Abstract
This paper delves into Selective Laser Sintering (SLS) 3D printing technology. It explores the scientific principles, recent technological breakthroughs, current industry trends, existing challenges, and future research directions. SLS, a significant additive manufacturing method, has the potential to transform multiple industries. By comprehensively analyzing various aspects of SLS, this study aims to provide a thorough understanding of the technology for professionals, researchers, and enthusiasts in the manufacturing field.
1. Introduction
In modern manufacturing, 3D printing has emerged as a revolutionary technology. Among additive manufacturing techniques, Selective Laser Sintering (SLS) stands out. It uses high – powered lasers to fuse powdered materials into solid objects layer by layer. Since its development in the 1980s, SLS has evolved significantly, with applications spanning from aerospace to healthcare. This paper will explore the science behind SLS, its recent breakthroughs, current trends, challenges, and future directions.
2. The Science of SLS 3D Printing
2.1 How SLS Operates
The SLS process involves several sequential steps. First, a thin layer of powdered material, which can be polymer, metal, or ceramic, is evenly spread across the build platform. This powder is carefully selected based on the desired properties of the final product. Second, a high – powered laser scans the powder bed surface. The laser selectively heats the powder particles, causing them to fuse and form a solid layer. After each laser pass, the build platform lowers slightly, and the process repeats for the next layer. Once the layer is formed, it cools and solidifies. The unsintered powder surrounding the part acts as a support structure, preventing warping and distortion. Finally, after the printing is complete, the build chamber is cooled, and excess powder is removed. The part may undergo post – processing steps such as sanding, painting, or finishing to achieve the desired surface quality.
A visual representation of the SLS process is presented in Table 1:
Step | Description |
1. Powder Layering | A thin layer of powder is spread across the platform. |
2. Laser Scanning | The laser selectively fuses the powder to create a solid layer. |
3. Layering | The platform lowers, and the process repeats for each layer. |
4. Cooling | The part cools and solidifies, supported by un – sintered powder. |
5. Post – Processing | Excess powder is removed, and the part is finished as needed. |
2.2 Materials Utilized in SLS
SLS is known for its material versatility. Polymer powders, such as Nylon (PA12, PA11), are widely used due to their durability and flexibility. They offer excellent mechanical properties and chemical resistance. Thermoplastic Polyurethane (TPU), a flexible material, is suitable for creating rubber – like parts, especially in applications requiring elasticity and impact resistance. Polypropylene (PP), valued for its lightweight nature and chemical resistance, finds applications in automotive and consumer goods.
Metal powders are also crucial in SLS. Stainless steel, with its strength and corrosion resistance, is used for functional prototypes and end – use parts. Aluminum powders, being lightweight and strong, are applied in aerospace and automotive sectors for weight – sensitive structures.
Ceramic powders, like Alumina and Zirconia, are used for high – temperature applications. They can be sintered to produce dense and strong components.
2.3 Key Components of an SLS Printer
The laser system is the core component of an SLS printer. It generates the energy required to sinter the powder, typically operating in the 10 – 100 – watt range. The build chamber is the enclosed space where printing occurs. Maintaining a controlled temperature in this chamber minimizes thermal stresses and ensures consistent results.
The powder handling system is responsible for evenly spreading the powder layer and managing excess powder after printing. An efficient cooling system is essential for proper layer solidification, preventing warping and dimensional inaccuracies. Advanced software is used to slice the 3D model into layers, control the laser path, and monitor the printing process in real – time.
3. Recent Breakthroughs in SLS Technology
3.1 Material Innovations
In the realm of polymers, new high – performance polymers like PA6 (Polyamide 6) and Polycarbonate (PC) have emerged. These polymers offer improved mechanical properties, heat resistance, and chemical stability, making them valuable for aerospace and automotive applications. Additionally, there is a growing trend towards sustainability, with the development of bio – based and recycled powders. These materials reduce the environmental impact of SLS printing.
