Selective Laser Sintering (SLS) 3D printing has revolutionized manufacturing by enabling complex, functional parts without support structures. At the heart of this technology lies nylon—a polymer that balances strength, flexibility, and thermal resistance. This article explores nylon’s critical role in SLS, evaluates its advantages and limitations, and examines its evolving applications across industries.
Understanding SLS 3D Printing
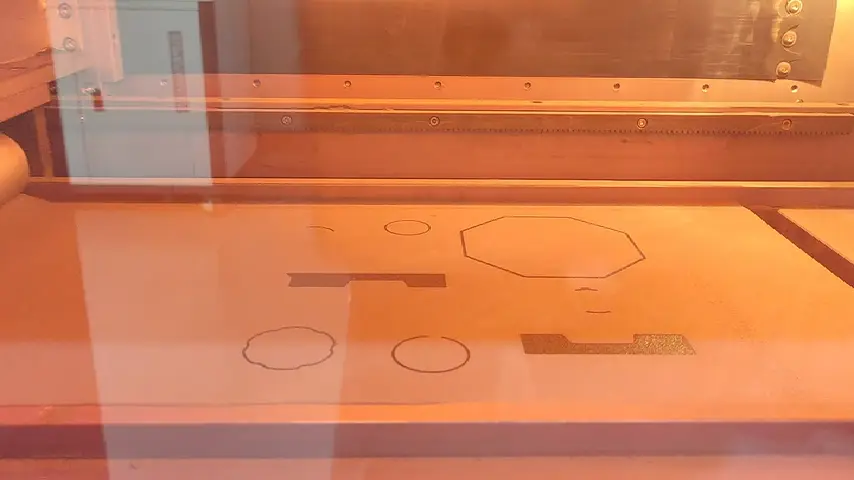
SLS uses a high-powered laser to fuse powdered materials layer by layer. The process begins with spreading a thin layer of nylon powder across a build platform, pre-heating it to near melting point, and selectively sintering particles with a laser. Unsintered powder acts as natural support, enabling intricate geometries and efficient material reuse (up to 80% recycling rates).
Key Advantages of SLS Over Other Technologies:
- No Supports Required: Ideal for hollow structures and interlocking parts.
- Material Efficiency: Minimal waste compared to FDM or CNC machining.
- Isotropic Strength: Uniform mechanical properties in all directions.
- Batch Production: Cost-effective for small to medium volumes (e.g., 50–500 units).
However, SLS faces challenges, including high machine costs (industrial systems start at ~$200,000), limited material options, and post-processing requirements.
Nylon’s Role in SLS: Strengths and Limitations
Nylon, particularly polyamide (PA) variants, dominates SLS due to its unique properties:
Advantages
- Mechanical Performance:
- Tensile Strength: PA12 offers 45–50 MPa, suitable for functional prototypes and end-use parts like automotive brackets.
- Fatigue Resistance: Withstands over 100,000 bending cycles, ideal for snap-fit enclosures.
- Impact Absorption: Critical for drone mounts and robotics components.
- Thermal Stability:
- PA12 maintains structural integrity at temperatures up to 175°C, making it viable for under-the-hood automotive parts (e.g., Porsche’s SLS-printed air ducts).
- Chemical Resistance:
- Resists oils, fuels, and solvents, as seen in fluid-handling systems.
- Lightweight Design:
- At 1.01 g/cm³, nylon reduces weight by 40–60% compared to aluminum in aerospace applications (e.g., Airbus A350 cabin ducts).
Limitations
- Moisture Sensitivity:
- Nylon powder absorbs humidity, leading to defects like porous surfaces. Solutions include drying powder at 80°C pre-print and using sealed storage.
- Post-Processing Demands:
- Bead blasting, dyeing, or epoxy coating are often required to achieve smooth finishes, adding time and cost.
- Environmental Impact:
- Petroleum-based PA12 generates ~5 kg CO₂ per kg of material. Bio-based PA11 (derived from castor oil) reduces emissions by 30% but costs 50% more.
- Cost Barriers:
- Industrial SLS machines and nylon powder (~$120/kg) make the technology less accessible for small-scale production.
