In the realm of modern manufacturing, 3D printing has emerged as a game-changer, pushing the boundaries of what’s possible. Among the various 3D printing technologies available, Selective Laser Sintering (SLS) stands out for its unparalleled ability to handle complex geometries with ease. This article delves deep into the world of SLS 3D printing, exploring its unique advantages and how it has revolutionized the manufacturing of intricate parts.
From the aerospace industry to medical devices, the demand for complex geometries has never been greater. Traditional manufacturing methods often fall short when it comes to producing such intricate designs, leading to compromised functionality and increased costs. Enter SLS 3D printing, a technology that has redefined the rules of the game. With its design freedom, material versatility, and precision, SLS has become the go-to choice for engineers and designers seeking to master complex geometries.
What is Selective Laser Sintering (SLS)?
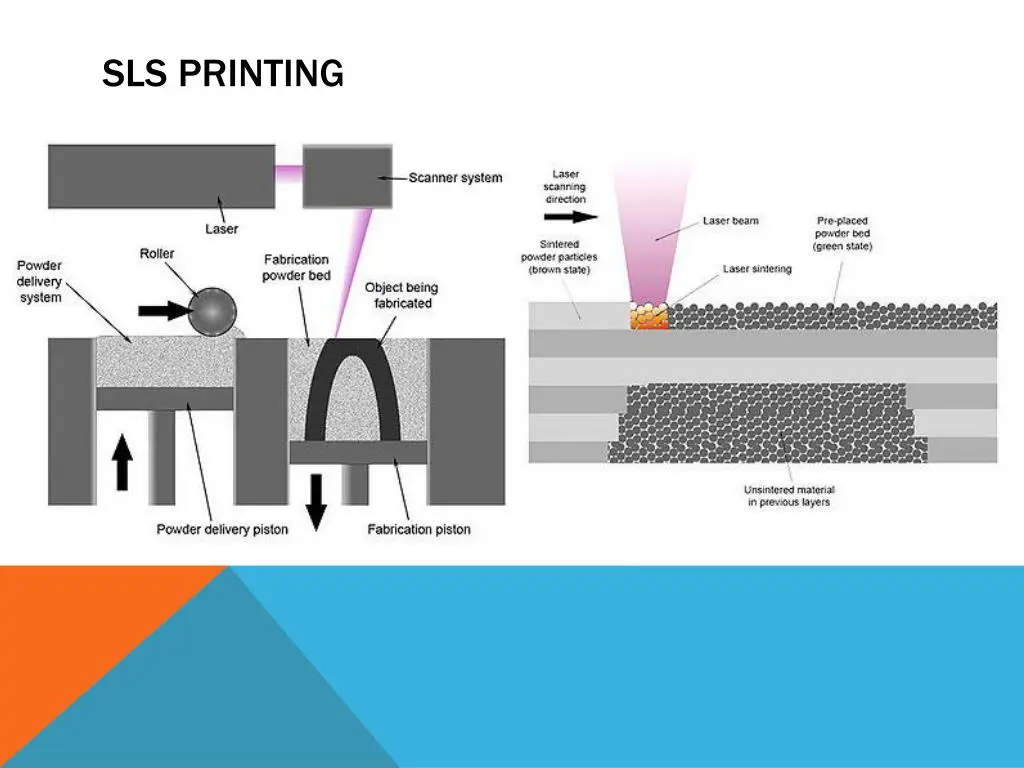
Selective Laser Sintering (SLS) is an additive manufacturing technique that uses a high-power laser to fuse small particles of plastic, metal, ceramic, or glass powders into a mass that has a desired three-dimensional shape. The process is akin to building an object layer by layer, with each layer being fused by the laser.
How SLS Differs from Other 3D Printing Technologies
SLS stands out from other 3D printing methods in several key ways:
- No Support Structures: Unlike FDM (Fused Deposition Modeling), SLS doesn’t require support structures. This is because the surrounding powder supports the object as it’s being printed, which is particularly beneficial for complex geometries.
- Material Versatility: SLS can work with a variety of materials, including nylon, glass-filled nylon, and even metal powders, offering a wide range of mechanical properties.
- Strength and Durability: Parts produced by SLS are known for their strength and durability, making them suitable for functional prototypes and end-use parts.
How Does SLS Work?