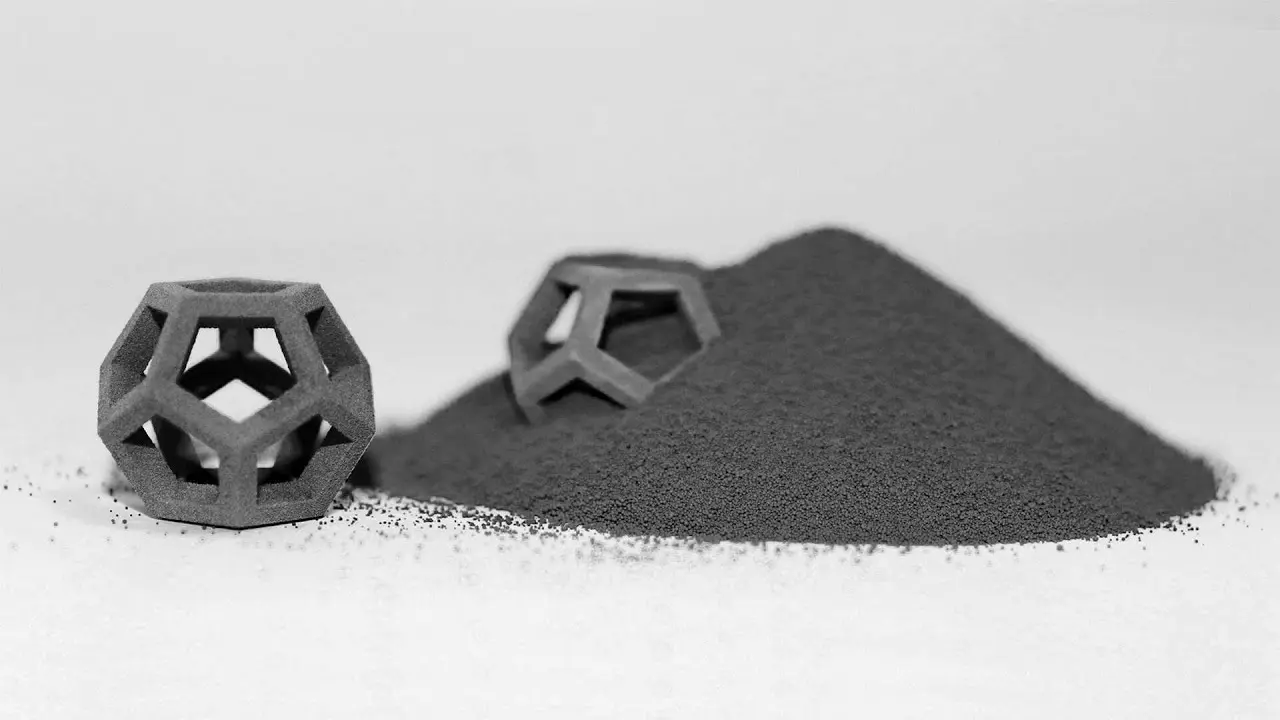
Regarding metal powders, innovative alloys designed specifically for SLS printing have expanded the possibilities. For example, Inconel 718, a nickel – chromium alloy, is increasingly used in aerospace due to its high strength and resistance to extreme temperatures.
Composite materials, especially carbon – fiber – reinforced powders, have enhanced the mechanical properties of printed parts. These composites offer a better strength – to – weight ratio, making them suitable for applications that require lightweight yet robust components.
3.2 Printer Technology Advancements
Modern SLS printers are equipped with higher – power lasers, reaching up to 400 watts. This increase in power boosts the sintering speed and allows for larger build volumes. Some advanced SLS systems now use multi – laser setups, with multiple lasers working simultaneously. This reduces print times and improves production efficiency.
Software solutions for SLS printers have also advanced. Smart slicing algorithms optimize the build process, reducing material waste and minimizing print failures. Real – time monitoring, enabled by advanced sensors and data analytics, allows for immediate adjustments during printing to maintain quality and precision.
Automation and integration are other significant trends. Automated powder handling systems streamline the workflow, making SLS more suitable for high – volume production. Moreover, many SLS printers are designed to integrate with Industry 4.0 environments, using IoT technologies for data collection and process optimization.
3.3 Case Studies
Boeing has utilized SLS technology to produce lightweight, complex parts for its aircraft. By using high – performance polymer powders, Boeing has reduced the weight of certain components by up to 50%, leading to fuel savings and improved efficiency.
Materialise developed customized surgical guides and implants using SLS technology. By leveraging patient – specific data, they can create tailored solutions that enhance surgical outcomes and improve patient recovery times.
Ford Motor Company implemented SLS for rapid prototyping of parts in its vehicle development process. This has led to faster design iterations and reduced time – to – market for new models, enhancing its competitive edge.
A summary of these breakthroughs is presented in Table 2:
Area of Innovation | Description | Impact on Industry |
Advanced Polymers | High – performance and bio – based materials | Expanded application range |
Metal Alloys | Novel alloys for complex geometries | Increased lightweight designs |
Composite Materials | Carbon – fiber – reinforced powders | Enhanced strength – to – weight ratios |
Laser Systems | Higher power and multi – laser capabilities | Reduced print times |
Smart Software | Optimized slicing and real – time monitoring | Improved quality and efficiency |
Automation | Automated powder handling and integration with IoT | Streamlined workflows |
4. Current Trends in SLS 3D Printing
4.1 Industry – Wide Adoption
In the aerospace industry, SLS is used for rapid prototyping of lightweight, complex parts. It is also increasingly being considered for end – use parts, especially in non – structural applications where weight savings are crucial.
