Introduction to SLS 3D Printing: Unveiling the Layers of Innovation
Imagine a world where the physical limitations of manufacturing are no longer a barrier to innovation—a world where complex geometries, intricate designs, and bespoke creations come to life layer by layer, all at the command of a digital blueprint. This is not the stuff of science fiction; it’s the reality of Selective Laser Sintering (SLS) 3D printing, a technology that is revolutionizing industries and redefining the art of the possible.

SLS 3D printing stands at the forefront of additive manufacturing, a process that builds objects from the ground up, offering unparalleled design freedom and material efficiency. Unlike traditional subtractive manufacturing, which cuts away from a solid block, SLS adds material only where it’s needed, layer by microscopic layer. This means less waste, faster production times, and the ability to create structures that were once deemed impossible.

But how exactly does this cutting-edge technology work? What makes it different from other forms of 3D printing? And why is it becoming the go-to choice for professionals across various sectors—from aerospace engineers to fashion designers? In this comprehensive guide, we’ll peel back the layers of SLS 3D printing, revealing its inner workings, exploring its materials and applications, and forecasting its exciting future.
Prepare to embark on a journey into the heart of SLS technology, where we’ll uncover the secrets behind its transformative power and how it’s shaping the future of manufacturing. Whether you’re a seasoned expert or a curious newcomer, this article will illuminate the intricate dance of laser and powder that gives birth to some of the most innovative creations of our time. So, let’s dive in and explore the depth of SLS 3D printing, one layer at a time.
Understanding the Basics of SLS 3D Printing
In an era where customization is king and speed is the currency of choice, Selective Laser Sintering (SLS) 3D printing emerges as a beacon of innovation. But to truly appreciate its prowess, we must first delve into the foundational elements that define SLS. This chapter will serve as your primer, setting the stage for a deeper exploration of this transformative technology.
What Is SLS 3D Printing?
SLS 3D printing is a form of additive manufacturing that uses a high-powered laser to fuse small particles of polymer powder, layer by layer, to create complex and durable objects. It’s a process that transcends the boundaries of traditional manufacturing, offering unparalleled freedom in design and function.
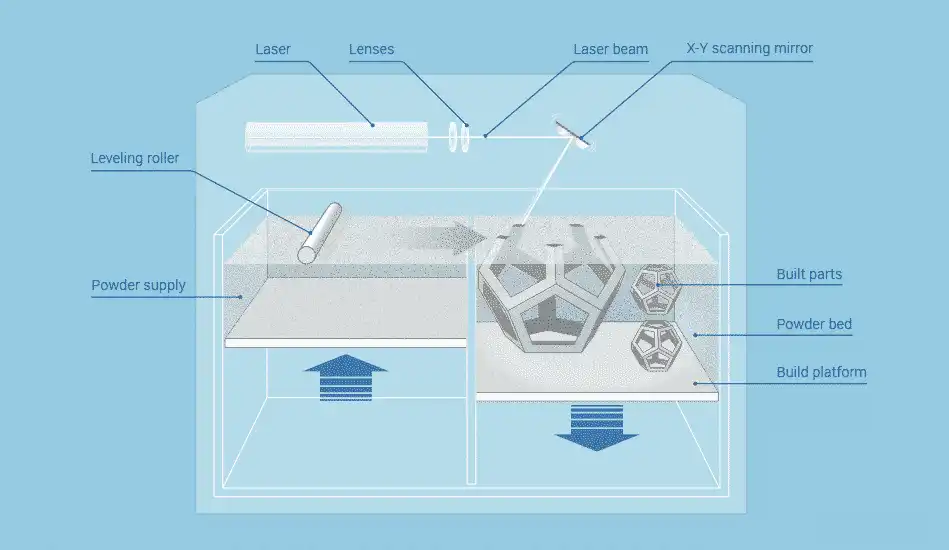
A Brief History: The Evolution of SLS Technology
The journey of SLS began in the mid-1980s, with Dr. Carl Deckard and Dr. Joe Beaman at the University of Texas at Austin. Their pioneering work laid the foundation for a technology that would grow to become a cornerstone of modern manufacturing.
