In the realm of 3D printing, material selection is crucial for project success. Nylon has emerged as a favored material for SLS 3D printing due to its unique combination of properties. This article delves into the details of why nylon is highly suitable for SLS, exploring its characteristics, advantages, limitations, and applications.
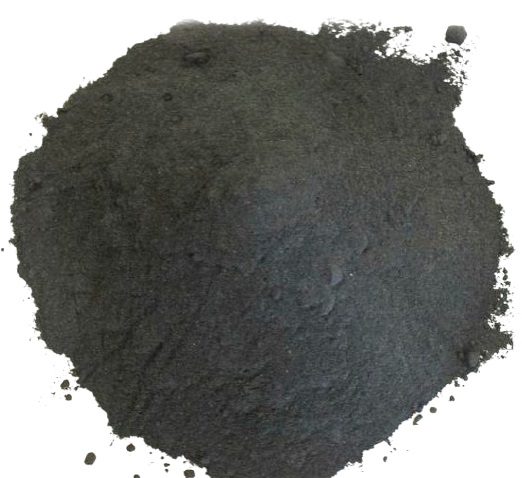
SLS 3D Printing Basics
Definition and Process
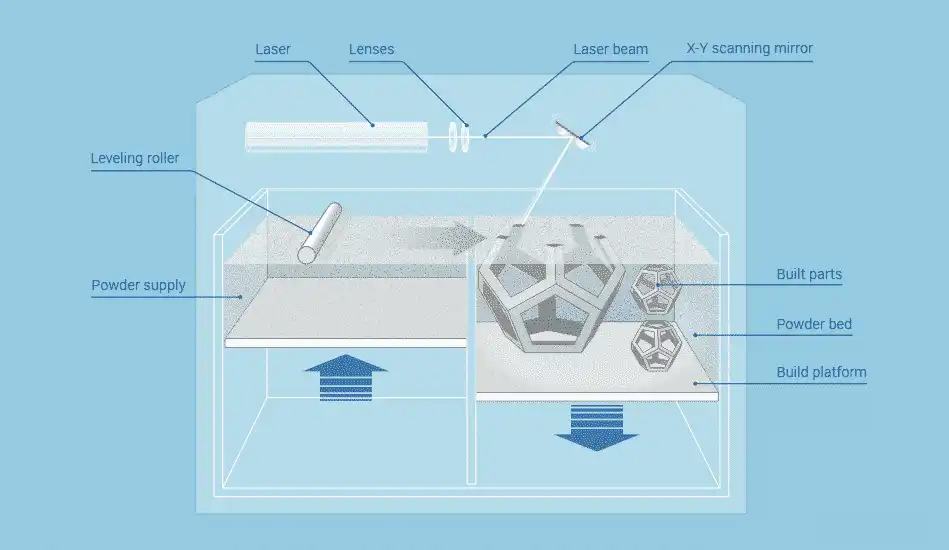
SLS is an additive manufacturing process that utilizes a high-powered laser to fuse powdered materials layer by layer, directly constructing parts from a digital 3D model. The process involves spreading a thin layer of powdered material (commonly nylon) evenly across the build platform and heating it close to its melting point. The laser then scans the surface, selectively fusing particles according to the model’s geometry. After each layer is sintered, the build platform lowers, and a new layer of powder is added. Once the printing is complete, the build chamber cools, and the unfused powder is removed.
Advantages of SLS
- No Support Structures Required: Unlike some other 3D printing methods, SLS does not need additional support structures for overhangs or complex geometries. The unfused powder provides natural support, facilitating the creation of intricate designs.
- High Strength and Durability: Parts fabricated via SLS exhibit robust mechanical properties, making them suitable for functional prototypes and end-use applications.
- Minimal Material Waste: The ability to reuse unfused powder contributes to cost savings and environmental sustainability.
- Versatility of Materials: SLS supports a wide range of materials, with nylon being a prominent option, along with glass-filled composites and certain metals depending on the printer.
Comparison with Other 3D Printing Technologies
When compared to FDM (Fused Deposition Modeling) and SLA (Stereolithography), SLS offers distinct advantages. It uses powdered materials (such as nylon) instead of filaments or resins. In terms of support structures, SLS has an edge as it doesn’t require them. The surface finish of SLS parts is smooth but powdery, differing from the moderate visible lines of FDM and the smooth, glossy finish of SLA. SLS parts also possess higher strength compared to FDM and SLA parts. These characteristics make SLS a preferred choice for industrial applications where precision, strength, and cost-efficiency are crucial.
