Introduction
Imagine a world where intricate designs materialize layer by layer, where the only limit to creating complex objects is the boundary of the mind. This is the realm of 3D printing, a revolutionary technology that has transformed the way we conceive and fabricate items across industries. At the forefront of this innovation is Stereolithography (SLA)—the grandmaster of 3D printing technologies, known for its precision and versatility.
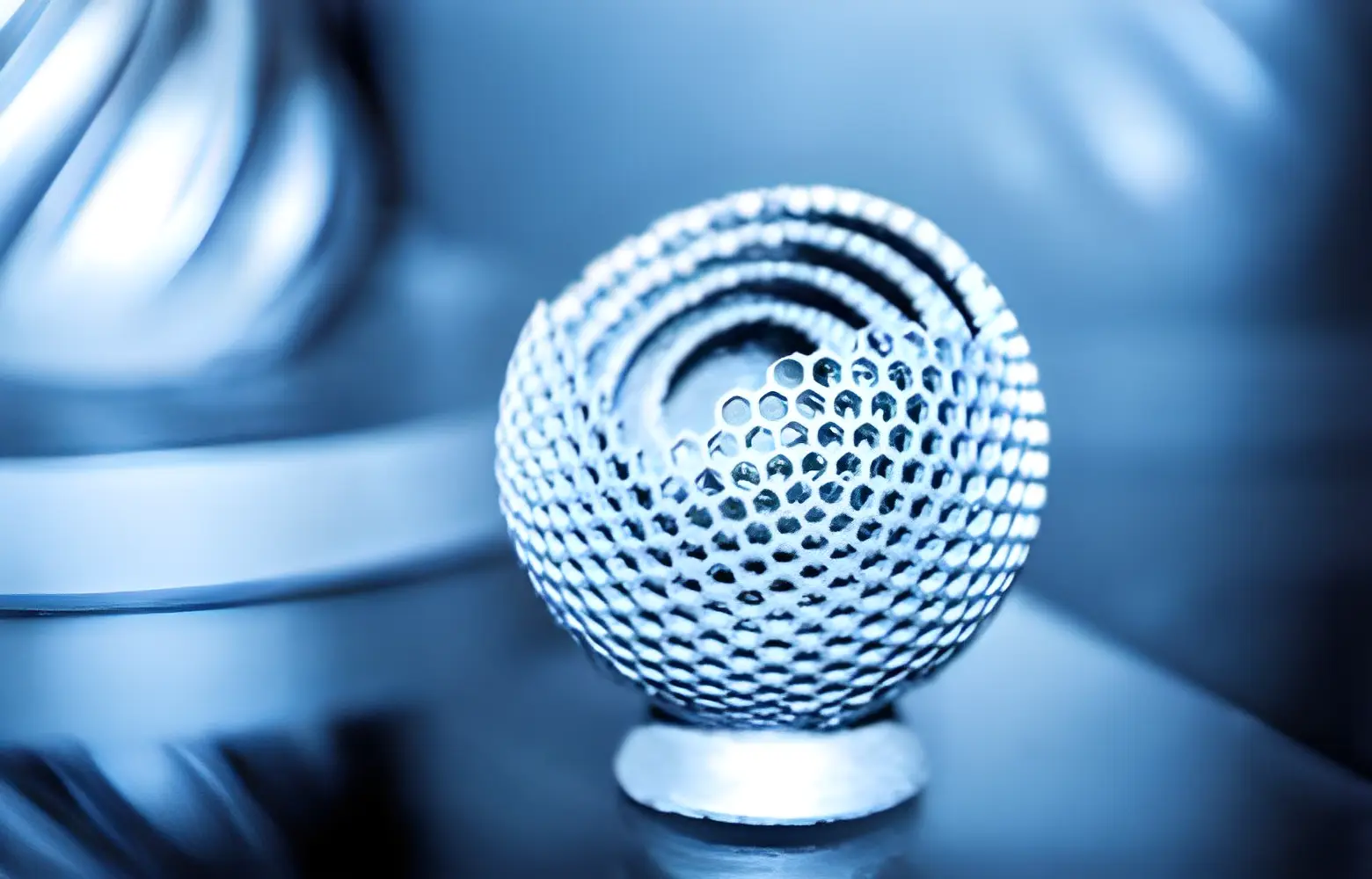
SLA 3D printing stands as a beacon of progress, a method that has refined the art of turning liquid resin into solid, tangible artistry. It is a process that begins with a pool of raw, potential-rich material and ends with a creation that is as detailed as it is functional. This technology is not just about printing; it’s about bringing to life the intricate details that other methods cannot capture, about pushing the boundaries of manufacturing and design.
In this comprehensive exploration, we will delve into the intricacies of the SLA 3D printing process. From the initial spark of design to the final post-processing touches that bring a model to its lustrous completion, we will uncover every layer of this fascinating procedure. Whether you are a seasoned engineer, a curious hobbyist, or a visionary designer, this journey will illuminate the path from conceptual shadows into the light of creation.
Join us as we demystify the SLA 3D printing process, a journey that melds science and art into the prints of tomorrow. Let’s embark on this transformative voyage, where the digital world seamlessly transitions into the physical one, and where the only limit is the expanse of imagination.
Understanding SLA 3D Printing

In the ever-evolving landscape of additive manufacturing, Stereolithography (SLA) stands out as a paragon of precision and detail. It’s a process that has captivated the imagination of innovators and creators alike. But what exactly is SLA 3D Printing, and how does it differentiate itself from the myriad of other technologies in the 3D printing universe? Let’s dive into the depths of this pioneering technology.
What is SLA 3D Printing?
SLA, or Stereolithography, is a form of 3D printing that transforms liquid resins into solid objects through the meticulous application of light. Invented in the 1980s by Chuck Hull, SLA has the distinguished honor of being the very first 3D printing technology. It operates on the principle of photopolymerization, a chemical process where light causes chains of molecules to link together, forming polymers that harden into a solid structure.
Key Components of SLA Printing:
- Resin Tank: Holds the photopolymer resin.
- Build Platform: Where the object is constructed, layer by layer.
- Ultraviolet Laser: Precisely cures and solidifies the resin.
- Galvanometers: Steering devices that direct the laser across the resin’s surface.
