In the ever-evolving landscape of modern manufacturing, innovation is the key to staying ahead. Among the myriad of technologies pushing the boundaries of what’s possible, Selective Laser Sintering (SLS) 3D printing stands out as a trailblazer.
SLS 3D printing is not just a technological advancement; it’s a revolution in how we think about manufacturing processes and product development. With roots tracing back to the 1980s, SLS has matured significantly, becoming a cornerstone of rapid prototyping and small-batch production. But what exactly makes SLS so special? How does it work, and why is it considered more efficient than traditional manufacturing methods?
In this comprehensive blog series, we will dive deep into the world of SLS 3D printing. From its intricate processes and diverse material options to the plethora of applications and future trends, we’ll explore every facet of this transformative technology.
What is SLS 3D Printing?
Selective Laser Sintering (SLS) 3D printing is one of the most advanced and versatile additive manufacturing technologies available today. At its core, SLS uses a high-powered laser to fuse small particles of polymer powder into a solid structure based on a 3D model. But to truly appreciate the capabilities of SLS, let’s dive deeper into what this technology is all about.
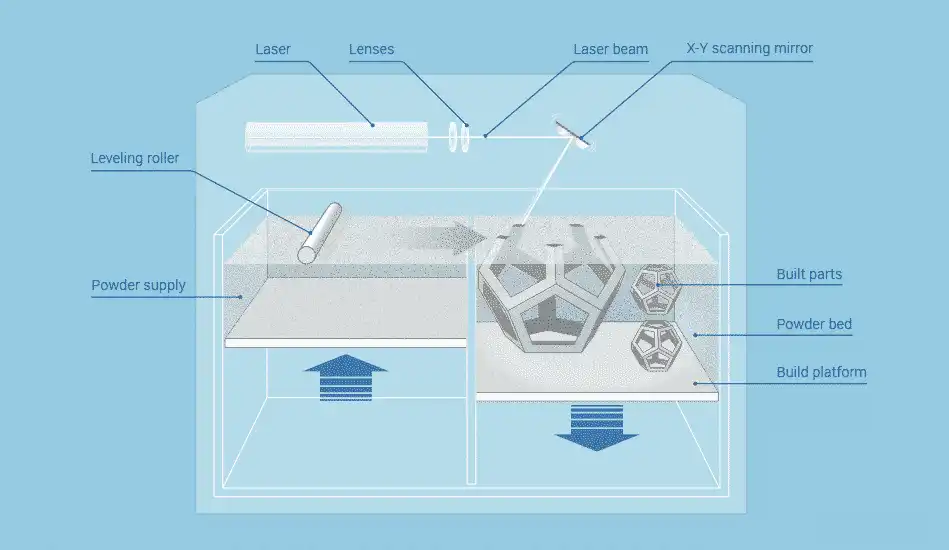
Understanding Selective Laser Sintering (SLS)
SLS 3D printing is a type of additive manufacturing that leverages the power of lasers to create detailed and complex parts layer by layer. Unlike other 3D printing methods that might use liquid resins or filament, SLS employs a fine powder as its raw material. Here’s a step-by-step breakdown of the process:
- Preparation of Powder Bed: A thin layer of powder is spread evenly across the build platform.
- Laser Sintering: A high-powered laser selectively fuses the powder particles together, following the cross-section of the 3D model.
- Layering: The build platform lowers slightly, and a new layer of powder is spread over the previous layer.
- Repetition: The process repeats until the entire part is built up layer by layer.
- Cooling and Post-Processing: Once the build is complete, the part is allowed to cool and then undergoes various post-processing steps to achieve the desired finish and properties.
Comparison with Other 3D Printing Technologies
To fully grasp the uniqueness of SLS, it’s helpful to compare it with other popular 3D printing technologies:
Technology | Material | Process | Advantages | Disadvantages |
FDM | Filament (PLA, ABS) | Extrusion of melted thermoplastic | Cost-effective, easy-to-use | Lower resolution, visible layer lines |
SLA | Liquid resin | Curing resin with a UV laser | High resolution, smooth surface finish | Expensive materials, post-processing |
SLS | Powder (Nylon, etc.) | Laser sintering of powdered material | No support structures needed, durable parts | High initial cost, requires expertise |
Why Choose SLS 3D Printing?
