In the fast-paced world of innovation, where ideas transform into tangible products at breakneck speeds, every second counts. Imagine holding the future in your hands – a groundbreaking prototype that could redefine industries – within days instead of months. This is the promise of Selective Laser SLSintering (SLS) 3D printing, a technology that has transcended the realm of imagination and become a cornerstone of modern product development.
SLS stands at the forefront of the additive manufacturing revolution, harnessing the power of lasers to fuse powdered materials into intricate, functional prototypes. More than just a buzzword, it’s a catalyst for change, empowering designers and engineers to iterate faster, push boundaries, and bring their visions to life swiftly and efficiently. As traditional prototyping methods struggle to keep pace with the demands of a rapidly evolving marketplace, SLS emerges as the answer to a critical question: How can we accelerate product development without sacrificing quality or creativity?
This comprehensive guide dissects the intricacies of SLS 3D printing, exploring its mechanisms, advantages, and real-world applications across various industries. We’ll delve into why this technology is a game-changer for rapid prototyping, discussing its potential to cut lead times, enhance design complexity, and streamline costs. From aerospace to medical devices, automotive to consumer electronics, SLS is reshaping how we approach innovation, one layer at a time.
The Benefits of SLS 3D Printing for Prototyping
Faster Time to Market
One of the most significant advantages of SLS 3D printing in prototyping is the drastic reduction in time it takes to go from design to physical model. Traditional methods often involve lengthy lead times for tooling and production, which can delay the product development process by months or even years. SLS 3D printing, on the other hand, allows for rapid prototyping, with some models being produced in a matter of hours or days. This speed enables companies to iterate on designs quickly, test products sooner, and bring new ideas to market faster than ever before.
Design Flexibility and Complexity
SLS 3D printing technology excels at producing parts with complex geometries that are challenging or impossible to create with traditional manufacturing methods. This level of design freedom allows designers to explore innovative shapes, structures, and functionalities that were once the realm of science fiction. The ability to print intricate internal structures, moving parts, and conformal cooling channels opens up a world of possibilities for product development.
Cost-Effectiveness in the Manufacturing Process
The cost savings associated with SLS 3D printing are substantial. By eliminating the need for expensive tooling and reducing material waste, companies can significantly reduce their upfront costs. Additionally, the on-demand nature of 3D printing means that only the necessary number of prototypes need to be produced, further reducing costs. This makes SLS 3D printing an attractive option for startups and small businesses looking to bring new products to market without the financial burden of traditional manufacturing.
Durability and Strength of SLS Printed Parts
The parts produced by SLS 3D printing are known for their durability and strength, thanks to the high-quality materials used and the precise nature of the printing process. This is particularly important in industries where prototypes must withstand rigorous testing, such as in the aerospace, automotive, and medical device sectors. The ability to create strong and reliable prototypes ensures that products are not only designed well but also built to last.
Customization and Personalization Options
SLS 3D printing allows for a level of customization that is unparalleled in traditional manufacturing. With 3D printing, each prototype can be tailored to specific needs and requirements, making it possible to create personalized solutions for individual customers or specific use cases. This flexibility is a game-changer for industries that require bespoke designs, such as in the medical and dental fields.
Environmental Sustainability
In an era where sustainability is paramount, SLS 3D printing stands out as a more environmentally friendly option. By reducing waste and energy consumption, 3D printing can help companies reduce their carbon footprint. The ability to print only what is needed, when it is needed, eliminates the need for storing and transporting large quantities of materials, further contributing to a more sustainable manufacturing process.
SLS 3D printing has revolutionized the prototyping process, offering a multitude of benefits that traditional manufacturing simply cannot match. From faster time to market and design flexibility to cost-effectiveness and environmental sustainability, SLS 3D printing has become an indispensable tool for companies looking to innovate and stay ahead in today’s competitive marketplace. As technology continues to evolve, the possibilities for SLS 3D printing in prototyping are endless, paving the way for a future where products are developed with unprecedented speed, precision, and creativity.
The SLS 3D Printing Process
Step-by-Step Guide to SLS Printing
The SLS 3D printing process is a marvel of precision and technology. Here’s a simplified overview of how it works:
- Material Preparation: The first step is to prepare the printing material, which is typically a fine powder made from nylon, polyamide, or other high-performance materials. The powder is spread evenly across the build platform.
