Ever envisioned grasping a convoluted, operational entity in your palm, crafted directly from a digital blueprint? This vision materializes courtesy of Selective Laser Sintering (SLS) 3D printing innovation. In contrast to conventional filament-based techniques, SLS employs a laser to amalgamate powdered synthetic materials incrementally, fabricating exceptionally robust and precise components.
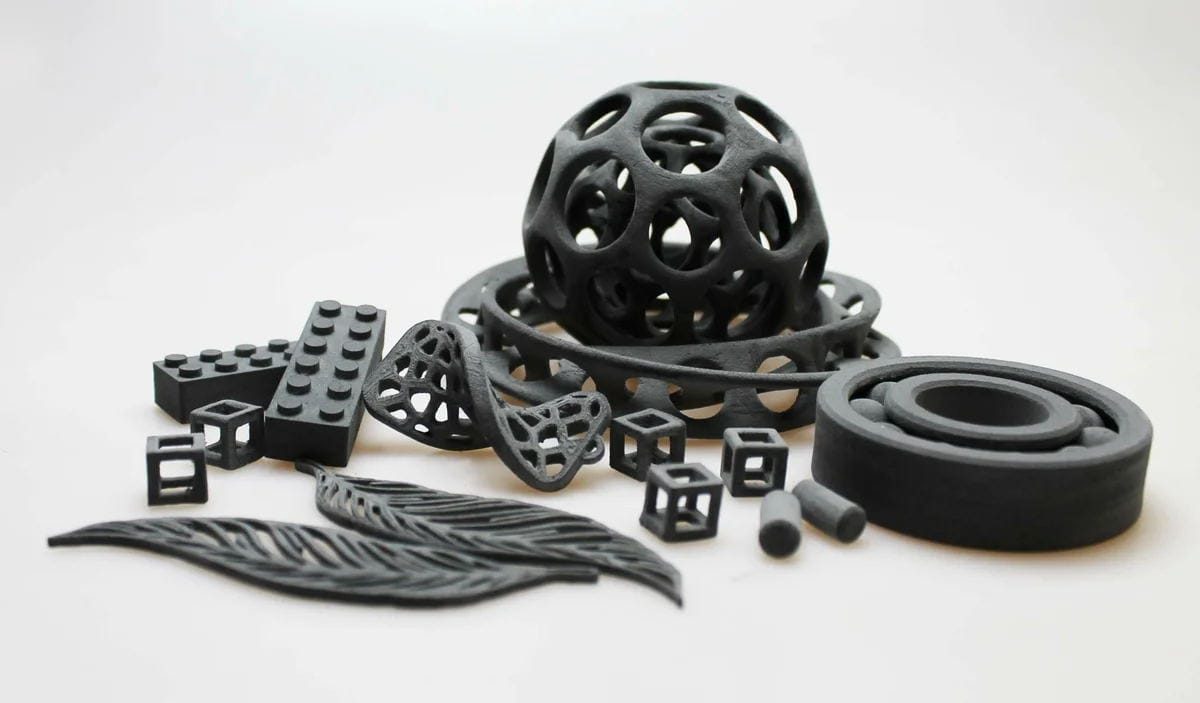
This transcends mere creation of aesthetically pleasing forms – SLS heralds a paradigm shift across sectors ranging from aerospace to healthcare. Picture featherweight components for spacecraft or bespoke surgical implements, all fabricated with unparalleled accuracy and creative liberty.
