With the dizzying world of 3D printing, between SLS and FDM, one can either make or mar a project. Whether you are a hobbyist or a professional engineer or a business person who is considering integrating 3D printing into their processes, it is important to know how each of these two popular methods stands in terms of their advantages and disadvantages. This ultimate face-off will take a detailed look at SLS and FDM-in doing so, it should empower its users into making a balanced choice for their next 3D printing project.
Standing in front of the junction-like crossroads of different technologies in 3D printing, with one selection being SLS and another as FDM, you now have to determine which road to take. SLS guarantees high precision and durability but is a costly affair. On the other hand, FDM is inexpensive as well as versatile but may not give you the detail and strength.
In this blog post, the basic principles of SLS and FDM will be elucidated-a detailed split of the pros and cons in deliberation of the face-off shall follow. By the end of the post, it will be quite clear which technology fits your purposes, be they prototyping, manufacturing, or creative in nature. Download and unleash the truth hidden between these two formidable-drying methods!
Understanding SLS 3D Printing
Selective Laser Sintering (SLS) is the cutting-edge 3D printing technology, which revolutionized the way we think about manufacturing. From seasoned engineers to curious hobbyists, learning about the nitty-gritty of SLS is sure to give an edge to the respective person in any of his projects. So let us go down the rabbit hole of what makes SLS special and discuss advantages, disadvantages, and everything in between.
What is SLS 3D Printing?
The SLS is an additive manufacturing process that employs a high-powered laser to fuse powdered materials, layer by layer, into a solid 3D object. This method belongs to the family of powder bed fusion 3D printing technologies and is characterized by great detailing and the structural integrity of parts.
How SLS Works
- Powder Bed Preparation: The process begins with a thin layer of powdered material spread evenly across the build platform.
- Laser Sintering: A high-powered laser selectively fuses the powder particles together based on the 3D model’s cross-section.
- Layer-by-Layer Building: The build platform lowers slightly, and a new layer of powder is spread over the previous layer. The laser then fuses the next cross-section.
- Repeat: This process repeats until the entire object is complete.
- Cooling and Removal: Once printing is finished, the object is allowed to cool before being removed from the powder bed.
Materials Used in SLS
SLS is versatile in terms of materials, but it primarily uses powdered substances. Here are some of the most common materials:
- Nylon (Polyamide): Known for its strength and flexibility, nylon is the most commonly used material in SLS.
- Polyamide 12 (PA 12): A type of nylon that offers excellent mechanical properties and is widely used in industrial applications.
- Polyamide 11 (PA 11): Derived from renewable resources, PA 11 is known for its impact resistance and flexibility.
- Specialty Materials: Includes materials like polypropylene, TPU (thermoplastic polyurethane), and even metals in some advanced SLS systems.
Advantages of SLS 3D Printing
SLS offers a range of benefits that make it a popular choice for various applications:
- High Precision and Detail: SLS can produce parts with intricate details and high precision, making it ideal for complex geometries.
- Strong and Durable Parts: The layer-by-layer fusion process results in strong, isotropic parts that are uniform in all directions.
- No Need for Support Structures: Unlike some other 3D printing methods, SLS does not require support structures, as the unfused powder acts as a support.
- Batch Production: SLS allows for the printing of multiple parts in a single build, making it efficient for small-batch production.
Disadvantages of SLS 3D Printing
While SLS has many advantages, it also comes with some drawbacks:
- Higher Cost: Both the initial investment in SLS printers and the operational costs are higher compared to other 3D printing methods.
- Limited Material Options: SLS is primarily limited to powdered materials, which may not be suitable for all applications.
- Post-Processing Requirements: Parts often require post-processing steps such as cleaning, polishing, and sometimes additional treatments to achieve the desired finish.
Applications of SLS 3D Printing
SLS is used across various industries for a wide range of applications:
- Aerospace: Production of lightweight, high-strength components.
- Automotive: Manufacturing of prototypes and functional parts.
- Medical: Creation of custom implants and surgical tools.
- Consumer Goods: Production of durable, detailed consumer products.
