Think of living in a world where production is much quicker, more effective, and cheaper. In such a world, complicated designs would no longer be an obstacle to manufacturing, and the meaning of waste would be a thing of the past. Well, that would sound like a utopian dream, wouldn’t it? What if I told you such a world exists now due to the game-changing technology of SLS 3D printing?
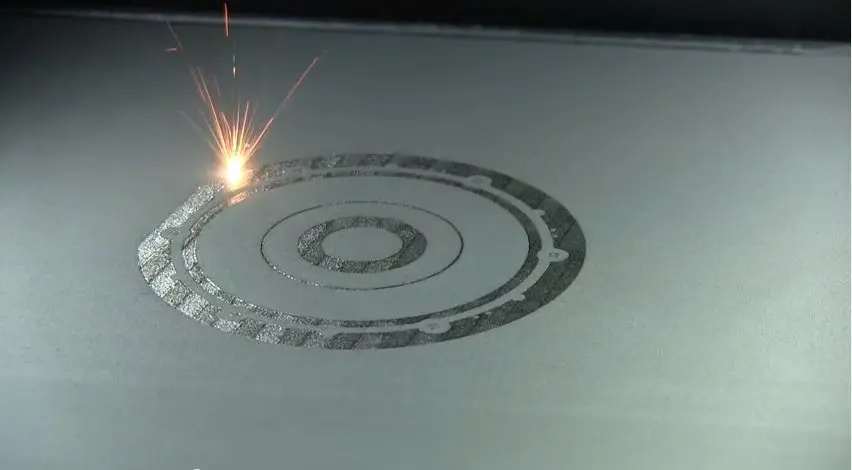
Traditional manufacturing methods have been the mainstay of industries, ranging from aerospace to automotive and medical, for decades. Yet they have their own critical limitations, including everything from requiring very expensive tooling, or even painfully slow and labor-intensive, sometimes with significant amounts of material waste. But what if there was some way to overcome these limitations and revolutionize the way we produce goods?
SLS 3D printing has been on the rise over the last decade, and this is for very good reason. It provides an easier way to turn complex parts and products in a faster, more efficient, and cost-effective way. Using a laser to sinter together particles of a powdered material, SLS 3D printing builds robust, durable, and highly detailed parts that have been unreachable this fast and this accurate.
In the following paper, we review what a vast world SLS 3D printing is, which very soon may well supplant conventional ways of producing items. We understand further ahead in what ways SLS 3D printing is beneficial and its relative advantages, its application areas, and challenges/limitations accompanying the technology. We will have a glance at some real-life case studies where SLS 3D printing has been implemented and will review the future of this technology. Be it a manufacturer, a product designer, or an enthusiast interested in state-of-the-art developments within the context of technological advancement, this article will broadly explain how SLS 3D printing impressively revolutionizes aspects of production.
What is SLS 3D Printing?
SLS is a powerful 3D printing technology going to revolutionize the way we manufacture goods. But what is SLS 3D printing, and how does it work?
The Basics of SLS 3D Printing
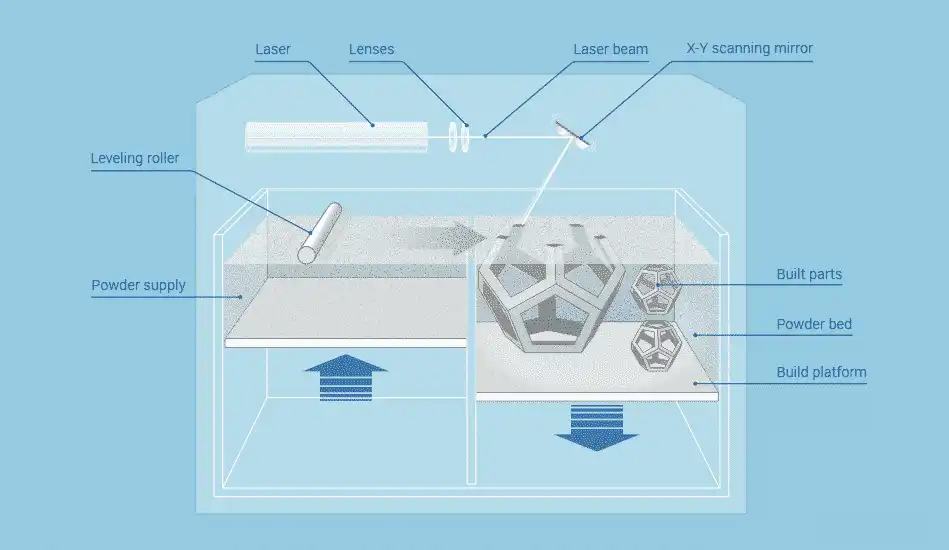
SLS stands for the selective laser sintering process in which particles of powdered material are sintered by a laser and then combined. This is a process of building up in layers a solid part or product without the use of molds or tooling.
