In a world where technological advancement occurs at lighting speed, 3D printing has emerged as the phoenix of innovation, transforming ideas into tangible realities. Whether it’s the construction of intricate architectural models or the mechanism of building delicate medical instruments, 3D printing harbors the magic of creation at its most immediate and extravagant.
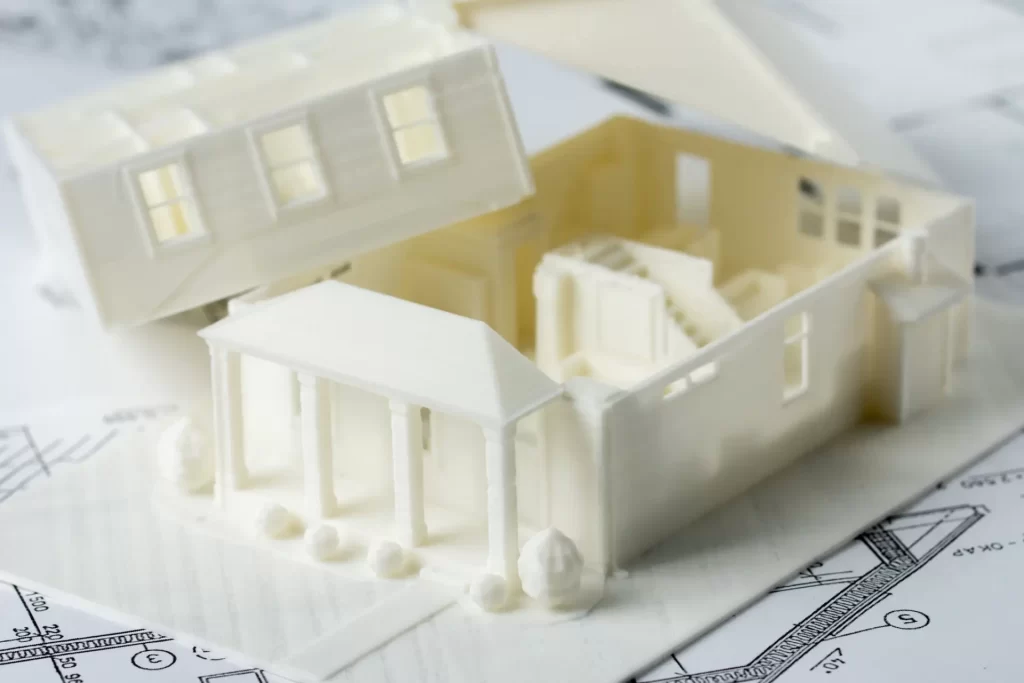
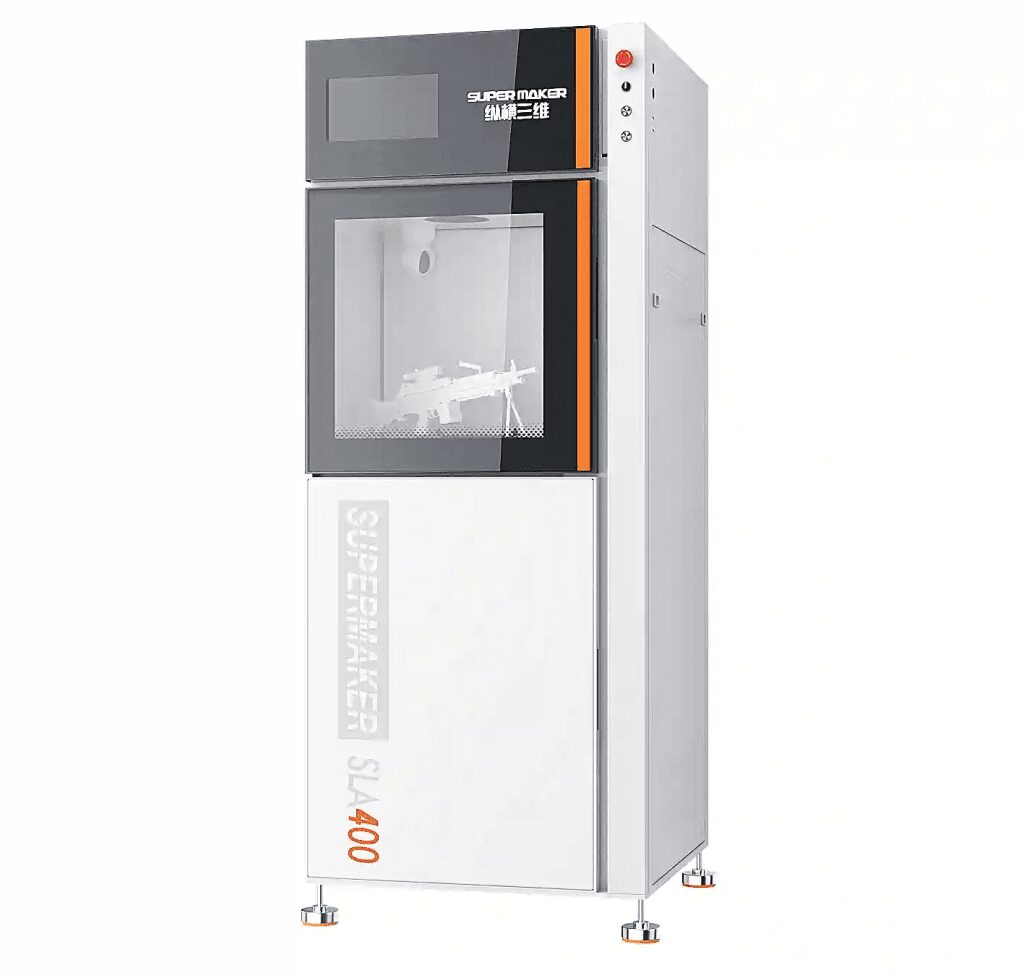

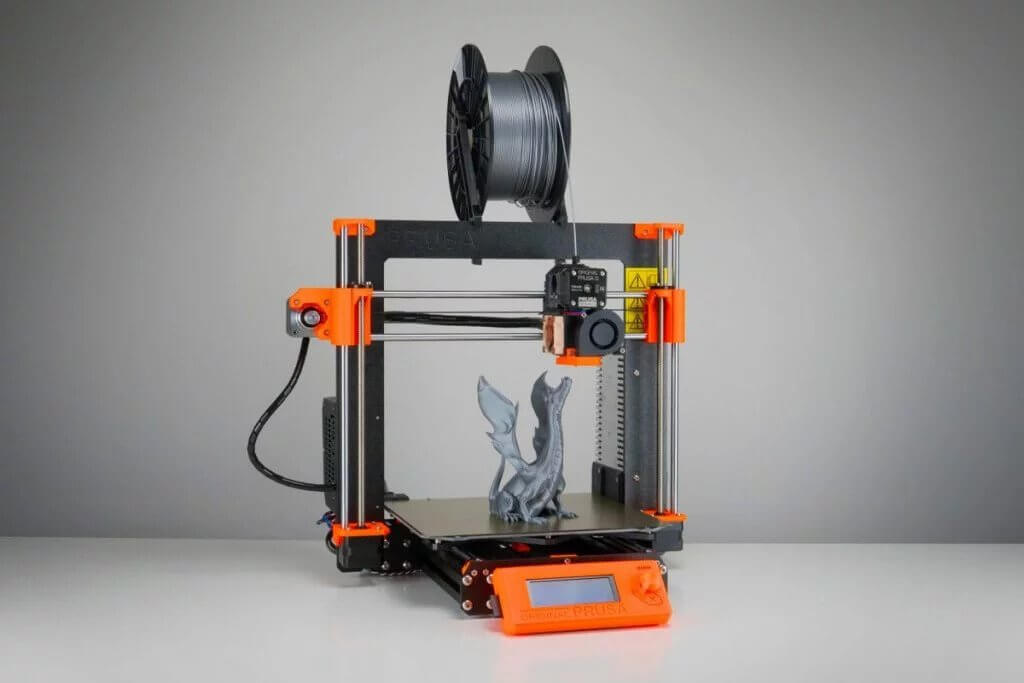
Journey into the World of 3D Printing
To comprehend the differences between SLA, DLP, and FDM, it’s crucial to set a sturdy foundation by understanding 3D Printing and its transformative potential and impact.
A Deeper Understanding of 3D Printing
3D Printing, or Additive Manufacturing, is the process of creating three-dimensional solid objects from a digital file. This is achieved using additive processes, i.e., creating a physical object by laying down successive layers of material until the object is complete.
Every layer corresponds to a thinly sliced horizontal cross-section of the eventual object. From prosthetics, movie props, architectural models, to complex experimental aircraft parts, 3D printing is leaving its mark everywhere!