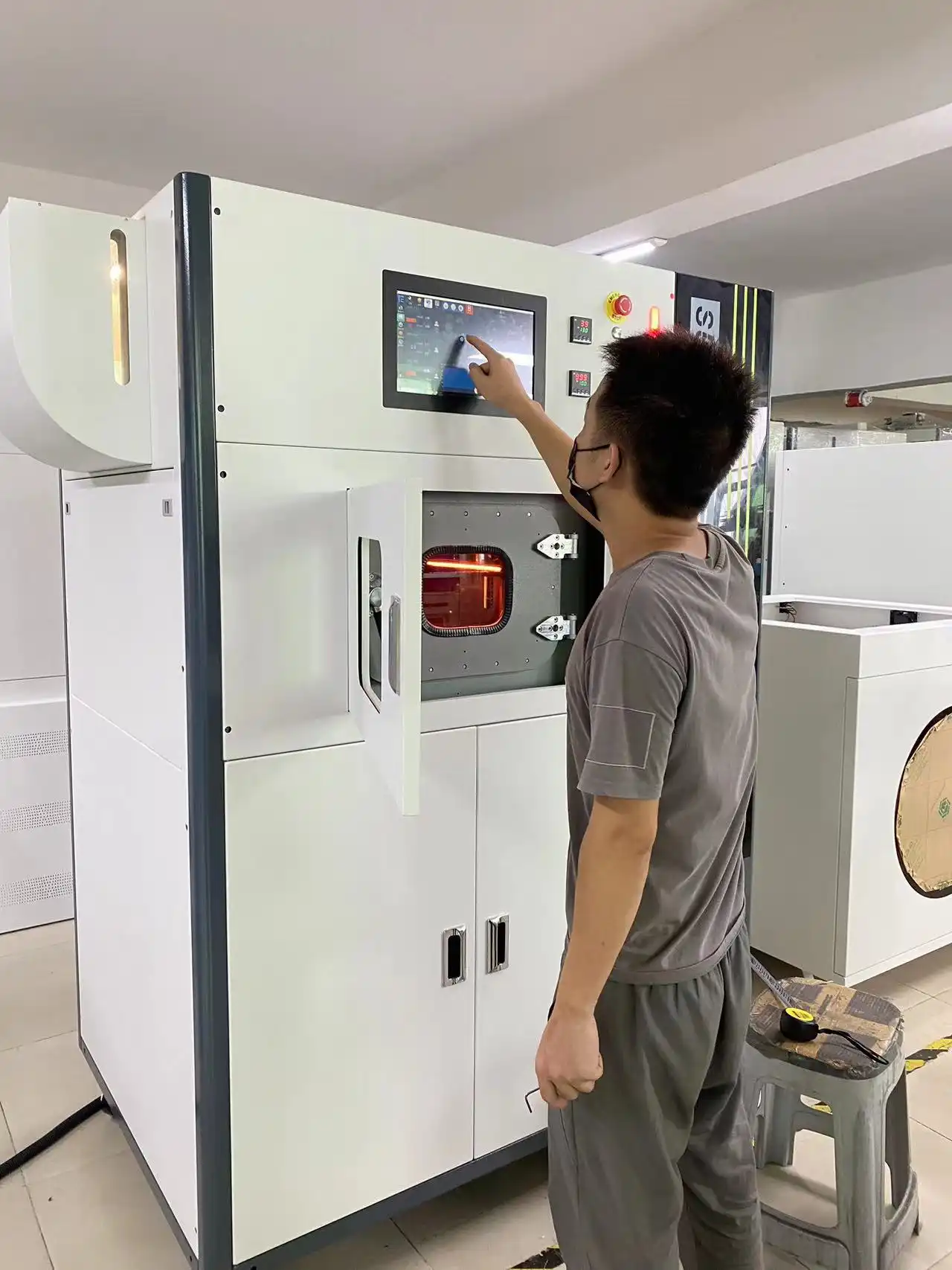
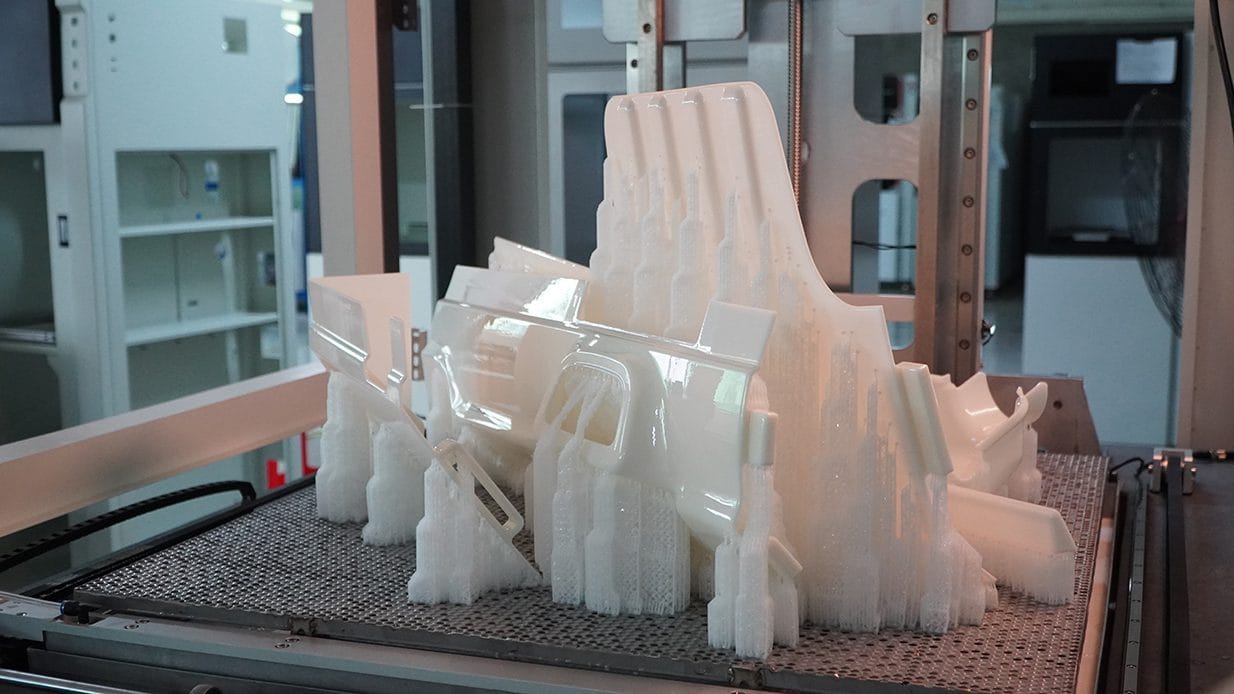
How SLA Differs from Other 3D Printing Technologies
SLA is often mentioned in the same breath as Fused Deposition Modeling (FDM) and Selective Laser Sintering (SLS), but it’s the nuances that set them apart.
- FDM vs. SLA: FDM printers extrude thermoplastic filaments through a heated nozzle, building up layers until the object is complete. SLA, on the other hand, uses a laser to cure liquid resin into hardened plastic. The result? SLA achieves finer details and smoother surface finishes than FDM.
- SLS vs. SLA: SLS uses a laser to sinter powdered material, typically nylon, to form solid objects. Unlike SLA, SLS doesn’t require support structures as the powder acts as its own support. However, SLA wins when it comes to surface quality and transparency in materials.
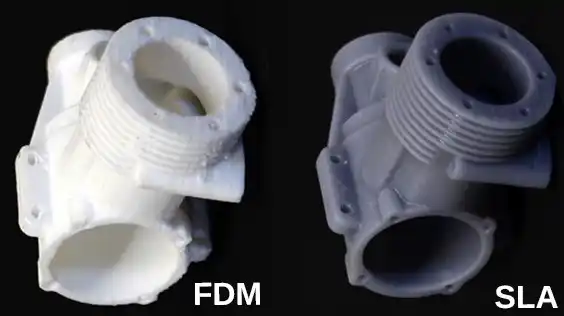
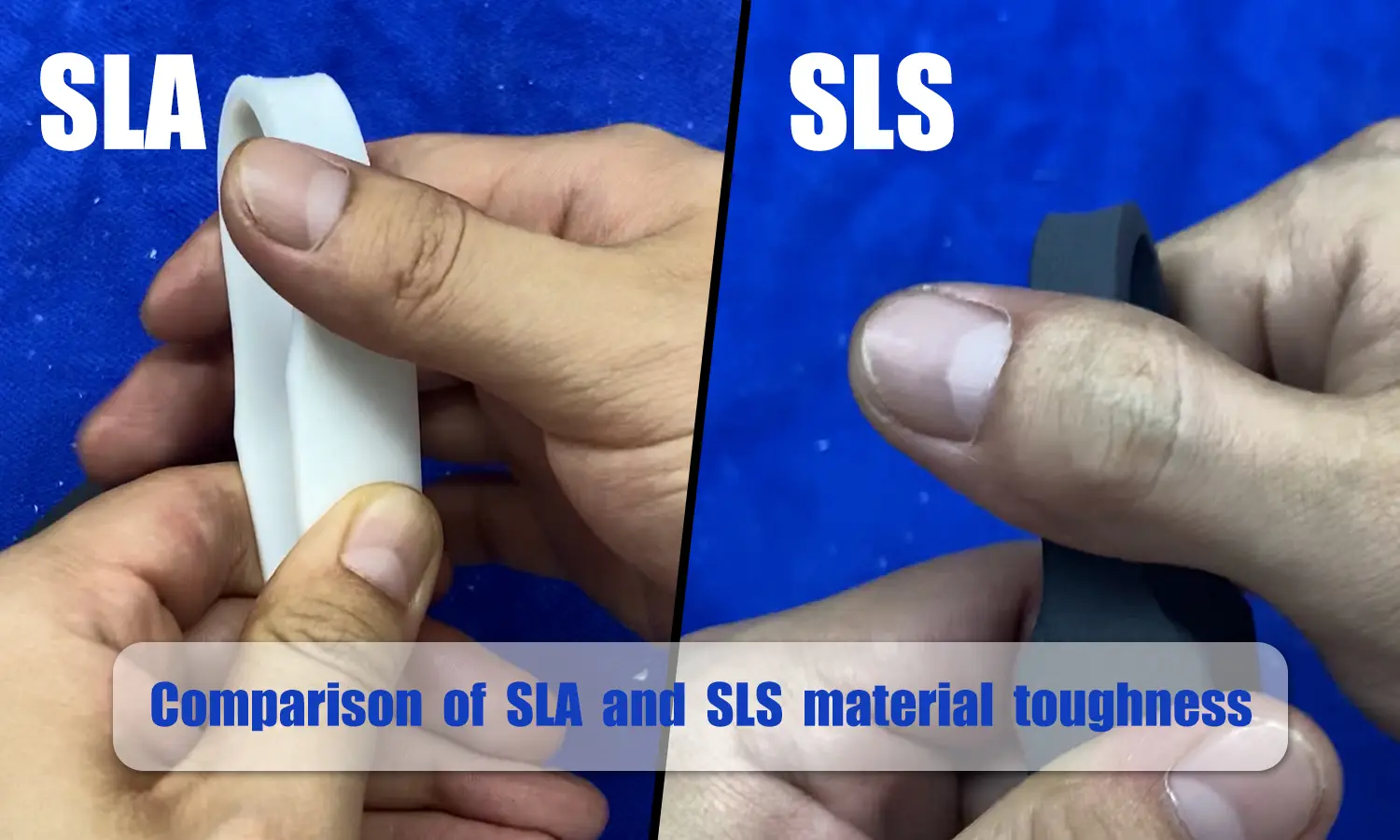
The SLA Printing Process: A Closer Look
The SLA printing process is a ballet of precision and technological grace, occurring in three main acts: the pre-printing preparations, the printing process itself, and the post-processing finish.