Comparison of SLS Materials
Material | Strength | Flexibility | Impact Resistance | Common Applications |
Nylon (PA 12) | High | Moderate | High | Industrial parts, prototypes |
PA 11 | Moderate | High | High | Flexible parts, consumer goods |
Polypropylene | Moderate | High | Moderate | Medical devices, consumer goods |
TPU | Low | Very High | High | Flexible parts, wearables |
Selective Laser Sintering (SLS) is a powerful 3D printing technology that facilitates the manufacturing of objects with high precision, good mechanical strength,and natural complex geometries. Its disadvantages include higher costs and limited material options; however, their contributions make them valuable accessories for different sectors. Whether it is prototyping or manufacturing, whether innovation is the goal, using an SLS system could really open the door to what you can achieve with your projects.
Understanding FDM 3D Printing
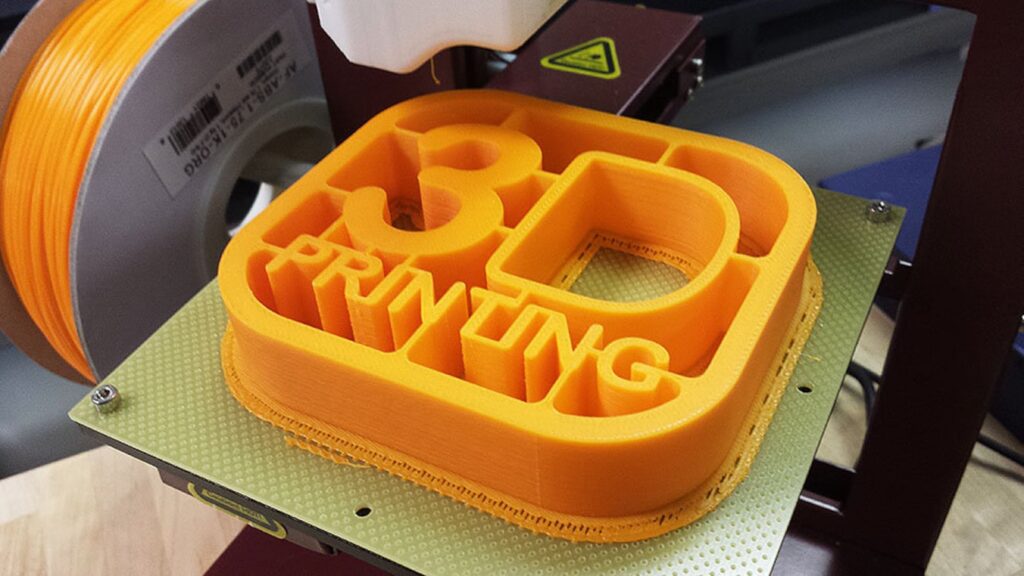
Fused Deposition Modeling (FDM), or Fused Filament Fabrication (FFF), is a widely accepted and easily available mean of 3D printing technology in this epoch. For a novice in 3D printing or an experienced maker wanting to mature on to much larger things, understanding FDM is critical. Let’s take you through the basics of FDM, what advantages it has and what it does not, as well as the variety of materials and uses it has.
What is FDM 3D Printing?
Fused deposition modeling is a technique of additive manufacturing that extrudes plastic filaments, built-in layers as a 3D object. The process is rather easy, quite cheap, and widely versatile, thus preferred by hobbyists, educators, and professionals alike.
How FDM Works
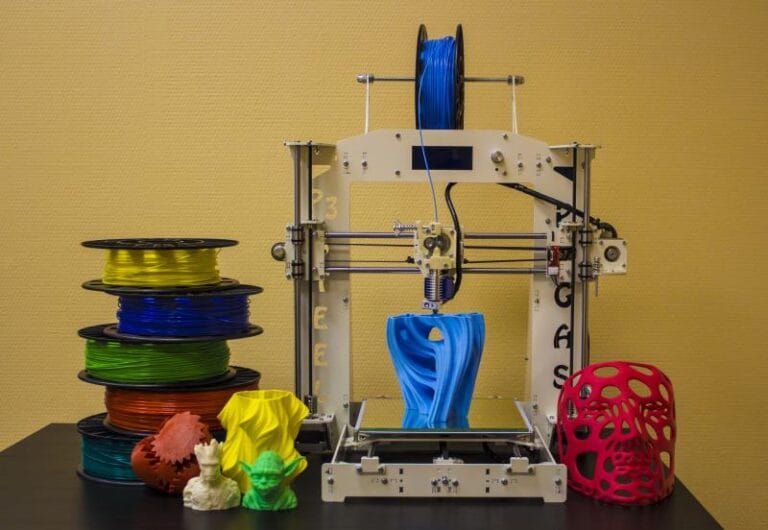
- Filament Feeding: The process begins with a spool of thermoplastic filament, which is fed into the printer’s extruder.
