Resin 3D printing has witnessed a surge in popularity, captivating hobbyists and professionals alike with its ability to create objects featuring intricate details and smooth surfaces. However, when delving into this technology, individuals often encounter different acronyms, with SLA (Stereolithography) and LCD (Liquid Crystal Display) resin printing being two of the most common. Although both fall under the umbrella of Vat Polymerization, they differ significantly in terms of their working mechanisms, performance, cost, and more. This guide aims to comprehensively explore these differences to assist readers in making an informed decision.
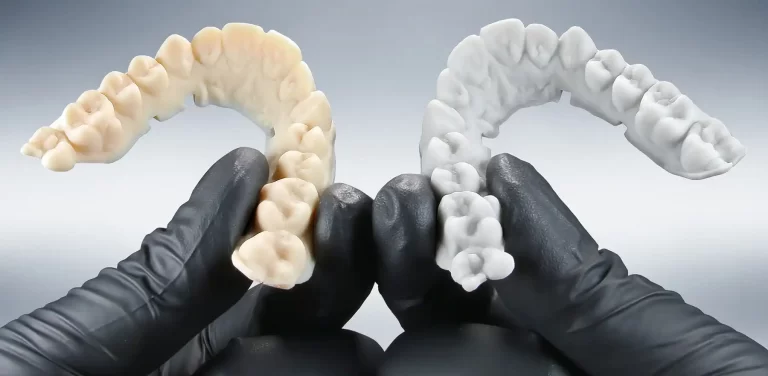
How Does Resin 3D Printing Work?
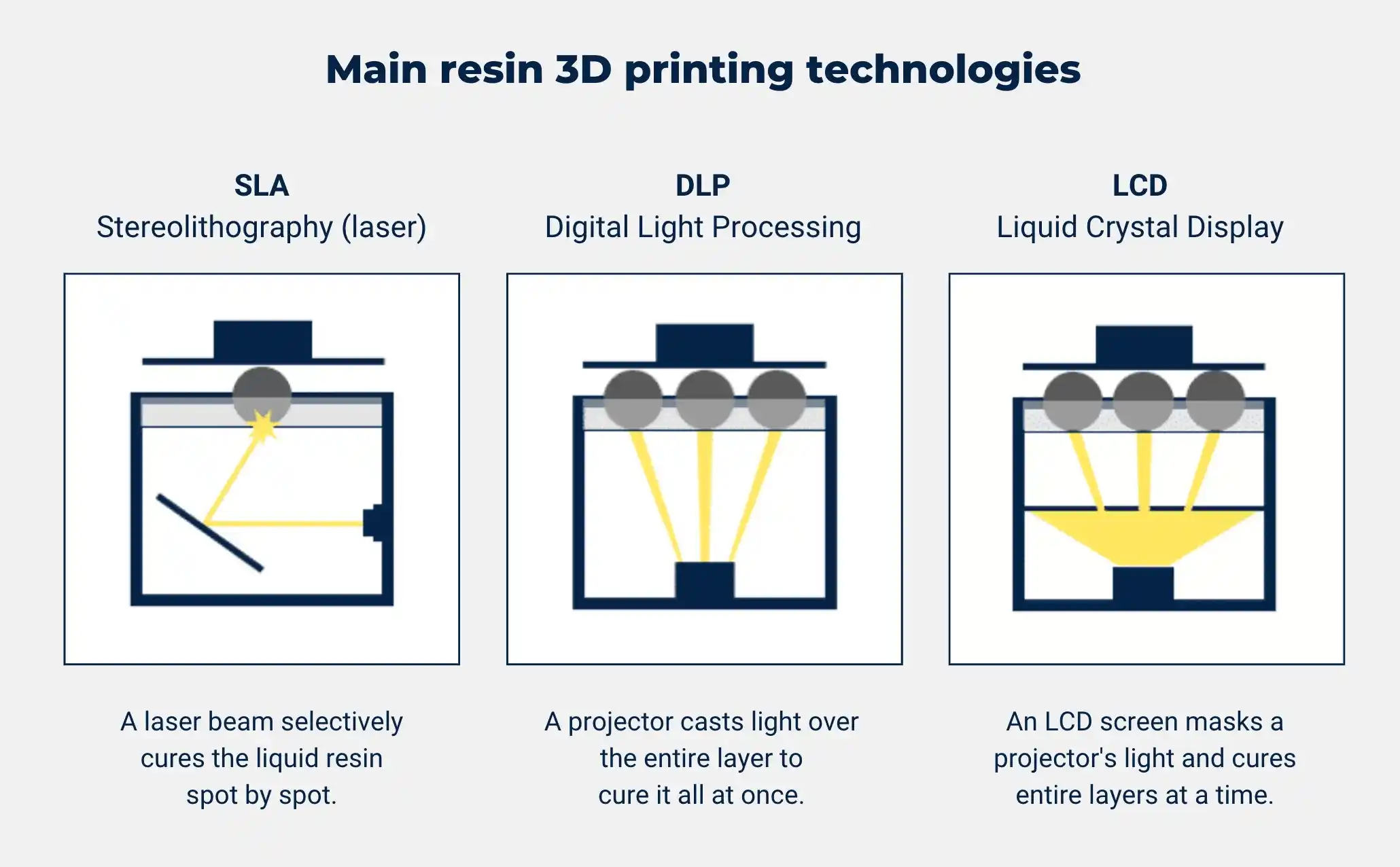
