In the realm of manufacturing and design, 3D printing has revolutionized the way products are conceived, prototyped, and produced. This groundbreaking technology enables creators to transform digital designs into tangible objects, sparking innovation across various industries, from aerospace to healthcare. However, with an ever-growing array of 3D printing technologies available, selecting the right one for your specific needs can be a daunting task.
Enter two of the most prominent technologies in the 3D printing landscape: Selective Laser Sintering (SLS) and Digital Light Processing (DLP). Each method offers unique advantages and is tailored to different applications, making the choice between them critical for maximizing efficiency, quality, and cost-effectiveness. So, how do you determine which technology is right for you?
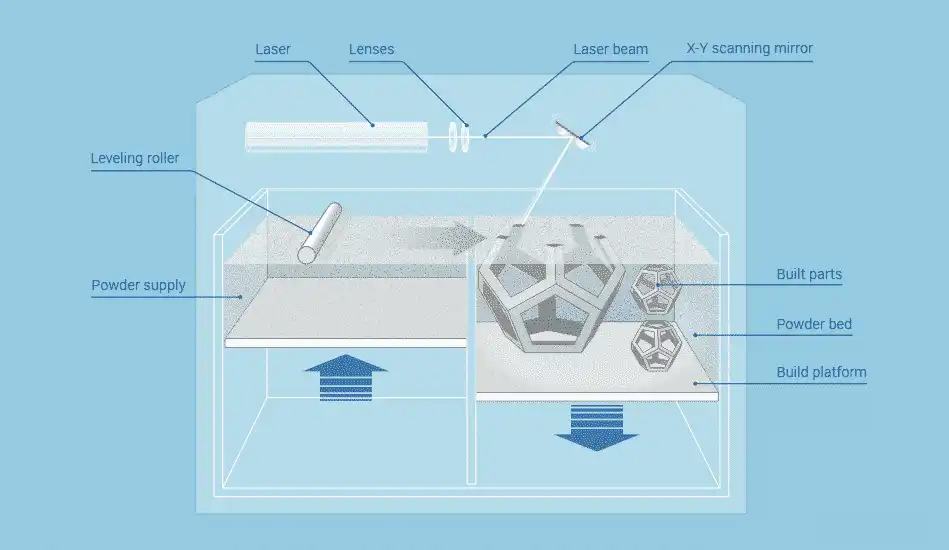
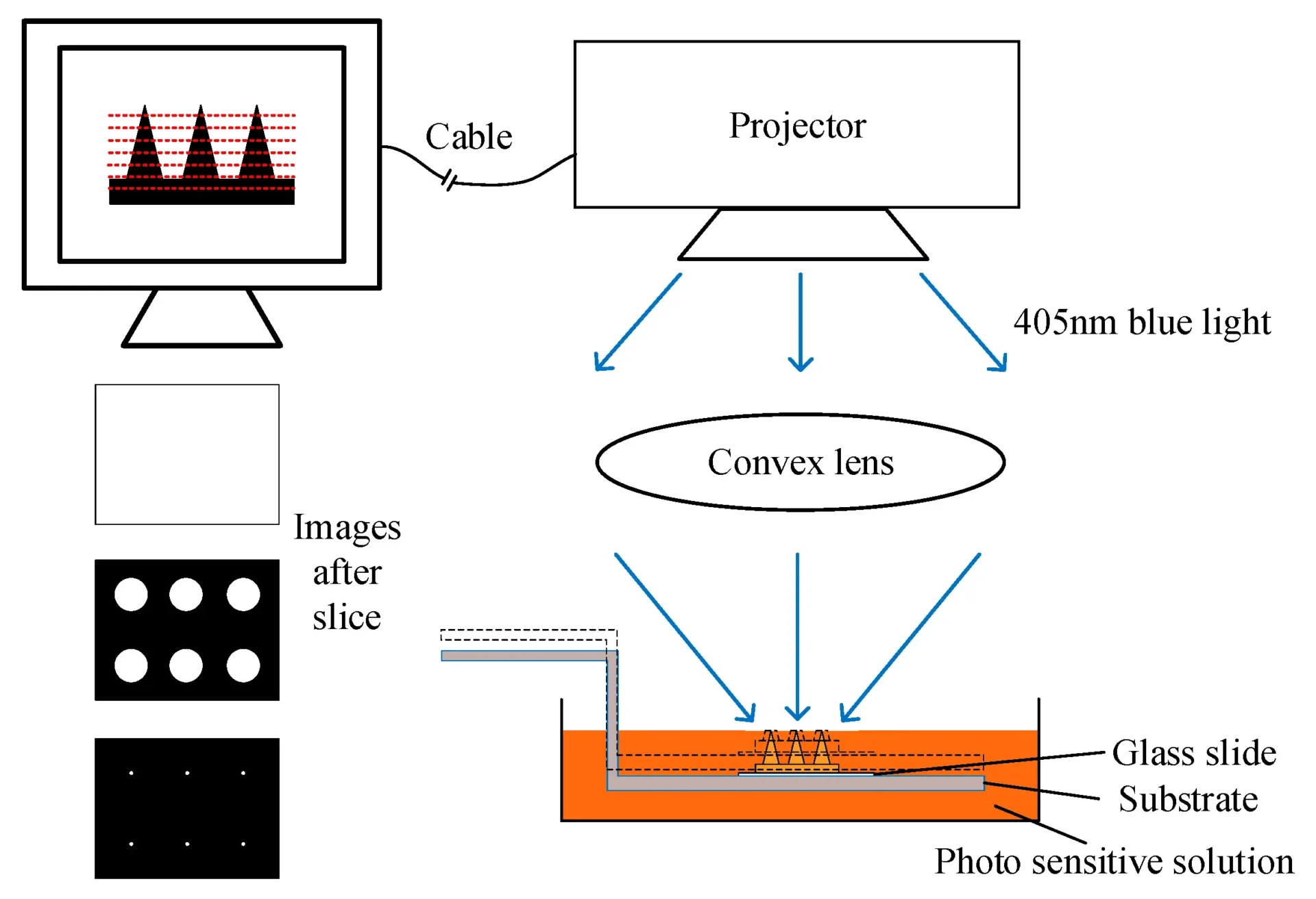
In this article, we will delve deep into the nuances of SLS and DLP, comparing their processes, material properties, costs, and practical applications. We’ll explore their strengths and weaknesses and provide insights into real-world use cases to help guide your decision-making process. Whether you are a hobbyist, an engineer, or a business owner, understanding these technologies will empower you to make informed choices that align with your goals.
Understanding the Basics of SLS and DLP 3D Printing
As the world of 3D printing continues to expand, understanding the fundamental concepts behind different technologies is essential for making informed choices. In this section, we will break down the basics of two prominent 3D printing methods: Selective Laser Sintering (SLS) and Digital Light Processing (DLP). We will explore their unique processes, the materials they use, and their common applications.