- Extrusion: The extruder heats the filament to its melting point and pushes it through a nozzle, depositing the molten material onto the build platform.
- Layer-by-Layer Building: The build platform or the extruder moves in the X, Y, and Z axes to deposit the material layer by layer, following the 3D model’s cross-sections.
- Support Structures: For complex geometries with overhangs, support structures are often printed simultaneously and later removed.
- Cooling and Solidification: As the material is extruded, it cools and solidifies, forming the final object.
Materials Used in FDM
One of the standout features of FDM is the wide range of materials it supports. Here are some of the most common filaments used in FDM:
- PLA (Polylactic Acid): A biodegradable and easy-to-print material, ideal for beginners and prototyping.
- ABS (Acrylonitrile Butadiene Styrene): Known for its strength and heat resistance, commonly used in industrial applications.
- PETG (Polyethylene Terephthalate Glycol): A durable and food-safe material with excellent layer adhesion.
- TPU (Thermoplastic Polyurethane): A flexible and impact-resistant material, perfect for functional parts and wearables.
- Specialty Materials: Includes materials like nylon, polycarbonate, and even metal-infused filaments for specialized applications.
Advantages of FDM 3D Printing
FDM offers several benefits that make it a popular choice for various applications:
- Cost-Effective: FDM printers and filaments are generally more affordable compared to other 3D printing technologies.
- Wide Range of Materials: FDM supports a vast array of thermoplastic materials, offering versatility for different projects.
- Ease of Use: FDM printers are user-friendly, making them accessible for beginners and hobbyists.
- Accessibility: FDM printers are widely available, with numerous options for DIY kits, pre-assembled machines, and even large-scale industrial printers.
Disadvantages of FDM 3D Printing
While FDM has many advantages, it also comes with some drawbacks:
- Lower Precision and Detail: FDM prints often have visible layer lines and may not achieve the same level of detail as other methods.
- Weaker Layer Adhesion: The layer-by-layer extrusion process can result in weaker points between layers, affecting the overall strength of the part.
- Need for Support Structures: Complex geometries with overhangs require support structures, which need to be removed post-printing.
- Warping and Shrinkage: Some materials, like ABS, are prone to warping and shrinkage, which can affect print quality.
Applications of FDM 3D Printing
FDM is used across various industries for a wide range of applications:
- Education: Teaching students about 3D printing and prototyping.
- Hobbyist Projects: Creating custom parts, models, and functional objects.
- Prototyping: Developing and testing product designs before mass production.
- Manufacturing: Producing end-use parts, jigs, and fixtures.
Comparison of FDM Materials
Material | Strength | Flexibility | Heat Resistance | Common Applications |
PLA | Moderate | Low | Low | Prototyping, educational projects |
ABS | High | Low | High | Industrial parts, functional prototypes |
PETG | High | Moderate | Moderate | Food-safe containers, durable parts |
TPU | Low | Very High | Low | Flexible parts, wearables |
Nylon | High | Moderate | High | Industrial parts, functional prototypes |
Fused Deposition Modeling is a low-cost technology for 3D printing, easy to use, and amenable to most materials. Although it does not reach the levels of detail and precision seen in SLS, since SLS technology is more expensive and complicated, FDM has also some advantages for hobbyists, educators, and professionals alike. For prototyping/manufacturing/innovation, FDM has the affordances of bringing an idea to fruition.