Pre-Printing Stage
Designing the 3D Model
Before the printing can begin, one must design a 3D model. This is typically done using CAD (Computer-Aided Design) software. The model is then converted into a file format compatible with the SLA printer, usually STL or OBJ.
Tips for Optimizing Design for SLA Printing:
- Ensure wall thickness meets the minimum requirement.
- Design supports for overhangs and complex structures.
- Consider orientation for the best surface quality.
Preparing the Printer and Resin
Selecting the right resin and setting up the printer are crucial steps. Resins vary in properties, with options ranging from standard resins for general use to specialty resins for specific mechanical properties or castability.
Printer Setup Checklist:
- Calibrate the build platform for even layer application.
- Strain the resin to avoid any particulates.
- Top up the resin tank, ensuring there’s enough to complete the print.
Printing Stage
The Role of the Laser in SLA
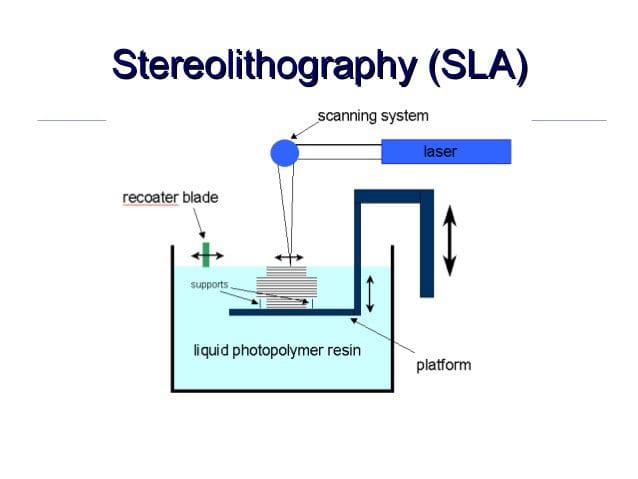
The laser in an SLA printer is the heart of the operation. It cures the resin with pinpoint accuracy, guided by the galvanometers. The settings of the laser, such as power, speed, and cure time, are meticulously adjusted to match the resin’s properties and the desired outcome.
Layer-by-Layer Building
SLA printers create objects one layer at a time. The thickness of these layers can be as fine as 25 microns, or even less, allowing for an exceptional level of detail.
Factors Affecting Layer Resolution:
- Laser Precision: The finer the laser point, the more detailed the print.
- Resin Properties: Different resins react differently to the laser’s light.
- Printer Settings: Fine-tuning the settings can improve the finish.
Post-Printing Stage
Washing and Curing
Once the print is complete, it’s bathed in isopropyl alcohol (IPA) to wash away any uncured resin. Afterward, it’s post-cured under UV light to achieve its final hardness and strength.
Finishing Touches
The final step is the finishing process, which may include sanding to remove any support marks, painting for aesthetics, or even additional curing for added stability.
SLA 3D printing is a dance of light and chemistry that brings the digital into the physical realm with unmatched finesse. It’s a process that has not only stood the test of time but continues to evolve, pushing the boundaries of what’s possible in additive manufacturing. Whether you’re creating prototypes, intricate models, or bespoke components, SLA offers a level of detail and finish that is truly a cut above.
Materials and Equipment in SLA 3D Printing
Dive into the core of SLA 3D printing, where the synergy between innovative materials and sophisticated equipment paves the way for the creation of objects with unparalleled precision. This section will guide you through the diverse resins that give life to your designs and the intricate machinery that makes it all possible.
Types of Resins Used in SLA Printing
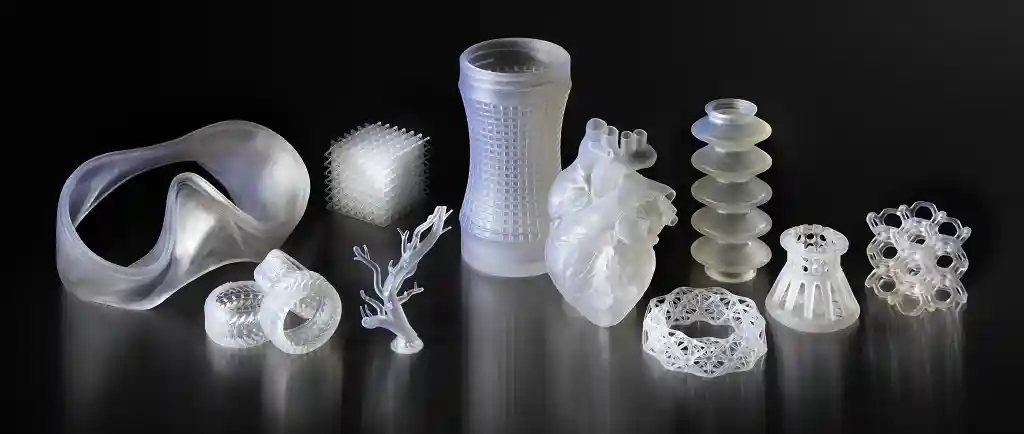
In the world of SLA 3D printing, resins are the lifeblood, offering a spectrum of properties that cater to various end-use applications. Each type of resin brings its unique characteristics to the table, influencing the durability, flexibility, and aesthetic of the final print.
Standard Resins:
- Clear Resin: Ideal for parts requiring translucency and a smooth, glossy finish.
- White Resin: Perfect for models that need a high level of detail with a neutral tone.
- Tough Resin: Designed for parts that require higher tensile strength and durability.
Engineering Resins:
- High-Temperature Resin: Best for components that will undergo sustained heat exposure.
- Durable Resin: Offers the most flexibility, simulating polyethylene plastics, ideal for containers and packaging prototypes.
- Rigid Resin: Infused with glass or ceramic for added stiffness, suitable for industrial parts and molds.
Specialty Resins:
- Castable Resin: Leaves no ash when burned out, perfect for jewelry and dental applications requiring casting.
- Biocompatible Resin: Certified for medical use, such as surgical guides or hearing aids.
Resin Type | Properties | Applications |
Standard | Detail, Aesthetics | Prototypes, Display Models |
Engineering | Mechanical Strength | Functional Parts, Thermal Exposure |
Specialty | Unique Capabilities | Casting, Direct Use in Healthcare |
The SLA Printer Hardware
The SLA printer is a marvel of engineering, a machine that harnesses light to transform liquid into solid. Understanding its components is key to mastering the printing process.
