Imagine peering through a window into the future of manufacturing, and you’ll likely see a DLP 3D printer in action, intricately crafting objects layer by layer with unparalleled precision. Digital Light Processing (DLP) 3D printing stands at the vanguard of an industrial revolution, presenting a blend of speed, detail, and reliability that traditional manufacturing methods struggle to match.
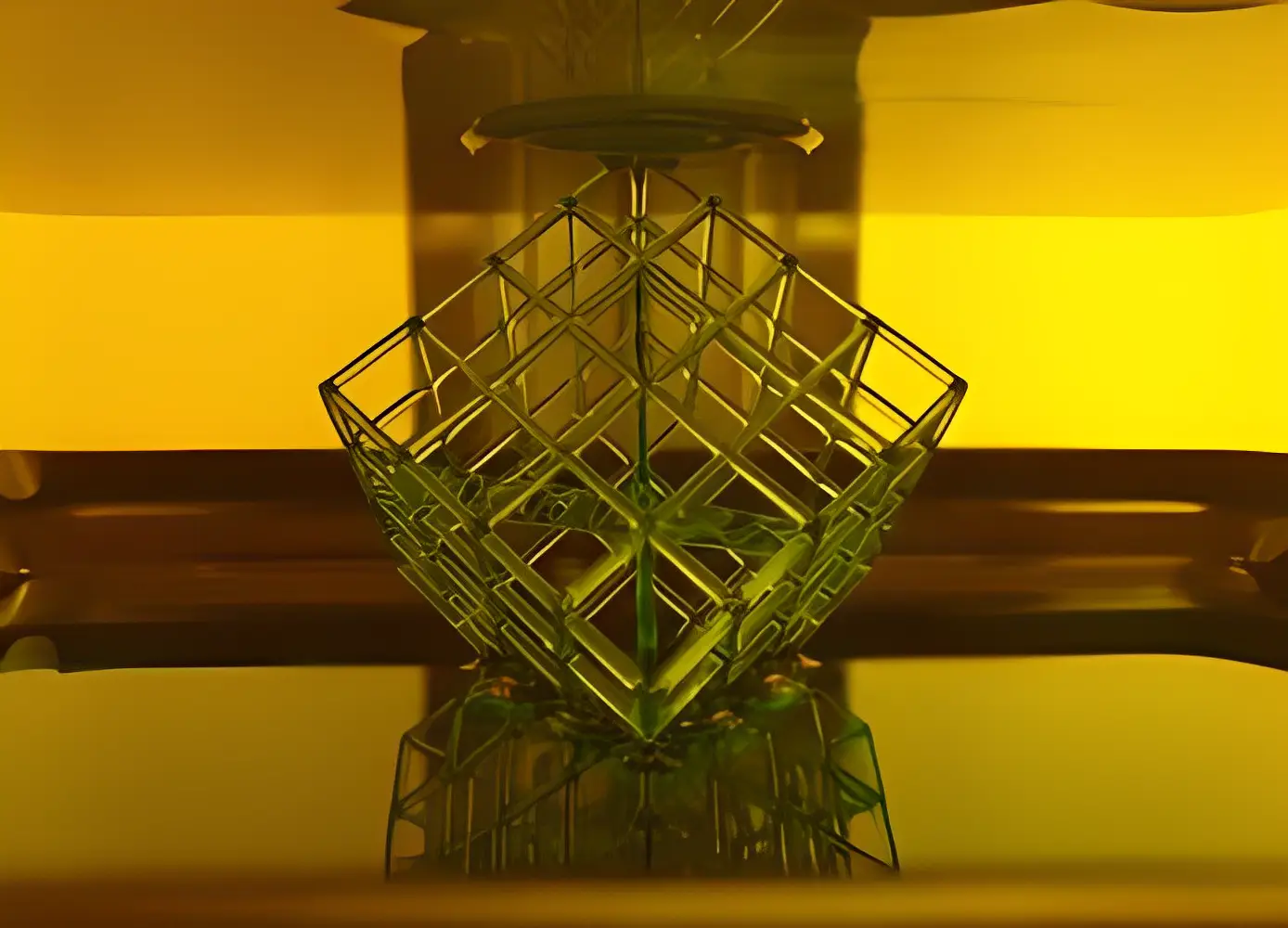
Fascination with three-dimensional creatives is no longer confined to the realms of science fiction. As you walk down the bustling avenues of innovation, from the dentist’s clinic with its custom dental appliances to the sophisticated design studios where the next generation of products takes shape, DLP 3D printing technology is there, quietly transforming dreams into tangible reality.
But what is DLP 3D printing, and why is it capturing the attention of professionals across such diverse fields? Through the lens of this comprehensive guide, we invite you to delve deep into the mechanics of DLP 3D printing, explore its numerous applications, and unravel the materials and methodologies that set it apart. We’ll weigh its advantages against its limitations and cast an eye toward the future it’s rapidly shaping.
Prepare to embark on a journey that transcends the printed page, as we dissect the technology that’s redefining industries and empowering designers, engineers, and visionaries around the globe. This isn’t just about observing a new trend – it’s about exploring an evolution, a leap into the next dimension of creation. Welcome to the exhilarating world of DLP 3D printing – let’s begin our exploration.