- Powder Preparation: A fine powder, typically made of thermoplastics or metals, is spread across the build platform.
- Laser Sintering: A laser is used to selectively heat and fuse the powder in the areas defined by the digital model, binding it together to form a solid structure.
- Layer-by-Layer Build-Up: After each layer is sintered, a new layer of powder is applied, and the process is repeated until the part is complete.
- Post-Processing: Once the part is printed, it undergoes post-processing, which includes cooling, powder removal, and any necessary finishing steps.
How Does SLS Differ from Other 3D Printing Technologies?
Comparison with Other 3D Printing Technologies
Technology | Process | Material Properties | Build Volume Limitations |
SLS | Laser sintering of powdered materials | Good mechanical properties | Larger build volumes |
FDM | Melting and extruding of filament | Lower mechanical properties | Smaller build volumes |
SLA | Laser curing of liquid resin | Good surface finish | Smaller build volumes |
PolyJet | Jetting of photopolymer ink | Good for multicolor prints | Smaller build volumes |
Advantages of SLS 3D Printing for Complex Geometries
In the realm of additive manufacturing, Selective Laser Sintering (SLS) stands out as a beacon of innovation, particularly when it comes to creating complex geometries. This section will explore the unique capabilities of SLS that make it a preferred choice for designers and engineers pushing the boundaries of what’s possible in manufacturing.
Design Freedom and Complexity Achievable with SLS
SLS 3D printing opens up a world of possibilities for designers and engineers, allowing them to push the boundaries of what’s deemed possible in manufacturing. Here’s why SLS is the go-to choice for complex geometries:
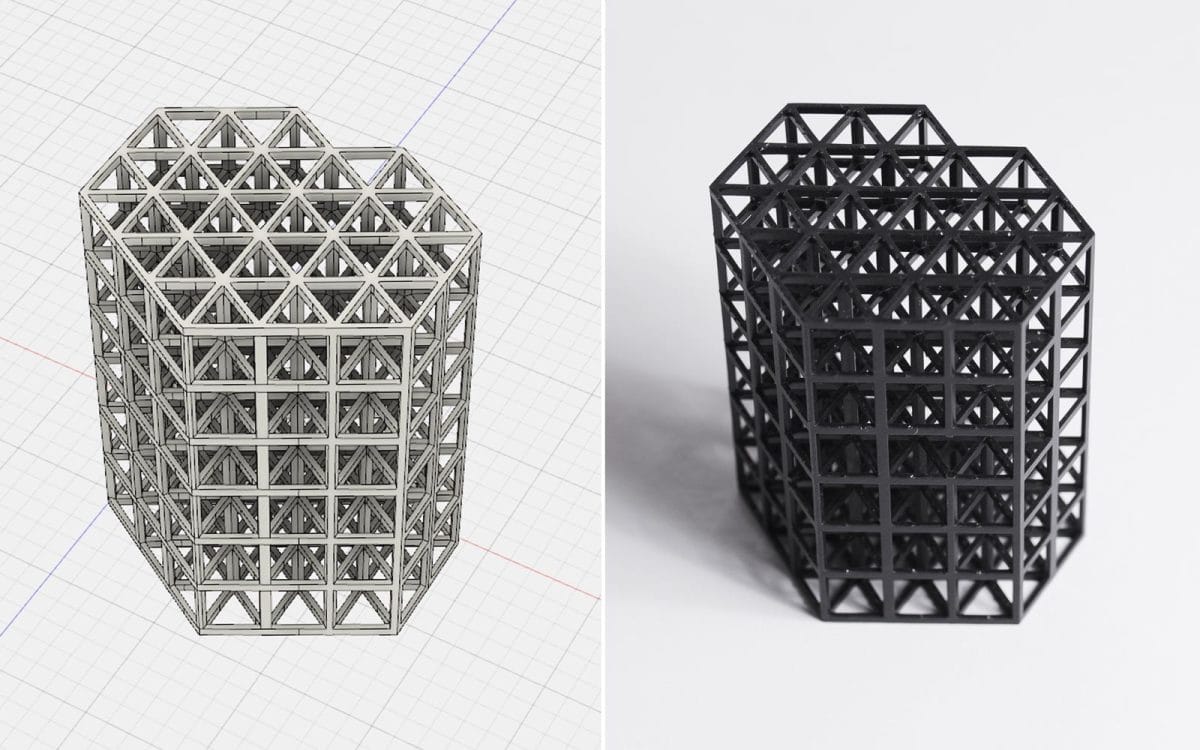
Key Advantages of SLS for Complex Geometries
- No Need for Supports: Unlike other 3D printing technologies, SLS prints parts in a powder bed, eliminating the need for supports. This means you can create complex, interlocking parts without worrying about post-printing removal or structural integrity.