Here are some game-changing advantages of 3D Printing:
- Speed: Rapid prototyping is possible with 3D printing.
- Cost: Less material waste and no need for expensive tools.
- Flexibility: Ability to print various shapes and structures.
That said, it’s not a panacea. There are also a few limitations:
- Size constraints: Large products cannot be printed.
- Material restrictions: Only materials suitable for 3D printing can be used.
- Finish: Some methods may not offer a great surface finish.
Stereolithography (SLA) 3D Printing: An Overview
Let’s kickstart our deep dive with Stereolithography (SLA), the pioneer of the 3D printing world. As the first-ever 3D printing technology, SLA is the big brother that led the additive manufacturing revolution.
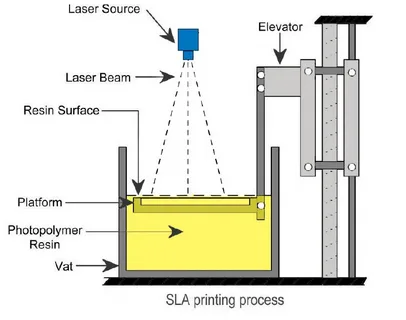
Defining SLA 3D Printing
SLA is a type of 3D printing within the broader category of photopolymerization, which involves using light to cure a liquid into a hardened solid. It works by concentrating a beam of ultraviolet light, directed by a computer-controlled mirror, onto the surface of a vat filled with liquid photopolymer.
Working Mechanism of SLA 3D Printing
The intricate dance of SLA printing follows these steps:
- Design Process: A SketchUp 3D design is created using CAD software, and the design file is sliced into thin cross-sectional layers.
- Preparation: The build platform is lowered into the photopolymer vat, just below the surface.
- Printing: The laser beam, guided by the STL file, draws out each layer, causing the liquid photopolymer to harden upon contact.
- Layering: Once a layer is complete, the platform descends slightly, the sweeper re-coats the surface, and the next layer is drawn out. This is repeated until the object is fully printed.
- Cleaning: The object is then removed from the vat, excess resin is cleaned off, and the print is further cured under UV light to solidify and enhance its properties.
Advantages and Disadvantages of SLA 3D Printing
Here’s a tabular view of the SLA printing’s pros and cons:
Advantages | Disadvantages |
Exceptional accuracy and precision | Relatively slow printing speed |
Great surface finish | Limited choice of materials |
Ability to print complex geometries | Requires post processing |
A tour of Digital Light Processing (DLP) 3D Printing
With the refresher on 3D printing and SLA technology behind us, let’s leapfrog into another intriguing realm – Digital Light Processing (DLP). A technology, just as fascinating, and versatile in its own unique way.
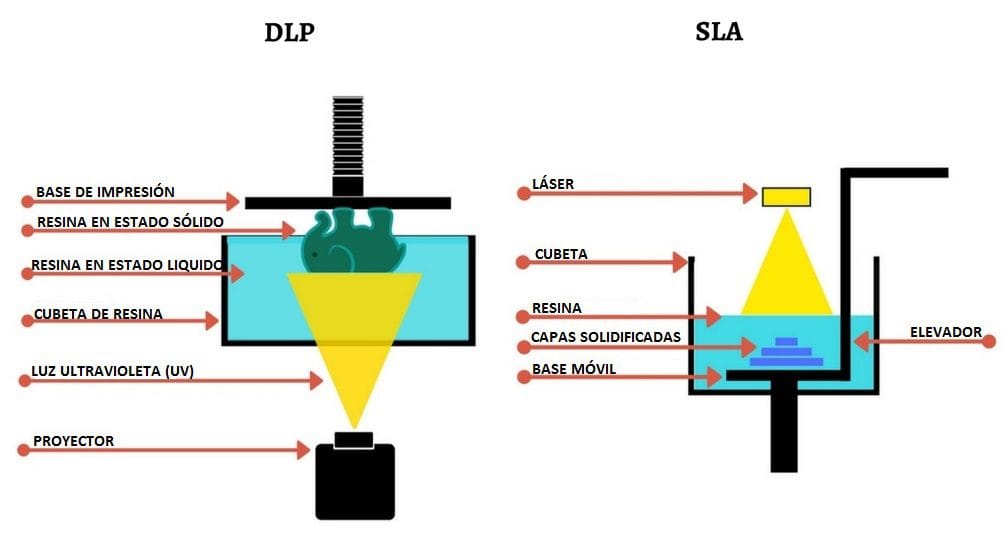
DLP 3D Printing: Decoding the Digital
DLP, like SLA, falls under the wider umbrella of vat photopolymerization 3D printing. It’s an additive manufacturing process that creates 3D parts from a liquid photopolymer resin, using a digital light projector screen.
