Discuss different resin types
SLA 3D Printer Resin Types
Understanding Resin 3D Printing: A Modern Manufacturing Marvel
Resin 3D printing is a cutting-edge technology within the realm of additive manufacturing. Unlike traditional methods that carve out material to form an object, resin 3D printing constructs items layer by layer. This meticulous process transforms liquid resin into solid, intricate structures, offering precision and detail hard to match with older techniques.
Key Differences from Subtractive Construction
- Process Overview: While subtractive methods like milling or carving remove excess material to reveal the desired shape, resin 3D printing adds material in successive layers. This results in less waste and greater efficiency.
- Material Use: Traditional subtractive processes often involve solid blocks of material, which are whittled down. In contrast, resin 3D printing utilizes a liquid base, hardening it through a curing process such as UV light exposure.
- Precision and Complexity: Resin 3D printing shines in its ability to produce complex geometries with fine details, a challenge for many subtractive techniques that can falter on intricate designs.
- Waste Reduction: By building up rather than cutting away, resin 3D printing significantly minimizes material wastage, making it a more sustainable choice for prototyping and production.
Resin 3D printing represents a shift in how objects are made, leveraging technology for more detailed, efficient, and sustainable manufacturing solutions.
Advantages of Stereolithography (SLA) Printers Over Other 3D Printers
Stereolithography, commonly known as SLA printing, offers several key advantages when compared to other types of 3D printing technology. Here’s a closer look at why SLA printers stand out:
- Material Versatility
SLA printers utilize liquid resins, which provide a unique flexibility for creating diverse projects. From transparent sculptures to rubber-like molds, the range of available resins ensures that there’s a suitable option for virtually any creative undertaking. - Precision and Detail
One of the standout features of SLA printing is its ability to produce highly detailed and intricate objects. The process involves directing a UV laser on specific points within the resin, solidifying only the targeted areas. This precision allows for extremely fine resolutions that are difficult to achieve with other 3D printing technologies. - Smooth Surface Finish
The nature of the liquid resin and the curing process contributes to an exceptionally smooth surface finish. This minimizes the need for post-processing, making SLA printers ideal for applications where aesthetics are paramount. - Complex Geometries
SLA technology supports the creation of complex geometries that might be challenging for other 3D printers. This is particularly beneficial for artists and designers who wish to explore intricate designs that push the boundaries of typical 3D printing capabilities. - Range of Applications
The versatility and precision of SLA printers make them suitable for a wide range of applications, from creating dental and medical models to producing exquisite art pieces and functional prototypes.
In summary, SLA printers stand out for their precision, material flexibility, and capability to produce detailed and smooth-finished objects, making them a preferred choice for many who require high-quality 3D prints.
What are Resins, and How are They Used in 3D Printing?
Resins are versatile and sticky substances that can be found in both solid and liquid states at room temperature. They may originate from natural sources, such as tree sap, or be synthetically created from various chemicals. Typically, resins are polymers, which means they consist of long, repeating chains of molecules—a structure that contributes to their adhesive nature.
Natural vs. Synthetic Resins
- Natural Resins: These include substances like amber, derived from the fossilized form of tree resin.
- Synthetic Resins: These are engineered to achieve specific properties and are often associated with industries such as plastic manufacturing.
Resins in 3D Printing
In the realm of 3D printing, resins play a crucial role thanks to their unique properties. Here, synthetic photopolymers are common. These types of resins are initially viscous liquids at room temperature. Their magic occurs when they’re exposed to light, usually ultraviolet (UV). This light exposure initiates a curing process, transforming the liquid resin into a solid form.
Key Features of 3D Printing Resins:
- Viscosity and Fluidity: Initially, they have a thick, fluid consistency allowing them to be precisely manipulated in the printing process.
- Curing Process: When subjected to specific light wavelengths, they undergo a chemical reaction that makes them harden into solid structures.
- Precision and Detail: Ideal for creating detailed and fine features in 3D printed models due to their ability to solidify in thin layers.
Resins have revolutionized the 3D printing landscape by providing materials that can create fine, detailed, and durable objects, making them indispensable in industries ranging from prototyping to custom manufacturing.
How Do SLA Printers Use UV Lasers to Cure Liquid Resins?
SLA printers, also known as stereolithography machines, utilize a unique process to transform liquid resin into solid objects. This method relies on the precision of a UV laser. Here’s how it works:
- Start with a Digital Blueprint: The process begins with a digital 3D model. This serves as the blueprint, instructing the printer on where to direct the laser.
- Selective Targeting: Using this blueprint, the SLA printer emits a UV laser that is meticulously focused on specific areas of the liquid resin.
- Curing with Precision: The UV laser emits light that only solidifies the resin it touches, thanks to its precise targeting. This phase-by-phase hardening is what gradually builds up the layers of the final object.
- Layer-by-Layer Construction: As each thin layer of resin solidifies, the printer lowers the build platform slightly, allowing for the next layer to be cured. This repetitive process continues until the entire object is fully formed.
By manipulating the UV laser with precision and following a meticulous pattern, SLA printers are able to create intricate and highly detailed 3D objects.
What Kinds of 3D Printers Fabricate Objects Using Resins, and How Do Their Processes Differ?
When it comes to 3D printing with resins, two primary technologies lead the charge: Digital Light Processing (DLP) and Stereolithography (SLA) printers. Both utilize liquid resins but differ in how they cure these materials into solid forms.
DLP Printers
DLP printers excel in speed, curing entire layers of an object simultaneously using a digital light projector. This technique allows for efficient production, making them ideal for projects requiring quicker turnaround times without compromising detail.
SLA Printers
On the other hand, SLA printers shine in precision and complexity. They use a laser to cure the resin with meticulous accuracy, solidifying portions of the object sequentially. This process can accommodate intricate designs with fine detail. Depending on the model, SLA printers may cure the resin from the top moving downward or from the bottom upward, allowing for more flexibility in design and build volume. Advanced industrial SLA printers can handle large projects, offering build volumes up to or exceeding 1 cubic meter.
Comparison with FDM Printers
It’s crucial to distinguish these resin-based technologies from Fused Deposition Modeling (FDM) printers, which use thermoplastic filaments. While FDM devices are excellent for rapid prototyping and creating basic forms, their reliance on extruded filament limits their capacity for detailed artistry.
Conclusion
Thus, while DLP and SLA printers both fabricate using resins, the choice between them depends on the requirements of speed and detail resolution. For those seeking precision and the capability to produce detailed miniatures or large objects, SLA printers are the preferred option. Conversely, DLP printers are optimal for projects where speed is a priority.
