In the dynamic realm of 3D printing, Stereolithography (SLA) stands out as a revolutionary technology. It uses a high – precision laser to transform liquid resin into intricate 3D objects layer by layer. This process is not only a marvel of modern engineering but also has far – reaching implications across diverse industries, from rapid prototyping and dental applications to jewelry design and aerospace manufacturing.
The Fundamentals of SLA 3D Printing
SLA is a trailblazing technology in 3D printing. At its core, it cures liquid resin into solid structures using a laser, enabling the creation of highly detailed and precise objects. Understanding its basic principles, materials, components, and safety aspects is crucial for anyone interested in this field.
The SLA Process Unveiled
The SLA process can be divided into three main stages: model preparation, printing, and post – processing.
During model preparation, a 3D model is first created with computer – aided design (CAD) software like SolidWorks, Autodesk Fusion 360, or Tinkercad. The model is then saved in a compatible format, such as STL or OBJ. Next, specialized slicing software, such as Chitubox, PreForm, or Lychee Slicer, slices the 3D model into thin layers. Users need to select appropriate layer thickness (usually ranging from 25 to 100 microns), determine the optimal orientation for printing to minimize support requirements and enhance strength, and add support structures where necessary.
In the printing stage, the printer’s build platform is submerged in a vat of liquid photopolymer resin. A high – powered UV laser is activated, and its beam is directed onto the resin’s surface. The laser moves according to the sliced data, curing the resin layer by layer. After each layer is cured, the build platform lifts slightly, allowing fresh resin to flow in. This process repeats until the entire model is printed.
Once the printing is complete, post – processing begins. The printed object is carefully removed from the build platform using tools like spatulas or pliers. It is then cleaned with isopropyl alcohol (IPA) to remove any uncured resin. For a more thorough clean, an ultrasonic cleaner can be used. Finally, the object undergoes further curing under UV light to enhance its strength and durability.
Key Components of SLA 3D Printing
SLA 3D printing relies on several key components. The resin tank holds the liquid photopolymer resin used for printing. The build platform is the surface where the object is formed and can move vertically. The laser system, a high – precision UV laser, cures the resin layer by layer. The control software manages the entire printing process, including slicing the model and controlling the printer’s operations.
Materials for SLA 3D Printing
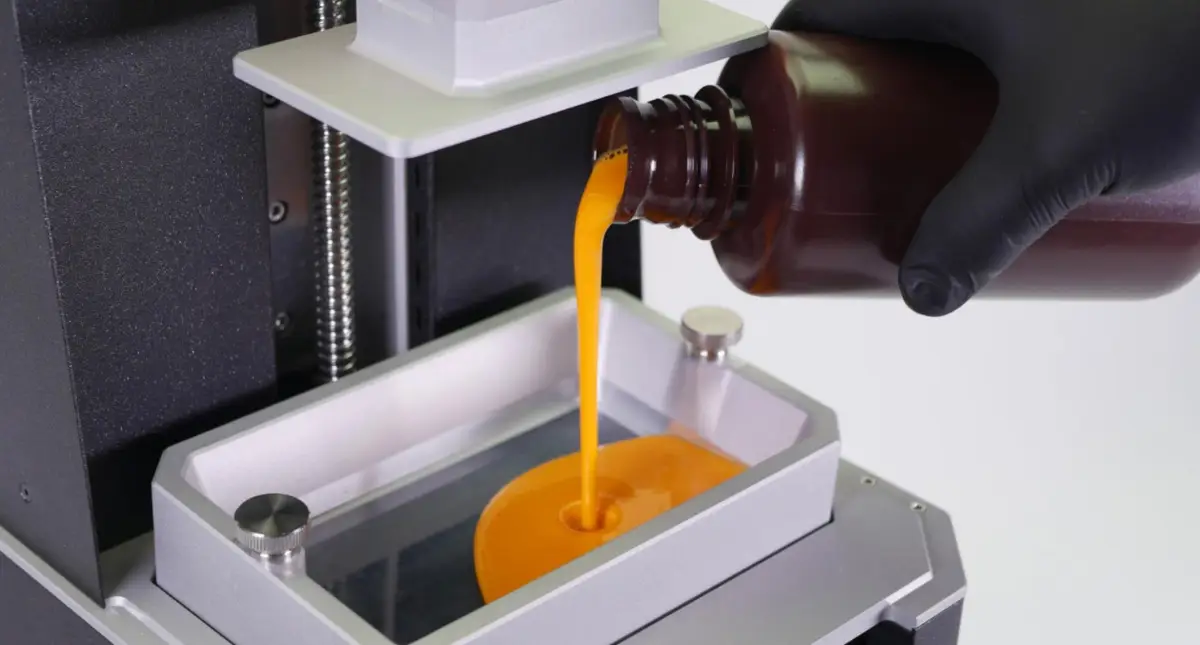
The choice of material significantly impacts the quality, strength, and finish of SLA – printed objects. Standard resins offer good detail, a smooth finish, and reasonable durability, making them suitable for prototyping and general – purpose models. Flexible resins have rubber – like flexibility and good elongation, which are useful for functional prototypes and soft – touch applications. Castable resins are designed specifically for jewelry and dental applications, as they burn out cleanly during investment casting. Dental resins are biocompatible and highly precise, used for dental models, surgical guides, and orthodontic devices. High – temperature resins can resist high temperatures and thermal deformation, making them ideal for parts that require thermal stability.