Resin 3D printing operates on the principle of Vat Polymerization. It begins with a photopolymer resin, a liquid plastic that reacts to light. The resin is placed in a vat, and a build platform is lowered into it, leaving a small gap. A light source, typically emitting UV light, shines through the bottom of the vat. When the light hits the resin in the gap, a chemical reaction called photocuring occurs, hardening the resin into a solid plastic layer. The build platform then lifts, peeling the newly cured layer off the vat’s bottom, and the process repeats for each subsequent layer.
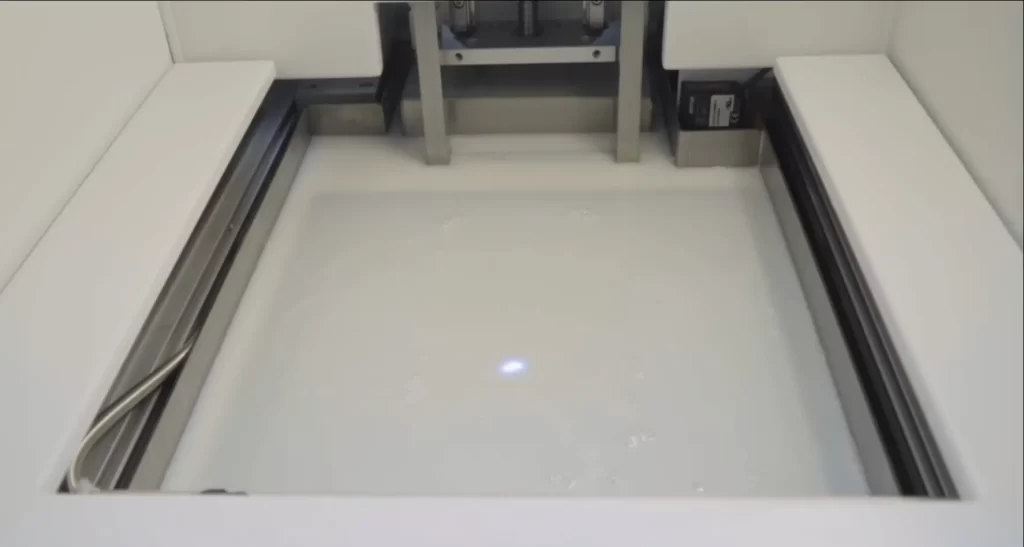
Key Components
- Photopolymer Resin: The crucial material in resin 3D printing, it hardens rapidly when exposed to UV light. Resins come in various types, each with distinct properties such as toughness, flexibility, or biocompatibility.
