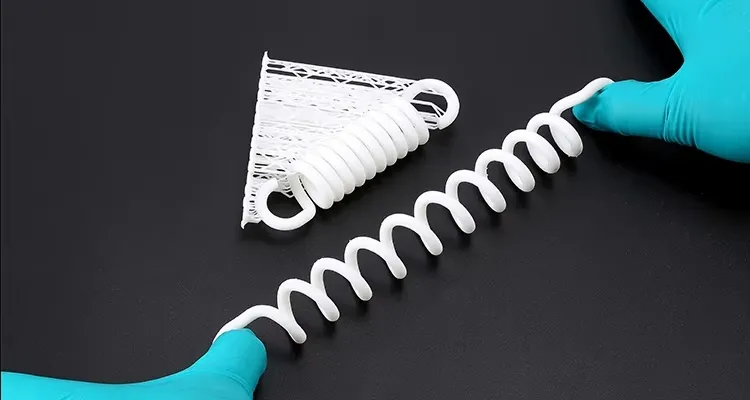
In the consumer product realm, flexible resins find extensive use. They are utilized in the production of wearables like wristbands and phone cases, providing a comfortable fit and protection. Ergonomic grips for tools and handles enhance user experience. Custom shoe soles can also be fabricated, offering better cushioning and flexibility.
Medical Prototypes
In the medical field, flexible resins play a crucial role. Orthopedic models, customized prosthetics, and soft molds for surgical simulations can be created with these resins. Their ability to mimic the properties of soft tissues makes them invaluable in medical research and device development.
Industrial and Automotive Uses
For industrial and automotive applications, flexible resins are employed in shock-absorbing seals and gaskets, flexible tubing and connectors, and vibration-dampening components. These parts need to withstand mechanical stress and maintain their functionality in harsh environments.
Creative Projects
Artists and designers leverage flexible resins in creative projects. They can produce artistic sculptures with bendable parts, functional jewelry like rings and bracelets, and props and cosplay elements that require flexibility. The smooth surface finish of these resins also adds to the aesthetic appeal of the creations.
Advantages and Challenges of Using Flexible Resins
Advantages
Flexible resins offer several benefits. They exhibit high durability, resisting wear and tear even under repeated stress. SLA technology ensures precise printing of detailed parts, maintaining the integrity of the soft material. Their versatility allows them to be used in a wide range of applications, from functional to artistic. Additionally, properties such as Shore hardness and color can often be customized to meet specific requirements.
Challenges
Despite their advantages, flexible resins present some challenges. They are generally more expensive than standard resins. While flexible, they may not possess the same level of strength or impact resistance as tough resins. Not all SLA printers are optimized for these resins, necessitating careful calibration of settings. Post-processing can also be tricky, as removing supports without damaging the soft material requires precision and care.
How Does SLA 3D Printing Work with Flexible Resins?
SLA 3D Printing Process Overview
SLA 3D printing involves curing liquid photopolymer resin layer by layer using a UV laser or projector. First, a 3D model file in STL or OBJ format is prepared and sliced using appropriate software. The printer’s resin vat is filled with the flexible resin, and the laser or light source projects the cross-section of the model onto the resin, hardening it. After each layer is cured, the build platform moves slightly to allow the next layer to be processed. Once the printing is complete, the part undergoes post-processing steps including washing in isopropyl alcohol to remove uncured resin, curing under UV light to enhance strength, and careful removal of supports.
Why SLA is Suitable for Flexible Resins
SLA technology is well-suited for flexible resins due to its high precision. It can accurately reproduce the soft, rubber-like textures of the resins with fine layer resolutions, resulting in smooth surfaces and intricate details. The material versatility of SLA printers allows for the use of a wide variety of resins, including flexible ones. The controlled curing process ensures the proper formation of each layer, maintaining the mechanical properties of the flexible resins. Moreover, SLA printing enables the creation of complex geometries, which is essential for many flexible applications.
Factors to Consider When Printing with SLA Flexible Resins
When using SLA printers with flexible resins, several factors need to be considered. Printer compatibility is crucial, as not all printers can handle the viscosity and curing requirements of these resins. Using a finer layer height, such as 50 microns, can improve surface quality. Post-processing requirements, including careful support removal and proper curing, must be adhered to. Additionally, proper storage and handling of the resins are necessary, as they are sensitive to light and heat.
Key Features and Benefits of Flexible Resins
Key Features
The elasticity of flexible resins allows parts to deform and return to their original shape, making them suitable for applications requiring repeated stress resistance. They are available in a range of Shore hardness levels, enabling customization for different applications. Their tear and impact resistance ensure durability in functional parts. The smooth surface finish produced by SLA printing reduces the need for additional finishing work. They also offer a wide variety of color and transparency options, facilitating creative and aesthetic designs.