The Mechanics of DLP 3D Printing: A Detailed Exploration
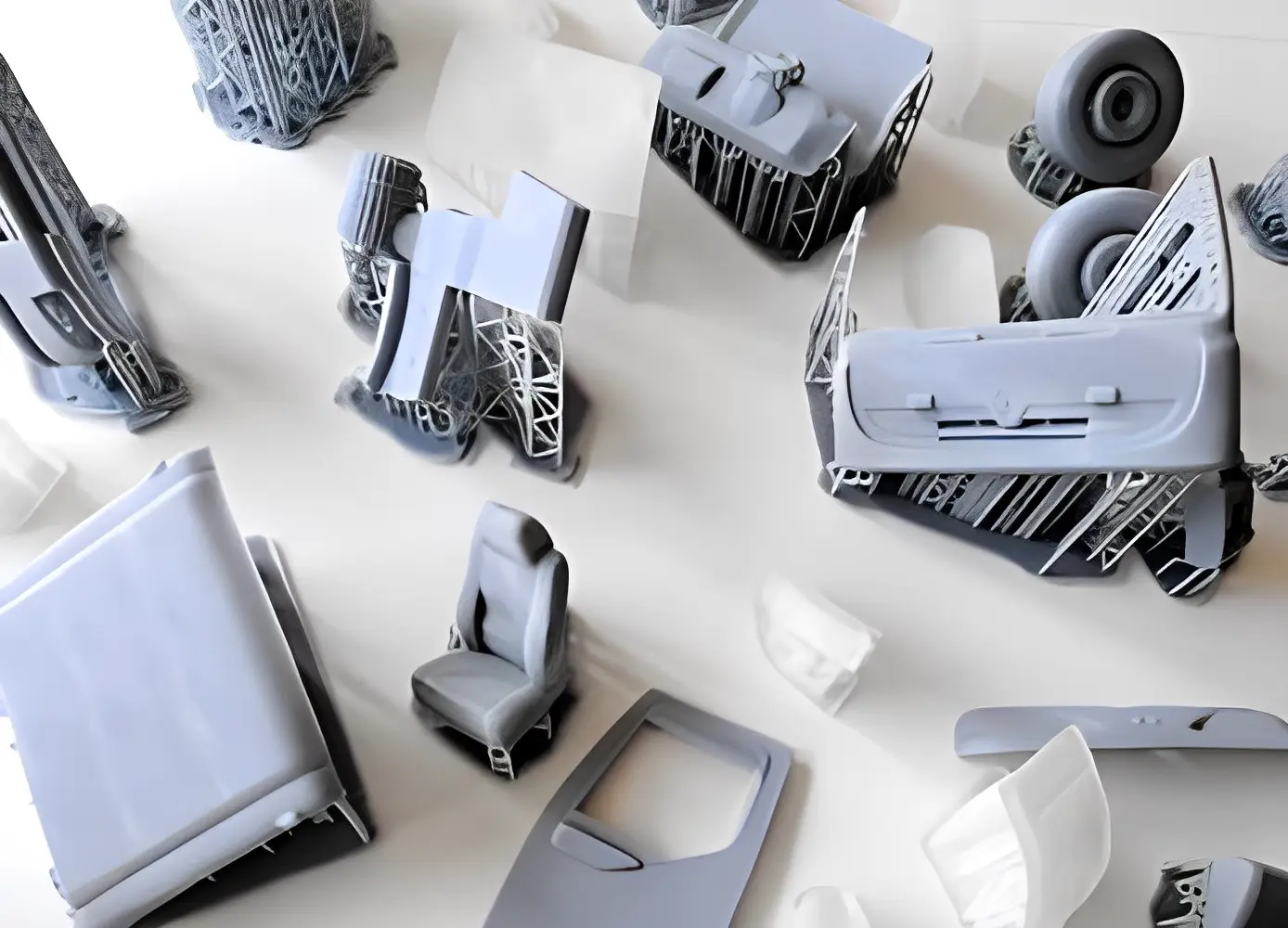
In the realm of additive manufacturing, Digital Light Processing (DLP) stands as a beacon of innovation, offering a unique approach to 3D printing that emphasizes speed and detail. Here, we delve into the fascinating world of DLP 3D printing, dissecting the intricate dance of light and polymers that brings complex designs to life with astonishing finesse.
Understanding the Core Components
At the heart of a DLP 3D printer are several core components working in unison:
- Light Source: A high-intensity light, often an array of LEDs, casts ultraviolet (UV) light to cure photosensitive resin.
- DLP Chip: This is the printer’s central processing unit, consisting of thousands of microscopic mirrors that reflect light patterns with exceptional precision.
- Resin Tank: A vat filled with liquid photopolymer resin where the objects are formed layer by layer.
- Build Platform: The stage that moves vertically, allowing each layer to be cured by the light source before raising to add the next layer.
Step-by-Step Breakdown of the DLP Process
- Designing the Model:
- A 3D model is created or acquired and loaded into a slicing software specific to DLP printing.
- Slicing the Model:
- The software divides the model into thin horizontal layers and converts each into a digital cross-sectional pattern corresponding to the DLP chip’s mirrors.