SLS 3D printing offers several distinct advantages that make it a preferred choice for many applications:
- High Efficiency: The ability to build parts without the need for support structures means that multiple parts can be produced simultaneously, maximizing efficiency.
- Design Flexibility: Complex geometries and intricate details are easily achievable, allowing for the creation of parts that would be impossible with traditional manufacturing methods.
- Material Versatility: SLS can use a wide range of materials, including various polymers and composites, each offering unique properties suitable for different applications.
Applications of SLS 3D Printing
The versatility and efficiency of SLS make it suitable for a variety of industries. Some notable applications include:
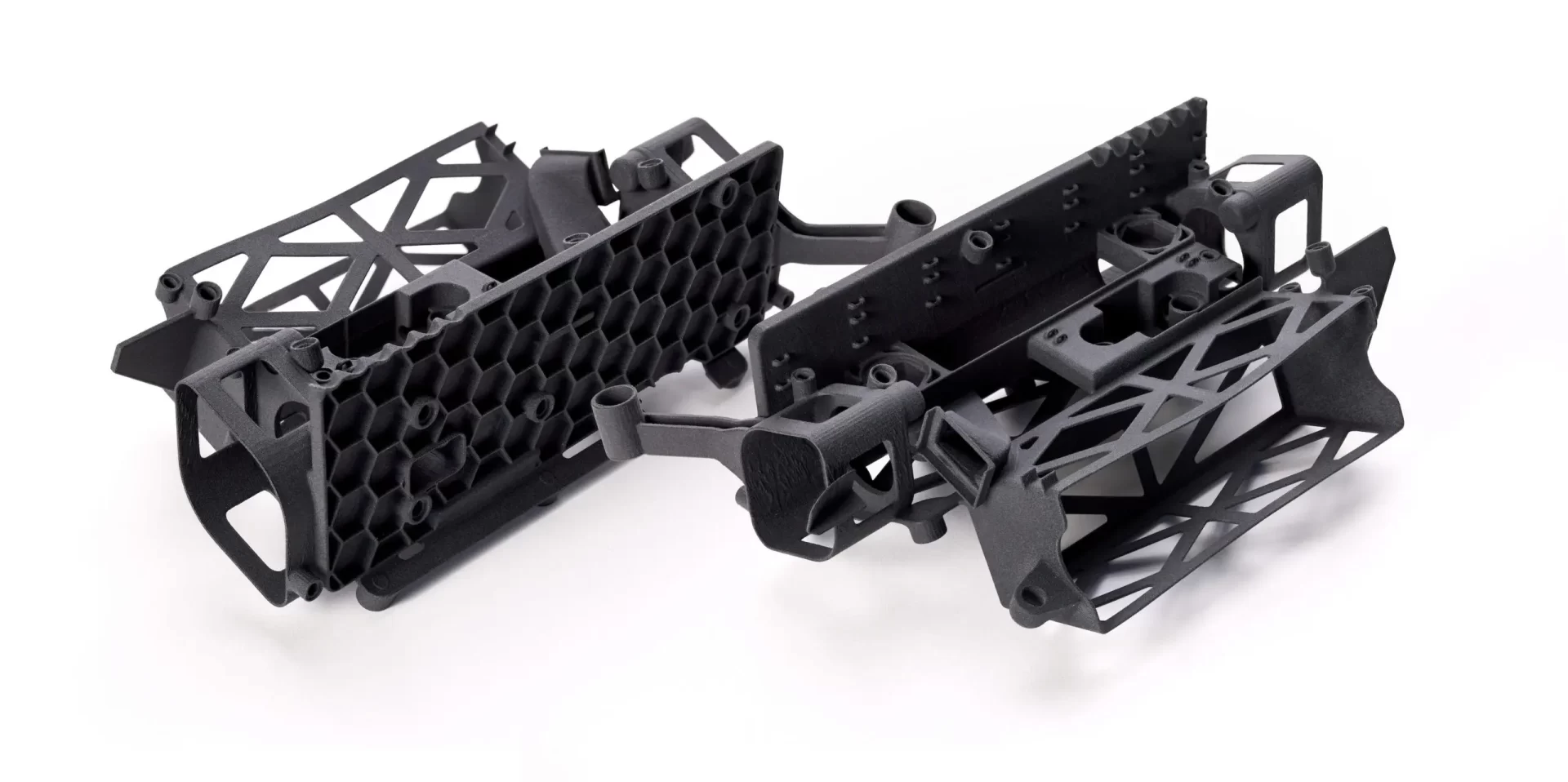
- Prototype Development: Rapid creation of functional prototypes for testing and validation.
