In the ever-changing landscape of military technology, the term ‘innovation’ has evolved from a buzzword to a grim necessity. For many decades, the defense industry has been a crucible for pioneering development, driving a growth pattern that often spills over into civilian use. Many technologies we take for granted today, from the Internet to GPS, originated from the needs of national defense. Now, a new frontier is emerging that could radically change the way military forces design, manufacture, and deploy their equipment. This frontier is known as Selective Laser Sintering (SLS) 3D printing.
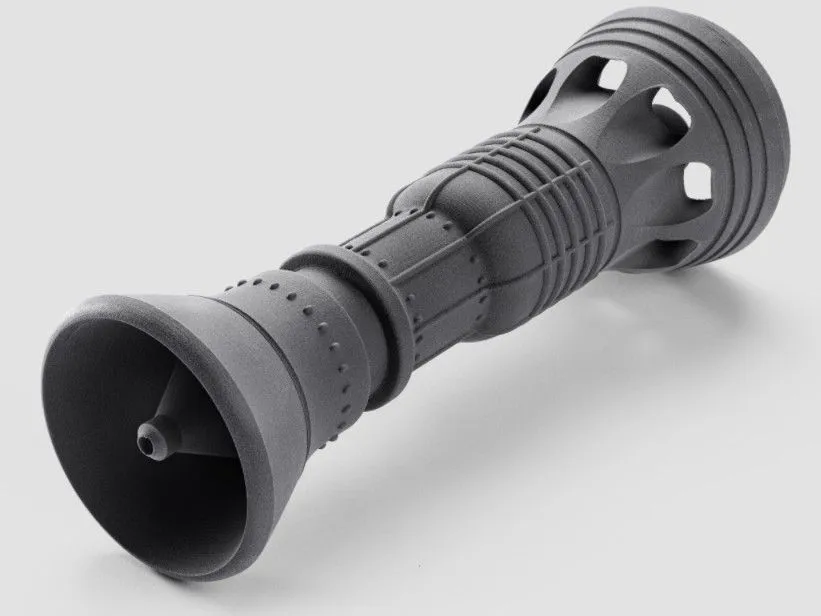
SLS 3D printing is more than just a new tool in the manufacturing toolbox; it is a game-changer. Imagine a world where military forces can create intricate parts on the field with unprecedented accuracy. Imagine a scenario where the logistical challenges of spare parts transportation across conflict zones are a thing of the past. These are not distant dreams but emerging realities, thanks to the transformative potential of SLS 3D printing.
The Intersection of SLS 3D Printing and Military Applications
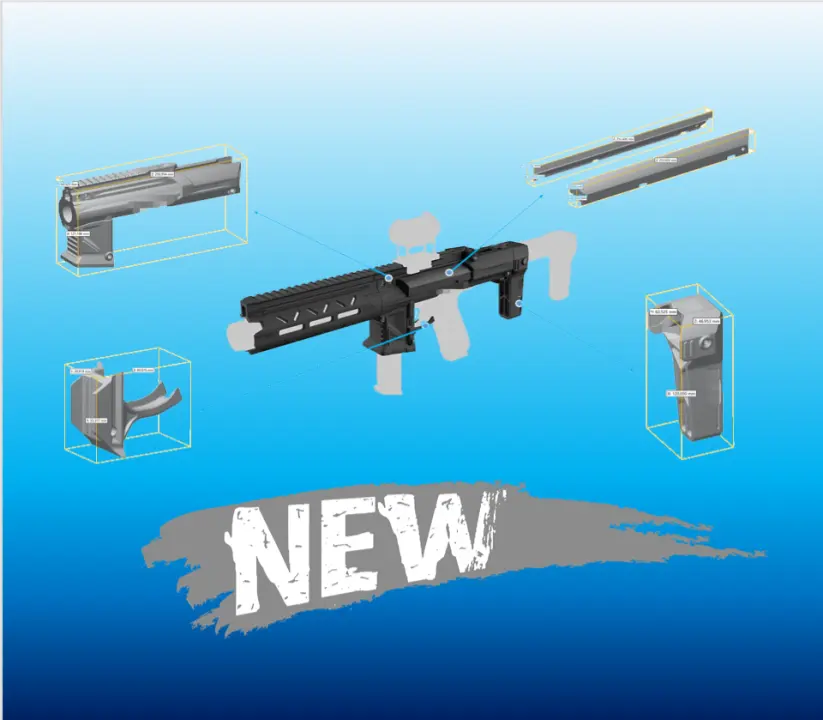
The defense sector has always been fertile ground for technological innovation. From the development of radar during World War II to the advent of stealth technology, many of the major technological innovations of the past century have been driven by military needs. As we step into a new era of manufacturing, SLS 3D printing emerges as another revolutionary tool that promises to redefine the military’s capabilities and capacities.
