In the dynamic realm of 3D printing, Selective Laser Sintering (SLS) emerges as a revolutionary technology. It transforms the way complex parts are conceptualized and fabricated. SLS can create intricate geometries without support structures, which has made it popular across diverse industries, including aerospace and healthcare. However, like any advanced technology, SLS 3D printing has its challenges. Understanding common issues and their solutions is crucial for efficient operation. This article delves into SLS technology, identifies frequent printing problems, and offers practical solutions to optimize the printing process.
Understanding SLS 3D Printing
SLS is an innovative and versatile 3D printing technology. It uses lasers and powdered materials to create highly detailed, complex parts that are hard to achieve with traditional manufacturing. This section explores SLS technology, its benefits, and common applications.
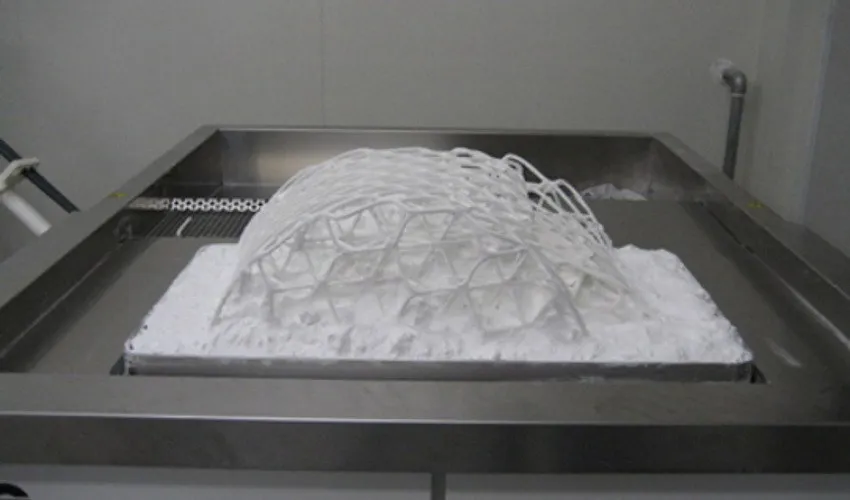
What is SLS 3D Printing?
At its core, SLS 3D printing is an additive manufacturing process. It employs a high-powered laser to fuse powdered materials into solid structures. Here’s how it works:
- Powder Layering: A thin layer of powdered material spreads across the build platform.
- Laser Sintering: The laser scans the layer. It selectively heats and fuses powder particles according to the 3D model.
- Layer-by-Layer Construction: After the laser completes a layer, the build platform lowers slightly. A new powder layer is applied on top. This process repeats until the part is fully formed.
- Cooling and Removal: After printing, the part cools. Excess powder is removed to reveal the final product.
Benefits of SLS Technology
SLS 3D printing offers several advantages over other additive manufacturing techniques:
Benefit | Description |
Support-Free Designs | SLS can create complex geometries and internal structures without support materials. |
Material Versatility | Compatible with various materials, such as plastics, ceramics, and metals. |
High Precision | Capable of producing parts with intricate details and tight tolerances. |
Functional Prototypes | Ideal for creating functional prototypes and end-use parts with mechanical properties similar to injection-molded components. |
Scalability | Suitable for low to medium production volumes, making it cost-effective for different applications. |
Common Applications of SLS Printing
SLS technology is used in multiple industries:
- Prototyping: To quickly iterate designs and create functional prototypes for form, fit, and function testing. For example, a product design company can use SLS to rapidly produce different versions of a new gadget’s casing to check its ergonomics.
- Aerospace Components: To manufacture lightweight, durable parts that can withstand extreme conditions. Parts like aircraft engine brackets can be made with SLS for better performance.
- Medical Devices: To create customized implants or prosthetics tailored to individual patient needs. A patient-specific dental implant can be 3D printed using SLS for a perfect fit.