- ResinVat: This container holds the liquid resin. Its bottom is transparent, usually made of materials like FEP (Fluorinated Ethylene Propylene) or PFA (Perfluoroalkoxy), to allow light to pass through and facilitate the peeling of cured layers.
- Build Platform: A solid plate, often metal, onto which the print adheres and builds. It moves vertically to control the layer height.
- Light Source: The source of UV light that initiates the curing process. The type of light source and its projection method vary between SLA and LCD printers and significantly impact the printing process.
- Z – Axis Mechanism: Precision machinery, typically a lead screw and stepper motor, that controls the up – and – down movement of the build platform, determining the vertical resolution.
Understanding these components and the fundamental working principle of resin 3D printing is essential as it provides a basis for comprehending the differences between SLA and LCD printing technologies.
Stereolithography (SLA) 3D Printing

SLA was the first commercialized 3D printing technology, invented in the 1980s by Chuck Hull. It has played a significant role in establishing high – resolution printing in the resin 3D printing landscape.
Core Mechanism
At the heart of an SLA printer is a UV laser. The laser beam is directed across the resin surface by a pair of galvanometers, which act as computer – controlled mirrors. One mirror deflects the laser along the X – axis, and the other along the Y – axis. This enables the laser to trace the cross – sectional pattern of the object for each layer, point by point. This method, known as vector – based curing, results in the precise drawing of the solid areas onto the liquid resin, curing it instantly where the laser spot hits. Once a layer is complete, the build platform moves up (or the vat moves down), fresh resin flows in, and the process continues for the next layer.
Key Characteristics
- Fine Detail Potential: The resolution of an SLA print is largely determined by the size of the laser spot. Modern SLA systems can achieve small spot sizes, allowing for the creation of sharp edges, tiny features, and intricate textures.
- High Accuracy: The precise control of the laser path contributes to high dimensional accuracy across the build platform. The vector – based approach also enables smoother curves compared to pixel – based methods, although modern anti – aliasing techniques in other technologies have reduced this advantage.
- Variable Print Speed: The print speed of SLA depends on the complexity and surface area of the model on each layer. A layer with a small cross – section will print quickly, while a large, solid cross – section or multiple small parts will take longer as the laser has more area to cover.
- Smooth Surface Finishes: The continuous path drawn by the laser often leads to very smooth surfaces, especially on curved or angled faces, without the grid pattern sometimes visible in pixel – based technologies.
SLA: Then and Now
Initially, SLA machines were large, complex, and expensive, mainly used in industrial settings for rapid prototyping and tooling. However, advancements have led to the development of more accessible options. Desktop SLA printers, such as those by Formlabs, offer high resolution in a more compact and affordable package. Additionally, some lower – cost SLA printers have emerged, targeting the prosumer market.