- Medical Devices: Custom implants and prosthetics designed for specific patient needs.
- Automotive Parts: Lightweight, durable components for vehicles.
- Consumer Products: Customized goods like eyewear and fashion accessories.
Applications and Benefits
Industry | Application | Benefits |
Automotive | Lightweight components | Increased fuel efficiency, reduced weight |
Medical | Custom implants, prosthetics | Personalized patient care, quicker recovery |
Consumer Goods | Custom eyewear, fashion accessories | Unique, high-quality products |
Aerospace | Prototype parts, complex geometries | Reduced development time, enhanced performance |
Selective Laser Sintering (SLS) 3D printing is a powerful technology that offers unparalleled flexibility and efficiency in modern manufacturing. Whether you’re creating a prototype or producing end-use parts, SLS provides the tools and capabilities to transform your ideas into reality. By understanding the process and its benefits, you can leverage SLS to drive innovation and efficiency in your manufacturing endeavors.
Materials Used in SLS 3D Printing
Selective Laser Sintering (SLS) 3D printing is renowned for its versatility and ability to work with a diverse range of materials. The choice of material significantly impacts the properties and applications of the final product. In this section, we’ll explore the most commonly used materials in SLS 3D printing, their properties, and how they contribute to the efficiency and effectiveness of the manufacturing process.
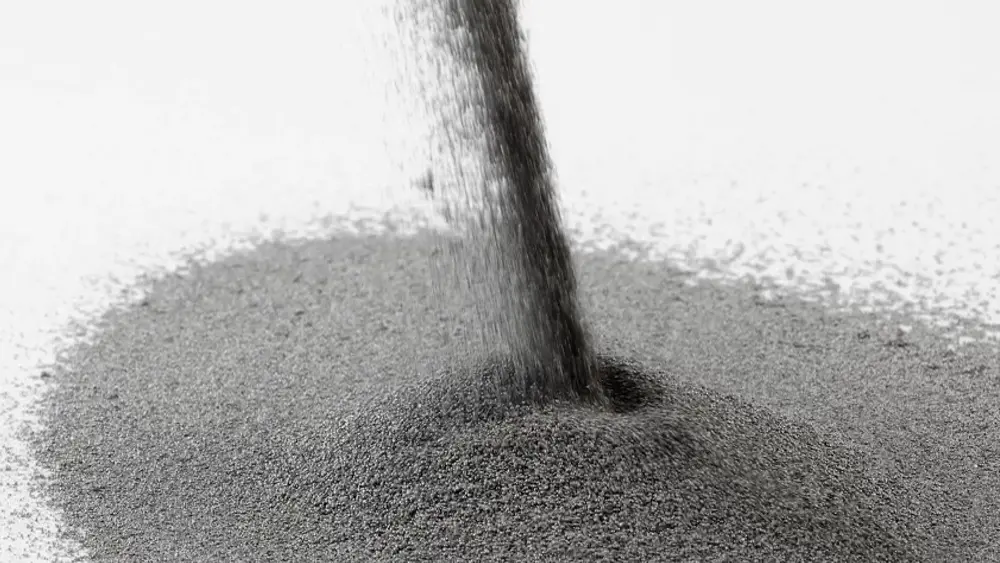
Common Materials in SLS 3D Printing
Polymers: The most widely used materials in SLS 3D printing are polymers. These materials are chosen for their excellent mechanical properties, versatility, and cost-effectiveness.
- Nylon (Polyamide 12 – PA12):
- Description: Nylon is the most commonly used polymer in SLS. It offers a good balance of strength, flexibility, and durability.