Following is a step-by-step explanation of how the SLS 3D printing process works:
- Design: A digital model of the part or product under design is created with the use of computer-aided design software.
- Slicing: The model is digitally sliced into very thin layers, which act as guidelines for making the physical part.
- Powder Deposition: A thin layer of powdered material is disposed onto a build platform.
- Laser Sintering: Energy from a laser is applied to the particles in the powdered material to fuse them together in a solid bond.
- Layered Formation: Steps 3-4 are repeated; each layer is bonded to the previous one, forming a solid part.
SLS 3D Printing Materials
SLS 3D printing can use a wide range of materials, including:
Material | Description |
Nylon | A strong, flexible, and impact-resistant material. |
Alumide | A strong, lightweight material with a metallic appearance. |
Glass-filled Nylon | A strong, stiff, and impact-resistant material. |
Carbon-filled Nylon | A strong, lightweight material with a high stiffness-to-weight ratio. |
Benefits of SLS 3D Printing Materials
- High accuracy: SLS 3D printing materials can be printed with high accuracy and detail.
- Good mechanical properties: SLS 3D printing materials have good mechanical properties, such as strength and stiffness.
- Chemical resistance: SLS 3D printing materials have good chemical resistance and can be used in a wide range of applications.
SLS 3D printing is a powerful technology that is literally going to change the very process of goods manufacture. Giving complex parts and products high accuracy and detailed resolution, SLS 3D printing opens attractive opportunities in wide industries. Further, the review will present the benefits of SLS 3D printing in comparison with traditional methods of manufacture.
SLS 3D Printing Parameters
The following parameters can be adjusted to control the SLS 3D printing process:
Parameter | Description |
Layer Thickness | The thickness of each layer, which can range from 0.1-0.3mm. |
Laser Power | The power of the laser, which can range from 10-100W. |
Scan Speed | The speed at which the laser scans the powder bed, which can range from 1-10m/s. |
Hatch Distance | The distance between each scan line, which can range from 0.1-1mm. |
SLS 3D Printing Machines
There are several types of SLS 3D printing machines available, including:
- Open-Source Machines: These machines are open-source, meaning that the design and software are freely available.
- Commercial Machines: These machines are designed for industrial use and offer high levels of precision and accuracy.
- Hybrid Machines: These machines combine SLS 3D printing with other manufacturing technologies, such as CNC machining.
SLS 3D Printing Software
There are several software options available for SLS 3D printing, including:
- Slic3r: A popular open-source slicing software.
- Magics: A commercial slicing software designed for industrial use.
- Materialise: A software suite that includes slicing, build preparation, and post-processing tools.
We explained in detail the SLS 3D printing process: the steps involved, the parameters that can be changed, and the machines and software currently available. In the following paragraphs, we will be emphasizing the strengths of SLS 3D printing and how it can be used to a competitive advantage for manufacturing.
Benefits of SLS 3D Printing
SLS 3D printing offers quite a numerous number of added advantages and hence is one of the options that are in demand by the manufacturers. This section shall take a look at the advantages associated with SLS 3D printing and how this can actually enhance the manufacturing process
Advantages of SLS 3D Printing
Certain specific advantages of SLS 3D printing include the following:
- Fast Production: SLS 3D printing saves more time in production as compared to the conventional technique.