Industry Applications: Balancing Innovation and Practicality
Nylon SLS bridges prototyping and production across sectors:
- Automotive:
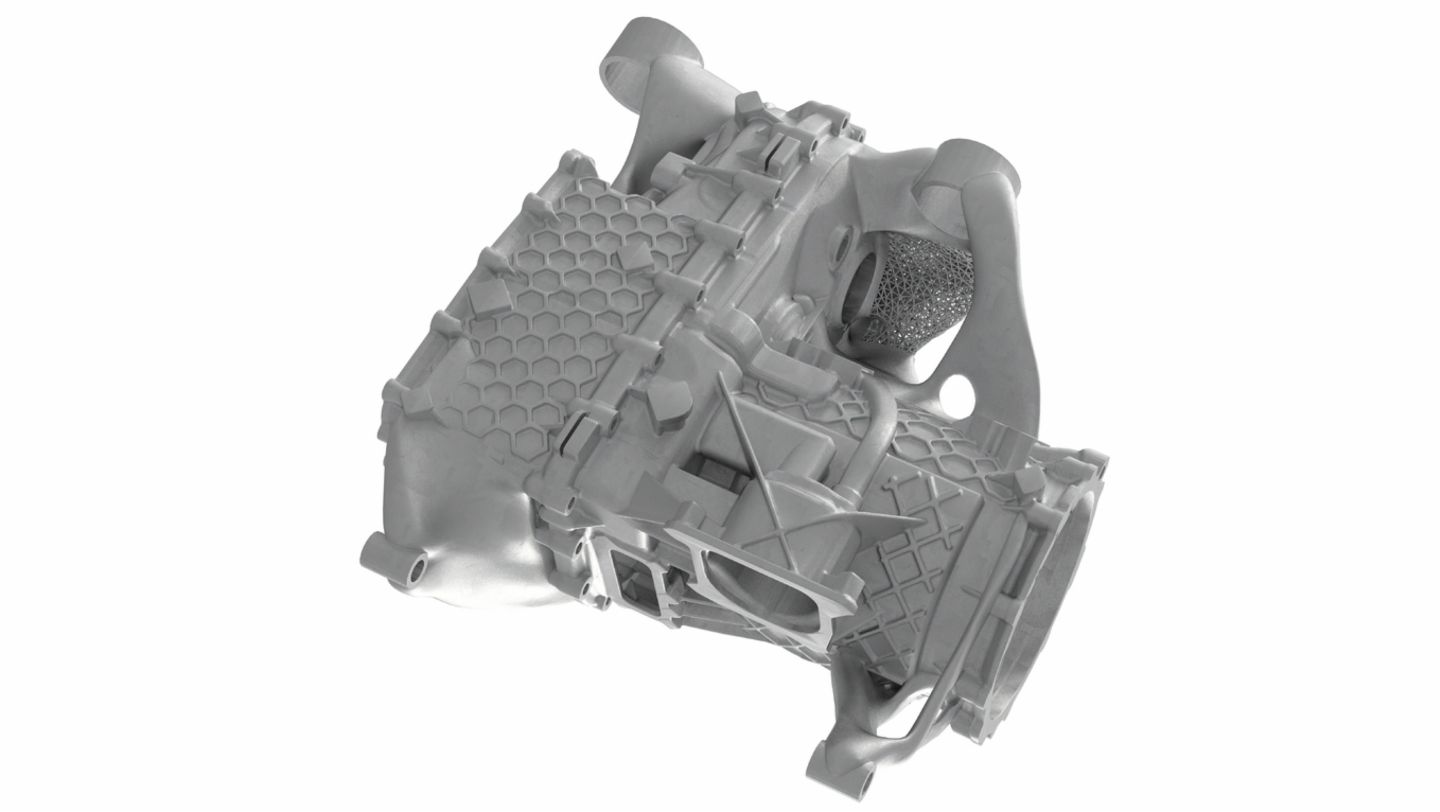
- Use Case: Custom jigs and heat-resistant brackets (PA12-GF).
- Result: Porsche reduced prototyping costs by $250,000 using SLS air ducts (source: Porsche Engineering, 2021).