- Laser Sintering: A high-powered laser then scans the cross-section of the part to be printed, as specified by the CAD file. The laser melts and fuses the powder in the desired areas, layer by layer.
- Layer by Layer: Once the first layer is complete, the build platform lowers, and a new layer of powder is spread evenly across the surface. The laser then re-fuses the powder in the areas corresponding to the next layer of the part. This process continues until the entire part is built.
- Post-Processing: After the printing process is complete, the part is still surrounded by loose powder. The excess powder is removed, and the part may undergo various post-processing steps to achieve the desired surface finish and mechanical properties. This can include cleaning, curing, painting, or coating.
Material Selection for SLS Printing
SLS 3D printing offers a range of materials that cater to various applications and design requirements. Some of the most common materials used include:
Material | Properties | Applications |
Nylon (PA) | Durable, flexible, good chemical resistance | Functional prototypes, end-use parts |
TPU | Elastic, abrasion-resistant | Flexible hinges, seals, wearables |
Alumide | Combination of nylon and aluminum | Mechanical parts requiring stiffness |
Metal Powders (e.g., Stainless Steel, Titanium) | High strength, heat resistance | Aerospace, automotive, medical implants |
Pre-Processing Requirements for SLS Printing
Before an SLS 3D printer can create a physical object from a digital design, several pre-processing steps are necessary:
- CAD Model Preparation: The digital design of the part must be created in a CAD program and then sliced into layers, which the printer will use as a blueprint for building the part.
- Support Structure Creation: For complex designs, support structures may need to be added to the model to ensure that the part is built correctly and without deformation.
- Material Selection and Preparation: The appropriate material for the application must be chosen, and the powder must be spread evenly across the build platform.
- Print Settings Configuration: The printer’s settings, such as laser power, scan speed, and layer thickness, must be optimized to ensure the best quality print.
The Role of CAD in SLS Printing
Computer-Aided Design (CAD) software is the cornerstone of the SLS 3D printing process. It allows designers to create complex geometries and intricate details that can be directly translated into a 3D printable file. CAD software is used to:
- Design the Part: Designers can create parts with complex internal structures, undercuts, and thin walls that are challenging or impossible to achieve with traditional manufacturing methods.
- Prepare the Model for Printing: CAD software includes tools for preparing models for 3D printing, such as adding support structures and ensuring the model fits within the build volume of the printer.
- Generate Print Files: The software can slice the model into layers, creating a set of instructions that the 3D printer will follow to build the part layer by layer.
The integration of CAD with SLS 3D printing technology enables designers to bring their most ambitious concepts to life, revolutionizing the way products are developed and manufactured.
Applications of SLS 3D Printing in Different Industries
The versatility of SLS 3D printing technology has made it a game-changer across a wide array of industries. From the early days of rapid prototyping to its current role in producing end-use parts, SLS has proven its worth in numerous applications. This section will explore how SLS 3D printing is transforming industries such as aerospace, automotive, healthcare, and consumer goods.
Aerospace and Defense
In the aerospace industry, where weight reduction and performance are critical, SLS 3D printing has become a valuable tool. Complex parts such as engine components, airframe parts, and even entire aircraft structures can be printed with SLS, offering improved strength-to-weight ratios and reduced production costs. The ability to produce parts with intricate internal structures and conformal cooling channels has led to significant advancements in aircraft design and performance.
Automotive Manufacturing
Automotive manufacturers are leveraging SLS 3D printing to accelerate the design and development of new vehicles. From concept models and tooling to final production parts, SLS allows for rapid prototyping and customization. The technology is used to create everything from dashboard components and door handles to complex engine parts, enabling automakers to iterate quickly and bring innovative designs to market faster.
