Imagine a world in which very complex customized parts can be manufactured with unparalleled precision and speed; truly a marvel, indeed, from aerospace to health sciences. This, however, is merely an introduction to the realm of Selective Laser Sintering (SLS) 3D printing that is already changing manufacturing methods, enabling innovation and great transformation.
The blog post will summarize the basic understanding of SLS 3D printing, various components that make it work, the pros and cons, and the very necessary applications in different industries to benefit mankind by presenting interesting cases of these using SLS. The last part of this blog will dissect the trends that might shape the technologies of the future. In conclusion, SLS 3D printing shows promise – it is a game changer that could disrupt and revolutionize the world markets.
Understanding SLS 3D Printing
SLS 3D printing is not just a manufacturing technology; it represents a breakthrough process altering industries worldwide. But, what is SLS 3D printing, and how is it accomplished? Let’s take on a journey into this marvelous technology’s world.
What Is SLS 3D Printing?
SLS 3D printing is an additive manufacturing process that uses a very high-powered laser to join small particles of plastic, metal, ceramic, or glass powders together. SLS builds parts in a layer-by-layer manner: starting from nothing and building up, giving it a very precise and complicated nature as compared to traditional manufacturing processes that work subtractively, tearing away from a large block of material.
Basic Work Sequence of SLS 3D Printing
The SLS 3D printing process can be described in the following simplified stepwise manner:
Design and Preparation: It starts with a 3D digital model designed by the Computer-Aided Design (CAD) software. The model is then sliced into thin layers, each representing cross-sections of the object.
Powder Distribution: A fine layer of the powdered material is spread over the platform.
Laser Sintering: A high-powered laser selectively fuses powder particles together according to the cross-sectional settings from the 3D model.
Layer Building: The build platform drops a half millimeter, and the next layer of powder material is distributed and sintered.
Repeat and Complete: The entire process continues until the object has built up fully, layer by layer.
Cooling and Removal: After completion, the part cools inside the powder bed and gets removed, and the remaining powder gets recycled for subsequent use.
Key Components of SLS 3D Printing
Materials Used
SLS 3D printing employs a variety of materials, each possessing unique characteristics that make them suitable for different applications.
Polymers: The most commonly used materials are nylon (PA12), polypropylene (PP), and thermoplastic polyurethane (TPU). These materials are diverse and can be used in an array of contexts.
Metals: Metals such as stainless steel, titanium, and aluminum are used in strong, durable structures.
Ceramics and Glass: These materials are generally used in specialized applications involving heat resistance and chemical inertness.
Equipment and Technology
The high-tech equipment and technology form the working backbone of SLS 3D printing.
- 3D Printers: Specialized SLS printers having powerful lasers and highly efficient control systems.
- Software: CAD software for designing 3D models and slicing software for preparing the models for printing.
- Post-Processing Tools: Tools for cleaning, finishing, and polishing the printed objects.
Benefits of SLS 3D Printing
Several benefits make SLS 3D printing the go-to technique for various industries:
Precision and Accuracy
High Resolution: SLS 3D printing can yield very fine details, rendering it appropriate for complex geometries and elaborate designs.
Consistent Quality: Owing to layer-wise construction, SLS printing guarantees a consistent quality during the length of the whole part.
Speed and Efficiency
Rapid Prototyping: They can be produced rapidly, allowing for shortening of design and testing stages.
Quick Turnaround: Enhanced production rates mean fast turnaround times for finished goods.
Cost-effective
Material Efficiency: The unconsumed powder may be recycled, reducing wastage and material costs.
Decreased tooling costs: Low tooling or molding means more cost-effective small-batch production.
Challenges and Limitations
While SLS 3D printing has a plethora of advantages, a numerable set of challenges remain in its advancement.
Material Constraints
Limited Material Applications: Not all materials are appropriate for use in SLS; furthermore, some require specialized equipment.
Material Properties: The properties of sintered materials differ from conventional manufactured materials.
Post-Processing
Finishing: The finished printed objects may require additional steps for finishing such as polishing or coating.
Support Structures: In some cases, difficult-to-print geometries may lead to the inclusion of support structures whose removal afterward is challenging.
Comparison of SLS 3D Printing with Other Manufacturing Methods
Feature | SLS 3D Printing | Traditional Manufacturing |
Material Usage | Efficient, recyclable | often wasteful |
Precision | High | Variable |
Speed | Fast | Slower |
Cost | Lower for small batches | Higher for small batches |
Complexity | Can handle complex designs | Limited by tooling |
Post-Processing | Often required | Often required |
SLS 3D printing stands out as a versatile and efficient manufacturing method, offering unique advantages that make it a game-changer in various industries. As we continue to explore its applications and future developments, the potential for innovation and transformation becomes even more apparent. Stay tuned for the next section, where we’ll delve into the innovative applications of SLS 3D printing across different industries.