Core Components of an SLA Printer:
- Resin Tank: A container that holds the photopolymer resin, typically made of transparent material to allow the passage of the laser.
- Build Platform: The stage where the object is built, moving upward incrementally as each layer is cured.
- Ultraviolet Laser: The precision tool that solidifies the resin, its beam directed by mirrors controlled by galvanometers.
- Galvanometers (Galvos): Motorized mirrors that aim the laser across the tank, defining the shape of each layer with extraordinary accuracy.
Maintenance and Calibration of the Printer:
- Cleaning the Resin Tank: Essential to prevent contamination and ensure flawless prints.
- Checking the Laser Pathway: Regular inspection and cleaning to maintain the quality of the laser’s focus.
- Updating Firmware: Keeping the printer’s software up-to-date ensures optimal performance and access to the latest features.
Printer Calibration Checklist:
- Leveling the Build Platform: Ensures that each layer is uniformly cured across the entire build area.
- Fine-Tuning the Laser: Adjusting the intensity and spot size for the resin being used.
- Galvo Calibration: Ensuring the laser hits the correct coordinates for precise layer curing.
SLA 3D printing is not just about what you make; it’s about the journey from liquid to solid. The resins and the printer are your companions on this voyage, each playing a pivotal role in bringing your vision to life. With the right resin and a finely tuned printer, the possibilities are as limitless as your imagination. Whether you’re crafting intricate jewelry, robust engineering prototypes, or delicate medical devices, the materials and equipment of SLA 3D printing stand ready to transform your ideas into reality.
Applications of SLA 3D Printing
Embark on a journey through the diverse landscapes where SLA 3D printing leaves its indelible mark. From the precision-required realms of industrial design to the life-altering field of medicine, SLA 3D printing is not just a tool but a transformative process that reshapes how we approach fabrication and design. In this exploration, we’ll uncover the myriad of applications where SLA’s precision and versatility shine.
Industrial Applications
In the industrial sector, SLA 3D printing is revered for its ability to produce parts with tight tolerances and smooth finishes, making it an invaluable asset for a range of applications.
Prototyping:
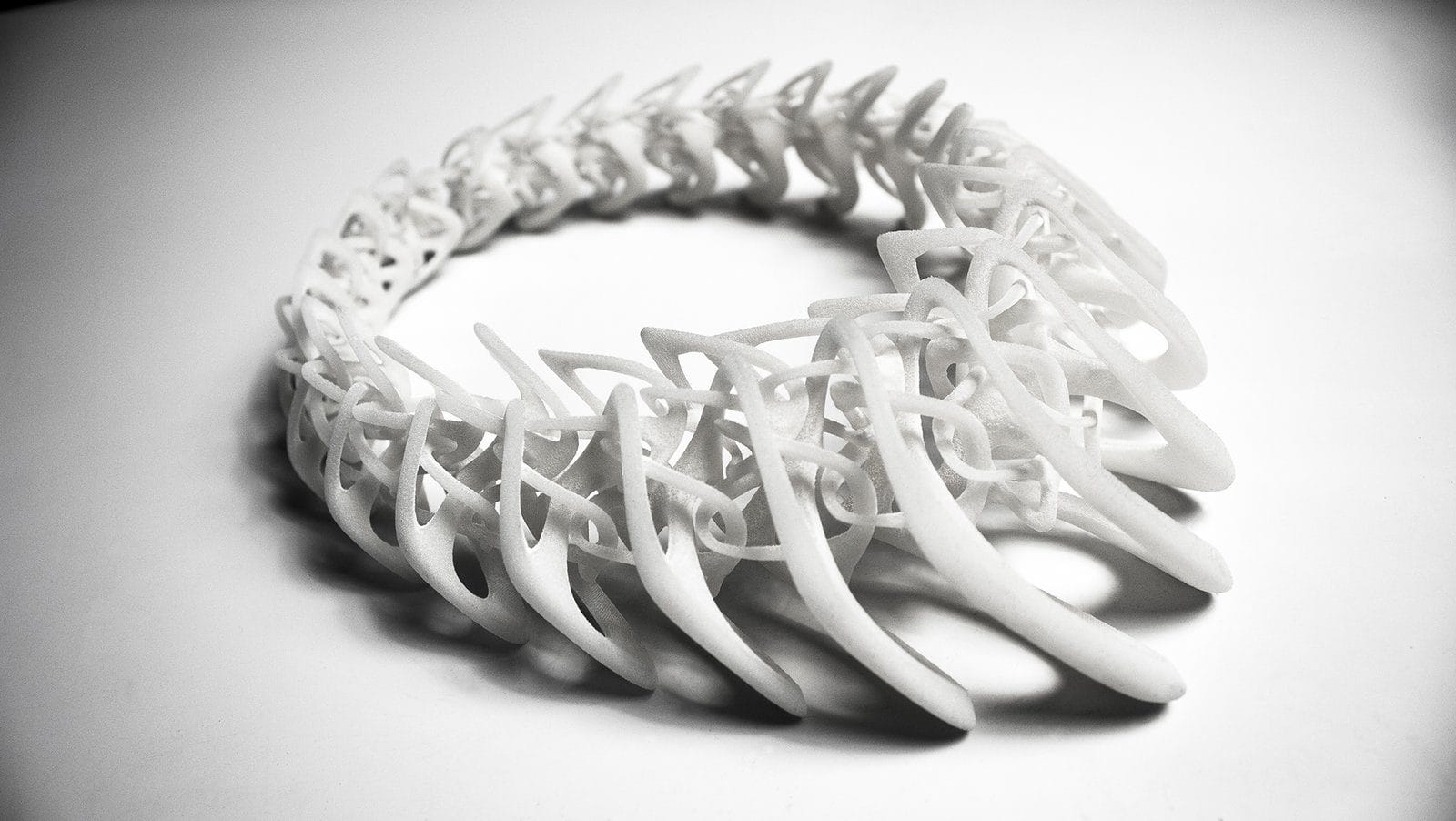
- Design Verification: Test the form, fit, and function of prototypes before committing to mass production.
- Complex Geometries: Create intricate designs that are impossible to achieve with traditional manufacturing methods.
Tooling:
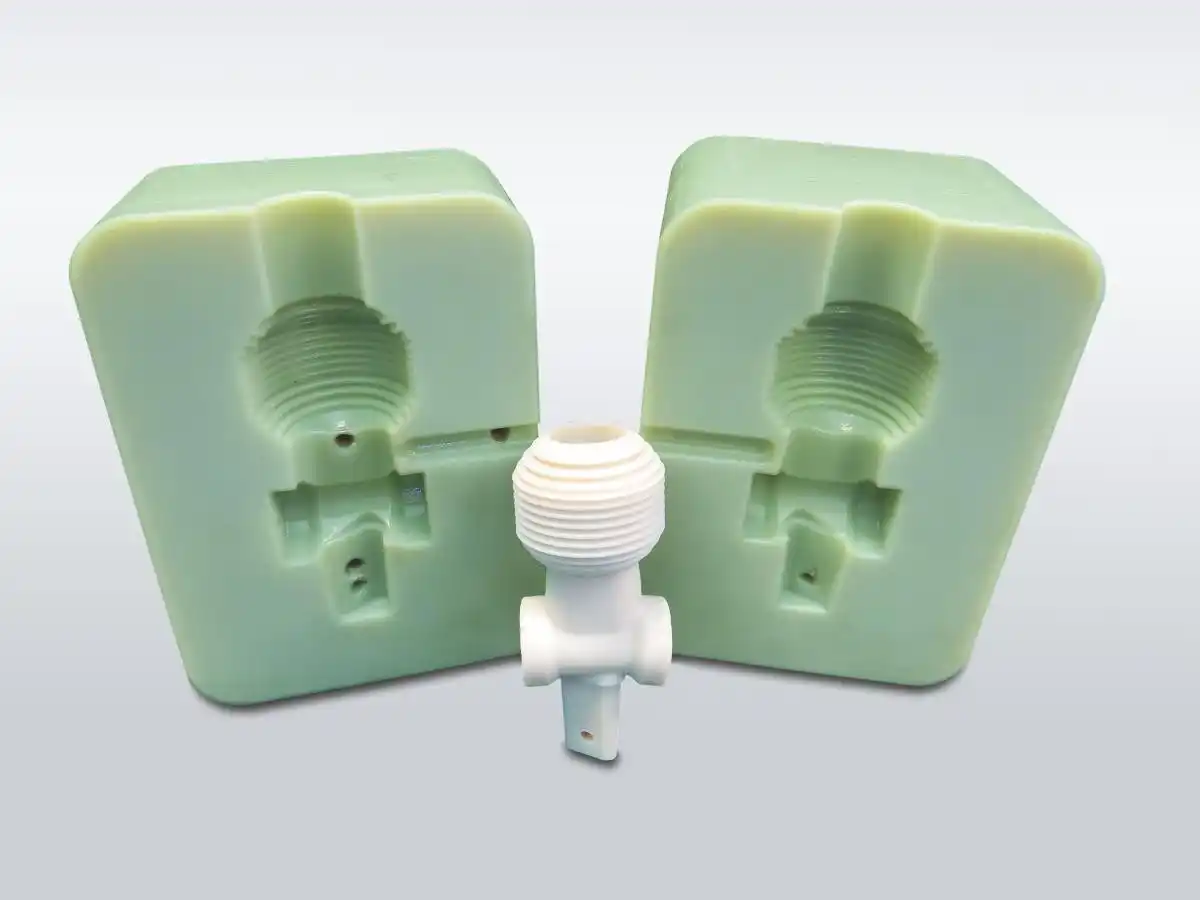
- Injection Molds: Produce small batches of injection-molded prototypes quickly and cost-effectively.