How Does SLS Differ from Other 3D Printing Technologies?
SLS is often mentioned in the same breath as other 3D printing techniques like Fused Deposition Modeling (FDM) and **Stereolithography (SLA)**. However, it stands apart in several key areas:
- Material Efficiency: SLS does not require support structures as the unsintered powder acts as a support, leading to material savings and easier post-processing.
- Strength and Durability: Parts produced by SLS are known for their robustness, suitable for functional prototypes and end-use products.
- Complexity without Compromise: With SLS, designing complex geometries doesn’t come at the cost of structural integrity.
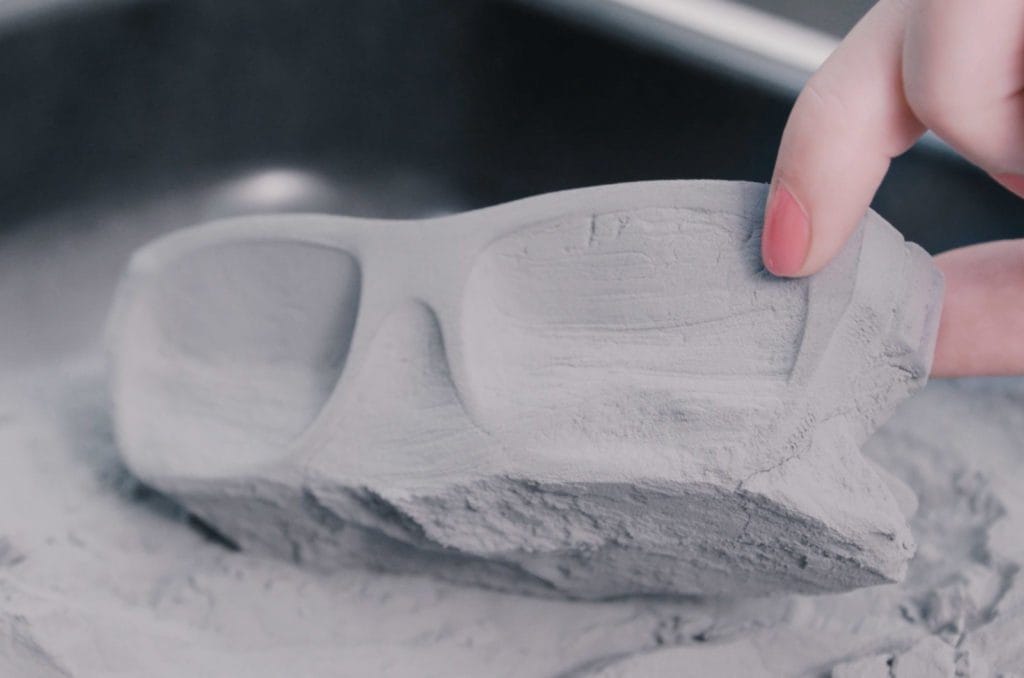
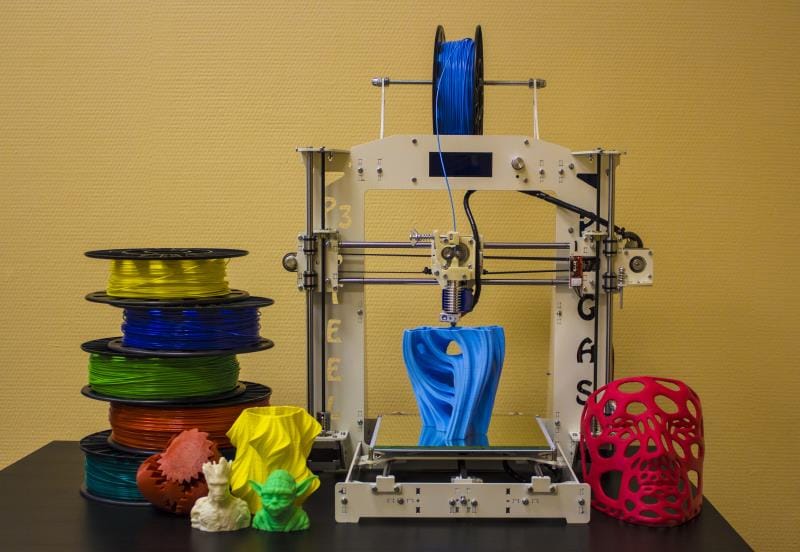
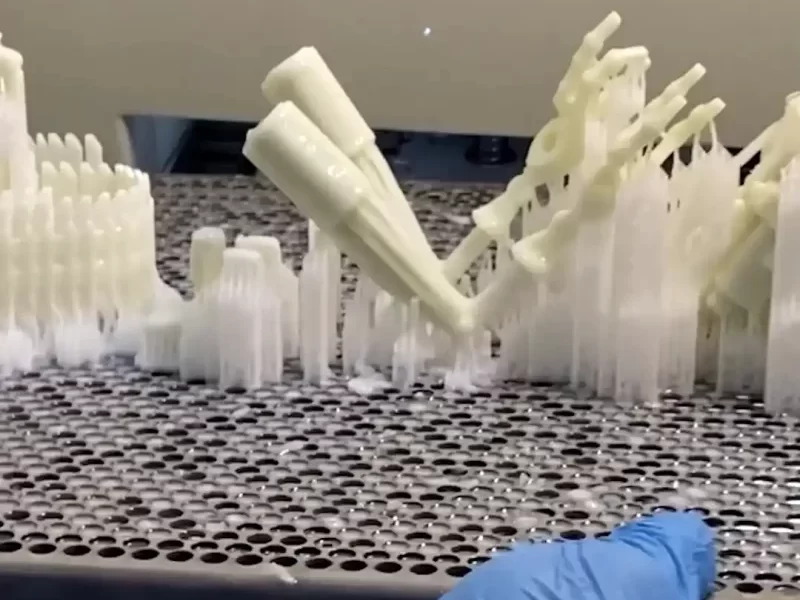
Feature | SLS | FDM | SLA |
Support Structures | Not required | Required | Required |
Material Wastage | Minimal | Moderate | Moderate |
Part Strength | High | Moderate | Varies |
Design Complexity | High | Low | Moderate |
The SLS 3D Printing Process: A Closer Look
The SLS process is a symphony of precision engineering and material science, consisting of several key stages:
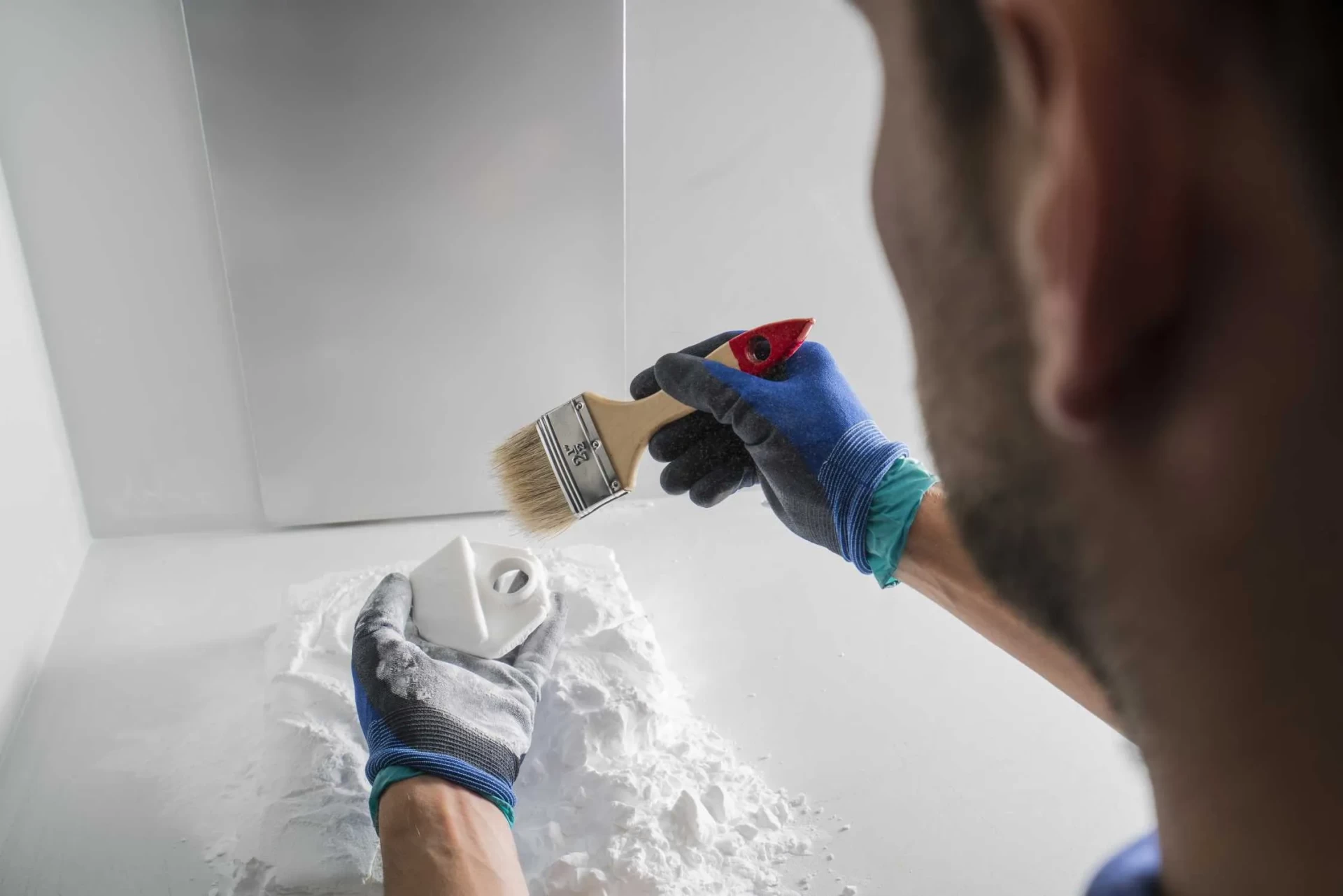
- Designing for SLS: Every print begins with a digital 3D model, tailored for SLS with specific design considerations to optimize the final product.
- Software Preparation: Specialized software slices the digital model into thin, horizontal layers and calculates the precise path the laser must follow.
- Machine Setup: The SLS printer is prepped, with the powder material evenly spread across the build platform.
- The Printing Phase: A laser beam, guided by the software’s instructions, selectively fuses the powder, layer by layer, to build the object.
- Cooling and Extraction: The build chamber is allowed to cool before the finished object is removed from the excess powder.
- Post-Processing: Additional steps such as sandblasting or painting are applied to achieve the desired finish.
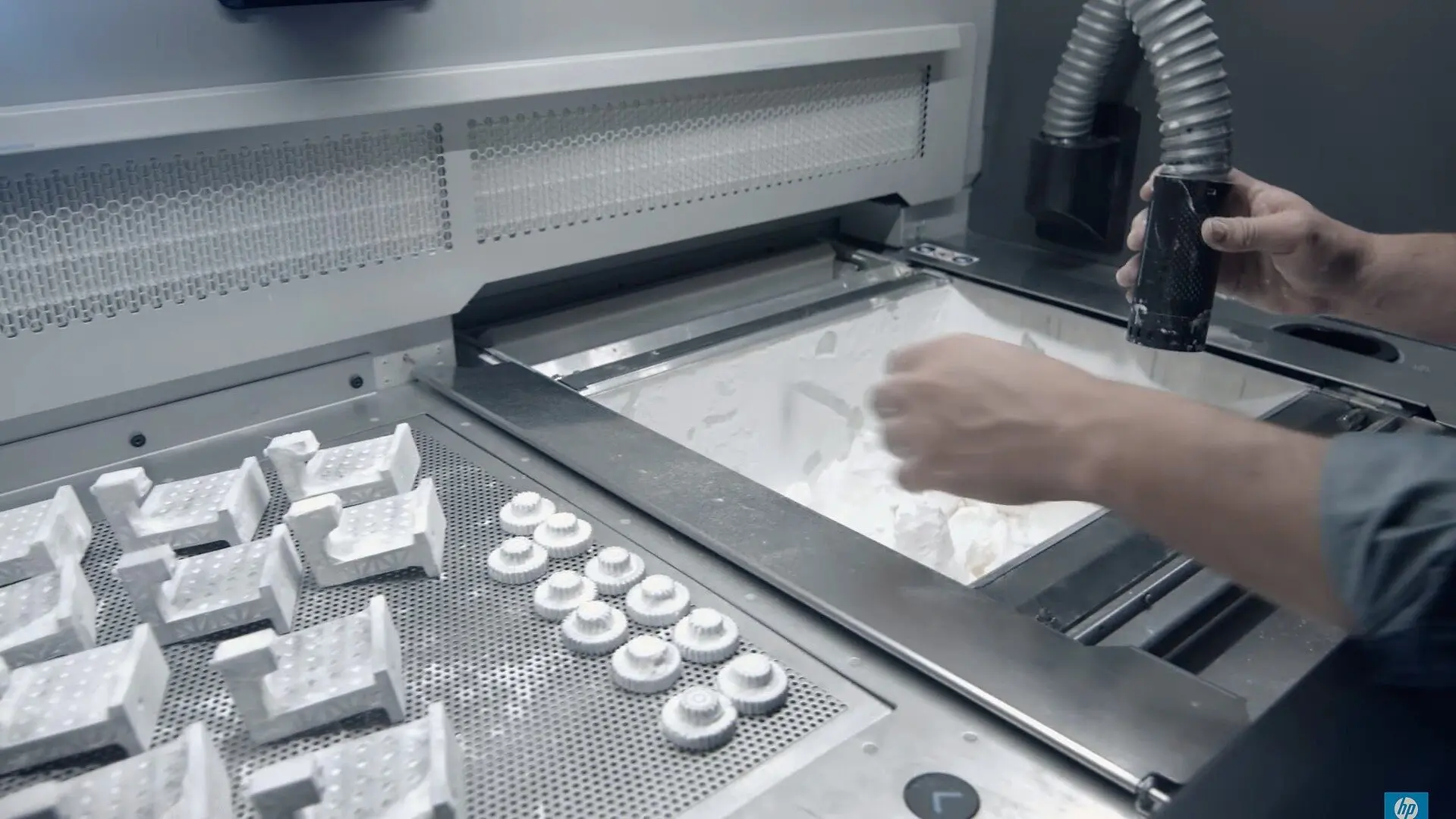
Each stage is crucial, transforming a digital file into a tangible object with the potential to impact industries and lives.
The SLS 3D Printing Process – From Powder to Prototype
The world of Selective Laser Sintering (SLS) is a fascinating realm where the barriers between digital dreams and tangible realities blur. It is here that a meticulous process transforms powdered materials into solid, functional objects with a finesse that traditional manufacturing methods can hardly match. Let’s embark on a detailed exploration of the SLS 3D printing process, dissecting each phase to understand how a mere powder evolves into a precision prototype or a final product.
