In the rapidly evolving world of technology, 3D printing stands out as a revolutionary innovation, transforming how we create, design, and prototype. Among the various 3D printing technologies, Digital Light Processing (DLP) has emerged as a popular choice for enthusiasts and professionals alike. But what sets Top down DLP 3d printers apart, and why should you consider it for your next project?
Imagine being able to bring your creative ideas to life with precision and speed. That’s the promise of DLP 3D printers, especially the top-down models that offer unique advantages in the prototyping process. Whether you’re an engineer working on the next big invention or a hobbyist eager to explore new possibilities, understanding the intricacies of top-down DLP printing can unlock a world of potential.
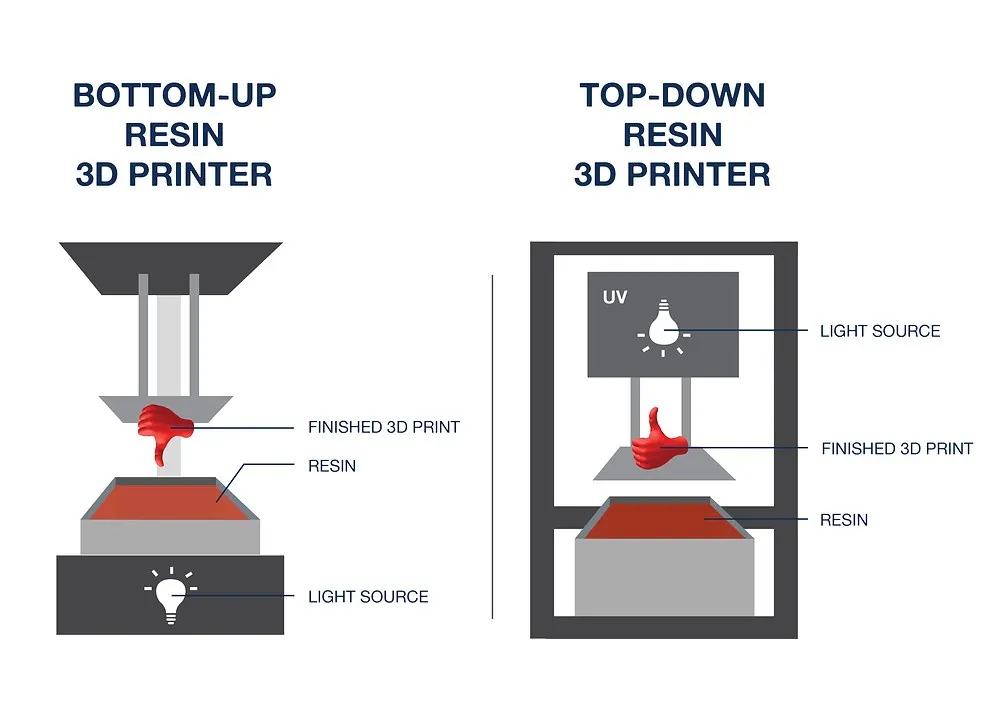
This guide will take you on a journey through the fascinating world of top-down DLP 3D printing. We’ll explore how these printers work, what makes them unique, and how you can leverage them to create successful prototypes. From choosing the right printer and materials to mastering the design and printing process, this comprehensive guide covers everything you need to know to succeed in the realm of top-down DLP 3D printing.
What is Top Down DLP 3D Printing?
The New Era of Precision and Innovation
Digital Light Processing (DLP) 3D printing has been making waves in the world of additive manufacturing, offering a unique blend of precision, speed, and versatility. But what exactly is top-down DLP 3D printing, and why is it generating so much buzz? Let’s dive deep into the details to uncover the magic behind this cutting-edge technology.
The Basics: Understanding DLP Technology
Digital Light Processing (DLP) is a 3D printing technology that uses a digital light projector to cure photopolymer resin layer by layer, creating highly detailed and accurate 3D objects. Unlike other 3D printing methods, DLP offers remarkable resolution and surface finish, making it ideal for applications where precision is paramount.
How DLP Works
- Light Projection: A digital projector shines light onto a vat of liquid photopolymer resin.
- Layer Curing: The light selectively cures the resin, hardening it layer by layer to form the desired object.
- Building Up: The build platform moves incrementally, allowing new layers of resin to be cured on top of the previous ones.
Top-Down vs. Bottom-Up DLP Printers
One of the key distinctions within DLP technology is the orientation of the printing process: top-down versus bottom-up.
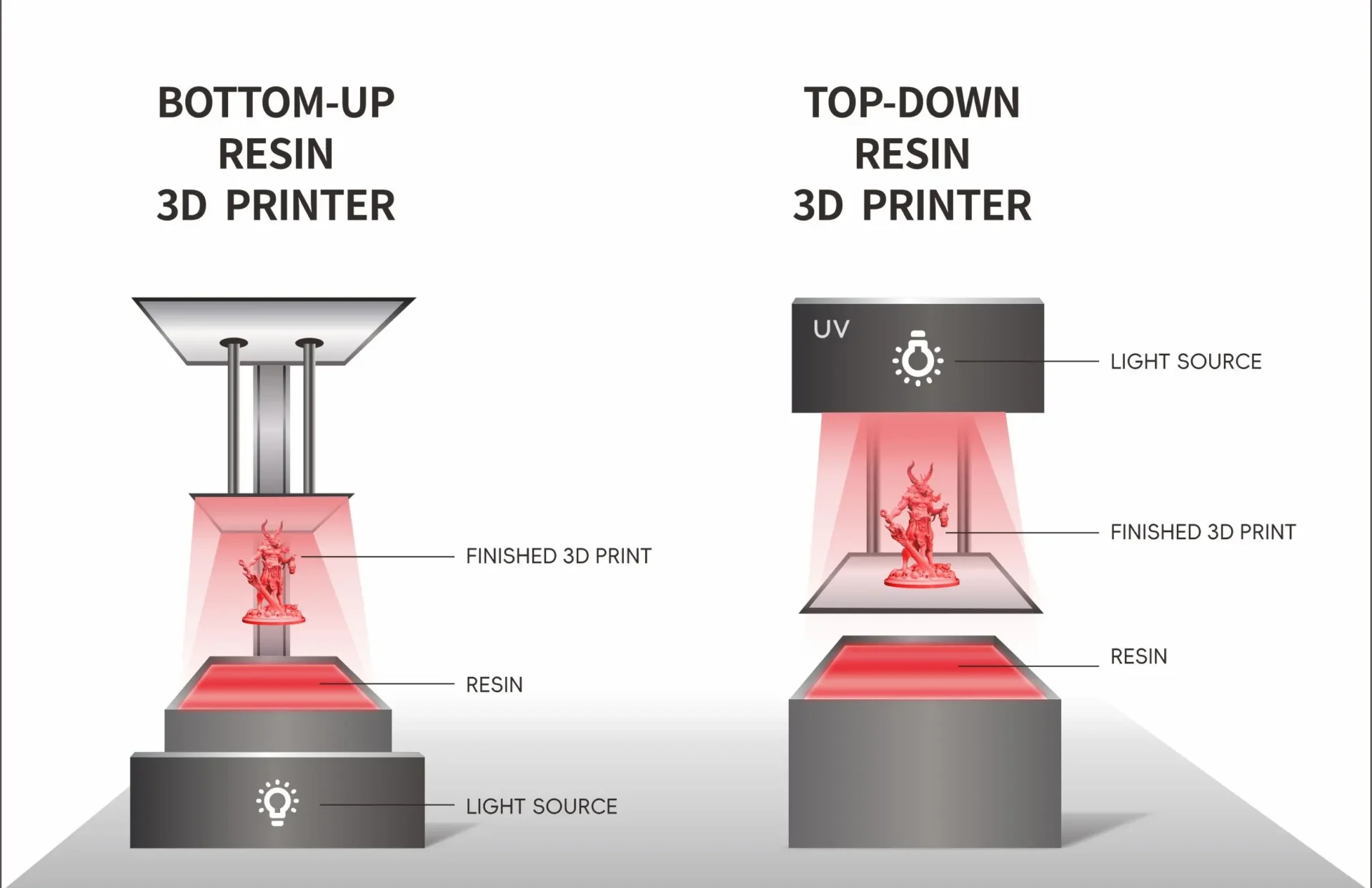
Aspect | Top-Down DLP Printers | Bottom-Up DLP Printers |
Orientation | The resin vat is above the build platform | The build platform is above the resin vat |
Layer Formation | Layers are cured from the top down | Layers are cured from the bottom up |
Advantages | Fewer support structures, easier resin management | Faster layer curing, reduced exposure time |
Challenges | Potential for resin waste, complex calibration | Requires robust support structures, potential sticking issues |
Why Choose Top-Down DLP Printers?
Top-down DLP printers offer several unique advantages that make them an attractive choice for various prototyping needs:
- Superior Surface Finish: The top-down approach often results in smoother surfaces and fewer visible layer lines.
- Reduced Support Structures: Since the print grows downwards, there’s less need for extensive support structures, simplifying post-processing.
- Easier Resin Management: Managing the resin vat is generally more straightforward, allowing for quicker material changes and less waste.
Key Components of a Top-Down DLP Printer
To fully appreciate the capabilities of top-down DLP printers, it’s essential to understand their key components:
- Digital Light Projector: Projects the light patterns that cure the resin.
- Resin Vat: Holds the photopolymer resin, positioned above the build platform.
- Build Platform: Moves incrementally to allow layer-by-layer curing.