Deep Dive into SLS Applications by Industry
Selective Laser Sintering (SLS) 3D printing isn’t a one-size-fits-all solution. Its unique capabilities shine in various industries, each with its own set of challenges and exciting possibilities. Let’s take a comprehensive look at how SLS is transforming these sectors:
Soaring High in Aerospace & Defense
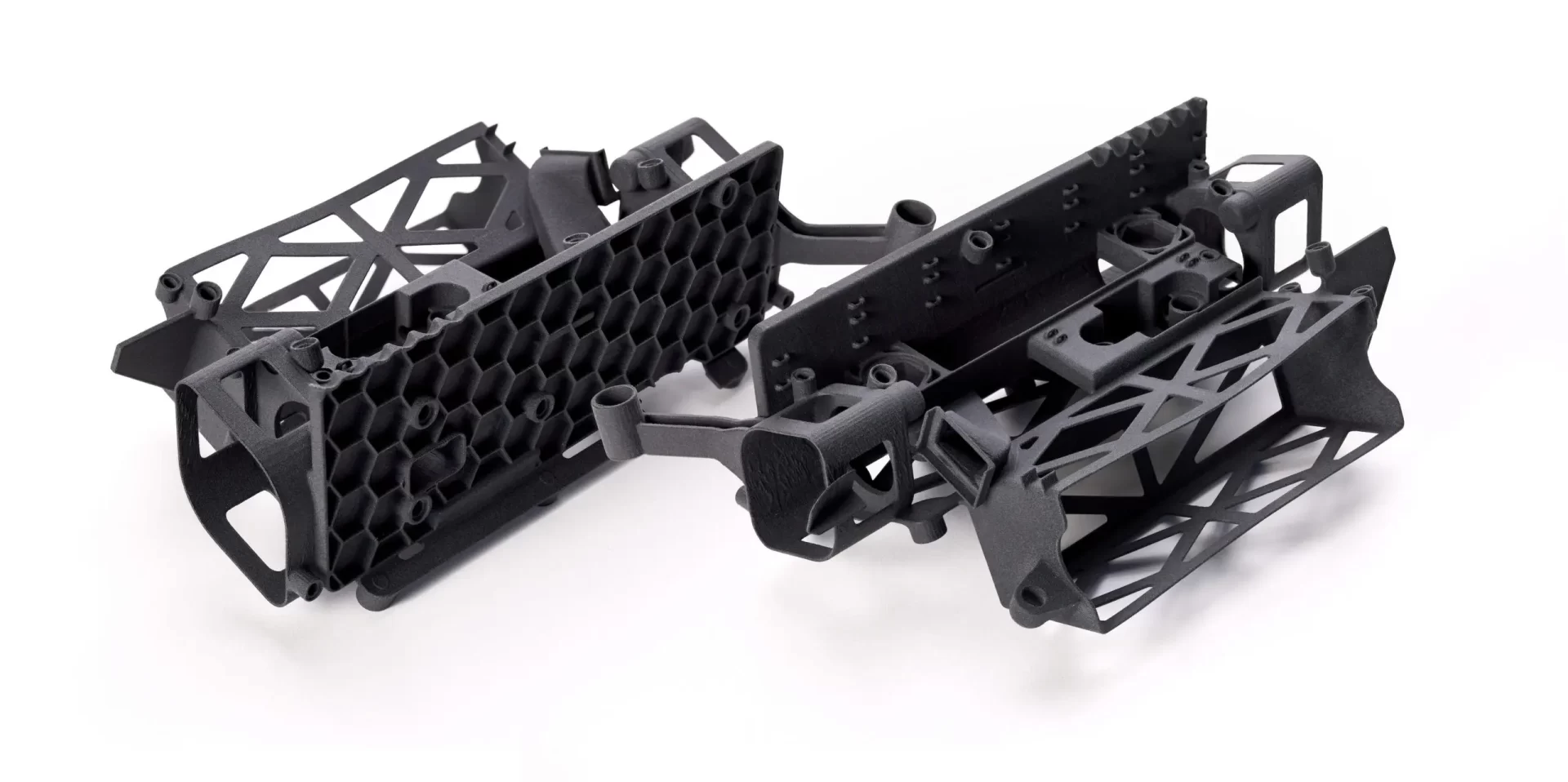
The aerospace industry demands lightweight yet high-strength materials for everything from spacecraft to fighter jets. SLS perfectly fits the bill, offering several advantages:
- Reduced Weight: SLS parts can be significantly lighter than traditionally manufactured components, leading to improved fuel efficiency and overall aircraft performance.
