Ever wondered how those amazing 3D – printed parts that you see in movies or used in high – tech gadgets go from a raw, printed form to a smooth, polished, and fully functional product? Well, the secret often lies in the world of post – processing. Selective Laser Sintering (SLS) 3D printing is an incredible technology that can create complex shapes from various materials, but the real magic happens after the print job is done.
Picture this: You’ve just finished a long – awaited SLS 3D printing project. You eagerly pull out the part from the printer, and while it already looks pretty cool in its raw state, it has rough edges, powder clinging to its surface, and a somewhat dull appearance. It’s far from being ready to be used as a high – quality, professional – grade item. This is where post – processing steps in to transform your basic print into a masterpiece.
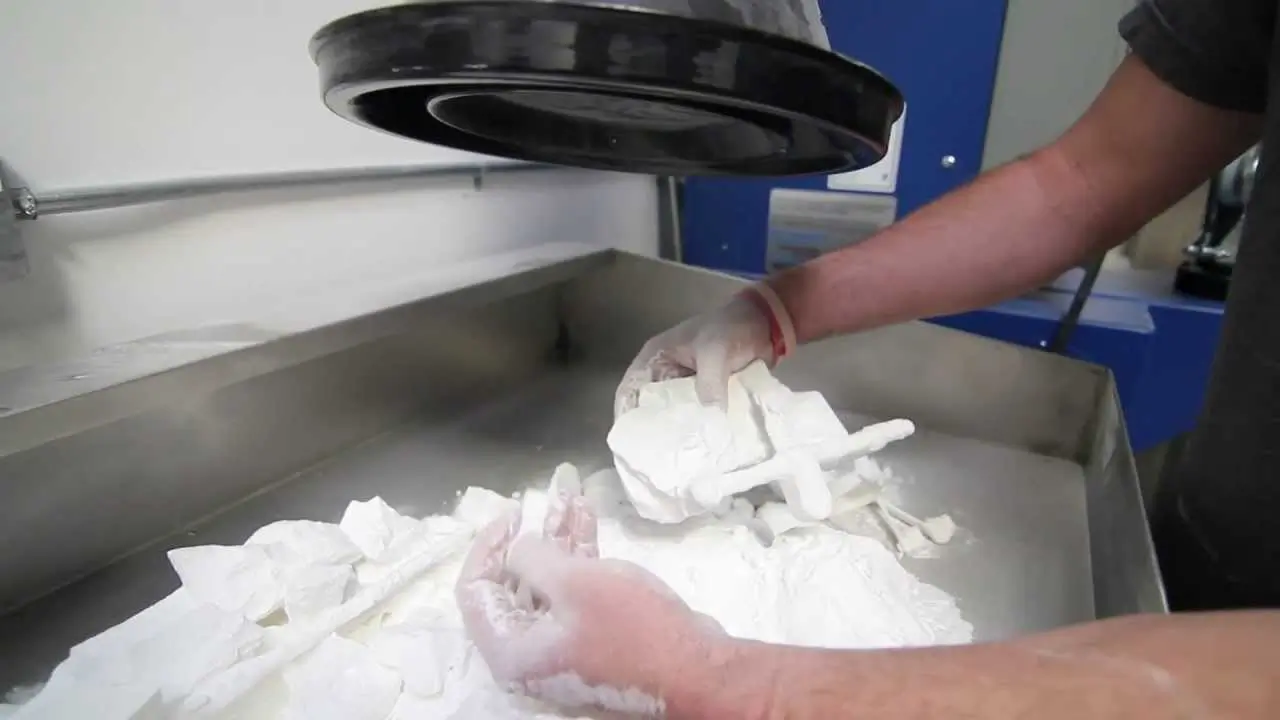
In this blog post, we’re going to take a deep dive into the art and science of mastering SLS 3D printing post – processing. We’ll cover everything from simple cleaning tricks to advanced finishing techniques. Whether you’re a hobbyist looking to take your 3D – printed creations to the next level or a professional in the manufacturing industry, these tips and techniques will come in super handy.