How Do SLA Printers Differ from FDM Printers in Terms of Fabrication and Detail?
SLA (Stereolithography) and FDM (Fused Deposition Modeling) printers utilize distinct methods for fabricating 3D objects, which result in notable differences in precision and detail.
Fabrication Process Differences
- SLA Printers:
- Use a laser to cure liquid resin, solidifying it layer by layer.
- Each section is precisely targeted and solidified before being connected.
- Can operate by either building from the top-down or bottom-up within a resin reservoir.
- FDM Printers:
- Work by extruding melted thermoplastic filament to construct an object layer by layer.
- The filament is deposited in strands, building up parts gradually.
- Ideal for quickly assembling rough prototypes.
Level of Detail
- SLA Printers:
- Known for their exceptional precision, capable of producing complex, highly detailed pieces.
- The laser curing process ensures that even intricate designs are accurately realized without losing any detail.
- Suitable for both small-scale miniatures and large objects in industrial applications.
- FDM Printers:
- Tend to have limitations with finer details due to the nature of the filament material.
- Best used where speed and simplicity are prioritized over intricate detail.
- While effective for basic prototypes, they lack the finesse of SLA’s detailed resolutions.
In summary, SLA printers excel in delivering fine details due to their laser precision, making them ideal for projects where accuracy is critical. In contrast, FDM printers are advantageous for speed and simplicity, albeit at the cost of intricate detail.
What Types of Resins Do Fabrication Companies Use for Professional-Grade 3D Objects?
When it comes to crafting professional-grade 3D objects, fabrication companies have a variety of resin options to choose from. Each type of resin serves different needs based on durability, flexibility, and the specific application of the 3D-printed object. Here’s a breakdown:
Standard SLA Resin
Ideal for projects where appearance is key, standard SLA resins are cost-effective and deliver smooth, highly detailed results. However, they can be brittle post-curing, making them best for prototypes or models that won’t require extensive handling.
ABS-Like SLA Resins
These resins provide a tough alternative to standard options, mimicking many qualities of ABS plastic used in FDM 3D printing. They produce detailed prints with enhanced stiffness and impact resistance, making them suitable for industrial applications.
Tough SLA Resins
For applications demanding resilience, tough SLA resins are the go-to. These resins are engineered to endure repeated stress and are often used for functional prototypes or parts exposed to intense conditions. Some variants are designed to tolerate high temperatures, making them invaluable in demanding industrial environments.
Draft or Rapid Resins
Speed is the differentiator here. Draft resins allow for rapid prototyping with a focus on quick print times and minimal finishing, greatly accelerating the production process for large components.
Medical SLA Resins
Designed for biocompatibility, medical resins are safe for use in close contact with human and animal tissue. These resins can withstand sterilization processes, making them suitable for crafting medical and dental equipment.
Flexible SLA Resins
These resins remain pliable after curing, offering a material that bends but doesn’t fully harden. They are best for applications needing flexibility, though they can become more rigid with continued UV exposure.
Elastic or Rebound Resins
These resins allow for parts that remain stretchable post-curing. They are perfect for items that need to spring back or provide a cushioned feel, adding versatility to the range of 3D-printed creations.
Transparent or Clear SLA Resins
Transparent resins offer glass-like finishes, available either clear or tinted. They require meticulous finishing to achieve the desired transparency or translucence, making them perfect for objects where visual clarity or aesthetics are paramount.
By understanding these resin types, fabrication companies can select the ideal material to create 3D objects that meet their specific professional-grade requirements. Each resin type offers unique attributes that cater to different aspects of the manufacturing process, whether it be speed, durability, flexibility, or clarity.
Choosing the Best Resin for Your 3D Printing Project
Selecting the right resin for your 3D printing project can significantly impact the quality and functionality of the final product. To make an informed decision, consider the following factors:
Printer Compatibility
Start by verifying which resins are compatible with your 3D printer model. Compatibility is crucial to ensure smooth printing and prevent damage to your equipment.
Project Purpose
Evaluate the intended use of the 3D-printed items. Ask yourself about the specific roles these objects will play and the duration they need to perform. Knowing their purpose will help you determine the appropriate strength, flexibility, and durability of the resin.
Size and Dimensions
Consider the size of the items you plan to create. Identify the minimum and maximum dimensions, as these will influence the type of resin you should use. Larger objects may require more robust resins to ensure stability.
Detail and Complexity
Think about the level of detail your project requires. Will you produce simple solid shapes or intricate designs? Some resins are better suited for capturing fine details and complex structures than others.
Desired Finish
Decide on the finish you need for your pieces. Do you prefer a smooth finish, or will you be applying additional materials? Your choice of resin should match the end finish you envision.
Appearance Preferences
Define the appearance you want for your objects. Options can range from opaque to translucent, solid to hollow. Your creative vision should guide you in selecting a resin that meets these aesthetic criteria.
Durability Needs
Reflect on the durability requirements of your items. If they must withstand industrial-grade conditions or high-traffic use, choose a resin known for its strength and stability.
Accuracy and Shrinkage
Assess how precisely your final object should match its design file. Some resins are more prone to shrinkage during curing, which can affect dimensional accuracy. Choose one that aligns with your precision needs.
Production Speed and Volume
Determine your production timeline and the volume of objects you need. Some resins cure faster, facilitating quicker production times. Ensure your chosen resin supports your schedule and quantity demands.
Budget Considerations
Finally, balance your project’s budget with the cost of materials. Allocate an appropriate portion of your budget to the resin without compromising the quality required for your project.
By weighing these factors, you can choose a resin that not only fits your project needs but also enhances the overall success of your 3D printing endeavors.
How Do Artists and Makers Choose the Best Resin for Their 3D Printing Projects?
Selecting the ideal resin for 3D printing requires careful consideration of several key factors. Not all resins are created equal, and the success of a project often hinges on choosing a resin that aligns with specific project requirements. Here’s a step-by-step guide to help artists and makers make the best choice:
1. Understand Your 3D Printer’s Compatibility
Begin by determining which resins are compatible with your 3D printer. Each printer has specific requirements, so it’s vital to ensure you pick a resin that will work seamlessly with your equipment.
2. Define the Purpose of Your Project
Identify the function of your 3D-printed items. Are they decorative pieces, functional prototypes, or durable parts for industrial use? This will significantly impact your resin choice since different resins offer varying levels of strength and durability.
3. Consider Size and Dimensions
Evaluate the size requirements of your project. Whether you’re creating a large-scale model or a small intricate piece, knowing the minimum and maximum dimensions will help narrow down your options.
4. Detail and Complexity Matter
Assess the level of detail required in your design. For intricate, complex designs, you might need a resin that captures fine details and supports high-resolution printing.