- Complex Designs: SLS excels at creating intricate geometries with internal channels and lattices, optimizing weight and part functionality.
- Functional Prototypes: Aircraft require rigorous testing before mass production. SLS allows for the creation of realistic prototypes that undergo wind tunnel testing and functional performance evaluation.
Taking Flight with SLS Applications:
- Spacecraft components: From satellite housings to antenna brackets, SLS produces lightweight and durable parts for space exploration.
- Drone components: Complex and customized drone parts like airframes and internal structures can be readily created using SLS.
- Wind tunnel models: Highly accurate wind tunnel models for testing aerodynamic properties can be rapidly produced using SLS.
- Customized air ducts: Aircraft often require specialized air ducts for efficient airflow. SLS enables the creation of complex and customized ducts for optimal performance.
Challenges and Considerations:
Strict regulations and stringent testing requirements are a hallmark of the aerospace industry. SLS parts need to meet these rigorous standards, and manufacturers must ensure proper certifications for materials and processes.
Here’s a table summarizing the key points:
Benefit | Application Examples | Challenge |
Lightweight Parts | Spacecraft components, Drone components | Strict regulations and testing requirements |
High Strength | Wind tunnel models | Material certifications needed |
Complex Designs | Customized air ducts |
This is just the beginning of SLS’s journey in the aerospace industry. As technology advances and materials improve, we can expect to see even wider adoption of SLS for critical aerospace applications.
Revving Up the Future: SLS 3D Printing in Automotive
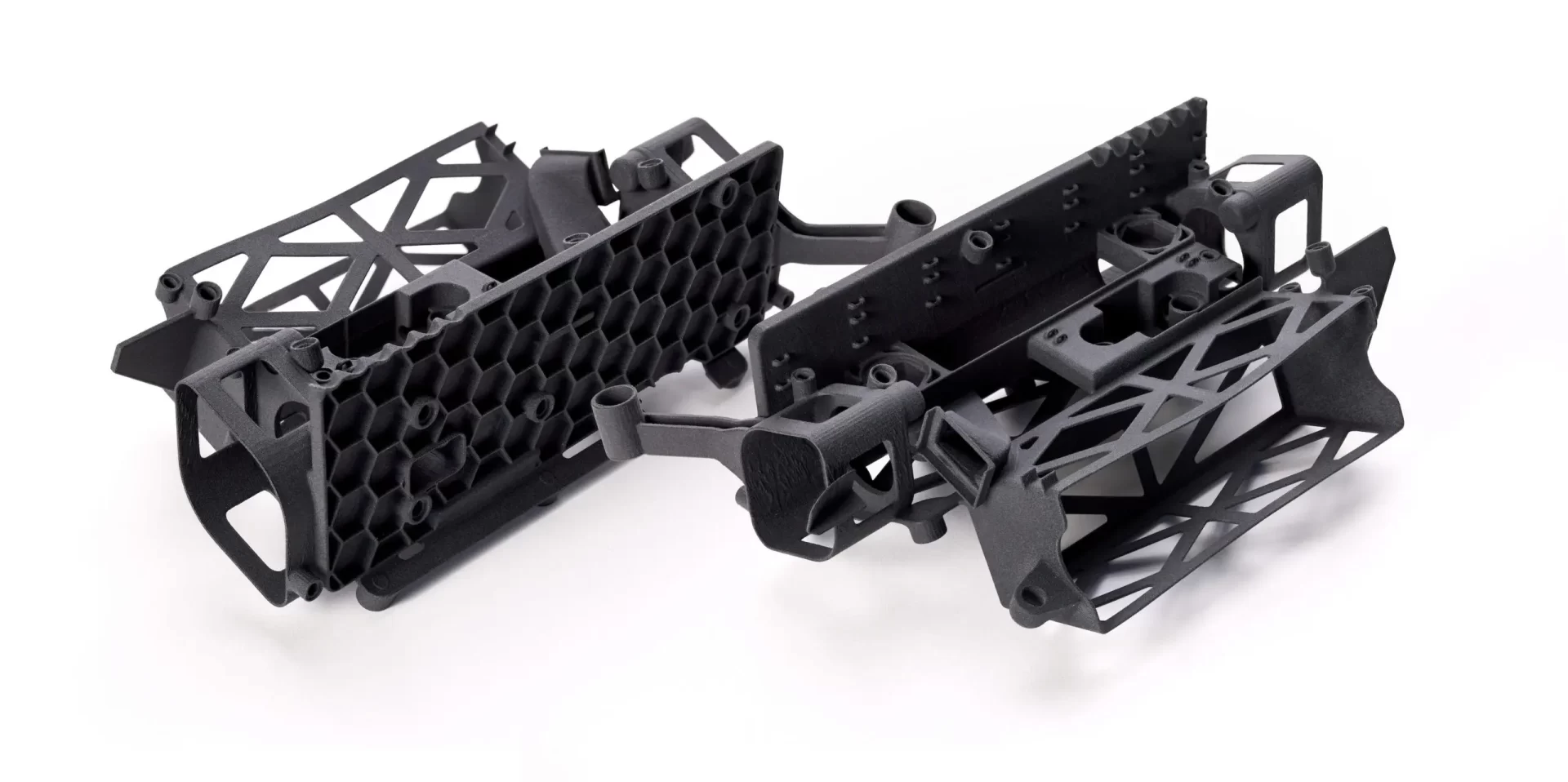
Imagine a world where car manufacturers can create not just concept car models, but also functional prototypes and even low-volume production parts – all with incredible speed and design freedom. This is the exciting reality brought on by SLS 3D printing in the automotive industry.
For carmakers, SLS offers a unique set of benefits:
- Rapid Prototyping: Gone are the days of lengthy and expensive traditional prototyping methods. SLS allows for the creation of realistic and functional prototypes in a fraction of the time, accelerating the design and development process.
- Low-Volume Production: SLS is perfect for producing limited-edition parts, customized components, or even short-run production of niche vehicles. This flexibility helps manufacturers cater to diverse needs and experiment with innovative designs.
- Jigs & Fixtures: SLS excels at creating complex jigs and fixtures used on the assembly line. These tools can be customized for specific needs and produced on-demand, streamlining production processes.
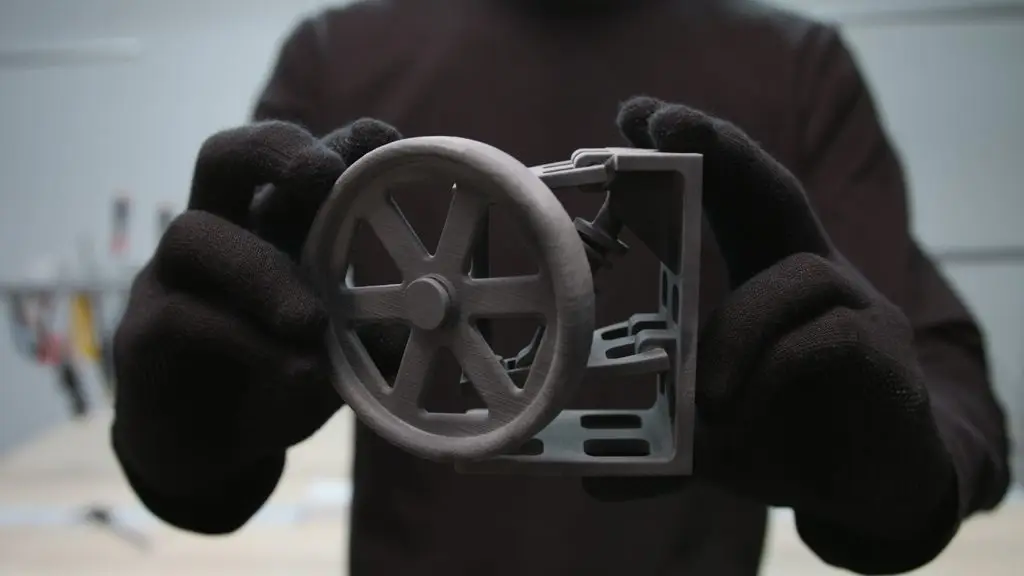
Under the Hood of SLS Applications:
- Jigs & Fixtures: SLS-printed jigs and fixtures can hold car parts in place during assembly, ensuring accuracy and repeatability. Complex internal channels and customized features are easily achievable with SLS.