Historical Context and Adoption
To understand the impact of SLS 3D printing, it’s important to look back at its origins and early adoption in the defense sector. Developed in the mid-1980s by Dr. Carl Deckard and Dr. Joe Beaman at the University of Texas at Austin, SLS 3D printing uses a laser to sinter powdered material, layer by layer, into a solid structure. This technology enables the creation of highly complex and accurate parts that traditional manufacturing methods cannot achieve.
Current Military Applications of SLS 3D Printing
Today, SLS 3D printing is utilized across various military applications. Its ability to produce complex, durable parts on-demand has made it an invaluable tool for modern armed forces.
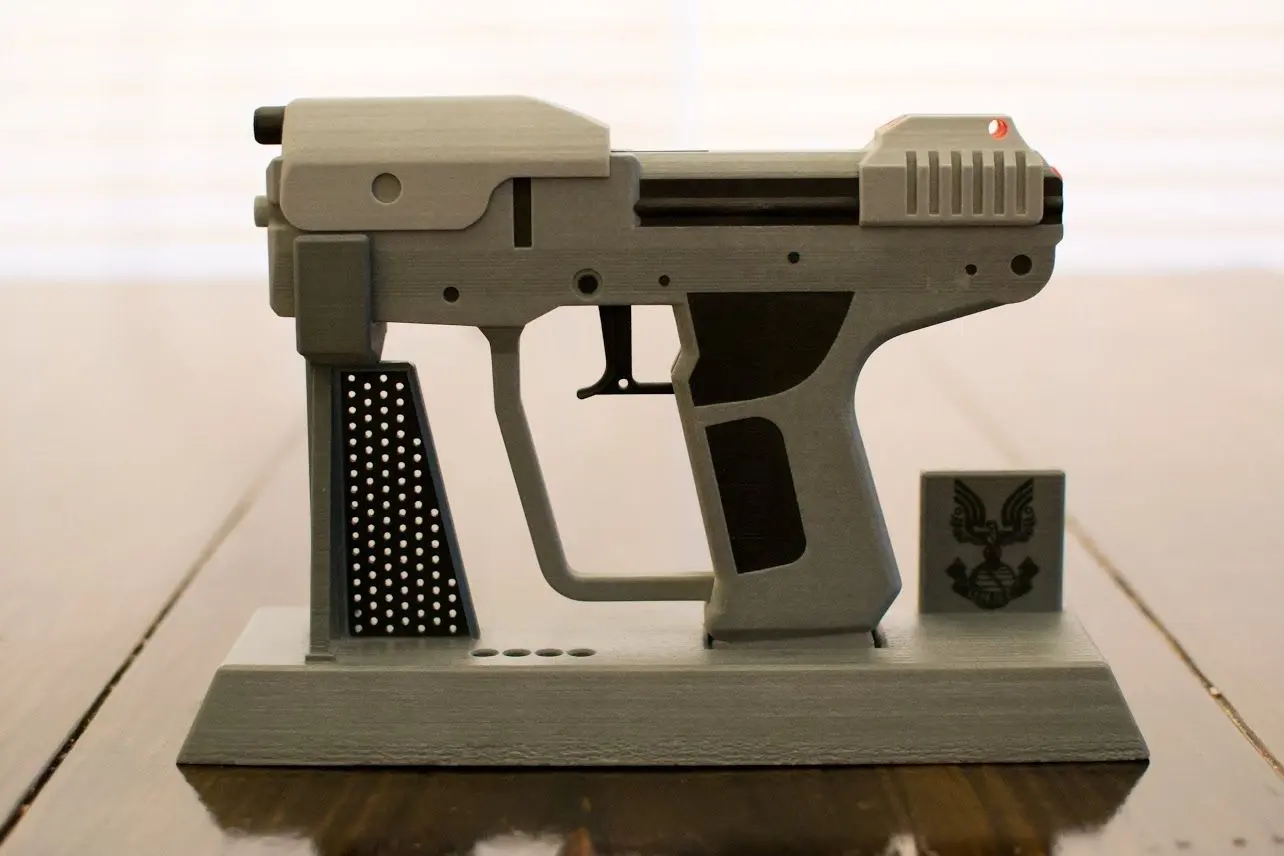
Examples of Military Equipment and Components Produced Using SLS:
- Prototyping and Design Iteration:
- Rapid prototyping of new weapon systems and vehicles.