Pre-Printing Phase: Setting the Stage for SLS
Before the laser even fires up, a series of critical steps lay the groundwork for a successful print. This pre-printing phase is all about preparation and precision.
Designing for SLS: The Art of the Possible
Designing for SLS is not just about creativity; it’s about understanding the nuances of the technology. Here’s what designers must consider:
- Wall Thickness: Ensuring minimum wall thickness to support the structure.
- Escape Holes: Including holes to allow unsintered powder to escape.
- Nesting: Optimizing the orientation and placement of parts within the build volume to maximize efficiency.
Software Used in SLS Design: The Digital Craftsmen
The right software is the unsung hero of SLS printing. It translates the designer’s vision into a language the printer can understand. Popular choices include:
- CAD Software: For creating the initial 3D designs.
- Slicing Software: To slice the model into layers and generate the path for the laser.
Preparing the 3D Model: The Blueprint of Success
The 3D model is the blueprint from which the SLS machine crafts the object. Preparing it involves:
- Checking for Errors: Ensuring there are no design flaws that could cause printing issues.
- Optimizing for Printing: Adjusting the model to align with the capabilities and limitations of the SLS printer.
Printing Phase: The Heart of SLS
This is where the magic happens. The printing phase is a dance of light and powder, a delicate process that demands both precision and patience.
The SLS Machine Setup: The Arena of Innovation
An SLS printer is more than a machine; it’s the arena where innovation takes physical form. Here’s what goes into setting it up:
- Loading the Powder: The chosen material is loaded into the printer, ready to be sintered.
- Calibrating the Laser: The laser must be precisely calibrated to ensure it fuses the powder correctly.
Powder Materials Used in SLS: The Building Blocks
The choice of powder material is crucial as it defines the properties of the final object. Commonly used materials include:
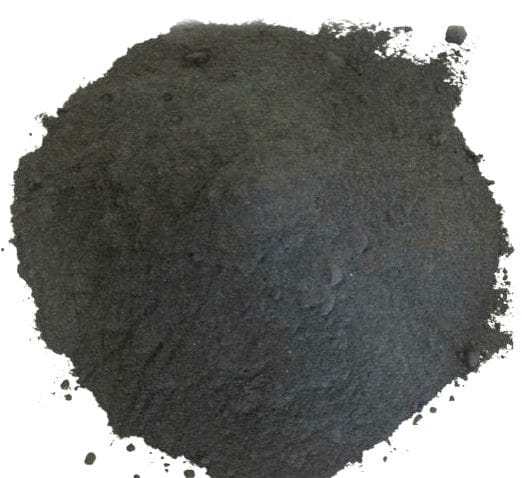
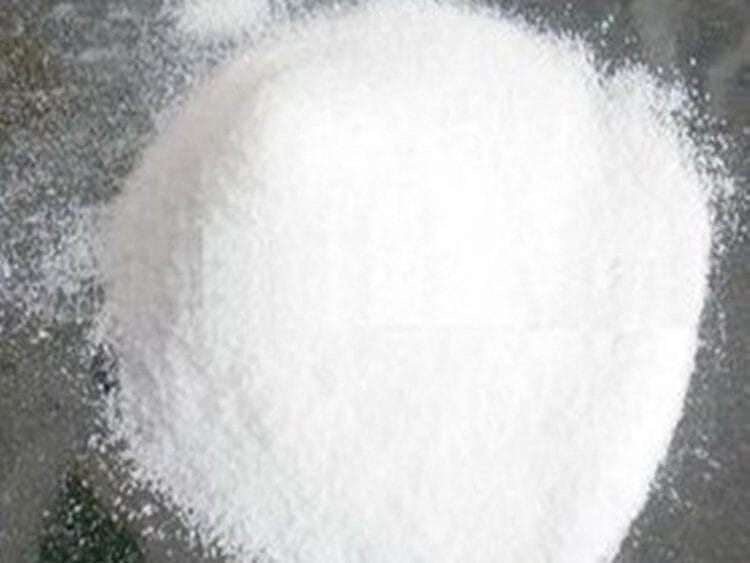
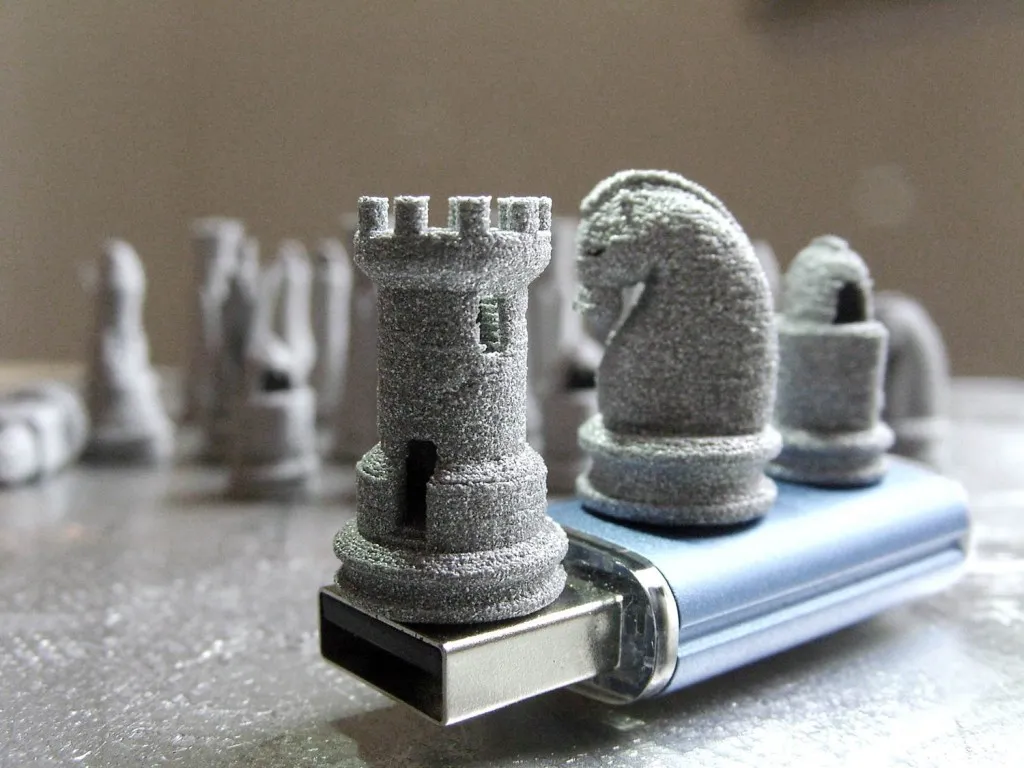
- Nylon (Polyamide): Known for its durability and flexibility.
- Polystyrene: Used for creating castings in metal casting processes.
- Alumide: A blend of nylon and aluminum powder, offering increased stiffness.
The Role of the Laser in SLS: The Conductor of Creation
The laser in an SLS printer is like the conductor of an orchestra, guiding the instruments to create a symphony. It selectively fuses the powder according to the 3D model’s instructions, layer by layer.
Layer-by-Layer Sintering Process: The Essence of SLS
The layer-by-layer sintering process is the heart of SLS printing. Here’s how it unfolds:
- Spreading the Powder: A thin layer of powder is spread across the build platform.
- Sintering: The laser sinters the powder where the object is to be formed.
- Lowering the Build Platform: After one layer is complete, the build platform lowers, and the process repeats.
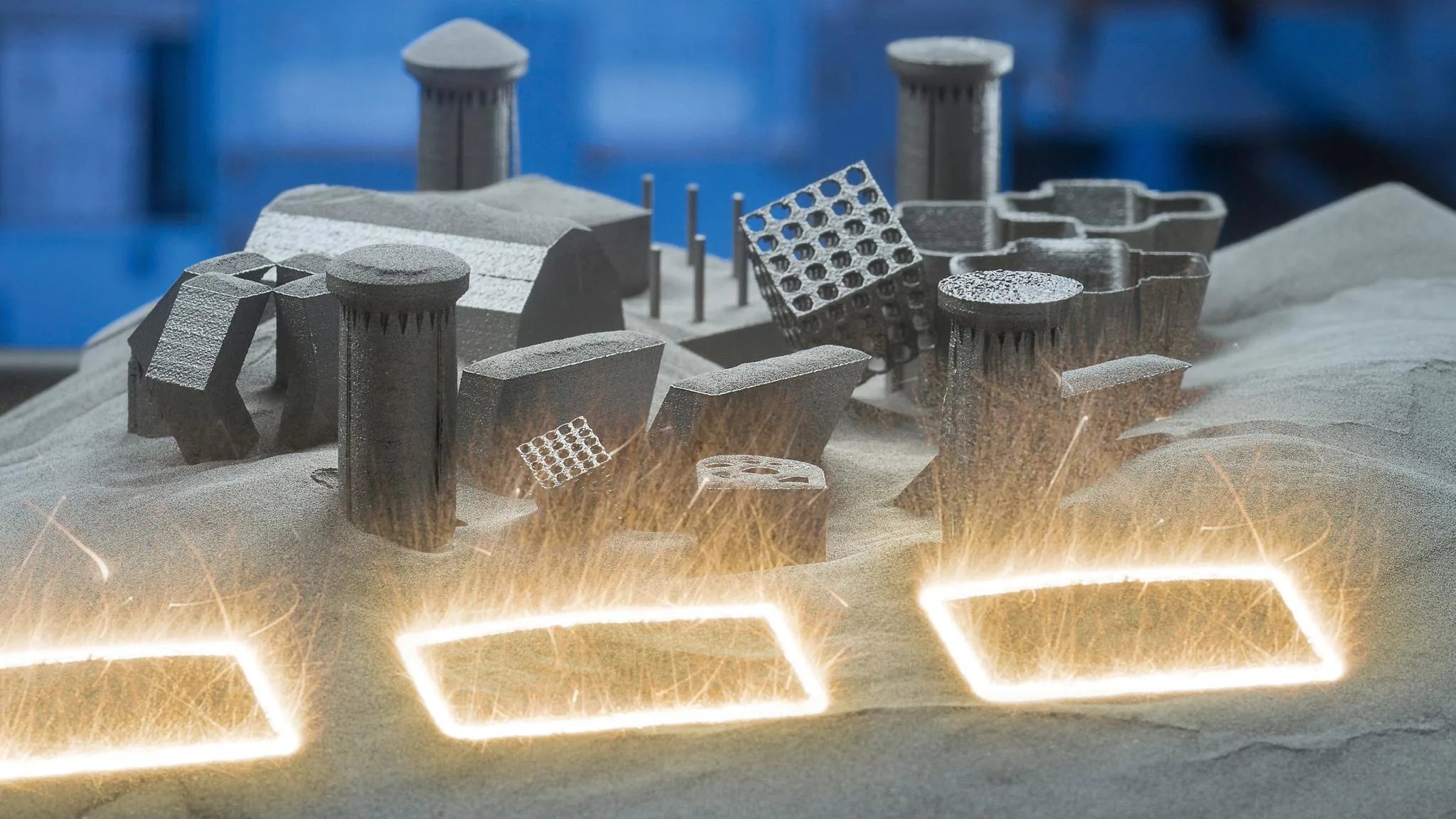
Post-Printing Phase: Bringing the Object to Life
Once the printing is complete, the object is not quite ready to step into the world. It needs to go through the post-printing phase, which involves:
Cooling and Cleaning the Printed Object: The Unveiling
The newly printed object must cool down before being removed from the powder bed. Then, it’s carefully cleaned to remove any excess powder.