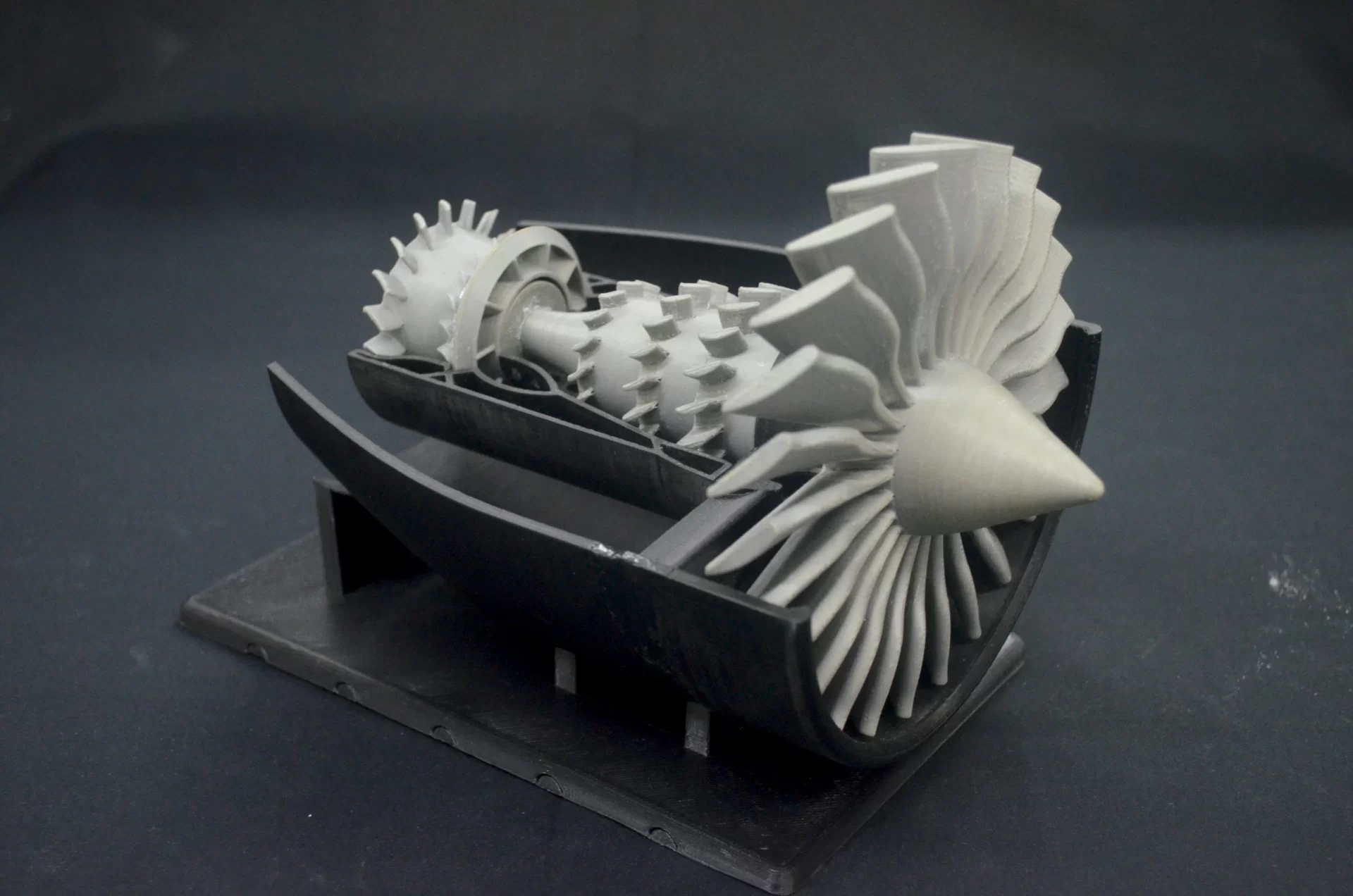
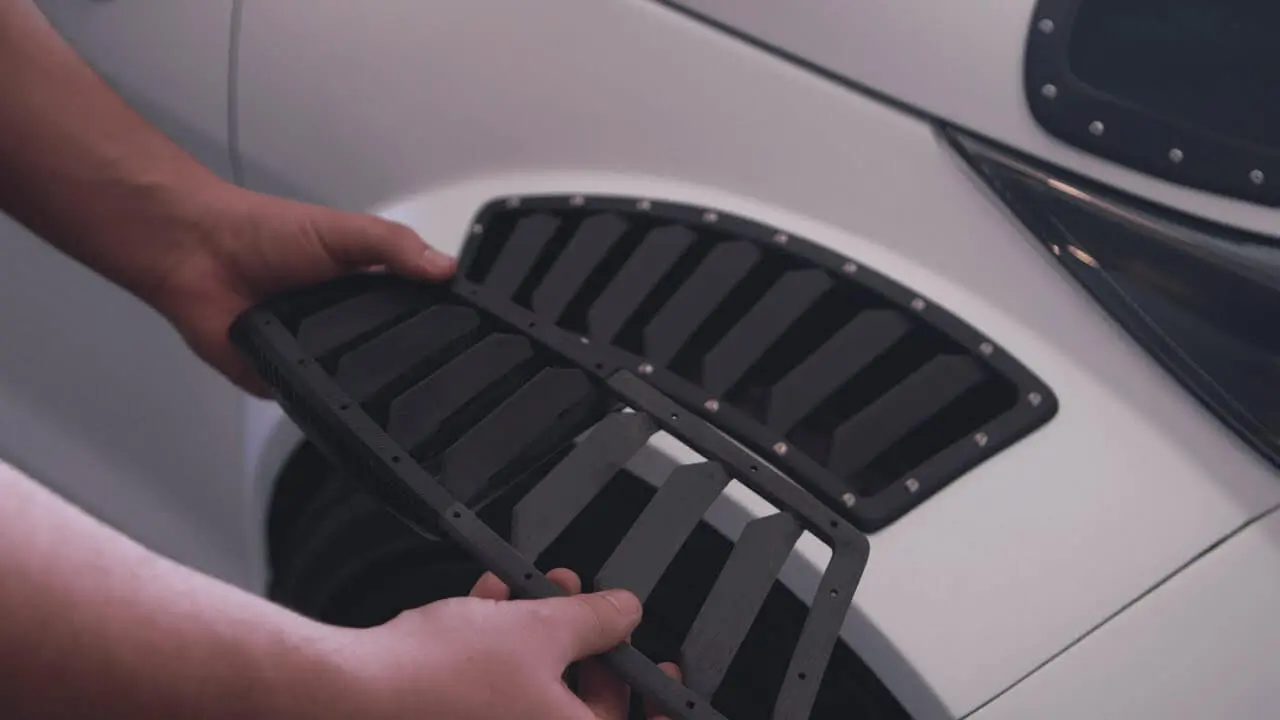
Healthcare and Medical Devices
SLS 3D printing is revolutionizing the healthcare industry by allowing for the creation of patient-specific implants, prosthetics, and surgical tools. Medical devices such as custom-fit hearing aids and dental crowns can be produced with a high degree of accuracy and comfort, thanks to the design flexibility offered by SLS. The technology also enables the production of anatomical models for surgical planning, which can improve outcomes and reduce costs.
Consumer Goods and Electronics
SLS 3D printing is being used to create innovative consumer products with complex geometries and intricate designs. The technology is ideal for producing