- Iterative testing and refinement of designs.
- Spare Parts and Maintenance:
- On-demand production of spare parts in the field.
- Reduction of logistical challenges and downtime.
- Personalized Equipment:
- Custom-fit gear and equipment for individual soldiers.
- Enhanced comfort and performance.
A notable example is the U.S. Navy’s use of the technology to create custom drone parts. These parts are often geometrically complex and must operate under various environmental stresses, making SLS an ideal fabrication method. Similarly, the U.S. Air Force has used SLS 3D printing to manufacture specialized components for fighter jets, a process much faster and cheaper than traditional methods.
Advantages of SLS 3D Printing for the Defense Sector
In the high-stakes world of defense, every advantage matters. Technological innovations can be the difference between mission success and failure. Integrating SLS 3D printing into the defense arena comes with a set of advantages that cannot be ignored, from enhancing design capabilities to cost savings and material efficiency.
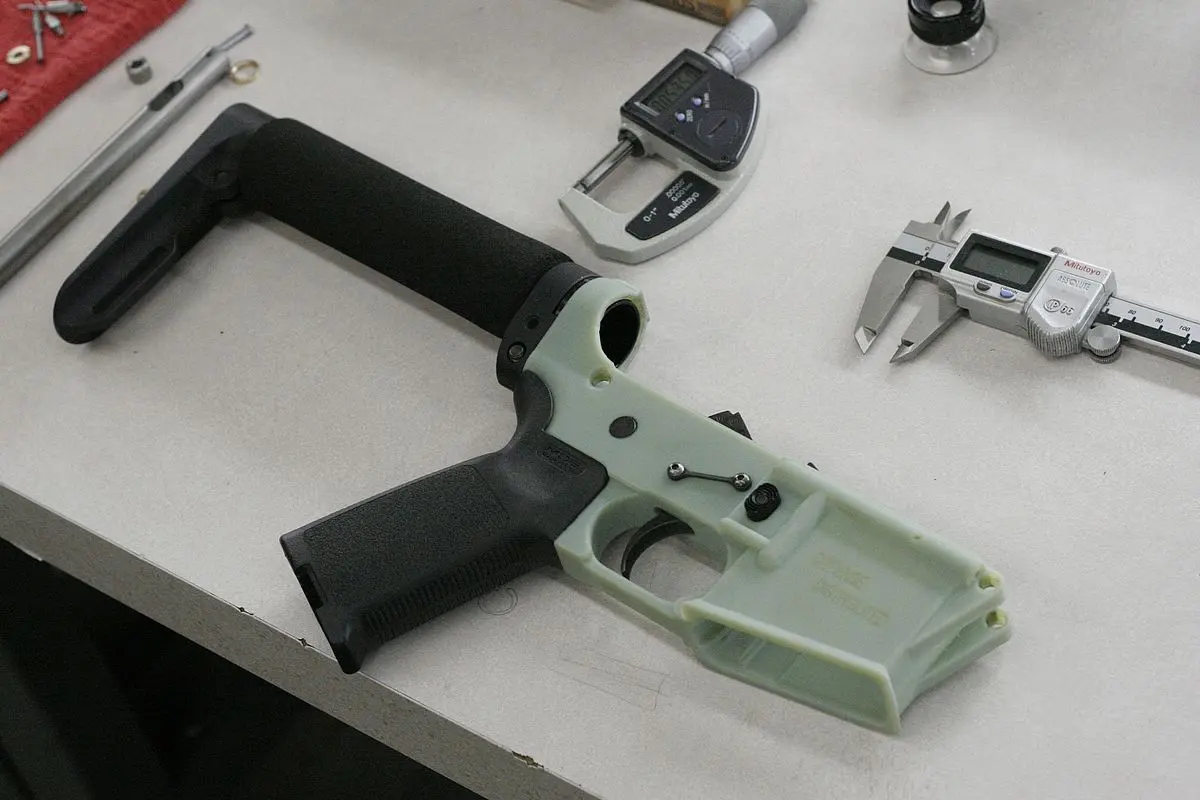
Better Design and Prototyping:
- Speed of Prototyping: Engineers can quickly produce and test multiple versions of a design, significantly reducing development time.
