Understanding SLS 3D Printing
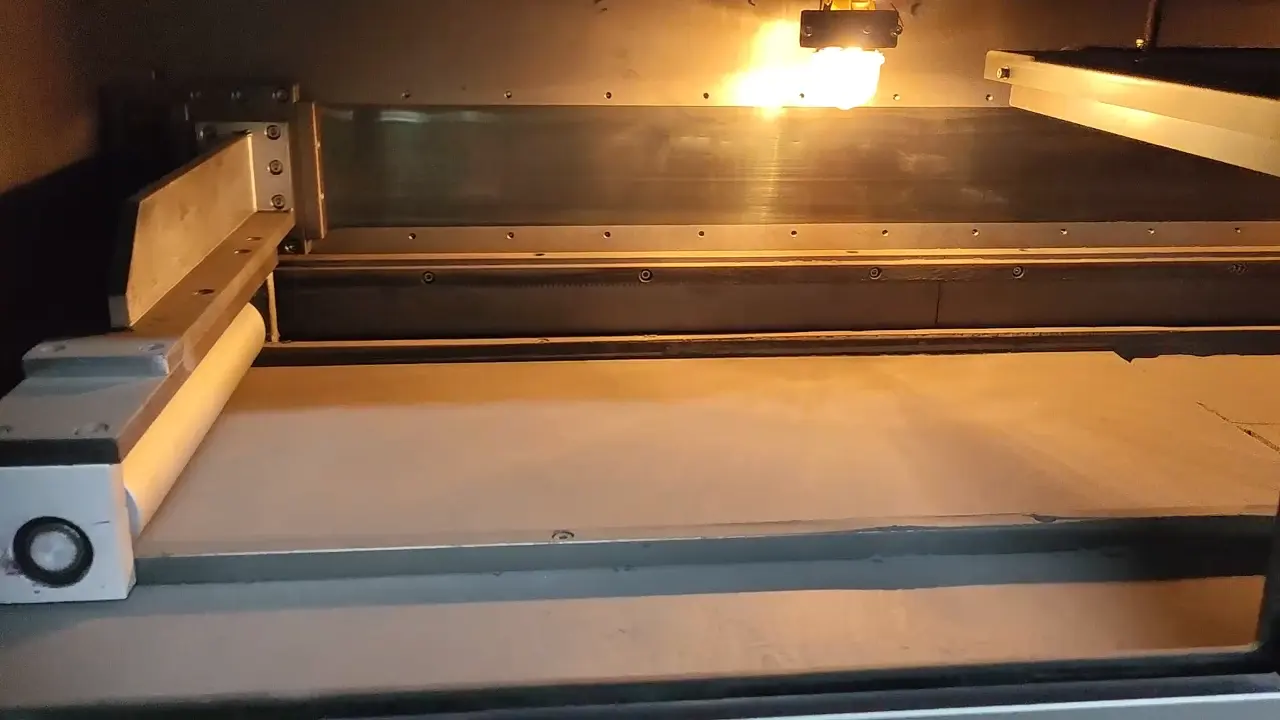
Selective Laser Sintering (SLS) represents a transformative additive manufacturing technology. It constructs three-dimensional objects by fusing powdered materials with a laser beam. This process builds components layer by layer, offering significant advantages over traditional subtractive manufacturing methods.