- Consumer Products: To manufacture unique and complex designs for items like eyewear and footwear. Some high – end fashion brands use SLS to create one – of – a – kind shoe designs.
- Automotive Parts: To develop specialized vehicle components, enabling faster design cycles and cost reduction. A car manufacturer might use SLS to produce custom – made engine parts for a new concept car.
Grasping the fundamentals of SLS 3D printing is essential for those looking to utilize this technology. Its ability to create complex, support – free designs with various materials makes it a top choice for industries seeking innovation. The following sections will explore common SLS printing issues and solutions to optimize the printing process.
Common SLS 3D Printer Issues
Despite its advantages, SLS 3D printing has challenges. Understanding common problems and their solutions is crucial for achieving good results. This section examines frequently encountered SLS 3D printer issues, their symptoms, causes, and solutions.
1. Printing Failures
Printing failures are frustrating for SLS users. They can appear as incomplete prints, missing layers, or total print failures.
- Symptoms of Printing Failures:
- The part doesn’t adhere to the build platform.
- There are missing sections in the print.
- The part has significant deformation or collapse.
- The layer thickness is inconsistent.
- Possible Causes:
- Incorrect laser settings, like improper power or speed, can cause inadequate sintering.
- Low – quality or contaminated powder can affect the fusion process.
- Misaligned laser or build platform due to printer calibration issues can lead to failures.
- Solutions:
- Experiment with different laser power and speed settings to find the best combination for the material.
- Use high – quality, compatible powders from reliable suppliers.
- Regularly calibrate the printer. Check the laser and build platform alignment before each print.
2. Incomplete Prints
Incomplete prints waste time and materials.
- Symptoms of Incomplete Prints:
- The part has missing significant sections.
- There are weak or brittle areas in the printed part.
- The print stops during the process.
- Possible Causes:
- Insufficient laser energy may prevent the powder from fully melting.
- Uneven powder distribution can lead to improper fusing in some areas.
- Solutions:
- Ensure the laser settings are suitable for the specific material.
- Check that the powder is evenly distributed on the build platform before sintering each layer.
3. Poor Surface Finish
A poor surface finish affects the aesthetics and functionality of the printed part.
- Symptoms of Poor Surface Finish:
- The surface is rough and uneven.
- Visible layer lines or striations are present.
- There is an unwanted texture on the part’s surface.
- Possible Causes:
- Incorrect laser settings, such as high speeds or low power, can cause insufficient powder melting.
- Excessive cooling can lead to warping and affect surface quality.
- Solutions:
- Optimize the printing speed and laser power for a smoother finish.
- Consider post – processing techniques like sanding or chemical smoothing to improve the surface quality.
4. Warping and Deformation
Warping and deformation impact the dimensional accuracy of prints.
- Symptoms of Warping and Deformation:
- Parts don’t fit together as expected.
- The shape or dimensions are distorted.
- There are cracks or separations in the printed material.
- Possible Causes:
- Uneven cooling creates thermal stresses that cause warping.
- Fluctuations in temperature and humidity due to poor environmental control can affect print stability.
- Solutions:
- Maintain a stable temperature and humidity level in the printing area.
- Allow prints to cool slowly and evenly after sintering.
5. Inconsistent Layer Adhesion
Inconsistent layer adhesion makes parts weak and prone to breaking.
- Symptoms of Inconsistent Layer Adhesion:
- Parts break apart easily.
- There are visible gaps between layers.
- Printed sections flake or crumble.
- Possible Causes:
- Improper laser parameters result in inadequate energy input, leading to poor layer adhesion.
- Contaminated or improperly stored powder can affect adhesion.
- Solutions:
- Calibrate the laser settings for optimal layer bonding.
- Use fresh, dry, and uncontaminated powder for better layer adhesion.
6. Excessive Powder Consumption
Excessive powder consumption increases costs and indicates inefficiencies in the printing process.