- Z-Axis Mechanism: Controls the vertical movement of the build platform with high precision.
In-Depth Look: How Top-Down DLP Printing Works
Let’s break down the process step by step:
- Preparation: Load the digital 3D model into the printer’s software. The software slices the model into thin layers.
- Resin Loading: Fill the resin vat with the chosen photopolymer resin.
- Projection: The digital projector shines light onto the first layer of the resin, curing it.
- Layer Building: The build platform lowers incrementally, allowing each new layer of resin to be cured on top of the previous one.
- Completion: Once all layers are cured, the final object is carefully removed from the build platform.
Comparison with Other 3D Printing Methods
How does top-down DLP printing stack up against other popular 3D printing methods like FDM (Fused Deposition Modeling) and SLA (Stereolithography)?
Feature | Top-Down DLP | FDM | SLA |
Resolution | High | Moderate | High |
Surface Finish | Smooth | Rough | Smooth |
Material Choices | Limited to photopolymer resins | Wide variety of thermoplastics | Limited to photopolymer resins |
Speed | Fast | Moderate | Moderate |
Cost | Moderate to high | Low to moderate | Moderate to high |
Top-down DLP 3D printing represents a fascinating and powerful approach to additive manufacturing. By leveraging the unique benefits of DLP technology and the top-down orientation, you can achieve exceptional precision and efficiency in your prototyping efforts. Whether you’re a seasoned professional or a curious newcomer, understanding the nuances of top-down DLP printing opens up a world of creative possibilities.
How Does Top Down DLP Printing Work?
Unveiling the Magic Behind Precision Printing
Top-down DLP (Digital Light Processing) 3D printing is an incredible feat of modern engineering, merging light and liquid resin to create stunningly detailed 3D objects. But how exactly does this process work? Let’s peel back the layers and see the magic unfold step by step.
The Core Principle: Light and Resin
At the heart of top-down DLP printing lies a simple yet powerful principle: **using light to solidify liquid resin**. This method leverages a digital projector to shine light onto a vat of photopolymer resin, curing it layer by layer to build a 3D object.
Key Components of a Top-Down DLP Printer
To understand the process, we first need to familiarize ourselves with the key components:
- Digital Light Projector: Projects precise light patterns to cure the resin.
- Resin Vat: Holds the liquid photopolymer resin, positioned above the build platform.
- Build Platform: Moves incrementally to allow new layers to form.
- Z-Axis Mechanism: Controls the vertical movement of the build platform with high precision.
The Step-by-Step Process
Let’s break down the entire top-down DLP printing process into clear, manageable steps:
- Preparation:
- 3D Model Creation: Design your object using 3D modeling software.
- Slicing: The 3D model is sliced into thin layers using specialized software.
- Resin Selection: Choose the appropriate photopolymer resin based on your project’s requirements.
- Setup:
- Load the Resin: Pour the liquid resin into the resin vat.
- Calibrate the Printer: Ensure the build platform is leveled and properly calibrated.
- Printing:
- Layer Projection: The digital projector shines light onto the first layer of resin, curing it.
- Incremental Lowering: The build platform lowers incrementally, allowing each new layer of resin to be cured on top of the previous one.
- Repeating the Process: This process repeats until the entire object is built.
- Post-Processing:
- Object Removal: Carefully remove the printed object from the build platform.
- Cleaning: Rinse the object to remove any uncured resin.
- Curing: Perform additional curing if necessary to harden the object fully.
Advantages of Top-Down DLP Printing
Top-down DLP printing offers several distinct advantages that make it a preferred choice for many applications:
- High Resolution: The use of a digital projector allows for extremely fine detail and high resolution.