- Preparing the Printer:
- The build platform lowers into the resin tank, leaving only a hair’s breadth between the platform and the bottom of the tank.
- Printing Begins:
- The light source activates, projecting a single layer’s image onto the surface of the resin.
- Wherever the UV light strikes, the resin cures and solidifies.
- Layer Formation:
- Once a layer is cured, the platform lifts to separate it from the tank’s bottom, allowing more resin to flow beneath it.
- Repeating the Process:
- The build platform lowers back down, and the light cures the next layer, which adheres to the first.
- Finalizing the Print:
- This cycle repeats until the entire object is built. Finally, the print undergoes cleaning in a solvent and further curing to harden completely.
Comparing DLP with Other 3D Printing Technologies
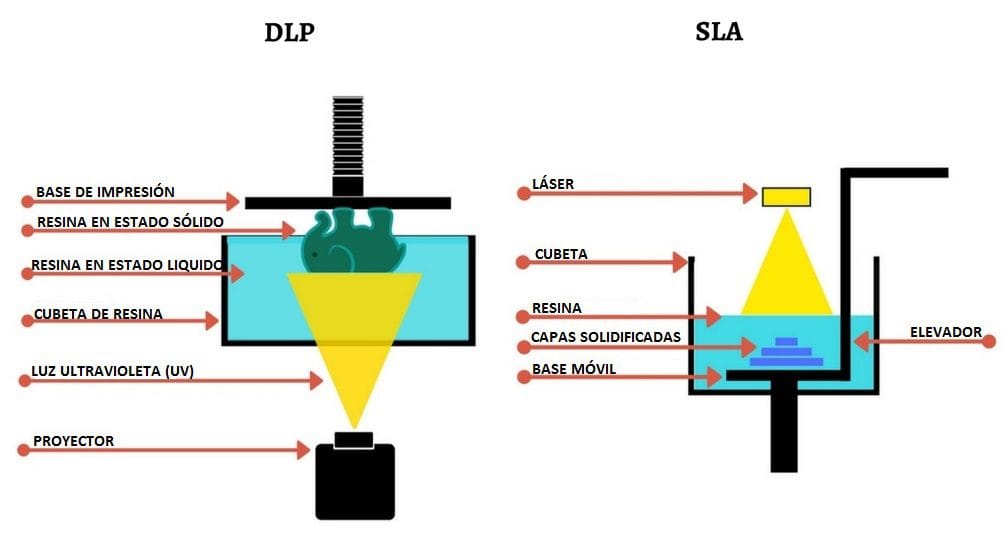
DLP vs. SLA (Stereolithography)
- Speed: DLP generally operates faster than SLA because it cures whole layers at once rather than tracing each layer point by point.
DLP vs. FDM (Fused Deposition Modeling)
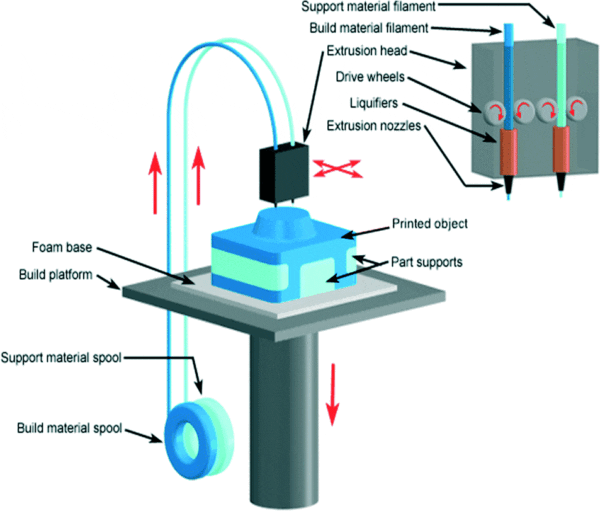
- Precision: DLP offers greater detail compared to FDM, as it can produce smoother finishes and finer features.
- Material Differences: FDM utilizes thermoplastic filaments, whereas DLP uses photopolymer resins.
The beauty of DLP technology lies in its ability to print intricate details swiftly. Its application, which was initially niched in the prototyping domain, is now expanding, with use cases flourishing in various sectors due to its high efficiency and resolution.
As we navigate through the nuances of the DLP 3D printing process, we uncover the relentless pursuit of perfection this technology embodies. From the subtle choreography of UV lights to the delicate emergence of an object, poised layer by layer, DLP is not just a manufacturing method—it’s a symphony of digital craftsmanship.
By equipping ourselves with a thorough understanding of DLP’s inner workings, we’re not just observers; we become informed participants in the evolving narrative of 3D printing technology. And in the quest for hyper-detailed, precision manufacturing, DLP 3D printing is, without a doubt, a game-changer in its field.
Applications of DLP 3D Printing: Transforming Industries
The versatility of Digital Light Processing (DLP) 3D printing has made it an invaluable asset across numerous sectors. By enabling the creation of highly detailed and complex structures with remarkable speed, DLP has revolutionized the way professionals approach design and production. Let’s explore the various applications of DLP 3D printing, highlighting how this technology is not just an asset but a transformative force in industry.