Innovative Applications of SLS 3D Printing
Selective Laser Sintering (SLS) 3D printing is more than just a manufacturing method; it has become the world’s most disruptive innovation, a change in any industry or profession an industry’s working framework in general. From aerospace to healthcare, SLS 3D printing is transforming how we design, manufacture, and use products. SLS 3D printing and its world-altering application in various sectors will be discussed.
Aerospace Industry
It is an industry that requires precise, durable, and lightweight components, all of which SLS 3D printing can provide.
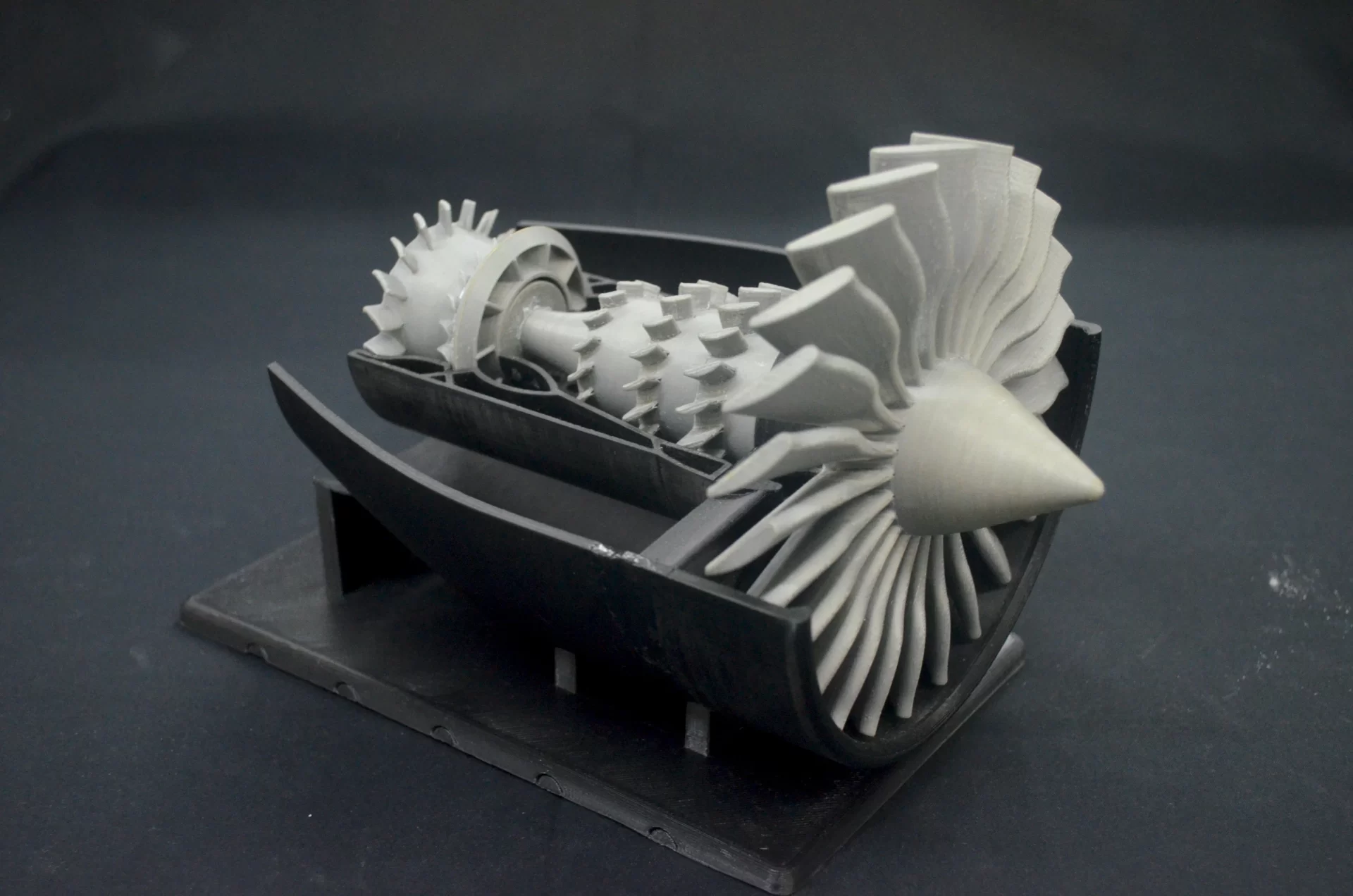
Lightweight and Durable Parts
Weight Reduction: SLS enables the production of complex, lightweight structures to shed overall aircraft weight for increased fuel efficiency.