- Symptoms of Excessive Powder Use:
- Higher – than – expected powder usage.
- Increased costs and waste.
- Possible Causes:
- Poor print orientation can lead to unnecessary powder use.
- Incorrect printer settings may cause over – sintering and powder waste.
- Solutions:
- Position parts to minimize powder use while maintaining structural integrity.
- Review and adjust printer settings to reduce unnecessary powder consumption.
Troubleshooting Steps
A systematic approach to troubleshooting SLS 3D printer issues saves time, materials, and frustration. This section covers a comprehensive troubleshooting guide, printer calibration, material handling, software settings, and maintenance.
1. General Troubleshooting Guide
A well – structured troubleshooting guide helps identify and resolve issues quickly. Follow these steps:
- Identify the Problem: Carefully observe the issue’s symptoms, such as printing failures or poor surface finish.
- Document the Symptoms: Take notes or photos of print failures for later reference.
- Consult the Manual: Check the printer’s user manual for model – specific troubleshooting tips.
- Refer to Online Resources: Look for forums, videos, or articles on similar issues.
- Test Small Adjustments: Make one change at a time to find the problem’s cause.
- Perform Test Prints: After adjustments, run small test prints to check the changes’ effectiveness.
- Analyze Results: Review test print results and decide on further actions.
2. Printer Calibration
Calibration is crucial for proper SLS printer operation and high – quality prints.
- Importance of Calibration:
- Accuracy: Ensures the laser aligns correctly with the build platform.
- Consistency: Provides uniform layer thickness and print quality.
- Prevents Failures: Reduces print failures and material waste.
- Calibration Steps:
- Check Laser Alignment: Use calibration tools or follow the manufacturer’s guidelines to ensure the laser aligns with the build area center.
- Adjust Build Platform Level: Verify the build platform is level using a level or calibration sheet. Uneven platforms cause uneven powder distribution.
- Set Layer Height: Adjust the layer height based on the material and desired detail. Smaller layer heights offer finer details but increase print time.
- Calibrate Temperature Settings: Ensure the printer’s heating elements work correctly. Temperature affects powder flow and sintering. Monitor and adjust the build chamber temperature as needed.
- Run Calibration Prints: Execute calibration prints to test adjustments. Analyze the results for accuracy and quality.
3. Material Handling and Storage
Proper material handling and storage impact print quality. Contaminated or improperly stored powders cause issues.
- Best Practices for Handling SLS Materials:
- Wear gloves to prevent powder contamination from skin oils and moisture.
- Keep different materials separate and ensure tools and containers are clean to avoid cross – contamination.
- Store materials in airtight containers to protect from moisture and contaminants.
- Storage Conditions:
- Store powders in a cool, dry place to prevent degradation.
- Use desiccants or humidity control packs to maintain low moisture levels.
4. Software Settings
Optimizing printer software settings affects print quality.
- Key Software Parameters
Parameter | Description |
Laser Power | Adjust to ensure proper sintering without burning the powder. |
Scan Speed | Optimize based on material type and desired detail. |
Layer Thickness | Set according to the desired resolution and print time. |
Cooling Settings | Manage cooling rates to prevent warping or cracking. |
- Recommended Settings for Different Materials:
- Nylon: Use moderate laser power, medium scan speed, and 0.1 mm layer thickness for detailed parts.
- Polystyrene: Use lower laser power, faster scan speed, and 0.1 mm layer thickness for high – detail parts.
5. Maintenance Tips
Regular maintenance keeps the SLS printer in good condition and prevents issues.
- Recommended Maintenance Routines:
- Daily Checks: Inspect the build chamber for residual powder and clean as needed. Check for visible wear on the laser optics.
- Weekly Maintenance: Clean filters and fans to prevent overheating and ensure proper airflow. Lubricate moving parts as per the manufacturer’s instructions.
- Monthly Maintenance: Thoroughly inspect the printer’s components and connections. Update software and firmware for improved performance.