- Jigs and Fixtures: Fabricate custom tools that aid in the manufacturing process, enhancing precision and efficiency.
Production Parts:
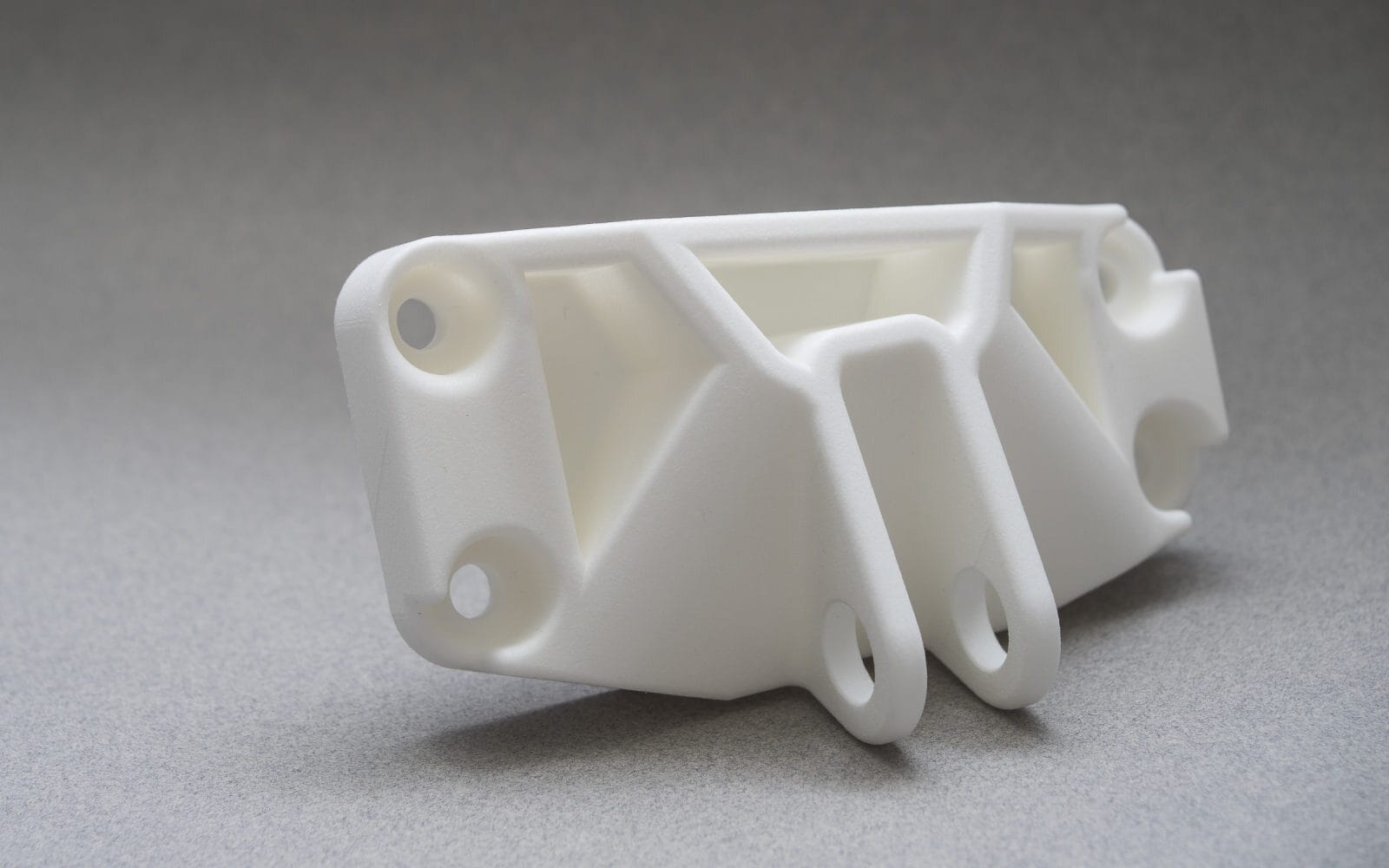
- End-use Components: Manufacture parts for final products, particularly in small volumes where traditional tooling would be prohibitively expensive.
- Customization: Tailor components to specific requirements or customer personalization.
Medical and Dental Applications
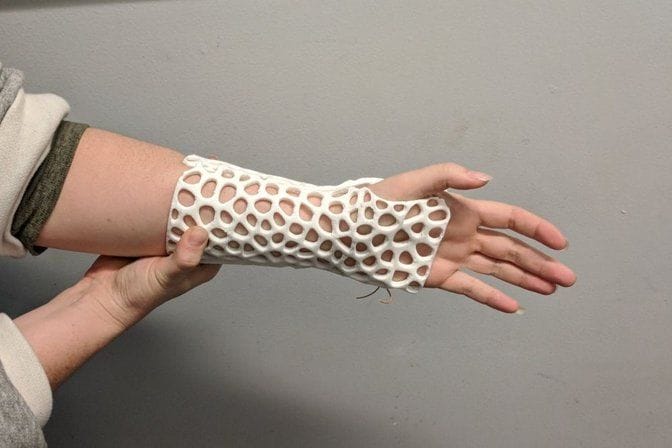
The precision and biocompatibility of certain SLA resins have opened up new frontiers in medical and dental practices.
Custom Prosthetics:
- Personalized Fit: Create prosthetics tailored to the individual for improved comfort and functionality.
- Rapid Prototyping: Quickly iterate on design to perfect the prosthetic’s form and fit.
Dental Devices:
- Dental Models: Produce accurate models for planning and practice.
- Orthodontic Appliances: Fabricate retainers and aligners customized to the patient.
Bioprinting:
- Tissue Engineering: Experiment with scaffolds for tissue regeneration.
- Research Models: Create anatomical models for educational and research purposes.