What is 3D Printing?
At its core, **3D printing**—also known as **additive manufacturing**—is a process that creates three-dimensional objects by building them layer by layer from a digital model. Unlike traditional manufacturing methods that often involve subtracting material (like cutting or drilling), 3D printing adds material until the desired object is formed. This process opens up a wealth of possibilities in design, customization, and production efficiency.
Key Benefits of 3D Printing:
- Customization: Easily create tailored products to meet specific needs.
- Complex Geometry: Produce intricate designs that would be challenging or impossible with traditional methods.
- Reduced Waste: Minimize material waste compared to subtractive manufacturing.
Introduction to Selective Laser Sintering (SLS)
What is SLS?
Selective Laser Sintering (SLS) is a powder-based 3D printing technology that uses a laser to fuse powdered material together. This method is renowned for its ability to create robust and functional parts, making it ideal for both prototyping and production.
How Does SLS Work?
- Layering: A thin layer of powder material (usually nylon, polyamide, or metal) is spread across the build platform.
- Laser Fusion: A high-powered laser selectively scans the powdered surface, fusing the material together according to the design.
- Layering Again: Once the laser has completed one layer, the build platform lowers, and another layer of powder is applied. This process repeats until the object is fully formed.
- Cooling and Post-Processing: After printing, the part is allowed to cool and is then cleaned of excess powder.
