Imagine holding a 3D printed object that’s so smooth and detailed it looks like it was made using traditional injection molding. Think about those tiny miniatures with features you can barely see, or prototypes that seem ready for retail. This isn’t just a dream—this is what Stereolithography (SLA) 3D printing can do.
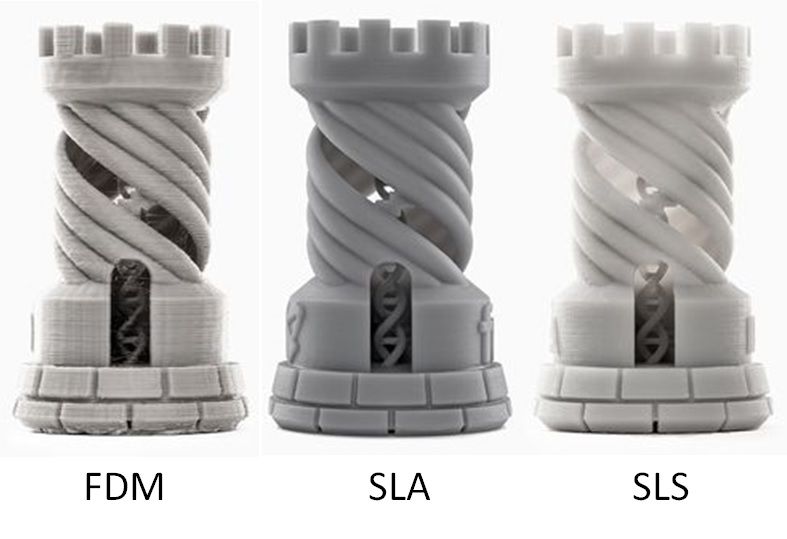
While many people use Fused Deposition Modeling (FDM) printers that melt plastic filament, SLA stands out for its ability to create stunning detail and a smooth finish. If you’ve ever been impressed by the sharp edges and flawless surfaces of certain 3D prints, you were likely looking at something made with SLA technology, where liquid resin is cured by light.
So, what is SLA? It’s an additive manufacturing process that’s part of the vat polymerization family. Here’s how it works: a focused light source—often a UV laser, but sometimes a digital projector—cures liquid resin layer by layer. Imagine building an object from a pool of liquid, where each slice solidifies with light before the next layer is added. This curing process is called photopolymerization.
Originally, SLA printers used lasers (Laser SLA). Now, we have newer methods like Digital Light Processing (DLP), which uses a projector, and Masked SLA (MSLA), which uses an LCD screen to control a UV light source. MSLA has become popular for home and professional use because it’s fast and cost-effective, providing high resolution over the entire build area at once.
Why write a whole guide on SLA? Because getting those amazing results requires more than just hitting “print.” SLA involves key steps before and after printing. You need to know how to prepare your digital models, use slicing software, and handle post-processing tasks like washing and curing. Plus, you need to understand safety procedures for the resins and solvents involved. If you skip or misjudge any of these steps, especially in post-processing, you risk failed prints or even safety issues.
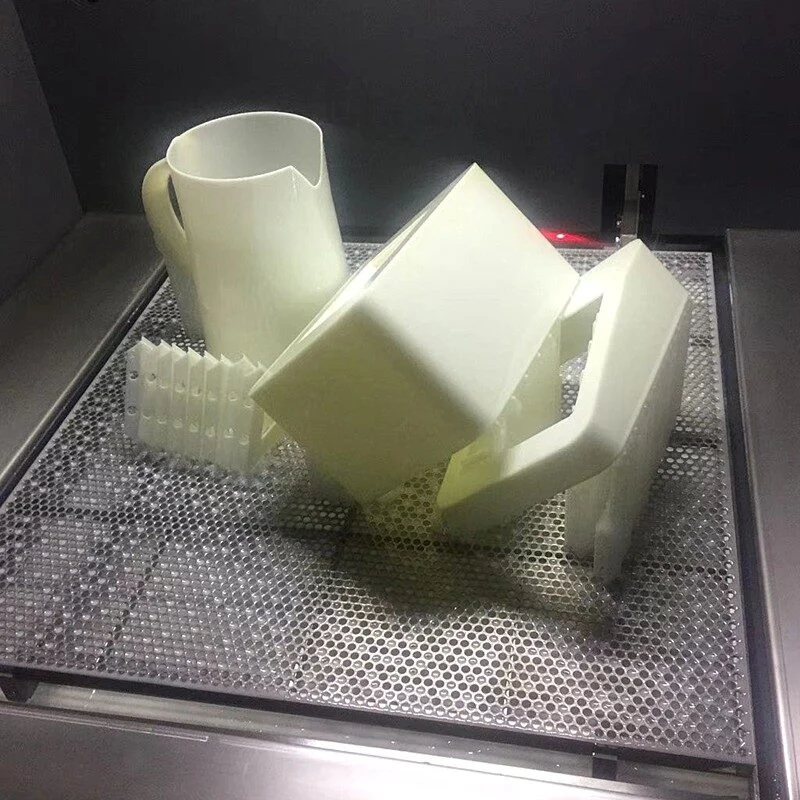
Whether you’re new to SLA, want to improve your skills, or are thinking about trying this tech, this guide will help you master the whole process and tap into the high-resolution potential of Stereolithography. Let’s get started!
How SLA 3D Printing Works
Ever wondered how Stereolithography (SLA) printers turn a vat of gooey resin into detailed objects? It may seem magical, but it’s all about clever science and engineering. Unlike FDM, which melts plastic, SLA works with light and chemistry. Let’s break down the fascinating tech behind SLA.
The Star of the Show: Photopolymerization
The heart of SLA printing is a process called photopolymerization. It may sound complicated, but the idea is simple:
- The Liquid: It starts with a special liquid called photopolymer resin. This isn’t just any liquid; it’s a mix of monomers, oligomers, and photoinitiators.
- The Trigger: Photoinitiators are like tiny soldiers waiting for their cue. That cue is UV light—typically around 405nm for most printers.
- The Reaction: When UV light hits the resin, the photoinitiators activate. They absorb the light and kick off a chemical reaction, linking monomers and oligomers into long, cross-linked chains.
- The Result: Where the light shines, the resin hardens quickly into solid plastic. Where it doesn’t hit, the resin stays liquid.
This selective hardening is what allows SLA printers to build objects, layer by layer.
Meet the Components of an SLA Printer
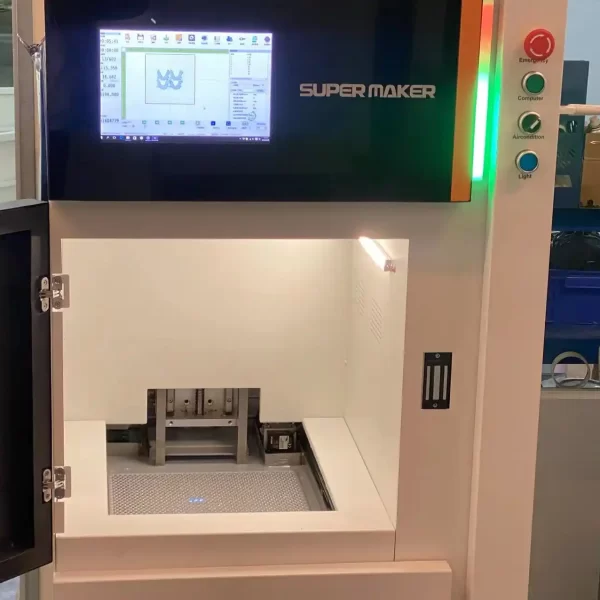
For SLA printers to perform this light-curing magic consistently, they rely on several key parts:
- The Resin Vat:
- Holds the liquid resin during printing.
- The bottom is usually a transparent film (like FEP or PFA) that lets UV light pass through to cure the resin against the build platform.
- This film’s non-stick property helps the cured layer peel off easily.
- The Build Platform:
- This is where the object is printed, lowered into the resin vat.
- The first layers cure directly onto its surface, with later layers sticking to the previous ones.
- It’s often metal, textured for better adhesion, and moves vertically.
- The Light Source:
- This is the heart of the photopolymerization process. There are three main types:
- UV Laser: Used in traditional SLA, drawing the layer’s pattern point by point.
- DLP Projector: This flashes an image of the entire layer at once, like a mini digital slide projector.
- LCD + UV LEDs: In MSLA, a UV LED array shines through an LCD mask to create the layer pattern.
- This is the heart of the photopolymerization process. There are three main types:
- The Z-Axis Mechanism:
- Controls the vertical movement of the build platform.
- It lowers into the resin and lifts slightly after curing each layer, determining the layer height, which affects resolution and speed.
The Layer-by-Layer Process
Let’s visualize how the printing process unfolds step-by-step:
- Initialization: The build platform lowers into the resin vat, leaving a gap equal to the desired layer height (e.g., 0.05mm).
- First Layer Exposure: The light source activates, curing the resin in the shape of the first layer directly onto the platform.
- The Peel: Once the layer is cured, the platform lifts, peeling the solidified layer off the film. This action often creates characteristic sounds during printing and allows fresh resin to flow into the gap.