small batches of consumer goods, such as sporting goods, jewelry, and fashion accessories, with a high degree of customization. In the electronics industry, SLS is used to print functional prototypes of circuit boards and electronic enclosures, reducing the time and cost associated with product development.
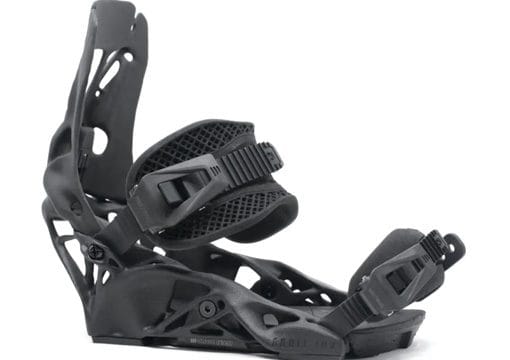
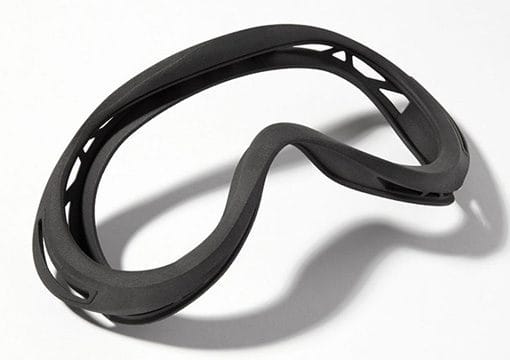
Education and Research
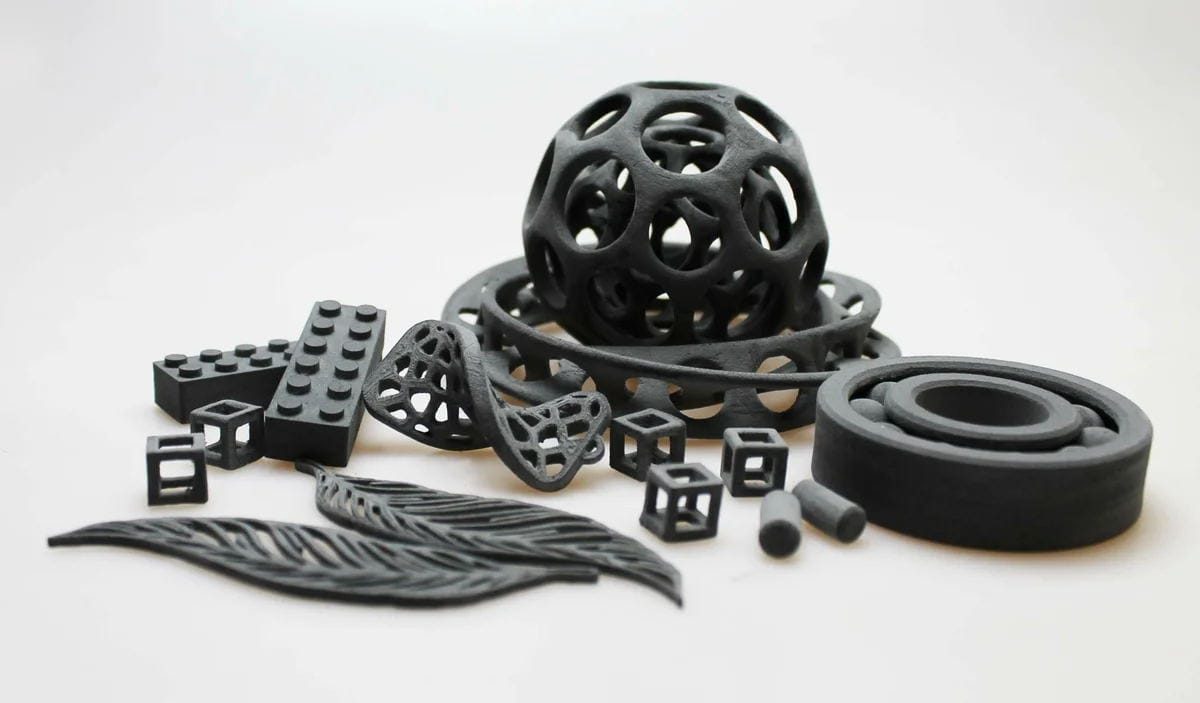
SLS 3D printing is a valuable tool in educational settings, allowing students to learn about engineering and design principles through hands-on experience with 3D printed models. In research, SLS enables the creation of complex structures and parts for scientific experiments, helping to advance knowledge across various disciplines.
SLS 3D printing has become an indispensable technology for industries seeking to innovate, reduce costs, and speed up production. Its ability to create complex parts with high precision and durability has opened up new possibilities for product development. As technology continues to evolve, the applications of SLS 3D printing will likely expand into new sectors, further revolutionizing the way we design and manufacture products.
Challenges and Considerations in Embracing SLS 3D Printing
While SLS 3D printing presents a horizon of opportunities, it’s essential to acknowledge the challenges and considerations accompanying this technology. Addressing these head-on ensures a smoother adoption process and optimized outcomes.