Consumer Products
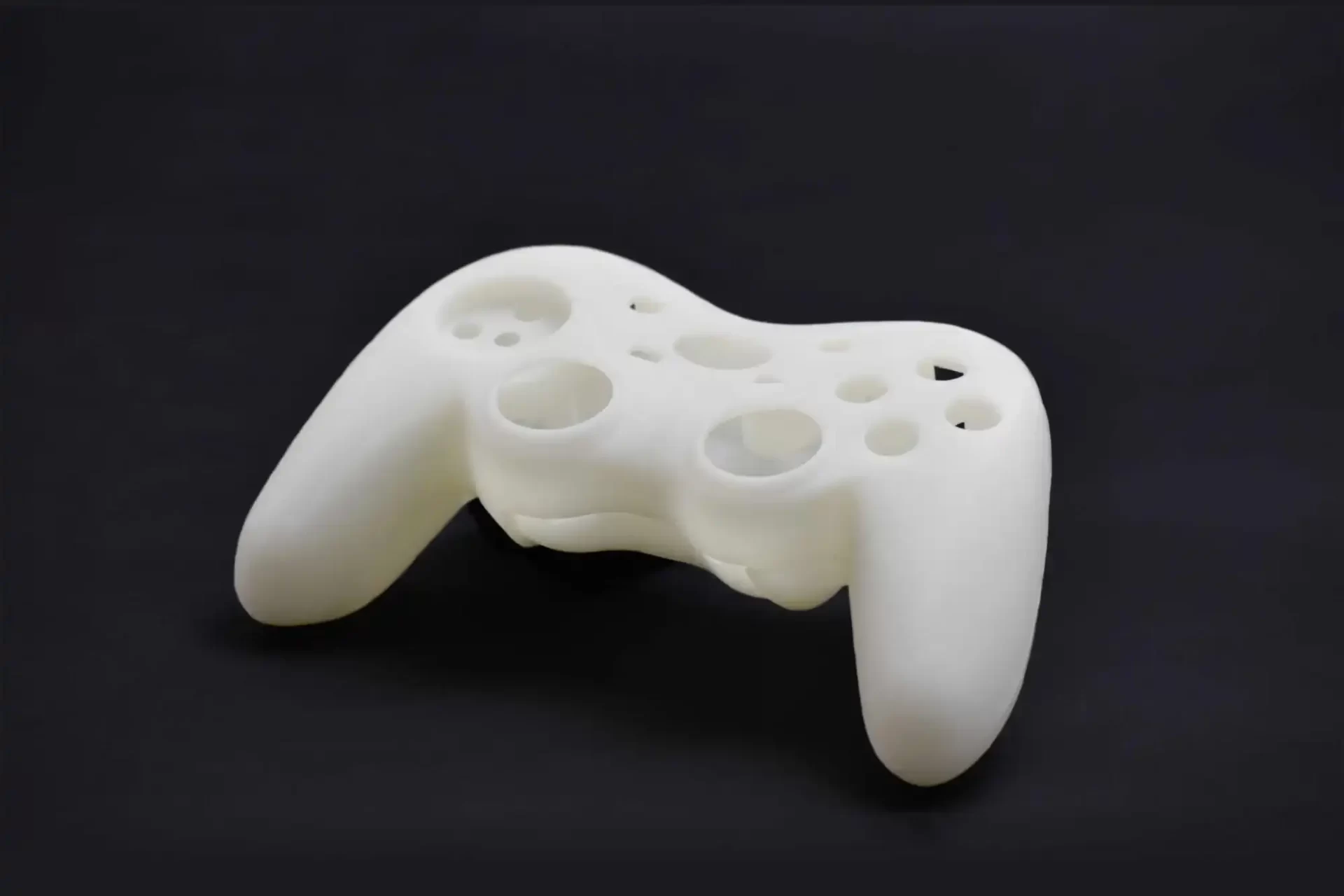
SLA 3D printing is not confined to the realms of industry and healthcare. It also caters to the consumer market, providing bespoke products and intricate designs.
Jewelry:
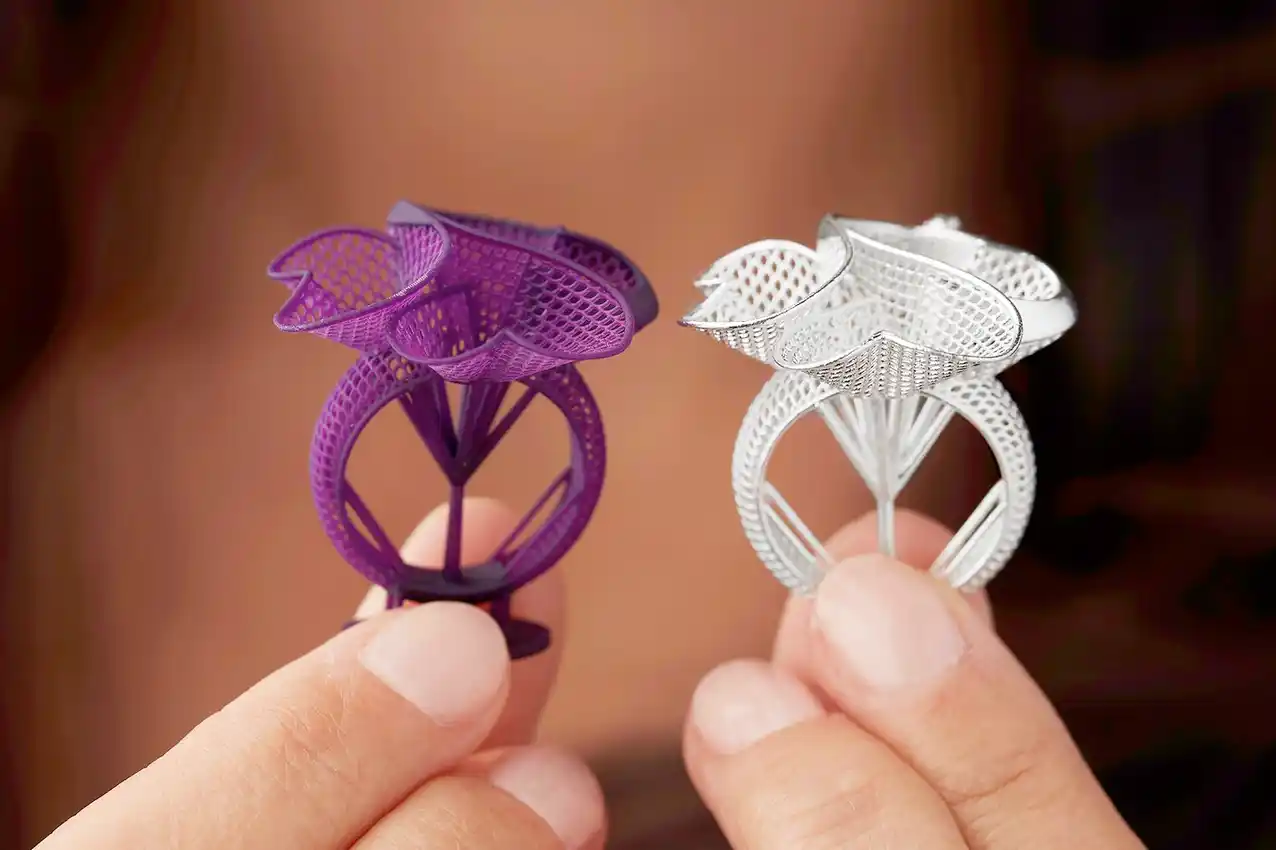
- High Detail: Craft intricate patterns and delicate features with a high-quality finish.
- Custom Designs: Offer personalized jewelry that caters to individual tastes and styles.