Benefits
Flexible resins’ versatility enables their use in diverse industries, such as wearables, automotive, medical, and creative fields. They can produce functional and durable parts that can absorb shocks and vibrations and withstand bending and stretching. In ergonomic designs, their rubber-like feel provides comfort and usability. The combination of SLA technology and flexible resins allows for the creation of highly detailed and complex geometries. The lightweight nature of the parts makes them ideal for portable and wearable applications. Their aesthetic appeal, thanks to the smooth surface finish, is beneficial in applications where appearance is important.
Choosing the Right Flexible Resin for Your Project
Key Factors to Consider
When selecting a flexible resin, several factors are critical. Shore hardness determines the flexibility and firmness of the printed part, with different applications requiring specific ranges. Tear strength and elongation at break are important for durability under stress. Printer compatibility must be ensured, considering the resin’s viscosity and curing requirements. Color and transparency options should match the design intent. For medical and skin-contact applications, biocompatibility is essential. Cost is also a factor, as flexible resins tend to be more expensive, so it is necessary to balance the budget with project requirements.
Popular Flexible Resin Brands and Products
There are several popular brands of flexible resins available. The following table presents some of them:
Brand | Product | Features | Best For |
Formlabs | Elastic Resin 50A | Very soft, high elongation | Soft touch parts, medical prototypes |
Formlabs | Flexible Resin 80A | Firmer, durable and impact-resistant | Ergonomic grips, seals, functional prototypes |
Anycubic | Flexible UV Resin | Affordable, good for general flexible projects | Consumer goods, creative projects |
Siraya Tech | Tenacious Flexible Resin | Tough and flexible, great tear resistance | Functional parts, industrial prototypes |
Photocentric | UV Flexible Resin | High elongation, smooth finish | Wearable devices, artistic applications |
It is advisable to refer to the resin’s datasheet for specific performance metrics and conduct tests to find the most suitable option.
Testing and Evaluation Process
To determine the right flexible resin for a project, a systematic process can be followed. First, clearly define the project requirements, including the desired level of flexibility, durability, and any specific features like biocompatibility or color. Obtain small samples of different resins and print test parts to evaluate Shore hardness, tear strength, and surface finish. Experiment with printer settings such as exposure time, layer height, and support structures to optimize print quality. Perform stress tests on the printed parts to assess their behavior under real-world conditions.
Printing with Flexible Resins
Printer Compatibility and Settings
Before printing with flexible resins, it is essential to confirm printer compatibility. The resin tank should be made of a durable material, preferably with a high-quality FEP film to prevent sticking. The printer’s laser power or exposure source may need adjustment, as flexible resins often require slightly longer curing times per layer. The build platform should be clean, level, and textured to ensure proper adhesion. Recommended settings include using a smaller layer height for better resolution and slower print speeds to allow for even curing. Support structures should be carefully designed, with denser supports for overhangs and proper placement to avoid damaging the part during removal.
Best Practices
To achieve optimal results when printing with flexible resins, several best practices should be followed. Agitate the resin thoroughly before use to ensure consistent properties. Orient the model to minimize stress during printing and facilitate proper support placement. Keep the build plate clean and leveled using isopropyl alcohol. Utilize resin-specific slicer profiles provided by manufacturers, if available. Conduct small test prints before starting a full-scale production to identify and resolve potential issues.
Common Challenges and Troubleshooting
Printing with flexible resins may encounter several challenges. The following table lists common problems, their causes, and solutions:
Problem | Cause | Solution |
Poor adhesion to build plate | Low initial exposure or unclean build surface | Increase base layer exposure and clean plate |
Warping or deformation during print | Uneven curing or improper supports | Adjust exposure settings and add more supports |
Supports damaging flexible parts | Overly dense or poorly placed supports | Reduce support density and reposition supports |
Resin not curing properly | Incorrect exposure settings | Use manufacturer-recommended exposure times |
Print failures at higher layers | Lift speed too fast or peeling force too high | Reduce peel speed and lift height |
By addressing these issues promptly, the printing process can be optimized.
Post-Processing Flexible Resin Prints
Importance of Post-Processing
Post-processing is vital for flexible resin prints as it ensures the final part has the desired properties. Cleaning removes uncured resin residues that could affect flexibility and surface quality. Curing solidifies the material’s properties, enhancing its strength and durability. Support removal must be done carefully to avoid damaging the soft part. Finishing touches can improve the part’s appearance and functionality.