Understanding SLS 3D Printing Basics
How SLS 3D Printing Works
SLS 3D printing uses a high – powered laser to fuse small particles of powdered material together. These materials can range from plastics like nylon to metals in some industrial applications. The laser scans across a thin layer of powder, sintering (or fusing) the powder according to the digital model’s specifications. After one layer is completed, a new layer of powder is spread over it, and the process repeats until the entire object is formed.
Advantages and Limitations of SLS 3D Printing
- Advantages
- Complex geometries: SLS can create parts with incredibly intricate designs that would be impossible or very difficult to make with traditional manufacturing methods. For example, parts with internal channels or lattice structures can be easily printed.
- No support structures: Unlike some other 3D – printing methods, SLS doesn’t require support structures because the unsintered powder supports the printed part during the printing process.
- Material variety: A wide range of materials can be used in SLS 3D printing, each with its own unique properties.
- Limitations
- Surface finish: The raw printed surface of an SLS part is usually rough, with a grainy texture due to the powder particles.
- Part porosity: Some SLS – printed parts may have a certain degree of porosity, which can affect their strength and performance.
Importance of Post – Processing in SLS 3D Printing
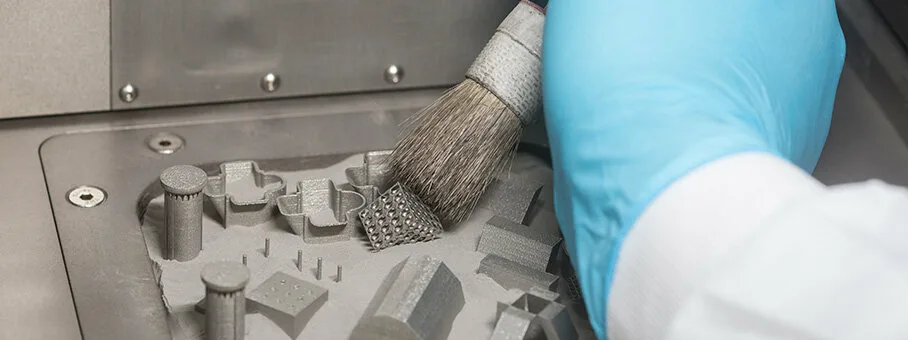
Improving Surface Finish
The rough surface of a freshly printed SLS part is often not suitable for many applications. Whether it’s for aesthetic reasons (like creating a smooth and shiny consumer product) or functional reasons (such as needing a low – friction surface for a mechanical part), post – processing can significantly improve the surface finish.
There are several ways to achieve a better surface finish:
- Sanding: This is one of the most basic and widely used post – processing techniques. By using sandpaper of different grits, you can start with a coarse grit to remove large bumps and then move to finer grits for a smoother finish.
- Vapor smoothing: For plastic SLS parts, vapor smoothing involves exposing the part to a solvent vapor. The vapor slightly melts the surface of the plastic, filling in small pores and creating a smooth, glossy finish.
Enhancing Mechanical Properties
Post – processing can also enhance the mechanical properties of SLS – printed parts. For example, heat treatment can relieve internal stresses that may have formed during the printing process. Annealing, a type of heat treatment, can increase the part’s strength and toughness by improving the material’s internal structure.
Ensuring Dimensional Accuracy
Sometimes, the printed part may not have the exact dimensions specified in the digital model due to factors like shrinkage during cooling. Post – processing techniques such as machining can be used to achieve the desired dimensional accuracy. For example, if a part needs to fit precisely into another component, machining can trim or shape the part to the required size.
Post – Processing Steps
Powder Removal
The first step in post – processing an SLS 3D – printed part is to remove the excess powder. This is important not only for the appearance of the part but also to ensure its proper function.
- Brushing and Blowing: A soft – bristled brush can be used to gently remove loose powder from the surface of the part. Compressed air can also be used to blow away powder from hard – to – reach areas.