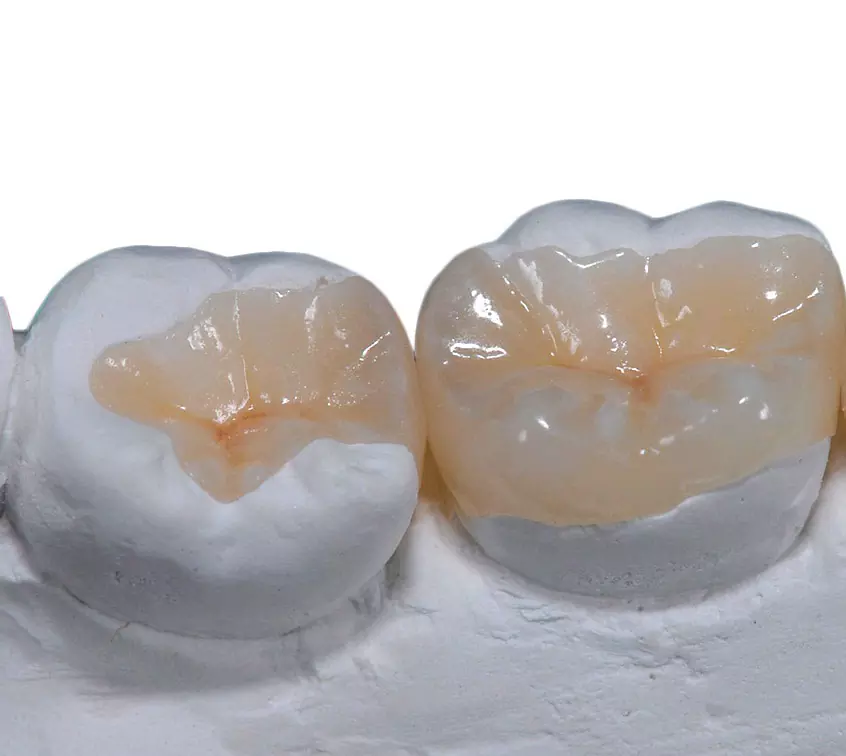
Dental Industry: Precision at the Service of Health
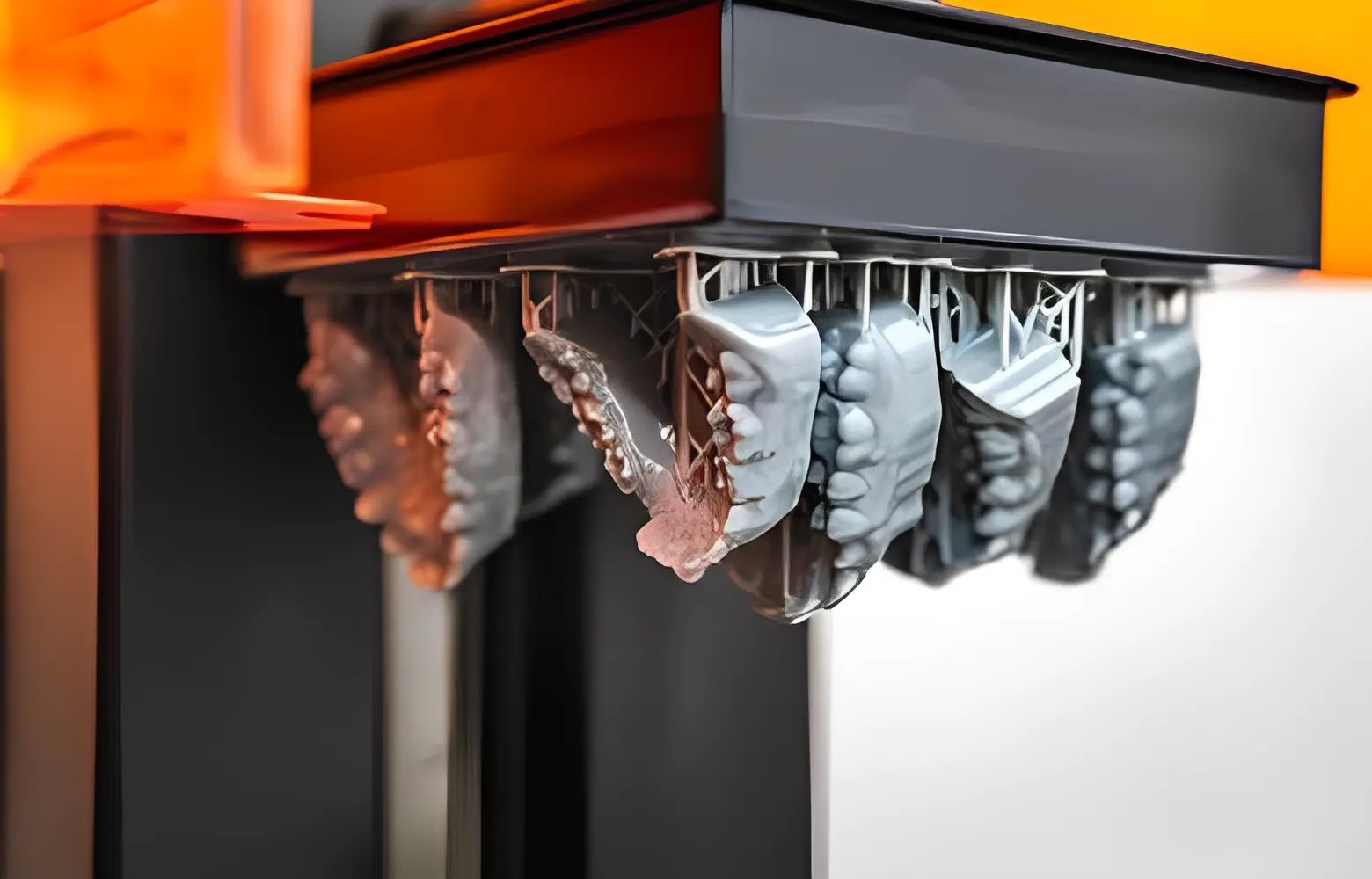
DLP printing has made a formidable impact in dentistry:
- Dental Appliances: Custom dental crowns, bridges, and orthodontic devices are produced with unmatched speed and precision.