- More Complexity: SLS 3D printing allows one to make geometries and structures that cannot be made through any conventional technique.
- Material Waste Reduction: SLS 3D printing is an additive technique. In simple words, material is added only when needed, hence reducing the amount of material getting wasted and saving money.
- High Accuracy: The SLS 3D printing process provides very high accuracy and detail, making it perfect for applications that have to be highly accurate.
- Cost-Effective Solution: The SLS 3D printing process will cut costs because it reduces waste of materials, reduces labor, and allows the creation of geometries that are complicated.
Advantages of SLS 3D Printing in Various Industries
Among many others, some major benefits of SLS 3D printing for several industries are listed below:
Aerospace: The complicated aircraft parts, including engine components and satellite parts, are 3D printed with the SLS.
Automotive: They include car parts made by the SLS 3D printing, such as dashboard components and parts used in the engine.
Medical: The SLS 3D printing process is being applied to the fabrication of individually designed implants, prosthetics, and even surgical guides.
Consumer Products: SLS 3D printing of customized phone casings, jewelry, and various other consumer products.
Practical Applications and Benefits of SLS 3D Printing
The following are some practical examples of the benefits of SLS 3D printing:
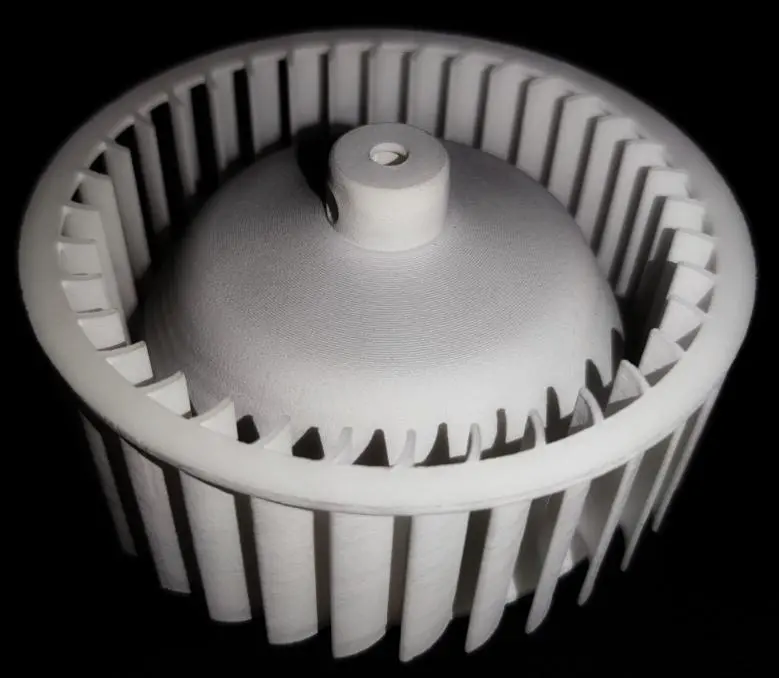
Airbus
Realized a 3D printed aircraft component with SLS 3D printing, which reduced the weight by 30%.
BMW
It used SLS 3D printing for producing a 3D printed car part and achieved a reduction of production time by 50%.
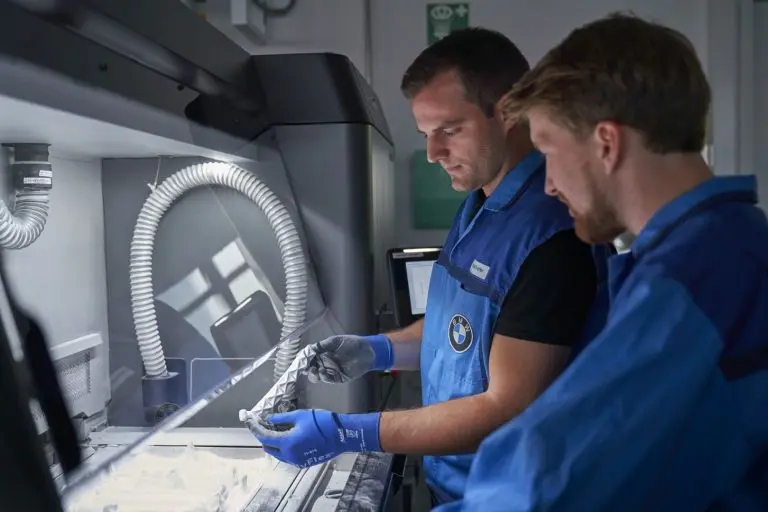
We’ve talked about the benefits of SLS 3D printing and how such technology can help further manufacturing processes. From speed-that is, faster production times-to higher levels of intricacy and complexity, SLS 3D printing offers quite a few advantages over traditional methods of manufacturing. Now let’s examine the applications in greater detail.