Automakers are leveraging SLS for customization. They can produce custom parts for vehicles, enhancing personalization. SLS is also used for creating tooling, jigs, and fixtures, which improves manufacturing efficiency and reduces downtime.
In healthcare, SLS is revolutionizing the production of medical devices. Patient – specific implants and surgical guides can be created, improving surgical precision and patient outcomes. Rapid prototyping of medical devices also speeds up the time – to – market.
Consumer product brands are using SLS for low – volume production. This allows them to create unique items for niche markets without the high costs associated with traditional manufacturing methods. SLS’s design freedom enables the creation of intricate shapes that are not possible with conventional techniques.
4.2 Sustainability in SLS
Recycling of SLS powders is a significant sustainability initiative. Un – sintered powder can be reused, reducing waste and material costs. Companies are adopting closed – loop systems for efficient powder recycling.
The development of eco – friendly materials is another trend. Biodegradable polymers and materials derived from renewable resources are being researched and developed to minimize the environmental footprint of SLS production.
Advances in SLS technology are also leading to more energy – efficient printing processes. Manufacturers are focusing on reducing energy consumption during printing and post – processing, contributing to overall sustainability. A summary of these sustainability trends is shown in Table 3:
Sustainability Initiative | Description | Impact on Industry |
Powder Recycling | Reusing un – sintered powders to minimize waste | Reduced material costs and waste |
Eco – Friendly Materials | Development of biodegradable and renewable materials | Lower environmental footprint |
Energy Efficiency | Optimizing processes to reduce energy consumption | More sustainable manufacturing |
4.3 Integration with Industry 4.0
SLS printers are increasingly integrating IoT technologies. This allows for remote monitoring, management, and optimization of the printing process. Data analytics tools are used to collect and analyze data from SLS operations. This enables manufacturers to optimize workflows, predict maintenance needs, and enhance product quality.
Automation in SLS processes, from powder handling to post – processing, streamlines operations and reduces manual labor. This leads to increased efficiency and productivity. The ability to produce customized parts on – demand, a result of Industry 4.0 integration, allows companies to respond quickly to market demands, enabling a more agile manufacturing approach. A summary of Industry 4.0 trends is presented in Table 4:
Industry 4.0 Element | Description | Impact on Industry |
IoT Integration | Remote monitoring and management of SLS processes | Enhanced operational efficiency |
Data Analytics | Analyzing operational data for optimization | Improved product quality |
Automation | Streamlined processes through automation | Increased productivity |
5. Challenges Facing SLS 3D Printing
5.1 Technical Limitations
Most SLS printers have size limitations, restricting the dimensions of parts that can be produced. Larger systems, although available, are often cost – prohibitive for smaller manufacturers. The resolution of SLS prints is generally lower than that of some other 3D printing technologies, such as Stereolithography (SLA). The layer height in SLS can affect the surface finish and detail of the final product, resulting in a rough surface that may require additional post – processing.
Maintaining tight tolerances, especially for small or intricate parts, is challenging in SLS. Variability in the thermal behavior of powders during sintering can lead to dimensional inaccuracies. While the range of materials available for SLS is expanding, it still lags behind methods like Fused Deposition Modeling (FDM) in terms of variety. Some specialized applications may require materials not yet available for SLS. A summary of these technical challenges is presented in Table 5:
Technical Challenge | Description | Impact on Production |
Build Size Limitations | Restrictions on part dimensions | Limited application scope |
Surface Finish Issues | Rough surface textures requiring post – processing | Increased production time |
Dimensional Accuracy | Difficulty maintaining tight tolerances | Compromised part functionality |
Material Limitations | Fewer available materials compared to other methods | Constraints on design flexibility |
5.2 Economic Considerations
SLS printers are significantly more expensive than many other 3D printing systems. This high initial investment can deter small and medium – sized enterprises (SMEs) from adopting the technology. The operational costs of SLS, including material costs, maintenance, and the need for skilled labor, can be substantial. These costs impact the overall return on investment (ROI).
Although SLS is advantageous for low – volume production and customization, it may not be as cost – effective as traditional manufacturing methods, such as injection molding, for high – volume production. The price of high – quality SLS powders, despite powder recycling, can still be relatively high, affecting the economic viability of the process for certain applications. A summary of these economic challenges is shown in Table 6:
Economic Challenge | Description | Impact on Adoption |
High Initial Investment | Significant upfront costs for equipment | Deters SMEs from adopting SLS |
Operational Costs | Costs associated with materials and maintenance | Reduces potential ROI |
Cost – Effectiveness | May not compete with traditional methods for high – volume | Limits market share in some sectors |
5.3 Regulatory and Safety Concerns
In sectors like aerospace and healthcare, ensuring that SLS – produced parts meet industry standards is critical. However, the variability in printing processes can complicate compliance efforts. Parts often need to undergo rigorous testing and certification, which is time – consuming and costly, potentially delaying the launch of new products.