SLS vs FDM: Head-to-Head Comparison
With a sound knowledge of Selective Laser Sintering and Fused Deposition Modeling, it’s now time for an insightful comparison of how these two technologies stack against each other. This section shall shed detailed light on these technologies so that either you are able to choose the ones to put your money into or you simply get to know what their differences are.
SLS vs FDM Comparison
Criteria | SLS | FDM | Winner |
Precision and Detail | High precision, fine details | Lower precision, visible layer lines | SLS |
Strength and Durability | Strong, isotropic parts | Weaker layer adhesion, anisotropic parts | SLS |
Cost | Higher initial and operational costs | Lower initial and operational costs | FDM |
Material Options | Limited to powdered materials | Wide range of filament materials | FDM |
Ease of Use | More complex operation | User-friendly, accessible | FDM |
Post-Processing | Requires post-processing | Minimal post-processing | FDM |
Applications | Industrial and professional use | Versatile use, wide range of applications | Tie |
The choice between SLS and FDM ultimately depends on your specific needs and priorities. If you require high precision, durability, and are willing to invest more, SLS is the way to go. On the other hand, if you’re looking for affordability, versatility, and ease of use, FDM is the better option.
Maximizing Your 3D Printing Experience
Now that you know pretty much everything there is to know about SLS and FDM 3D technologies, implement means to maximize your 3D printing experience. These tips and best practices will provide the kick-off point whether you are new to 3D printing or a knowledgeable professional looking to perfect your workflow.
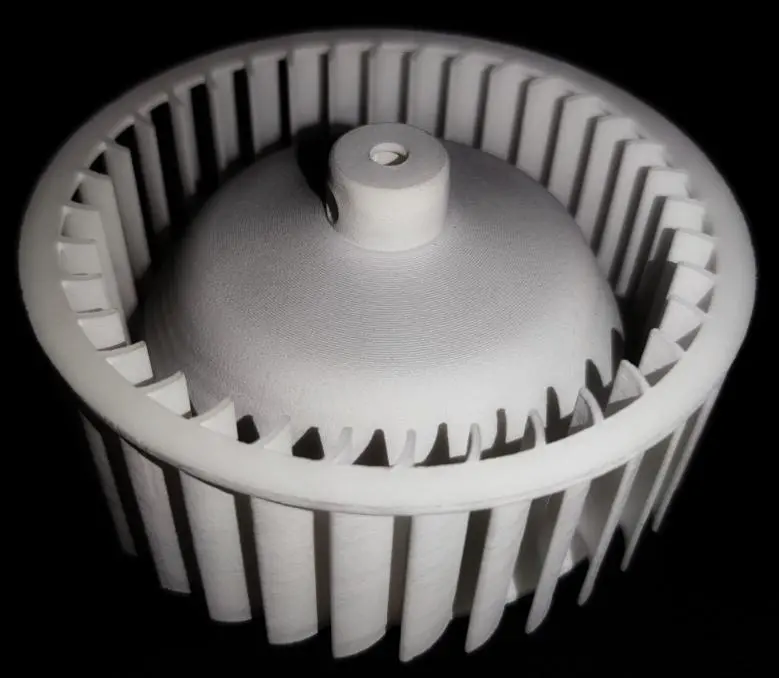
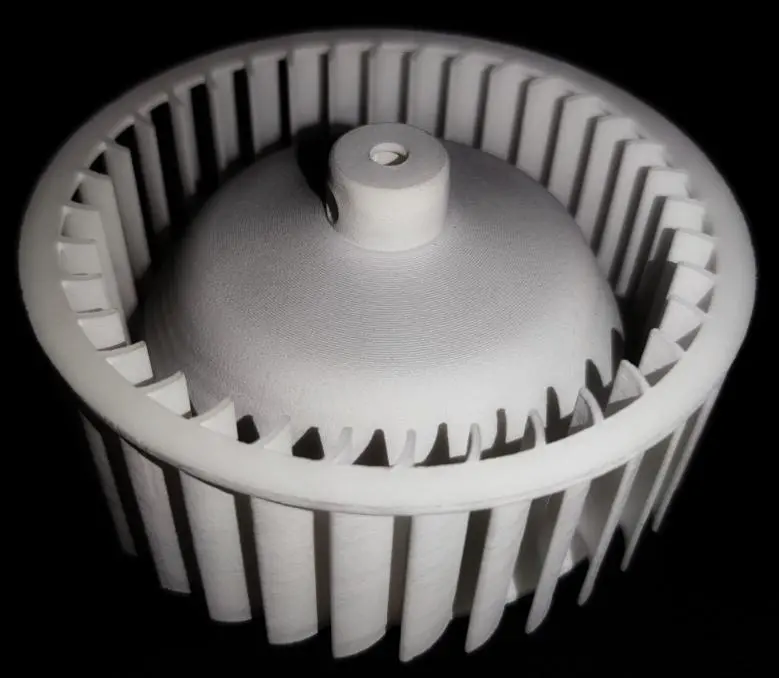
Choosing the Right Technology
When to Use SLS
- High Precision and Detail: If your project requires intricate details and high precision, SLS is the ideal choice.