LCD (MSLA) Resin 3D Printing
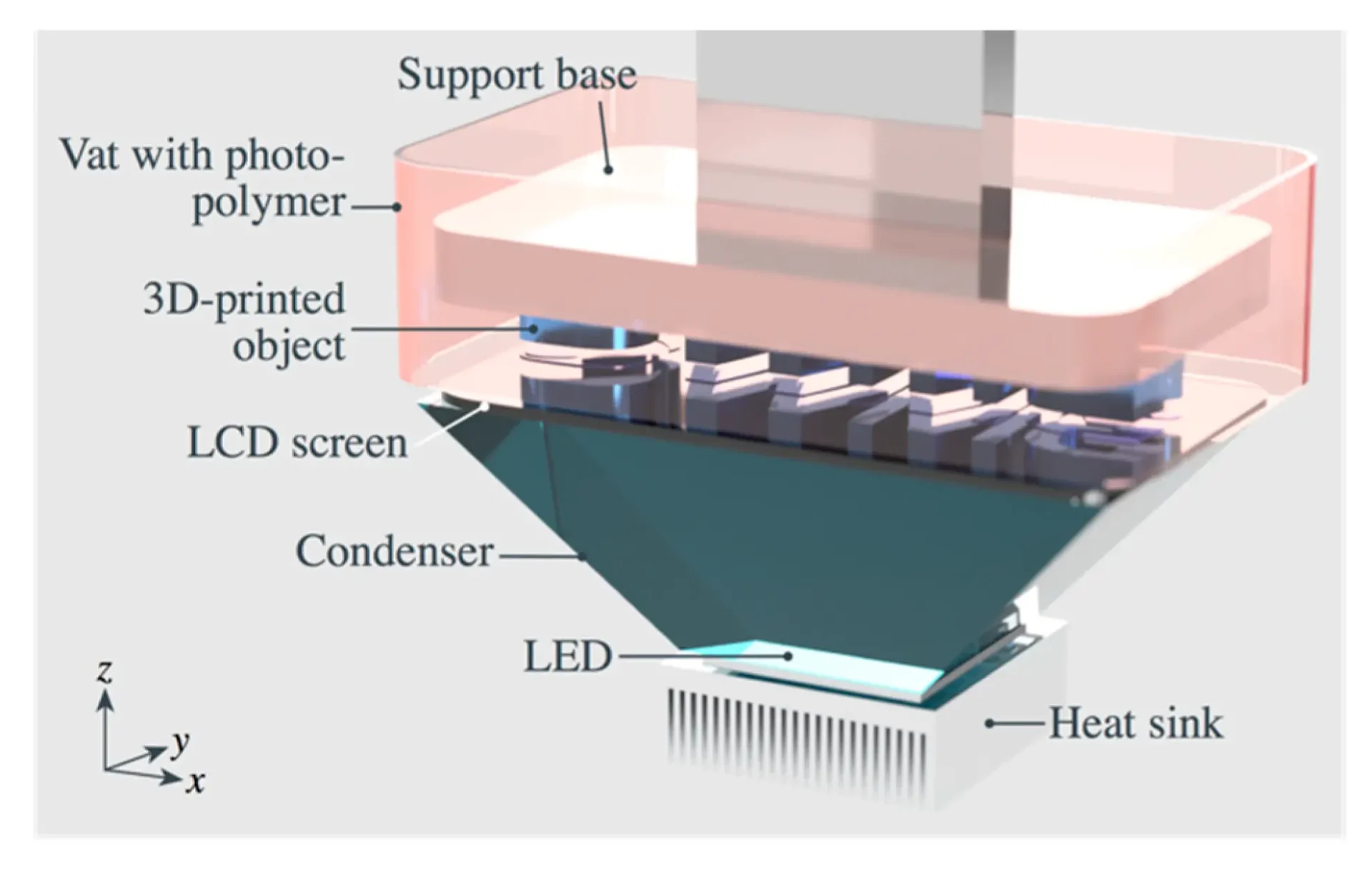
LCD – based resin printing has democratized high – resolution 3D printing, making it accessible to a wider audience. The terms LCD and MSLA (Masked Stereolithography) are often used interchangeably in the context of resin 3D printing.
How LCD/MSLA Printers Work
LCD printers use an array of UV LEDs as the light source, positioned below the resin vat. A monochrome LCD screen is placed between the LED array and the transparent bottom of the vat. For each layer of the print, the printer’s processor instructs the LCD screen to display a black – and – white cross – section of that layer. The white pixels on the LCD become transparent to the UV light from the LEDs, while the black pixels block the light. As a result, the LCD screen acts as a dynamic photomask. When the UV LED array is turned on, the light passes through the transparent pixels, curing the resin in the vat into a solid layer in the shape dictated by the mask. The entire layer is cured simultaneously, regardless of its complexity. After curing, the build platform lifts, peels the layer from the vat bottom, and the process repeats for the next layer.