Materials Used in SLS
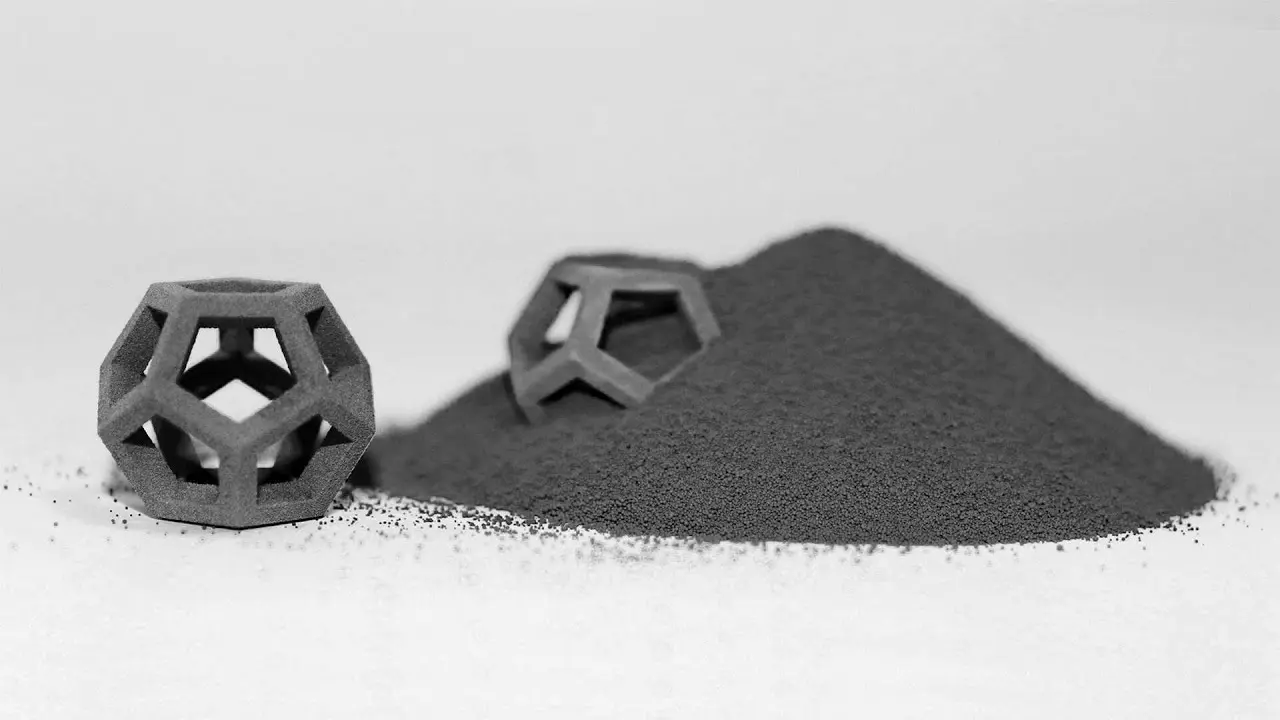
SLS can utilize a variety of materials, including:
- Nylon: Known for its strength and flexibility.
- Metal Powders: Often used for industrial applications where high strength is crucial.
- Composite Materials: Blends with special additives for enhanced properties.
Common Applications of SLS
SLS technology shines in various applications, such as:
- Prototyping: Rapid creation of functional prototypes for testing and validation.
- End-Use Parts: Production of durable components for automotive and aerospace industries.
- Medical Devices: Custom implants and prosthetics tailored to individual patients.
Introduction to Digital Light Processing (DLP)
What is DLP?
Digital Light Processing (DLP) is another innovative 3D printing technology that uses a digital light projector to cure liquid resin into solid objects. It is recognized for its high resolution and speed, making it a preferred choice for certain applications.
How Does DLP Work?
- Resin Layering: A vat filled with liquid photopolymer resin is prepared.
- Light Projection: A digital light projector flashes an entire layer of the object onto the surface of the resin, curing it instantly.
- Layering Again: The build platform rises slightly, allowing a new layer of resin to flow over the previous layer. This process repeats until the final object is created.