- Yearly Overhaul: Schedule professional service to find hidden issues and perform necessary repairs or replacements.
Advanced Troubleshooting Techniques
As you gain more experience with SLS 3D printing, you may encounter complex issues. Advanced troubleshooting techniques involve analyzing print data, adjusting laser settings, and considering environmental factors.
1. Analyzing Print Data
Analyzing print data helps diagnose persistent SLS printing problems.
- Importance of Print Data:
- Identifies trends in failures, helping to find underlying issues.
- Guides parameter adjustments for better results.
- Tracks improvements over time.
- Key Data Points to Analyze
Data Point | Description |
Laser Power Levels | Shows the energy used during printing. |
Print Speed | Indicates the laser’s movement speed during printing. |
Layer Height | Displays the thickness of each printed layer. |
Cooling Rates | Tracks how quickly the part cools after printing. |
Material Usage | Monitors powder consumption during the print. |
- Techniques for Analyzing Print Data:
- Use diagnostic software that comes with the printer to visualize print data.
- Compare successful and failed prints to spot differences in data points.
- Keep a log of print settings and results to track changes and identify successful adjustments.
2. Adjusting Laser Settings
The laser is crucial in SLS printing. Proper laser adjustments can solve many print quality issues.
- Key Laser Settings to Adjust
Setting | Impact on Print Quality |
Laser Power | Affects the energy applied to the powder. Too low power causes incomplete fusions, while too high power can burn the material. |
Scan Speed | Determines how fast the laser moves across the powder. A slower speed can improve adhesion. |
Point Distance | Controls the spacing of laser points, affecting surface finish and detail. |
- Techniques for Adjusting Laser Settings:
- Print small test patterns with different laser power and speed settings to find the optimal settings for the material.
- Use feedback from print data analysis to adjust settings. For example, if failures occur at certain power levels, change them accordingly.
- Consult the 3D printing community or experts for insights on effective laser settings for different materials.
3. Environmental Factors
The printing environment affects SLS print quality. Temperature, humidity, and air circulation are important.
- Importance of Environmental Control:
- Maintains print stability for consistent results.
- Preserves material integrity by preventing powder from absorbing moisture or contaminants.
- Key Environmental Factors to Monitor
Factor | Ideal Conditions |
Temperature | Typically between 20°C to 25°C (68°F to 77°F) for optimal printing. |
Humidity | Preferably below 50% to prevent powder from absorbing moisture. |
Air Quality | A clean, dust – free environment minimizes contamination. |
- Techniques for Managing Environmental Factors:
- Use climate control systems or dehumidifiers to maintain optimal temperature and humidity in the printing area.
- Install air filters or purifiers to keep the environment dust – free.
- Use temperature and humidity sensors to monitor conditions and make adjustments as needed.
Case Studies
Real – world case studies offer valuable insights into SLS 3D printer troubleshooting. They show how users overcame challenges. This section explores case studies highlighting common issues, troubleshooting strategies, and key takeaways.
Case Study 1: Incomplete Prints Due to Inadequate Laser Power
- Background: A small prototyping firm using an SLS printer had many incomplete prints. This affected their clients’ product development.
- Troubleshooting Steps:
- The team documented the incomplete prints and compared them to successful ones. They noticed failures often occurred with a specific material.
- They reviewed the printer logs and found the laser power was set lower than recommended for that material.
- After consulting the material supplier, they increased the laser power gradually and conducted test prints to find the optimal setting.
- They conducted more test prints and closely monitored the results.
- Outcome: The adjustments led to complete prints that met the specifications. The firm restored client confidence.
- Key Takeaways:
- Regularly review and adjust laser power settings according to material specifications.
- Document print outcomes to identify patterns for troubleshooting.
Case Study 2: Surface Finish Issues with Nylon Prints
- Background: A consumer products company had poor surface finishes on nylon prints. This was unacceptable for their high – end clients.