Key Characteristics
- Consistent Print Speed: One of the major advantages of LCD printing is its consistent print speed per layer. Since the entire layer is cured at once, the time taken to cure a layer depends only on the resin’s exposure time and the desired layer height, not on the model’s complexity or the number of parts on the build plate. This makes LCD printers faster than traditional SLA for most print jobs.
- Resolution Based on Pixels: The detail an LCD printer can achieve is determined by the physical characteristics of its LCD screen, including pixel density (PPI), screen resolution (e.g., 2K, 4K, 8K), and pixel pitch. Smaller pixels result in higher potential detail.
- Potential for Pixelation: Due to the pixel – based nature of the mask, curved or angled edges may sometimes exhibit a stair – stepping effect, known as aliasing. However, modern LCD printers and slicer software use anti – aliasing techniques to smooth these transitions and reduce visible layer lines.
- Affordability: LCD screens and LED arrays are mass – produced components, making LCD printers more affordable compared to SLA printers. This affordability has made them dominant in the budget – friendly and mid – range resin printing market.
- LCD Screen as a Consumable: The intense UV light gradually degrades the liquid crystals in the LCD screen. Although modern monochrome screens can last 2000+ hours, they are still a consumable part that will eventually need replacement.
SLA vs. LCD Resin Printing: A Comparison
Light Source & Curing Method
- SLA: Utilizes a single, focused UV laser beam steered by galvanometers. It cures resin through vector – based, point – by – point drawing of the layer’s pattern.
- LCD: Employs a UV LED array and an LCD screen. The LCD acts as a mask, allowing light to pass through only where needed to cure the entire layer simultaneously.
Print Speed
- LCD Advantage: For most print jobs, LCD printers are generally faster. Their consistent layer – curing time makes them efficient for printing multiple parts or large – footprint objects.
- SLA Nuance: SLA speed depends on the surface area and complexity of the model within each layer. It can be faster for single, very small objects with a tiny cross – section but slower for large, solid objects or multiple parts.
Resolution, Detail & Accuracy
- XY Resolution: In LCD printers, it is defined by the pixel pitch of the LCD screen. SLA’s resolution is determined by the laser spot diameter, which can potentially be smaller than an LCD pixel, allowing for finer features.
- Z Resolution: Both SLA and LCD printers can achieve very thin layer heights, and the precision of the Z – axis motor and lead screw determines this aspect for both technologies.
- Achievable Detail & Surface Finish: SLA is often praised for its smooth surfaces, especially on curves. LCD printers may show faint pixel lines on angled or curved surfaces, but anti – aliasing techniques in modern models produce results that are often indistinguishable from SLA to the naked eye.
- Accuracy: Both technologies can achieve high dimensional accuracy. SLA may have a slight edge in large – print accuracy, while LCD accuracy depends on screen quality and calibration.
Cost Considerations
- Printer Purchase Cost: LCD printers are significantly more affordable due to the use of mass – produced components. SLA printers, with their precision lasers and galvanometer systems, are generally more expensive.
- Running Costs & Consumables: Resin costs are comparable for both technologies. However, the LCD screen is a consumable in LCD printers, while the laser and galvanometer system in SLA printers, although long – lasting, can be expensive to replace if they fail.
Build Volume
- Consumer/Prosumer Market: LCD printers often offer larger build volumes at the same price point compared to desktop SLA printers.
- Industrial Market: While both technologies have large – format printers, high – capacity industrial SLA machines have a longer history of producing large single parts.
Durability & Maintenance
- LCD: The main maintenance task is replacing the LCD screen. Regular FEP/PFA film replacement and cleaning are also required. The printer is mechanically simpler, with the screen being the main point of failure.
- SLA: Maintenance involves FEP/PFA film replacement, vat cleaning, and potentially more involved calibration. The laser/galvos are robust but expensive to repair if they fail.
Materials Compatibility
Most standard 405nm UV photopolymer resins are compatible with both SLA and LCD printers. However, some specialized resins may be optimized for either laser or LED sources.