Comparison with Traditional Methods
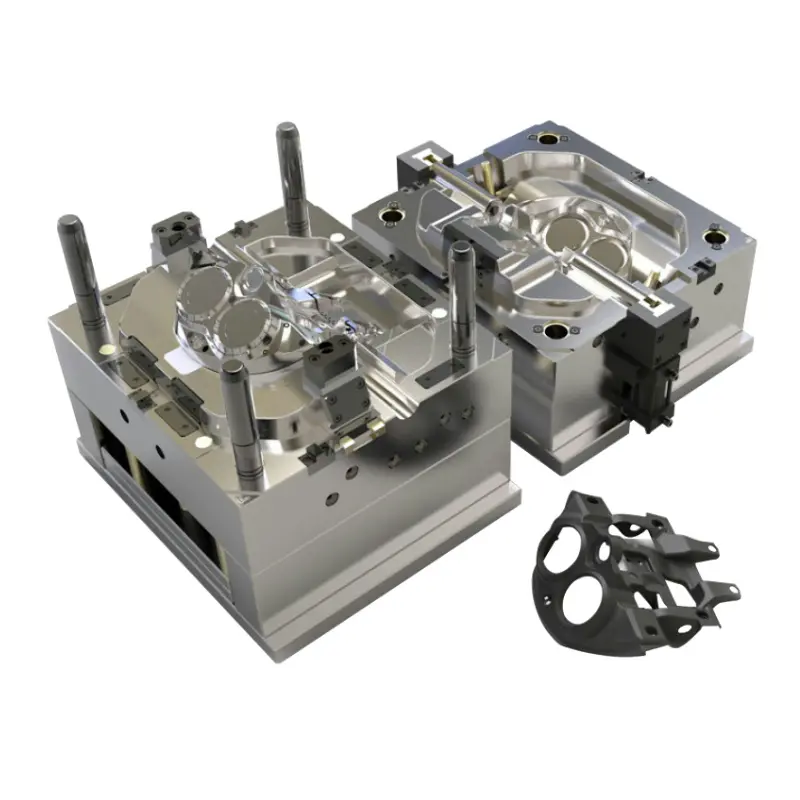
SLS 3D printing is usually compared to traditional manufacturing methods like injection molding and CNC machining. As such, in this section, we are going to take a closer look at the differences between SLS 3D printing and traditional techniques and also the uses of SLS 3D printing towards improving manufacturing processes.
Traditional Manufacturing Methods
SLS 3D printing is often compared to the following conventional methods of manufacturing:
• Injection Molding: This is a process where molten plastic is filled into a mold with the aim of attaining a part.
• CNC Machining: Actually, this is a process where the base material is cut out and shaped into parts with the use of a computer-controlled machine.
• Casting: This is a process wherein liquid metal is poured into a mold to form a part.