Overcoming Technical Hurdles
Post-Processing Puzzles
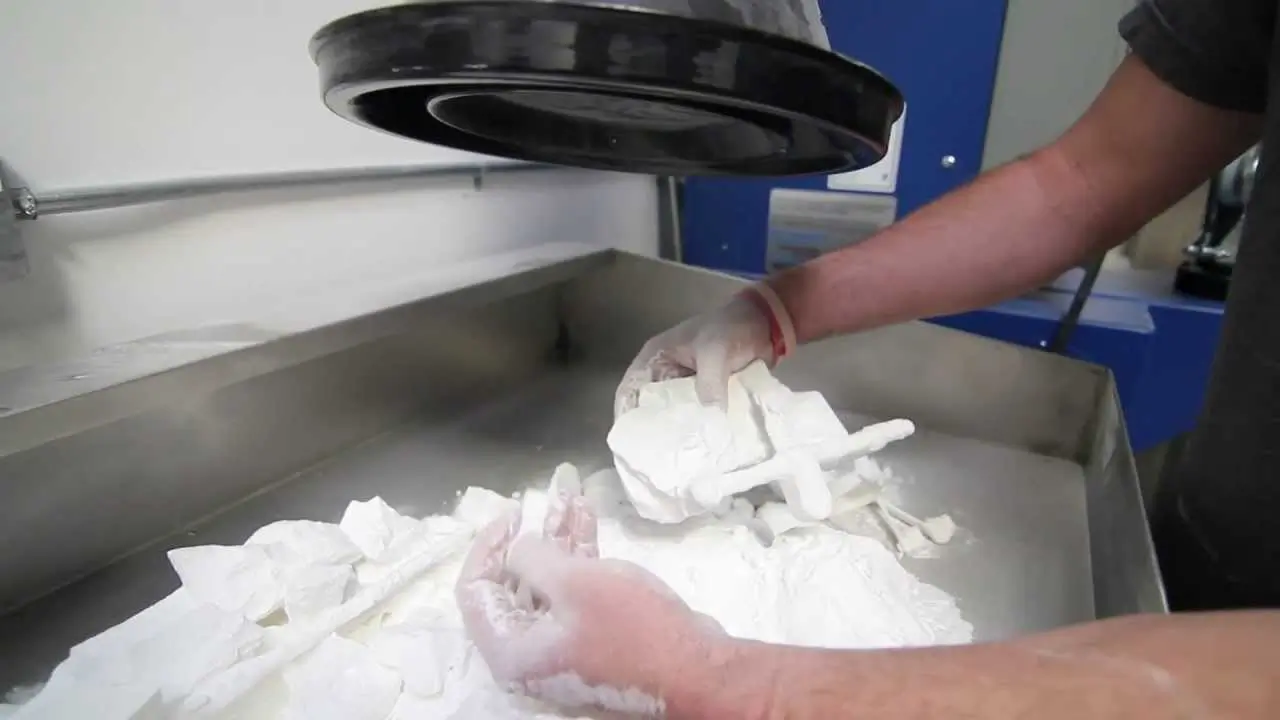
- Cleaning and Finishing: Removing excess powder post-printing can be labor-intensive and requires specialized equipment.
- Surface Quality: Additional steps like sanding, coating, or painting may be necessary to achieve desired aesthetics.
Design for Additive Manufacturing (DfAM) Learning Curve
- Optimizing Designs: Understanding how to design for SLS’s strengths, such as incorporating lightweight structures, can require new skills and training.
Economic Factors
Initial Investment
- High-Cost Entry: SLS machines and setup costs can be substantial, especially for high-end industrial systems, posing a barrier for smaller companies or startups.
Material Expenses
- Specialty Materials: While SLS supports a wide array of materials, some high-performance options come at a premium price.
Access and Expertise
Skilled Operators and Engineers
- Technical Know-How: Efficient operation and maintenance of SLS systems require trained personnel, which may be scarce.
Service Bureau Dependence
- Outsourcing Decisions: Businesses without in-house capabilities might rely on service bureaus, impacting control, turnaround time, and intellectual property concerns.
Environmental Sustainability
Material Waste and Recycling
- Unused Powder: While unused powder can be recycled, managing this process efficiently and ensuring material integrity is crucial.
Energy Consumption
- Printing and Cooling: SLS machines consume considerable energy during operation and require cooling systems, contributing to environmental impact.
Mitigation Strategies and Best Practices
Embracing DfAM Education
- Training Programs: Invest in employee training on DfAM principles to unlock SLS’s full potential and minimize material waste.
Smart Outsourcing
- Selecting Service Bureaus: Choose partners with a proven track record in handling sensitive projects and offering consultation for design optimization.
Sustainable Material Management
- Closed-Loop Systems: Implement systems for efficient powder handling and recycling, ensuring minimal waste and maintaining material quality.
Energy-Efficient Operations
- Efficient Machinery: Opt for energy-efficient SLS machines and implement cooling systems that minimize environmental footprint.
Long-Term Vision
- ROI Analysis: Conduct a thorough cost-benefit analysis considering long-term savings from reduced lead times, design flexibility, and potential for innovation.