- Smooth Surfaces: The top-down approach often results in smoother surfaces, reducing the need for extensive post-processing.
- Efficient Resin Use: Managing the resin vat is more straightforward, allowing for efficient material use and quick changes.
Challenges and Considerations
While top-down DLP printing is powerful, it also comes with its own set of challenges:
- Resin Management: Handling and storing photopolymer resin requires care to avoid contamination and waste.
- Calibration: Precise calibration is crucial to ensure high-quality prints and avoid errors.
- Material Limitations: The range of available resins may be limited compared to other 3D printing materials.
Comparison with Other 3D Printing Methods
To fully appreciate top-down DLP printing, it’s helpful to compare it with other popular 3D printing methods:
Feature | Top-Down DLP | FDM | SLA |
Resolution | High | Moderate | High |
Surface Finish | Smooth | Rough | Smooth |
Material Choices | Limited to photopolymer resins | Wide variety of thermoplastics | Limited to photopolymer resins |
Speed | Fast | Moderate | Moderate |
Cost | Moderate to high | Low to moderate | Moderate to high |
Real-World Applications
Top-down DLP printing is used in various industries, including:
- Jewelry: Creating intricate and detailed designs.
- Dental: Producing custom dental implants and orthodontic devices.
- Prototyping: Rapidly creating prototypes for product development.
Top-down DLP 3D printing is a fascinating and powerful technology that offers unparalleled precision and efficiency. By understanding the step-by-step process and leveraging its unique advantages, you can unlock new possibilities in your creative and professional projects. Whether you’re a seasoned professional or a curious newcomer, mastering the intricacies of top-down DLP printing will open up a world of innovation and creativity.
Choosing the Right Top Down DLP Printer
Navigating the World of DLP Technology
With the increasing popularity of top-down DLP 3D printing, choosing the right printer for your needs can be a daunting task. How do you ensure you make the best investment? What features should you prioritize? Let’s break down everything you need to consider when selecting a top-down DLP printer.
Understanding Your Needs
Before diving into specifications, it’s crucial to **identify your specific needs**. Consider the following questions:
- What type of projects will you be working on?
- How important is print resolution to you?
- What is your budget?
- Do you need a large build volume?
Key Factors to Consider
When evaluating top-down DLP printers, focus on these essential factors:
1. Resolution
- Importance: Resolution determines the level of detail in your prints.
- Consideration: Look for a printer with a high resolution if you need fine details, such as in jewelry or dental applications.
2. Build Volume
- Importance: The build volume dictates the maximum size of the objects you can print.
- Consideration: Choose a printer with a build volume that suits your project needs.
3. Speed
- Importance: Speed affects how quickly you can complete a print job.
- Consideration: If time is a factor, look for printers known for faster printing speeds.
4. Material Compatibility
- Importance: Different printers support different types of resin.
- Consideration: Ensure the printer supports the materials you intend to use.
5. Ease of Use
- Importance: User-friendly interfaces and software can simplify the printing process.
- Consideration: Look for printers with intuitive controls and comprehensive support resources.
Popular Top-Down DLP Printer Models
Here are some popular models to consider, each offering unique features:
Model | Resolution | Build Volume | Speed | Price Range |
Model A | High | Medium | Fast | $$ |
Model B | Very High | Large | Moderate | $$$ |
Model C | Moderate | Small | Fast | $ |
Budget Considerations
Top-down DLP printers can vary widely in price. Here’s how to approach budgeting:
- Entry-Level: Typically range from $500 to $1,500. Suitable for hobbyists and small projects.
- Mid-Range: Priced between $1,500 and $5,000. Ideal for more serious enthusiasts or small businesses.
- High-End: Over $5,000. Designed for professional use and high-demand applications.
Making the Final Decision
When choosing a printer, consider:
- Reviews and Recommendations: Read reviews and seek recommendations from trusted sources.
- Manufacturer Support: Ensure the manufacturer offers good customer support and warranty options.
- Future Proofing: Consider whether the printer can be upgraded or expanded to meet future needs.
Choosing the right top-down DLP printer requires careful consideration of your specific needs, budget, and the printer’s capabilities. By focusing on key factors such as resolution, build volume, speed, and material compatibility, you can find a printer that perfectly aligns with your goals. Whether you’re a hobbyist or a professional, investing in the right printer will pave the way for successful and innovative projects.
Materials for Top Down DLP Printing
Unlocking the Potential of Photopolymer Resins
Choosing the right material is crucial for the success of your top-down DLP 3D printing projects. The material not only affects the final appearance and durability of your prints but also impacts the printing process itself. In this section, we’ll explore the various types of photopolymer resins available, their properties, and how to select the best one for your needs.
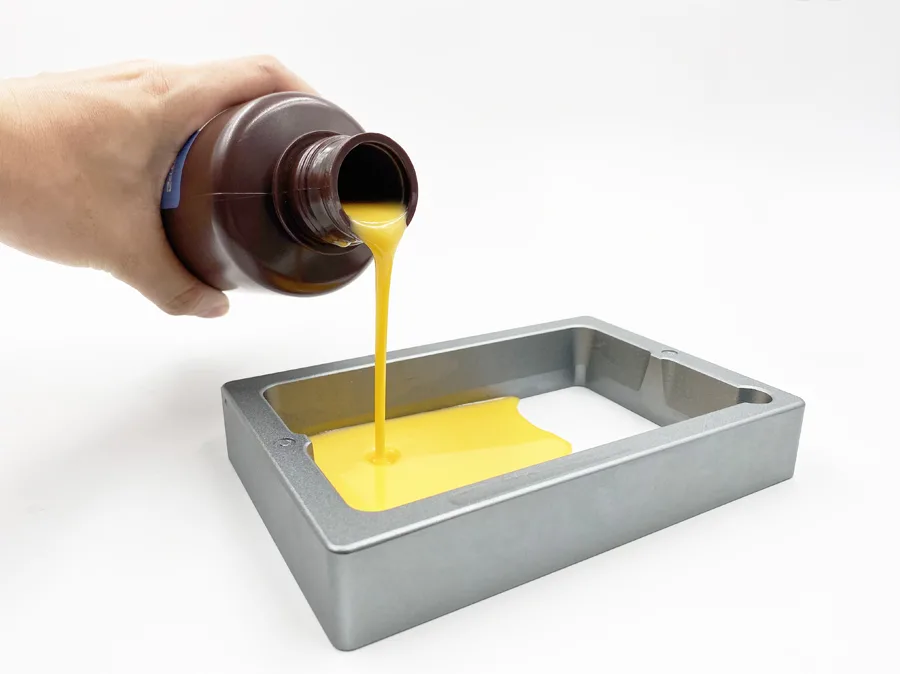
What Are Photopolymer Resins?