Ease of Use
LCD printers are often designed with the consumer/hobbyist market in mind, offering a user – friendly experience with simple setup and operation. Professional SLA systems can involve more complex calibration procedures, although desktop SLA units have become more user – friendly.
Pros and Cons of SLA and LCD Resin Printing
Stereolithography (SLA)
- Pros:
- Potential for extremely fine feature resolution due to the small laser spot size.
- Historically high accuracy and smooth surface finishes, especially on curves.
- Long lifespan of core light engine components.
- Mature and well – understood technology, especially in industrial and professional settings.
- Cons:
- Generally higher initial printer cost.
- Print speed heavily dependent on model complexity.
- Potentially more complex mechanics and calibration.
- Expensive repairs if key components fail.
Liquid Crystal Display (LCD/MSLA)
- Pros:
- Significantly lower initial printer cost.
- Faster overall printing with consistent layer times.
- Excellent detail and accuracy for most needs, especially with high – resolution screens and anti – aliasing.
- Simpler mechanics and often easier to use.
- Wide variety of affordable models available.
- Cons:
- LCD screen is a consumable, adding a recurring running cost.
- Resolution limited by the pixel grid, which may result in less sharp corners or visible pixel patterns in some cases.
- Potential for uneven light distribution in some older or low – cost models, although this is less common in modern designs.
Choosing the Right Resin Printing Technology
The choice between SLA and LCD resin printing depends on several factors.
Identifying Priorities
- Budget: If low initial cost is a priority, LCD is the better choice. However, if long – term consumable costs are a concern and the budget allows, SLA can be considered.
- Print Speed & Throughput: For consistent speed and high throughput, especially when printing multiple parts or large objects, LCD is generally faster. SLA may be faster for single, very small, intricate items.
- Ultimate Detail, Resolution & Accuracy: SLA has a theoretical edge in achieving the finest details, but modern high – resolution LCD printers can deliver excellent results for most applications.
- Specific Use Case: For hobbyist – printed miniatures and models, LCD is often the best choice. In general prototyping, LCD offers a good balance of speed, accuracy, and cost. For jewelry, both SLA and LCD are used, with high – resolution LCDs being popular for cost and detail, and SLA for ultra – fine detail. In dental applications, both technologies are widely adopted, with LCD dominating the affordable end and SLA (or high – end DLP) being preferred for specific requirements. For engineering/high – accuracy parts, SLA may be needed for the highest precision, while LCD can be sufficient for less critical prototypes. For large parts, industrial SLA machines have a history of producing large single components, but large – format LCD printers offer better value for consumers.
- Ease of Use & Learning Curve: LCD printers are often more beginner – friendly, with simpler interfaces and workflows.
Scenario – Based Recommendations
- Hobbyists printing D&D miniatures and display models should choose an 8K or higher resolution LCD printer for affordable, detailed results.
- Small businesses prototyping product designs should opt for LCD printers for their speed, accuracy, and cost – effectiveness.
- Jewelers can consider high – resolution LCD printers first for value and detail, and explore desktop SLA if their designs require the highest precision.
- Aerospace engineering applications demanding certified high – dimensional accuracy should investigate professional – grade SLA or high – end DLP systems.
- Those looking for a cheap entry into resin printing should choose an entry – level LCD printer.
- For production environments requiring consistent speed and willing to manage screen replacements, LCD printers are the ideal choice.
DLP (Digital Light Processing) 3D Printing
DLP is another important technology in vat polymerization. It uses a specialized chip covered in microscopic mirrors (DMD chip) to reflect light where needed. DLP printers typically use a powerful UV projector lamp or UV LED light sources. The DMD chip, developed by Texas Instruments for digital projectors, contains hundreds of thousands or millions of individually controlled mirrors. Each mirror corresponds to a pixel in the projected image. The printer’s processor sends the layer’s cross – section image data to the DMD chip, and the mirrors tilt either towards or away from the light source to create the layer image. The reflected light passes through lenses and is projected onto the resin vat to cure the entire layer simultaneously.