- Applications: Ideal for functional prototypes, end-use parts, and complex geometries.
- Properties:
- Tensile Strength: High
- Flexibility: Moderate
- Durability: High
- Nylon 11 (PA11):
- Description: Similar to PA12, but offers better impact resistance and flexibility.
- Applications: Suitable for parts requiring high elasticity, such as hinges and snap-fits.
- Properties:
- Tensile Strength: High
- Flexibility: High
- Durability: High
- Glass-Filled Nylon:
- Description: Nylon mixed with glass beads to enhance stiffness and thermal resistance.
- Applications: Used in applications requiring high rigidity and thermal stability.
- Properties:
- Tensile Strength: Very High
- Flexibility: Low
- Durability: High, with increased thermal resistance
Composites and Filled Powders: These materials combine polymers with other substances to enhance specific properties.
- Alumide (Aluminum-filled Nylon):
- Description: Nylon filled with aluminum particles, offering a metallic appearance and increased stiffness.
- Applications: Suitable for aesthetic prototypes and parts requiring higher rigidity.
- Properties:
- Tensile Strength: High
- Flexibility: Low
- Durability: Moderate
- Aesthetic: Metallic finish
Material Properties
Selecting the right material for SLS 3D printing depends on the required properties of the final product. Here are some key properties to consider:
- Mechanical Properties:
- Tensile Strength: Determines the material’s resistance to breaking under tension.
- Flexibility: The ability of the material to bend without breaking.
- Durability: The overall lifespan and resistance to wear and tear.
- Thermal Properties:
- Heat Resistance: The ability to withstand high temperatures without deforming.
- Thermal Stability: Resistance to changes in properties at varying temperatures.
- Electrical Properties:
- Conductivity: Some applications may require materials with specific electrical conductivity or insulation properties.
Common SLS Materials and Their Properties
Material | Tensile Strength | Flexibility | Durability | Thermal Resistance | Applications |
Nylon (PA12) | High | Moderate | High | Moderate | Prototypes, end-use parts, complex geometries |
Nylon 11 (PA11) | High | High | High | Moderate | Hinges, snap-fits |
Glass-Filled Nylon | Very High | Low | High | High | Parts requiring high rigidity and thermal stability |
Alumide | High | Low | Moderate | Moderate | Aesthetic prototypes, rigid parts |
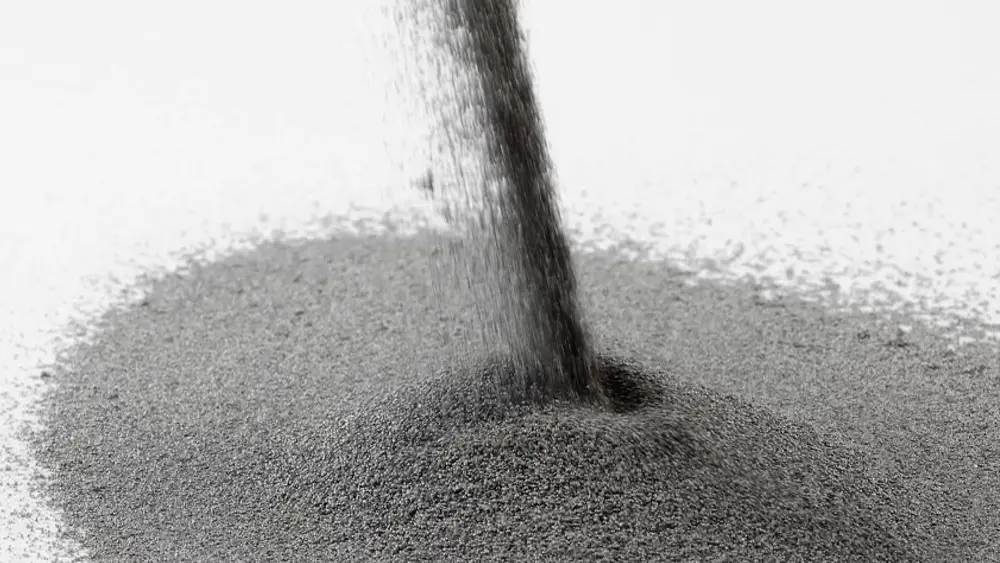