Feature | SLS | FDM | SLA |
Material | Powder (nylon, composites) | Thermoplastic filaments | Photopolymer resin |
Support Structures | Not Required | Required | Required |
Surface Finish | Smooth but powdery | Moderate, visible lines | Smooth, glossy |
Strength | High | Moderate | Low |
Applications | Functional parts, prototypes | Prototypes, hobby models | High-detail prototypes |
Common Applications
SLS has found applications in various industries. In aerospace and automotive, it is used to produce lightweight and durable parts like brackets, housings, and ducts, as well as prototypes capable of withstanding high stress and heat. In healthcare, it enables the fabrication of custom prosthetics, orthotics, and surgical guides, along with medical-grade nylon parts for biocompatible applications. Consumer goods benefit from SLS for customized eyewear, wearable devices, and footwear, as well as functional prototypes for rapid product development. In manufacturing, SLS is employed to create jigs, fixtures, and tooling for assembly lines, streamlining production processes.
Nylon: An Overview
Definition and Properties
Nylon is a synthetic polymer belonging to the polyamide family. It was first developed by DuPont in the 1930s and has since gained widespread use across multiple industries. Nylon is characterized by its lightweight yet durable nature, resistance to abrasion, heat, and chemicals, and flexibility with excellent impact resistance and elasticity.
Key Mechanical, Thermal, and Chemical Properties
- Mechanical Properties: Nylon exhibits a high strength-to-weight ratio, making it ideal for structural applications where weight reduction is important. Its flexibility allows it to bend under stress without cracking, providing good impact resistance. Additionally, it is highly durable, capable of withstanding repeated use.
- Thermal Properties: With a high melting point, nylon can endure high-temperature environments without deforming, ensuring stability during the SLS printing process and in end-use applications.
- Chemical Properties: Nylon is resistant to oils, fuels, and many solvents, making it suitable for automotive and industrial components. While it is hygroscopic to some extent, advancements in material formulations have mitigated this issue.
Types of Nylon Used in SLS 3D Printing
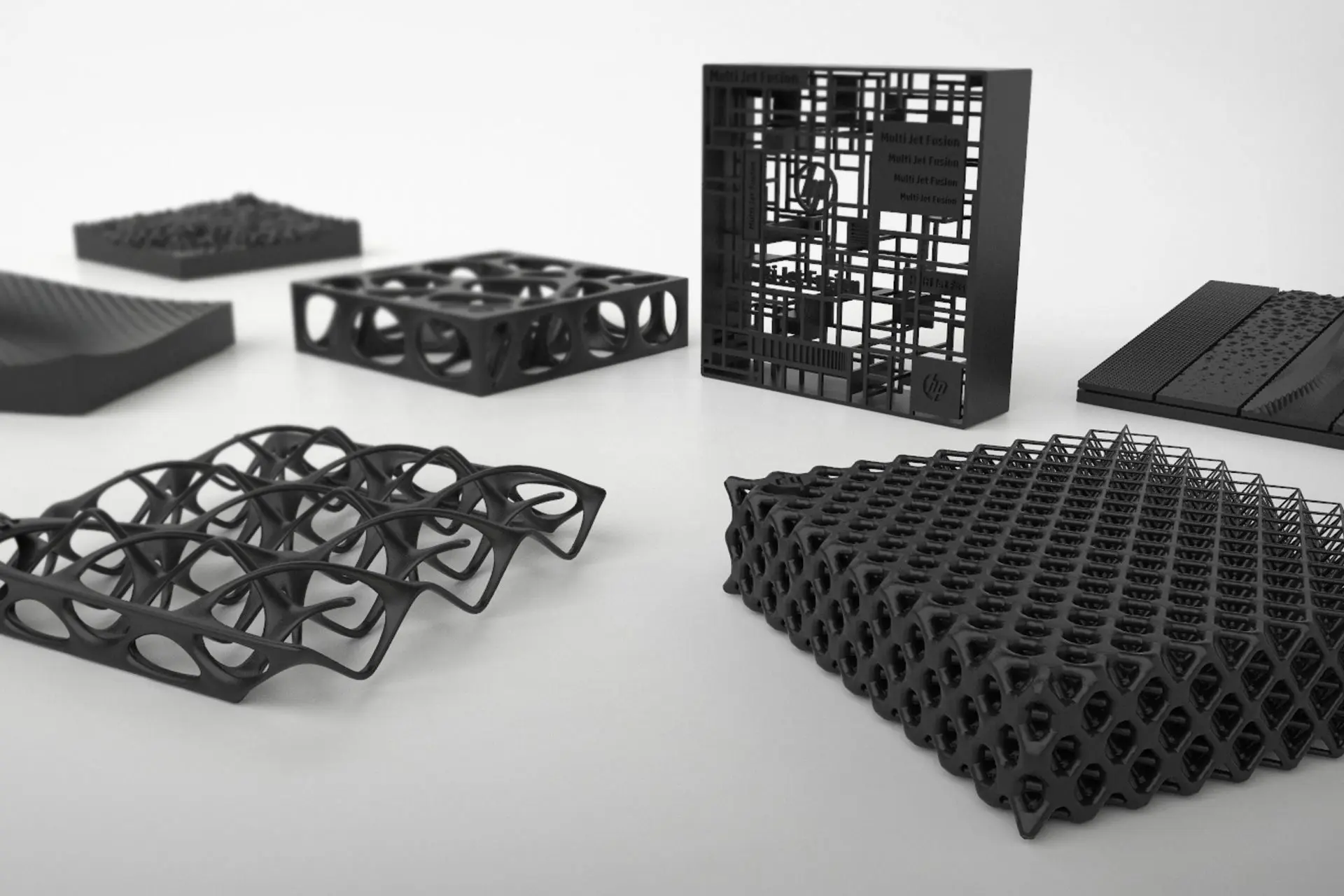