- Troubleshooting Steps:
- The team documented the roughness and noticed it was related to certain design geometries.
- They asked for advice on online forums.
- They found that their scan speed was too fast, causing rough surfaces.
- They slowed down the scan speed and adjusted the layer thickness for a balance between quality and print time.
- They explored post – processing techniques like chemical smoothing.
- Outcome: The surface quality improved, leading to satisfied clients and repeat orders. The company made post – processing a standard procedure for some product lines.
- Key Takeaways:
- Engage with the 3D printing community for solutions.
- Small adjustments in print parameters can improve quality.
Case Study 3: Warping Issues in Detailed Parts
- Background: An engineering firm faced warping issues when printing intricate aerospace parts. This affected the prototypes’ dimensional accuracy.
- Troubleshooting Steps:
- The team noticed warping mainly occurred in larger, detailed parts printed in a specific orientation.
- They found temperature fluctuations in the printing environment.
- They experimented with different orientations and support structures to reduce thermal stress.
- They controlled the environment by insulating the printer and maintaining stable temperature and humidity.
- Outcome: Warping decreased, and the prototypes met the aerospace industry’s strict requirements.
- Key Takeaways:
- Consider part orientation for print quality and stability.
- Control the printing environment, especially for detailed parts.
Resources and Tools
Having the right resources and tools is essential for SLS 3D printing and troubleshooting. This section lists recommended tools, online communities, and emphasizes manufacturer support.
1. Recommended Tools for Troubleshooting
Invest in these essential tools for efficient troubleshooting:
Tool | Purpose |
Calipers | Accurately measure part dimensions and check tolerances. For instance, when verifying if a printed component’s diameter matches the design specifications, calipers can provide precise measurements. |
Laser Power Meter | Measure the output of the laser to ensure it functions correctly. This helps in detecting if the laser is delivering the appropriate energy for sintering, which is crucial for print quality. |
Leveling Tool | Guarantee that the build platform is level. An unlevel platform can lead to uneven powder distribution, affecting the print’s integrity. A leveling tool helps in achieving a flat surface for consistent printing. |
Thermal Imaging Camera | Monitor temperature variations in the build chamber during printing. By observing temperature patterns, users can identify areas of uneven heating or cooling, which may cause issues like warping or incomplete sintering. |
Dust – free Cloth | Clean optics and other sensitive components without leaving residue. This is important as any debris on the optics can scatter the laser beam, leading to inaccurate sintering and poor print quality. |
Sieve | Filter out clumps or contaminants in the powder before use. Contaminated powder can result in printing failures, and a sieve helps in ensuring that only fine, uniform powder is used for printing. |
Material Storage Containers | Airtight containers keep powders dry and free from contaminants. Moisture – laden powder can affect the sintering process, and these containers maintain the powder’s quality during storage. |
2. Online Communities and Forums
Joining online communities and forums provides access to a wealth of knowledge from fellow SLS 3D printing enthusiasts:
- Reddit: Subreddits such as r/3Dprinting and r/AdditiveManufacturing are great platforms. Here, users can ask questions, share their experiences, and learn from others. For example, someone facing issues with a new material can post about their problem and get advice from those who have already worked with it.
- 3D Printing Stack Exchange: It is a Q&A site dedicated to 3D printing. Users can browse through existing questions or post their own to receive community feedback. This is useful for getting targeted answers to specific SLS – related problems.
- Facebook Groups: There are numerous Facebook groups focused on 3D printing and SLS technology. These groups facilitate connections with like – minded individuals. Members can share their latest projects, offer tips on troubleshooting, and discuss new developments in the field.
- Forums: Websites like 3DPrintBoard and Print3DForum have dedicated sections for discussions about various 3D printing technologies, including SLS. These forums often have in – depth threads on specific topics, making it easy to find solutions to common and not – so – common issues.