The handling of fine powders in SLS poses inhalation hazards. Manufacturers must invest in proper ventilation systems and provide personal protective equipment (PPE) to ensure worker safety. In metal SLS, the use of highly flammable powders raises concerns about fire risks during both printing and post – processing. A summary of these regulatory and safety challenges is presented in Table 7:
Regulatory/Safety Challenge | Description | Impact on Operations |
Compliance Issues | Ensuring parts meet industry standards | Lengthens certification processes |
Health Risks | Handling fine powders poses inhalation hazards | Requires investment in safety measures |
Fire Hazards | Flammable materials increase fire risk | Necessitates stringent safety protocols |
6. Future Directions in SLS Research and Development
6.1 Technology Advancements
Research is ongoing to develop new materials for SLS. High – performance polymers, metal alloys, and composites with superior properties are expected to be developed, expanding the application scope of SLS. Smart materials that can change properties in response to environmental stimuli, such as temperature or light, will also be integrated into SLS – printed parts, enhancing their functional capabilities.
Innovations in laser technology, including higher – power and multi – laser systems, are likely to reduce printing times, making SLS more competitive with traditional manufacturing. Automated post – processing systems for cleaning, curing, and finishing are expected to be developed, further streamlining the workflow.
Artificial intelligence (AI) and machine learning will be increasingly used to optimize the SLS process. AI – powered optimization will cover aspects such as material selection, part design, and real – time monitoring and adjustment during printing. Enhanced simulation tools will help identify potential issues before printing, minimizing failures and optimizing build parameters. A summary of these future predictions is presented in Table 8:
Area of Advancement | Description | Anticipated Impact |
Material Development | New high – performance and smart materials | Broadened application scope |
Process Efficiency | Faster printing speeds and automated post – processing | Increased competitiveness |
Software Solutions | AI – powered optimization and enhanced simulation tools | Improved quality and reduced failures |
6.2 New Applications
In the consumer goods sector, SLS will be used for personalized products, such as jewelry and footwear. This customization on demand will enhance customer satisfaction.
The development of biocompatible materials for SLS may open up opportunities in bioprinting. Tissue scaffolds and custom implants tailored to individual patients could be created, improving medical outcomes.
As aerospace and defense industries continue to seek lightweight and complex components, SLS will likely be used to produce parts that meet strict performance and safety standards, optimizing performance and safety.
In architecture, SLS technology can revolutionize the rapid prototyping of intricate building models. This will facilitate better visualization and presentation for clients. A summary of these emerging applications is shown in Table 9:
Application Area | Description | Potential Benefits |
Consumer Goods | Customization of products for individual preferences | Enhanced customer satisfaction |
Bioprinting | Creation of tissue scaffolds and implants | Improved medical outcomes |
Aerospace and Defense | Production of lightweight, complex components | Optimized performance and safety |
Architectural Models | Rapid prototyping of intricate designs | Better client visualization |
6.3 The Role of Collaboration
Partnerships between academia and industry are crucial for driving innovation. Joint research initiatives can combine theoretical research with practical applications, ensuring that new developments are relevant and market – ready.
Open – source projects in SLS can foster community engagement and encourage the sharing of best practices, materials, and software solutions. This knowledge sharing will accelerate technological progress.
Cross – industry collaboration, for example, between healthcare, aerospace, and consumer products industries, can lead to innovative applications of SLS technology. Interdisciplinary approaches can solve complex challenges by leveraging insights from different fields. A summary of these collaborative strategies is presented in Table 10:
Collaboration Strategy | Description | Expected Outcomes |
Academia – Industry Partnerships | Joint research initiatives to drive innovation | Relevant, market – ready solutions |
Open – Source Projects | Community engagement and knowledge sharing | Accelerated technological progress |
Cross – Industry Collaboration | Interdisciplinary approaches to tackle challenges | Innovative applications and solutions |
7. Conclusion
SLS 3D printing has emerged as a transformative technology in additive manufacturing. Understanding its scientific principles, recent breakthroughs, current trends, challenges, and future directions is essential for stakeholders in the manufacturing industry.
The technology’s ability to produce complex geometries, along with recent material and printer – technology innovations, has expanded its applications across multiple industries. However, challenges such as technical limitations, economic considerations, and regulatory and safety concerns need to be addressed for broader adoption.
Future research and development in SLS are expected to focus on material advancements, process efficiency improvements, and new applications. Collaboration between academia, industry, and open – source communities will play a vital role in driving innovation and overcoming existing challenges. As SLS continues to evolve, it has the potential to revolutionize manufacturing through enhanced customization, efficiency, and sustainability.