5. Desired Finish and Appearance
Think about the finish you want your final piece to exhibit. Decide if you need a specific color, whether the piece should be opaque, transparent, or translucent, and consider if any additional finishing processes will be applied.
6. Durability Requirements
For objects intended for high-stress environments, select a resin that offers enhanced strength and stability. Knowing the longevity and resilience needed can steer you toward resins that provide industrial-grade robustness.
7. Accuracy and Precision Needs
Evaluate how precise your finished object needs to be relative to your design file. Some resins are prone to shrinking during curing, which could affect the accuracy of your print.
8. Production Speed and Volume Needs
Reflect on how quickly you need to complete your project and the number of items you intend to produce. Certain resins cure faster than others, impacting your production timeline.
9. Budget Constraints
Determine your overall project budget. Calculate what portion can be devoted to resin, ensuring you select a suitable option that doesn’t compromise on quality but fits within financial limits.
By addressing these considerations, artists and makers can confidently select the resin that best suits their 3D printing projects. Each factor plays a crucial role in the success of the final output, ensuring the chosen resin meets both practical and creative needs.
Standard Resin
Standard resin is the most common material used for Stereolithography or SLA 3D printing. It provides a rigid plastic material with properties akin to basic injection-molded plastics. Standard resin yields 3D printed parts with good resolution and medium strength for general prototyping and production applications.
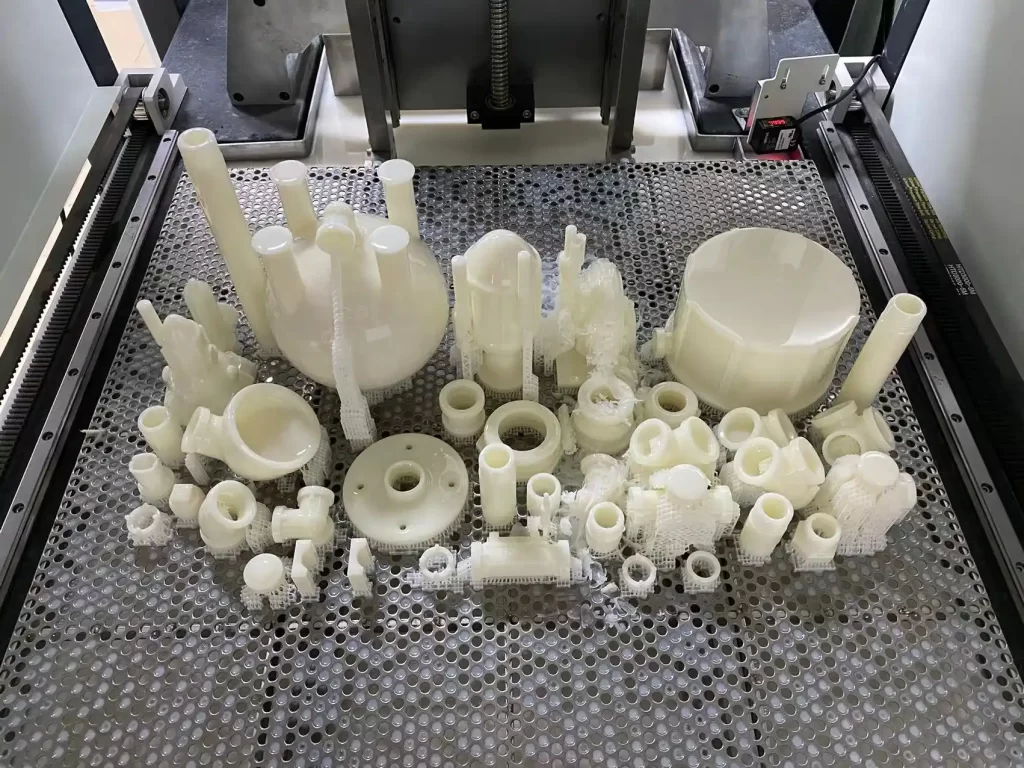
Properties
Standard SLA resin creates 3D printed parts with the following properties:
• Tensile strength: 10-50 MPa
• Hardness (Rockwell R): 30-100
• Heat deflection temperature: 45-70°C
• Density: 1.1-1.3 g/cm3
The most popular base materials for standard SLA resin are acrylate monomers combined with various polymers such as epoxy, urethane or vinyl ester resins. The specific chemistry depends on the requirements for strength, flexibility, durability or other properties. Standard resins provide a good balance of cost and performance for common industrial applications.
Applications
Standard SLA resin is suitable for:
• Conceptual modeling – Quickly produce multiple design iterations.
• Prototyping – Create functional prototypes for testing fit, form and function.
• Short production runs – For small quantities less than 10,000 units per year.
• Jigs, fixtures and manufacturing aids – Provide tooling support structures.
• Presentation models – Develop high quality display models, mockups and sculptures.
• Research & development – Test new product designs and industrial parts.
How Do ABS-like SLA Resins Compare to Standard Resins?
Properties
ABS-like SLA resins stand out due to their enhanced strength and hardness, making them less prone to brittleness compared to standard resins. This makes them an attractive option for applications requiring durability. The term “ABS-like” refers to their ability to mimic the properties of acrylonitrile butadiene styrene (ABS) plastic, known for its toughness and impact resistance. In contrast, standard resins tend to be more brittle, which can limit their use in rigorous applications.
Applications
Thanks to their robust properties, ABS-like SLA resins are favored in professional and industrial settings where the creation of strong, durable objects is crucial. Industries that require precision and detailed surfaces often prefer these resins for applications where clean finishes and structural integrity are essential. On the other hand, standard resins might suffice for prototyping or projects where high impact resistance isn’t a necessity.
In summary, while both ABS-like and standard resins have their own merits, the choice boils down to the specific needs of your project, with ABS-like resins providing a superior option for professional-grade applications.
Popular standard resins for SLA 3D printing include Somos NeXt, PerFORM and ProtoGen from 3D Systems, Accura 25 and RenShape SL 7830 from Huntsman, and Formlabs Standard Resin. These general-purpose SLA materials provide basic material properties for a range of applications where rapid prototyping, product development and short-run production are required.
Tough Resin
Tough resin is an SLA 3D printing material with enhanced durability, impact strength and resistance to fractures. It contains rubber additives and polymers designed for rigid parts that experience higher loads and stresses. Tough resin is more durable than standard resin and well suited for functional prototyping applications.