- Concept Car Models: Eye-catching concept car models showcasing innovative designs can be rapidly produced using SLS. The technology allows for the creation of intricate details and smooth finishes, perfect for captivating audiences.
- Race Car Parts: High-performance race cars often require lightweight and aerodynamic components. SLS is ideal for producing customized parts like air intake ducts, spoilers, and even certain engine components.
- Wind Tunnel Models: Accurate wind tunnel models for testing car aerodynamics can be efficiently created using SLS. This allows for design optimization and improved fuel efficiency.
- Customized Engine Components: Certain low-stress engine components, like water pump housings or intake manifolds, can be produced using SLS for prototyping or limited-run applications.
Challenges and Considerations:
When it comes to automotive applications, factors like heat resistance and wear & tear properties are crucial. While SLS materials are constantly evolving, some may not be suitable for high-stress engine parts exposed to extreme temperatures.
Here’s a table summarizing the key points for SLS in Automotive applications:
Benefit | Application Examples | Challenge |
Rapid Prototyping | Concept car models, Race car parts | Material properties like heat resistance |
Low-Volume Production | Jigs & Fixtures, Customized components | Wear & tear properties for certain parts |
Despite these considerations, SLS is rapidly transforming the automotive industry. As materials become more advanced and production processes are further optimized, we can expect to see SLS playing an even greater role in the future of car design and manufacturing.
Healing Touches: SLS 3D Printing in Medical & Healthcare
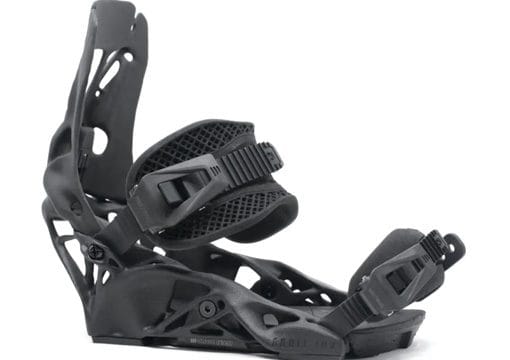
The field of medicine is constantly pushing boundaries, and SLS 3D printing is emerging as a powerful tool for improving patient care. Unlike traditional manufacturing methods, SLS offers several advantages perfectly suited for medical applications:
- Biocompatible Materials: Certain SLS materials are biocompatible, meaning they can be safely implanted in the body. This opens doors for the creation of customized prosthetics, implants, and even surgical instruments.
- Complex Geometries: SLS excels at producing intricate shapes with internal structures and latticework. This allows for the creation of prosthetics that mimic natural bone structures or medical models with highly realistic details.
- Patient-Specific Customization: Using medical scans, SLS can create personalized implants and prosthetics perfectly tailored to a patient’s unique anatomy. This level of customization can significantly improve surgical outcomes and patient recovery.
From Scan to Surgery: A Look at SLS Applications in Medicine
- Surgical Instruments: Complex surgical instruments with intricate features can be produced using SLS, allowing for improved precision and minimally invasive procedures.
- Prosthetics: Customized prosthetics like limbs, joints, and even facial prosthetics can be created using SLS, offering patients a perfect fit and improved functionality.
- Dental Implants: SLS-printed dental implants can be designed for optimal biocompatibility and osseointegration (fusion with bone).