Comparison of SLS 3D Printing and Traditional Methods
The following is a comparison of SLS 3D printing and traditional manufacturing methods:
Manufacturing Method | SLS 3D Printing | Injection Molding | CNC Machining | Casting |
Production Time | Fast | Medium | Slow | Slow |
Complexity | High | Medium | Low | Low |
Material Waste | Low | High | Medium | High |
Accuracy | High | Medium | High | Medium |
Cost | Low | High | Medium | High |
When to Use SLS 3D Printing vs. Traditional Methods
Following are some guidelines about when to use SLS 3D printing and when to use traditional methods:
Use SLS 3D printing for:
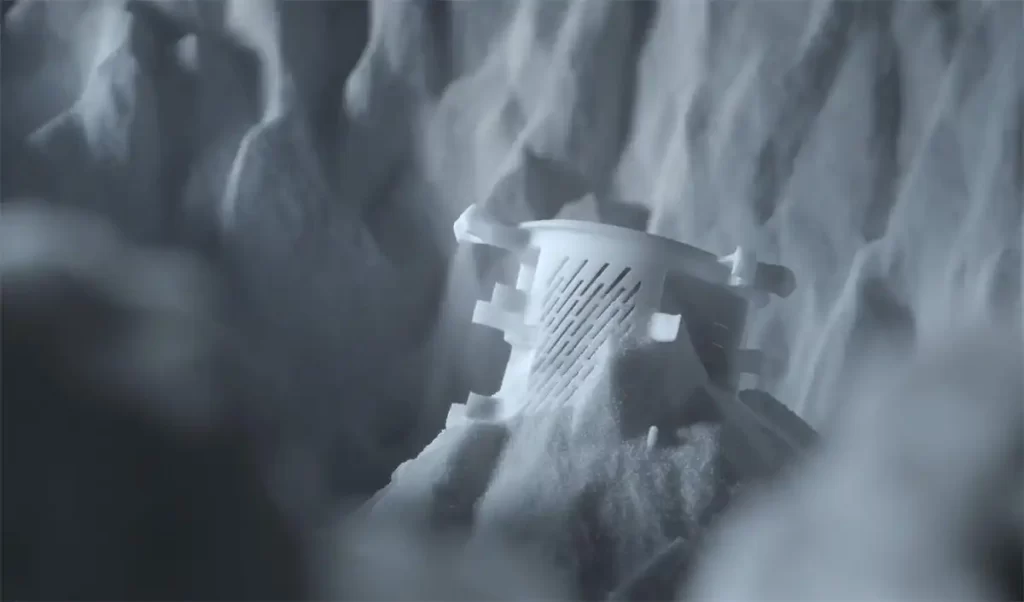
- Geometries and complex structures
- Small to medium-sized production runs
- Parts needing high accuracy and precision
Use traditional methods for:
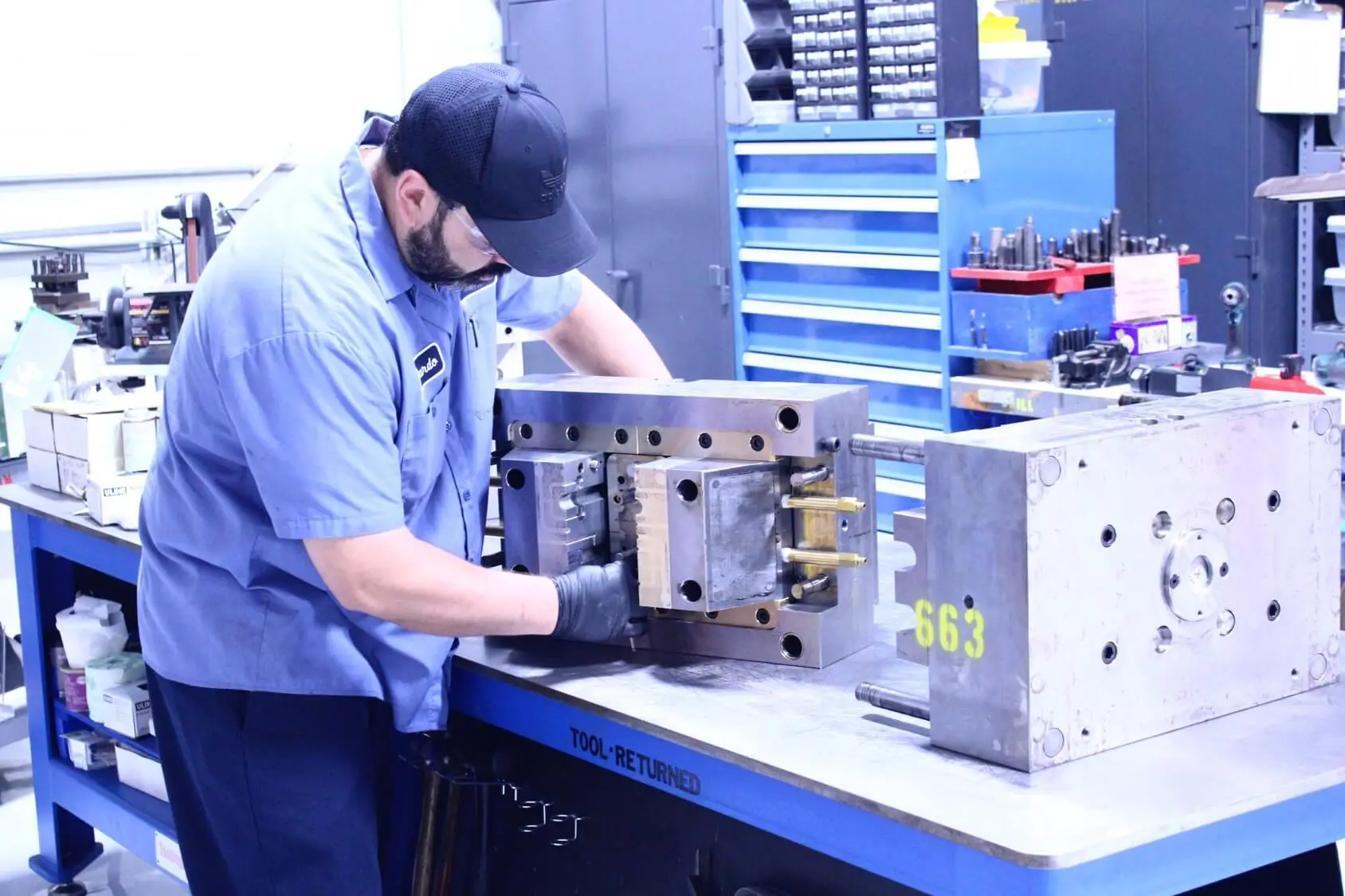
- Large production runs
- Geometries and simple structures
- The parts which do not need high accuracy and precision
We have discussed how SLS 3D printing compares with traditional methods of manufacturing. While it does have points where traditional methods are superior, there is a much greater good to be had with SLS 3D printing, where most of the aforementioned benefits are increased: higher production speeds, complexity, and less material waste. The following section will look in greater detail at the applications for SLS 3D printing.
Advantages of SLS 3D Printing over Traditional Methods
SLS 3D printing offers a number of advantages over traditional manufacturing methods, including:
Reduced Tooling Costs
SLS 3D printing eliminates the need for expensive tooling, which can be a significant cost savings for manufacturers. Traditional methods, such as injection molding, require the creation of molds, which can be costly and time-consuming to produce.