Post-Processing Techniques: The Finishing Touches
Post-processing can involve several techniques to enhance the object’s appearance and properties:
- Sandblasting: To smooth the surface and improve the finish.
- Sealing: To seal the porous surface and protect the part.
- Dyeing or Painting: To add color or aesthetic details.
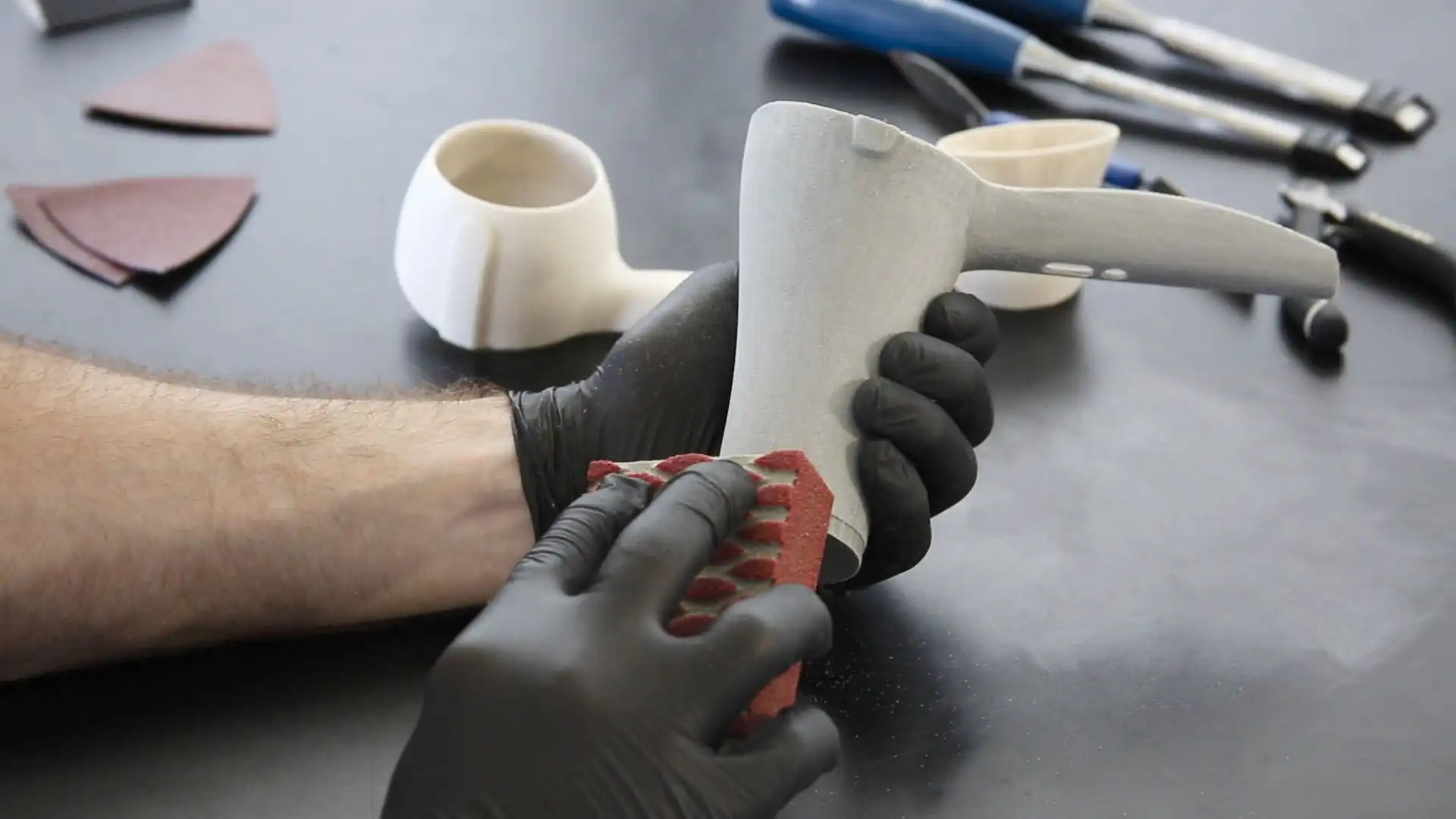
The SLS 3D printing process is a journey from digital file to physical form that encapsulates the essence of modern manufacturing. It’s a blend of art and science, where every parameter and phase must be meticulously managed to achieve the desired outcome. With each layer, the SLS printer not only constructs a part but also lays the foundation for the future of manufacturing—a future that’s built on precision, efficiency, and boundless creativity.
The Materials of SLS 3D Printing – A Deep Dive into Powders
In the alchemy of Selective Laser Sintering (SLS) 3D printing, the choice of material is as crucial as the design itself. It is the powder that forms the substrate for the SLS process, offering a palette of properties that can be fine-tuned to meet the demands of various applications. This chapter will take you on an in-depth exploration of the powders that are the lifeblood of SLS 3D printing, their characteristics, and their transformative impact on the final product.
The Foundation of SLS: Understanding Powder Materials
The powders used in SLS are more than mere grains; they are engineered for performance. Each material brings its own set of properties to the table, influencing the strength, flexibility, and thermal resistance of the printed object.
Common SLS Powder Materials
Here’s a closer look at some of the most commonly used SLS materials:
- Nylon 12 (Polyamide 12): Renowned for its excellent mechanical properties and durability, it’s the go-to material for functional parts.
- Nylon 11: Valued for its flexibility and impact resistance, ideal for snap-fit assemblies and living hinges.
- Glass-Filled Nylon: Infused with glass beads, this material offers enhanced stiffness and thermal resistance.
- Alumide: A composite of Nylon and aluminum powder, offering metal-like aesthetics and good thermal properties.
The Characteristics of SLS Materials: A Comparative Analysis
Each SLS material has a unique profile that makes it suitable for specific applications. Here’s a comparative analysis to help you understand their differences:
Material | Strength | Flexibility | Durability | Heat Resistance | Application Examples |
Nylon 12 | High | Moderate | High | Moderate | Automotive parts, consumer goods |
Nylon 11 | Moderate | High | High | Low | Wearable devices, sports equipment |
Glass-Filled Nylon | Very High | Low | High | High | Aerospace components, industrial tools |
Alumide | High | Low | Moderate | High | Prototypes, decorative items |
The Impact of Particle Size and Shape
The size and shape of the powder particles play a pivotal role in the quality of the print. Uniform particle size leads to better packing density and surface finish, while the shape influences the flowability and spreadability of the powder.
The SLS Printing Process Revisited: Material Considerations
The choice of material affects each stage of the SLS printing process:
- Pre-Printing: Material selection guides the design constraints and machine settings.
- Printing: Particle properties dictate the laser power and speed, as well as layer thickness.
- Post-Processing: Different materials require specific post-processing methods to achieve the desired finish.
Innovations in SLS Materials: Pushing the Boundaries
The quest for new materials is relentless in the world of SLS printing. Researchers and manufacturers are constantly developing new powders to expand the capabilities of SLS technology:
- Bio-Compatible Materials: For medical implants and prosthetics.
- Conductive Powders: Opening doors for electronics manufacturing.
- High-Temperature Resistant Powders: Suitable for aerospace and automotive industries.
Sustainable SLS Materials: The Green Revolution
Sustainability is becoming a significant factor in material development. Recycled powders and bio-based materials are gaining traction, promising a greener future for SLS printing.
The materials used in SLS 3D printing are as diverse as the applications they enable. From robust nylons to composite alumides, each powder offers a unique set of properties that can be harnessed to create objects with specific characteristics. As we continue to innovate and develop new materials, the potential of SLS printing expands, paving the way for advancements in manufacturing, design, and beyond.