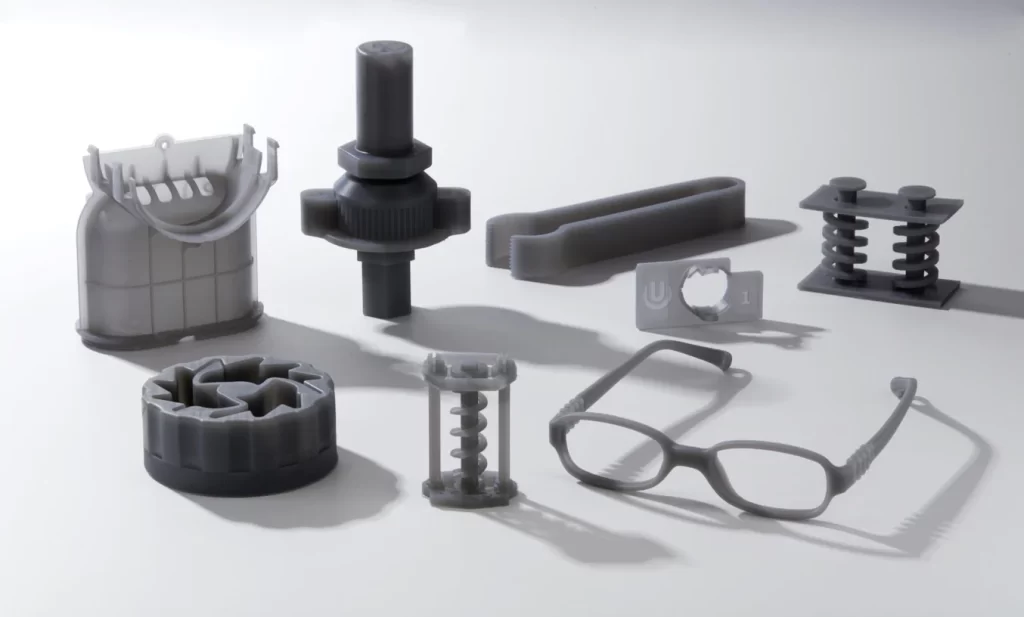
Properties
Typical properties for tough SLA resin include:
• Tensile strength: 20-70 MPa
• Elongation at break: 2-25%
• Izod impact strength: 15-50 J/m
• Hardness (Rockwell R): 50-110
• Density: 1.1-1.4 g/cm3
Tough resins utilize urethane, epoxy and acrylate chemistries along with rubber particles to increase fracture toughness. The rubber additives absorb impact stresses and prevent brittle cracking under repeated loading or drop impacts. Popular base materials include urethane acrylate, epoxy acrylate and vinyl ester resins modified with butadiene rubbers.
Applications
Tough SLA resin is well suited for:
• Functional prototypes – Where higher durability and impact strength are required for testing.
• Jigs and fixtures – For high load applications that experience repeated impacts.
• Short run end-use parts – Consumer products, covers, cases or applications requiring high toughness.
• Automotive components – Headlamp bezels, ducting, under the hood parts where chemical/heat resistance is important.
• Electrical enclosures and connectors – Applications where flame retardancy, high tensile and impact strength are necessary.
Popular tough resins for SLA 3D printing include DuraForm® PA from 3D Systems, Somos® NeXt and DSM’s Novomind 1030 FR which provides a flame retardant, fiber-reinforced nylon alternative. These durable SLA materials yield 3D printed parts with exceptional strength, rigidity and high-temperature resistance for functional prototyping and end-use applications where exceptional toughness and high durability are required.
Flexible Resin
Flexible resin is an elastomeric SLA 3D printing material used to produce rubber-like parts with high flexibility and compressibility. It contains urethane, silicone and other thermoset elastomers to enable highly stretchable 3D printed components that bend and flex without fracturing. Flexible resin provides a 3D printable alternative to molded rubber.
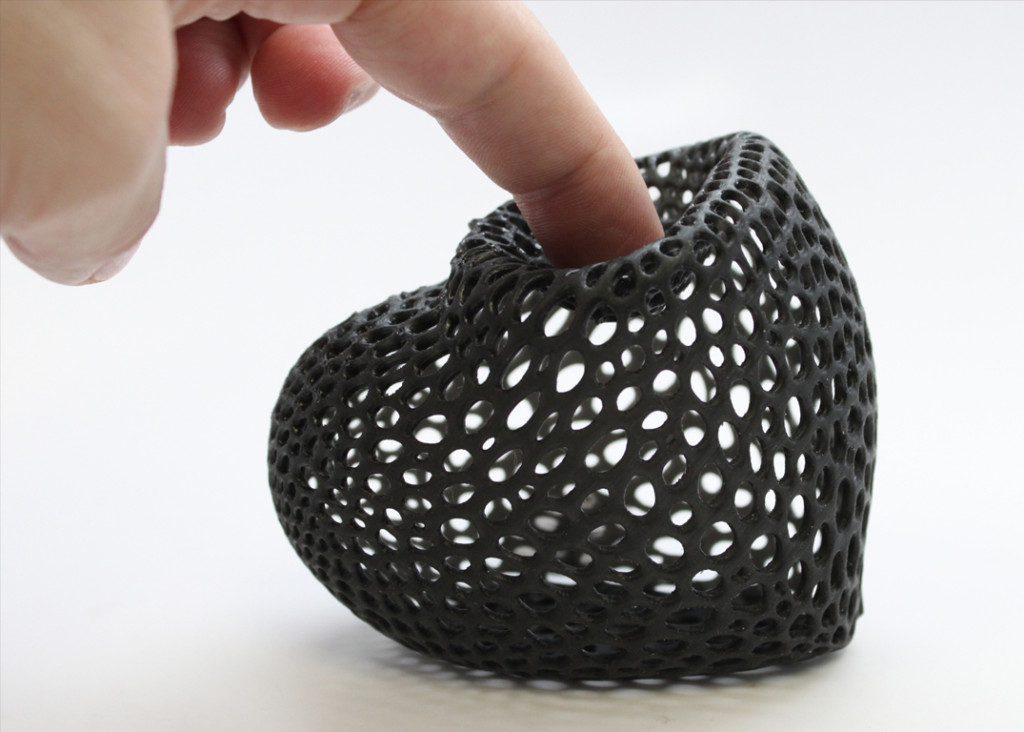
Properties
Typical properties of flexible SLA resin include:
• Tensile strength: 3-10 MPa
• Elongation at break: 100-500%
• Hardness (Shore A): 30
• Tear strength: 10-30 kN/m
• Density: 1.1-1.3 g/cm3
Flexible resins utilize silicone, urethane and other thermoset elastomers to provide high elasticity and resilience. Popular base chemistries include urethane acrylate oligomers and silicone monomers combined with plasticizers and rubbers to achieve a Shore hardness of 30A to 70A. Flexible resins offer stretchability ranging from 3-10 times their original length.