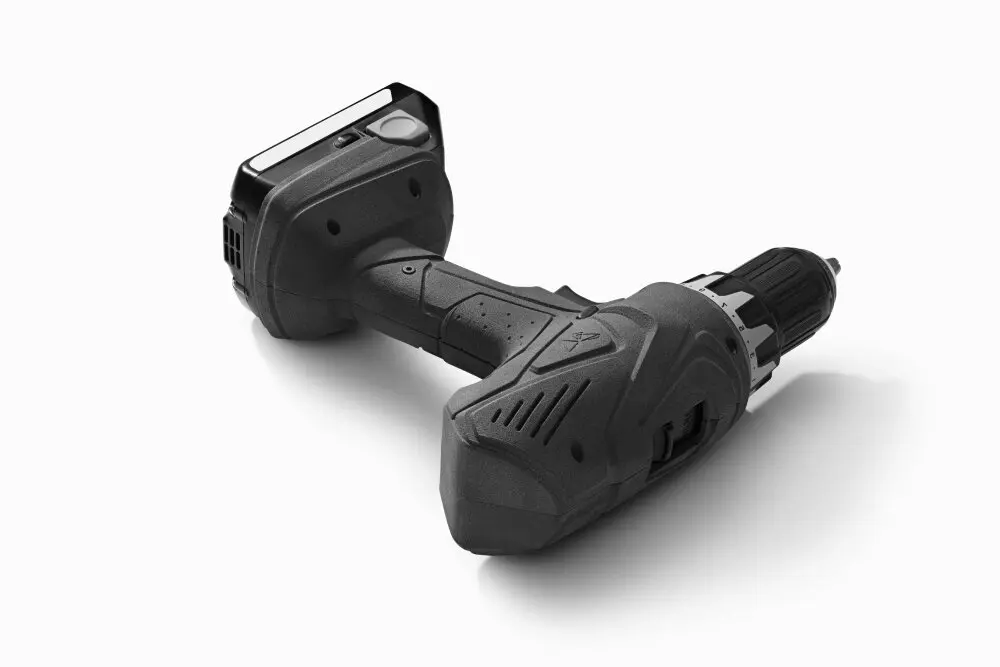
The choice of material in SLS 3D printing is crucial as it directly impacts the functionality, appearance, and longevity of the final product. By understanding the properties and applications of various SLS materials, manufacturers can make informed decisions to optimize their processes and achieve the desired outcomes. Whether you need high strength, flexibility, or thermal resistance, SLS offers a material solution to meet your specific requirements, making it a powerful tool in modern manufacturing.
Advantages of SLS 3D Printing
Selective Laser Sintering (SLS) 3D printing has rapidly emerged as a leading technology in the field of additive manufacturing. Its unique process and material capabilities offer several significant advantages over traditional manufacturing methods and other 3D printing technologies. In this article, we will explore these advantages in detail, highlighting why SLS 3D printing is a game-changer in modern manufacturing.
High Efficiency
One of the most compelling benefits of SLS 3D printing is its high efficiency. This efficiency can be attributed to several factors:
- Speed of Production: SLS can produce multiple parts in a single build cycle without the need for support structures. This capability significantly reduces the time required to manufacture complex parts.
- Batch Production: The ability to nest parts within the build chamber allows for the simultaneous production of multiple items, optimizing the use of the build volume and further enhancing efficiency.
- Material Utilization: Unfused powder can be recycled and reused, minimizing material waste and reducing overall costs.
Precision and Accuracy
SLS 3D printing is known for its exceptional precision and accuracy, making it ideal for producing intricate and detailed parts.
- High Tolerance Levels: SLS can achieve tight tolerances, which is crucial for creating parts that need to fit together precisely. This makes it suitable for producing functional prototypes and end-use components.
- Surface Finish Quality: The laser sintering process yields parts with good surface finish quality, reducing the need for extensive post-processing. Although some finishing may still be required, the initial quality is often sufficient for many applications.
Design Flexibility
SLS 3D printing provides unparalleled design flexibility, enabling the creation of complex geometries that are difficult or impossible to achieve with traditional manufacturing methods.