Photopolymer resins are light-sensitive materials that harden when exposed to a specific wavelength of light. In DLP 3D printing, these resins are cured layer by layer using a digital projector. The choice of resin can significantly influence the quality, strength, and appearance of the final print.
Types of Photopolymer Resins
1. Standard Resins
- Description: These are the most commonly used resins, suitable for a wide range of applications.
- Properties:
- Good surface finish
- Moderate strength
- Easy to work with
- Applications: Prototyping, general-purpose models, hobbyist projects
2. Tough Resins
- Description: Designed to withstand wear and tear, these resins are more durable than standard resins.
- Properties:
- High impact resistance
- Greater flexibility
- Enhanced durability
- Applications: Functional prototypes, mechanical parts, end-use products
3. Flexible Resins
- Description: These resins offer flexibility and elasticity, making them ideal for parts that need to bend or compress.
- Properties:
- High elasticity
- Soft and rubber-like texture
- Good tear resistance
- Applications: Soft-touch grips, flexible hinges, wearable devices
4. High-Temperature Resins
- Description: Suitable for applications requiring high thermal resistance.
- Properties:
- High heat deflection temperature
- Good dimensional stability
- Excellent mechanical properties
- Applications: Mold making, heat-resistant parts, automotive components
5. Castable Resins
- Description: Used for investment casting, these resins burn out cleanly, leaving minimal residue.
- Properties:
- Excellent burnout properties
- Smooth surface finish
- High detail resolution
- Applications: Jewelry, dental casting, precision metal parts
Key Factors to Consider When Choosing a Resin
When selecting a photopolymer resin, consider the following factors:
1. Mechanical Properties
- Strength: How much load the material can bear.
- Flexibility: The ability to bend without breaking.
- Durability: Resistance to wear and tear.
2. Thermal Properties
- Heat Resistance: Ability to withstand high temperatures.
- Thermal Expansion: How much the material expands or contracts with temperature changes.
3. Aesthetic Properties
- Surface Finish: Smoothness and quality of the print surface.
- Color: Available color options and translucency.
- Detail Resolution: Ability to capture fine details.
Comparison of Resin Types
Here’s a quick comparison of the different types of photopolymer resins:
Property | Standard Resin | Tough Resin | Flexible Resin | High-Temp Resin | Castable Resin |
Strength | Moderate | High | Low | High | Moderate |
Flexibility | Low | Moderate | High | Low | Low |
Durability | Moderate | High | Moderate | High | Low |
Heat Resistance | Low | Moderate | Low | High | Low |
Surface Finish | High | Moderate | High | High | Very High |
Detail Resolution | High | Moderate | High | High | Very High |
Tips for Working with Resins
1. Storage and Handling
- Storage: Keep resins in a cool, dark place to prevent premature curing.
- Handling: Use gloves and protective eyewear to avoid skin and eye contact.
2. Mixing
- Homogeneity: Stir the resin well before use to ensure uniform consistency.
- Additives: Some resins may require additives to enhance properties like color or viscosity.
3. Post-Processing
- Cleaning: Rinse prints in isopropyl alcohol to remove uncured resin.
- Curing: Use a UV curing station to fully harden the print and achieve optimal mechanical properties.
Choosing the right photopolymer resin is a critical step in ensuring the success of your top-down DLP 3D printing projects. By understanding the different types of resins and their properties, you can make informed decisions that align with your specific needs and applications. Whether you’re creating detailed jewelry, durable functional parts, or flexible components, the right resin will unlock the full potential of your DLP printer.
Specialized Applications of Top Down DLP Printing
Exploring the Diverse Use Cases
Top-down DLP 3D printing is a versatile technology that finds applications across a wide range of industries. Its ability to produce high-resolution, detailed, and complex parts makes it suitable for specialized applications that demand precision and quality. In this section, we’ll explore some of the most notable applications of top-down DLP printing and how this technology is revolutionizing various fields.
Medical and Dental Applications
1. Medical Models and Surgical Guides
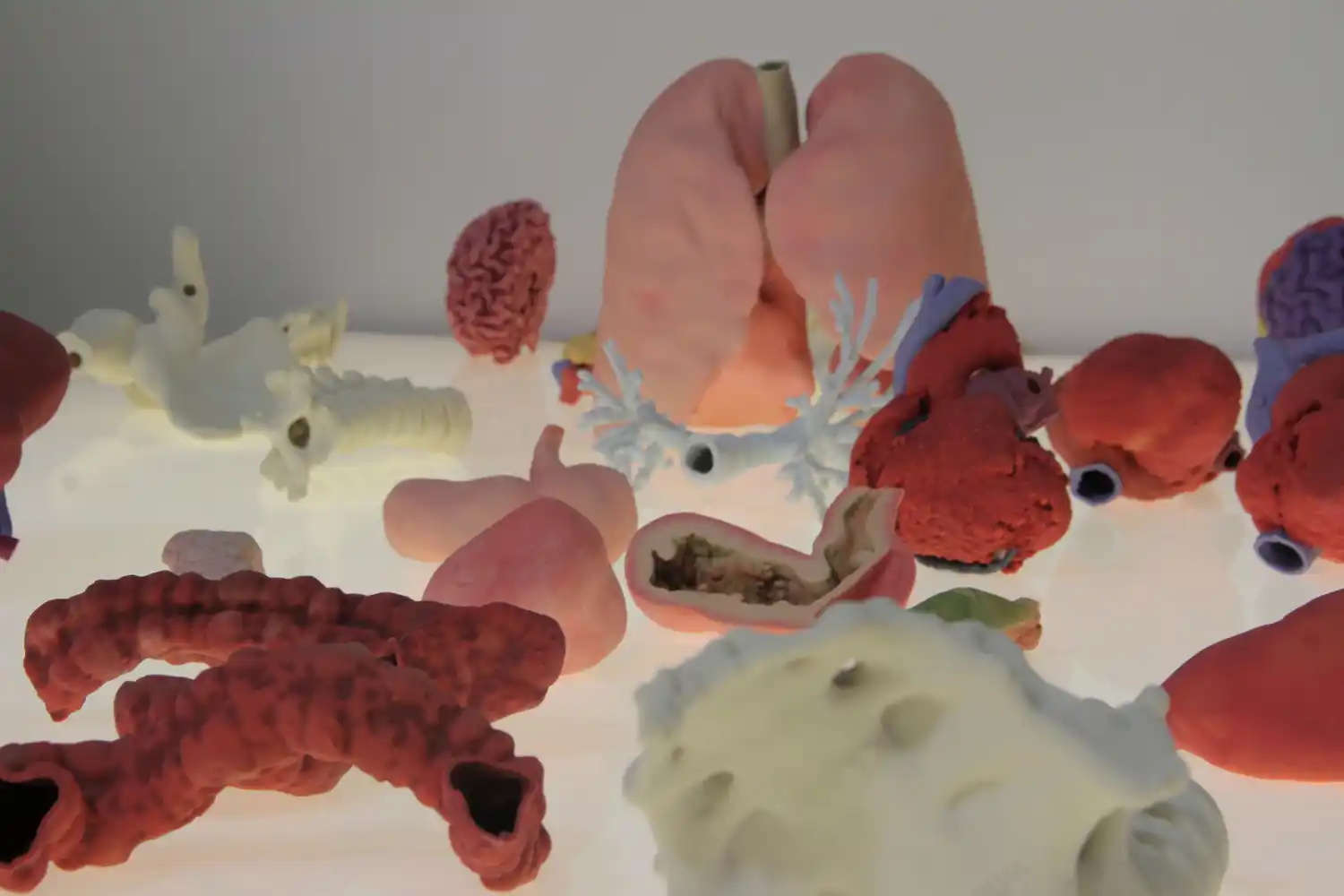
- Purpose: Create accurate anatomical models and surgical guides to assist in pre-surgical planning and intraoperative procedures.