- Intricate Geometric Patterns: SLS allows for the creation of intricate honeycombs, lattices, and nested structures, which are difficult to achieve with traditional manufacturing. These patterns can enhance product performance by reducing weight while maintaining strength.
- Enhanced Product Customization: SLS printing enables mass customization, allowing designers to tailor products to individual needs without incurring high production costs.
Examples of Complex Geometries
- Honeycombs: Used in lightweight structures, honeycombs can provide excellent strength-to-weight ratios.
- Lattices: These structures mimic nature’s efficient designs, offering high strength with minimal material usage.
- Nested Assemblies: Design intricate assemblies that fit together like puzzle pieces, reducing the need for multiple components and assembly steps.
Enhanced Material Properties
The layer-by-layer sintering process in SLS not only allows for complex geometries but also contributes to improved material properties:
- Isotropic Strength: SLS parts exhibit similar mechanical properties in all directions, ensuring consistent strength and durability.
- High Temperature Resistance: Some SLS materials can withstand high temperatures, making them suitable for applications in engines or underhood components.
- Biocompatibility: SLS can use materials that are safe for medical and dental applications, such as biocompatible nylon powders.
Material Properties at a Glance
Material Property | Description |
Strength | SLS parts can achieve high mechanical strength, comparable to traditionally manufactured parts. |
Flexibility | Certain SLS materials offer flexibility, making them suitable for soft robotics or gaskets. |
Tolerance | SLS printing can achieve tight tolerances, ensuring precise fits for complex assemblies. |
Material Options in SLS 3D Printing
From thermoplastics to metals, the versatility of materials in SLS opens up a wide range of applications and possibilities. Let’s dive into the material options and their impact on part quality and mechanical properties.
Overview of Materials Used in SLS Printing
SLS 3D printing has a diverse range of material options, each with its unique properties and applications. Here’s a quick overview:
Thermoplastics: The most commonly used materials in SLS printing, thermoplastics offer a good balance of strength, flexibility, and durability. Examples include Nylon 12 (PA12), Nylon 11, and TPU.
Elastomers: These materials provide flexibility and elasticity, making them ideal for applications such as gaskets, seals, and soft robotics.
Metal Powders: While less common, some SLS printers can process metal powders, allowing for the production of metal parts with complex geometries.
Material Properties and Their Impact
Tensile Strength: The material’s ability to withstand pulling forces without breaking.
Flexibility: The material’s ability to bend without fracturing.
Heat Resistance: The temperature at which the material softens or deforms.
Biocompatibility: The material’s suitability for use in medical and dental applications.