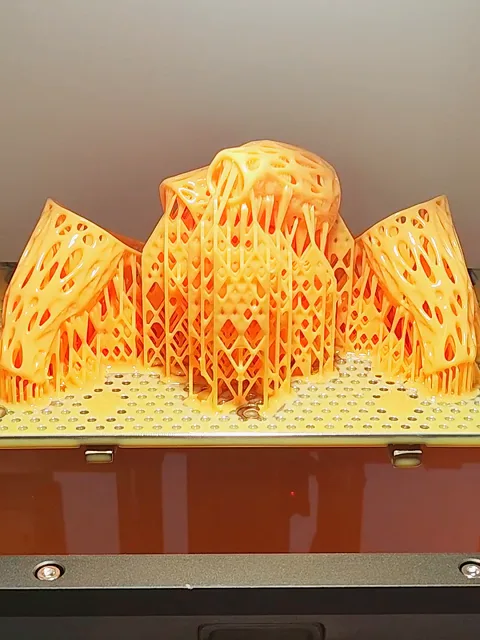
DLP differs from LCD in that it uses reflective micromirrors instead of a transmissive screen to shape the light. DLP projectors often produce more focused pixels, have longer – lasting components, and can achieve higher light intensity. Compared to SLA, DLP projects a full – layer image and is generally faster. DLP printers are more commonly found in professional desktop and industrial machines, especially in dentistry, audiology, and jewelry manufacturing. They are generally more expensive than LCD printers but less expensive than traditional industrial SLA machines.
Safety Precautions for Resin 3D Printing
Working with photopolymer resins requires strict adherence to safety protocols. Uncured resin can cause skin irritation, respiratory problems, eye damage, and environmental harm. To ensure safety:
- Ventilation: Work in a well – ventilated area, use a printer enclosure with an exhaust fan, and consider an air purifier.
- Personal Protective Equipment (PPE): Wear Nitrile gloves, safety glasses or goggles, a respirator mask (especially in less – ventilated areas), and protective clothing.
- Resin Handling: Minimize skin contact, use appropriate tools, protect the workspace, and clean spills immediately.
- Storage & Disposal: Store resin in tightly sealed, opaque containers in a cool, dark place. Dispose of unused resin, contaminated materials, and dirty IPA properly, ensuring they are fully cured before disposal.
- Post – Processing: Be mindful of safety during washing and curing processes, wearing PPE and avoiding direct exposure to UV light.
Future Trends in Resin 3D Printing
- Faster Printing: Advancements in resin chemistry, more powerful light sources, and optimized mechanics aim to reduce overall print times. Faster – curing resins, more efficient light sources, and improved peeling processes are expected.
- Higher Resolution: Denser LCD screens, smaller laser spots, and improved projection optics will lead to higher resolution and finer details in prints.
- Scaling Up and Down: Larger – format consumer printers and more specialized, compact machines are likely to be developed, making resin printing more accessible for different applications.
- Smarter Printing: Automation, including automated resin handling, advanced calibration, and monitoring, as well as integrated cloud workflows and environmental controls, will make resin printing more user – friendly and reliable.
- Resin Innovations: Resins with enhanced properties, eco – friendly options, a wider color palette, and biocompatible materials will expand the range of applications for resin printing.
Conclusion
In the world of resin 3D printing, there is no one – size – fits – all solution. SLA and LCD technologies each have their own strengths and weaknesses, and the choice between them depends on individual needs, priorities, and budget. LCD offers affordability, speed, and good detail for a wide range of applications, making it popular among hobbyists, small businesses, and in some professional fields. SLA, on the other hand, provides the potential for the highest precision and is often preferred in professional environments where extreme accuracy is crucial. By understanding the differences between these technologies and considering personal requirements, individuals can make an informed decision and unlock the creative potential of resin 3D printing.