Strength and Durability: Parts made from high-strength materials such as titanium or advanced polymers are rugged and dependable.
Customized Components
Tailored Designs: SLS enables the production of requested designs meeting specific performance criteria, such as optimized aerodynamics or improved structural integrity.
Rapid Prototyping: Quickly produce and test prototypes for speedy development of newer aircraft and spacecraft.
Automotive Industry
SLS 3D printing has taken the automotive sector by storm, allowing for the quick and efficient manufacture of complex, high-performance parts and components.
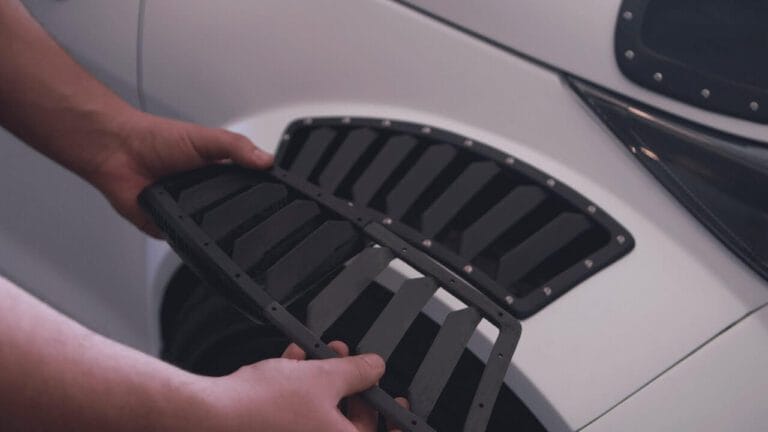
Complex Geometry and Designs
Intricate Parts: SLS allows parts to be manufactured with complex geometries that would be very difficult and potentially impossible to make using any other manufacturing processes.
Design Freedom: Engineers can try new designs without the restraints of traditional tooling.
Reduced Lead Times
Faster Production: SLS enables rapid production of parts, which reduces lead times and accelerates development.
Just-in-Time Manufacturing: Parts can be produced on demand, thereby minimizing inventory and waste.
Enhanced Performance Parts
Lightweight Parts: Create lightweight parts that enhance fuel efficiency and performance.
High-Strength Materials: Advanced materials are available for manufacturing durable, high-performance components.
Innovative Applications of SLS 3D Printing Across Industries
Industry | Application | Benefits |
Aerospace | Lightweight parts, custom components | Weight reduction, improved performance |
Automotive | Complex geometries, enhanced performance parts | Faster production, improved efficiency |
SLS 3D printing is a versatile and powerful technology that will transform industries the world over. From aerospace to electronics, these revolutionary applications for SLS 3D printing drive progress, boost performance, and create new fronts in creativity and sustainability. As we ruminate about the future of this technology, the prospects for turning another corner for innovation and transformation are more evocatively asserted. Hang on for the next section, where we will dissect case studies and success stories in real life that underline the benefits of SLS 3D printing.
Selective Laser Sintering (SLS) 3D Printing Case Studies and Success Stories
Selective Laser Sintering (SLS) 3D printing is not merely a theoretical concept but has established an impactful presence across various industries. This will further investigate some real-world case studies and success stories that showcase the enabling capabilities of SLS 3D Printing.