- Ultrasonic Cleaning: For more thorough powder removal, ultrasonic cleaning can be employed. The part is placed in a bath of a cleaning solution and exposed to ultrasonic waves, which create tiny bubbles that collapse on the surface of the part, dislodging powder particles.
Surface Smoothing
As mentioned earlier, surface smoothing is crucial for many applications. Here are some techniques in more detail:
- Sanding:
- Grit selection: Start with a low – grit sandpaper (around 80 – 120 grit) to remove large bumps and unevenness. Then, gradually move to higher – grit sandpaper (up to 600 or even 1000 grit) for a finer finish.
- Technique: Sand the part in a consistent direction to avoid creating scratches. Apply even pressure to ensure an even surface.
- Vapor Smoothing:
- Solvent choice: Different plastics require different solvents. For example, acetone can be used for ABS – like plastics.
- Safety precautions: Vapor smoothing should be done in a well – ventilated area, and appropriate safety gear such as gloves and a respirator should be worn.
Dyeing and Coloring
If you want to give your SLS – printed part a more vibrant and attractive appearance, dyeing or coloring is a great option.
- Dyeing Process: For plastic parts, they can be immersed in a dye bath. The temperature and time of immersion will depend on the type of plastic and the desired color intensity.
- Spray Painting: Another option is to use spray paint. Make sure to clean and prime the part before painting for better adhesion.
Assembly and Joining
Sometimes, you may need to assemble multiple SLS – printed parts together to create a larger structure. There are several ways to join them:
- Adhesives: Choose an adhesive that is compatible with the material of the printed parts. For example, epoxy adhesives work well for many plastic and metal parts.
- Mechanical Fasteners: Screws, bolts, and nuts can also be used to join parts. However, you may need to drill holes in the printed parts accurately.
Tips and Tricks for Effective Post – Processing
Planning Ahead
Before you start post – processing, it’s important to have a clear plan. Consider the final application of the part and what post – processing steps are required to meet those requirements. For example, if the part needs to be watertight, you’ll need to focus on techniques that can seal any pores.