- Bone Models for Surgery Planning: Highly accurate 3D models of bones, created using patient scans and SLS printing, can be used for pre-surgical planning and simulating complex procedures.
Challenges and Considerations:
Biocompatibility and sterilization are paramount concerns in the medical field. SLS materials need to undergo rigorous testing and meet strict regulations before being used in patient care. Additionally, proper sterilization procedures are essential to ensure implant and instrument safety.
Here’s a table summarizing the key points for SLS in Medical applications:
Benefit | Application Examples | Challenge |
Biocompatible Materials | Prosthetics, Dental implants | Rigorous biocompatibility testing and certifications |
Complex Geometries | Bone models for surgery planning | Sterilization procedures for implants and instruments |
Patient-Specific Customization | Surgical instruments |
SLS is revolutionizing medical care by enabling personalized medicine and advancing surgical techniques. As material science progresses and regulations are streamlined, we can expect even more groundbreaking applications of SLS 3D printing in the future of healthcare.
Exploring Other Industries Embracing SLS
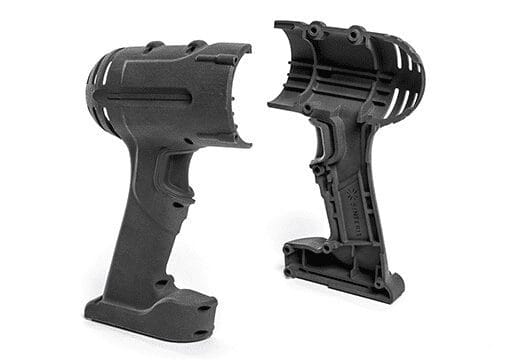
While we’ve focused on major applications, SLS 3D printing is finding its way into various other industries, each with its unique opportunities:
Architecture & Construction:
- Building Models: Highly detailed and accurate architectural models can be produced using SLS, showcasing intricate designs and facilitating better communication during construction projects.
- Design Mockups: Complex design mockups for buildings, including facades and interior layouts, can be rapidly created using SLS for design visualization and client approval.
Military:
- Replacement Parts: SLS can be used to create on-demand replacement parts for military equipment, reducing downtime and improving operational efficiency.
- Weapon Prototypes: Functional prototypes of weapons and weapon components can be created using SLS for testing and design iteration before mass production.
Heavy Industry:
- Sand Casting Patterns: SLS-printed sand casting patterns offer intricate details and dimensional accuracy, leading to high-quality castings in metal production.
- Tooling: Jigs, fixtures, and other tooling used in heavy industry can be produced using SLS for durability and customization.
Factors to Consider for SLS Applications
SLS 3D printing offers a vast array of possibilities, but it’s crucial to understand the key factors that influence its application for your specific needs. Here’s a breakdown of essential considerations:
Design for SLS: Embracing the Potential
To maximize the benefits of SLS, consider these design principles:
- Part Size and Complexity Limitations: While SLS excels at complex geometries, there are limitations on part size due to the printing chamber dimensions. Additionally, very thin walls or delicate features might require support structures or design modifications.
- Wall Thickness Considerations: Maintaining a minimum wall thickness is essential for part strength and structural integrity. SLS materials have specific recommended wall thicknesses to ensure successful printing and functionality.
- Minimizing Support Structures: SLS parts can be self-supporting for certain geometries. However, complex designs may require support structures, which add cost and post-processing needs. Designing parts to minimize support structures is crucial for optimizing the SLS process.