Art and Design:
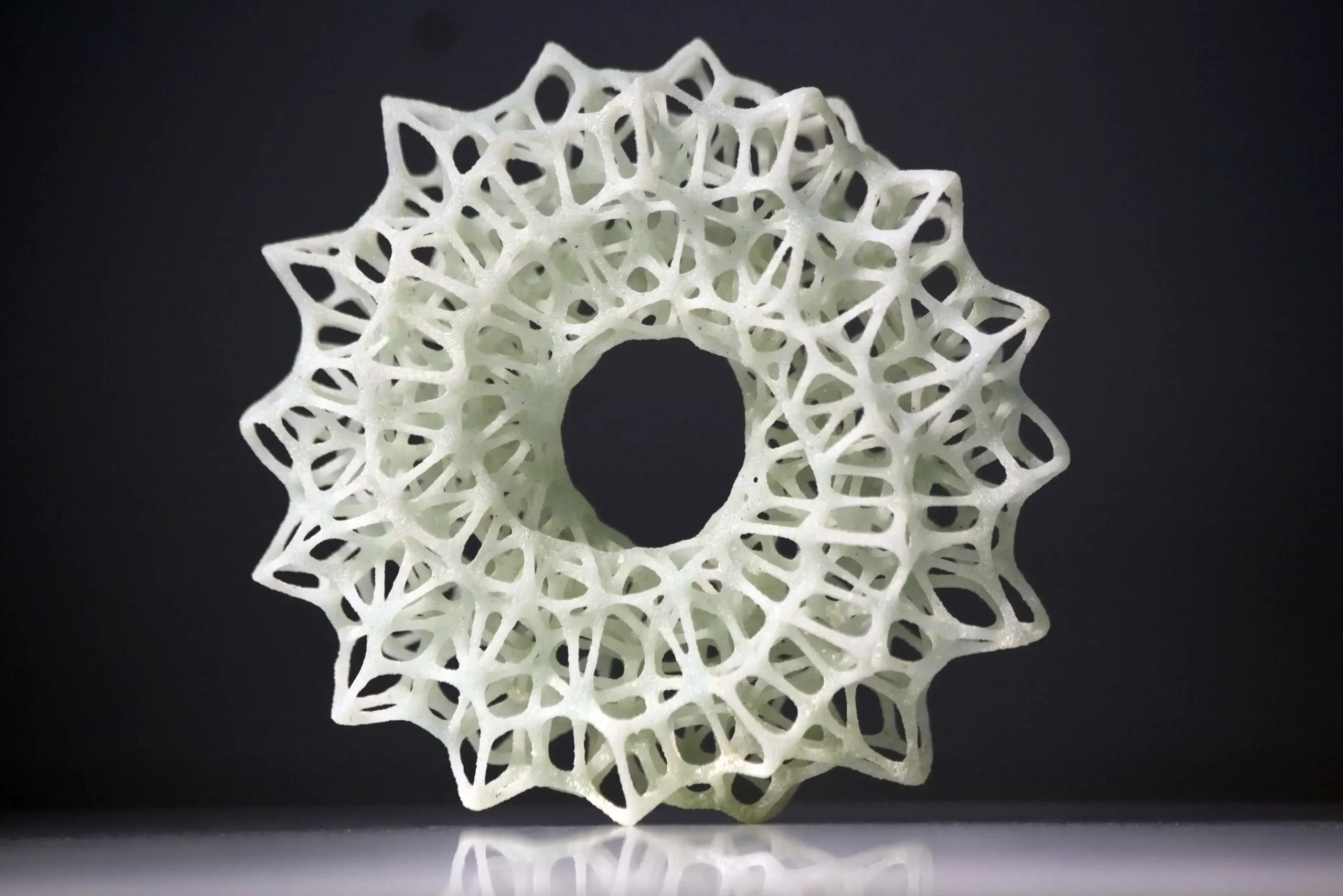
- Complex Art Pieces: Bring to life complex art installations that require a high level of detail.
- Architectural Models: Create detailed scale models of buildings for presentations and displays.
Gaming Miniatures:
- Fine Features: Produce gaming pieces with intricate designs and fine details.
- Rapid Prototyping: Quickly iterate on designs to meet the fast-paced demand of the gaming industry.
SLA 3D printing’s applications are as varied as they are groundbreaking. It’s a technology that not only streamlines the manufacturing process but also democratizes the production of complex, customized, and precise objects. Whether it’s a prototype that leads to a groundbreaking product, a dental device that brings a smile to someone’s face, or a piece of art that inspires awe, SLA 3D printing is the silent partner that brings these visions to life with meticulous detail and boundless potential.
Advantages and Limitations of SLA Printing
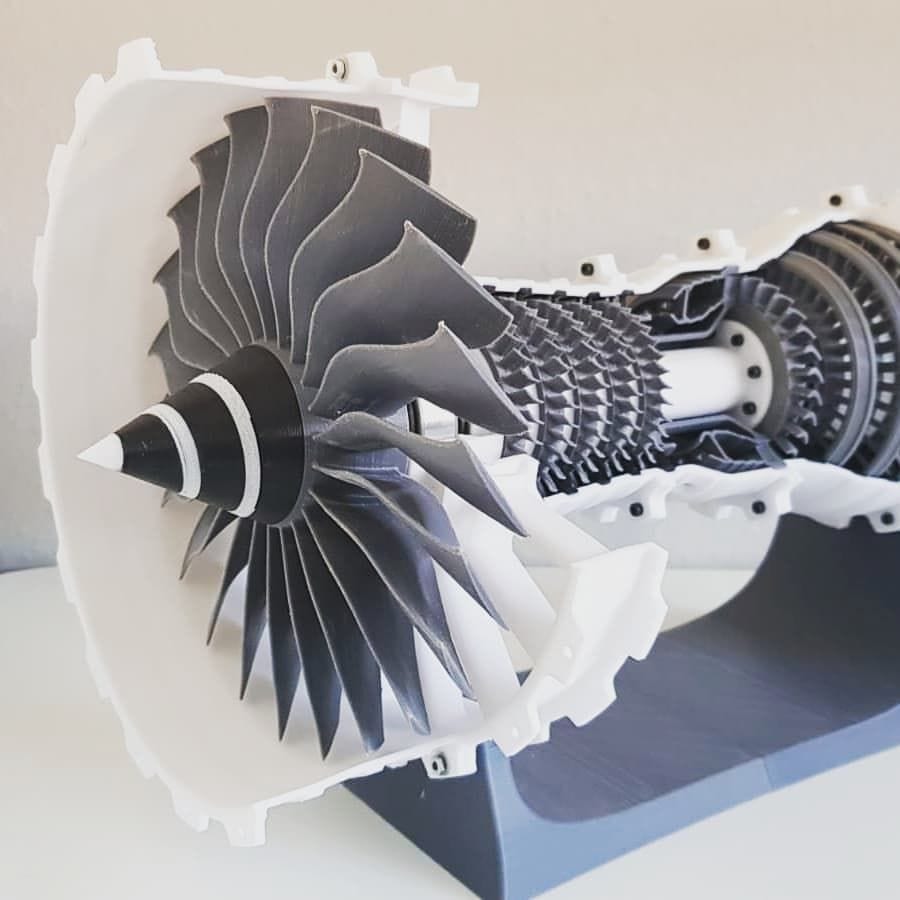
SLA 3D printing, a symphony of light and resin, has carved its niche in the manufacturing world with its unique capabilities. Yet, like any technology, it comes with its own set of strengths and challenges. In this detailed examination, we will navigate through the advantages that make SLA a preferred choice for many and the limitations that one must strategize around to fully leverage this innovative technology.
Advantages of SLA Printing
The allure of SLA printing lies in its exceptional ability to produce parts with high accuracy and a smooth surface finish, among other benefits.
Precision and Detail:
- High Resolution: SLA printers can achieve incredibly fine details, making them ideal for intricate designs.
- Accuracy: The precision of the laser allows for tight tolerances in the production of parts.
Surface Finish Quality:
- Smooth Surfaces: SLA parts have a naturally smooth finish, reducing the need for post-processing.
- Aesthetic Qualities: The quality of the surfaces makes SLA prints particularly suitable for visible end-use parts.
Material Versatility:
- Range of Resins: With a wide array of resins available, SLA printing can produce parts with varied properties, from rigid to flexible, transparent to opaque.
- Functional Prototypes: The ability to simulate different materials allows for functional testing of prototypes in conditions similar to the final product.
Limitations and Challenges
Despite its impressive capabilities, SLA printing is not without its drawbacks. Understanding these limitations is crucial for optimizing the use of SLA technology.
Printing Size Limitations:
- Build Volume: SLA printers typically have a smaller build volume compared to other 3D printing technologies, which can limit the size of parts that can be printed in one piece.
Post-Processing Requirements:
- Cleaning: SLA prints require cleaning to remove any uncured resin, which can be a messy and time-consuming process.
- Curing: Additional curing is often necessary to achieve the final material properties, necessitating extra equipment and time.
Resin Handling and Safety:
- Chemical Sensitivity: Resins can be toxic, and handling them requires care, including the use of gloves and proper ventilation.
- Storage and Disposal: Proper storage to prevent premature curing and safe disposal of used resin and contaminated materials are important considerations.
Cost Considerations:
- Resin Expense: The materials used in SLA printing can be more expensive than those used in other forms of 3D printing, impacting the cost-effectiveness for large runs.
- Machine Maintenance: Regular maintenance of the printer and its components, such as the resin tank and the laser, can add to the overall operating costs.