Applications
Flexible resin is suitable for producing:
• Flexible seals, gaskets and o-rings – For applications requiring a tight, compressible seal.
• Soft touch overmolds – Providing padding, grip and shock absorption.
• Living hinges – Enabling bendable, flexing pivot points with high tear strength.
• Elastomeric pads – For vibration dampening, sound proofing and non-slip applications.
• Soft actuators and robotic parts – Where compliant, stretchable materials are necessary.
• Orthopedic parts – Including shoe insoles, orthotics and custom braces.
• sporting goods – Balls, hand grips, and other equipment requiring a soft, pliable material.
Understanding Elastic or Rebound Resins
Elastic or rebound resins are a type of material that, once cured, maintain a flexible and stretchable nature. Think of them as the modern equivalent of classic toys like Stretch Armstrong, which showcase impressive elasticity.
How They Function Post-Curing
- Flexibility and Stretchability: After curing, these resins remain highly elastic, capable of being stretched and deformed without losing their original shape when released.
- Applications: They’re ideal for crafting parts that need flexibility, such as springs, or for creating objects that require a cushioned, soft touch. This can include ergonomic grips or protective padding.
- Durability: Despite their elasticity, these resins are also known for their durability, able to withstand repeated stretching and use without breaking down easily.
By providing both stretch and strength, elastic or rebound resins are essential in applications that demand a balance between flexibility and durability.
Popular flexible resins for SLA 3D printing include DuraForm® Flex, Formlabs Flexible Resin and 3M 3530 which offer a silicone-based SLA printing material. These soft, rubbery 3D printing resins produce highly flexible and elastic parts with Shore hardnesses ranging from A30 to A70 and elongations up to 500% for applications demanding compliant, resilient 3D printed components.
Castable Resin
Castable resin is a specialized SLA 3D printing material used to produce foundry patterns for investment casting metal parts. It contains engineered polymers and fillers that burn out cleanly during casting to leave an accurate mold cavity. Castable resin enables 3D printed molds to be used directly for casting metals such as aluminum, steel and nickel alloys.
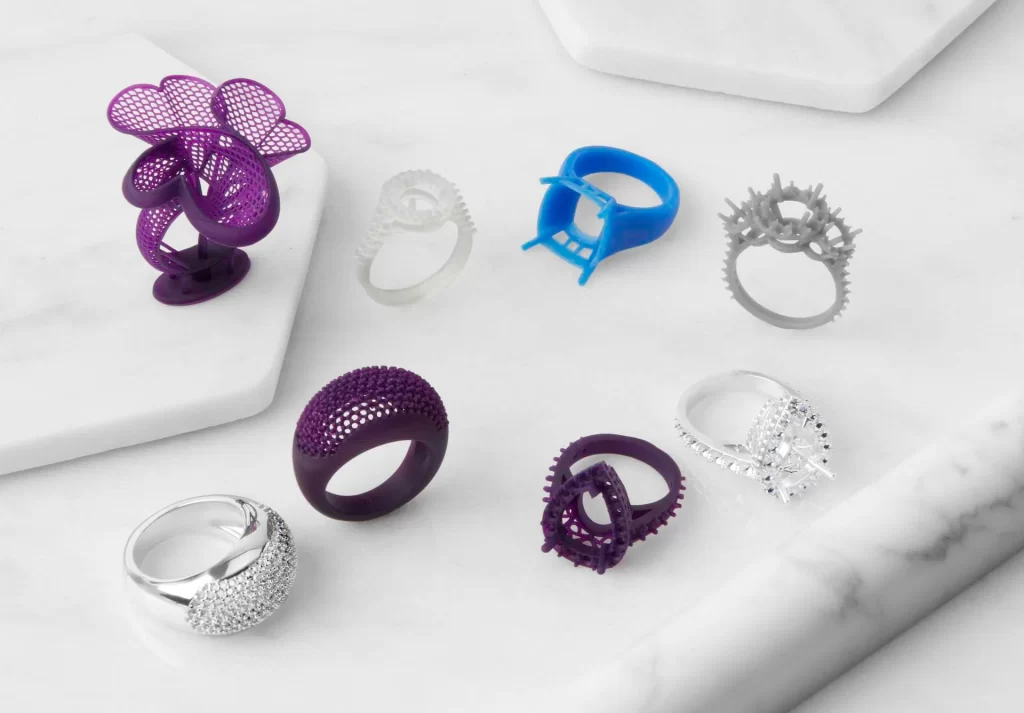
Properties
Properties of castable SLA resin include:
• High thermal stability – Resists melting and deterioration up to 1000°C to withstand metal casting processes.
• Low ash content – Produces little to no residue upon burnout to avoid mold cavity imperfections.
• Medium strength – Strong enough for handling yet easily deconstructed during burnout.
• Non-toxic fumes – Emits little odor or hazardous gases when burned out according to foundry standards.
• Density – Ranges from 1.1 to 1.4 g/cm3, similar to standard SLA resins.
Castable resins typically contain high-temperature polymers such as polyimide, polyetherimide or phenolic along with mineral or ceramic fillers to improve burnout properties. The resin is formulated to carbonize and decompose into gaseous byproducts when exposed to high heat leaving minimal ash behind in the mold cavity.
Applications
Castable resin is specifically designed for 3D printing investment casting patterns including:
• Metal alloy prototypes – Quickly produce aluminum, steel or nickel alloy cast parts.
• Precision cast components – Enable rapid tooling for parts requiring tight tolerances.
• Art castings – 3D print complex, intricate patterns for custom metal sculptures and decorations.
• Low volume production runs – For niche or obsolete parts where tooling is not feasible.
• Directional solidification – Produce patterns for controlling grain structure and optimizing mechanical properties.
Opportunities Unlocked by Resin Printing for Artists and Makers
Resin printing opens a world of possibilities for artists and makers, enabling the creation of detailed and sophisticated designs. This technology allows for the crafting of:
- Intricate Sculptures: Artists can produce highly detailed statues and miniatures, capturing fine details that would be challenging with other methods.
- Custom Jewelry: Makers can design and print unique jewelry pieces, experimenting with forms and finishes that cater to niche markets or personal projects.
- Prototypes and Models: Perfect for engineers and designers, resin printing allows the creation of high-fidelity prototypes and models, aiding in visualization and testing.
- Functional Parts: With advances in resin material, it’s possible to print strong, durable parts suitable for functional applications, expanding the scope beyond art.