- Repositioning: The platform lowers again, maintaining the precise gap for the next layer.
- Next Layer Exposure: The light source cures the next layer, bonding it to the previous one.
- Repeat: Steps 3, 4, and 5 are repeated many times, building the object layer by layer until it’s fully formed, suspended from the platform and ready for post-processing.
Laser vs. DLP vs. MSLA/LCD
While the core principle remains the same, the type of light source significantly impacts speed, resolution, and cost:
Feature | Laser SLA (L-SLA) | DLP SLA | MSLA / LCD SLA |
Light Source | UV Laser | Digital Light Processing (DLP) Projector | UV LED Array + LCD Screen |
How it Cures | Draws the layer pattern point-by-point with a beam | Flashes the entire layer image at once | Flashes the entire layer image (masked by LCD pixels) |
Speed | Can be slower, especially for large/solid layers | Faster than laser (cures whole layer simultaneously) | Generally fastest (cures whole layer simultaneously) |
Resolution XY | Determined by laser spot size and galvanometer precision | Determined by projector resolution & projection size | Determined by LCD pixel size (fixed resolution across build plate) |
Pros | Potentially very large build volumes, mature tech | Fast layer times, good accuracy | Very fast layer times, cost-effective, high resolution potential |
Cons | Slower for complex layers, often more expensive | Projector resolution limits detail, potential edge distortion, expensive bulbs | LCD screen is a consumable (lifespan limited), potential visible pixel grid |
Common Use | Industrial, large-format printers | Dental, Jewelry, some desktop printers | Most common for desktop/consumer printers, prosumer |
For many newcomers to SLA 3D printing, MSLA/LCD printers strike a great balance between speed, high resolution, and affordability. Understanding that the LCD screen acts as a pixelated mask is essential. This is how these popular printers achieve such impressive detail.
The “magic” of SLA is not really magic at all. It’s a well-coordinated process involving controlled photopolymerization, precise mechanical movements, and targeted exposure to UV light. Grasping these basics will set you up well as we move into preparing your digital models and getting your printer ready for its light-curing performance.
Before the Print: Mastering the SLA Pre-Printing Phase
So, now you get how photopolymerization works and how SLA printers create objects layer by layer. But before you start pouring resin and dreaming of those high-resolution prints, there’s an important step: Pre-Printing. Think of this as the planning and setup phase. Getting this right is crucial for successful, beautiful SLA prints.
This phase is all about turning your digital 3D model into something the printer can work with while getting your physical setup ready for success. It involves choosing the right settings, positioning your model wisely, adding supports, and prepping the printer and materials. Skipping or rushing these steps can lead to failed prints and frustration. Let’s dive into how to set the stage for SLA success!
Step 1: Your Digital Blueprint – The 3D Model
Everything begins with a digital file. This file is the blueprint your SLA printer will transform into a physical object. You can find these models in a few different ways:
- CAD Software: Design your own models from scratch using tools like Fusion 360, Blender (which is free!), SolidWorks, or ZBrush. This gives you complete creative control.
- 3D Scanning: Capture real-world objects using 3D scanners, though you might need to clean up and repair the mesh afterward.
- Online Repositories: Download pre-made models from sites like Thingiverse, MyMiniFactory, Cults3D, Printables, and other specialized marketplaces. This is great for getting started or finding existing designs.
No matter the source, your model will typically be in one of these common mesh file formats:
- STL (STereoLithography): The long-standing industry standard. It represents surfaces as triangles (a mesh), is simple and widely compatible, but lacks color or material data.
- OBJ (Object File): Another popular format that can store color, texture, and material info, though not all SLA workflows use this data.
- 3MF (3D Manufacturing Format): A newer, XML-based format designed to improve upon STL. It can bundle more information (like settings and materials) into one file. It’s becoming more common, but STL still dominates.
Key takeaway: Make sure your model is “watertight” (no holes in the mesh) and manifold (no unrealistic geometry). Most slicers have basic repair functions, but complex issues might need specialized software like Meshmixer or Windows 3D Builder.
Step 2: The Slicer – Turning Digital into Physical Layers
You can’t just send an STL file straight to your SLA printer. You need software called a Slicer to translate your model into layers. For SLA, the slicer does much more than just cut the model into horizontal layers:
- It helps you position the model correctly on the build plate.
- It generates necessary support structures.
- It allows you to hollow out the model and add drainage holes.
- It applies specific print settings (like layer height and exposure times).
- It outputs the final file in a format the printer understands (like .ctb, .cbddlp, .goo, .photon, .zip, etc.).
Think of the slicer as your mission control for the print job. Some popular choices for resin printers include:
- ChiTuBox (Free/Pro): Very popular, widely compatible, with powerful features.
- Lychee Slicer (Free/Pro): User-friendly with excellent support generation tools and an auto-orientation feature.
- PreForm (Formlabs): Designed for Formlabs printers, known for reliability and ease of use.
- Anycubic Photon Workshop: Proprietary slicer from Anycubic.
- PrusaSlicer: Mostly for FDM but gaining capabilities for resin printing.
Step 3: Getting It Right – Key Slicer Settings & Strategies
Now we reach the heart of pre-printing—the critical settings and strategies in your slicer:
A. Orientation: The Art of Angle
How you position your model on the build plate is essential. Don’t just lay it flat! Proper orientation affects:
- Support Needs: Angling models (30-45 degrees) reduces surface area needing support, minimizing marks and easing removal.
- Surface Quality: Avoid printing large, flat surfaces parallel to the build plate to prevent suction issues during peeling. Angling helps lessen these forces and hides layer lines.
- Print Success: Gradual cross-sectional area changes reduce the force needed to peel each layer, boosting reliability.
- Detail Preservation: Position the model to protect fine details from heavy supports.
- Print Time: While angling may increase height (thus time), it can reduce peel forces, balancing the overall time.
General Rule: Experiment with different angles. Tilt your models! Avoid flat bases directly on the platform unless necessary, and even then, consider slight angling with a raft.
B. Supports: Building a Solid Foundation
In SLA printing, supports are crucial for:
- Overhangs and Islands: They anchor parts that would otherwise print in mid-air.
- Structural Integrity: Supports prevent warping or shifting during peeling.
- Initial Layers: They help lift the model slightly off the build plate to avoid over-curing.
Key Support Settings:
- Types:
- Light: Small contact points, easy to remove, good for delicate areas.
- Medium: A good balance for most situations.
- Heavy: Large contact points for heavier parts, harder to remove cleanly.
- Contact Point Size & Depth: Balance is key; smaller tips cause less damage but offer weaker holds, while larger tips are stronger but can leave marks.
- Density: Higher density means better support but more cleanup afterward.
- Shape: Adjust the upper/lower diameter to influence the support’s structure.
- Rafts: A thick base layer under supports improves adhesion and stability. Recommended for most prints.
- Auto vs. Manual Supports: Start with auto-generated supports, then manually refine them as needed. Always check the model layer-by-layer in the slicer preview.
C. Hollowing & Drainage Holes: Save Resin, Reduce Forces
For larger models, hollowing is a smart move:
- Saves Resin: Cuts down on material costs.
- Reduces Peel Forces: A hollow object has less surface area interacting with the FEP film.
- Lightens Weight: Makes handling easier.
But remember, if you hollow a model, you must add drainage holes!
- Why? Without holes, resin gets trapped inside during printing, and trapped liquid can expand and potentially crack the print during curing.
- Placement: Add at least two holes (one for drainage, one for air intake) at the lowest points of the model.
- Size: Make them large enough (3-5mm diameter) for easy draining.
D. Print Settings: The Numbers Game
These settings directly control the layer-by-layer curing process:
Setting | What it Does | Impact & Considerations | Typical Desktop Range (Resin Dependent!) |
Layer Height (mm) | Thickness of each individual layer. | Smaller = Higher detail, smoother curves, longer print time. Larger = Lower detail, more visible layer lines, faster print time. | 0.025 – 0.1 mm (0.05mm is common) |
Bottom Layer Count | Number of initial layers cured directly to the build plate. | These get extra exposure for strong adhesion. | 4 – 8 layers |
Bottom Exposure (s) | Exposure time per layer for the bottom layers. | CRITICAL for adhesion. Needs to be significantly longer than normal exposure. Too short = fails. Too long = hard removal. | 20 – 60+ seconds |
Normal Exposure (s) | Exposure time per layer for the rest of the model. | CRITICAL for detail & success. Resin-specific! Under-exposed = weak/failed print. Over-exposed = loss of detail, tight tolerances lost. | 1.5 – 8+ seconds |
Lift Distance (mm) | How high the build plate lifts after each layer exposure. | Must be high enough for FEP to peel and resin to flow back. | 5 – 10 mm |
Lift Speed (mm/min) | How fast the build plate lifts. | Faster = shorter print time, higher peel forces (riskier). Slower = longer print time, gentler peel (safer). | 40 – 180 mm/min |
**Retract Speed (mm/min) | How fast the build plate lowers back down. | Can usually be faster than lift speed. | 100 – 240 mm/min |
Light-Off Delay (s) | Pause after retracting before the UV light turns on for the next layer. | Allows resin to settle, prevents blurring/shifting. Important for viscous resins or high detail. | 0.5 – 2 seconds |
Anti-Aliasing (AA) | Blurs the edges of pixels on the LCD mask. | Smooths slanted surfaces, reduces visible voxel/pixel lines. Can slightly soften sharp details if set too high. | On/Off, Levels (e.g., 4x, 8x) |
Exposure time is one of the most crucial settings dependent on the resin you’re using. It’s essential to begin with the exposure recommendations provided by the resin manufacturer for your specific printer. After establishing these baseline settings, you should print calibration models, such as the “Resin XP2 Validation Matrix” or models from AmeraLabs, to fine-tune your exposure time. This process will help you achieve optimal detail and dimensional accuracy in your prints.