- Strength and Durability: For applications that demand strong and durable parts, SLS offers superior mechanical properties.
- Complex Geometries: SLS is perfect for printing complex geometries without the need for support structures.
When to Use FDM
- Cost-Effective Solutions: If budget is a primary concern, FDM offers a more affordable option for both printers and materials.
- Versatility: For projects that require a wide range of materials and applications, FDM provides the flexibility you need.
- Ease of Use: If you’re new to 3D printing or prefer a user-friendly experience, FDM is the way to go.
Optimizing Print Settings
SLS Print Settings
- Layer Thickness: Adjust the layer thickness to balance between print speed and detail. Thinner layers result in higher detail but longer print times.
- Build Orientation: Optimize the build orientation to minimize support structures and improve print quality.
- Post-Processing: Plan for post-processing steps such as cleaning, polishing, and finishing to achieve the desired surface quality.
FDM Print Settings
- Extrusion Temperature: Ensure the extrusion temperature is optimized for the specific filament material to achieve the best layer adhesion.
- Print Speed: Balance print speed and quality. Slower speeds generally result in better print quality.
- Support Structures: Use support structures wisely to print complex geometries without compromising the final part.
Material Selection
SLS Materials
- Nylon (PA 12): Ideal for industrial parts and prototypes that require strength and flexibility.
- Polyamide 11 (PA 11): Suitable for flexible parts and consumer goods with excellent impact resistance.
- Specialty Materials: Explore specialty materials like polypropylene and TPU for specific applications.
FDM Materials
- PLA: Perfect for beginners and prototyping due to its ease of use and biodegradable nature.
- ABS: Ideal for industrial parts and functional prototypes that require strength and heat resistance.
- PETG: A durable and food-safe material with excellent layer adhesion, suitable for various applications.
- TPU: Great for flexible parts and wearables due to its high flexibility and impact resistance.
Post-Processing Techniques
SLS Post-Processing
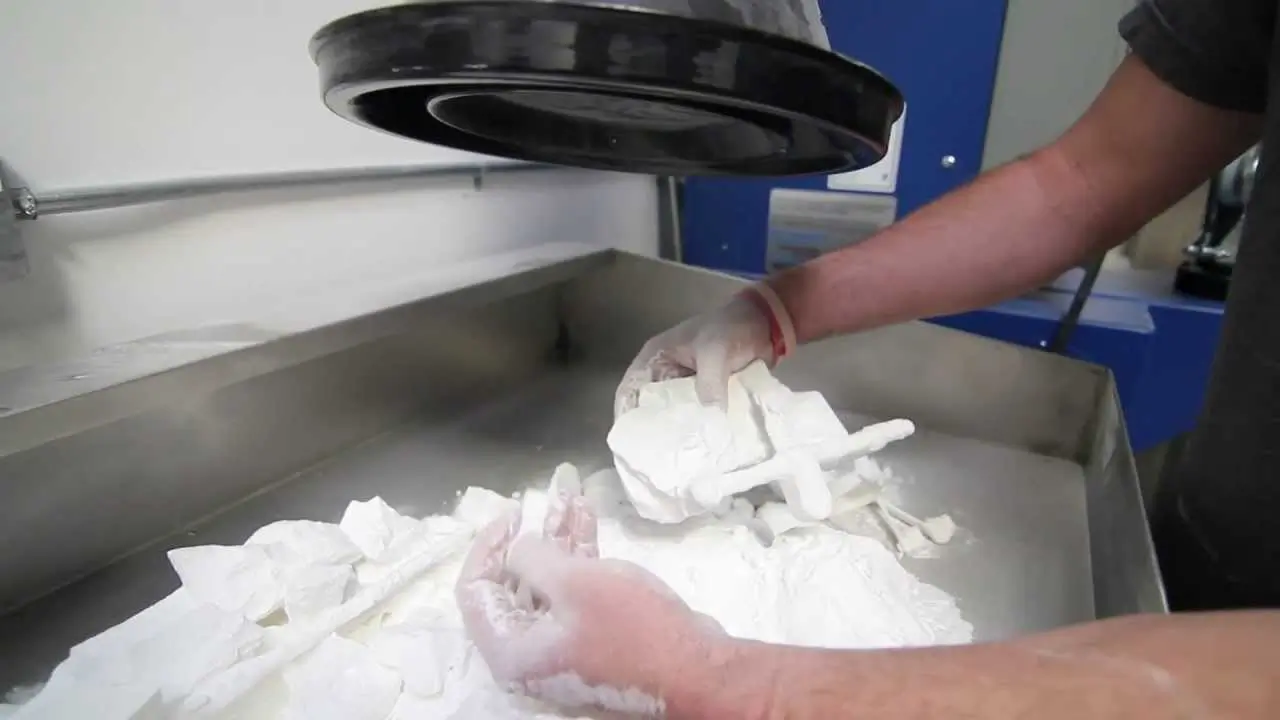
- Cleaning: Remove unfused powder carefully to avoid damaging the printed part.
- Polishing: Use polishing techniques to achieve a smooth and glossy finish.
- Finishing: Apply additional treatments like dyeing or coating to enhance the part’s appearance and properties.
FDM Post-Processing
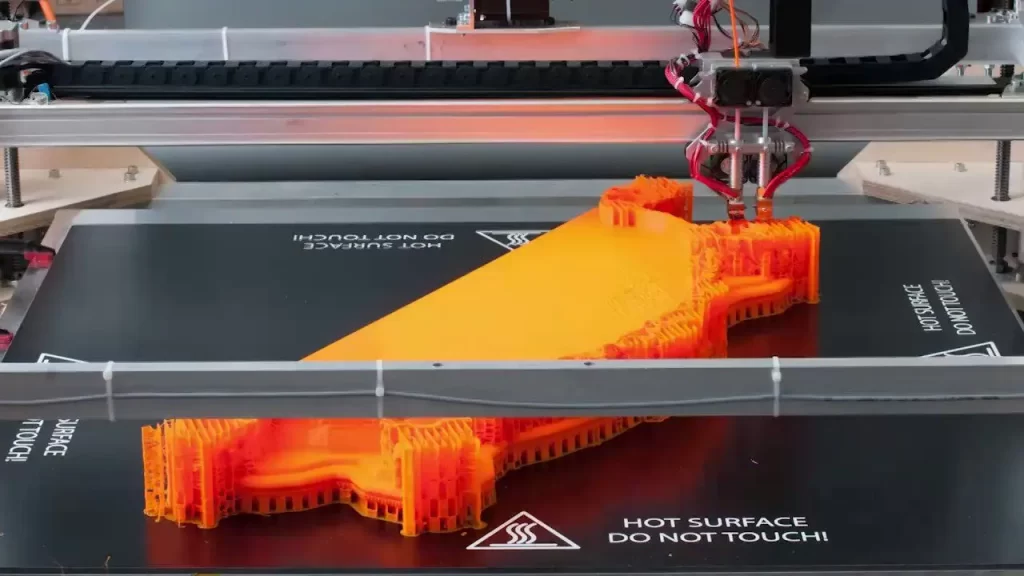
- Support Removal: Carefully remove support structures to avoid damaging the printed part.