- Cleaning and Curing: After printing, the part is cleaned to remove any uncured resin and often subjected to additional UV light for final curing.
Materials Used in DLP
DLP typically utilizes:
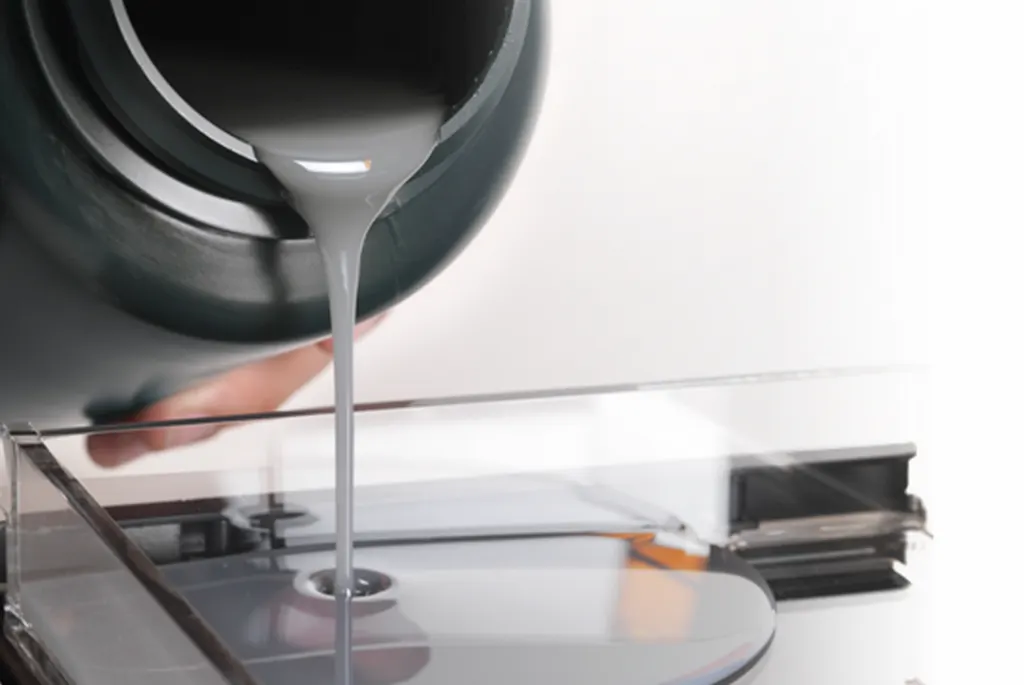
- Photopolymer Resins: Available in various formulations to achieve different characteristics such as rigidity, flexibility, and color.
- Specialty Resins: Certain formulations are designed for specific applications, like dental or jewelry printing.
Common Applications of DLP
DLP technology is highly effective in:
- Jewelry Making: Producing intricate designs with high detail for casting.
- Dental Prototyping: Creating accurate dental models and custom aligners.
- Rapid Prototyping: Quick production of detailed prototypes for engineering and design.
Summary
Understanding the basics of SLS and DLP technologies is crucial for making an informed decision about which method fits your 3D printing needs. Both technologies have unique processes, materials, and applications that cater to various industries and requirements. SLS excels in producing durable, functional parts suitable for a wide range of applications, while DLP offers high resolution and speed, making it optimal for detailed designs.
Technical Comparison: SLS vs DLP 3D Printing
When it comes to selecting the right 3D printing technology, understanding the technical aspects is essential. Selective Laser Sintering (SLS) and Digital Light Processing (DLP) are both powerful methods, but they differ significantly in their processes, speed, surface finish, and material properties. In this section, we will provide a comprehensive comparison of SLS and DLP, highlighting their strengths and weaknesses to help you make an informed choice.
Printing Process: How They Work
SLS Printing Process
The SLS process involves several steps that create a three-dimensional object from powdered material. Here’s a detailed breakdown:
- Powder Bed Preparation: A thin layer of powder is spread evenly over the build platform.
- Laser Scanning: A high-powered laser selectively fuses the powder according to the CAD design.
- Layer-by-Layer Building: After one layer is completed, the platform lowers, and a new layer of powder is applied. This continues until the object is fully formed.