Safety Considerations in SLA Printing
When working with SLA 3D printing, safety is of utmost importance. Personal protective equipment (PPE), such as gloves, goggles, and a mask, should be worn to prevent skin and eye contact with the resin. The working area must be well – ventilated to minimize the inhalation of fumes. Resins should be stored in a cool, dark place, away from direct sunlight and heat sources to prevent degradation.
The Intricacies of the SLA Printing Process
Pre – Processing: Laying the Foundation
Before printing, preparing the 3D model is a critical step. CAD software is used to create the model, and then slicing software divides it into layers. The layer thickness selection is crucial; thinner layers result in finer details but longer print times. The model’s orientation also matters. For example, in a complex jewelry design, orienting the model correctly can reduce the need for supports and ensure the integrity of delicate features. Support structures are added where necessary, like under overhangs. For instance, when printing a model with a large, protruding section, supports prevent it from sagging or collapsing during printing.
Printing: The Laser’s Role
Once the model is sliced and ready, the printing process starts. The build platform is lowered into the resin tank, just below the resin’s surface. The high – powered UV laser is then activated. It moves across the resin surface, tracing out each cross – section of the model layer by layer. As it moves, the laser cures the resin. After each layer is completed, the platform lifts by the layer height, allowing fresh resin to flow in. This continuous process builds the object from the bottom up.
Post – Processing: Polishing the Final Product
Post – processing is essential for SLA – printed objects. After removing the print from the build platform, it is cleaned to remove uncured resin. IPA is commonly used for this purpose. For parts with intricate details, an ultrasonic cleaner can be highly effective. Once cleaned, the object is cured under UV light. This post – curing process significantly enhances the object’s strength and stability. For example, a dental model printed with SLA needs to be post – cured to ensure it can withstand the handling during dental procedures.
Tips for a Flawless SLA Printing Process
To ensure a successful SLA printing process, several tips should be followed. Regular printer calibration is essential for precise movements and accurate layer curing. Monitoring the resin level and quality is crucial; old or contaminated resin can lead to poor print quality. The printing environment also plays a role. Maintaining a stable temperature and humidity can prevent issues such as resin viscosity changes and laser performance fluctuations.
Precision and Accuracy in SLA Printing
Deciphering Laser Precision
The high – powered UV laser is the heart of SLA technology. It operates at a wavelength of around 405 nm, which is optimal for curing photopolymer resin. The laser beam’s spot size can be as small as 0.1 mm, allowing for the creation of fine details in printed objects. During the curing process, the laser precisely controls the energy delivered to different areas of the resin. This precision enables the production of sharp edges, intricate geometries, and fine details that are difficult to achieve with other printing methods. SLA printers use high – resolution motors and encoders to ensure accurate laser positioning, resulting in layer heights ranging from 25 to 100 microns, which contributes to the overall print detail.