- Biocompatible Resins: Use of specialized resins that are safe for medical use within the human body.
- Cost-Efficiency: DLP reduces material waste and speeds up the production process, resulting in cost savings for both dental practices and patients.
Product Design: Prototyping at the Speed of Thought
For product designers, DLP 3D printing is like a superpower for prototyping:
- Rapid Iteration: Designers can iterate prototypes quickly, moving from concept to physical object at an unprecedented pace.
- Complex Geometries: Ability to create intricate designs that would be impossible or prohibitively expensive with traditional methods.
Jewellery Making: Crafting Dreams with Light
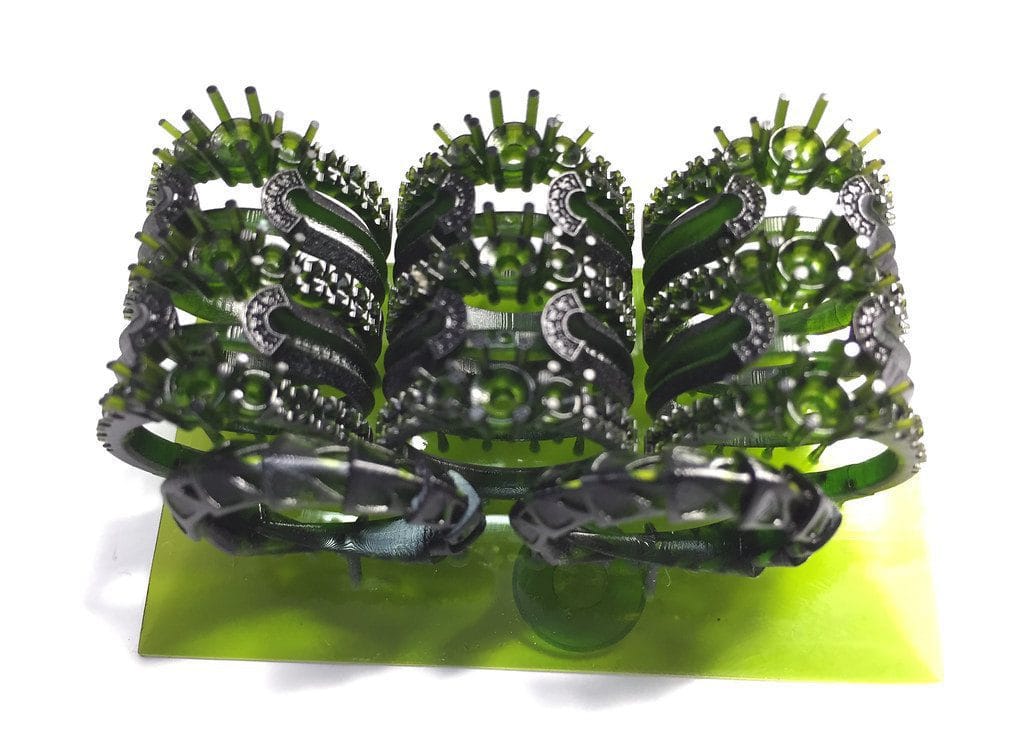
In the jewellery business, the benefits of DLP are clear:
- Exceptional Detail: Capture every nuanced curve and edge of intricate jewellery designs.
- Wax Casting Models: Create patterns for lost wax casting, streamlining the jewellery manufacturing process.
- Customization: Easily customize designs for clients, adding a personal touch to every piece.