Increased Design Flexibility
SLS 3D printing allows for the creation of complex geometries and structures that cannot be produced using traditional methods. This means that designers and engineers have more freedom to create innovative and complex designs.
Improved Accuracy
SLS 3D printing offers high levels of accuracy and precision, making it ideal for applications where precision is critical.
Reduced Material Waste
SLS 3D printing is an additive process, which means that material is only added as needed, reducing waste and saving costs.
Faster Production Times
SLS 3D printing can produce parts much faster than traditional methods, which can be a significant advantage for manufacturers who need to produce parts quickly.
Increased Customization
SLS 3D printing allows for the creation of custom parts with complex geometries and structures, which can be a significant advantage for manufacturers who need to produce custom parts.
Comparison of SLS 3D Printing and Traditional Methods
The following is a comparison of SLS 3D printing and traditional manufacturing methods:
Manufacturing Method | Tooling Costs | Design Flexibility | Accuracy | Material Waste | Production Time | Customization |
SLS 3D Printing | Low | High | High | Low | Fast | High |
Injection Molding | High | Medium | Medium | High | Medium | Low |
CNC Machining | Medium | Low | High | Medium | Slow | Medium |
Casting | High | Low | Medium | High | Slow | Low |
Challenges and Limitations of SLS 3D Printing
While SLS 3D printing offers many benefits, it also has some challenges and limitations that need to be considered.