Factors Influencing Precision
Although SLA is known for its high precision, several factors can affect print accuracy. Layer thickness has a direct impact; thinner layers offer better detail but increase print time. Different resins have varying curing characteristics, which can influence detail retention. For example, some resins may shrink more during curing, affecting the final dimensions of the print. Print speed can also be a factor; faster speeds may compromise accuracy, especially in complex designs. Environmental conditions, such as temperature and humidity, can change resin viscosity and laser performance, potentially leading to less precise prints.
Comparing SLA with Other 3D Printing Technologies
SLA’s precision sets it apart from other common 3D printing methods. Compared to Fused Deposition Modeling (FDM), which has a moderate precision of 0.1 – 0.4 mm and typical layer heights of 100 – 300 microns, SLA offers higher precision (up to 0.1 mm) and finer layer heights (25 – 100 microns). Selective Laser Sintering (SLS) has a precision range of 0.1 – 0.2 mm and layer heights of 100 – 200 microns. SLA is particularly suitable for applications that require intricate designs, such as jewelry making, dental applications, and high – fidelity prototyping.
Applications Benefiting from SLA’s Precision
SLA’s high precision makes it invaluable in several industries. In the dental field, it is used to create highly detailed dental models, surgical guides, and orthodontic appliances. For example, a surgical guide printed with SLA can help dentists perform procedures with greater accuracy. In jewelry design, SLA allows for the production of complex and detailed designs that can be directly cast or used as prototypes. In prototyping, SLA enables the development of high – fidelity prototypes where visual appearance and precise dimensions are crucial. In the aerospace and automotive industries, SLA is used to manufacture lightweight, complex components with strict tolerances and high strength – to – weight ratios.
Advantages of SLA 3D Printing
High Resolution and Detail
One of SLA’s most significant advantages is its ability to produce highly detailed and intricate designs. It can achieve layer resolutions as fine as 25 microns, enabling the reproduction of complex geometries. For instance, in jewelry design, it can capture the most delicate patterns. SLA – printed objects also have a smooth surface finish, which is a major advantage over other 3D printing methods, especially for applications where aesthetics are important.
Superior Surface Finish Quality
SLA prints typically have a superior surface finish. This means less post – processing is required compared to FDM parts. For example, a consumer product prototype printed with SLA can be presented to clients immediately after printing without extensive sanding or finishing. The smooth finish also enhances the visual appeal of products, making it ideal for medical device prototypes and marketing samples.
Material Versatility
SLA offers a wide range of photopolymer resins for different applications. Standard resins are great for general prototyping, while flexible resins are suitable for functional prototypes that require flexibility. Castable resins are specifically designed for jewelry and dental casting, and dental resins are biocompatible for medical use. High – temperature resins can withstand elevated temperatures, making them suitable for parts in high – heat environments.
Rapid Prototyping Capabilities
SLA is well – suited for rapid prototyping. The layer – by – layer curing process allows for quick turnaround times. Designers can iterate rapidly on their models, which is crucial for reducing time – to – market. For example, in the automotive industry, SLA can be used to quickly produce prototypes for new car parts, allowing for faster testing and validation.
Complex Geometries and Design Freedom
SLA printing excels in creating complex geometries that are difficult or impossible to achieve with traditional manufacturing methods. It has no design restrictions like traditional machining or injection molding. Designers can create intricate internal structures and organic shapes without the need for complex tooling. For instance, in aerospace, lightweight lattice structures can be designed and printed using SLA, reducing material usage while maintaining strength.
Environmentally Friendly Options
Many SLA resins are being developed with environmental considerations in mind. Biodegradable resins are becoming more common, allowing users to minimize their ecological footprint. Additionally, SLA’s additive manufacturing nature means that material is used only where needed, resulting in less waste compared to subtractive manufacturing processes.
Limitations of SLA 3D Printing
Build Size Limitations
SLA printing has limitations in terms of build size. Most SLA printers have a limited build volume, typically ranging from 120 mm x 120 mm x 150 mm to 300 mm x 300 mm x 400 mm. For larger objects, users may need to print sections separately and assemble them later. This not only complicates the design process but also increases time and effort.