- Flexible Molds: Artists can manufacture flexible molds, which can be used in casting metals or other materials, enhancing production capabilities.
In essence, resin printing is revolutionizing how artists and makers approach creation, pushing the boundaries of what’s possible with its detailed and versatile output.
Popular castable resins for SLA 3D printing include Somos® Element, 3D Systems Accura® CastProTM and ProtoCastTM from Huntsman. These high-temperature, low-ash SLA resins produce 3D printed foundry patterns suitable for a range of industrial investment casting applications to produce ferrous and non-ferrous metal end-use components.
Dental Model Resin
Dental model resin is a specialized SLA 3D printing material used for producing biocompatible parts for dental applications and orthodontic treatments. It meets ISO and FDA standards for temporary insertion into the human mouth. Dental model resin can produce highly accurate crown and bridge frameworks, orthodontic thermoforming models, surgical cutting guides and other dental components.
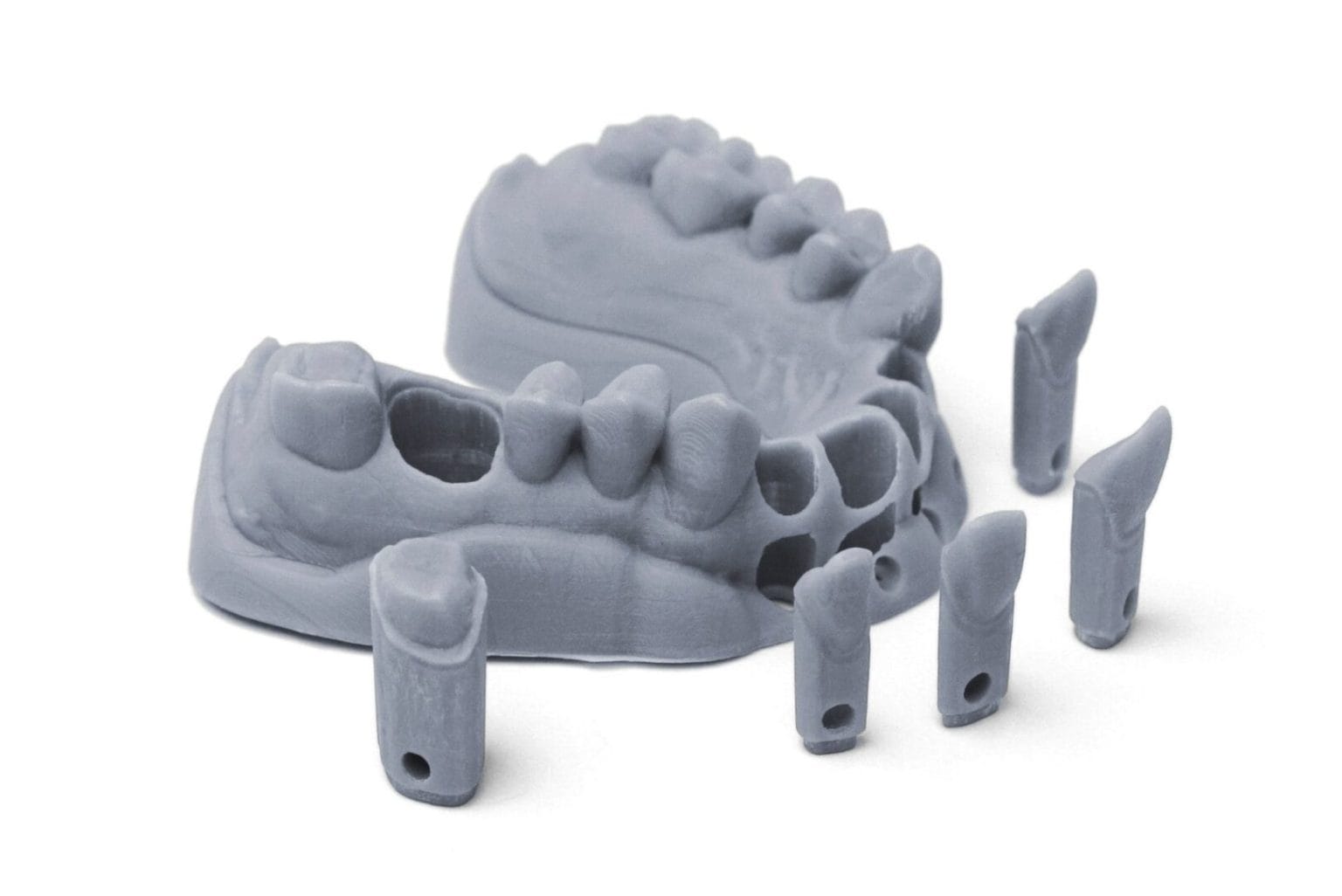
Properties
Dental model resin exhibits the following properties:
• Biocompatibility – Meets ISO 10993 and USP Class VI standards for limited exposure in the mouth.
• High resolution – Provides fine details suitable for miniature dental geometries.
• Strong and durable – Rigid enough for dental purposes yet resists fracturing on removal.
• Non-toxic – Formulated with biocompatible, medical-grade monomers to be inert when exposed to human tissues and fluids.
• Density – Ranges from 1.1 to 1.3 g/cm3, typical of SLA photocuring resins.
Dental resins contain specialized acrylate, epoxy and urethane monomers approved for medical use. They utilize biocompatible polymers and crosslinking agents tailored for dental devices and components requiring placement in the mouth for a temporary period. Dental resins offer a 3D printable and quicker alternative to traditional dental plaster and stone models.
Applications
Dental model resin is designed specifically for SLA 3D printing of:
• Crown and bridge frameworks – Provide support structures for dental prosthetics.
• Orthodontic thermoforming models – Enable clear aligner therapy and retainers.
• Surgical cutting guides – Provide custom templates for precise implant placement.
• Temporary crowns and bridges – Produce short term dental restorations.
• Maxillofacial models – Enable design and testing of customized prosthetics and implants.
• Nightguards and occlusal splints – Allow production of dental appliances for protecting teeth from grinding or trauma.
Popular dental model resins for SLA 3D printing include 3D Systems DuraForm® MDO, Formlabs Dental Model Resin and Asiga CompoCare® which provide biocompatible SLA materials tailored to a range of dental and orthodontic applications. These specialized 3D printing resins yield high resolution, sterilizable parts suitable for temporary insertion in the human mouth during treatment. Dental model resin enables labs and clinics to transition to more efficient and cost-effective 3D printing technologies.