Material Matters: Choosing the Right SLS Material
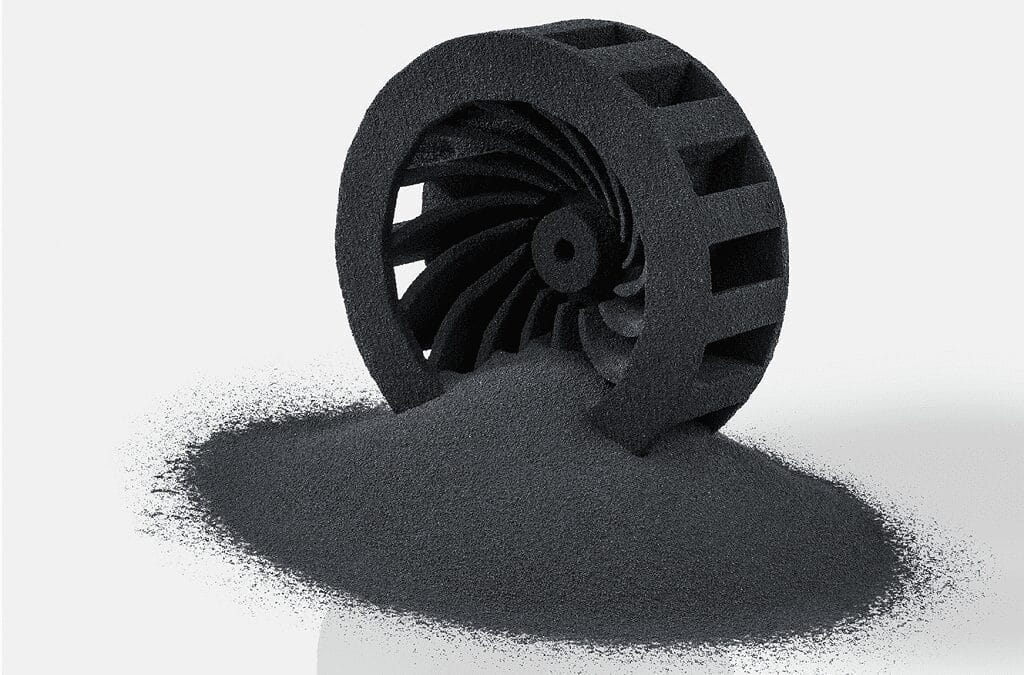
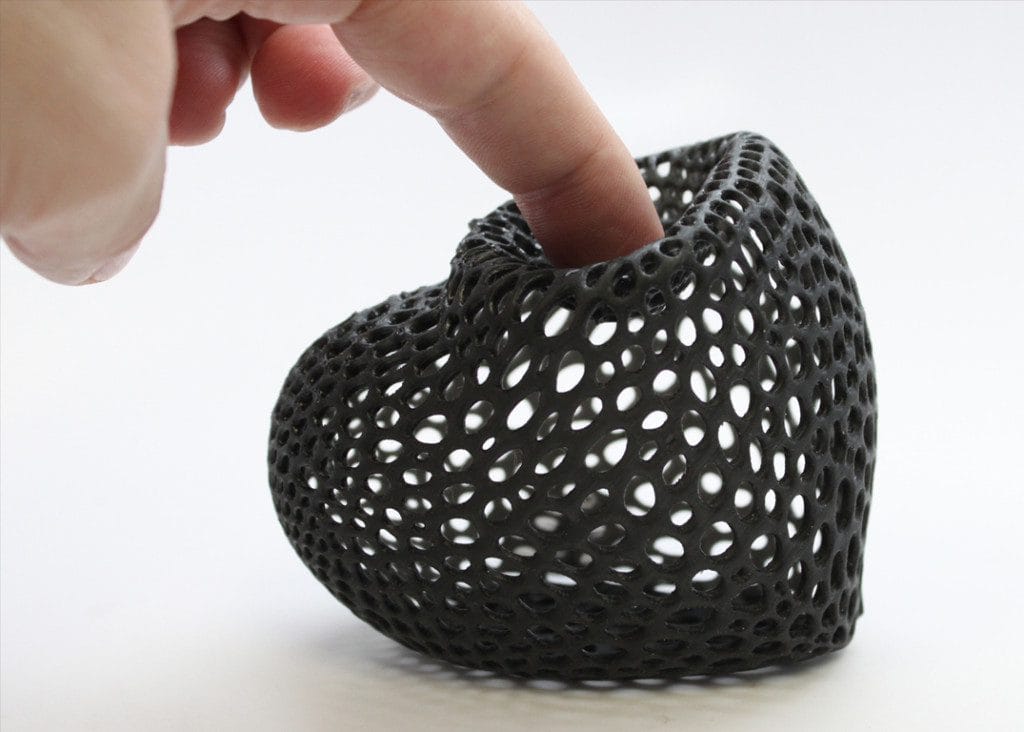
The material you choose for your SLS print significantly impacts its properties and suitability for your application. Here’s a breakdown of some common SLS materials:
- Nylon PA 12: A versatile and widely used SLS material known for its good strength, durability, and heat resistance. It’s a great choice for functional prototypes and various end-use parts.