Step 4: Hardware Prep – Getting the Printer and Resin Ready
Software sorted? Great! Now it’s time to prep your physical equipment for the printing journey ahead:
Build Plate Leveling
This is crucial to ensure that the build plate is perfectly parallel to the LCD screen and FEP film, maintaining the correct initial gap (Z=0 height).
- Why It’s Vital: An uneven plate can cause one side to be too close (leading to squashed layers and difficult removal), while the other side might be too far (resulting in poor adhesion).
- How to Level: Follow your printer manufacturer’s instructions carefully. It usually involves loosening screws, homing the plate onto a piece of paper or directly onto the vat/FEP (using a spacer), applying gentle pressure, and then tightening the screws. Remember to re-level periodically or if you encounter adhesion issues.
Resin Vat Check
Before pouring resin, inspect the FEP or PFA film at the bottom of the vat:
- Look for Damage: Check for deep scratches, punctures, or dents that could lead to print failures (like light bleeding through or layers sticking) or even resin leaks onto your LCD screen—an expensive repair.
- Check Transparency: Ensure the film is not cloudy or foggy. Over time, the film can wear and become less transparent, potentially requiring longer exposure times or causing print failures.
- Cleanliness: Make sure the vat is free of any cured resin debris from previous prints. You can gently push from underneath the FEP to check for any stuck particles.
- FEP Tension: If applicable, check the tension of the FEP film—it should be taut like a drum skin. Loose FEP can lead to various issues.
- Replacement: If the film is damaged or worn, replace the FEP/PFA film, as it’s a consumable item.
Resin Preparation
- Wear Your PPE! Always put on nitrile gloves and safety glasses before handling resin.
- Shake the Bottle Vigorously: Resin components, including pigments and photoinitiators, can settle over time. Insufficient mixing can lead to inconsistent curing and failed prints. Shake the bottle for at least 30-60 seconds, making sure to listen for the mixing ball (if present). Try to avoid creating excessive bubbles.
- Filter If Necessary: If you’re reusing resin from a previous print (especially if it failed), filter it through a fine mesh filter (like paint filters) to remove cured particles that could damage the FEP or block light.
- Pour Carefully: Pour the well-shaken resin into the clean vat, avoiding splashes. Don’t overfill—adhere to the max fill line indicated on your vat.
- Temperature Matters: Most standard resins perform best at room temperature (around 20-25°C / 68-77°F). Cold resin is more viscous and can cause flow and peeling issues.
With your model sliced, settings adjusted, printer leveled, vat checked, and resin poured, you’ve successfully navigated the pre-printing phase. You’ve laid the groundwork and significantly increased your chances of a successful print. Now, you’re ready to transfer that file to the printer and initiate the light-curing process.
The Main Event: What Happens While Your SLA Printer is Running
You’ve done the prep work: your model is sliced, supports are meticulously placed, settings are dialed in, the printer is level, and the vat is filled with well-shaken resin. Now comes the moment of truth—hitting ‘Start’ and watching (or listening) as your SLA printer begins its mesmerizing light-curing dance.
This phase might seem passive since the machine does the work, but understanding what’s happening, what to listen for, and how to monitor the process can save you time, resin, and heartache. Let’s break down the printing process.
Step 1: Liftoff! Loading the File & Initiating the Print
First, you need to get the sliced file (the .ctb, .photon, .cbddlp, etc. file your slicer generated) onto the printer. Common methods include:
- USB Drive: This is the most common method for many desktop printers. Load the file onto a compatible USB stick, plug it into the printer, and use the printer’s touchscreen interface to navigate and select your file.
- Wi-Fi/Network Transfer: Some printers offer network connectivity, allowing you to send files directly from your slicer (like ChiTuBox or Lychee) over your local network. This method is often more convenient than dealing with USB drives.
- Cloud Services: Certain printer ecosystems might have cloud integration for file transfer and remote monitoring.
Once you select your file on the printer’s interface, you’ll typically see a final confirmation screen with a preview image, estimated print time, and key settings. Double-check that you’ve selected the correct file! Then, take a deep breath, ensure the printer’s protective cover or door is securely in place (to block ambient UV light and contain fumes), and press Start or Print.
Step 2: The Symphony of Creation – What’s Actually Happening?
As the printer comes to life, here’s a breakdown of the typical sequence and what you can expect:
- Homing & Lowering: The build platform usually performs a homing sequence (if it hasn’t already) and then slowly lowers into the vat of resin until it reaches the starting Z=0 position for the first layer.
- Bottom Layer Exposure: The light source (UV LEDs behind the LCD mask in MSLA printers) turns on, exposing the very first layer. This initial step takes longer due to the longer exposure times (e.g., 20-60 seconds). You might even see a faint glow of the UV light under the vat.
- The First Peel: This is often a tense moment. After the first layer cures, the build platform begins its lift sequence. You’ll likely hear a distinct “pop” or “snap” sound—it’s usually a good sign! This sound indicates that the newly cured layer is successfully peeling off the FEP film. A clean peel shows good adhesion to the build plate.
- Resin Flow & Retraction: The platform lifts to the set lift distance, allowing fresh resin to flow back into the gap underneath. It then retracts back down, preparing for the next layer.
- Normal Layer Cycle: The light source flashes on again, curing the next layer with a much shorter exposure time (e.g., 1.5-8 seconds). The platform lifts (another peel sound, possibly quieter), resin flows, it retracts, and the cycle repeats.
- Rinse and Repeat: This cycle of expose > lift (peel) > retract continues, layer by tiny layer. You’ll hear the rhythmic peeling sound and the whir of the Z-axis motor as the print gradually grows downwards from the build platform. The printer’s screen will typically display:
- Current layer number / Total layers
- Estimated time remaining (often inaccurate initially but becomes more reliable as the print progresses)
- A visual representation of the current layer being printed.
Step 3: Watching the Process – Monitoring Your Print
While you don’t need to stare at the printer the entire time, occasional monitoring—especially early on—is wise:
- Check Initial Adhesion: After the first 10-20 minutes, consider pausing the print briefly to check adhesion. Use a plastic scraper or tool to gently feel if the base/raft of your print is adhered to the build platform. Avoid metal tools while resin is present to prevent damaging the FEP film. If the print hasn’t stuck after 20 minutes, it might have failed at the adhesion stage. Stop the print, clean up, and troubleshoot (check leveling, bottom exposure, etc.).
- Listen for Consistent Peeling: The rhythmic peeling sound is a good indicator that the print is progressing normally. If the sound stops or changes significantly, it may signal a problem (like detachment from the supports or build plate).
- Look for Debris (Carefully!): If you suspect a failure (e.g., parts breaking off), you might see small cured pieces floating in the resin or stuck to the FEP film. Avoid poking around in the vat while printing. If there’s significant debris, it’s often best to pause or stop the print to prevent further damage.
- Monitor Temperature: Ensure the ambient temperature around the printer stays stable and within the recommended range for the resin (typically 20-25°C / 68-77°F). Significant temperature drops can affect resin viscosity and curing characteristics.
- Avoid Unnecessary Pauses: While it’s okay to pause for a quick initial check, frequent or prolonged pauses can introduce layer lines or adhesion issues. If everything seems fine, let the print run uninterrupted.
What if it Fails Mid-Print? If the print detaches from the build plate or supports and falls into the vat, stop the print immediately. Continuing will cure a flat sheet of resin onto the FEP film for every subsequent layer, wasting resin and creating a bigger cleanup job. You’ll need to filter the vat and clean the FEP and build plate before you try again.
Step 4: The Waiting Game – Factors Affecting Print Time
SLA printing isn’t always quick, especially for tall or high-resolution models. Several interconnected factors influence total print time:
- Model Height: This is the primary driver of print time. Taller objects require more layers, regardless of volume.
- Layer Height: Thinner layers (e.g., 0.025mm) result in more layers needed for the same height compared to thicker layers (e.g., 0.1mm), significantly increasing print time but improving vertical resolution.
- Exposure Time (Normal Layers): Even a second or two per layer adds up over thousands of layers. Faster-curing resins can shorten exposure times.
- Lift Speed & Distance: Slower lift speeds or longer lift distances increase the time spent moving between layers.
- Light-Off Delay: A small pause before each layer exposure contributes to the overall time.
- Bottom Layer Settings: Long bottom exposure times for prints with large bases can noticeably increase time upfront.