SLS 3D Printing Applications – Revolutionizing Industries
The versatility of Selective Laser Sintering (SLS) 3D printing is a gateway to innovation across a multitude of industries. From aerospace to healthcare, SLS technology is not just an alternative to traditional manufacturing methods; it’s often the superior choice due to its ability to create complex, durable, and precise parts. In this chapter, we delve into the myriad applications of SLS printing, showcasing how this technology is revolutionizing industry practices and pushing the boundaries of what’s possible.
Aerospace and Aviation: Soaring with SLS
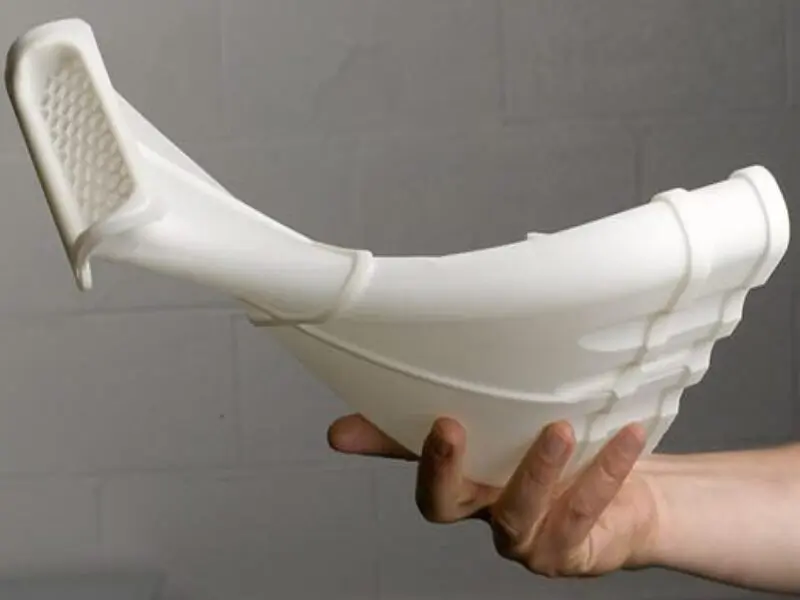
In the skies, every gram counts, and SLS is instrumental in producing lightweight yet robust components for aerospace applications.
- Customized Air Ducts: Optimized for airflow and reduced weight.
- Satellite Components: Complex geometries with high strength-to-weight ratios.
- UAV Parts: Durable, lightweight parts for unmanned aerial vehicles.
Automotive Industry: The Drive Towards Efficiency
The automotive sector benefits from SLS’s ability to produce end-use parts and prototypes rapidly.
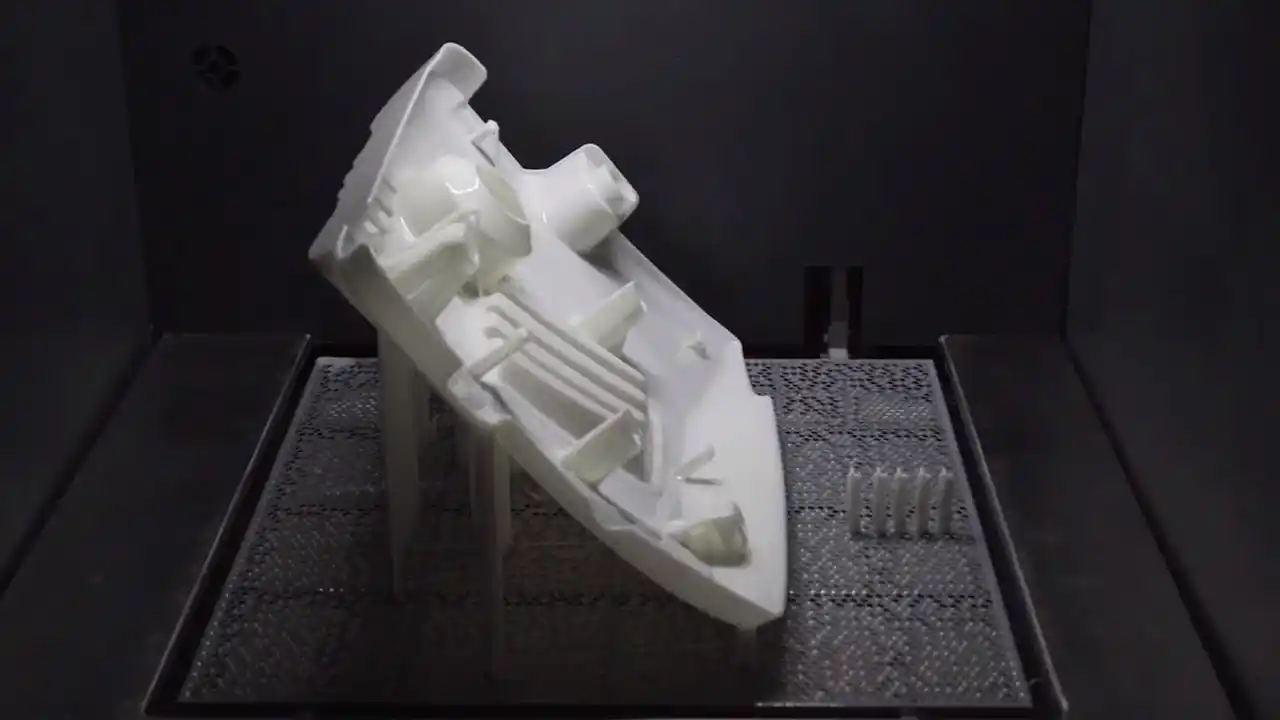
- Custom Interior Components: Tailored parts for luxury vehicles.
- Functional Prototypes: Rapid testing of design concepts.
- Complex Engine Parts: Heat-resistant components with intricate designs.
Medical and Dental: Personalized Care with Precision
SLS printing is a boon for personalized medicine, offering custom solutions for patients and healthcare providers.
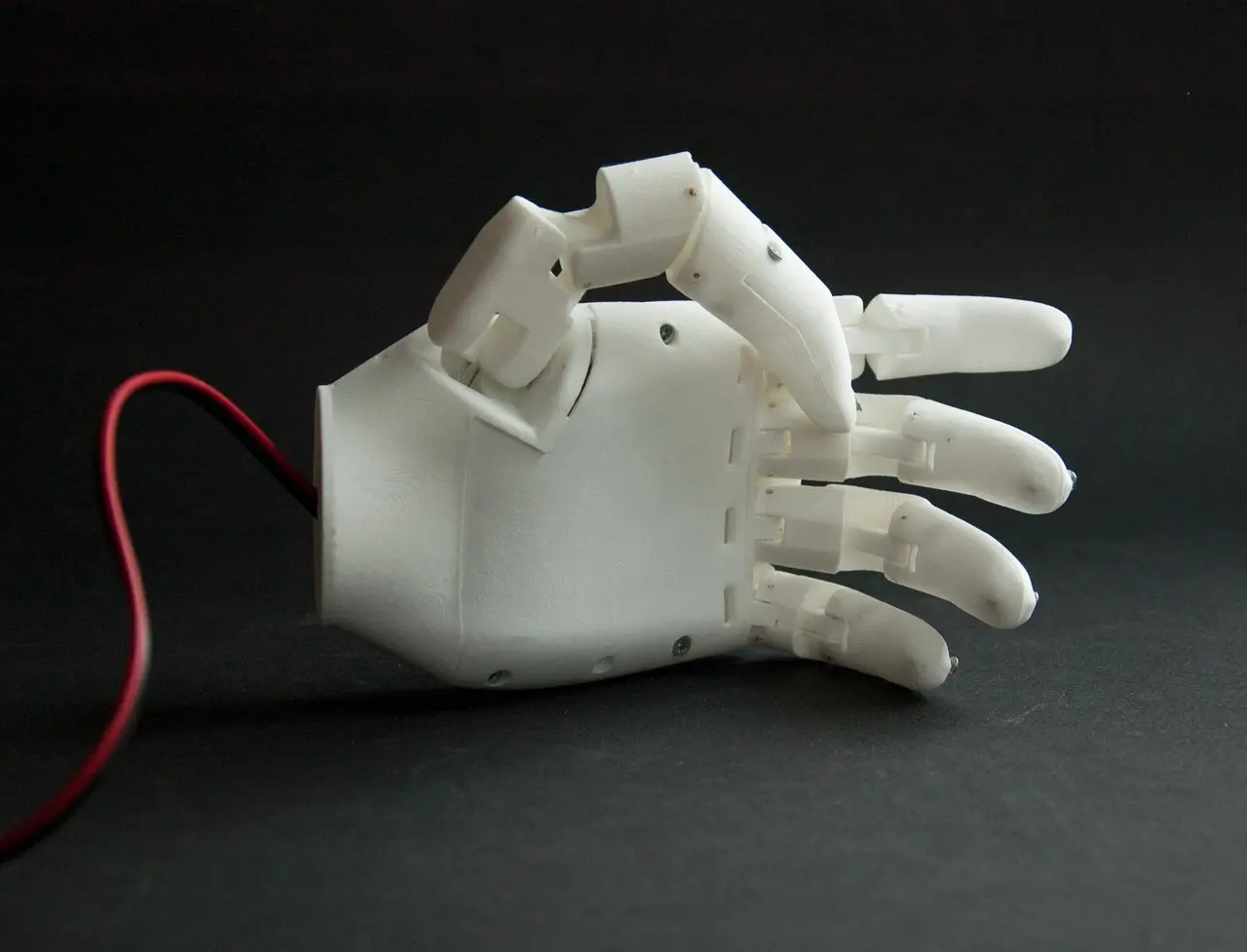
- Prosthetics and Orthotics: Custom-fitted devices for improved comfort.