- Nylon 11 (PA 11): This bio-based nylon is sourced from renewable materials like castor beans. It offers higher elasticity and impact resistance compared to Nylon 12 and finds applications in medical implants, prosthetics, and parts requiring flexibility.
- Nylon 12 (PA 12): The industry standard for SLS, Nylon 12 strikes a balance of properties. It has high strength and low moisture absorption, making it suitable for functional parts in industrial and automotive applications, such as aerospace components, jigs and fixtures, and durable consumer products.
- Glass-Filled Nylon (GF Nylon): Reinforced with glass fibers, this type of nylon significantly increases stiffness and strength, making it ideal for structural or load-bearing parts.
- Carbon-Fiber-Reinforced Nylon: This variant offers enhanced mechanical properties, being ultra-lightweight yet extremely strong. It is used in high-performance parts in aerospace and robotics.
Why Nylon is Ideal for SLS 3D Printing
Compatibility with SLS Process Requirements
- Powder Form and Processability: Nylon’s fine powder form spreads evenly during SLS printing, enabling consistent sintering by the laser. It has a low tendency to warp, facilitating the printing process.
- Recyclability: The reusability of unfused nylon powder is a significant advantage. It makes SLS printing with nylon cost-effective and environmentally friendly.
- Versatility for Applications: Nylon combines strength, flexibility, and chemical resistance, meeting the demands of diverse industries such as automotive, aerospace, medical, and consumer goods.
Comparison with Other SLS Materials
When compared to other materials used in SLS, such as TPU (Thermoplastic Polyurethane), PA-AF (Aluminum-Filled Nylon), and glass-filled nylon, nylon offers a balanced combination of properties. It has high strength, flexibility, and durability, while other materials may have limitations in certain areas. For example, TPU has excellent flexibility but lower strength and heat resistance, PA-AF is heavier and more expensive despite enhanced stiffness and thermal conductivity, and glass-filled nylon has reduced flexibility.
Advantages of Using Nylon in SLS 3D Printing
Mechanical Properties
Nylon’s mechanical properties, including its high strength-to-weight ratio, flexibility, abrasion and wear resistance, and fatigue resistance, make it highly suitable for both prototypes and end-use parts. For instance, a nylon SLS-printed hinge can endure thousands of bending cycles without cracking, outperforming materials like PLA or ABS.