- Complex Part Geometries: The layer-by-layer construction method allows for the production of highly complex shapes, including internal features and undercuts.
- Customization Capabilities: SLS allows for easy customization, enabling manufacturers to produce tailored solutions quickly and cost-effectively. This is particularly beneficial for industries like healthcare, where custom implants and prosthetics are often required.
Advantages
Advantage | Description | Benefits |
High Efficiency | Fast production speed, batch production, and material recycling | Reduced time-to-market, cost savings, minimal material waste |
Precision and Accuracy | High tolerance levels and good surface finish quality | Functional prototypes, minimal post-processing |
Design Flexibility | Ability to create complex geometries and customized parts | Innovative designs, tailored solutions for specific needs |
Case Studies
To illustrate the real-world impact of SLS 3D printing, let’s look at a few case studies:
Industry Applications
Prototyping
One of the primary applications of SLS 3D printing is rapid prototyping. The ability to quickly produce functional prototypes allows designers and engineers to test and iterate their designs efficiently.
- Functional Prototypes: SLS can create highly detailed and durable prototypes that can be used for functional testing, helping to identify design flaws early in the development process.
- Iterative Design: The quick turnaround time allows for multiple iterations within a short period, speeding up the overall product development cycle.
Small Batch Production
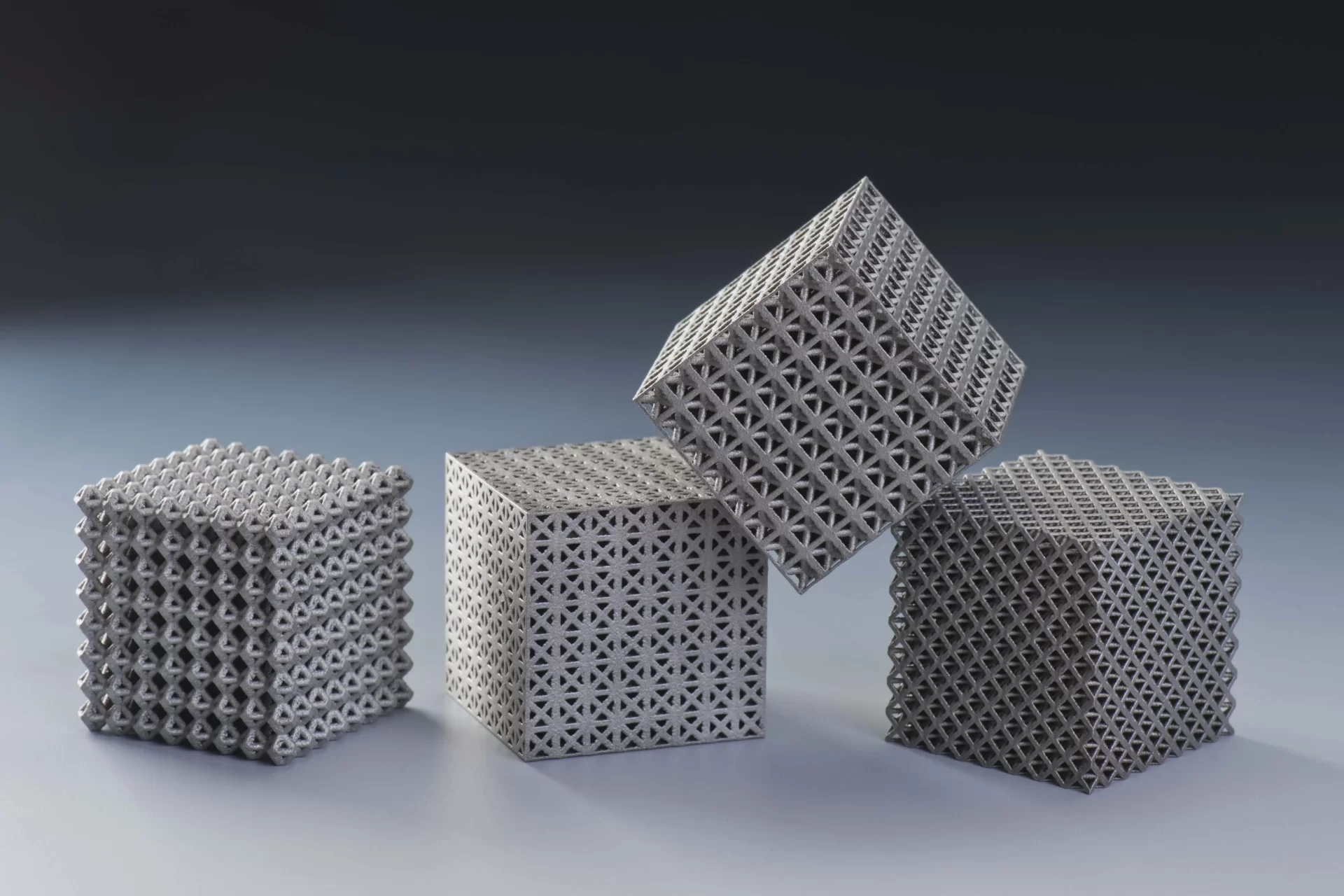
SLS 3D printing is highly efficient for small batch production, eliminating the need for costly tooling and molds.