- Model Cross-Section: While MSLA/DLP cures layers simultaneously, very large cross-sections might benefit from slightly longer light-off delays or slower lift speeds to manage peel forces, indirectly affecting time.
Understanding these factors helps you estimate print times and make informed decisions when setting up your prints in the slicer—balancing speed, quality, and reliability.
Post-Processing: Beyond the Build Plate
Your SLA printer has finally fallen silent, and there it is—your freshly printed creation, glistening with uncured resin. Success! But hold on—you’re not done yet. In fact, you’ve just entered the most crucial phase for determining the final quality, strength, and safety of your print: Post-Processing.
Unlike FDM printing, where you might just pop a part off the bed and call it a day, SLA post-processing is absolutely necessary. That shiny, dripping object is still chemically active, potentially tacky, and coated in toxic uncured resin. Skipping or rushing through these next steps can lead to parts that are dimensionally inaccurate, brittle, sticky, or unsafe to handle.
Think of post-processing as refining your raw print into a finished product. It primarily involves three core steps: Washing, Support Removal, and Curing, followed by optional finishing touches. Let’s break down each step to ensure your stunning prints reach their full potential safely.
Safety First Reminder: Before you even think about touching that print or build platform, put on your PPE! Nitrile gloves and safety glasses are the bare minimum. Always work in a well-ventilated area.
Step 1: The Great Detachment – Removing the Print
Your first task is to detach the print from the build platform.
- Remove the Build Platform: Carefully unlock and remove the entire build platform from the printer arm, keeping it tilted so excess resin drips back into the vat. Some printers include holders for the platform to minimize mess.
- Prepare Your Workspace: Have a designated area ready, preferably covered with paper towels or a silicone mat to catch drips. Keep your removal tool handy.
- Choose Your Scraper: Most printers come with a scraper.
- Metal Scrapers: Effective for stubborn prints but use with extreme caution. Angle it low and try to slide it under the raft or base, avoiding gouging the print itself. Be mindful of scratching the build platform.
- Plastic Scrapers/Putty Knives: Safer for both you and the build plate but may struggle with very strong prints. A good first choice is a razor-blade plastic scraper.
- The Technique:
- Find an edge of the raft or the print’s base.
- Gently slide the scraper under the edge. A gentle tap on the back of the scraper with your (gloved) hand can help initiate separation.
- Work your way around, gradually prying the print loose. Listen for the crackling sound of separation.
- Avoid excessive force directly on delicate parts. Focus on the raft or base structure.
- Once loose, carefully lift the print off the platform. It will still be coated in sticky, uncured resin.
Step 2: The Big Clean-Up – Washing Away Uncured Resin
This step is crucial for removing all residual liquid resin from the print. If left on, it will cure improperly, affect the finish, obscure details, and pose a skin irritant.
- Purpose: Dissolve and remove all uncured liquid resin.
- Common Cleaning Agents:
- Isopropyl Alcohol (IPA): The most common solvent. Concentrations of 91% or ideally 99% are recommended. It evaporates relatively quickly but is highly flammable—use with excellent ventilation and away from ignition sources.
- Tripropylene Glycol Monomethyl Ether (TPM): A less volatile and less flammable alternative to IPA. However, it evaporates slowly, which may require an additional water wash step, and may not be compatible with all resins.
- Specialized Resin Cleaners: Some companies offer proprietary cleaning solutions designed for their resins—often less harsh than IPA but potentially more expensive.
- Water (ONLY for Water-Washable Resins): If you’re using “Water Washable” resin, you can clean the prints with plain tap water. Important: The resulting water is contaminated with resin and cannot be poured down the drain—it must be treated (filtered and UV cured) before disposal according to local regulations. Note that water-washable resins can sometimes be more brittle than standard resins.
Method | Pros | Cons | Best For |
Manual Dunk & Swish | Cheap, simple setup (two sealable containers). | Messy, requires manual agitation, less effective for complex geometries. | Occasional prints, small parts, low budget. |
Automated Wash Station | Convenient, consistent cleaning, often has timer, less direct handling. | Initial cost, takes up space, still requires solvent handling/disposal. | Regular printing, higher volume, convenience. |
Ultrasonic Cleaner | Very effective, cleans intricate details and internal channels well. | Can potentially damage very fine features if too aggressive, requires specific handling with flammable solvents (IPA). | Complex parts, high detail, batch cleaning. |
The two-bath method is an effective technique for cleaning your SLA prints to ensure they are free from uncured resin. Here’s how to do it:
- Dirty Wash:
- Process: Dunk and agitate the print in a container filled with used or dirty isopropyl alcohol (IPA) or another appropriate solvent. This initial wash helps remove the bulk of the uncured resin from the surface of the print.
- Clean Rinse:
- Process: After the dirty wash, transfer the print to a second container filled with clean IPA for a final rinse. This step ensures that any remaining residue from the first wash is removed, helping to keep your “clean” bath cleaner for longer.
- Maintaining Your Baths:
- Changing the Baths: When the dirty wash becomes too saturated with resin, dispose of it properly. Move the clean rinse to serve as the new dirty wash, and refill the clean rinse container with fresh solvent. Regular maintenance of your washing solutions is key to achieving the best results.
Washing Duration: How Long Should It Take?
The ideal duration for washing your prints can vary based on several factors:
- Factors to Consider:
- Size of the part
- Complexity (e.g., presence of internal channels)
- Resin viscosity
- Type of cleaning agent used
- Level of agitation applied during washing
- General Guideline:
- Typically, a washing duration of a few minutes (around 3-6 minutes) with active agitation or soaking in an automated washing station is sufficient for most prints.
- Caution Against Over-Soaking:
- It’s essential not to over-soak your prints. Leaving them in solvent (especially IPA) for too long (greater than 10-15 minutes) can result in the prints absorbing the solvent, leading to swelling and becoming overly soft. This can cause brittleness after curing or even develop surface cracks.
Drying Your Prints
After washing, it’s vital to ensure that your prints are completely dry before proceeding to the next steps (support removal or curing). Any residual solvent can interfere with the curing process and may leave white marks on the finished part.
- Drying Methods:
- Air Drying: Allow your prints to air dry. IPA evaporates quickly, making this a simple option.
- Compressed Air: You can also use compressed air to gently speed up the drying process and blow solvent out of crevices. Be cautious not to blast delicate parts with high pressure, as this could damage them. Additionally, placing the prints on paper towels can help absorb any excess solvent.
Step 3: Off With Their Heads! – Support Removal
Now that your print is clean and dry (some prefer to remove supports before washing), it’s time to take off the scaffolding.
Timing – Before or After Curing?
This is a topic of debate among users, each approach having its pros and cons:
- Before Curing:
- Benefits: The resin is slightly softer, making the supports easier to snip off. This requires less force, which can reduce the risk of damaging delicate features of the print. This method is often preferred.
- After Curing:
- Benefits: The part becomes stronger and less likely to break during removal. However, the supports may be harder and more brittle, which could lead to awkward snapping and leave worse marks (like divots or bumps). This method requires more force and careful handling.
Tools You’ll Need:
- Flush Cutters: Essential for support removal! Good quality, sharp flush cutters allow you to snip supports very close to the model surface, minimizing leftover nubs.
- Hobby Knife (X-Acto): Useful for precise trimming of stubborn support remnants or slicing through thicker supports. Handle this tool with care!
- Tweezers: Handy for pulling away small, detached support pieces.
- Needle Files / Sandpaper: Ideal for smoothing down contact points after removal, usually performed after curing.
Techniques for Effective Support Removal:
- Work Systematically: Start removing supports from the outer edges and more accessible areas, then work your way inward.
- Snip Close: Use flush cutters right against the model surface where each support tip connects.
- Gentle Wiggling/Twisting: For some supports, a slight twist with pliers or tweezers before snipping can help break the connection cleanly.
- Addressing Support Marks: You will typically have small marks or bumps where supports were attached. This is normal. Minimizing the size of the contact points in your slicer can help, but final finishing (like sanding) is often needed for a perfect surface.
Step 4: The Final Transformation – Post-Curing
Your washed, support-free print might look finished, but it is likely still only partially cured and hasn’t reached its optimal mechanical properties. The final mandatory step is UV Post-Curing.
Purpose of Post-Curing:
To fully polymerize the resin throughout the part, ensuring it achieves its intended hardness, strength, durability, and temperature resistance. This step also makes the part safer to handle long-term by cross-linking any remaining reactive molecules.
Methods for Post-Curing:
- Dedicated UV Curing Station:
- Best Option: These units provide controlled exposure using UV LEDs of the correct wavelength (usually 405nm, matching most resins), often with a turntable for even exposure and sometimes even temperature control.
- DIY UV Curing Box:
- Many users build enclosures lined with reflective material equipped with UV LED strips or lamps (ensure the wavelength is correct!). This method is less controlled but can be effective.
- Sunlight:
- While it’s free, sunlight is highly inconsistent. UV intensity can vary dramatically with weather, time of day, and season. Prolonged exposure can lead to over-curing or yellowing. Generally not recommended for reliable results but can work in a pinch for non-critical parts.