Design Freedom and Geometric Complexity
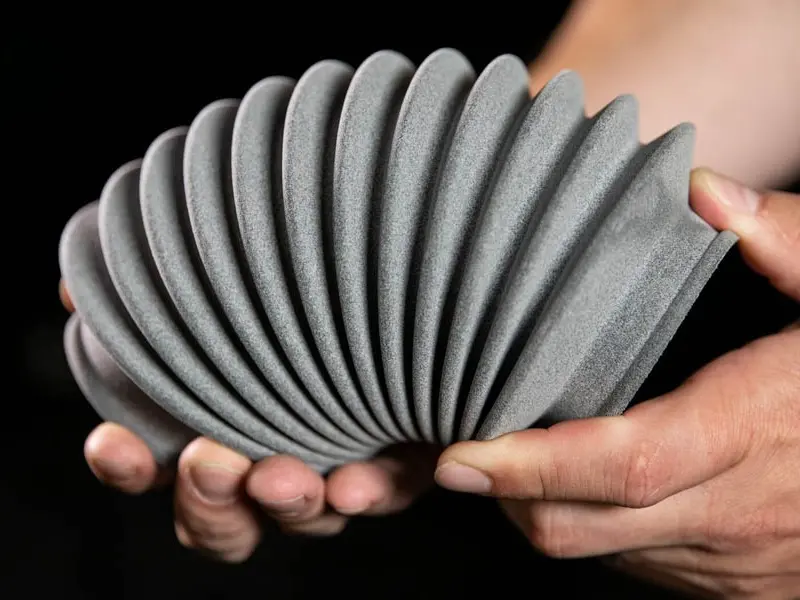
SLS combined with nylon’s properties allows for unparalleled design flexibility. The absence of the need for support structures due to the surrounding unfused powder enables the production of overhangs, hollow structures, and internal cavities. Nylon’s sintering properties also permit thin walls and delicate features without sacrificing strength, and it allows for the creation of interlocking or moving parts directly in the printer. This is particularly beneficial in applications like medical devices, where customized and complex designs are required.
Thermal Stability
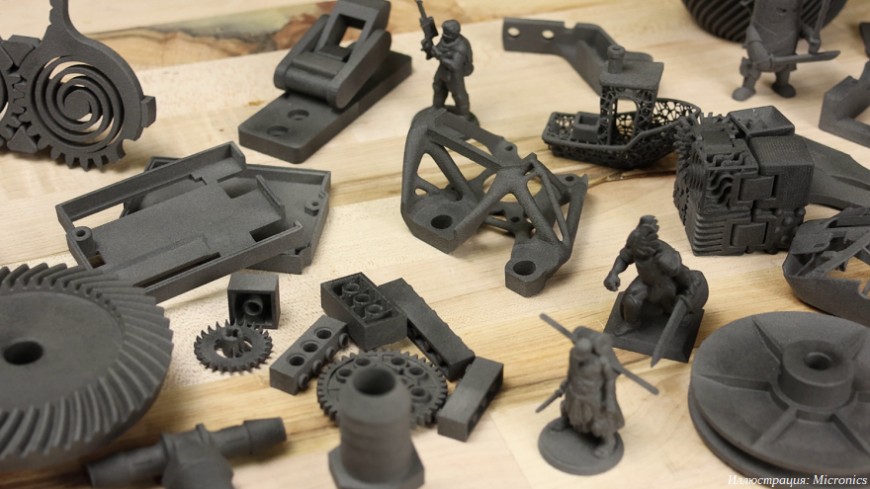
Nylon’s high melting point and thermal resistance ensure stability during the sintering process, minimizing warping and shrinking. It can also perform well in high-temperature end-use applications, such as engine components or industrial machinery, and has minimal thermal expansion, making it reliable for precision applications.