High Temperature Resin
High temperature resin is an SLA 3D printing material capable of producing heat resistant plastic parts. It utilizes high performance polymers with deflection temperatures over 260°C to enable functional components suitable for high temperature and energy applications. High temperature resin provides a 3D printable alternative to injection molded plastics for engineering applications.
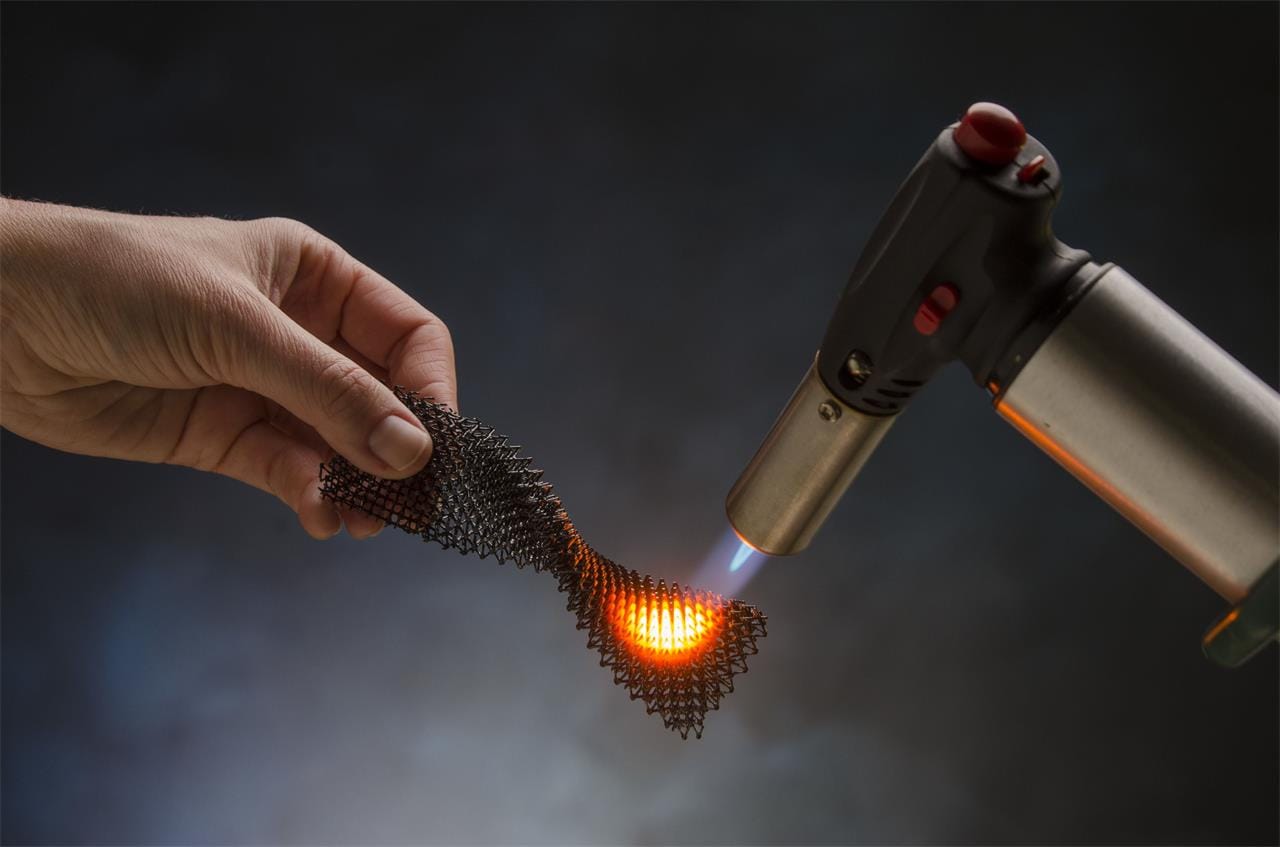
Properties
Typical properties of high temperature SLA resin include:
• Heat deflection temperature – Ranges from 260 to 330°C.
• High tensile strength – 50 to 120 MPa at 23°C.
• Chemical resistance – Resists a wide range of solvents, fuels and corrosive chemicals.
• Low flammability – Meets UL94 V-0 and FAR 25.853 standards for reduced fire risk.
• High hardness – Rockwell M 90-120 scale.
• Density – 1.3 to 1.6 g/cm3 depending on polymer type.
High temperature resins employ specialized polymers such as PEI (polyetherimide), PES (polyethersulfone), PPSU (polyphenylsulfone) and PEKK (polyetherketoneketone). These high performance thermoplastics provide continuous operating temperatures up to 260°C with peaks over 300°C. The resins contain flame retardant and reinforcing additives to increase mechanical strength, rigidity and reduce the risk of fire in high heat applications.
Applications
High temperature resin is suitable for 3D printing:
• Under-the-hood automotive parts – Sensors, connectors, brackets and enclosures.
• Aerospace components – Small to medium interior aircraft, engine and exhaust ducting parts.
• Electrical insulation – High voltage connectors, switches, coil forms and spacers.
• Chemical processing equipment – Valves, pumps, pipes for exposure to harsh chemicals.
• Power generation – Components for generators, turbines, solar heat exchangers and nuclear systems.
• Firewalls and battery boxes – For high heat containment and electrical shielding.
• Industrial tooling – Injection molds, thermoforming tools, kiln furniture where high durability and heat resistance are necessary.
Creating Stunning Visual Effects with Transparent or Clear SLA Resins
Transparent or clear SLA resins are incredibly versatile for producing captivating visual effects. Here’s how they can be skillfully used:
- Glass-like Appearance: Once cured, these resins can closely replicate the look of glass or acrylic, delivering an elegant and sophisticated aesthetic.
- Tinting Options: Available in both clear and tinted varieties, these resins offer flexibility. Additive colorants can be used to achieve the desired hue, enhancing your project with subtle or bold color effects.
- Translucent Finishing: By employing specific finishing techniques, these resins can be treated to mimic frosted glass, which softens light transmission and adds a dreamy, ethereal quality.
- Perfecting the Shine: To achieve a polished, glossy finish, careful sanding and application of a clear coat are essential. This step is crucial for maintaining clarity and maximizing the visual impact.
- Amazing Textures: Through advanced printing techniques, you can create intricate patterns and textures that catch and reflect light in unique ways, further enhancing the visual appeal of your designs.
By utilizing these resins creatively, you can transform any ordinary project into a striking visual masterpiece.
How Working with 3D Printing Experts Simplifies Resin Selection and Streamlines Your Project
Collaborating with 3D printing specialists eases the often daunting task of resin selection. These experts draw on vast experience and industry knowledge to help you choose the optimal resin for your project. This not only ensures that the material meets your specific requirements but also maximizes performance and durability.