- Dental Models: Accurate, patient-specific dental and orthodontic models.
- Surgical Guides and Tools: Sterilizable instruments tailored to individual surgeries.
Consumer Goods: The Customization Craze
The demand for personalized products is met with SLS’s ability to economically produce small batches of customized items.
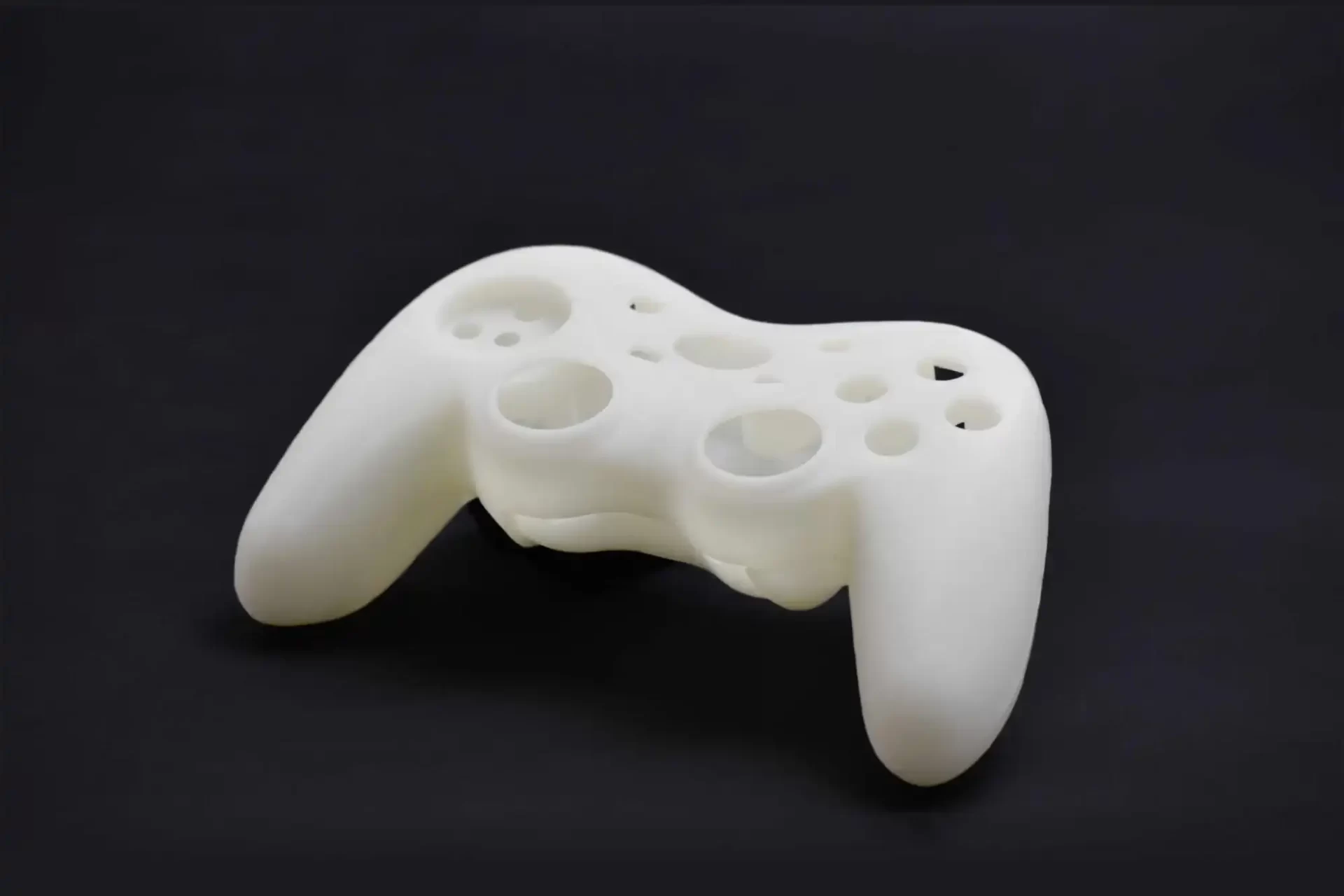
- Wearable Technology: Ergonomic designs that conform to the wearer’s body.
- Fashion Accessories: Intricate jewelry and eyewear designs.
- Home Decor: Unique items that cater to individual tastes.
Industrial Manufacturing: The Power of Prototyping
SLS is a powerful tool for industrial manufacturers, providing the ability to quickly iterate and refine prototypes.
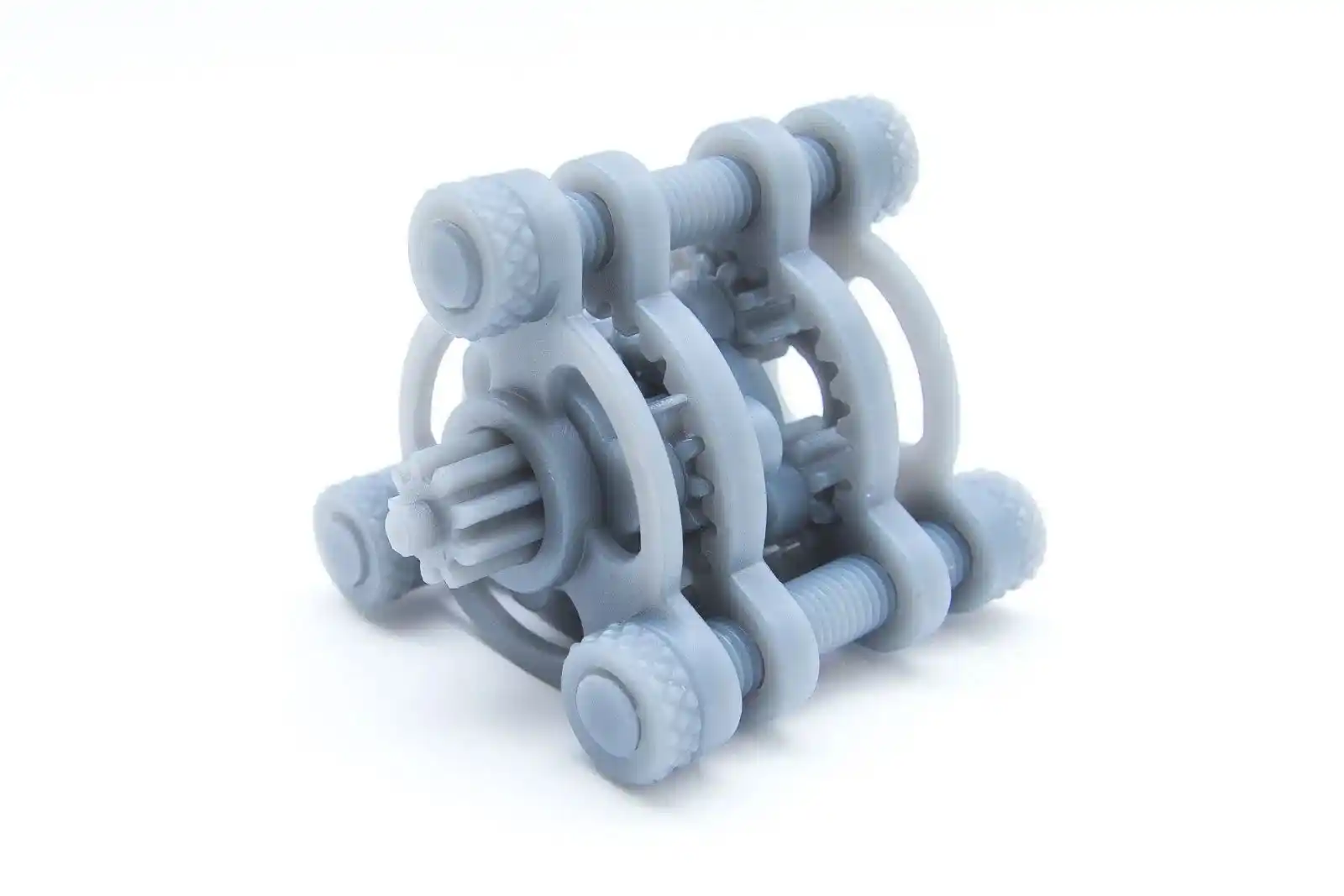
- Tooling and Fixtures: Custom jigs and fixtures for manufacturing lines.
- High-Performance Gears: Durable parts that withstand high stress.
- Complex Assembly Mock-ups: Accurate models for fit and function testing.
The Impact of SLS in Education and Research
Educational institutions and research facilities leverage SLS to push the envelope of scientific inquiry and innovation.