- Design Freedom: SLS 3D printing can create intricate designs that would be difficult or impossible to achieve with traditional methods.
Material Efficiency and Waste Reduction:
- Reduced Waste: SLS 3D printing uses only the material needed for the part, minimizing waste.
- Cost Savings: The efficiency of the SLS process can lead to significant cost savings in production.
Economic Impacts and Investment Opportunities
The economic implications of SLS 3D printing in the defense sector are profound. By reducing production costs and improving efficiency, SLS 3D printing offers substantial long-term financial benefits.
Cost Reduction and Budget Efficiency:
- Lower Production Costs: Material savings and optimized material use lower production costs.
- Cost-Effective Prototyping: Rapid prototyping reduces the overall cost of development.
Challenges and Limitations of SLS 3D Printing in the Defense Sector
While SLS 3D printing offers numerous advantages, it’s essential to address the challenges and limitations that come with integrating this technology into the defense sector.
Technical Challenges:
- Material Limitations: The range of materials suitable for SLS 3D printing may not meet the mechanical properties required for specific military applications.
- Durability and Reliability: Ensuring that 3D printed parts meet the durability and reliability standards for military applications is a significant challenge.
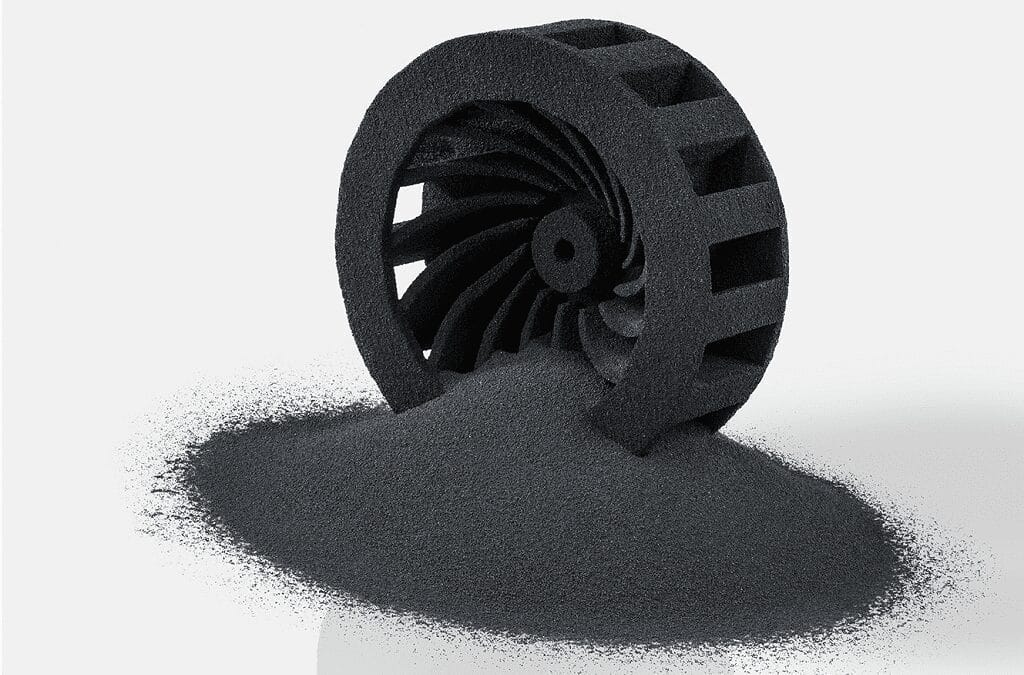
Regulatory and Security Concerns:
- Intellectual Property: Protecting the intellectual property associated with 3D printed parts is critical.
- Compliance and Standards: Compliance with military standards and regulations is essential for the adoption of any new technology in the defense sector.
Case Studies and Real-World Applications
Rapid prototyping is one of the most immediate and impactful applications of SLS 3D printing in the defense sector. It allows military engineers to develop and refine innovative solutions more quickly than ever before.