In-Depth Material Understanding
3D printing professionals are well-versed in the properties of different resins—from durable options like Formlabs’ Tough Resin to flexible choices such as Somos® ElastoGrey. They provide insights into which material will work best based on your project’s unique needs, whether it involves resistance to heat, flexibility, or aesthetic precision.
Access to Cutting-Edge Technology
By working with a full-service firm, you’re not just getting recommendations; you’re leveraging state-of-the-art technology that ensures precision and quality. Advanced equipment and software facilitate thorough testing of materials, ensuring that the resin selected performs impeccably in real-world applications.
Project Management Expertise
Beyond resin selection, these specialists offer comprehensive project management support. Their expertise covers every stage—from design consultation to the final print—ensuring timelines are met and quality is maintained throughout. This streamlined approach reduces errors and costly delays.
Cost Efficiency
An expert team can also identify cost-saving opportunities by choosing the right material and optimizing designs for efficient production. They help you avoid common pitfalls that can lead to excess material usage or unnecessary expenses.
Summary
Ultimately, partnering with experienced 3D printing experts transforms a complex process into a seamless experience. They guide you effortlessly from material selection to project completion, delivering superior results with minimal hassle.
How Draft or Rapid Resins Prioritize Speed in 3D Printing Projects
Draft or rapid resins are specially formulated to enhance the speed of 3D printing, focusing on efficiency rather than the highest durability. These resins are ideal for creators aiming to produce fast prototypes with minimal finishing work.
Key Advantages:
- Accelerated Printing: By using draft resins, large components can be created significantly quicker than with traditional 3D printing methods. In fact, when employing an SLA printer, the process can be up to ten times faster compared to using an FDM printer.
- Streamlined Post-Production: Draft resins require less time for curing and post-production tasks, allowing designers and artists to iterate rapidly without being bogged down by lengthy finishing processes.
This speed-enhancing characteristic makes draft or rapid resins perfect for industries that prioritize quick prototyping and efficiency in the design phase, providing a competitive edge in project timelines.
Popular high-temperature resins for SLA 3D printing include 3DXSTATTM ETX from 3D Systems, Solvay’s KetaSpire® PEEK and Huntsman’s Araldite® 1059 which provide extreme heat and chemical resistant SLA materials reinforced for high performance engineering applications in harsh, elevated temperature environments. These resins yield fully dense 3D printed parts with the highest deflection temperatures and strength suitable for end-use production of components exposed to intensive heat, corrosive media and heavy loads.
FAQ
1.How do flexible SLA resins differ from other types of resins in terms of flexibility and exposure to light?
Flexible resin is an elastomeric SLA 3D printing material used to produce rubber-like parts with high flexibility and compressibility. It contains urethane, silicone, and other thermoset elastomers to enable highly stretchable 3D printed components that bend and flex without fracturing. Flexible resin provides a 3D printable alternative to molded rubber.
How Flexible SLA Resins Differ
Flexible SLA resins stand out because they retain the ability to bend even after curing, unlike other resins that become rigid once exposed to light. The curing process involves exposure to light, which solidifies the resin but not completely. This partial solidification allows for continued flexibility. However, it’s important to note that prolonged exposure to UV light can cause flexible resins to become more rigid over time. This makes them ideal for applications where the product has a short lifecycle or can be shielded from light sources.
Properties
Typical properties of flexible SLA resin include:
- Tensile strength: 3-10 MPa
- Elongation at break: 100-500%
- Hardness (Shore A): 30
- Tear strength: 10-30 kN/m
- Density: 1.1-1.3 g/cm³
Flexible resins utilize silicone, urethane, and other thermoset elastomers to provide high elasticity and resilience. Popular base chemistries include urethane acrylate oligomers and silicone monomers combined with plasticizers and rubbers to achieve a Shore hardness of 30A to 70A. Flexible resins offer stretchability ranging from 3-10 times their original length, allowing for versatile applications in various industries.
By understanding these unique properties and behaviors, users can better select flexible SLA resins for projects requiring elasticity while managing exposure to light for optimal performance.
2.What are the properties and uses of medical SLA resins?
Dental and Medical SLA Resins
Medical SLA resins are crucial in the crafting of biocompatible components for both medical and dental applications. These resins are designed to withstand the rigors of long-term exposure to human or animal tissue. A key property is their ability to endure heat sterilization and other stressors without degrading, making them ideal for use in environments where sterility and durability are paramount.
Dental Model Resin
Dental model resin is a specialized SLA 3D printing material used for producing biocompatible parts for dental applications and orthodontic treatments. It meets ISO and FDA standards for temporary insertion into the human mouth. Dental model resin can produce highly accurate crown and bridge frameworks, orthodontic thermoforming models, surgical cutting guides, and other dental components.
Properties
Dental model resin exhibits the following properties:
- Biocompatibility – Meets ISO 10993 and USP Class VI standards for limited exposure in the mouth.
- High resolution – Provides fine details suitable for miniature dental geometries.
- Strong and durable – Rigid enough for dental purposes yet resists fracturing on removal.
- Non-toxic – Formulated with biocompatible, medical-grade monomers to be inert when exposed to human tissues and fluids.
- Density – Ranges from 1.1 to 1.3 g/cm³, typical of SLA photocuring resins.
Dental resins contain specialized acrylate, epoxy, and urethane monomers approved for medical use. They utilize biocompatible polymers and crosslinking agents tailored for dental devices and components requiring temporary placement in the mouth. Dental resins offer a 3D printable and quicker alternative to traditional dental plaster and stone models.
Applications
Dental model resin is designed specifically for SLA 3D printing of:
- Crown and bridge frameworks – Provide support structures for dental prosthetics.
- Orthodontic thermoforming models – Enable clear aligner therapy and retainers.
- Surgical cutting guides – Provide custom templates for precise implant placement.
- Temporary crowns and bridges – Produce short-term dental restorations.
- Maxillofacial models – Enable design and testing of customized prosthetics and implants.
- Nightguards and occlusal splints – Allow production of dental appliances for protecting teeth from grinding or trauma.
Popular dental model resins for SLA 3D printing include options that provide biocompatible SLA materials tailored to a range of dental and orthodontic applications. These specialized 3D printing resins yield high-resolution, sterilizable parts suitable for temporary insertion in the human mouth during treatment. Dental model resin enables labs and clinics to transition to more efficient and cost-effective 3D printing technologies.
By incorporating these properties and applications, both medical and dental SLA resins play a pivotal role in advancing healthcare technologies, ensuring that devices and models are both functional and safe for use in sensitive environments.