Key Process Features
- Material Versatility: Supports polymers (nylon, polystyrene) and metallic powders
- Self-Supporting Structure: Eliminates need for auxiliary support structures
- Precision Engineering: Achieves micron-level accuracy for intricate geometries
Operational Mechanism
- Digital Preparation: CAD model slicing into 2D layers
- Material Deposition: Uniform powder spreading via roller system
- Laser Fusion: Directed energy sintering of targeted areas
- Vertical Progression: Incremental platform lowering for layer stacking
- Post-Processing: Debinding and surface finishing operations
Performance Advantages
Attribute | Description |
Mechanical Strength | High-density parts through thermal fusion |
Design Freedom | Complex internal channels and lattice structures possible |
Material Efficiency | Up to 95% powder recyclability |
Functional Prototyping | Direct-use testing with production-grade material properties |
Customization | On-demand manufacturing of tailored components |
Essential SLS 3D Printer Accessories
1. Powder Management System
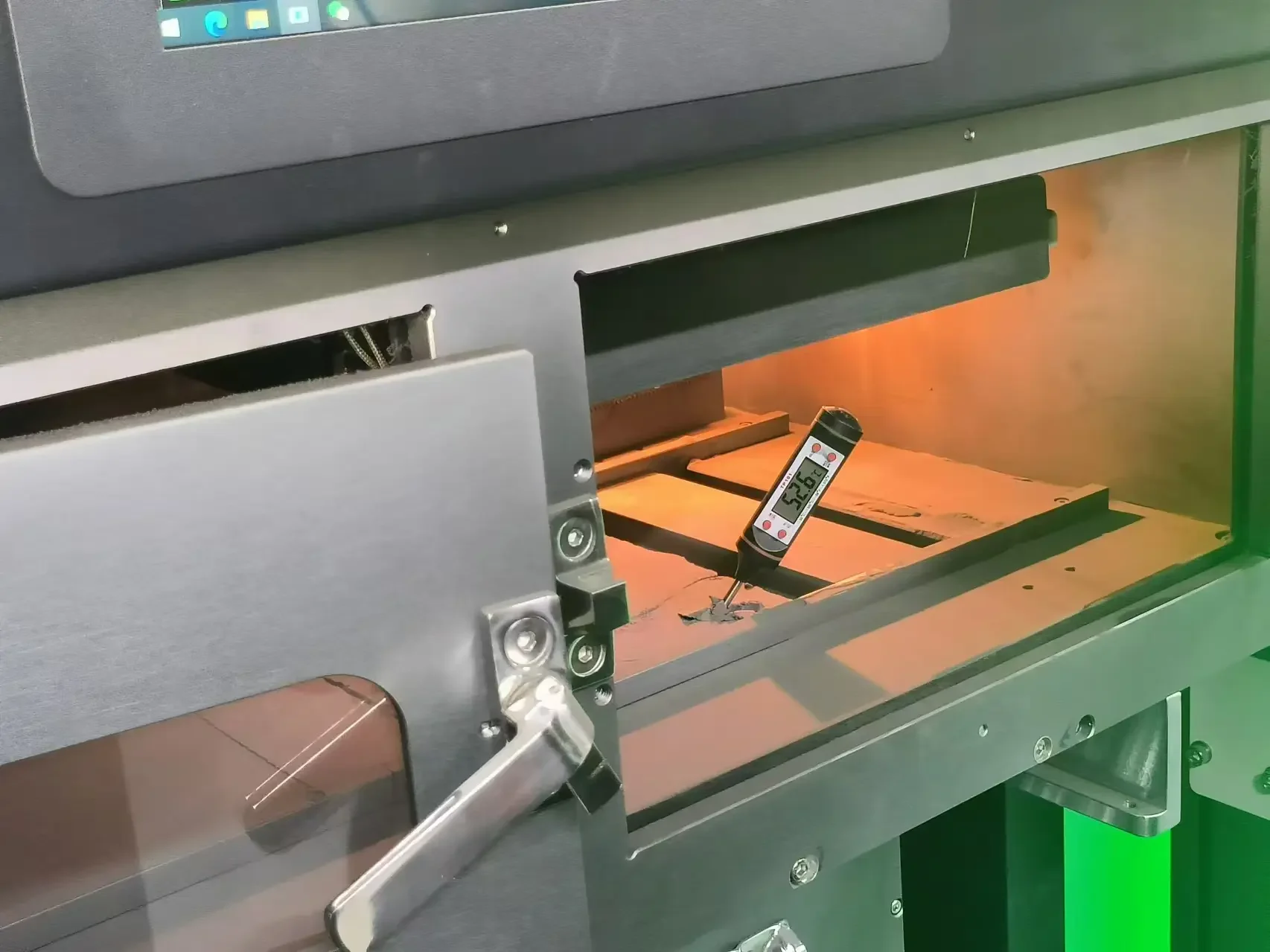
1.1 Storage Solutions
- Airtight containers with humidity control
- Vacuum-sealed packaging for extended material shelf life
1.2 Reclamation Technology
- Mechanical sieving units (mesh sizes: 50-150μm)
- Cyclonic separation systems for fine particle removal
2. Post-Processing Tools
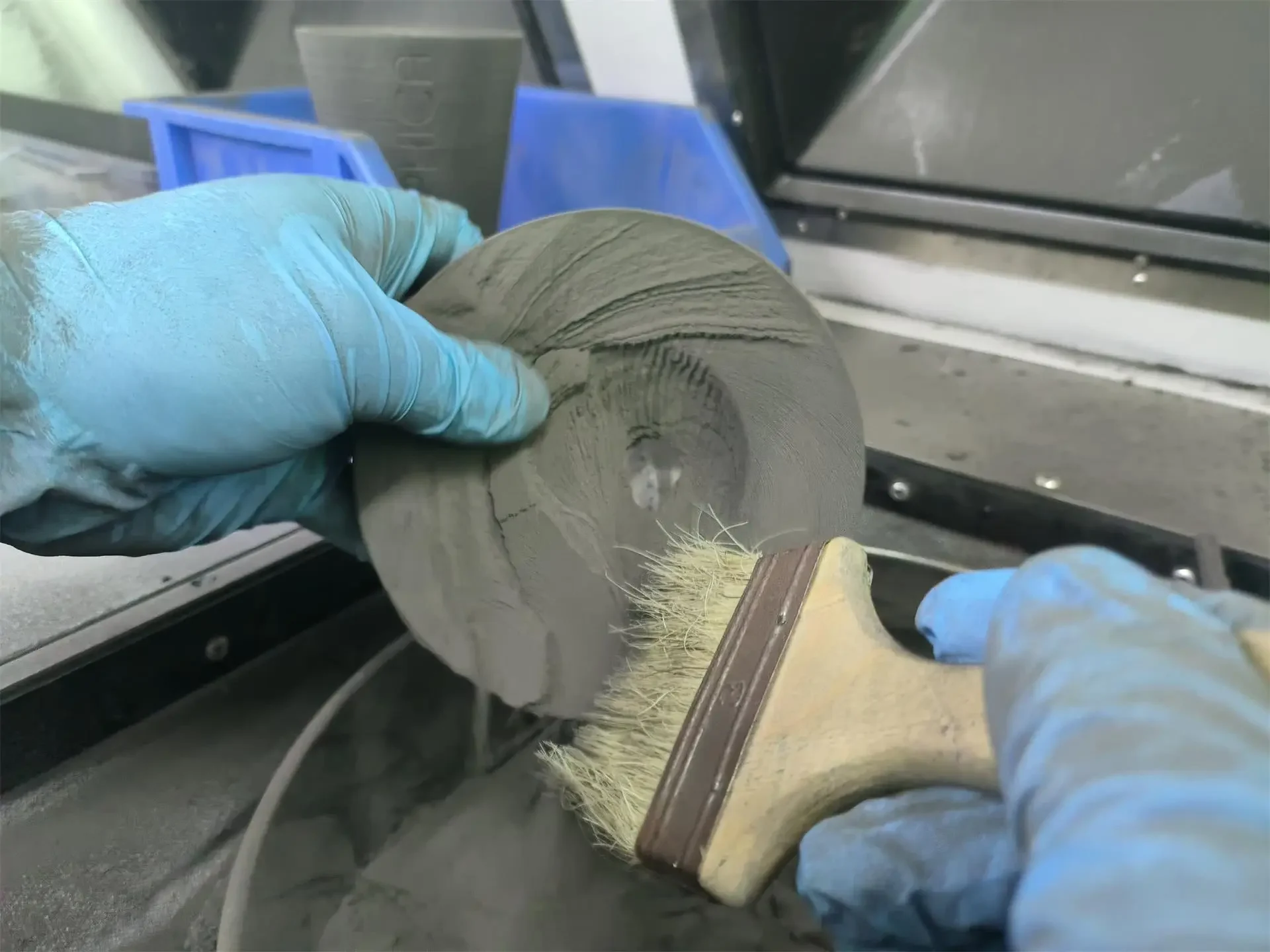
2.1 Surface Finishing
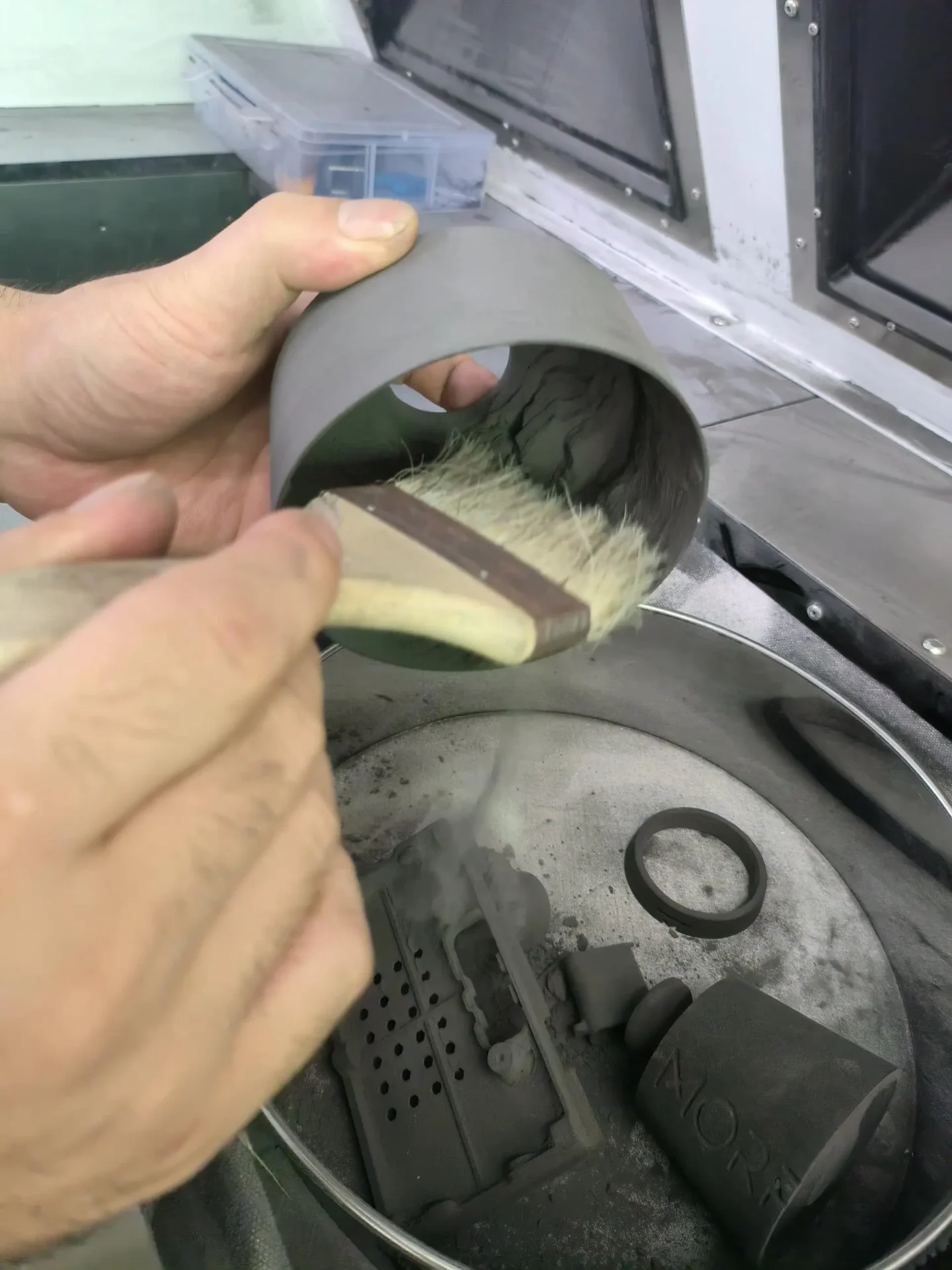
- Abrasive blasting equipment (aluminum oxide media)
- Polishing kits with diamond-coated tools
2.2 Cleaning Systems
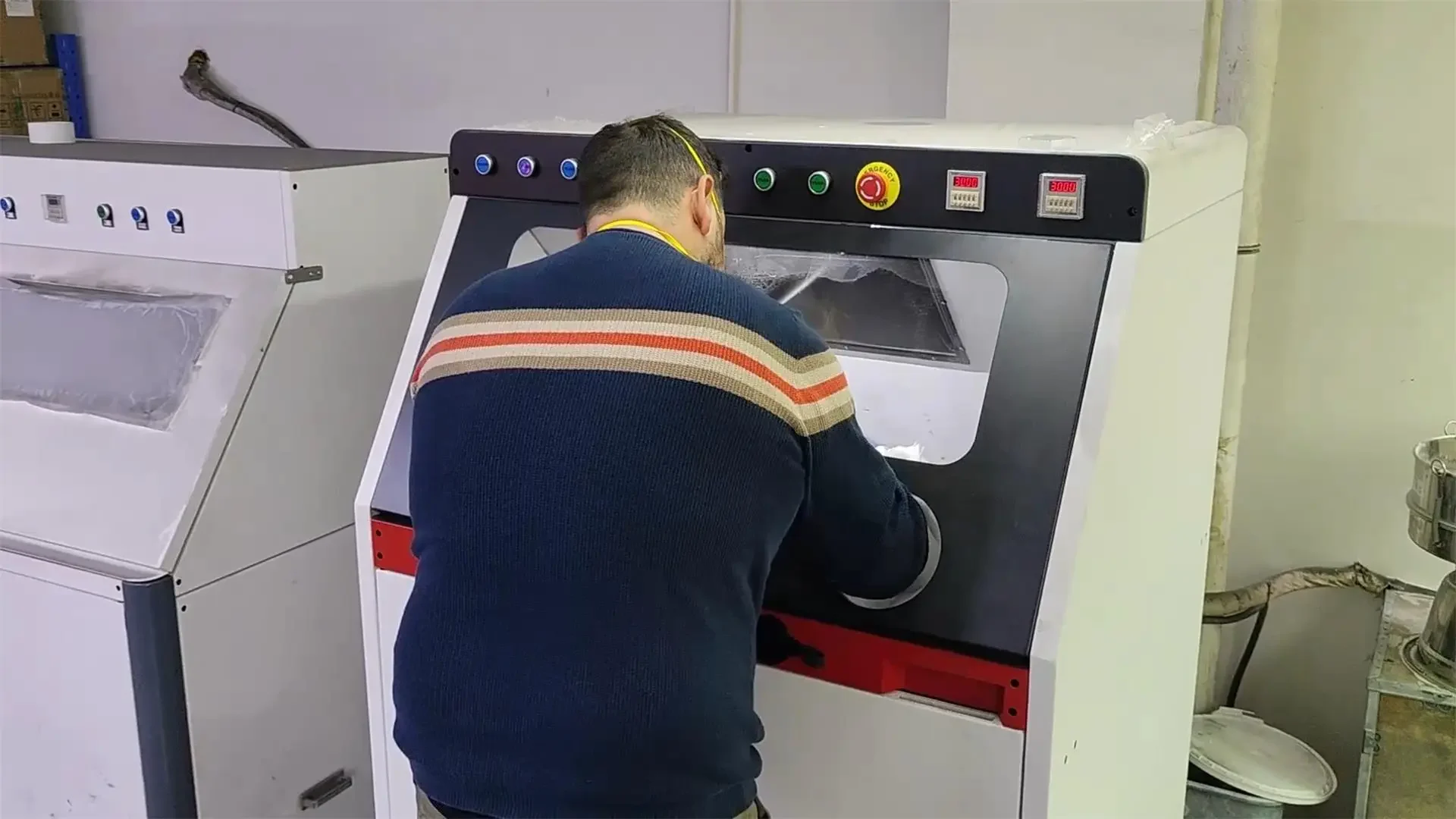
- Ultrasonic bath with 40kHz frequency
- High-pressure air blowers (60-90 PSI)
3. Safety Apparatus
- N95-rated particulate respirators
- Chemical-resistant gloves (nitrile rubber)
- HEPA-filtered fume extraction systems
4. Maintenance Tools
- Laser alignment kits with precision optics
- Thermal imaging cameras for platform temperature mapping
- Lubrication kits for moving components