Importance of Wavelength:
Most common desktop SLA resins are designed to react optimally to UV light around the 405nm wavelength. Using a UV source with a significantly different wavelength (for example, many UV nail lamps operate at 365nm) may result in incomplete or inefficient curing. Always check your resin specifications to match your curing source accordingly.
Curing Time:
Curing time varies significantly based on several factors:
- Resin Type & Color: Clear resins cure faster than heavily pigmented, dark resins. Engineering resins might have specific requirements, so always check the manufacturer’s recommendations.
- Part Size & Thickness: Larger, thicker parts require more time for UV light to penetrate fully.
- Curing Unit Power: More powerful curing stations will typically cure faster.
- Target Properties: Functional parts requiring maximum strength may need longer cure times compared to simple display models.
- General Guideline: Curing times can range from a few minutes for small, clear parts in a powerful station to 30 minutes or even hours for large, opaque parts or using lower-power methods. Some users recommend curing in water (submerged) to block oxygen inhibition, leading to a harder, tack-free surface, although this adds complexity.
The Risk of Over-Curing:
Yes, it is possible to cure for too long! Over-curing tends to make resins more brittle, can cause yellowing (especially in clear or light-colored resins), and may lead to dimensional changes (shrinkage). It’s best to stick to recommended times whenever possible.
Step 5: The Finishing Touches (Optional but Recommended)
With the core post-processing complete, your part is functional and safe to handle, but you might want to elevate it further:
- Sanding: Use fine-grit sandpaper (wet sanding often yields good results) or needle files to smooth out support marks, faint layer lines, or other minor imperfections.
- Filling: Tiny pinholes or gaps can sometimes be filled with a drop of the same liquid resin (carefully cured with a UV flashlight) or specialized modeling putty.
- Priming: Applying a primer creates a uniform surface and improves paint adhesion if you plan to paint your model.
- Painting: Acrylic paints are commonly used; airbrushing provides the smoothest finish.
- Polishing: For clear resins, progressive sanding with increasingly fine grits (up to micro-mesh) followed by polishing compounds can achieve a glass-like transparency.
Mastering these post-processing steps transforms your SLA print from a raw output into a polished piece. It requires patience, attention to detail, and adherence to safety practices, but the stunning, high-resolution results are well worth the effort.
Liquid Gold: A Deep Dive into Choosing and Using SLA Resins
In the realm of SLA 3D printing, the printer provides the method, but the resin defines the result. Think of resin as the “ink” for your light-based printer—it’s the raw material transformed from liquid potential into solid reality. Unlike simple ink cartridges, the world of SLA resins is incredibly diverse, offering a broad spectrum of colors, properties, and functionalities.
Choosing the right resin is not only about aesthetics; it’s about matching the material characteristics to your specific needs. Using a basic, brittle resin for a functional part that needs to withstand stress is a recipe for disappointment. Conversely, using an expensive, high-temperature engineering resin for a simple display model is overkill.
Understanding the different types of resins available, their technical specifications, and proper handling techniques is crucial for unlocking the full potential of your SLA printer and ensuring your final parts meet your expectations. Let’s explore the fascinating and varied universe of photopolymer resins!
A Rainbow of Possibilities: Common Types of SLA Resins
Resin manufacturers are continuously innovating, but most resins fall into several broad categories based on their intended properties and applications:
- Standard Resins:
- What: These are the general-purpose workhorses of the SLA world, available in a wide array of colors (grey, white, black, clear, and various opaque and translucent shades).
- Properties: They typically offer good detail and a smooth surface finish, are relatively easy to print, but often tend to be somewhat brittle compared to engineering resins.
- Best For: Visual prototypes, concept models, miniatures, figurines, artistic prints, and general hobbyist use where high mechanical strength isn’t a primary requirement.
- Tough / Durable Resins (ABS-Like, Engineering Grade):
- What: Formulated to simulate the mechanical properties of common thermoplastics like ABS or polypropylene (PP), focusing on improved impact resistance, tensile strength, and flexibility.
- Properties: Less brittle and better able to withstand stress, bending, and impacts, though they may sacrifice some fine detail resolution.
- Best For: Functional prototypes that need testing, mechanical parts, jigs and fixtures, enclosures, and snap-fit components.
- Flexible Resins (TPU-Like, Rubber-Like):
- What: Designed to mimic rubber or TPU properties, remaining flexible and compressible after curing.
- Properties: High elongation and low shore hardness (measure of softness), good tear resistance. They can be tricky to print and may require heavy supports.
- Best For: Handles, grips, gaskets, seals, wearables, and shock absorbers.
- Castable Resins:
- What: A specialized category primarily for jewelry making and dental applications, designed to burn out cleanly during the investment casting process.
- Properties: High detail resolution is crucial, with clean burnout performance for creating accurate metal casts.
- Best For: Jewelry master patterns and dental frameworks.
- Biocompatible Resins (Medical / Dental Grade):
- What: Formulated and certified for specific applications involving direct contact with the human body, requiring rigorous testing and adherence to regulatory standards (e.g., ISO 10993).
- Properties: Must meet specific safety and non-toxicity requirements.
- Best For: Surgical guides, dental splints, and custom medical device prototypes.
- High-Temperature Resins:
- What: Engineered to withstand elevated temperatures after post-curing without significant deformation or loss of strength.
- Properties: High Heat Deflection Temperature (HDT), often more brittle at room temperature.
- Best For: Molds for injection molding or vacuum forming, heat-resistant fixtures, and airflow components.
- Water-Washable Resins:
- What: Designed to be cleaned with plain water instead of chemical solvents.
- Properties: Offers convenience but may be more brittle or absorb moisture over time. Contaminated wash water cannot go down the drain.
- Best For: Users wanting to avoid solvents, hobbyists, and prototypes where ultimate durability isn’t critical.
- Clear Resins:
- What: Standard or engineering resins formulated for optical clarity.
- Properties: Achieving true glass-like clarity requires meticulous post-processing.
- Best For: Lenses, light pipes, and transparent prototypes.
- Specialty Resins:
- What: A catch-all for unique formulations like ceramic-filled resins or high-speed draft resins.
- Properties: Highly varied based on the specific formulation.
- Best For: Niche applications requiring specific properties.
Decoding the Datasheet: Key Resin Properties Explained
When comparing resins, manufacturers provide technical datasheets (TDS) listing various mechanical and physical properties. Understanding these helps you make informed choices about which resin will best suit your project needs.
Property | What it Measures | Why it Matters | Units |
Viscosity | The resin’s thickness or resistance to flow. | Lower viscosity flows easily, good for fine details and faster printing/cleaning. Higher viscosity might be harder to clean, slower to level between layers. | mPa·s or cPs |
Hardness (Shore D/A) | Resistance to surface indentation (scratching, penetration). Shore D for hard plastics, Shore A for flexible rubbers. | Higher Shore D = harder, more scratch-resistant, often more brittle. Lower Shore A = softer, more flexible. | Shore D / Shore A |
Tensile Strength | Maximum stress a material can withstand while being pulled before breaking. | Higher value = stronger material under tension. Important for load-bearing parts. | MPa |
Young’s Modulus (Tensile Modulus) | Stiffness, or resistance to elastic deformation under tensile stress. | Higher value = stiffer material (less likely to bend). Lower value = more flexible. | GPa or MPa |
Elongation at Break | How much a material can stretch (as a % of original length) before breaking. | Higher value = more ductile, less brittle material. Tough resins have higher elongation than standard ones. Flexible resins have very high elongation. | % |
Impact Strength (Izod) | Ability to withstand a sudden impact or shock load without fracturing. | Higher value = tougher, less brittle material. Crucial for parts that might be dropped or hit. | J/m or ft·lb/in |
Heat Deflection Temp (HDT) | Temperature at which a material deforms under a specified load. | Indicates the maximum service temperature before the part loses rigidity. Critical for high-temp applications. | °C or °F |
Cure Speed / Exposure | How quickly the resin polymerizes under UV light. | Affects required exposure times per layer, thus overall print speed. Often listed as recommended settings for specific printers. | Seconds (s) |
Color / Transparency | The visual appearance of the cured resin. | Aesthetic choice, but pigments can affect cure times (darker colors often need longer exposure). Clarity is key for clear resins. | N/A |
Always refer to the manufacturer’s TDS for the specific resin you are considering, as properties can vary significantly even within the same category.
Making the Choice: Matching Resin to Application
Choosing the right resin for your project is crucial to achieving desired results. Here’s a quick guide to aligning different resin types with common goals:
- Detailed Miniatures / Display Models:
- Recommendation: Standard Resin (grey often preferred for detail visibility) or Clear resin for specific effects.
- Focus: Emphasize resolution and a smooth finish.
- Visual Prototypes (Looks-Like):
- Recommendation: Standard Resin.
- Note: Color might be important; mechanical properties are less critical.
- Functional Prototypes (Works-Like):
- Recommendation: Tough/Durable/ABS-Like Resin.
- Considerations: Evaluate tensile strength, impact strength, and elongation. Iterative testing may be necessary.
- Snap Fits, Jigs, Fixtures:
- Recommendation: Tough/Durable Resin.