- Polypropylene PP: A lightweight and flexible SLS material ideal for applications requiring chemical resistance or living hinges. However, it has lower strength compared to Nylon PA 12.
- TPU: Offering flexibility and rubber-like properties, TPU is suitable for applications requiring shock absorption or elastomeric characteristics.
Looking Ahead: Emerging SLS Materials:
The world of SLS materials is constantly evolving. Keep an eye out for exciting new options like:
- High-temperature filaments: SLS materials capable of withstanding higher temperatures, expanding applications in areas like automotive and aerospace.
- Biocompatible options: SLS materials specifically designed for medical applications, further promoting the use of SLS for implants and prosthetics.
Remember, consulting with an SLS service provider is crucial to select the ideal material for your specific requirements.
Cost Considerations: Understanding the Bottom Line
The cost of SLS printing is influenced by several factors:
- Part Size: Larger parts require more material and printing time, leading to higher costs.
- Material Choice: Different SLS materials have varying costs, with specialty materials typically costing more than standard options.
- Printing Time: The complexity of the design and part size affect printing time, which directly impacts cost.
- Post-Processing: Additional finishing steps like dyeing or polishing can add to the overall cost.
For a more accurate cost estimate, it’s recommended to obtain quotes from SLS service providers based on your specific design and requirements.
By carefully considering these factors, you can ensure that SLS 3D printing delivers the best possible results for your project.
The Future of SLS 3D Printing
SLS 3D printing technology is on a continuous trajectory of advancement, promising even greater things to come. Here’s a glimpse into what the future holds for SLS:
Speeding Up the Process: Advancements in SLS Technology
The future of SLS is all about efficiency and pushing the boundaries of what’s possible. Here are some exciting developments on the horizon:
- Faster Printing Speeds: New laser technologies and optimized printing processes are leading to faster printing times, making SLS a more viable option for high-volume production.
- More Diverse Material Options: The development of new materials with enhanced properties like high-temperature resistance, biocompatibility, and improved flexibility will open doors to a wider range of applications.
- Multi-material SLS Printing: Imagine SLS printing objects with different materials in a single build. This groundbreaking technology is in its early stages but holds immense potential for creating complex parts with varying functionalities.
A World Transformed: Expanding Applications of SLS
As SLS technology matures and becomes more cost-effective, we can expect to see its applications expand across various industries:
- Increased Adoption in End-Use Parts Production: SLS won’t be limited to prototyping anymore. With advancements in materials and printing processes, SLS will be used for large-scale production of functional end-use parts.
- Medical Implants and Customized Prosthetics: Biocompatible materials and improved printing techniques will revolutionize medical care, allowing for the creation of personalized implants and prosthetics that perfectly fit each patient’s needs.
- SLS for Sustainable Manufacturing: SLS offers a more sustainable manufacturing option compared to traditional methods. Reduced waste and the ability to use recycled materials make SLS an attractive choice for environmentally conscious production.
The future of SLS is brimming with possibilities. As the technology continues to evolve, it has the potential to transform the way we design, prototype, and manufacture a wide range of products, ultimately shaping a more efficient, innovative, and sustainable future.