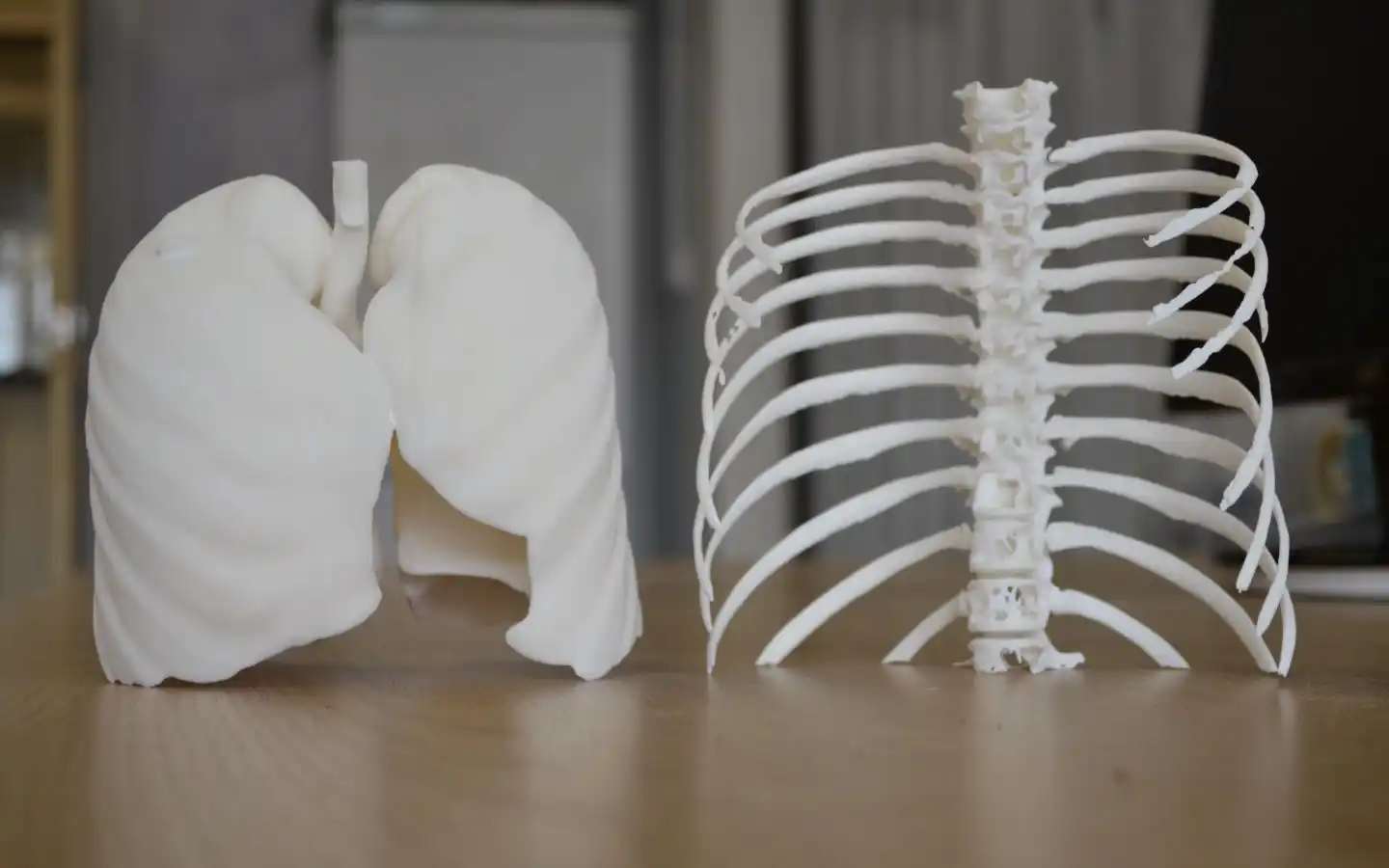
- Educational Models: Detailed anatomical models for medical students.
- Research Prototypes: Custom parts for experimental apparatus.
The Future of SLS Printing: Emerging Trends and Potential
As SLS technology continues to mature, its potential applications are expanding into new and exciting territories:
- Sustainable Manufacturing: Using recycled materials to reduce waste.
- Construction: Custom components for modular building designs.
- Art and Design: Complex sculptures and installations that challenge traditional fabrication methods.
Challenges and Considerations
Despite its many benefits, SLS printing also comes with challenges that must be addressed:
- Cost: While decreasing, the cost of SLS machines and materials can be prohibitive for some applications.
- Material Limitations: The range of materials available for SLS is still growing, with research ongoing to expand the options.
- Post-Processing: Some applications may require extensive post-processing, adding time and expense to the manufacturing process.
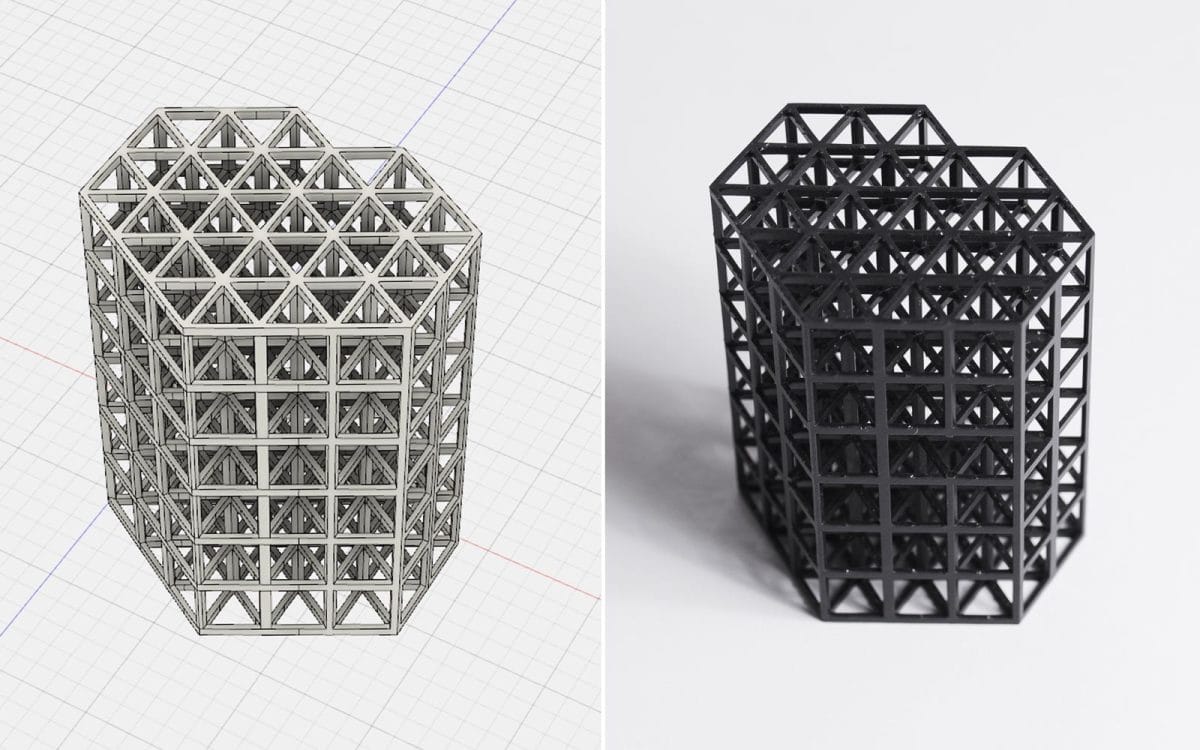
SLS 3D printing is a transformative force across industries, offering unparalleled flexibility, efficiency, and precision. As we continue to explore the capabilities of this technology, its applications are only limited by our imagination. The future of manufacturing is being reshaped by SLS, making it possible to turn the most intricate designs into reality, streamline production processes, and create products that were once thought impossible.
Advancements in SLS Machinery – Shaping the Future of 3D Printing
The evolution of Selective Laser Sintering (SLS) machinery is a story of relentless innovation and technical refinement. As the engines that power the SLS process, these machines are constantly being upgraded to become faster, more precise, and more user-friendly. This chapter will explore the latest advancements in SLS printers, the cutting-edge features that set them apart, and how they are shaping the future of 3D printing.
The Heart of Innovation: SLS Printer Evolution
SLS machines have come a long way from their early prototypes. Today’s printers are marvels of engineering, designed to meet the exacting demands of modern manufacturing.
Key Technological Advancements
- Increased Print Speeds: New laser systems and scanning technologies allow for faster layer sintering, significantly reducing print times.
- Improved Precision: Advances in laser calibration and powder layering result in higher resolution prints with finer details.
- Larger Build Volumes: Modern SLS printers offer larger build spaces, enabling the production of bigger parts or batch production of multiple items simultaneously.
Enhanced Usability and Maintenance
- User-Friendly Interfaces: Touchscreen panels and intuitive software make it easier for operators to manage print jobs.
- Automated Powder Handling: Systems that automate the feeding and recycling of powder reduce manual intervention and enhance safety.
- Modular Designs: Some SLS machines now feature modular components, simplifying maintenance and potential upgrades.
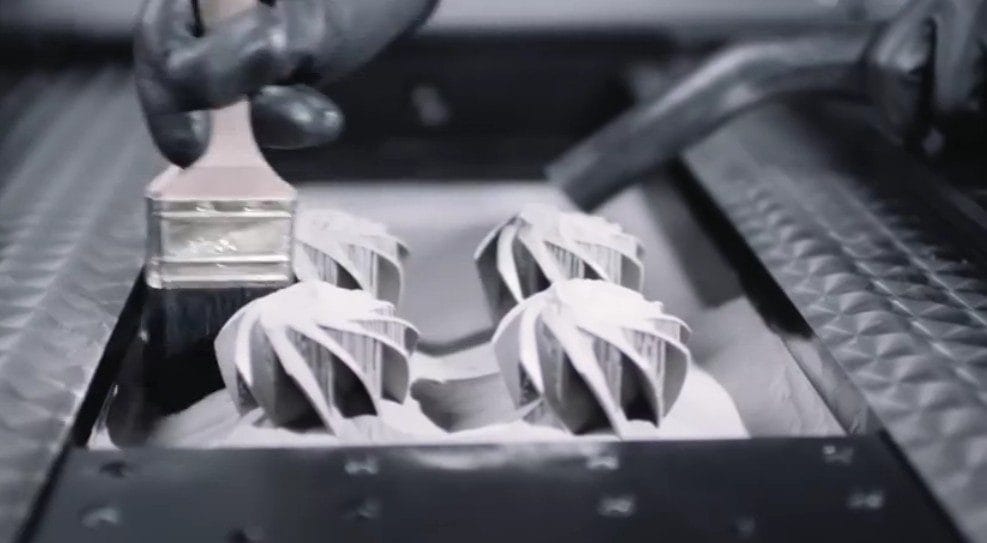
Breakthrough Features of Modern SLS Printers
Today’s SLS printers are packed with features that push the boundaries of what’s possible in additive manufacturing.