- Cooling and Cleaning: Post-printing, the object is allowed to cool before being cleaned of excess powder.
DLP Printing Process
DLP, on the other hand, uses light to cure liquid resin. Here’s how it works:
- Resin Preparation: The build platform is submerged in a vat of liquid photopolymer resin.
- Layer Exposure: A digital light projector flashes an entire layer of the object onto the resin, curing it instantly.
- Layer-by-Layer Building: The platform lifts slightly, allowing a new layer of resin to flow over the previous layer. This process is repeated until the model is complete.
- Post-Processing: The printed part is cleaned and often cured under UV light to enhance its mechanical properties.
Aspect | SLS | DLP |
Process Type | Powder-based | Resin-based |
Build Method | Layered fusion using a laser | Layered curing using a light projector |
Material State | Solid powder | Liquid resin |
Post-Processing | Cleaning excess powder | Cleaning and additional curing |
Speed and Efficiency
When evaluating 3D printing technologies, speed and efficiency are crucial factors that can affect production timelines.
Speed Comparison
- SLS: Typically, SLS can produce parts at a moderate pace. The speed can vary depending on the complexity of the model and the thickness of the layers. SLS is efficient for larger batches since multiple parts can be printed simultaneously within the same powder bed.
- DLP: DLP tends to be faster than SLS for smaller parts because it cures entire layers at once rather than scanning point by point. This makes DLP especially advantageous for rapid prototyping and small-scale production.
Efficiency Overview
- SLS Efficiency: While the initial setup time can be longer due to the need for powder preparation and post-processing, the ability to print multiple parts in one go can lead to cost savings and reduced lead times for larger runs.
- DLP Efficiency: DLP’s major strength lies in its quick production of highly detailed parts, but it may require more frequent refilling of resin and additional post-processing time.
Surface Finish and Detail
The quality of the final product is often determined by the surface finish and detail achievable with each printing method.
SLS Surface Finish
- Surface Quality: SLS typically produces parts with a rougher surface finish due to the nature of the powder particles. However, this can be advantageous for certain applications that require texture or grip.
- Detail Resolution: SLS can achieve good detail but is generally not as fine as DLP when it comes to intricate designs and smooth finishes.
DLP Surface Finish
- Surface Quality: DLP can produce parts with an exceptional surface finish, often requiring minimal post-processing. The smoothness is ideal for applications such as jewelry and dental models where aesthetics are crucial.
- Detail Resolution: DLP offers high resolution and can capture fine details in complex geometries, making it a preferred choice for intricate designs.
Aspect | SLS | DLP |
Surface Finish | Generally rough | Very smooth |
Detail Resolution | Good for functional parts | Excellent for intricate designs |
Material Properties
The choice of material can significantly impact the performance and application of the printed parts.
SLS Material Properties
- Strength: SLS parts are known for their durability and mechanical strength, making them suitable for functional prototypes and end-use parts.
- Material Variety: SLS supports a range of materials, including nylon, metal powders, and composites, each offering different properties like flexibility, heat resistance, and weight.
DLP Material Properties
- Aesthetic Quality: DLP photopolymers can achieve a wide range of colors and finishes, making them ideal for applications requiring visual appeal.
- Material Limitations: While DLP materials can offer excellent detail, they may not always match the strength and durability of SLS materials, especially for industrial applications.
Aspect | SLS | DLP |
Material Strength | High | Variable, often lower than SLS |
Material Variety | Nylon, metal powders, composites | Photopolymers, specialty resins |
The technical comparison between SLS and DLP reveals that both technologies have unique strengths and limitations. SLS stands out for its robust material properties and suitability for functional parts, while DLP excels in delivering high resolution and superior surface finishes.
As you consider which technology best suits your needs, weigh your priorities—whether they be speed, detail, efficiency, or material characteristics.
Cost Analysis: SLS vs DLP 3D Printing
When considering 3D printing technologies, cost often plays a pivotal role in decision-making. From initial equipment investments to material expenses and operational costs, understanding the financial implications of Selective Laser Sintering (SLS) and Digital Light Processing (DLP) is essential for businesses and hobbyists alike. In this section, we will conduct a thorough cost analysis of SLS and DLP, breaking down the factors that influence pricing and helping you gauge which technology may better fit your budget.