- Low Volume Manufacturing: Ideal for producing small volumes of parts, reducing the cost and time associated with traditional manufacturing methods.
- Customization: Allows for the production of customized parts tailored to specific needs, making it ideal for niche markets and bespoke products.
Medical Field
Custom Implants
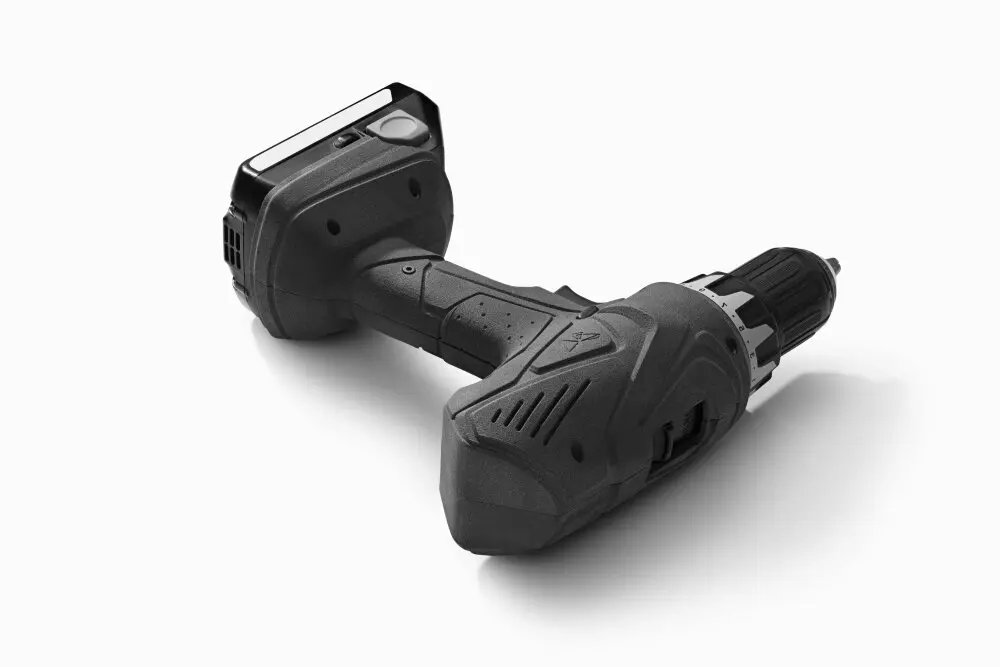
The medical field benefits significantly from the precision and customization capabilities of SLS 3D printing.
- Tailored Solutions: Custom implants can be designed to fit individual patients perfectly, improving comfort and outcomes.
- Complex Geometries: The ability to produce complex shapes allows for the creation of implants with intricate structures that would be challenging to achieve with traditional methods.
Orthopedic Devices
Orthopedic devices, such as braces and supports, are another area where SLS 3D printing excels.
- Personalized Fit: Devices can be customized to fit the patient’s anatomy precisely, enhancing comfort and effectiveness.
- Rapid Production: Quick production times ensure that patients receive their devices faster, improving their quality of life.