Post-Processing Steps
After printing, the part should be cleaned in an isopropyl alcohol bath for 2 – 5 minutes, gently agitated and using a soft brush for detailed areas. Rinse with fresh IPA to remove any remaining resin. Allow the part to air dry or use compressed air to speed up the process, ensuring it is completely dry before curing. Cure the part under UV light for the recommended time, usually 10 – 20 minutes at 405 nm, rotating it periodically for even exposure. When removing supports, pre-soften them with warm water or a heat gun, use precision tools like flush cutters or tweezers, and cut close to the surface. Sand any remaining support marks with fine-grit sandpaper. For finishing, options include painting with flexible paints, sanding and polishing edges, and using flexible adhesives for assembly or adding protective coatings.
Common Mistakes to Avoid
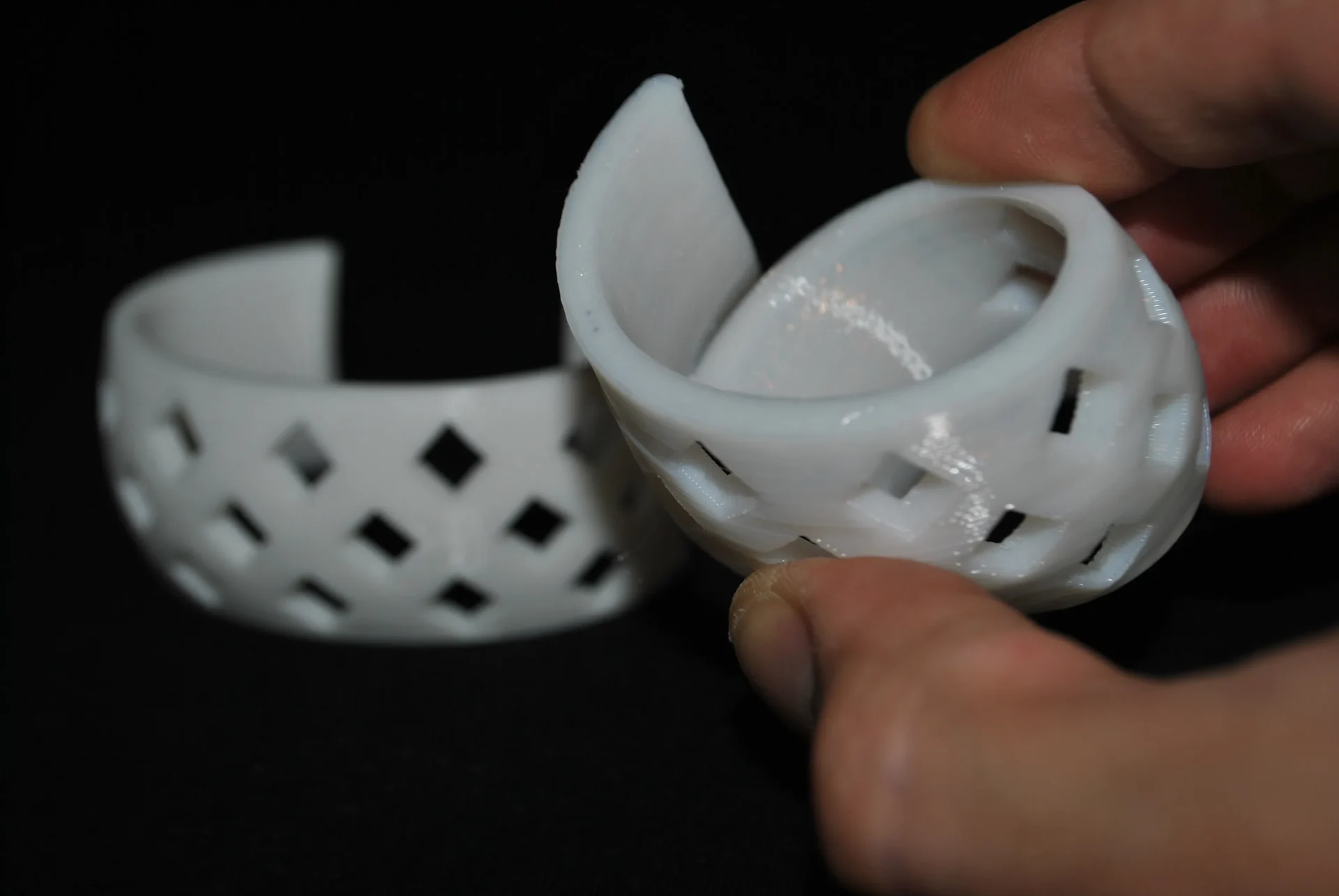
Avoid over-soaking the part in IPA, as it can weaken or deform the material. Follow the manufacturer’s recommended curing times to prevent over-curing and brittleness. Remove supports gently to avoid tearing or surface damage. Do not skip the drying step, as residual IPA can interfere with curing.