- Benefits: Enhances surgical precision, reduces operation time, and improves patient outcomes.
- Example: Customized models of a patient’s anatomy, such as bones or organs, to plan complex surgeries.
2. Dental Prosthetics and Aligners
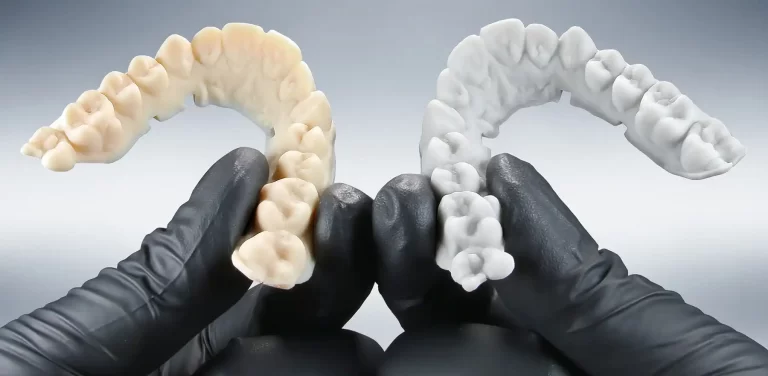
- Purpose: Produce dental prosthetics, crowns, bridges, and clear aligners with high precision.
- Benefits: Offers a perfect fit, improves patient comfort, and speeds up the production process.
- Example: Custom-fit dental aligners for orthodontic treatments.
Jewelry and Fashion
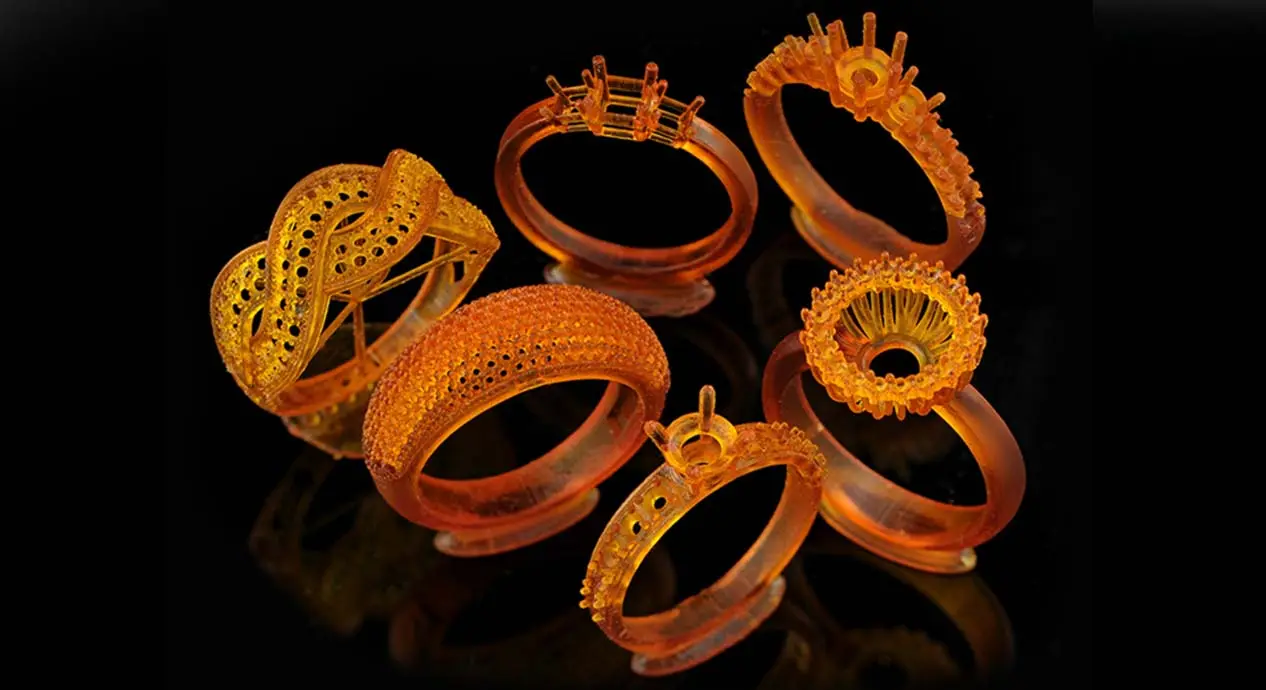
1. Intricate Jewelry Designs
- Purpose: Create detailed and intricate jewelry pieces with high precision and fine details.
- Benefits: Enables the production of complex designs that are difficult or impossible to achieve with traditional methods.
- Example: Custom-designed rings, earrings, and pendants with intricate patterns and fine details.
2. Fashion Accessories
- Purpose: Design and produce unique fashion accessories, such as buttons, buckles, and embellishments.
- Benefits: Allows for rapid prototyping and production of custom accessories tailored to specific fashion trends.
- Example: Custom-designed buttons and buckles for high-end fashion garments.