- Aerospace:
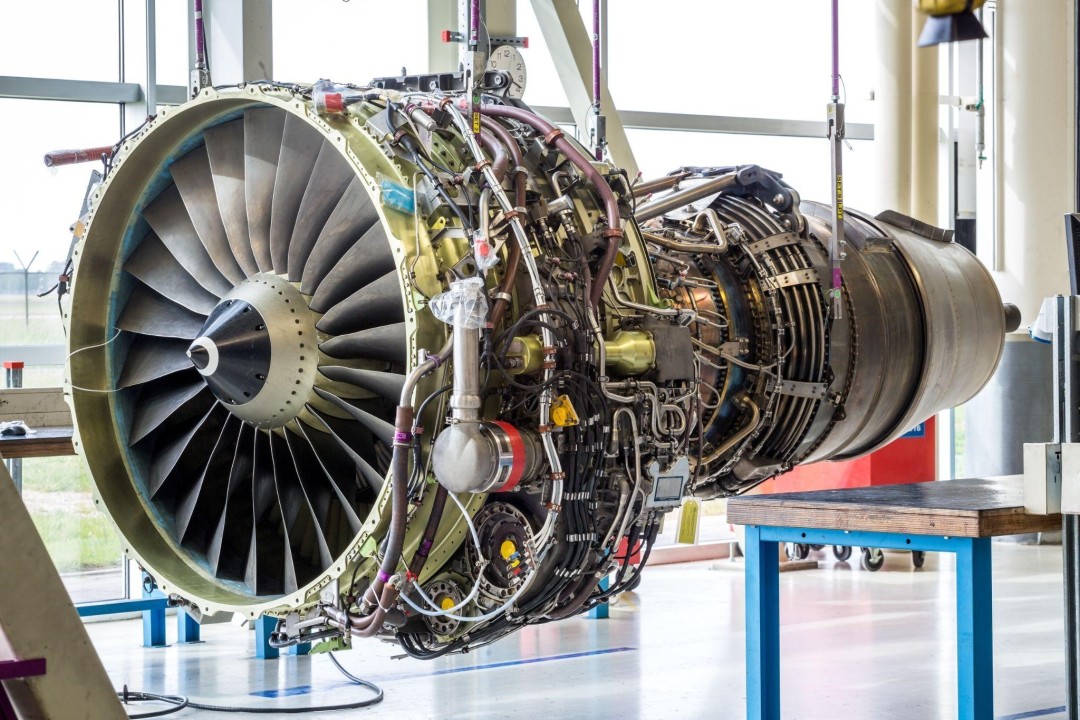
- Use Case: Satellite housings (PA12) and drone frames (PA-CF).
- Result: Lockheed Martin cut satellite cable mount weight by 60% (source: Lockheed Martin Case Study, 2023).
- Medical:
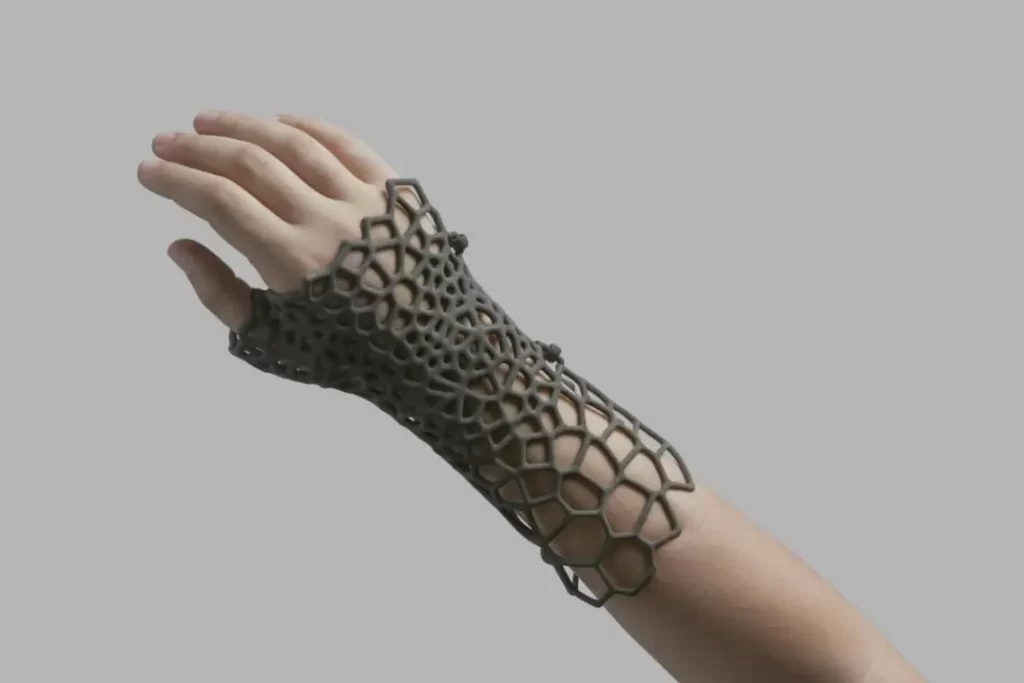
- Use Case: Prosthetic sockets (PA11) and surgical guides.