SLA 3D printing is a technology that marries the meticulousness of lasers with the versatility of resins to create objects of beauty and function. Its advantages make it a powerful tool for applications that demand precision and a high-quality finish. However, its limitations remind us that careful planning and consideration are essential to harness its full potential. Whether you’re an engineer, designer, or hobbyist, understanding both the strengths and constraints of SLA printing will empower you to make informed decisions and push the boundaries of what’s possible in the realm of 3D manufacturing.
Best Practices for SLA 3D Printing
To harness the full potential of SLA 3D printing, one must navigate the nuances of its process with finesse and precision. It’s a dance of technology and technique that, when performed correctly, yields results that are nothing short of extraordinary. In this segment, we delve into the best practices that are the keystones of successful SLA printing, ensuring that each print not only meets but exceeds expectations.
Design Optimization for SLA
The journey to a flawless SLA print begins long before the printer starts, right at the heart of the design phase. Here, certain considerations must be made to adapt to the unique capabilities and requirements of SLA technology.
Supports and Orientation:
- Strategic Support Placement: Design supports to facilitate easy removal and minimize post-processing, while ensuring the stability of the structure during printing.
- Optimal Orientation: Position your model to balance the print’s success with the final appearance, considering factors like gravity, print time, and resin usage.
Hollowing and Escape Holes:
- Internal Stress Reduction: Hollowing out your model can prevent warping and reduce the amount of resin used, saving costs and reducing internal stresses.
- Escape Holes: Ensure that any hollowed design includes holes for excess resin to escape, preventing deformation and pressure buildup.
Wall Thickness:
- Minimum Thickness: Adhere to the minimum recommended wall thickness to prevent breakage or warping.
- Uniformity: Aim for uniform wall thickness where possible to promote even curing and structural integrity.
Ensuring Quality and Accuracy
Quality and accuracy in SLA 3D printing are the byproducts of meticulous preparation and maintenance. A well-calibrated machine is the bedrock upon which precision is built.
Calibration and Testing:
- Regular Calibration: Keep your printer in top condition with regular calibration of the build platform and laser.
- Test Prints: Run test prints to ensure that the calibration has been successful and to adjust as necessary.
Troubleshooting Common Issues:
- Resin Temperature: Maintain the resin at a consistent temperature to ensure optimal viscosity and curing properties.
- Layer Adhesion: Monitor and adjust the fine-tuning settings if you notice issues with layer adhesion during prints.
- Laser Focus: Regularly check the focus of the laser as even slight deviations can lead to inaccuracies in the print.
Printer Maintenance:
- Clean Components: Keep the resin tank, build platform, and other components clean to prevent contamination and defects.
- Firmware Updates: Install firmware updates promptly to benefit from the latest improvements and fixes.
Documentation and Logs:
- Keep a Log: Document your print settings, maintenance schedules, and any issues encountered with their resolutions.
- Review and Refine: Use your logs to review past prints, identify patterns, and refine your processes for better results.
SLA 3D printing is akin to a high-stakes performance where every detail contributes to the final show. By adhering to these best practices, you can ensure that each layer of your print is a testament to the technology’s potential. Whether you’re creating a prototype, a piece of art, or a functional part, these guidelines will help you achieve the high resolution, accuracy, and immaculate surface finish that SLA is renowned for. Embrace the discipline these practices demand, and watch as your prints set new standards of excellence.
The Future of SLA 3D Printing
As we stand on the precipice of technological advancement, SLA 3D printing gazes into the horizon of possibility, ready to leap into a future rife with innovation and growth. This technology, once a fledgling idea, has burgeoned into a cornerstone of modern manufacturing and prototyping. In this section, we explore the burgeoning trends, potential advancements, and the exciting trajectory of SLA 3D printing.
Innovations in SLA Technology
The relentless pursuit of perfection drives the evolution of SLA printing, with researchers and engineers tirelessly working to push the boundaries of what’s possible.
New Resin Formulations:
- Eco-Friendly Resins: Development of biodegradable and bio-based resins to reduce environmental impact.
- Advanced Mechanical Properties: Creation of resins with enhanced strength, flexibility, and thermal resistance to open up new application areas.
Advanced Printer Features:
- Increased Print Speed: Innovations aimed at accelerating the printing process without sacrificing quality.
- Larger Build Volumes: Expansion of print area to accommodate bigger models or batch production of smaller parts.
Software Enhancements:
- Improved Slicing Algorithms: Software that can more efficiently translate designs into printable layers, optimizing print success and material usage.
- AI-Driven Quality Assurance: Integration of AI to predict and correct potential issues before they occur, improving reliability and consistency.
Trends and Predictions
The trajectory of SLA 3D printing is not just shaped by technological advancements but also by the changing tides of industry demands and consumer expectations.
Industry Adoption and Growth:
- Customization: As consumers increasingly demand personalized products, SLA printing’s ability to produce bespoke items efficiently will become even more valuable.
- Medical Advancements: Continued growth in the medical sector, with SLA printing playing a pivotal role in personalized healthcare solutions, from prosthetics to bioprinting.
Potential Future Applications:
- Construction: Exploration into printing large-scale structures or components for the construction industry.
- Electronics: Incorporation of conductive materials to print components with embedded wiring or circuitry.
Educational Impact:
- Increased Accessibility: As prices continue to drop and user-friendliness improves, SLA printers will become more accessible to educational institutions, fostering a new generation of designers and engineers.
The future of SLA 3D printing is a tapestry woven with threads of potential, each innovation a color added to the vibrant picture of what this technology will become. It’s a future that promises to revolutionize industries, empower creators, and redefine what’s possible in manufacturing and beyond. As we look forward to this bright and promising future, one thing is certain: SLA 3D printing will continue to be a beacon of innovation, guiding us towards a world where the only limit is our imagination.
Conclusion
As we draw the curtains on our in-depth exploration of SLA 3D printing, it’s clear that this technology is not just a method of manufacturing but a transformative force in the realm of production and design. From the meticulous process that begins with a vat of liquid resin to the final, post-processed piece that stands as a testament to precision, SLA 3D printing has proven its worth across a multitude of applications.
SLA printing, with its high resolution and superior surface finish, has set a standard for what can be achieved with additive manufacturing. It has empowered designers to push the boundaries of complexity, enabled engineers to iterate with rapid prototyping, and allowed medical professionals to tailor solutions to individual patient needs.
Yet, this journey through the layers of SLA 3D printing has also shed light on the challenges and limitations that come with such a sophisticated technology. We’ve seen that considerations around size, post-processing, and material handling are as much a part of SLA printing as the stunning results it can produce.
As we look to the future, the trajectory of SLA technology is poised for even greater heights. With advancements in resin chemistry, printer capabilities, and software algorithms, the potential for SLA to further revolutionize industries and hobbies alike is immense. The ongoing innovations suggest a future where SLA 3D printing could become even more accessible, efficient, and versatile.
In closing, SLA 3D printing stands as a beacon of high-fidelity manufacturing, a process that has matured from its nascent stages to a robust solution for a wide array of printing needs. Whether you are a seasoned professional or an enthusiastic novice, the world of SLA 3D printing offers a canvas limited only by the bounds of your creativity. As the technology continues to evolve, so too will the possibilities it unlocks, ensuring that SLA 3D printing remains at the forefront of the 3D printing revolution.
FAQs
To further aid your understanding, let’s address some frequently asked questions about SLA 3D printing:
- What is the main advantage of SLA over other 3D printing technologies?
- The main advantage of SLA is its ability to produce parts with very high detail and a smooth surface finish, making it ideal for applications where precision is paramount.
2. Can SLA printers produce large parts?
- While SLA printers typically have smaller build volumes than some other 3D printing technologies, they can produce large parts by printing in sections and then assembling them post-processing.
3. Are SLA printed parts durable?
- Yes, with the right resin and post-processing, SLA printed parts can be quite durable and suitable for a range of functional applications.
4. How environmentally friendly is SLA printing?
- The environmental impact of SLA printing depends on the type of resin used. There are eco-friendly resins available that are biodegradable or derived from bio-based sources.
5. What industries benefit most from SLA printing?
- Industries that benefit most from SLA printing include dental and medical, jewelry, consumer goods, and any field that requires detailed prototypes or end-use parts with a high-quality finish.