- Focus: Achieve a balance between strength and some flexibility (elongation).
- Parts Needing Flexibility/Gaskets:
- Recommendation: Flexible Resin.
- Considerations: Check Shore Hardness and elongation properties.
- Jewelry / Dental Casting:
- Recommendation: Castable Resin.
- Priority: Ensure clean burnout during casting.
- Parts Exposed to Heat:
- Recommendation: High-Temperature Resin.
- Considerations: Check Heat Deflection Temperature (HDT) and determine if thermal post-curing is required.
- Avoiding Solvents / Simpler Cleanup:
- Recommendation: Water-Washable Resin.
- Note: Accept potential trade-offs in properties and manage wastewater properly.
- Medical/Dental (Patient Contact):
- Recommendation: Only certified Biocompatible Resins adhering to validated workflows.
Care and Feeding: Storing and Handling Your Resins
Resins are sensitive chemicals that require proper care to ensure performance and safety:
Storage:
- Keep resin in its original opaque bottle, tightly sealed.
- Store in a cool, dark, dry place away from direct sunlight or UV light sources, as UV exposure will start to cure the resin in the bottle!
- Maintain a stable temperature, generally within the range specified by the manufacturer (often 15-30°C or 60-86°F). Avoid extreme cold or heat.
Shelf Life:
- Resins have a limited shelf life (usually 1-2 years from manufacture; check the bottle). Expired resin may not cure properly or consistently.
Mixing:
- Always shake the bottle vigorously before each use (as discussed in the pre-printing section). Pigments and active ingredients settle over time, and insufficient mixing is a common cause of print failures.
Handling:
- Remember your Personal Protective Equipment (PPE) such as gloves and safety glasses. Avoid skin contact and work in a well-ventilated area.
Cross-Contamination:
- Use separate vats for different resin types if possible, or thoroughly clean the vat before switching resins to avoid mixing, which can negatively affect properties and curing.
Filtering:
- Filter any resin poured back into the bottle from the vat after a print, especially if there were any print issues, to remove potentially cured particles.
By understanding the diverse landscape of SLA resins and their specific properties, you can create objects that are suited for their intended purpose, whether that’s stunning visual detail, robust mechanical function, or specialized applications like casting or medical use. Choose wisely, handle safely, and happy printing!
Your Portal to Precision: Choosing and Maintaining Your SLA 3D Printer
The stunning detail and smooth finishes of Stereolithography (SLA) printing are captivating. However, the magic doesn’t just happen in the resin vat; the printer itself is the intricate machine orchestrating the light-curing process. Selecting the right SLA printer for your needs and budget, followed by diligent maintenance, are fundamental steps to achieving consistently high-quality results and ensuring your investment lasts.
Choosing Your Weapon: Factors to Consider When Buying an SLA Printer
Before making a purchase, consider the following factors:
- Budget:
- Entry-Level Desktop ($150 – $500): Excellent value, often MSLA/LCD based with smaller build volumes and good resolution (2K/4K common), ideal for hobbyists, miniatures, and smaller parts.
- Prosumer / Mid-Range ($500 – $2500): Larger build volumes, higher resolution (6K/8K+), faster monochrome screens, and more features (Wi-Fi, filters). Suited for serious hobbyists and small businesses.
- Professional ($2500+): Largest build volumes with specialized features (automated washing/curing, advanced sensors). Aimed at businesses, dental labs, and high-throughput environments.
- Build Volume (Print Size):
- Measured in X, Y, and Z dimensions (e.g., 120mm x 68mm x 150mm).
- Consider the largest single part you anticipate printing, and balance needed size against physical desk space and budget.
- Resolution & Detail:
- XY Resolution: Determines the finest detail possible in the horizontal plane, influenced by pixel size for MSLA/LCD printers. Smaller pixels result in higher XY resolution.
- Z Resolution (Layer Height): Minimum layer thickness the printer can achieve. Most modern SLA printers offer fine Z resolution (down to 0.01mm or 10 microns), with practical heights often between 0.025mm to 0.05mm.
- Light Source Technology:
- MSLA (Masked SLA) and LCD printers dominate the affordable desktop market, using a UV LED array and an LCD screen.
- Monochrome vs. Color LCD: Monochrome LCDs permit more UV light, leading to faster cure times and longer lifespan.
- Print Speed:
- Influenced by exposure time per layer and Z-axis lift/retract speeds. Reliability is often more important than raw speed.
- Ease of Use & Software:
- Evaluate the printer interface, slicer software compatibility, and community support.
- Ecosystem & Material Compatibility:
- Consider open vs. closed systems for resin compatibility. Assess the availability of replacement parts like FEP/PFA films and LCD screens.
- Brand Reputation & Reliability:
- Research specific models and brands, reading reviews from multiple sources and checking user forums for common issues.
- Extra Features (Nice-to-Haves):
- Wi-Fi connectivity, built-in air filtration, automated resin management, and heated vats can enhance convenience and performance.
Keeping the Magic Alive: Essential SLA Printer Maintenance
An SLA printer requires more regular maintenance than its FDM counterparts. Consistent upkeep prevents failures, extends the life of components, and ensures high print quality. Incorporate these routines into your workflow:
Routine Checks & Cleaning (Before/After Prints):
- Build Plate: Clean thoroughly with IPA and paper towels/microfiber cloth after removing a print. Ensure no cured resin remains.
- Resin Vat & FEP/PFA Film:
- Visual Inspection: Check for scratches, dents, or cloudiness before pouring resin or printing.
- Debris Check: Use the printer’s “vat clean” function or gently run a soft silicone spatula across the FEP to remove any cured bits.
- Cleaning Spills: Immediately wipe up any resin spills with IPA and paper towels.
- Gentle Cleaning: Use microfiber cloths and IPA on the FEP film, avoiding abrasive tools.
- Resin Filtering: Always filter resin poured back into the bottle using a fine mesh filter to catch any cured particles.
Periodic Maintenance:
- FEP/PFA Film Replacement:
- When: Replace when visibly damaged or when experiencing print failures related to peeling.
- Lifespan: Highly variable (20-100+ prints) depending on usage and care.
- Procedure: Follow your printer manufacturer’s instructions carefully.
- LCD Screen Care (MSLA):
- Protection: Prevent resin leaks onto the screen; consider adding a screen protector.
- Cleaning: If resin cures on the screen, gently lift it using a plastic razor blade and clean with IPA.
- Lifespan: Monochrome screens typically last longer than color screens, but still require replacement.
- Z-Axis Lead Screw: Keep clean from dust and resin drips. Lubricate only if recommended by the manufacturer.
- Firmware Updates: Occasionally check for firmware updates to fix bugs or improve performance.
- Calibration Checks:
- Leveling: Re-level the build plate periodically, especially after moving the printer.
- Exposure: Re-run exposure calibration tests when switching resin types or colors.
Investing time in choosing the right SLA printer based on your specific needs and dedicating effort to regular maintenance will pay off in reliable operation, stunning print quality, and a less frustrating 3D printing experience. Treat your machine well, and it will reward you with precision creations.
When Prints Go Wrong: Your Troubleshooting Guide for Common SLA Issues
You’ve meticulously prepared your model, dialed in your settings, handled your resin safely, and initiated the print, only to return to find a frustrating failure. Whether nothing stuck to the build plate, the model looks warped or separated, or it’s a tangled mess stuck to the FEP film, don’t despair! Print failures are a normal part of the learning curve with SLA 3D printing, even for experienced users.
Troubleshooting can feel like detective work, but by systematically identifying the symptoms and understanding potential causes, you can usually diagnose and fix the problem. This guide will walk you through some of the most common SLA printing failures, their likely culprits, and how to get your printer back on track to producing perfect prints.
Before You Start: Remember the golden rule of troubleshooting: Change only one variable at a time. If you alter leveling, exposure, and supports all at once, you won’t know which change fixed the issue (or made it worse). Be methodical!
Problem 1: Print Not Sticking to Build Plate (Complete Adhesion Failure)
Symptom: The build plate is completely clean (or has just a few tiny cured flecks), and a flat, pancake-like layer of cured resin is stuck to the FEP film at the bottom of the vat.
Potential Causes & Solutions:
- Build Plate Not Leveled Correctly / Z=0 Too High:
- Solution: Re-level your build plate carefully following your printer manufacturer’s instructions. Ensure the Z=0 height is set correctly for optimal “squish” of the first layers.
- Insufficient Bottom Layer Exposure Time:
- Solution: Increase the ‘Bottom Exposure Time’ in your slicer settings by 5-10 seconds initially and test again. Refer to your resin manufacturer’s recommendations.
- Build Plate Surface Contamination:
- Solution: Clean the build plate thoroughly with Isopropyl Alcohol (IPA) and a clean paper towel or microfiber cloth. Optionally, lightly scuff the surface with fine-grit sandpaper to improve mechanical adhesion.
- Resin Temperature Too Low:
- Solution: Ensure your printing environment is warm enough (20-25°C or 68-77°F). Consider gently warming the resin bottle before use.
- FEP Film Too Cloudy or Damaged:
- Solution: Inspect the FEP film. If it’s extremely cloudy or damaged, replace it.