Chemical Resistance
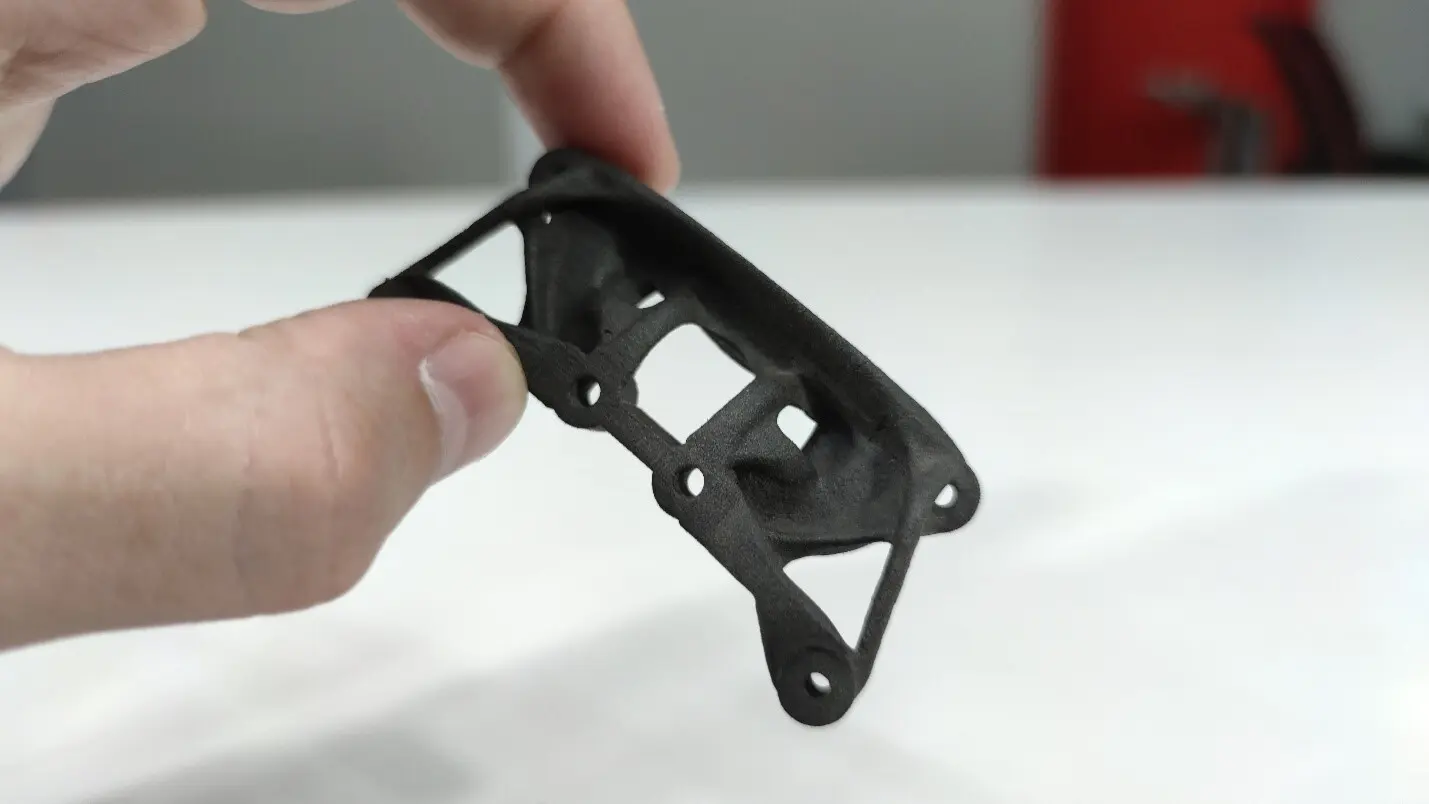
Nylon’s resistance to oils, solvents, and chemicals makes it an excellent choice for parts exposed to harsh environments. It is resistant to degradation and corrosion when in contact with moisture or certain chemicals and is also suitable for hygienic applications due to its biocompatibility.
Cost-Efficiency and Sustainability
Although the upfront cost of nylon powder may be higher than some other materials, its reusability in the SLS process reduces material waste and overall costs. SLS printing with nylon enables on-demand manufacturing, shorter lead times, and low-volume production, making it a more affordable option compared to traditional methods like injection molding. Additionally, the recycling of nylon powders contributes to environmental sustainability.