Definition of DLP 3D Printing
DLP, or Digital Light Processing, refers to a type of vat polymerization 3D printing technology that uses digital micromirrors laid out on a semiconductor chip. This technology projects light onto a vat of liquid photopolymer resin and works layer by layer to create the 3D model.
Unmasking the DLP Printing Process
Consider this as your step-by-step manual to DLP printing process:
- Designing: Starts with creating a 3D CAD model and splitting it up into layers using specific software.
- Layer Projection: A digital light projector shines an image of each layer across the entire platform.
- Photopolymerization: The liquid polymer hardens upon exposure to light, forming a layer of the 3D object.
- Repeat: This process is repeated for each layer until the 3D part is completed.
- Final Touch: Post-processing involves rinsing off extra resin, taking off support structures (if used), and curing under UV light for extra strength.
Pros and Cons of DLP 3D Printing
To highlight the strengths and limitations of DLP printing technology, here’s a comparative table:
Advantages | Disadvantages |
Fast printing speed | Relatively high operating cost |
Highly detailed models | Post-processing requirement |
Long lifespan of the light source | Limited material options |
Fused Deposition Modeling (FDM) – Disentangling the Layers
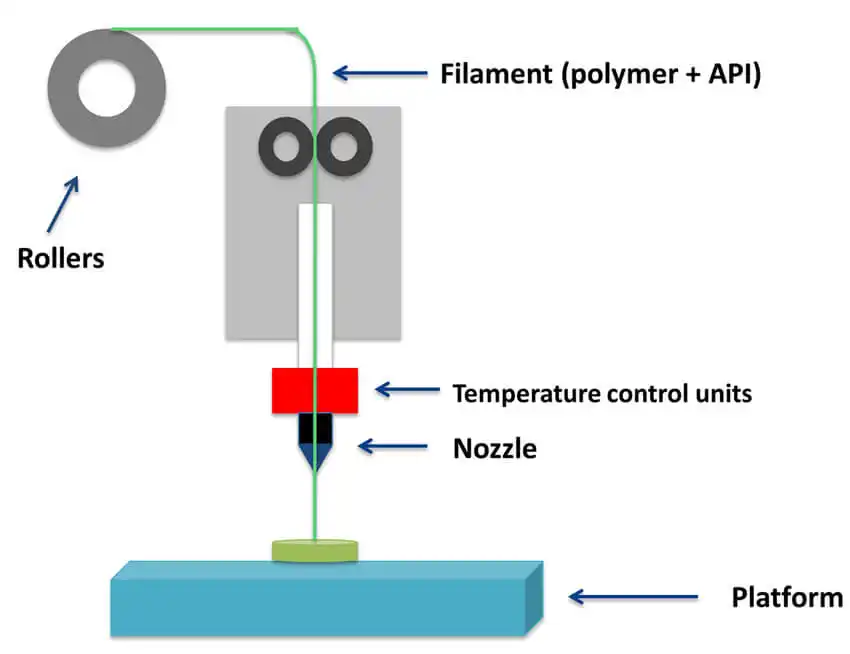
Having maneuvered through the light-focused strategies of SLA and DLP, let’s now shift gears towards a more material-centric method – Fused Deposition Modeling (FDM). This technology has paved the way for many groundbreaking applications, making it an important stop in our 3D printing exploration.
Unraveling FDM 3D Printing
Unlike SLA and DLP that use liquid resin, FDM takes a novel approach, focusing on thermoplastic filaments.
Defining FDM 3D Printing
FDM or Fused Deposition Modeling is an additive manufacturing process where a thermoplastic material is heated, extruded layer by layer, and then cooled to create a three-dimensional object.
The Intricacies of FDM Printing Process
Here’s your blueprint of the FDM printing process:
- Design & Preparation: Similar to previous technologies, it starts with creating a CAD model and slicing this model into manufacturable layers.
- Melting and Extrusion: A thermoplastic filament is fed into the printer’s extruder, melted, and deposited layer by layer onto the building platform.
- Layering: The print nozzle moves horizontally to create the shape of each layer, while the print bed moves vertically to allow the creation of subsequent layers.