Benefits of Engaging with Communities
- Knowledge Sharing: Learn from the experiences of others who have faced similar challenges. For example, if someone is struggling with layer adhesion problems, they can find posts from users who have overcome the same issue and get practical solutions.
- Networking: Connect with professionals and enthusiasts in the field. This can lead to collaborative opportunities, such as joint research projects or business partnerships.
- Stay Updated: Keep abreast of the latest trends, technologies, and best practices in SLS printing. Community members often share news about new materials, software updates, and innovative printing techniques.
3. Manufacturer Support and Documentation
Manufacturer support and documentation are invaluable resources:
- Importance of Manufacturer Support
- Technical Assistance: Manufacturer support teams can offer guidance specific to your printer model and the materials it uses. If you encounter a problem that seems unique to your printer, they can provide tailored solutions.
- Troubleshooting Guides: Many manufacturers offer detailed troubleshooting guides and manuals. These resources address common issues faced by users and provide step – by – step solutions.
- Software Updates: Staying updated with the latest software and firmware versions is crucial. Updates often include performance optimizations and bug fixes that can improve the printing process and resolve known issues.
- Documentation to Review
- User Manuals: Always refer to the user manual for your specific SLS printer model. It contains essential information on setup, operation, and troubleshooting. For example, the manual can guide you through the initial calibration process.
- Material Data Sheets: Review data sheets for the materials you are using. These documents provide critical information on material properties, such as melting points, recommended laser settings, and optimal printing temperatures.
- Online Resources: Many manufacturers provide online resources, including FAQs, video tutorials, and forums. These can be a quick source of answers to common questions and can help you get up – to – date information about your printer.
Conclusion
SLS 3D printing is a powerful technology with vast potential, but it comes with its share of challenges. By understanding the intricacies of SLS technology, identifying common issues, and implementing systematic troubleshooting methods, users can overcome these obstacles and achieve high – quality prints.
Key Takeaways
- Understand the Basics: A solid understanding of SLS technology and its benefits, such as support – free designs and high precision, is fundamental for maximizing its potential in various projects.
- Identify Common Issues: Familiarize yourself with typical SLS printing problems like incomplete prints, poor surface finishes, and warping. Recognizing the symptoms early allows for timely corrective action.
- Systematic Troubleshooting: Adopt a structured troubleshooting approach. Document symptoms, analyze print data, and make incremental adjustments. This systematic method helps in efficiently diagnosing and resolving issues.
- Calibration and Maintenance: Regular calibration and maintenance of your printer are essential for consistent performance. Keeping your equipment in top condition reduces the risk of failures and enhances print quality.
- Advanced Techniques: Utilize advanced troubleshooting techniques, such as analyzing print data and managing environmental factors. These can significantly improve print success rates, especially when dealing with complex issues.
- Use Resources: Leverage the available tools, online communities, and manufacturer support. Engaging with the 3D printing community can provide valuable insights, while manufacturer resources offer model – specific guidance.
Call to Action
Now that you have gained this knowledge, it’s time to put it into practice:
- Join the Conversation: Actively participate in online communities. Share your experiences, whether they are success stories or challenges. Your contributions can help others and also enrich your own understanding of SLS 3D printing.
- Experiment and Innovate: Don’t be afraid to experiment with different settings, materials, and techniques. Each print is an opportunity to learn and refine your skills. For example, try using a new combination of laser power and scan speed to achieve a unique surface finish.
- Stay Informed: Keep up with the latest developments in SLS technology and printing techniques. The 3D printing field is constantly evolving, and staying informed gives you a competitive edge in your projects.
Final Thoughts
SLS 3D printing opens up endless possibilities for creativity and innovation. By embracing the troubleshooting process as an integral part of your workflow, you can unlock the full potential of this technology. Remember, every challenge you encounter is a learning opportunity. Continuously strive to improve your skills and explore new frontiers in SLS 3D printing.