Educational Sector: Shaping Minds with 3D Printed Models
DLP 3D printing enhances education by providing tangible learning aids:
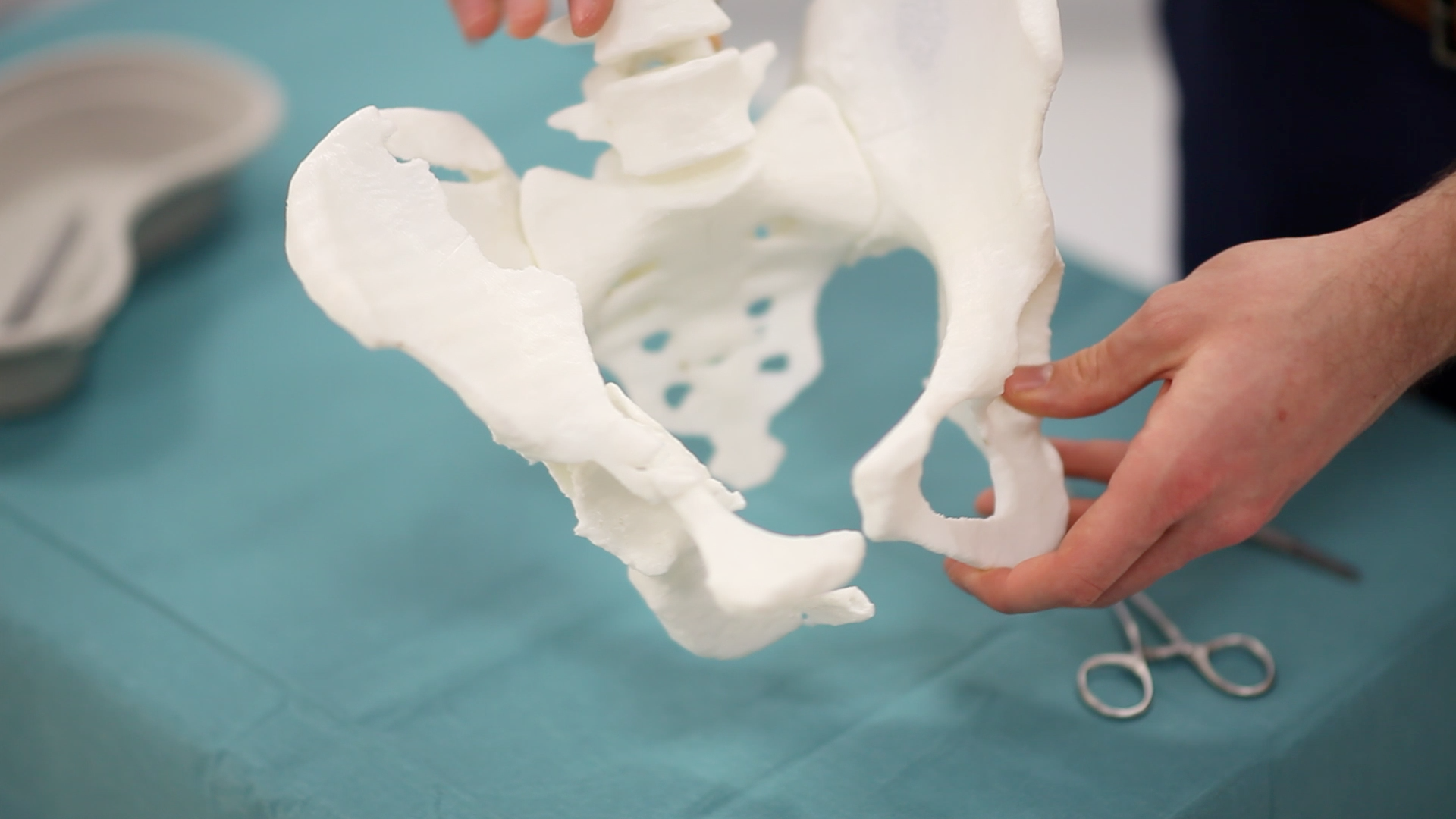
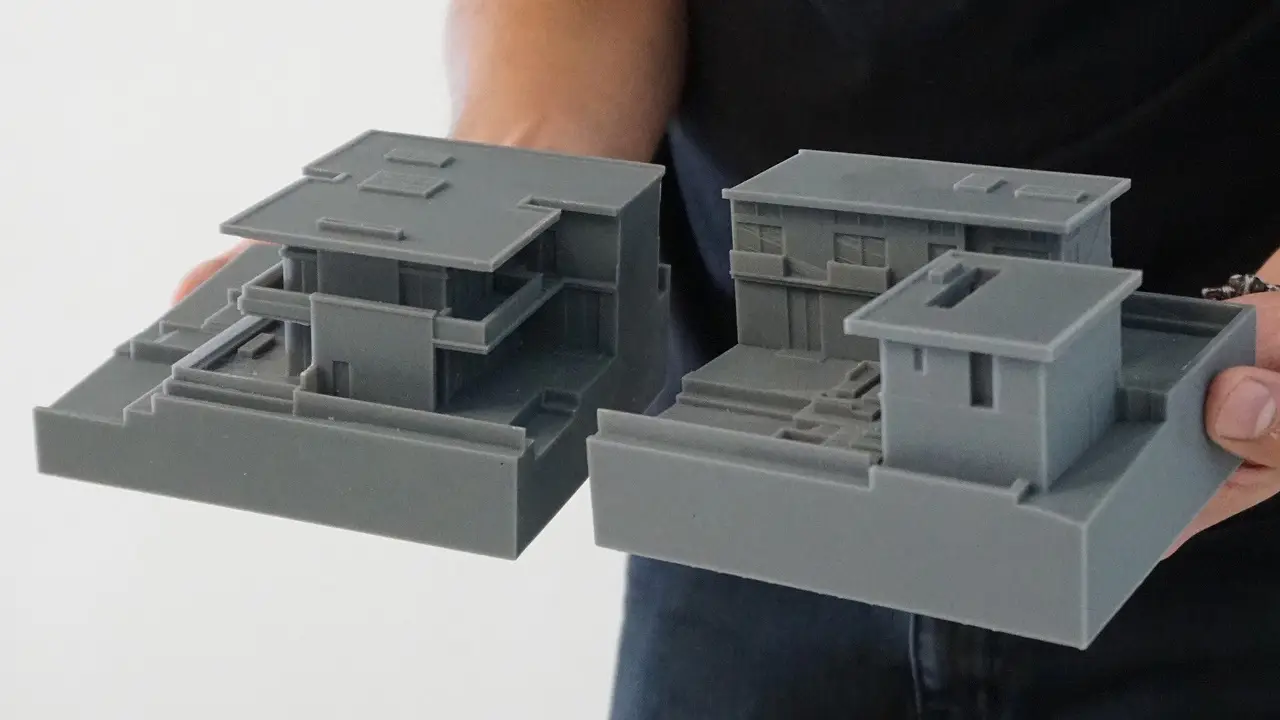
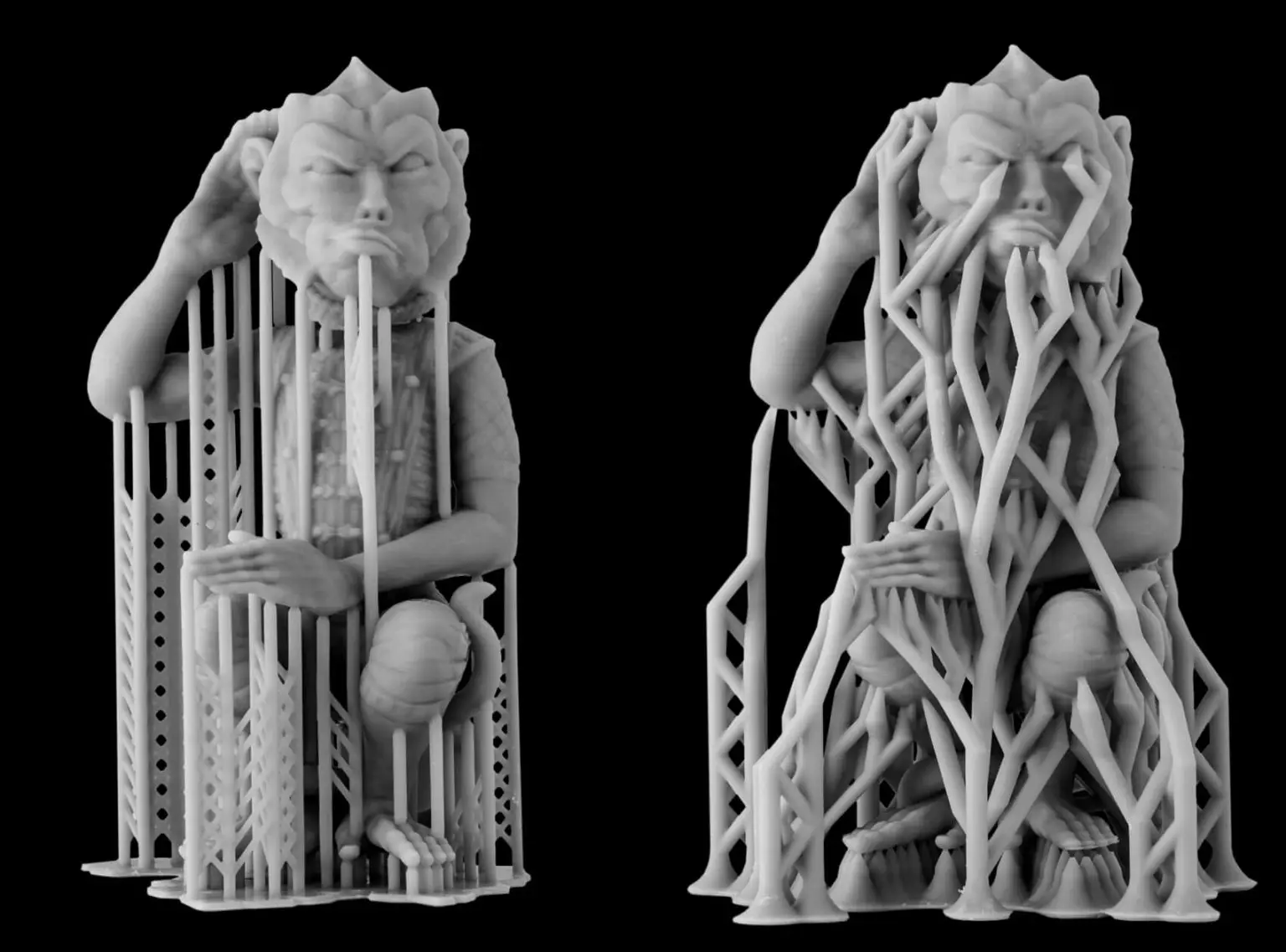
- Anatomical Models: Produce highly detailed anatomical models for medical students.
- Architectural Replicas: Allow architecture students to bring their blueprints to life.
- Historical Artifacts: Reproduce artifacts for history lessons, making past cultures accessible to students.