- Cooling: Each layer solidifies upon cooling, fusing it with the previous layer.
- Final Stages: Upon completion, the final object may require removal of support structures or a bit of fine sanding to smooth the surface.
Advantages and Disadvantages of FDM Printing
Let’s put into perspective FDM technology’s upsides and downsides:
Advantages | Disadvantages |
Broad range of materials | Lesser surface finish quality |
Low operating costs | Slower than DLP and SLA in many cases |
Minimal post-processing | Limited accuracy for intricate designs |
SLA vs. DLP vs. FDM – An Enlightening Showdown
We’ve undertaken an exciting exploratory journey through the astonishing world of 3D printing technologies. Now, let’s bring these technologies head-to-head in a comparative analysis to help discern which technology might work best depending upon specific needs and circumstances.
Comparing Technologies at a Glance
Given, the SLA, DLP, and FDM have unique strengths and limitations; a side-by-side comparison can illuminate the stark contrasts and subtle nuances between them.
Comparative Overview
Let’s scrutinize the criteria that might be crucial for your 3D printing projects.
Criteria/Technology | SLA | DLP | FDM |
Print Quality and Detail | High | High | Medium |
Printing Speed | Medium | High | Variable |
Material Options | Limited | Limited | Broad |
Operating Costs | Medium | High | Low |
Who Wins Where?
- Speed: DLP triumphs when it comes to speed, with the ability to cure an entire layer in one go.
- Cost: FDM takes the crown for being the most cost-effective, with affordable printers and thermoplastic materials.
- Material Versatility: FDM wins again, offering a wide range of thermoplastic materials for different applications.
- Detail and Precision: SLA and DLP outshine FDM, offering superior resolution and precision to create intricate details.
Making the Choice
Ultimately, the choice of technology depends on the parameters of your project.
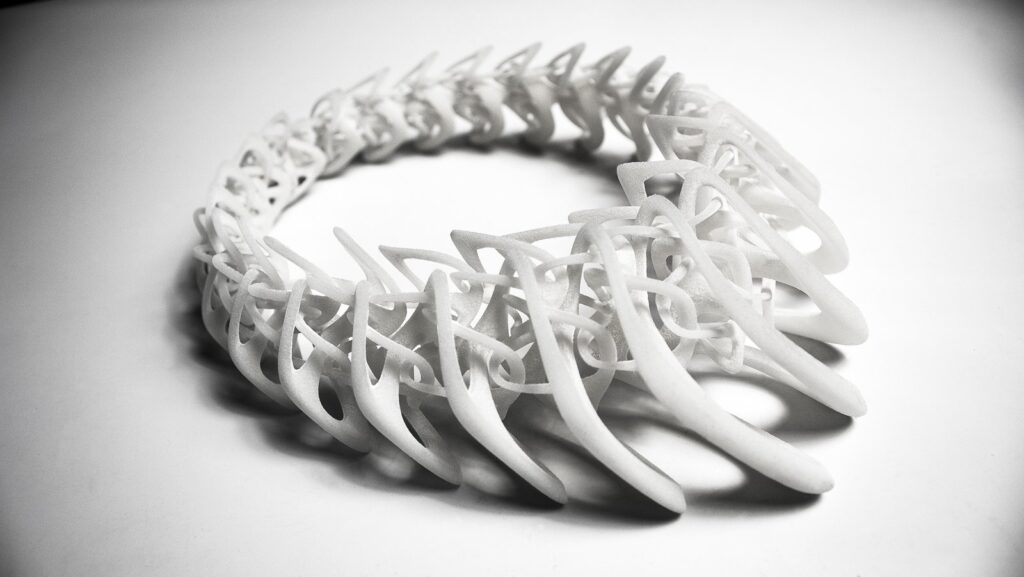
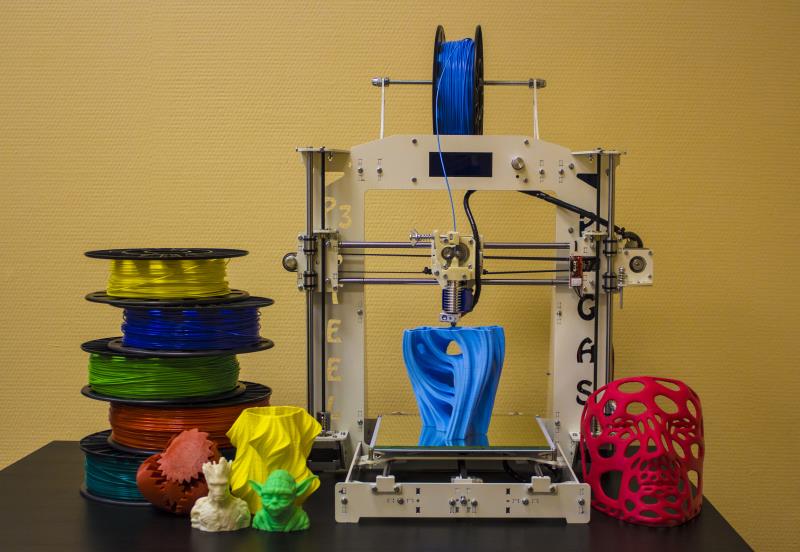
- SLA‘s and DLP‘s high detail and precision make them ideal candidates for jewelry, dental industries, and models requiring intricate details.