Real-World Applications of SLS 3D Printing
Aerospace Case History: Lightweight with Durable Components
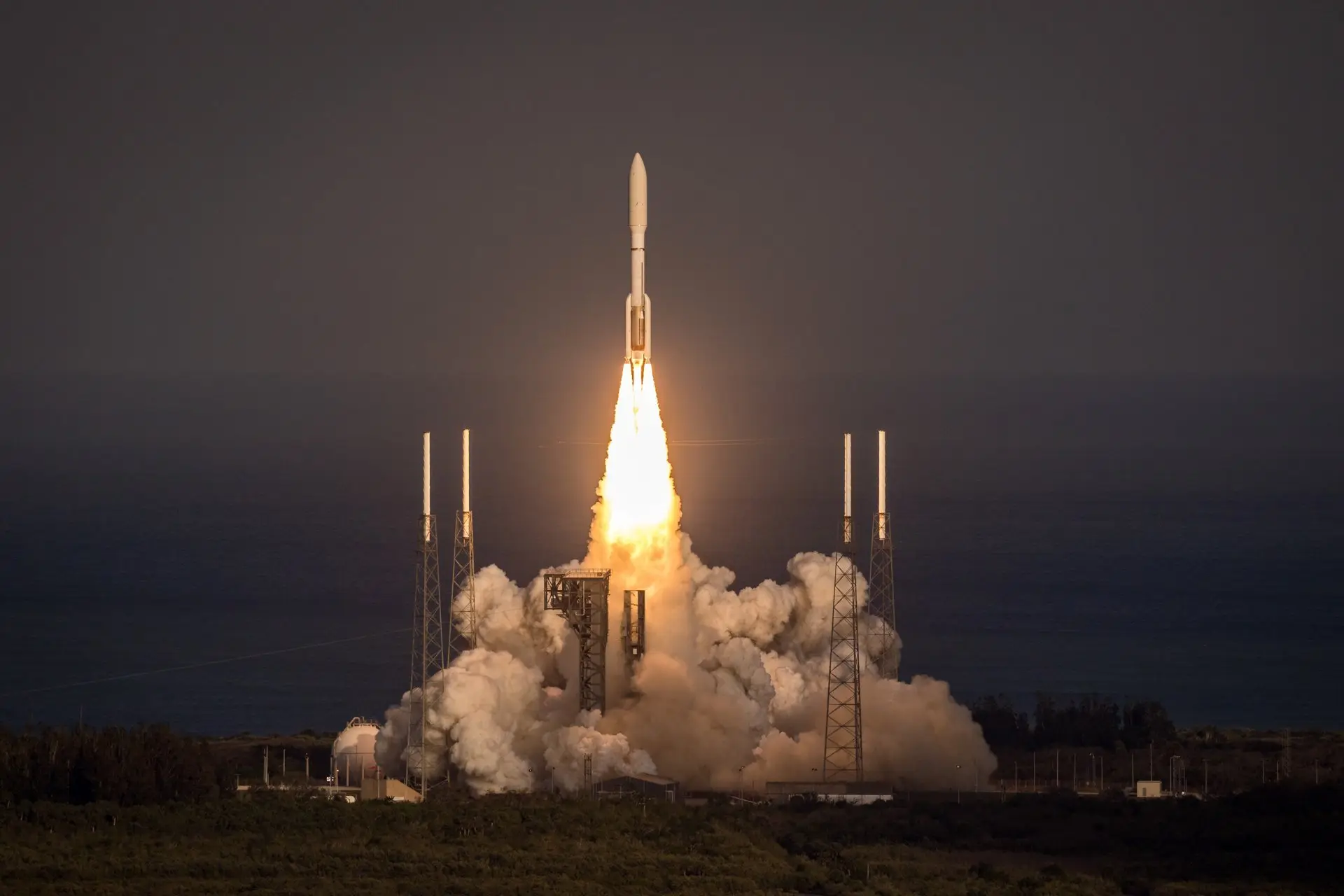
Unit: A leading company in the aerospace industry
Requirement: A need for lighter and durable components that would increase fuel efficiency and performance.
Provision: Utilizing SLS 3D printing technology to produce complex lightweight parts from high-strength materials such as titanium.
Results:
Mass Reduction: REF 30% mass reduction within parts for increased fuel efficiency.
Performance: Better structural integrity and performance of aircraft components.
Cost Savings: Reduced material waste, reduced production costs by efficient manufacturing techniques.
Impact: The company was able to satisfy critical regulations established in the industry and create an advantage for itself in providing better-performing aircraft with an edge on competition.