Surface Finish and Post-Processing Options
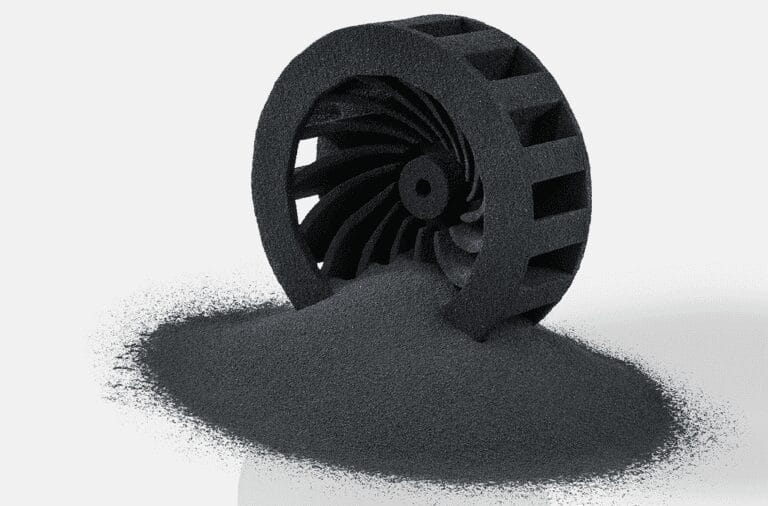
While raw SLS-printed nylon parts have a slightly powdery texture, they can be post-processed to achieve smooth, polished, and colored finishes. Nylon parts have a naturally smooth appearance compared to FDM prints and can be polished for a glossy finish, dyed to obtain vibrant colors, or coated for added protection or aesthetic enhancement.
Versatility Across Industries
Nylon’s adaptability makes it the material of choice in various industries. In aerospace, it is used for lightweight and heat-resistant parts like brackets and ducts. In the automotive industry, it is applied in engine components and prototypes. Healthcare benefits from its biocompatibility for prosthetics and surgical guides. Consumer goods utilize its durability and versatility for eyewear frames and electronics cases. In industrial manufacturing, it is used for jigs, fixtures, and tooling.
Common Applications of Nylon in SLS 3D Printing
Aerospace Industry
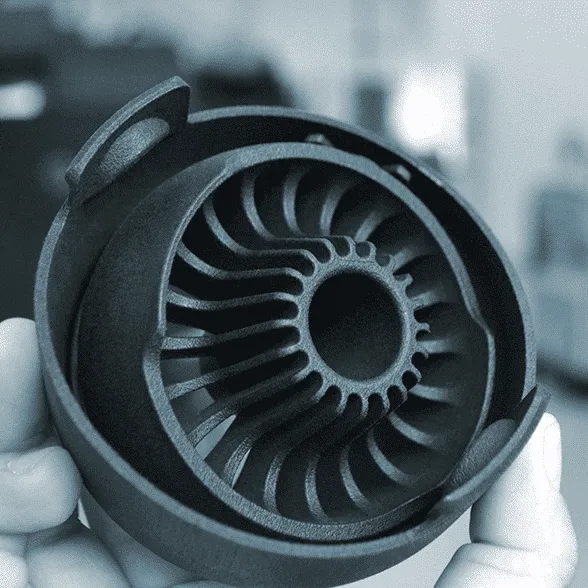
Aerospace parts require materials that are lightweight, durable, and can withstand extreme conditions. Nylon meets these requirements and enables the production of complex geometries. Applications include brackets and clamps that reduce aircraft weight, ducts and housings that can withstand heat and pressure, and prototypes for wind tunnel testing.