- FDM emerges as the front runner for prototypes, functional testing, and any application where strength is more important than detail.
3D printing isn’t a one-solution-fits-all situation. But, with the right knowledge and understanding, one can harness the power of each technology for their distinct realms in an innovative world that continues to evolve.
Choosing the Right 3D Printer
Your journey into the realm of 3D printing wouldn’t be complete without a comprehensive guide on how to choose the right 3D printer. In this section, let’s uncover the pivotal factors to consider when sifting through different 3D printers on the market.
Understanding Your Needs
Before exploring the array of 3D printers, it’s essential to understand your needs.
Defining the Purpose
Are you a hobbyist looking to create fun & decorative objects? Or are you a professional aiming to create prototypes or small parts for specific industries? Determine your goals to focus your search.
Considering the Budget
Your available budget will play a massive role in defining the range of 3D printers you can consider. Remember, apart from the initial expense of the printer, consider the costs of materials and maintenance as well.
Technical Considerations
Here are key technical factors to keep in mind when choosing a 3D printer:
Print Quality
If detail and accuracy are your topmost priorities, SLA or DLP printers would be the most suitable. For basic prototyping or when the finish is not a priority, consider FDM.
Material Options
The material may vary depending on your purpose. FDM printers provide a wide array of material choices. SLA and DLP offer specialized materials but are generally limited in comparison.
Print Speed
Speed matters when you must produce multiple parts or prototypes in a timeframe. DLP printers are typically faster.
Build Volume
The maximum object size the printer can output is crucial. Define the largest printing output you need before printer selection.
3D Printing – Revolutionizing Industries
We’ve delved deep into the intricacies of 3D printing technologies and the criteria to choose the right 3D printer. Now, it’s time to scale up and appraise how 3D printing is revolutionizing various industries.
3D Printing Across Industries
Here are a few ways 3D printing technologies have become game-changers in different industries:
i. Medical and Bio-Printing
3D printers have enabled the creation of patient-specific surgical models and custom prosthetics. There’s even ongoing research on creating organs via bio-printing, thus holding immense potential for the future.
ii. Aerospace and Automobiles
3D printers are used to fabricate lightweight and durable parts for aerospace and automotive applications. This not only results in cost-efficiency but also promotes sustainable practices by reducing waste.
iii. Prototyping and Product Development
3D printing accelerates the product development process by allowing quick and cost-effective prototyping. It helps refine product designs and speeds up the time to market.
iv. Construction
Massive 3D printers can now fabricate entire structures and buildings. This may lead to significant advancements in architecture and construction techniques, making processes more efficient and sustainable.
Looking to the Future
Looking ahead, 3D printing shows immense promise beyond these current applications:
- Personal Manufacturing: As 3D printers become more affordable, we may see a shift towards personalized manufacturing at home or small businesses.
- Food Printing: 3D food printers could change the way we prepare and consume food, with interesting prospects in precise nutrition and gourmet presentations.
- Recycling: 3D printers can potentially transform waste plastic into valuable products, promoting a circular economy.
We have come to an exciting point in history where technology like 3D printing can truly bring our imaginations to life. Let’s embrace the revolution, benefiting from its potential and addressing the challenges it poses. Only then can we foster a future filled with endless innovation and sustainable progress.
The future of 3D printing points towards advancements in biomedical printing, personal manufacturing, food printing, and recycling. As these innovations unfurl, we must adapt and learn to leverage these changes effectively.