- Build Plate Surface Too Smooth:
- Solution: Sand the build plate surface gently or ensure your slicer settings include a substantial raft under your print for increased adhesion.
Problem 2: Print Sticking to FEP Film Instead of Build Plate or Previous Layer
Symptom: The print adheres to the build plate initially but later layers detach and stick to the FEP film.
Potential Causes & Solutions:
- Insufficient Normal Layer Exposure Time:
- Solution: Slightly increase the ‘Normal Exposure Time’ (e.g., by 0.5 seconds) and use resin calibration tests to find optimal exposure.
- Lift Speed Too High:
- Solution: Decrease the ‘Lift Speed’ in your slicer settings to reduce suction forces during peeling.
- Insufficient Support Structures (Islands/Overhangs):
- Solution: Review your supports in the slicer preview. Ensure all islands have adequate support.
- FEP Film Nearing End of Life / Damaged:
- Solution: Inspect and replace the FEP film if it’s worn, cloudy, or damaged.
- Large Cross-Sectional Areas:
- Solution: Re-orient the model to minimize flat surfaces parallel to the build plate. Consider hollowing the model and adding drain holes.
- Insufficient Lift Distance:
- Solution: Ensure the ‘Lift Distance’ (typically 5-10mm) is adequate for your setup.
Problem 3: Layer Separation / Delamination / Skipping Layers
Symptom: Visible horizontal cracks or gaps within the print, with missing entire sections.
Potential Causes & Solutions:
- Under-Exposure (Normal Layers):
- Solution: Increase ‘Normal Exposure Time’ slightly and recalibrate your resin.
- Lift Speed Too High:
- Solution: Decrease the ‘Lift Speed’.
- Pausing the Print:
- Solution: Avoid pausing prints unless necessary. If you must, keep it brief.
- Temperature Fluctuations:
- Solution: Maintain a stable room temperature within the resin’s optimal range.
- Debris in Resin / Dirty Optics:
- Solution: Filter your resin and ensure the LCD screen and FEP film are clean.
- Insufficient Light-Off Delay:
- Solution: Increase the ‘Light-Off Delay’ slightly (e.g., by 0.5-1 second).
- Mechanical Issues (Z-Axis):
- Solution: Ensure the Z-axis lead screw is clean and properly lubricated.
Problem 4: Warping or Curling
Symptom: Parts of the print lift or curl away from the build plate, often detaching from supports.
Potential Causes & Solutions:
- Insufficient or Poorly Placed Supports:
- Solution: Add more supports, especially around edges and corners of flat areas.
- Uneven Curing / Shrinkage:
- Solution: Ensure appropriate exposure times and consider part orientation to distribute stress.
- Temperature Changes:
- Solution: Maintain a stable temperature environment during printing.
- Aggressive Washing/Curing:
- Solution: Follow recommended washing times and ensure even UV exposure during post-curing.
Problem 5: Surface Imperfections
Symptom: Issues affecting the surface quality of the print.
- Ragging:
- Cause: Light scattering or reflection causing unintended curing around layer edges.
- Solution: Reduce exposure time, ensure adequate edge support, and improve part orientation.
- Visible Voxel/Pixel Lines:
- Cause: Limitations of the LCD pixel grid.
- Solution: Enable Anti-Aliasing (AA) in your slicer and consider using smaller layer heights.
- Blooming / Loss of Detail / Over-Curing:
- Cause: Excessive exposure time causing light bleed.
- Solution: Reduce exposure time and calibrate for sharp details.
Problem 6: Support Failures / Difficult Support Removal
Symptom: Supports break mid-print or are difficult to remove without damaging the print.
Potential Causes & Solutions:
- Weak Supports:
- Solution: Increase support density, diameter, or contact point size.
- Poor Support Placement:
- Solution: Manually adjust auto-generated supports for better stability.
- Exposure Issues:
- Solution: Calibrate exposure times and adjust support contact point settings accordingly.
- Aggressive Lift Speeds:
- Solution: Reduce lift speed.
- Removal Technique:
- Solution: Use sharp flush cutters and remove supports carefully, ideally before final curing.
Problem 7: Dimensional Inaccuracy
Symptom: The final print dimensions do not match the digital model.
Potential Causes & Solutions:
- Resin Shrinkage:
- Solution: Account for expected shrinkage in your CAD design if high precision is needed.
- Incorrect Exposure:
- Solution: Calibrate exposure time using dimensional accuracy tests.
- Blooming/Light Bleed:
- Solution: Ensure correct exposure and consider resins known for lower light bleed.
- Warping/Distortion:
- Solution: Address causes of warping as mentioned in Problem 4.
Conclusion
Troubleshooting SLA failures is an iterative process. Keep detailed notes of your settings, the failures encountered, and any adjustments made. Regularly utilize calibration prints, especially with new resins. Don’t hesitate to consult online communities, forums, and manufacturer documentation. With patience and a methodical approach, you’ll learn to interpret the signs and overcome common printing problems. Happy diagnosing!
Where Does SLA Fit In? Comparing Stereolithography to Other 3D Printing Titans
Stereolithography (SLA) is renowned for producing prints with breathtaking detail and smooth surfaces, making it a powerhouse in the additive manufacturing landscape. However, it’s not the only technology available. Other methods, such as Fused Deposition Modeling (FDM) and Selective Laser Sintering (SLS), each offer unique advantages and disadvantages. Understanding how SLA stacks up against these technologies is crucial for selecting the right 3D printing method for your specific project needs, whether you prioritize intricate detail, functional strength, material variety, or cost-effectiveness.
Let’s explore the key differences between SLA and these other common 3D printing methods.
SLA vs. FDM (Fused Deposition Modeling): The Classic Showdown
FDM is perhaps the most recognized 3D printing technology, utilized in hobbyist workshops and industrial settings alike. It works by melting plastic filament and extruding it layer by layer through a nozzle. Here’s how SLA compares to FDM:
Feature | SLA | FDM |
---|---|---|
Core Technology | Vat Polymerization – Cures liquid resin with UV light. | Material Extrusion – Melts and deposits thermoplastic filament. |
Resolution & Detail | Major Advantage. Capable of finer details with smaller layer heights (e.g., 25-50 microns). XY resolution determined by light source precision, leading to very sharp features. | Limited by nozzle diameter (typically 0.4mm) and layer height (typically 100-300 microns). Fine details can be challenging to achieve. |
Surface Finish | Major Advantage. Produces very smooth surfaces directly from the printer; layer lines are often almost invisible. | Distinct, visible layer lines are characteristic; achieving a smooth surface usually requires significant post-processing. |
Material Variety & Properties | Growing range of resins (standard, tough, flexible, castable, biocompatible, high-temp, clear). Standard resins are usually brittle, while engineering resins improve properties but can be costly. Materials are thermosets and cannot be re-melted. | Major Advantage. Extensive variety of well-established, robust, and affordable thermoplastic filaments (PLA, PETG, ABS, ASA, Nylon, TPU, PC, composites). Many are suitable for end-use parts with excellent functional strength and durability. |
Strength & Durability | Parts tend to be isotropic (strength is similar in all directions), but standard resins are brittle. Tough SLA resins offer better impact resistance and flexibility, competing with some FDM materials but often at a higher cost. | Parts are typically anisotropic (stronger along printed lines, weaker between layers), with critical layer adhesion. Materials like PETG, ABS, and Nylon can be very strong and durable, often preferred for functional parts. |
Print Speed | It Depends. SLA (MSLA/DLP) cures entire layers at once, so speed is mainly dependent on height, not complexity. For short, intricate parts, SLA can be faster. | Speed depends on volume, complexity, and infill settings. For tall, bulky parts or filling the build plate horizontally, FDM can often be faster. |
Cost (Printer & Materials) | Generally higher ongoing costs (resin, IPA/solvents, replacement FEP films, potential LCD screen replacement). Entry-level printers are affordable, but material costs can add up. | Generally lower entry cost for printers, and filament is significantly cheaper per unit weight/volume compared to resin. |
Ease of Use & Post-Processing | Requires mandatory multi-step post-processing (washing, support removal, UV curing). Handling liquid resins requires strict safety protocols (PPE, ventilation) and can be messy. Support removal needs careful handling to avoid damaging smooth surfaces. | Can be simpler initially (no chemicals, less mess). Post-processing often involves support removal and optional smoothing/finishing, though dialing in settings can have a steep learning curve. |
SLA vs. SLS (Selective Laser Sintering): The Industrial Powerhouse
SLS is another prominent 3D printing technology that uses a laser to sinter powdered material, binding it together to create a solid structure. Here’s how SLA compares to SLS:
Feature | SLA | SLS |
---|---|---|
Core Technology | Vat Polymerization – Cures liquid resin with UV light. | Powder Bed Fusion – Uses a laser to sinter powdered material. |
Resolution & Detail | Major Advantage. Capable of intricate details and smooth finishes due to liquid resin properties. | Generally good resolution, but the surface finish may not be as smooth as SLA. |
Surface Finish | Major Advantage. Produces smooth surfaces directly from the printer. | Often requires post-processing for surface smoothing; surface finish can be grainy due to the nature of powdered materials. |
Material Variety & Properties | Growing range of resins; materials are thermosets. | Wide variety of materials, including nylon, metals, and elastomers. SLS materials can be thermoplastics that can be re-melted and recycled. |
Strength & Durability | Parts are isotropic, but standard resins may be brittle. Tough resins provide better performance. | Parts are typically strong and durable, suitable for functional applications, and can be reinforced with additives. |
Print Speed | SLA can be faster for small, intricate parts. Speed depends on layer height. | SLS can be slower for smaller parts but is efficient for bulk production due to the ability to pack multiple parts in a single build. |
Cost (Printer & Materials) | Higher material costs; initial printer prices can be lower. | Generally higher initial investment for printers, but material costs can be economical for larger production runs. |
Ease of Use & Post-Processing | Multi-step post-processing required. Liquid resin handling is messy. | Minimal post-processing; parts are usually self-supporting due to the powder bed but require cleaning to remove excess powder. |
Conclusion
Choosing the right 3D printing technology depends on your specific project requirements. SLA excels in producing high-detail, smooth-surface parts suitable for prototypes, jewelry, and intricate designs. FDM is the go-to for functional parts with a vast array of materials at an affordable price. SLS shines in industrial applications with strong, durable parts and the ability to produce functional prototypes.