Post – Processing Time and Complexity
Although SLA prints have a good surface finish, they require significant post – processing. Cleaning the printed parts to remove uncured resin often involves using IPA and may require specialized equipment. The post – curing process is essential for achieving optimal strength and durability but adds additional time to the overall workflow.
Cost of Materials and Equipment
SLA printing can be more expensive than other 3D printing methods. High – quality SLA printers can cost anywhere from $2,000 to over $10,000, which is a significant investment compared to more affordable FDM printers. Photopolymer resins are also more expensive than FDM filaments, with prices ranging from $50 to $300 per liter depending on the type and quality.
Limited Material Options
While SLA offers various resins, the range of materials is still more limited compared to other technologies. Many SLA resins do not match the mechanical properties of traditional thermoplastics used in FDM printing, such as strength and flexibility. Additionally, SLA prints often have lower heat resistance, restricting their use in applications exposed to high temperatures.
Handling and Safety Concerns
Working with SLA materials requires careful handling due to safety concerns. Many photopolymer resins are toxic and can cause skin irritation or other health issues if mishandled. Proper personal protective equipment must be worn during use. Resins also need to be stored properly to prevent degradation, which can lead to waste and increased costs.
Print Failure Risks
SLA prints are prone to failure. Adhesion issues may occur, where parts do not adhere properly to the build platform, especially if the surface is not adequately prepared. Variations in resin viscosity can affect layer curing and lead to inconsistent print quality, resulting in wasted materials and time.
Future Trends in SLA 3D Printing
Technological Innovations
Continuous Liquid Interface Production (CLIP) is a new SLA technology that allows for continuous printing instead of layer – by – layer curing. It uses a special oxygen – permeable window to maintain a curing interface while enabling the continuous flow of resin. This significantly increases print speed, reducing production time from hours to minutes, and also improves print quality by reducing layer adhesion issues.
Advanced laser systems are another area of innovation. High – power lasers are being developed to enhance curing speed and detail. These lasers can cure thicker layers more effectively, further reducing print times. Multi – laser systems, where SLA printers are equipped with multiple lasers, can simultaneously cure different areas of the print, improving efficiency and enabling larger builds.
Innovations in Materials
The demand for specialized applications is driving the development of new photopolymer resins. In the healthcare industry, biocompatible resins are in high demand for medical devices, dental applications, and surgical guides. In the future, more versatile resins that meet stringent biocompatibility standards are expected, expanding SLA’s use in medical applications.
High – performance resins are also being developed with enhanced mechanical properties, heat resistance, and flexibility. These materials will enable SLA to compete with traditional manufacturing methods for functional parts in industries like aerospace and automotive.
Industry – Specific Applications
In the automotive and aerospace sectors, SLA’s ability to produce high – fidelity prototypes quickly will continue to be valuable. As new materials emerge, SLA is expected to play a larger role in the production of end – use components that require lightweight, complex geometries. For example, in electric vehicle manufacturing, SLA – printed parts can help reduce vehicle weight and improve efficiency.
In the consumer goods industry, the rise of personalized products is driving the demand for SLA printing. It can be used for custom – made fashion items, electronics, and home goods. SLA’s rapid prototyping capabilities also make it ideal for small – batch production runs, allowing brands to test new designs without significant investment in tooling.
Integration with Other Technologies
SLA is likely to be integrated with other manufacturing technologies. Hybrid manufacturing, which combines SLA with methods like FDM or CNC machining, can leverage the strengths of each technology. For example, a part that requires high – detail features and robust mechanical properties can be produced by first printing the detailed parts with SLA and then machining or adding more robust elements with FDM.
Sustainability Initiatives
As environmental concerns grow, the 3D printing industry is moving towards more sustainable practices. The development of biodegradable and recyclable resins will be a priority for SLA. Additionally, innovations aimed at reducing energy consumption during the printing process will make SLA printing more sustainable.