Equipment Costs
Initial Investment
The initial cost of purchasing a 3D printer can vary significantly between SLS and DLP technologies.
- SLS Printers:
- SLS machines tend to be more expensive due to their complexity and advanced technology. Entry-level SLS printers can range from $50,000 to over $250,000, depending on size, capability, and manufacturer.
- Industrial-grade SLS systems can cost upwards of $500,000, making them a significant investment mainly for larger companies or specialized applications.
- DLP Printers:
- DLP printers are generally more affordable, with entry-level models starting around $2,000 to $10,000.
- Mid-range DLP printers can go up to $30,000, while high-end models suitable for industrial use may range from $50,000 to $100,000.
Type | SLS Printer Cost | DLP Printer Cost |
Entry-Level | $$50,000 -$$250,000 | $$2,000 -$$10,000 |
Mid-Range | $$250,000 -$$500,000 | $$10,000 -$$30,000 |
High-End | $500,000+ | $$50,000 -$$100,000 |
Maintenance and Operational Costs
In addition to the initial investment, ongoing maintenance and operational costs should be factored into the overall expense of each technology.
- SLSMaintenance Costs:
- SLS printers require regular maintenance due to their complexity. Maintenance costs can be 10%-20% of the initial purchase price annually.
- Users also need to consider the costs of replacing laser components, which can be substantial.
- DLPMaintenance Costs:
- DLP printers generally require less maintenance, and costs are lower, typically around 5%-10% of the initial purchase price annually.
- However, users should account for the potential need to replace projectors and other electronic components over time.
Material Costs
The choice of materials is a crucial factor in determining the overall costs associated with SLS and DLP technologies.
Material Pricing
- SLS Materials:
- SLS materials, such as nylon and metal powders, can be relatively expensive. Nylon powder prices can range from $50 to $100 per kilogram, while metal powders may reach upwards of $150 to $500 per kilogram** depending on the metal type.
- Additional costs may arise from the need for post-processing materials, such as support structures or finishing compounds.
- DLP Materials:
- DLP materials, specifically photopolymer resins, are generally more affordable. Standard resin costs range from $50 to $150 per liter.
- Specialty resins, on the other hand, can be significantly more expensive, particularly those designed for specific applications (e.g., dental or jewelry), costing up to $500 per liter.
Material Type | SLS Material Cost | DLP Material Cost |
Nylon Powder | $$50 -$$100 per kg | N/A |
Metal Powder | $$150 -$$500 per kg | N/A |
Photopolymer Resin | N/A | $$50 -$$150 per liter |
Specialty Resin | N/A | Up to $500 per liter |
Cost Efficiency for Different Applications
Cost efficiency can vary considerably depending on the specific applications of each technology.
SLS Cost Efficiency
- Mass Production: SLS is particularly cost-effective for mass production runs where multiple parts can be built simultaneously. The ability to print multiple parts in a single batch can reduce the overall cost per part significantly.
- Durable Parts: For applications requiring strong, functional parts, the investment in SLS may be justified due to the superior mechanical properties of the final products.
DLP Cost Efficiency
- Rapid Prototyping: DLP shines in scenarios where speed and detail are paramount. When producing small, intricate parts, DLP can save time and reduce material waste, leading to cost savings.
- Low-Volume Production: For small batch production of high-detail parts, DLP can be more cost-effective due to lower material costs and faster print times, even though the initial printer investment is lower.
In summary, the cost analysis between SLS and DLP highlights the stark differences in initial investments, ongoing operational costs, material expenses, and cost efficiency based on application. SLS may require a larger upfront investment and higher material costs but offers advantages in mass production and part durability. Meanwhile, DLP presents a more affordable path for those focusing on speed, detail, and low-volume production.
Ultimately, your choice will depend on your specific needs, budget, and application requirements.