Challenges of SLS 3D Printing
The following are some of the challenges of SLS 3D printing:
- High Cost: SLS 3D printing machines and materials can be expensive, making it a significant investment for businesses and individuals.
- Limited Build Size: SLS 3D printing machines have limited build sizes, which can make it difficult to print large objects.
- Material Limitations: SLS 3D printing is limited to printing with specific materials, such as nylon and alumide, which can limit its applications.
- Post-Processing: SLS 3D printing requires post-processing, such as sanding and painting, to achieve the desired finish.
Limitations of SLS 3D Printing
The following are some of the limitations of SLS 3D printing:
- Resolution: SLS 3D printing has a limited resolution, which can affect the accuracy and detail of the printed object.
- Surface Finish: SLS 3D printing can produce a rough surface finish, which may require additional post-processing.
- Material Properties: SLS 3D printing materials may not have the same properties as traditionally manufactured materials, such as strength and durability.
- Scalability: SLS 3D printing can be difficult to scale up for large production runs.
Overcoming the Challenges and Limitations of SLS 3D Printing
The following are some ways to overcome the challenges and limitations of SLS 3D printing:
- Investing in High-Quality Machines: Investing in high-quality SLS 3D printing machines can help to improve the accuracy and resolution of the printed object.
- Using Advanced Materials: Using advanced materials, such as carbon fiber and metal, can help to improve the strength and durability of the printed object.
- Optimizing Print Settings: Optimizing print settings, such as layer thickness and infill density, can help to improve the surface finish and material properties of the printed object.
- Post-Processing Techniques: Using advanced post-processing techniques, such as sanding and painting, can help to improve the surface finish and appearance of the printed object.
Future of SLS 3D Printing
The future of SLS 3D printing looks promising since the technology keeps on advancing. This comprises several potential improvements and trends that may have an effect on the future of the industry.
Improvements to SLS 3D Printing Technology
- Resolution Higher: A number of future SLS 3D printing machines will reach higher resolutions and provide prints which are far more detailed and accurate.
- Speed: New 3D printing machines using SLS will be able to print faster, whereby production times are reduced.
- Material Options: New materials for SLS 3D printing are under development, such as metals, ceramics, and even glass.
- Multi-material Printing: Future SLS 3D printing machines may enable printing with multiple materials simultaneously and hence enhance the creation of complex and functional prints.
Trends in SLS 3D Printing
- Increased Adoption: SLS 3D printing is becoming more widely adopted in various industries, including aerospace, automotive, and healthcare.
- Growing Demand for Customization: Consumers are increasingly demanding customized products, which SLS 3D printing can provide.
- Rise of Service Bureaus: Service bureaus that offer SLS 3D printing services are becoming more popular, making it easier for companies to access the technology.
- Integration with Other Technologies: SLS 3D printing is being integrated with other technologies, such as computer-aided design (CAD) and computer-aided manufacturing (CAM), to create more efficient and streamlined workflows.
Potential Applications of SLS 3D Printing
- Space Exploration: SLS 3D printing could be used to create parts and tools for space exploration, such as satellite components and spacecraft parts.
- Bioprinting: SLS 3D printing could be used to create living tissues and organs for transplantation.
- Custom Prosthetics: SLS 3D printing could be used to create custom prosthetics that are tailored to individual patients’ needs.
- Sustainable Manufacturing: SLS 3D printing could be used to create sustainable and environmentally friendly products, such as biodegradable plastics and recycled materials.
Challenges and Limitations of SLS 3D Printing
- High Cost: SLS 3D printing machines and materials can be expensive, making it difficult for some companies to adopt the technology.
- Limited Build Size: SLS 3D printing machines have limited build sizes, which can make it difficult to print large objects.
- Material Limitations: SLS 3D printing is limited to printing with specific materials, which can limit its applications.
- Post-Processing: SLS 3D printing requires post-processing, such as sanding and painting, to achieve the desired finish.
While there are challenges and limitations to overcome, the future of SLS 3D printing looks promising, with potential applications in space exploration, bioprinting, custom prosthetics, and sustainable manufacturing.