Understanding each technology’s strengths and weaknesses will empower you to make informed decisions based on your project’s needs, budget, and material requirements. Whether you lean toward the precision of SLA, the versatility of FDM, or the industrial capabilities of SLS, each technology has its rightful place in the 3D printing landscape.
Beyond the Benchtop: Where SLA Printing Makes Its Mark – Real-World Applications
We’ve journeyed through the intricate process of Stereolithography (SLA), from digital design to fully cured parts. We understand its strengths—remarkable detail, smooth finishes, and specialized materials. But where does this technology move beyond theory and process into practical, real-world impact? Where are those stunningly precise parts actually being used?
The answer is: in a surprisingly diverse range of fields! SLA isn’t just for hobbyists printing intricate figurines (though it excels at that). It’s a powerful tool enabling innovation across engineering, healthcare, design, manufacturing, and art. Exploring these applications helps solidify why someone might choose SLA and inspires new ways to leverage its unique capabilities. Let’s delve into the key areas where SLA printing is making a significant difference.
1. High-Fidelity Prototyping (Concept & Visual Models)
- The Need: Designers and engineers require rapid iterations on ideas, physical models for ergonomic testing, and visual designs for client showcases before committing to expensive tooling for mass production.
- Why SLA?
- Unmatched Detail & Smoothness: SLA captures fine features and complex curves with exceptional fidelity, producing prototypes that resemble the final product closely.
- Accuracy: SLA can create dimensionally accurate parts, essential for verifying component fit (form/fit testing).
- Speed for Visuals: SLA can produce highly detailed visual models relatively quickly compared to traditional methods or achieving the same finish with FDM.
- Examples: Consumer product enclosures (smartphones, remote controls), detailed architectural models, concept car dashboards, and packaging prototypes.
2. Jewelry Design & Manufacturing (Investment Casting Patterns)
- The Need: Jewelers need highly detailed master patterns of rings, pendants, and intricate pieces to create molds for investment casting in precious metals.
- Why SLA?
- Exceptional Detail: SLA reproduces tiny prongs, filigree, and intricate surface details essential for jewelry.
- Smooth Surface Finish: Reduces manual finishing required on the final metal cast.
- Castable Resins: Specialized resins burn out cleanly during casting, leaving minimal ash residue, which is critical for perfect metal casting.
- Examples: Custom engagement rings, detailed pendants, intricate bracelet charms printed in castable resin to create molds for final metal pieces.
3. Dental Applications (Guides, Models, Aligners)
- The Need: Dentistry requires high precision for patient-specific devices like surgical guides, orthodontic aligners, crowns, and highly accurate dental models.
- Why SLA?
- Accuracy & Resolution: Essential for ensuring devices fit perfectly in a patient’s mouth and that surgical procedures are accurately guided.
- Biocompatible Resins: Certified resins are available for devices intended for direct patient contact, meeting strict regulatory standards.
- Specialized Materials: Resins mimicking dental stone for accurate models and clear resins for aligners are available.
- Speed & Customization: Enables rapid production of custom devices from digital scans, improving workflow efficiency in dental labs and clinics.
- Examples: Drill guides for implant surgery, clear orthodontic aligners, highly accurate diagnostic dental models, and temporary crowns/bridges.
4. Medical Modeling & Surgical Planning
- The Need: Surgeons benefit from accurate physical models of a patient’s unique anatomy derived from CT or MRI scans, aiding in pre-operative planning and patient education.
- Why SLA?
- Anatomical Accuracy: SLA creates detailed anatomical replicas, capturing complex structures.
- Visualization: Models can be printed in clear or specific colors, improving understanding of spatial relationships.
- Biocompatible Options: While many models don’t need biocompatibility, guides used during surgery do, and SLA offers certified options.
- Examples: Patient-specific heart models for congenital defect repairs, bone models for reconstructive surgery, and models of complex tumors.
5. Miniatures, Figurines & Hobbyist Creations
- The Need: The tabletop gaming and collectibles market thrives on highly detailed miniatures and character figures, with hobbyists demanding crisp details and smooth surfaces.
- Why SLA?
- Supreme Detail: SLA perfectly captures tiny features, intricate details, and textures often impossible with FDM.
- Smooth Finish: Provides an ideal canvas for painting, minimizing the need for sanding layer lines.
- Accessibility: Affordable desktop SLA printers have made this capability available to hobbyists.
- Examples: Custom D&D character miniatures, detailed sci-fi or fantasy figures, and intricate busts.
6. Small Batch Production, Jigs & Fixtures
- The Need: Manufacturing environments often require custom jigs, fixtures, or small runs of specialized parts where tooling costs for injection molding would be prohibitive.
- Why SLA?
- Accuracy & Complexity: SLA can produce precise and complex geometries needed for custom tooling.
- Engineering Resins: Tough, durable, and high-temperature resins allow SLA parts to withstand mechanical stress.
- Cost-Effectiveness: Faster and cheaper to produce low volumes of custom tools compared to traditional CNC machining.
- Examples: Assembly jigs, inspection fixtures, custom end-of-arm tooling for robots, and short runs of specialized electronic enclosures.
7. Artistic Expression & Sculptural Forms
- The Need: Artists explore new mediums to bring complex and intricate forms to life.
- Why SLA?
- Geometric Freedom: Allows for the creation of highly complex and organic shapes.
- Surface Quality: The inherent smoothness can be a desired aesthetic or a good base for further artistic finishing.
- Material Variety: Clear, colored, and standard resins offer different visual possibilities.
- Examples: Intricate sculptures, complex geometric art pieces, and unique decorative items.
Conclusion: Your Journey into High-Resolution SLA Printing Starts Now
We’ve explored the complete journey of Stereolithography (SLA) 3D printing, from the initial digital spark to the final, fully cured object. We demystified photopolymerization, navigated pre-printing setup, monitored the light-curing process, and meticulously worked through essential post-processing steps. We also examined the diverse world of resins, discussed printer selection and maintenance, emphasized safety protocols, tackled common troubleshooting scenarios, and highlighted real-world applications of SLA.
The SLA Advantage: SLA printing offers unparalleled detail and surface smoothness by using UV light to selectively cure liquid resin, layer by intricate layer. Success hinges on mastering the entire workflow:
- Pre-Printing: Strategic model orientation, robust support generation, careful slicing, and printer/resin preparation are vital.
- Printing: While largely automated, monitoring the initial layers provides valuable feedback.
- Post-Processing: This hands-on phase—washing away uncured resin, removing supports, and post-curing—is crucial for achieving the desired final properties and safety.
Facing the Reality: The allure of SLA lies in producing parts with stunning visual fidelity, making it ideal for intricate models, jewelry casting, and precise medical applications. However, it’s important to acknowledge that SLA printing is messier than FDM, involving liquid chemicals that require strict safety precautions. Multi-step post-processing demands patience and diligence; while entry-level printers may be affordable, ongoing costs for resin and consumables are typically higher than for FDM.
Looking Ahead: The SLA landscape is evolving with trends towards:
- Faster printing through innovations in resin and light sources.
- New materials with improved properties.
- Larger formats and increased automation for streamlined workflows.
- Greater accessibility with falling prices and user-friendly software.
Your Turn to Create: Whether you’re inspired to purchase your first SLA printer, eager to refine existing techniques, or simply appreciate the technology, we hope this guide has equipped you with the knowledge and confidence to embark on your SLA journey. The potential to create intricate, beautiful, and functional objects is literally at your fingertips—protected by nitrile gloves, of course!
Don’t be intimidated by the process; embrace the learning curve. Start with simple models, prioritize safety, and don’t hesitate to consult online communities, manufacturer resources, or tutorials.
We encourage you to dive in! Ask questions, share your SLA triumphs and challenges, or explore further resources. The world of high-resolution 3D printing awaits.
Happy Printing!