Pros and Cons of SLS and DLP 3D Printing
Choosing between Selective Laser Sintering (SLS) and Digital Light Processing (DLP) can be a complex decision, as both technologies come with their own set of advantages and disadvantages. Understanding these pros and cons is vital for making an informed decision that aligns with your specific needs, whether you’re a hobbyist, a small business owner, or part of a larger manufacturing operation. In this section, we will delve into the strengths and weaknesses of both SLS and DLP, providing you with a comprehensive overview.
Pros of Selective Laser Sintering (SLS)
1. Versatile Material Options
- Wide Range of Materials: SLS supports various materials, including nylon, metal, and composites. This versatility allows for the creation of parts that can meet diverse functional requirements.
- Durability: Parts produced with SLS are known for their strength and toughness, making them suitable for end-use applications in automotive, aerospace, and other demanding industries.
2. No Support Structures Required
- Self-Supporting Design: Because the unsintered powder serves as support during the printing process, SLS can produce complex geometries without the need for additional support structures. This characteristic greatly simplifies the design process and reduces material waste.
3. Excellent for Functional Prototypes
- Real-World Testing: SLS is ideal for creating functional prototypes that can withstand real-world applications. Engineers and designers can test parts for fit, form, and function before moving to full-scale production.
4. Scalability
- Batch Production: SLS printing can efficiently produce multiple parts simultaneously within the same powder bed, making it suitable for batch production and reducing the cost per part.
Pros of SLS | Benefits |
Versatile Material Options | Supports various materials with high durability. |
No Support Structures Required | Enables complex designs without additional support. |
Excellent for Functional Prototypes | Allows real-world testing of designs for validation. |
Scalability | Efficient for mass production with reduced cost per part. |
Cons of Selective Laser Sintering (SLS)
1. High Initial Investment
- Costly Equipment: The significant upfront cost of SLS printers can be a barrier for small businesses or hobbyists. This includes both the printer itself and the associated materials.
2. Longer Print Times
- Slower Production Speed: Compared to DLP, SLS can have longer print times, especially for intricate designs or large parts, as it processes one layer at a time.
3. Rough Surface Finish
- Texture Limitations: The natural texture of SLS parts tends to be rougher compared to DLP. Additional post-processing may be required for applications where a smooth finish is crucial.
4. Complexity in Post-Processing
- Cleaning and Finishing: The need to remove excess powder can complicate post-processing, requiring additional labor and time.
Cons of SLS | Drawbacks |
High Initial Investment | Costly equipment may deter small businesses and hobbyists. |
Longer Print Times | Slower production can affect turnaround times. |
Rough Surface Finish | May require post-processing for a better finish. |
Complexity in Post-Processing | Time-consuming cleaning and finishing processes. |
Pros of Digital Light Processing (DLP)
1. High Resolution and Detail
- Exceptional Accuracy: DLP is capable of producing highly detailed parts with smooth surface finishes. This is particularly advantageous for applications requiring fine detail, such as jewelry and dental models.
2. Faster Production Speed
- Layer Curing: DLP cures entire layers at once, significantly reducing print times compared to SLS, especially for small to medium-sized parts.
3. Lower Material Costs
- Affordable Resins: DLP generally utilizes less expensive photopolymer resins, making it a more budget-friendly option for prototyping and low-volume production.
4. Simplicity of Print Process
- User-Friendly: DLP printers tend to have a more straightforward setup and operation process, making them accessible for newcomers to 3D printing.
Pros of DLP | Benefits |
High Resolution and Detail | Ideal for intricate designs requiring precision. |
Faster Production Speed | Cures entire layers simultaneously for quicker results. |
Lower Material Costs | More budget-friendly resins for various applications. |
Simplicity of Print Process | User-friendly operation, suitable for beginners. |
Cons of Digital Light Processing (DLP)
1. Limited Material Options
- Material Restrictions: DLP is primarily limited to photopolymer resins, which may not provide the same mechanical properties as SLS materials. This can restrict its use in certain industrial applications.
2. Post-Processing Needs
- Cleaning and Curing: DLP prints often require extensive post-processing, including cleaning excess resin and additional curing, which can add time and labor costs.
3. Fragility of Parts
- Lower Durability: Parts produced by DLP tend to be more brittle than those made with SLS, making them less suitable for applications that require high strength and impact resistance.