Testing on Small Samples
If you’re trying out a new post – processing technique or a new material, it’s a good idea to test it on a small sample first. This way, you can see the results and make any necessary adjustments without ruining your main print.
Maintaining a Clean Workspace
A clean workspace is essential for effective post – processing. Keep your tools organized and clean up any debris or powder regularly. This not only makes the post – processing process more efficient but also reduces the risk of contamination.
Monitoring and Documentation
Keep track of the post – processing techniques you use, the parameters (such as sanding grit, dyeing time, etc.), and the results. This documentation can be very useful for future projects and for troubleshooting if you encounter any issues.
Case Studies
Consumer Product Development
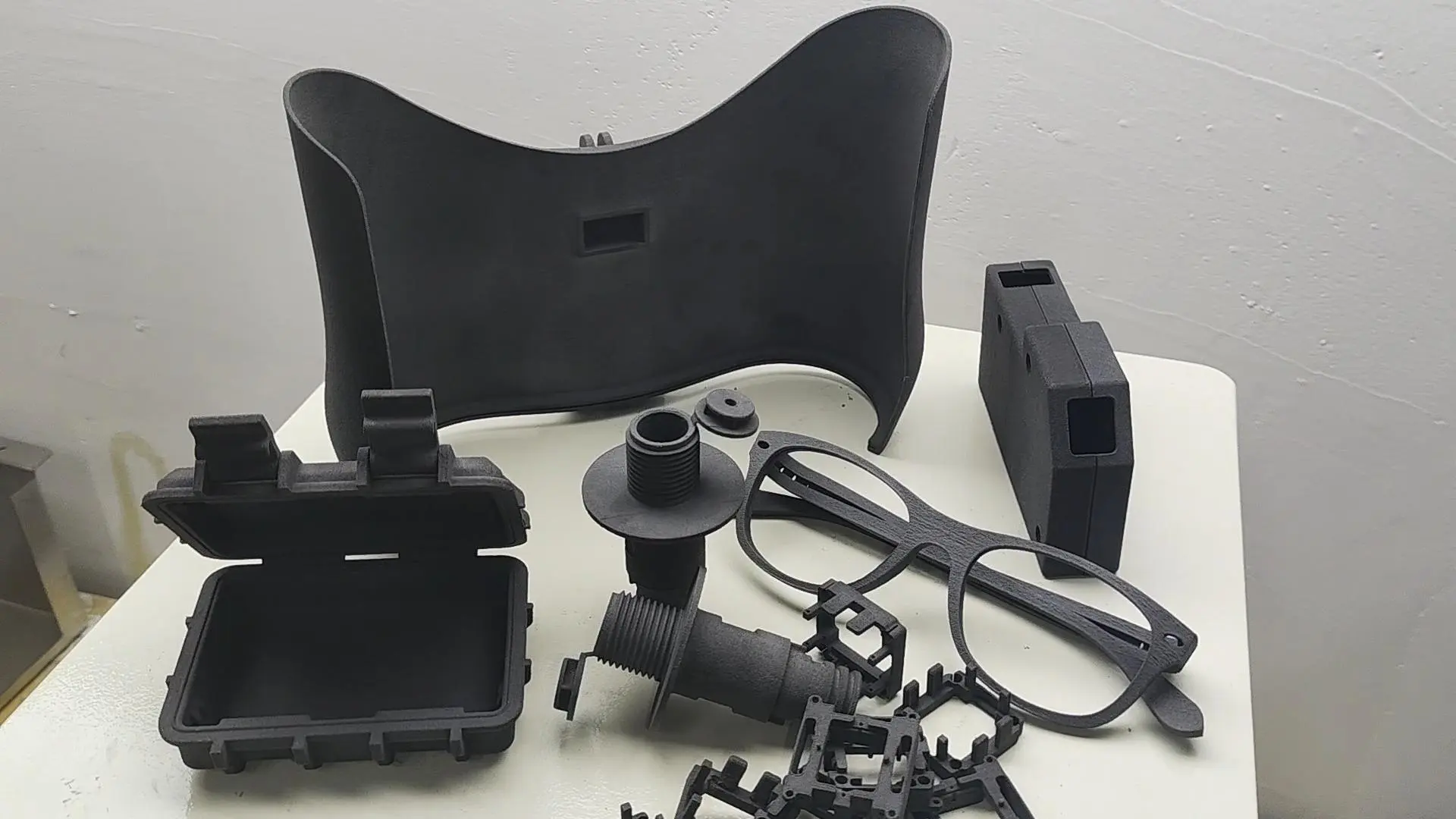
A company was developing a new line of smartphone cases using SLS 3D printing. The raw printed cases had a rough texture and a dull appearance. They used a combination of sanding and vapor smoothing to achieve a smooth, shiny finish. After dyeing the cases in various colors, they were able to create high – quality, attractive products that were well – received in the market.
Medical Device Manufacturing
In the medical field, a manufacturer was using SLS 3D printing to create custom – made surgical guides. The printed guides needed to have a high level of dimensional accuracy and a smooth surface to ensure proper functionality. By using post – processing techniques such as machining for dimensional adjustment and fine sanding for surface finishing, they were able to produce guides that met the strict medical standards.
Challenges in SLS 3D Printing Post – Processing
Material Compatibility
Not all post – processing techniques are suitable for all materials. For example, some solvents used in vapor smoothing may not work well with certain plastics or may even damage the part. It’s important to research and understand the material properties before applying any post – processing methods.
Environmental and Safety Concerns
Some post – processing steps, such as using solvents in vapor smoothing or certain dyes, can pose environmental and safety risks. It’s crucial to follow proper safety procedures, use appropriate protective equipment, and dispose of waste materials correctly.