The Impact of Material Choice on Part Quality and Mechanical Properties
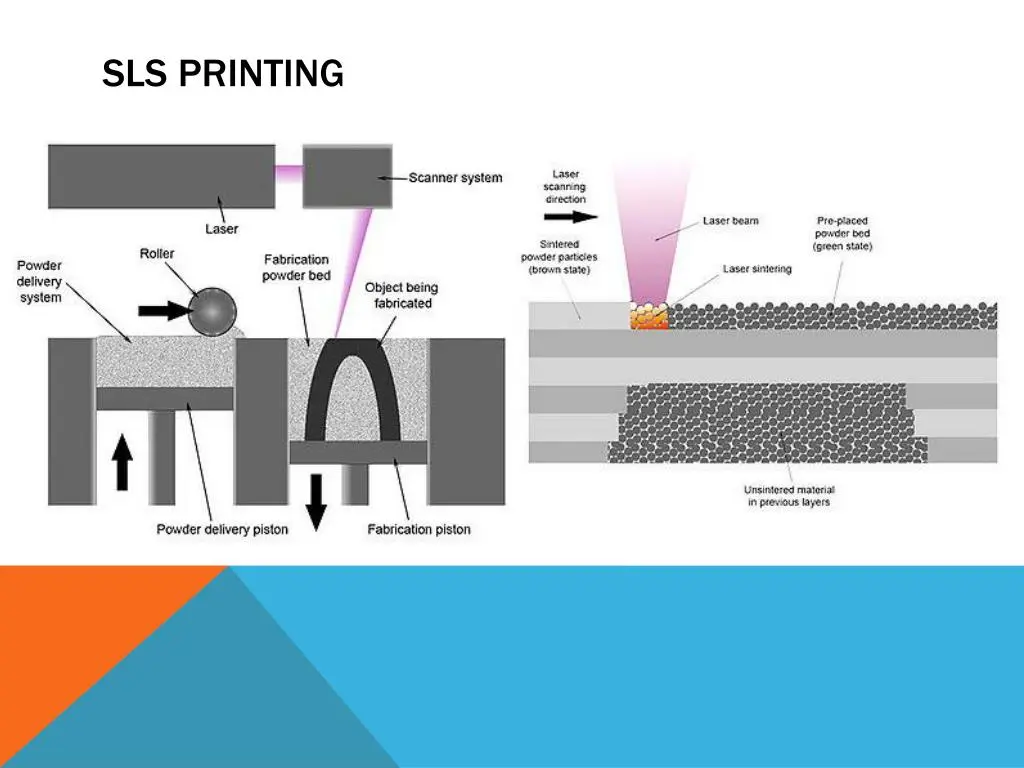
Strength and Stiffness: Materials with higher tensile strength and modulus of elasticity will result in stiffer and stronger parts, suitable for load-bearing applications.
Durability: Materials with good heat resistance and fatigue resistance will withstand harsh environments and repeated use.
Functionality: The choice of material can enable specific functionalities, such as flexibility for soft robotics or biocompatibility for medical implants.
Material Properties Table
Material | Tensile Strength (MPa) | Flexibility | Heat Resistance (°C) | Biocompatibility |
Nylon 12 (PA12) | 48-55 | Low | 80-120 | Good |
TPU | 35-55 | High | 80-120 | Good |
Elastomer | 15-25 | High | 60-80 | Good |
Metal Powder | Varies by alloy | Low | Varies by alloy | Not applicable |
Design Considerations for SLS 3D Printing
In our quest to master complex geometries with SLS 3D printing, the design of your part is crucial. From wall thickness to overhangs, every aspect of your design can impact the printability and functionality of your final product. In this section, we’ll delve into the design considerations that will help you create the perfect part for SLS printing.
Minimum Feature Size
Resolution Limitations: SLS printers have a minimum feature size, typically around 0.5 mm. Avoid designing features smaller than this to ensure they are accurately printed.
Consideration for Overhangs: Design overhangs with a minimum thickness of 1 mm to prevent warping and ensure structural stability.
Design Optimization
Weight Reduction: Utilize honeycombs, lattices, and other lightweight structures to reduce weight while maintaining strength.
Improved Functionality: Design for functionality by incorporating integrated assemblies, moving parts, and complex geometries that would be challenging or impossible with traditional manufacturing.
Applications of SLS 3D Printing in Complex Geometries
We’ll explore the diverse applications of SLS across various industries. From aerospace to medical, SLS 3D printing is revolutionizing the way complex geometries are designed and manufactured. Let’s take a look at the industries reaping the benefits of SLS 3D printing.
Aerospace and Automotive
SLS 3D printing has found a natural home in the aerospace and automotive industries, where lightweight structures and complex geometries are paramount.