Continuous Evolution
It’s important to note that the SLS landscape is continually advancing. Technological improvements and innovations are addressing many of these challenges. For instance, advancements in machine automation aim to simplify post-processing, while material science breakthroughs are expanding the range of more affordable and eco-friendly options.
Conclusion
Embracing SLS 3D printing involves acknowledging its challenges but also recognizing the vast potential for transformation. By strategizing around these considerations—enhancing design know-how, making informed investment decisions, securing skilled resources, and adopting sustainable practices—companies can harness SLS’s power to leapfrog competitors and redefine what’s possible in product development. As the technology matures and evolves, so too will the solutions to these challenges, paving the way for a future where SLS plays an even more integral role in accelerating innovation sustainably and efficiently.
Harnessing the Power: Selecting SLS Equipment and Service Providers
With a firm grasp on SLS’s potential and challenges, the next step is identifying the right equipment or service provider to propel your product development ventures. Making informed choices is crucial to maximizing SLS’s benefits.
Criteria for Selecting an SLS Printer
Build Volume
- Project Scope: Assess your typical project sizes to determine the required build volume. Larger volumes accommodate bigger parts or simultaneous printing of multiple smaller ones.
Laser Power and Accuracy
- Resolution & Detail: Higher laser power allows for faster sintering and can handle denser materials, while precision is key for intricate designs and fine features.
Material Compatibility
- Versatility: Ensure the printer supports a broad range of materials relevant to your industry, from nylon and TPU to specialized metals.
User Friendliness
- Software Integration: Seamless CAD/CAM compatibility and user-friendly interfaces speed up the design-to-print process.
Maintenance and Support
- Longevity & Assistance: Opt for manufacturers with reliable customer support and readily available replacement parts for uninterrupted operations.
Notable SLS Printers Comparison
Printer Model | Build Volume (mm^3) | Laser Type | Material Options | Price Range (Est.) |
Zongheng3D SLS-2030 | 200 x 200 x 300 | Fiber Laser | Nylon, PA 11,12 | $30,000 |
Formlabs Fuse 1 | 165 x 165 x 300 | Diode Lasers | Nylon, PA 12 | $10,000 – $20,000 |
EOS P 396 | 340 x 340 x 600 | CO2 | Wide range incl. metals | $>250,000 |
3D Systems ProX SLS 6100 | 381 x 330 x 460 | CO2 | Nylon, TPU, others | $>400,000 |
Entry-Level vs. Industrial-Grade
Evaluate your needs carefully. Entry-level printers are cost-effective for prototyping and small-scale production, while industrial machines offer larger build volumes, advanced materials, and higher throughput for demanding applications.
Collaborating with SLS Service Bureaus
Factors to Consider
- Expertise: Look for providers with a deep understanding of SLS and experience in your specific industry.
- Quality Assurance: Ensure they have rigorous QA processes in place, including material certification and ISO compliance.
- Turnaround Time: Fast turnaround is crucial; inquire about their typical lead times and rush order options.
- IP Protection: Verify their policies on data security and non-disclosure agreements (NDAs).
- Consultative Approach: Providers who offer design assistance and material recommendations can add significant value.
Vetting Process
- Request Samples: Evaluate sample prints to assess quality and consistency.
- Client References: Speak with past clients to gauge service levels and reliability.
- Pricing Transparency: Obtain detailed quotes, comparing costs per part and any additional fees (e.g., setup, design consultation).
Leading SLS Service Providers Snapshot
Service Provider | Specialties | Industries Served | Notable Features |
Shapeways | Complex geometries, large-scale production | Consumer goods, automotive | Extensive material library, design optimization services |
3D Hubs | Rapid prototyping, small batch production | Various | Global network, instant online quoting |
Protolabs | Quick turnaround, DfAM support | Medical, aerospace | In-depth design analysis, multiple manufacturing technologies |
Final Thoughts
Selecting the right SLS equipment or service provider is a strategic decision that can significantly influence your product development success. Whether investing in an in-house printer or partnering with a trusted service bureau, prioritize your specific requirements, balancing capabilities, cost-effectiveness, and long-term goals. As SLS technology continues to advance, staying abreast of the latest developments and best practices will ensure you harness its full potential, propelling your innovations forward with speed, precision, and a competitive edge.