Comparing Flexible Resins with Other Flexible Materials
Flexible Resins vs. Flexible Filaments (TPU/TPE)
Flexible resins used in SLA printing differ from flexible filaments like TPU and TPE used in FDM printing. The following table highlights the differences:
Property/Feature | Flexible Resins (SLA) | TPU/TPE (FDM) |
Printing Technology | SLA (Resin-based, laser curing) | FDM (Filament extrusion) |
Precision and Detail | Ultra-high precision, smooth surfaces | Moderate precision, visible layer lines |
Flexibility | Elastic with customizable Shore hardness | Highly flexible, more rubber-like |
Durability | Good tear resistance, suitable for stress | Excellent impact and wear resistance |
Applications | Prototypes, functional parts, artistic | Functional parts, high-stress applications |
Cost | Higher (resin and SLA printer required) | Lower (affordable filament and FDM printer) |
Ease of Use | Requires more skill and post-processing | Easier for beginners, minimal post-processing |
Surface Finish | Smooth and professional | Rougher, visible extrusion lines |
Material Properties | Customizable Shore hardness, biocompatible options | Wider range of stiffness and flexibility |
Advantages of Each Material
Flexible resins have advantages in precision, customizable Shore hardness, aesthetic appeal, and the ability to create complex geometries. They are ideal for applications such as wearable devices, medical models, and artistic projects. TPU/TPE filaments offer cost-effective printing, greater impact resistance, a simpler workflow with minimal post-processing, and a wider range of material flexibility and stiffness options. They are suitable for industrial parts like seals, gaskets, and shock absorbers, as well as durable consumer goods.
When to Choose Each Material
Choose flexible resins when high precision, smooth finishes, customizable flexibility, and complex geometries are required. TPU/TPE is a better option when durability, impact resistance, cost-effectiveness, and simplicity are prioritized. Consider the specific requirements of the project, such as the need for fine details, surface quality, and mechanical properties, to make the appropriate choice.
Future Trends and Innovations in Flexible Resins
Material Property Advancements
Manufacturers are focusing on improving the performance of flexible resins. This includes enhancing durability and tear resistance through the addition of additives, making them more suitable for industrial applications. Greater customizability in Shore hardness is being developed, with the potential for on-the-fly adjustment within a single part. Temperature and chemical resistance are also being improved, expanding their use in extreme environments and medical/industrial applications.
Biocompatible and Eco-Friendly Options
The future of flexible resins will see the development of more biocompatible options for medical use, meeting strict standards for direct skin contact and implantation. Eco-friendly alternatives, such as plant-based or biodegradable resins, are emerging to reduce the environmental impact of 3D printing. These resins may become recyclable and compostable, promoting sustainability in manufacturing.
Smarter and Adaptive Resins
Self-healing resins are being integrated into flexible resin formulations, allowing printed parts to repair small cracks or tears autonomously. Shape memory resins are being researched, enabling parts to change shape and return to their original form under specific stimuli. Responsive materials that react to external factors like pressure, temperature, and humidity are also being explored, opening up new possibilities in design and functionality.
Enhanced Printing Technologies
SLA printing with flexible resins will benefit from faster printing speeds, narrowing the gap with FDM. Multi-material printing capabilities will allow for the creation of single objects with both rigid and flexible parts. AI-optimized slicing software will automatically improve support structures, exposure settings, and model orientation, reducing print failures and increasing efficiency.
Expanding Applications
Flexible resins will find increased use in various industries. In healthcare, they will be used in customized prosthetics, implants, and surgical models. The automotive and aerospace sectors will utilize them in durable seals, lightweight components, and heat-resistant parts. Consumer electronics and goods will incorporate them in ergonomic grips and shock-absorbing cases. Soft robotics will rely on them for flexible joints and sensors. Fashion and footwear will use them in customized soles and wearable art.
Sustainability and Circular Design
The future will see the implementation of resin recycling programs and closed-loop systems to reduce waste. Lifecycle tracking of flexible resin parts using QR codes or RFID tags will also become more common, promoting a circular economy in 3D printing.
Conclusion
Flexible resins for SLA 3D printing offer unique opportunities in design and manufacturing. Understanding their properties, applications, advantages, challenges, and how to work with them is essential for maximizing their potential. As technology continues to evolve, the future of flexible resins holds great promise, with advancements in materials, printing technologies, and expanding applications across industries. By staying informed and adapting to these changes, 3D printing practitioners can leverage flexible resins to create innovative and functional products.