By catapulting the potential of rapid prototyping and manufacturing into sectors as diverse as healthcare and haute couture, DLP 3D printing isn’t just a tool—it represents a paradigm shift. In a world where the only constant is change, DLP 3D printing stands as a testament to human ingenuity, enabling us to build the future one layer at a time.
Whether forging brighter smiles through dental prosthetics or igniting the spark of knowledge with educational models, DLP 3D printing moves beyond mere production. It is an art form that imbues the objects it creates with the vitality of precision and the promise of innovation.
As we continue to harness the capabilities of DLP 3D printing, we pave the way for advancements that transcend the boundaries of imagination. Embracing the detailed craft that this technology lays at our fingertips, we can boldly state that the future isn’t just bright; it’s intricately layered with possibilities crafted by DLP 3D printing.
Limitations and Considerations of DLP 3D Printing
Despite its impressive capabilities, Digital Light Processing (DLP) 3D printing is not without its limitations and challenges. Understanding these can help users make informed decisions and potentially lead to improvements in the technology. Here’s a detailed look at the aspects where DLP may fall short and considerations that need to be taken into account.
Material Constraints: The Chemistry of Creation
One of the primary limitations of DLP is its dependency on specific photopolymer resins:
- Resin Diversity: Compared to other printing methods like FDM, there are fewer materials available for DLP printing.
- Resin Cost: DLP-compatible resins can be more expensive due to their specialized composition.
- Biodegradability: Many resins are not biodegradable, raising environmental concerns.
Mechanical Constraints: The Precision Paradox
While DLP excels at precision, this can also introduce some challenges:
- Support Structures: Intricate designs often require support structures that must be manually removed post-printing.
- Z-Axis Strength: Layers adhered with light rather than physical extrusion can have weaker z-axis strength compared to other methods.
Scale Issues: Size Does Matter
When it comes to size, DLP printers have their limitations:
- Build Volume: Most DLP printers have a smaller build volume, restricting the size of objects you can print in a single run.
- Large Objects: For larger objects, parts must be printed separately and then assembled, potentially impacting structural integrity.
Post-Processing: Finishing the Symphony
The post-printing stage can be labor-intensive and requires careful handling:
- Cleaning: Prints must be washed in solvents to remove excess resin.
- Curing: Additional UV curing is often necessary to achieve full material strength.
- Surface Finishing: Though DLP prints are smooth, they may still require sanding or painting for the final finish.
By exploring these limitations, we’re not just critiquing the technology; we’re setting the stage for innovation. The challenges thrown by DLP 3D printing are not roadblocks, but rather stepping stones for researchers and developers aiming to expand its horizons.
These considerations are checkpoints on the path of progress, alerting us to what needs refinement as we stretch the capabilities of DLP 3D printing. It’s a technology that’s constantly evolving, and with evolution comes a better understanding of both its strengths and areas for improvement.
As the journey of DLP 3D printing continues, we watch, learn, and adapt. For every limitation encountered, there’s an opportunity for innovation—an incentive to push the boundaries and achieve what was once deemed impossible. In recognising these limitations and considerations, we pave a wider, more accommodating road for the future of digital manufacturing.
Future Prospects: The Evolution of DLP 3D Printing
The arena of Digital Light Processing (DLP) 3D printing is not just about what the technology can achieve today, but also about what it promises for tomorrow. Its evolution is continuous, driven by research, user feedback, and technological breakthroughs. Here, we will explore the anticipated trajectory of DLP 3D printing, examining how it may expand its influence and transform future manufacturing landscapes.
Advancements in Material Science
The expansion of
material options marks a significant frontier for the evolution of DLP 3D printing:
- Eco-Friendly Resins: Development of biodegradable and bio-based resins would mitigate environmental concerns associated with current photopolymers.
- Enhanced Properties: Upcoming materials could offer improved strength, flexibility, and functionality, such as conductivity or temperature resistance.
Technological Integration
Integrating DLP with other technologies could lead to hybrid systems that amplify its capabilities:
- AI and Machine Learning: Incorporating AI could streamline the printing process, from design optimization to real-time error detection and correction.
- Internet of Things (IoT): Connected DLP printers could allow for more efficient workflow management and remote monitoring, further strengthening the additive manufacturing networks.
Breakthroughs in Printer Design
Innovations in the physical design of DLP printers are expected to stretch the current limitations:
- Larger Build Areas: Advancements in DLP printer design could lead to larger build volumes, enabling the production of bigger parts without the need for assembly.
- Improved Speed and Resolution: Ongoing optimizations in light source technology and DLP chip design are anticipated to further enhance printing speed and detail.
Customization and Personalization
As DLP progresses, the potential for customization will likely reach new heights:
- Mass Customization: Continued refinement of DLP may allow for economical customized production, particularly in sectors like healthcare for patient-specific solutions.
- Localized Manufacturing: DLP printers could become staples in shops and design studios, offering on-demand manufacturing capabilities that align with a shift towards localized production.
Training and Education
The growing availability of DLP technology might inspire a new wave of learning opportunities:
- Specialized Courses: To prepare the workforce for the future, educational institutions may offer courses dedicated to DLP printing techniques, materials science, and applications.
- Community Programs: Maker spaces and community centers might host workshops and seminars on using DLP technology, promoting widespread proficiency.