Practical Tips for SLA 3D Printing
Choosing the Right SLA Printer
When selecting an SLA printer, consider the build volume. Assess the maximum size of the parts you plan to print and choose a printer with an appropriate build volume. Desktop SLA printers usually have build volumes in the range of 120 mm x 120 mm x 150 mm to 300 mm x 300 mm x 400 mm, while larger industrial printers can handle bigger projects.
Resolution and layer height are also important factors. Look for printers that offer adjustable layer heights, typically from 25 to 100 microns. If you need high – resolution prints for intricate designs, prioritize printers known for their precision.
Budget is a crucial consideration. SLA printers vary widely in price, from a few hundred to tens of thousands of dollars. Determine your budget and consider the essential features for your work. Also, factor in the cost of photopolymer resins, as they can significantly impact your overall expenses.
Best Practices for Successful Printing
Use reliable slicing software that is compatible with your printer. Pay close attention to settings such as layer height, exposure time, and support structures. Optimize the orientation of your model to minimize the need for supports and enhance strength. For example, if printing a tall, thin object, orient it vertically to reduce the need for additional supports.
Strategically place support structures in areas with overhangs or delicate features. You can use software tools to automatically generate supports or manually place them for better design optimization. Plan for support removal after printing, as it may require additional post – processing time.
Check the quality of your resin regularly. Ensure it is not expired and has been stored correctly. Old or improperly stored resin can lead to poor print quality. Be cautious when mixing different resin types, as compatibility issues can affect the final print.
Maintenance and Troubleshooting
After each print, clean the build platform to prevent residue buildup. A clean surface ensures better adhesion for future prints. Regularly inspect the UV laser window for clarity and cleanliness. Any debris or resin buildup can disrupt the curing process. Periodically check the resin vat for leaks or damages and replace any damaged components to avoid contamination.
If you encounter issues like poor adhesion to the build plate, it may be due to a dirty surface or incorrect Z – axis calibration. Clean the platform and recalibrate the Z – axis. Layer separation could be caused by incorrect exposure time or resin issues; adjust the exposure settings and check the resin quality. Print failures may result from incorrect support placement or printer calibration; optimize the support structures and recalibrate the printer. Surface imperfections can be due to dust particles or resin quality; clean the printing area and use high – quality resin.
Experiment and Iterate
Don’t be afraid to experiment with different settings, resins, and designs. Through trial and error, you can discover the optimal conditions for your prints. Keep a log of successful prints and the settings used. This documentation will help you refine your approach over time and achieve better results. For example, if you’re working on a specific type of jewelry design, testing different resin formulations and printing settings can lead to more detailed and durable final products.
Conclusion
Stereolithography (SLA) 3D printing is a remarkable technology with a wide range of applications. It uses a laser to cure liquid resin layer by layer, enabling the creation of highly detailed and precise objects. The process involves model preparation, printing, and post – processing, each step being crucial for a high – quality outcome.
SLA is renowned for its high precision, which is a result of factors like laser characteristics and the curing process. This precision allows for intricate designs and smooth surface finishes, setting it apart from other 3D printing methods. It also offers several advantages, including superior surface finish quality, material versatility, rapid prototyping capabilities, and the ability to create complex geometries. These benefits make it suitable for various industries, from automotive and aerospace to dental and jewelry.
However, SLA has its limitations. Build size constraints mean that larger objects may need to be printed in sections and assembled later. The post – processing requirements are time – consuming and complex, and the cost of materials and equipment is relatively high. Additionally, the range of available materials is somewhat limited, and there are handling and safety concerns to consider.
Looking ahead, the future of SLA 3D printing is promising. Technological innovations such as Continuous Liquid Interface Production (CLIP) and advanced laser systems are set to enhance speed and efficiency. New materials, including biocompatible and high – performance resins, will expand its application scope. Integration with other technologies and a focus on sustainability will also shape the future of SLA.
To make the most of SLA technology, it’s essential to choose the right printer, follow best practices for model preparation and printing, and perform regular maintenance. Experimentation and iteration are key to improving skills and achieving optimal results. Whether you’re a professional in a specific industry or a hobbyist exploring the world of 3D printing, SLA offers a wealth of opportunities for creativity and innovation.