Advanced Performance Upgrades
1. Laser System Enhancement
- Fiber laser modules (100-500W power range)
- Multi-laser configurations for parallel processing
2. Build Platform Innovations
- Programmable heated platforms (temperature range: 50-200°C)
- Vacuum-assisted build surfaces for improved powder adhesion
3. Remote Monitoring
- IoT-enabled sensors for real-time process tracking
- Cloud-based analytics platforms with predictive maintenance algorithms
4. Material-Specific Tools
- Automated powder feeding systems with metering pumps
- Dew point controllers for hygroscopic materials
Budgeting Considerations
Cost Comparison Table
Accessory Category | Price Range (USD) | ROI Timeline |
Powder Handling | 200-3,000 | 6-12 months |
Post-Processing | 150-2,500 | 3-6 months |
Safety Equipment | 100-800 | Immediate |
Advanced Upgrades | 1,000-10,000+ | 12-24 months |
Cost-Saving Strategies
- Refurbished equipment procurement
- Volume purchasing agreements
- Modular system expansion
Optimization Best Practices
1. Community Engagement
- Participate in additive manufacturing forums (e.g., Reddit’s r/3Dprinting)
- Attend industry conferences (RAPID + TCT)
2. Continuous Education
- Enroll in AM courses (MITx Additive Manufacturing MicroMasters)
- Subscribe to peer-reviewed journals (Additive Manufacturing)
3. Process Refinement
- Implement Design for Additive Manufacturing (DfAM) principles
- Conduct DOE (Design of Experiments) for parameter optimization
4. Workflow Automation
- Integration with ERP systems (e.g., SAP Business One)
- Use of digital twins for process simulation
Conclusion
Maximizing SLS 3D printing potential requires a strategic combination of advanced accessories, process optimization, and continuous learning. By investing in high-quality tools and adopting best practices, manufacturers can achieve superior part quality, reduced material waste, and accelerated production cycles. Stay updated with emerging trends in materials science and automation to maintain competitive advantage in this dynamic field.