Aerospace and Automotive
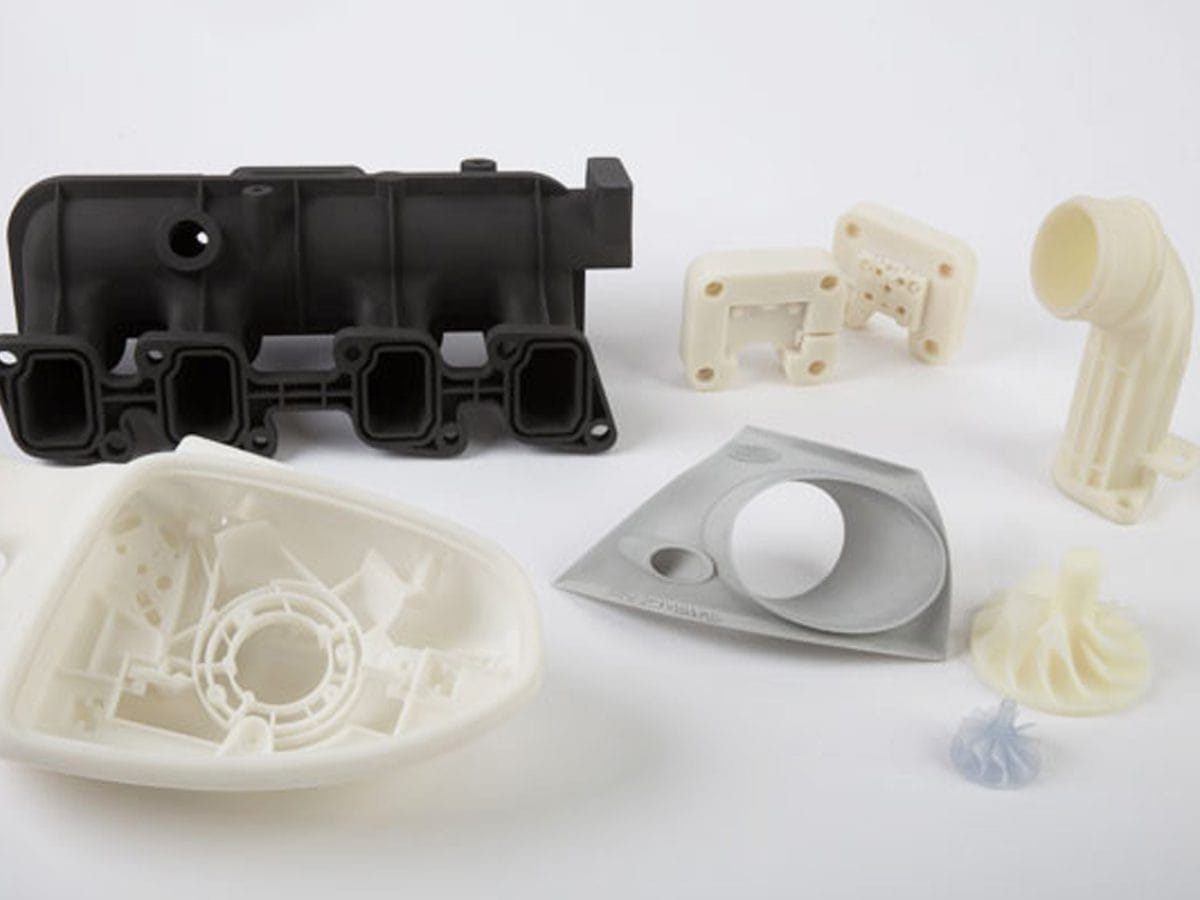
1. Lightweight Components
- Purpose: Produce lightweight yet strong components for aerospace and automotive applications.
- Benefits: Reduces overall weight, improves fuel efficiency, and enhances performance.
- Example: Lightweight structural components for aircraft and automotive parts.
2. Complex Geometries
- Purpose: Manufacture components with complex geometries that are difficult to produce using traditional methods.
- Benefits: Enables the creation of optimized designs for improved functionality and performance.
- Example: Complex air ducts and heat exchangers for aerospace applications.
Consumer Electronics
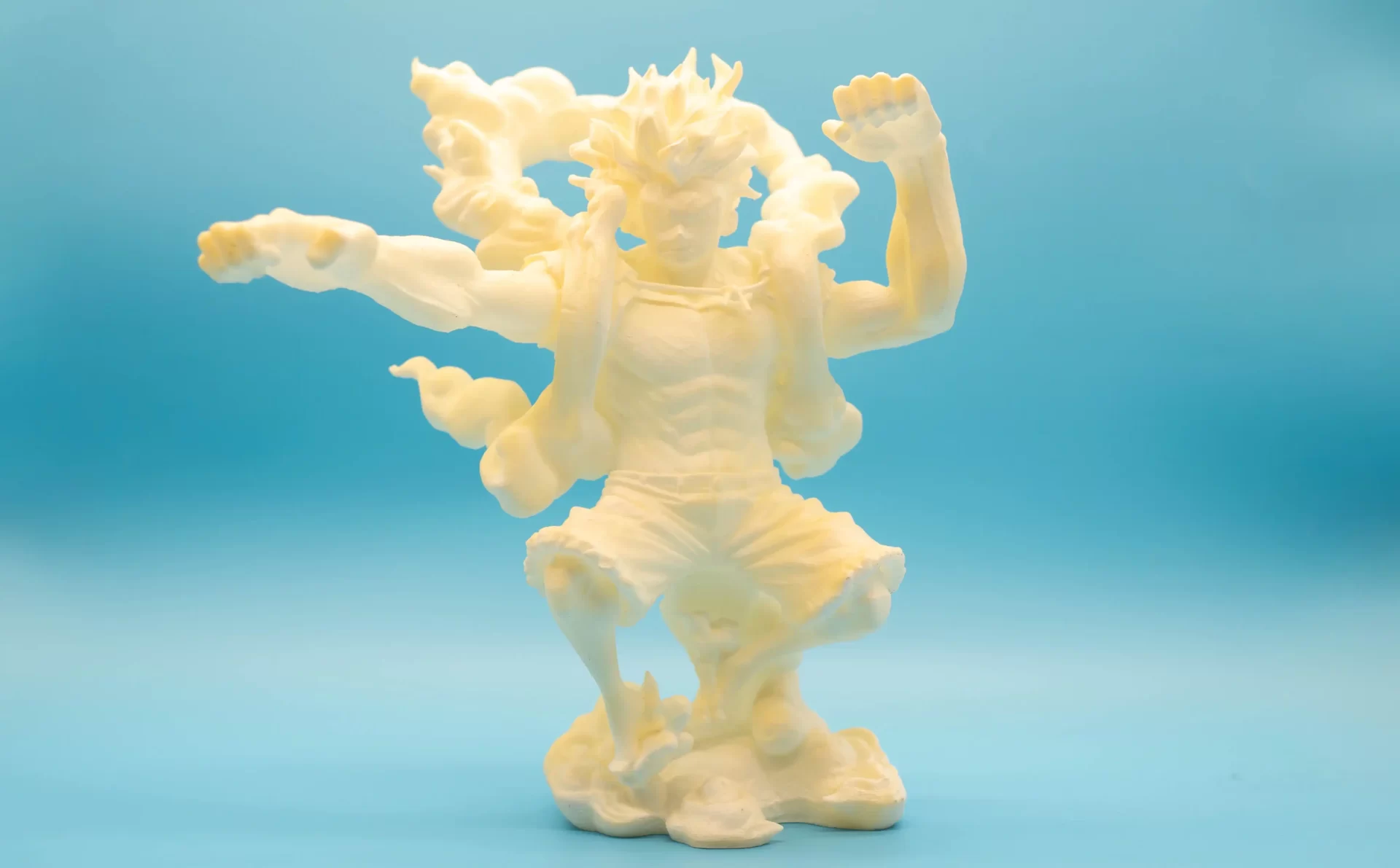
1. Prototyping and Product Development
- Purpose: Rapidly prototype and iterate on consumer electronics designs, such as cases, enclosures, and components.