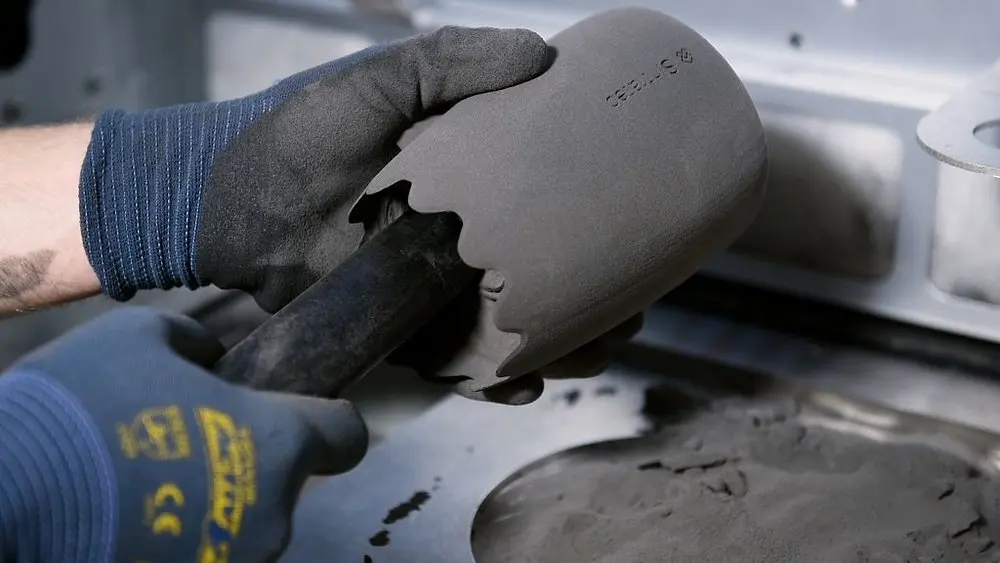
U.S. Army: Lightweight Armor Development:
- Reduced Development Time: The rapid prototyping capabilities of SLS 3D printing significantly shortened the development cycle.
- Improved Performance: Extensive testing and iteration led to a more effective armor design.
- Cost Savings: The ability to quickly test and refine designs reduced overall development costs.
The real-life applications and various case studies of SLS 3D printing in the defense sector provide tangible proof of its transformative power. It enables rapid prototyping and custom part production, field-based manufacturing, and logistics support—things that truly improve military readiness and capability.
While the technology is constantly evolving and maturing, there is little doubt that SLS 3D printing will find further innovative applications within the defense sector. The successes highlighted here let this technology revolutionize manufacturing and operations to set the path for a much leaner, more efficient, and responsive defense force.
As the technology continues to evolve, it’s important to address the challenges and limitations to fully realize the potential of SLS 3D printing in the defense sector. By resolving technical issues, navigating regulatory and security concerns, and continuing research and development, the true potential of SLS 3D printing can be harnessed.
Enhancing Technical Capabilities
To overcome material limitations, ongoing research is focused on expanding the range of materials suitable for SLS 3D printing. This includes developing new polymers and metals with the necessary mechanical properties for military applications. Additionally, improving the durability and reliability of printed parts is a priority, with ongoing testing and validation to ensure they meet the stringent requirements of military use.
Addressing Regulatory and Security Concerns
Protecting intellectual property is a critical concern in the defense sector. This involves securing digital designs from unauthorized access and navigating the legal landscape of patents related to 3D printing technologies. To mitigate the risk of IP theft and counterfeiting, robust cybersecurity measures and supply chain management practices are essential.
Compliance with military standards and regulations is also a significant challenge. This requires extensive certification processes to validate the suitability of 3D printed components for military use. Keeping up with evolving regulations and ensuring international compliance for defense projects across different countries is a continuous process.
Future Outlook
The future of SLS 3D printing in the defense sector is promising. As the technology matures, it is expected to find even more innovative applications, from improving the design and prototyping process to enhancing material efficiency and reducing production costs.
Conclusion
SLS 3D printing is not just updating military technology; it is redefining the possibilities of what can be created in defense manufacturing. By addressing the challenges and leveraging the advantages, this technology has the potential to revolutionize the way military forces design, manufacture, and deploy their equipment, leading to a more efficient and responsive defense sector.
As we look to the future, the integration of SLS 3D printing into the defense industry will continue to shape the landscape of military technology, offering new opportunities for innovation and strategic advantage.