- Result: Unlimited Tomorrow reduced prosthetic costs by 80% while improving comfort (source: Unlimited Tomorrow, 2022).
- Consumer Goods:
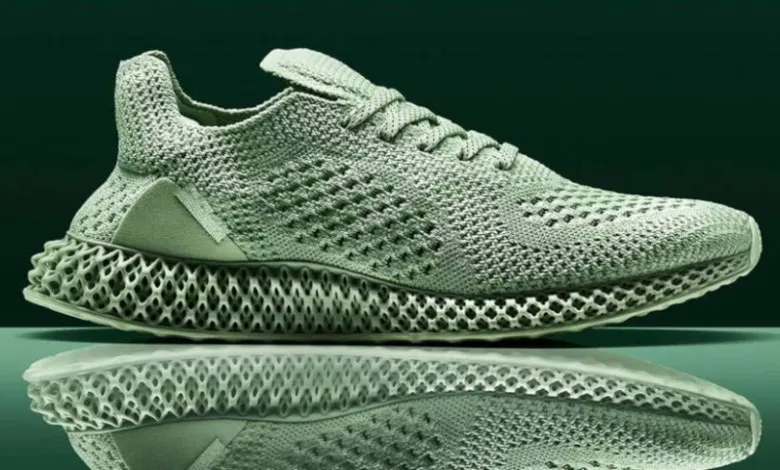
- Use Case: Adidas’ 4DFWD midsoles (15% recycled ocean plastic PA12).
- Result: 20% higher energy return than traditional foam (source: Adidas Sustainability Report, 2023).
Critical Analysis: Nylon vs. Alternatives
Material | Pros | Cons | Best For |
---|---|---|---|
PA12 | High strength, cost-effective | Moisture-sensitive, opaque | Functional prototypes |
TPU | Flexibility, fatigue resistance | Lower tensile strength | Wearables, seals |
PEEK | Extreme heat resistance (250°C) | High cost ($500–800/kg) | Aerospace components |
PA11 | Bio-based, flexible | Lower thermal stability | Eco-friendly consumer products |
Trade-Off Insights:
- While PA12 excels in general applications, PA6-GF’s stiffness (70 MPa tensile) justifies its cost in structural parts.
- TPU-nylon blends balance flexibility and durability for smartwatch bands but lack high-temperature resistance.
Future Trends: Innovation and Sustainability
- Advanced Composites:
- PA-MXene: Conductive nylon for EMI shielding (tested by Lockheed Martin in satellite housings).
- Self-Healing PA: Microcapsules repair cracks autonomously, extending part lifespan.
- Sustainable Solutions:
- Algae-Based PA11: Startups like AlgiKnit cut CO₂ emissions by 65% (source: AlgiKnit, 2023).
- Closed-Loop Recycling: Systems like AMPRO 600 achieve 95% powder reuse.
- AI Integration:
- Generative design tools (e.g., nTopology) optimize lattice structures, reducing weight by 50% while maintaining strength.
Conclusion
Nylon remains indispensable in SLS 3D printing due to its versatility and performance. However, its moisture sensitivity, environmental footprint, and cost barriers necessitate careful consideration. As bio-based materials and AI-driven processes evolve, nylon SLS will continue to redefine manufacturing—balancing innovation with practicality. For engineers, the key lies in selecting the right material blend and leveraging emerging technologies to overcome current limitations.