Automotive Sector
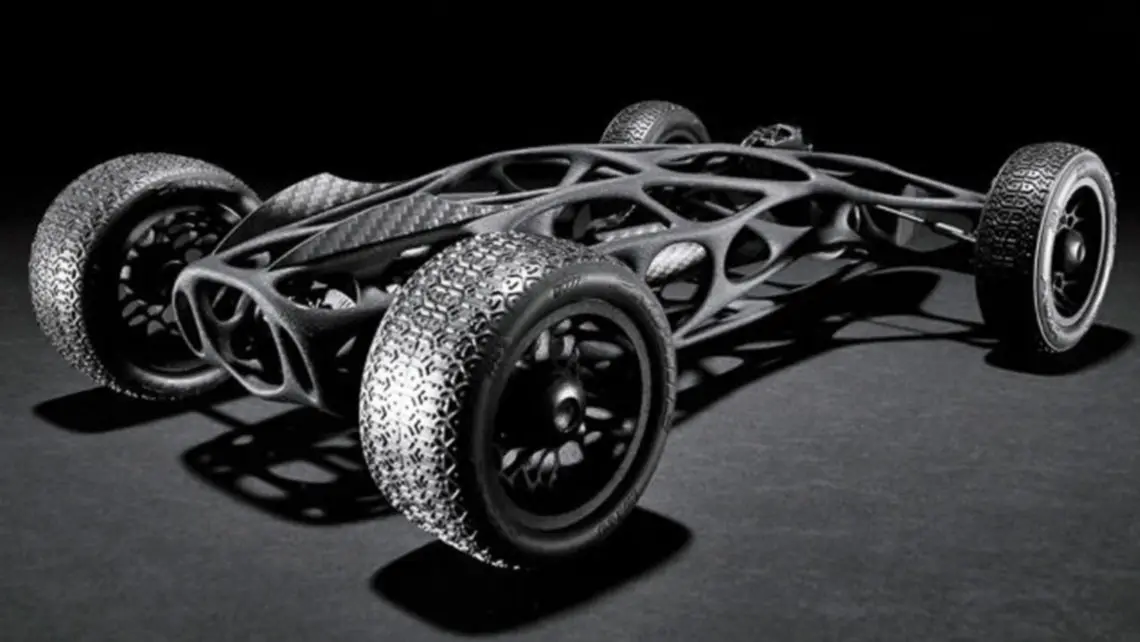
Lightweight Components
The automotive industry leverages SLS 3D printing to produce lightweight components that enhance vehicle performance and fuel efficiency.
- Weight Reduction: By using materials like Nylon and composites, manufacturers can create parts that are significantly lighter than traditional metal components.
- Performance Improvement: Lighter parts contribute to better fuel efficiency and overall vehicle performance.
Tooling and Fixtures
Custom tools and fixtures are essential for the manufacturing and assembly processes in the automotive sector.
- Custom Tooling: SLS 3D printing allows for the production of custom tools that fit specific production needs, improving efficiency and reducing downtime.
- Rapid Iteration: The ability to quickly create and iterate on tools helps manufacturers adapt to changes in the production process more swiftly.
The advantages of SLS 3D printing, including high efficiency, precision, and design flexibility, make it an invaluable tool in modern manufacturing. By leveraging these benefits, industries can innovate faster, reduce costs, and produce high-quality, customized products. Whether you’re in automotive, healthcare, or any other sector, SLS 3D printing offers the capabilities to meet your most demanding manufacturing needs.
Future Trends
The versatility of SLS 3D printing continues to drive innovation across various industries. Some emerging trends include:
- Increased Use of Composites: Enhanced material properties and performance.
- More Affordable Machines: Making SLS technology accessible to small and medium-sized enterprises.
- Advanced Customization: Further advancements in software and scanning technologies for even more precise customization.
Conclusion
The applications of SLS 3D printing are vast and varied, spanning industries from automotive to healthcare. Its ability to produce highly detailed, durable, and customized parts makes it an invaluable tool in modern manufacturing. As the technology continues to evolve, we can expect to see even more innovative applications and groundbreaking advancements that will further cement SLS 3D printing’s role in shaping the future of manufacturing.