- Benefits: Speeds up the product development cycle and allows for quick design changes and improvements.
- Example: Prototyping smartphone cases and electronic device enclosures.
2. Custom Components
- Purpose: Produce custom components and parts for consumer electronics, tailored to specific requirements.
- Benefits: Enables the creation of unique and personalized products.
- Example: Custom-designed buttons and knobs for electronic devices.
Education and Research
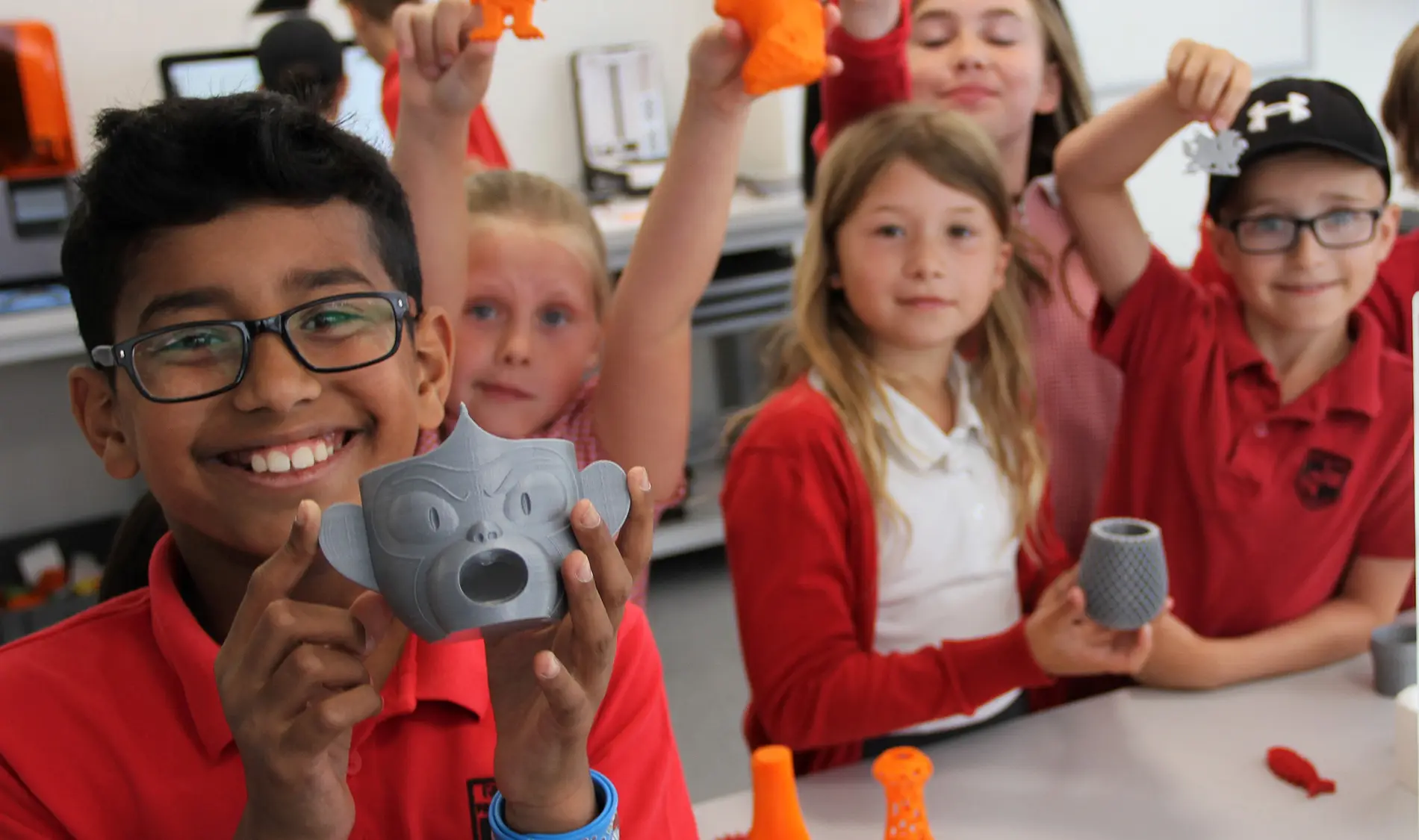
1. Educational Models
- Purpose: Create educational models and teaching aids for various subjects, such as biology, engineering, and art.
- Benefits: Enhances the learning experience with tangible, hands-on models.
- Example: Anatomical models for biology classes, architectural models for engineering courses.
2. Research Prototypes
- Purpose: Develop prototypes for research projects and experiments in various scientific fields.
- Benefits: Allows researchers to test and validate their concepts quickly and efficiently.
- Example: Prototyping experimental devices and components for scientific research.