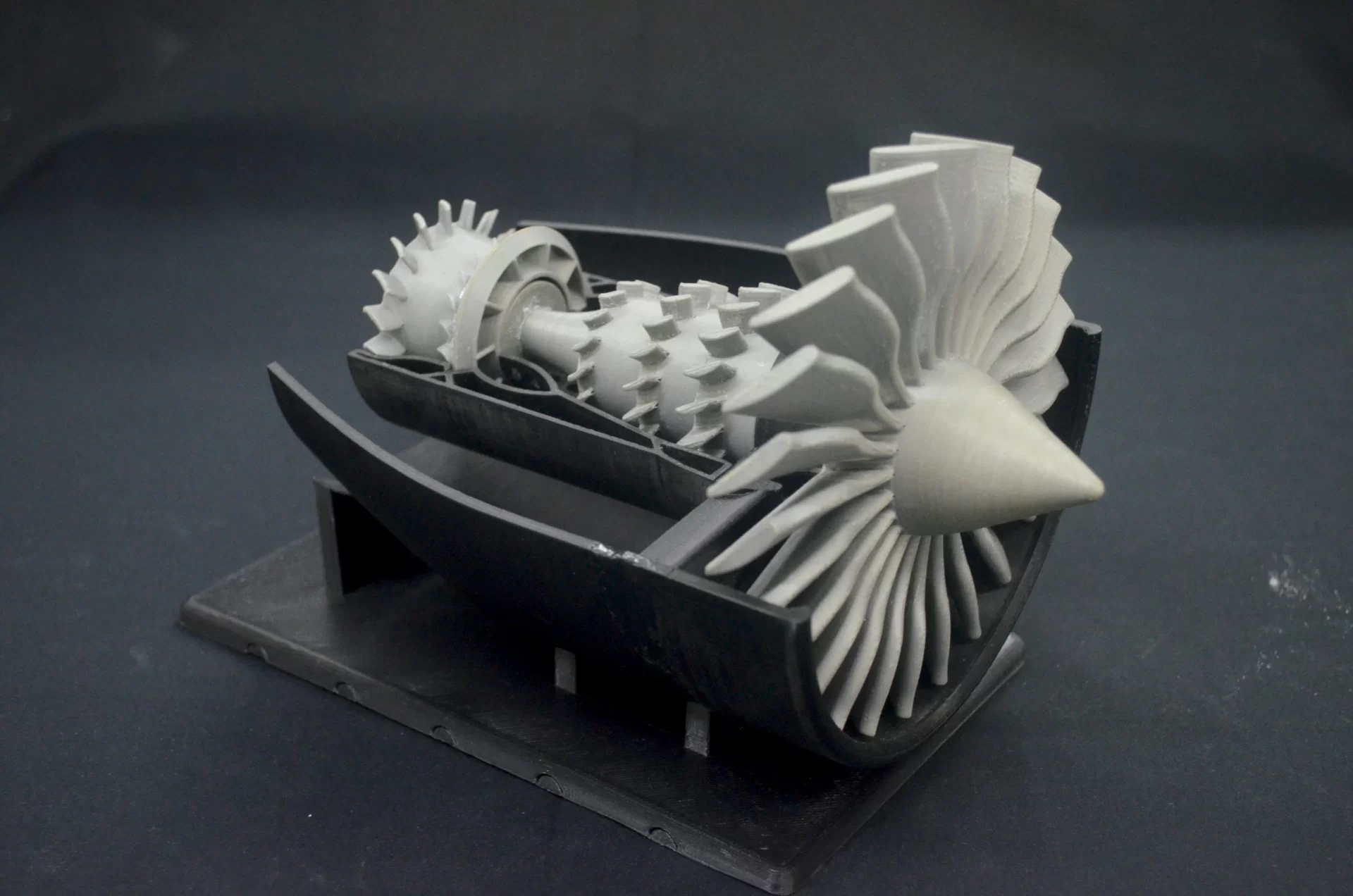
Examples of Applications
Lightweight Structures: SLS allows for the creation of lightweight structures with optimized strength, reducing weight and improving fuel efficiency.
Complex Brackets and Connectors: SLS printing enables the production of intricate brackets and connectors that are difficult or impossible to manufacture traditionally.
Medical and Dental
The medical and dental industries have embraced SLS 3D printing for its ability to create custom implants, prosthetics, and surgical instruments.