- Sanding: Use sanding techniques to smooth out layer lines and improve surface finish.
- Painting: Apply paint or other finishing techniques to achieve the desired aesthetic.
Maintenance and Troubleshooting
SLS Maintenance
- Regular Cleaning: Clean the build chamber and powder bed regularly to ensure optimal print quality.
- Calibration: Perform regular calibration to maintain the printer’s accuracy and precision.
- Troubleshooting: Address common issues like powder clumping or uneven sintering promptly to avoid print failures.
FDM Maintenance
- Nozzle Cleaning: Clean the extruder nozzle regularly to prevent clogging and ensure consistent extrusion.
- Bed Leveling: Ensure the build platform is level to achieve even layer adhesion and prevent warping.
- Troubleshooting: Address common issues like extrusion problems, layer shifting, or warping to maintain print quality.
Making the most of your 3D printing experience means choosing the right modality, optimizing the printing parameters, choosing the appropriate materials, and employing effective sort of post-processing. Whether SLS or FDM, regular maintenance of the machines and quick troubleshooting are crucial to be followed for consistent printing quality. Getting to know some aspects of the 3D printing community will also go a long way in ensuring you gain exotic skills and knowledge. —Our 3D Printing Resource Collection: ZONGHENG3D-Resource
The Future of 3D Printing
While discussing the intricacies relating to SLS and FDM 3D printing, one would find the technologies that have already proved revolutionary in different types of industries. But what is yet to come from 3D printing technology? In this context, the article touches upon subsequent and appealing developments significantly influencing the future of 3D printing, from novel materials to cutting-edge applications.
Emerging Materials
Advanced Polymers
- High-Performance Polymers: New polymer materials are being developed to offer enhanced mechanical properties, heat resistance, and chemical resistance.
- Biodegradable Materials: There is a growing focus on sustainable and biodegradable materials to reduce environmental impact.
Metal 3D Printing
- Powder Bed Fusion: Technologies like Selective Laser Melting (SLM) and Electron Beam Melting (EBM) are advancing rapidly, enabling the printing of complex metal parts.
- Binder Jetting: This method involves layering metal powder and binding agents, followed by sintering to create strong metal parts.
Composite Materials
- Fiber-Reinforced Polymers: Composites that combine polymers with reinforcing fibers (e.g., carbon fiber, glass fiber) offer enhanced strength and durability.
- Nanocomposites: Incorporating nanoparticles into printing materials can improve mechanical properties and functionality.
Innovative Technologies
Multi-Material Printing
- Hybrid Printers: Machines that can print with multiple materials simultaneously, allowing for the creation of complex, multi-functional parts.
- Gradient Materials: Technologies that enable the printing of parts with varying material properties within a single object.
4D Printing
- Smart Materials: Materials that can change shape or properties over time in response to external stimuli, such as heat, light, or moisture.
- Applications: 4D printing has potential applications in fields like biomedical engineering, aerospace, and robotics.
Bioprinting
- Tissue Engineering: The ability to print living tissues and organs using bioinks containing cells and biomaterials.
- Regenerative Medicine: Bioprinting has the potential to revolutionize regenerative medicine by creating customized tissue replacements.
Industrial Applications
Aerospace and Defense
- Lightweight Structures: 3D printing allows for the creation of lightweight, high-strength components, reducing fuel consumption and improving performance.
- Rapid Prototyping: Quickly producing and testing prototypes to accelerate the development of new technologies.
Automotive
- Custom Parts: Manufacturing customized parts on demand, reducing inventory and waste.
- Electric Vehicles: Developing lightweight and efficient components for electric vehicles to improve range and performance.
Medical
- Personalized Medicine: Creating customized medical devices, implants, and prosthetics tailored to individual patients.
- Surgical Tools: Printing precise and sterile surgical instruments and tools.
Conclusion
3D printing has great prospects with a few innovations bordering on a wide spectrum. Basic futuristic materials and technologies leading to far-reaching applications, sustainability initiatives, and so on, are well poised to blanket an entire process. The thought hovering in 3D printing seems endless, especially regarding the changeover of the industrial, medical, and educational fields among many others.