Art and Sculpture
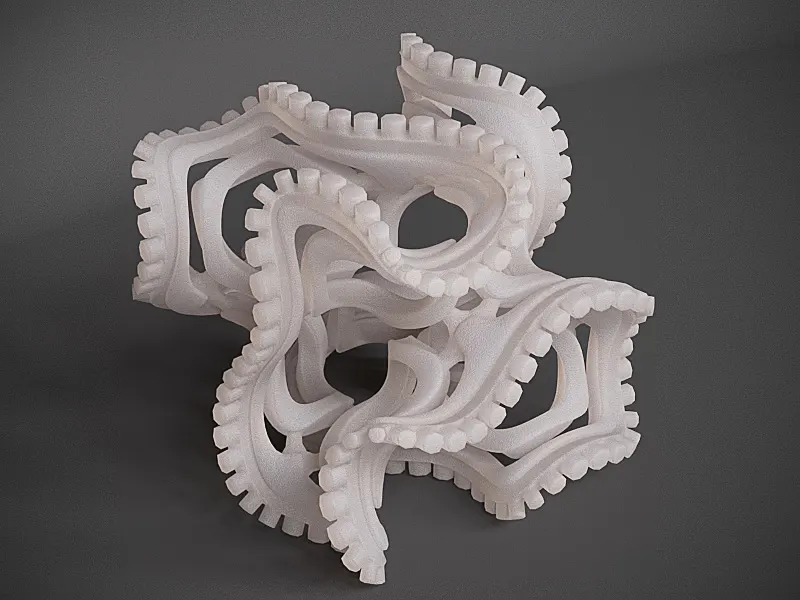
1. Custom Art Pieces
- Purpose: Design and produce custom art pieces and sculptures with intricate details and complex geometries.
- Benefits: Enables artists to realize their creative visions with precision and accuracy.
- Example: Custom-designed sculptures and art installations.
2. Restoration and Replication
- Purpose: Restore and replicate historical artifacts and sculptures with high fidelity.
- Benefits: Preserves cultural heritage and allows for the creation of accurate replicas.
- Example: Replicating ancient sculptures and artifacts for museums and exhibitions.
Conclusion
Top-down DLP 3D printing is a powerful and versatile technology that is transforming various industries with its ability to produce high-quality, precise, and complex parts. From medical and dental applications to jewelry, aerospace, consumer electronics, education, and art, the specialized applications of top-down DLP printing are vast and diverse. By leveraging this technology, professionals and creatives in these fields can push the boundaries of innovation and achieve new levels of excellence in their work.
Future Trends in Top Down DLP Printing
Anticipating the Next Wave of Innovations
As top-down DLP 3D printing continues to evolve, we can expect to see significant advancements that will further enhance its capabilities and expand its applications. In this section, we’ll explore some of the most promising future trends in top-down DLP printing, highlighting emerging technologies and innovations that are poised to shape the future of this exciting field.
Enhanced Material Science
1. New Photopolymer Resins
- Development: Researchers are continuously developing new photopolymer resins with enhanced properties, such as increased strength, flexibility, and biocompatibility.
- Impact: These advanced materials will enable the production of more durable and functional parts, expanding the range of applications for top-down DLP printing.
- Example: High-performance resins for aerospace components or biocompatible resins for medical implants.
2. Smart Materials
- Concept: Smart materials can change their properties in response to external stimuli such as temperature, light, or electrical fields.
- Impact: This will allow for the creation of adaptive and multifunctional components, opening up new possibilities in fields like robotics and wearable technology.
- Example: Temperature-responsive materials that change shape or stiffness in response to body heat.
Integration with AI and Machine Learning
1. AI-Driven Design Optimization
- Development: AI and machine learning algorithms can analyze and optimize designs for better performance and manufacturability.
- Impact: This will lead to more efficient and effective design processes, reducing the time and resources required to develop high-quality parts.
- Example: AI-driven software that suggests design modifications to improve structural integrity and reduce material usage.
2. Predictive Maintenance and Quality Control
- Concept: AI can be used to monitor and predict maintenance needs for 3D printers, as well as to ensure consistent print quality.
- Impact: This will minimize downtime and reduce the risk of print failures, ensuring a more reliable and efficient printing process.
- Example: Machine learning algorithms that predict when a printer component is likely to fail and recommend preemptive maintenance.
Hybrid Manufacturing
1. Combining Additive and Subtractive Techniques
- Development: Hybrid manufacturing systems that integrate additive (3D printing) and subtractive (CNC machining) techniques are becoming more prevalent.
- Impact: This will allow for the production of parts with complex geometries and high precision, combining the strengths of both methods.
- Example: A hybrid system that 3D prints a part and then uses CNC machining to achieve precise surface finishes and tight tolerances.
2. Multi-Process Printing
- Concept: Systems that combine multiple 3D printing processes, such as FDM, SLA, and DLP, within a single machine.
- Impact: This will enable the production of multi-material and multi-property parts, increasing the versatility and functionality of printed components.
- Example: A printer that uses FDM for the main structure and DLP for detailed features and fine surfaces.
Scaling Up and Industrial Applications
1. Large-Scale DLP Printing
- Development: Advances in projector technology and build platform design are enabling larger build volumes for top-down DLP printers.
- Impact: This will allow for the production of larger parts and assemblies, making DLP printing more suitable for industrial applications.
- Example: Large-scale prototypes and end-use parts for automotive and aerospace industries.
2. Automated Production Lines
- Concept: Integration of top-down DLP printers into automated production lines with robotic handling and post-processing.
- Impact: This will streamline the manufacturing process, enabling high-throughput production of 3D printed parts with minimal human intervention.
- Example: An automated production line that prints, cures, and inspects parts for mass production.
Sustainability and Eco-Friendly Practices
1. Recyclable and Biodegradable Resins
- Development: The creation of recyclable and biodegradable photopolymer resins to reduce environmental impact.
- Impact: This will make top-down DLP printing more sustainable, aligning with global efforts to reduce plastic waste and promote eco-friendly practices.
- Example: Biodegradable resins for consumer products that can be composted after use.
2. Energy-Efficient Printing
- Concept: Developing more energy-efficient DLP printing systems that consume less power and reduce overall energy usage.
- Impact: This will lower the carbon footprint of 3D printing operations, making it a greener manufacturing option.
- Example: Energy-efficient projectors and optimized printing algorithms that reduce power consumption.
Conclusion
The future of top-down DLP 3D printing is bright, with numerous exciting trends and innovations on the horizon. Enhanced material science, integration with AI and machine learning, hybrid manufacturing, large-scale applications, and sustainable practices are all set to drive the next wave of advancements in this field. By staying informed and embracing these emerging technologies, professionals and enthusiasts alike can continue to push the boundaries of what’s possible with top-down DLP printing.
Related All in One Industrial-Grade Top Down DLP 3D Printer
Super Maker DM200
Discover The Future Of High-Speed, High-Precision 3D Printing Start-Up machine.
Super Maker DM400
Discover The Future Of High-Speed, High-Precision 3D Printing Start-Up machine.