4. Limited Build Size
- Size Constraints: DLP printers generally have smaller build volumes than SLS printers, which can limit the size of parts that can be produced in a single print.
Cons of DLP | Drawbacks |
Limited Material Options | Primarily uses photopolymer resins with restricted properties. |
Post-Processing Needs | Requires additional time and labor for cleaning and curing. |
Fragility of Parts | Less durable, may not withstand high-stress applications. |
Limited Build Size | Smaller build volumes constrain part size options. |
Both SLS and DLP technologies have their unique sets of pros and cons, making each suitable for different applications and users. SLS is a powerful option for producing durable, functional parts and complex geometries, but it comes with higher costs and longer print times. Conversely, DLP offers exceptional detail and speed, making it ideal for rapid prototyping and applications requiring fine finishes, though it may fall short in material versatility and durability.
As you weigh these advantages and disadvantages, consider your specific project needs, budget, and desired outcomes. Ultimately, the right technology will align with your objectives and help you achieve your 3D printing goals.
Key Takeaways: Choosing Between SLS and DLP 3D Printing
Navigating the world of 3D printing can be overwhelming, especially when selecting the right technology for your needs. Both Selective Laser Sintering (SLS) and Digital Light Processing (DLP) offer unique advantages and challenges, making them suitable for different applications. In this concluding section, we will summarize the key points discussed throughout the article, providing you with actionable insights to help you make an informed decision.
Summary of Technologies
Selective Laser Sintering (SLS)
- Process Overview: SLS uses a laser to selectively fuse powdered materials layer by layer, resulting in durable, functional parts.
- Material Options: Supports a broad range of materials, including nylon, metal powders, and composites, which provide excellent mechanical properties.
- Applications: Well-suited for prototyping, end-use parts, and industries requiring high durability such as aerospace and automotive.
- Pros: Versatile materials, no need for support structures, excellent for functional prototypes, and scalable for batch production.
- Cons: High initial investment, longer print times, rough surface finishes requiring post-processing, and complexity in cleaning.
Digital Light Processing (DLP)
- Process Overview: DLP employs a digital light projector to cure photopolymer resin layer by layer, resulting in high-resolution, detailed prints.
- Material Options: Primarily uses photopolymer resins, which can be less durable than SLS materials but allow for intricate designs and fine details.
- Applications: Ideal for rapid prototyping, jewelry making, dental applications, and any projects requiring high precision and aesthetics.
- Pros: High resolution, faster production speed, lower material costs, and user-friendly operation.
- Cons: Limited material options, extensive post-processing needs, fragility of parts, and smaller build sizes.
Decision-Making Factors
When deciding between SLS and DLP, consider the following factors:
1. Project Requirements
- Durability: If your application involves functional parts requiring strength, SLS may be the better choice.
- Detail and Aesthetics: For projects emphasizing intricate designs and smooth finishes, DLP excels.
2. Budget Considerations
- Evaluate your initial investment capabilities. SLS is generally more expensive upfront, while DLP offers a lower entry point.
- Don’t forget to factor in ongoing operational and material costs, including maintenance and post-processing requirements.
3. Production Volume
- For small to medium runs with intricate details, DLP provides faster turnaround times.
- If you require mass production with multiple parts in one cycle, SLS is more efficient.
4. Material Needs
- If your project demands a specific material type (e.g., metals or composites), SLS is more versatile.
- For applications focused on visual appeal, DLP materials may suffice despite their limited mechanical properties.
5. Post-Processing Capabilities
- Consider the time and resources available for post-processing. SLS requires cleaning of excess powder, while DLP involves cleaning uncured resin.
Final Thoughts
In conclusion, both SLS and DLP technologies play essential roles in the 3D printing landscape. The right choice depends on your specific needs, whether you prioritize durability, detail, budget, or production efficiency.
To recap:
- SLS is powerful for functional applications, offering durability and versatility at a higher cost and complexity.
- DLP is ideal for precise, high-detail prints with a lower initial investment, though it may sacrifice some material strength and requires careful post-processing.
Ultimately, understanding these key differences will empower you to choose the best technology that aligns with your objectives, ensuring successful outcomes for your 3D printing projects.