Automotive Case History: Prototyping Speed Customization
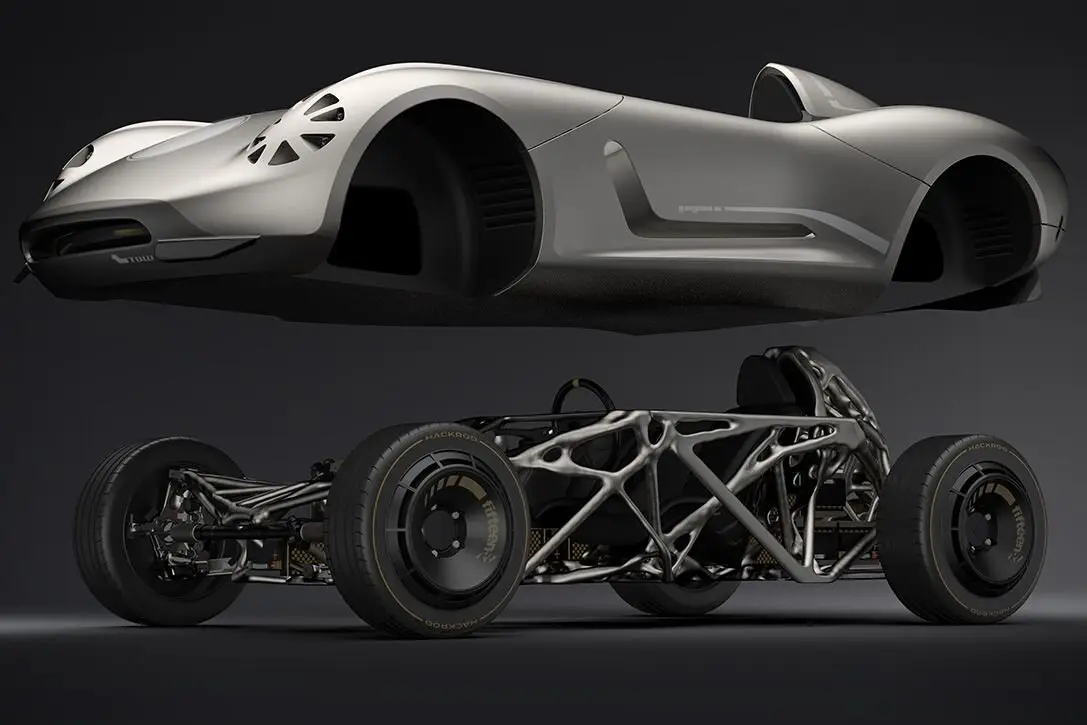
Unit: A high-profile automotive brand
Requirement: Short timelines for prototyping and customization of high-efficiency car parts.
Provision: Use of SLS 3D printing technology to easily produce complex geometries and tailor-made components.
Results:
Speed: 50% less lead time reduced the development time.
Customization: Custom parts for improved efficiency of luxury cars with aesthetics.
Quality: High precision and consistency in parts ensuring performance capabilities.
Impact: Launched designs in the market faster securing branding requirements giving customer satisfaction on personalized high-performance vehicles.
Future Trends and Developments in SLS 3D Printing
While Selective Laser Sintering (SLS) 3D printing has already made tremendous strides across many industries, more will undoubtedly follow. As the technology progresses and research continues, new trends and developments are lining up to turn a corner for ways of manufacturing and innovation. Let us enter this exciting future of SLS 3D printing.
Emerging Technologies and Materials
Advanced Polymers and Composites
New Polymers and Composites: Advanced research is going on to develop new polymers and composite polymers that can offer enhanced strength, durability, and functionalities.
Hybrid Materials: Combining several materials for developing hybrid composites that offer a compromise between various material properties, such as strength and flexibility.
Hybrid Manufacturing Techniques
Combined Processes: There is research to combine SLS 3D printing with other manufacturing processes such as CNC machining or injection molding to build complex parts with better intrinsic properties.
Multi-material Printing: The technologies are being developed to enable the same part to be created with different materials for more design freedom and functionalities.
Integration with AI and Machine Learning
Smarter Manufacturing: Incorporation of artificial intelligence and machine learning algorithms to optimize the printing process, increase control over quality, and yield a better efficiency.
Predictive Maintenance: AI systems for predictive maintenance when applied can predict the failure of equipment so that reliable and steady production can be assured.
Research and Development
Continued Research
Material Science: Early research is geared toward improved visibility into new materials and their properties, thereby advancing the different applications possible for SLS 3D printing.
Process Optimization: Studies on improving speed, accuracy, and efficiency of the SLS printing process.
Collaborations and Partnerships
Industry Collaboration: Joint efforts among industry, academy, and governmental agencies to create innovation and advance technology.
Joint Ventures: Collaborative ventures with various companies to combine their resources, information, and abilities stimulate mutual development.
Funding, Grants, and Possibilities: The government becomes actively involved since it has begun funding research and development in SLS printing. In addition, some governments also provide grant money to encourage and help research-oriented programs.
Future SLS 3D printing looks bright. The new technologies, new materials, and new collaboration paves the way for such vast innovation and transformation in the field. The change SLS 3D printing can bring, which would highly benefit through continuous research and expansion of the market, is glaring as a mascot. Stay tuned for the finale, where we would revisit the key points followed by SLS 3D printing’s potential to change the game altogether.