- Multi-Laser Systems: Printers equipped with multiple lasers can work on different parts of the powder bed simultaneously, drastically increasing productivity.
- Integrated Quality Control: In-built monitoring systems use cameras and sensors to ensure each print layer meets quality standards.
- Advanced Thermal Management: Sophisticated temperature control systems ensure consistent sintering across the entire build area, reducing warping and distortion.
The Role of Software in SLS Advancements
Software plays a pivotal role in the functionality of SLS machines, with developments focusing on:
- Smart Slicing Algorithms: These optimize print paths for speed and quality.
- Predictive Maintenance Tools: Software that anticipates machine issues before they occur, minimizing downtime.
- Cloud-Based Collaboration: Platforms that allow for remote design, machine operation, and monitoring to streamline the production process.
The Impact of SLS Machine Advancements on Industries
The improvements in SLS machinery have a direct impact on various industries, enabling:
- Rapid Prototyping: Faster turnarounds from design to prototype.
- Mass Customization: Economical production of customized parts in large volumes.
- Complex Manufacturing: Creation of parts with geometries that are impossible to achieve with traditional methods.
Challenges in SLS Machine Development
Despite significant progress, challenges remain in the development of SLS machines:
- High Costs: Advanced features come with a price tag that can be a barrier for small businesses and hobbyists.
- Material Compatibility: Each new material can require machine adjustments or even new hardware to print effectively.
- Energy Consumption: High-powered lasers and thermal systems can draw substantial energy, impacting operational costs and sustainability.
The advancements in SLS machinery are not just enhancing the capabilities of 3D printing; they are redefining the limits of manufacturing. As machines become more sophisticated, they open up new possibilities for design, innovation, and production efficiency. The future looks bright for SLS technology, with ongoing research and development promising to unlock even greater potential.
The Future of SLS 3D Printing
As we venture further into the 21st century, the future of Selective Laser Sintering (SLS) 3D printing looks brighter than ever. With rapid technological innovations and shifting market trends, SLS is poised to become even more integral to manufacturing and design processes across the globe. This chapter will explore the cutting-edge developments we can expect to see in SLS technology and how they may influence various sectors.
Technological Innovations
The relentless pace of technological progress continues to push the boundaries of SLS 3D printing, with significant advancements on the horizon.
Advances in Laser Technology
- Faster Scanning Speeds: Innovations in laser scanners are expected to increase the speed at which lasers can sinter the powder, further reducing production times.
- Multi-Wavelength Lasers: The development of lasers that can operate at multiple wavelengths simultaneously could allow for the sintering of different materials within the same print job, opening up new possibilities for multi-material printing.
- Improved Beam Quality: Enhancements in laser beam quality will provide even finer detail and surface finish, allowing for more intricate and precise products.
New Material Development
- Bio-Compatible Materials: The introduction of new bio-compatible powders will be particularly transformative for medical applications, allowing for the direct printing of implants and other in-body devices.
- Sustainable Materials: A focus on sustainability will lead to the creation of new, eco-friendly materials derived from renewable sources or recycled plastics.
- Smart Materials: Research into materials with embedded functionalities, such as conductivity or responsive properties, will expand the functionality of SLS-printed parts.
Market Trends
Market dynamics are an important indicator of how SLS 3D printing will evolve and be adopted in the coming years.
Industry Adoption Rates
- Aerospace and Automotive: These sectors will likely continue to lead in the adoption of SLS technology due to the high value of weight reduction and customization in production.
- Medical Sector: Increased adoption is anticipated as more biocompatible materials become available and as the benefits of personalized healthcare solutions become more evident.
- Construction: As materials and printers advance, there is potential for SLS to play a role in creating components for modular and custom-designed buildings.
Consumer Accessibility
- Lower Cost of Entry: As the technology matures, the cost of SLS printers is expected to decrease, making them more accessible to smaller businesses and even individual consumers.
- On-Demand Manufacturing: The rise of on-demand manufacturing services will allow more businesses to take advantage of SLS without the need for in-house capabilities.
- Education and Training: Increased emphasis on additive manufacturing in educational curricula will produce a workforce more skilled in SLS technologies, further driving innovation and adoption.
The future of SLS 3D printing is one of continued innovation and expansion. Technological advancements in laser technology and new material development, combined with evolving market trends, will open new doors for the application of SLS printing. From the production floors of major industries to the studios of designers and the homes of hobbyists, SLS is set to become a more prominent tool in the creation and manufacturing of products. As we look ahead, the potential of SLS 3D printing continues to grow, promising to revolutionize the way we think about and engage with the process of bringing ideas to life.
Getting Started with SLS 3D Printing
Embarking on the journey of SLS (Selective Laser Sintering) 3D printing can be an exhilarating venture for both beginners and seasoned professionals. This chapter is designed to guide you through the initial steps of entering the world of SLS 3D printing, from selecting the right equipment to tapping into the wealth of knowledge available.
Choosing an SLS Printer
When it comes to selecting an SLS printer, several factors should be taken into account to ensure that your choice aligns with your needs, budget, and the level of detail required for your projects.
Factors to consider
- Print Volume: Consider the size of the objects you plan to print and ensure the printer can accommodate them.
- Material Compatibility: Ensure the printer supports the range of materials you intend to use.
- Precision and Resolution: Determine the level of detail necessary for your prints and select a printer that can provide that resolution.
- Durability and Reliability: Research the longevity and maintenance requirements of the printer.
- Cost: Balance the initial investment against the expected print volume and the cost of materials and maintenance.
- Support and Warranty: Look for manufacturers with good customer support and warranty services.
Recommended SLS printers for beginners and professionals
- For Beginners: The XYZprinting SLS printer is a great entry-level option, offering a user-friendly interface and a decent print volume for those new to SLS printing.
- For Professionals: The EOS Formiga P 110 is highly recommended for professionals, known for its precision, reliability, and support for a wide range of materials.
Learning Resources
To master SLS 3D printing, one must engage with learning materials and communities dedicated to this technology.
Online courses and tutorials
- Coursera and Udemy: These platforms offer comprehensive courses on SLS 3D printing, covering the basics to advanced techniques.
- YouTube: A plethora of tutorials are available, ranging from setting up your SLS printer to optimizing your print jobs.
Books and community forums
- Books: “The 3D Printing Handbook” provides valuable insights into SLS technology, while “SLS 3D Printing: A Practical Guide” is a hands-on manual for beginners.
- Community Forums: Websites like Reddit’s r/3Dprinting and dedicated forums on 3D Hubs provide community support and a place to share knowledge and experiences.
With the right printer and a commitment to learning, anyone can start leveraging the power of SLS 3D printing. By considering the factors outlined above and engaging with the recommended resources, you’ll be well-equipped to begin your SLS 3D printing journey. Whether you’re a hobbyist looking to experiment or a professional aiming to integrate SLS into your workflow, the world of SLS 3D printing is now more accessible than ever.
Case Studies
In this chapter, we explore real-world applications of SLS 3D printing through detailed case studies. These examples illustrate the challenges faced by different industries, the SLS solutions implemented, and the outcomes that were achieved. By examining these case studies, we gain insight into the practical benefits and transformative potential of SLS technology.
Case Study 1: Aerospace Component Manufacturing
The aerospace industry is known for its stringent requirements for component precision, strength, and weight reduction. SLS 3D printing has emerged as a pivotal technology in meeting these demands.
The Challenge
A leading aerospace company faced the challenge of reducing the weight of their aircraft components to enhance fuel efficiency without compromising on strength or safety.
The SLS Solution
The company turned to SLS 3D printing to produce complex, lightweight structures that were previously impossible to create using traditional manufacturing methods. The SLS process allowed for the consolidation of multiple parts into single, intricate components, reducing assembly time and potential points of failure.
The Outcome
The SLS-produced components led to a significant reduction in weight, resulting in improved fuel efficiency and cost savings. Additionally, the shorter production times and decreased need for assembly resources contributed to a more streamlined manufacturing process.
Case Study 2: Custom Prosthetics
Customization is crucial in prosthetics, where a perfect fit can significantly improve a user’s comfort and mobility. SLS 3D printing offers a level of customization that traditional methods cannot match.
The Challenge
Patients in need of prosthetic limbs often faced long waiting times and discomfort due to the limitations of mass-produced prosthetics, which could not accommodate the unique anatomical features of each individual.
The SLS Solution
A prosthetics manufacturer adopted SLS 3D printing to create fully customized prosthetic limbs. By using patient-specific 3D scans, the company was able to design and produce prosthetics that matched the exact contours and dimensions of the patient’s residual limb.
The Outcome
The custom SLS prosthetics provided a much better fit, leading to enhanced comfort and improved mobility for patients. The use of SLS also reduced production time, allowing patients to receive their custom prosthetics much faster than before.
Conclusion
These case studies demonstrate the versatility and impact of SLS 3D printing across various sectors. By addressing unique challenges with tailored SLS solutions, industries are able to achieve outcomes that benefit both the providers and the end-users. As SLS technology continues to evolve, its applications are likely to expand, offering even more innovative solutions to complex problems.