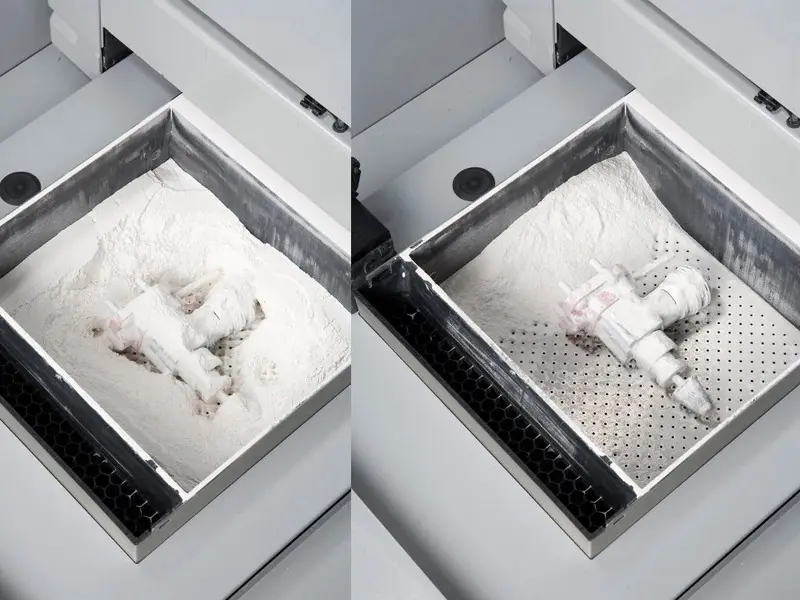
Examples of Applications
Custom Implants: SLS printing allows for the production of custom implants that are tailored to the patient’s anatomy, improving outcomes and patient comfort.
Prosthetics: SLS enables the creation of lightweight and comfortable prosthetics, providing enhanced mobility and quality of life for patients.
Fashion and Footwear
SLS 3D printing has also made its mark in the fashion and footwear industries, offering customization and innovative designs.
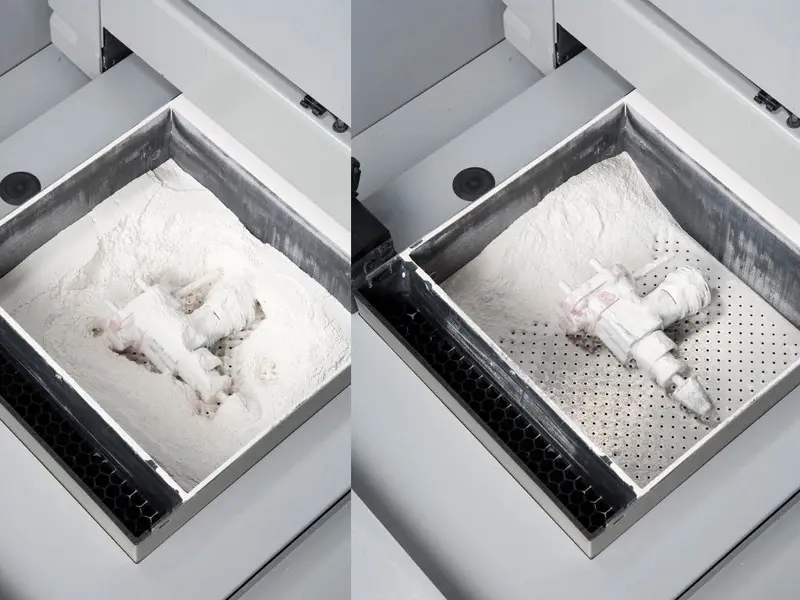
Complex Patterns: SLS allows for the creation of intricate patterns and designs that would be challenging or impossible to achieve with traditional manufacturing methods.
Customized Fit: SLS printing enables the production of custom footwear that is tailored to the individual’s foot shape, providing enhanced comfort and support.
Future Developments and Trends in SLS 3D Printing
Emerging Trends in SLS Technology and Materials
New Materials: Researchers are continuously developing new materials with improved properties, such as higher strength, better heat resistance, and increased flexibility.
Multi-Material and Full-Color Printing: Advances in SLS technology are enabling the printing of multi-material and full-color parts, expanding the design possibilities even further.
Integration with Other Manufacturing Processes: SLS is increasingly being integrated with other manufacturing processes, such as CNC machining and injection molding, to create hybrid manufacturing solutions.
More Exciting Developments
- Improved Build Speeds: Innovations in SLS technology are focusing on increasing build speeds, reducing print times, and improving overall efficiency.
- Enhanced Precision and Accuracy: Advances in laser technology and motion control systems are leading to higher precision and accuracy in SLS printing.
- Sustainability: Efforts are being made to make SLS printing more sustainable, including the development of biodegradable materials and the optimization of powder recycling processes.
As the technology matures and becomes more accessible, we can expect to see SLS 3D printing being adopted in an even wider range of industries.
With ongoing research and development, we can anticipate new materials, technologies, and applications that will further push the boundaries of what’s possible with SLS 3D printing.