Automotive Industry
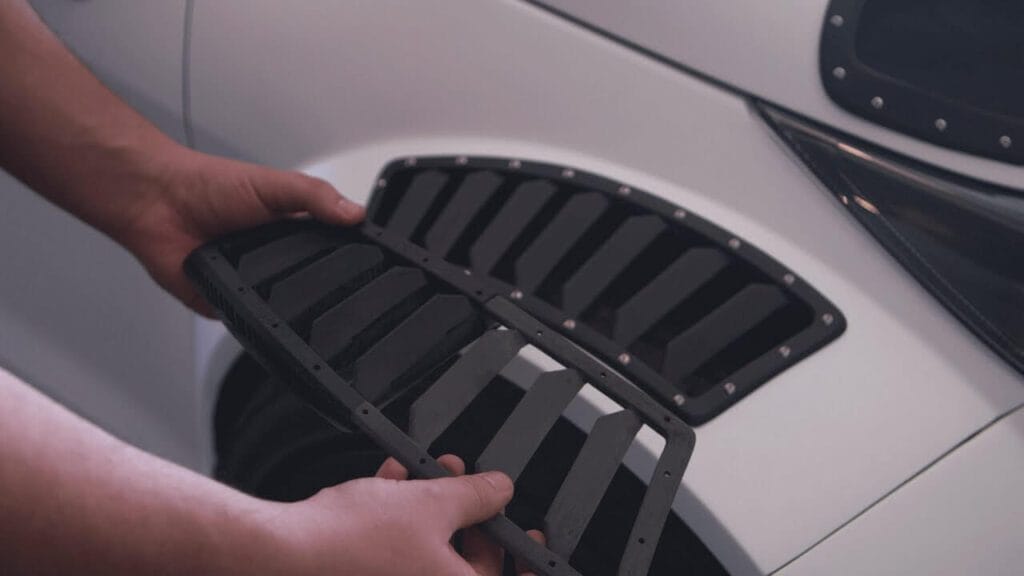
The automotive industry values durability, heat resistance, and lightweight materials. Nylon is used for engine bay components like air intake manifolds and covers, as well as interior and exterior parts such as clips and brackets. It is also employed for functional prototypes to test designs.
Healthcare and Medical Devices
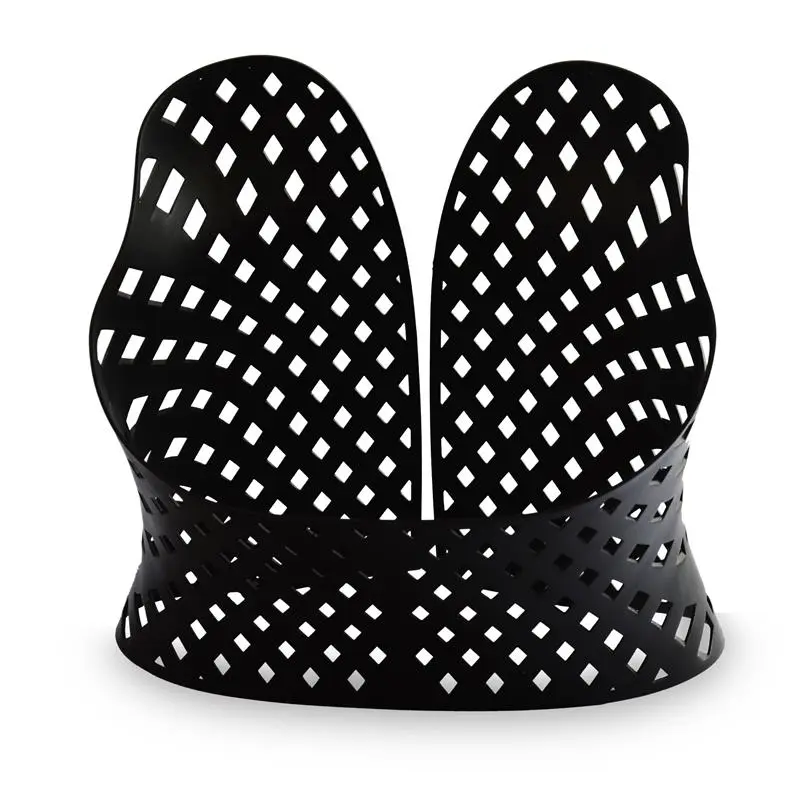
Nylon’s biocompatibility, durability, and customizability make it popular in healthcare. It is used for prosthetics and orthotics tailored to patients, surgical guides for accurate procedures, medical device housings, and dental applications.
Consumer Goods Industry
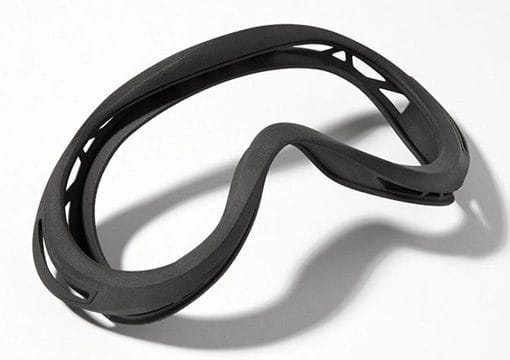
Nylon combines durability and versatility for consumer products. It is used in eyewear frames, wearable devices, electronics cases, and footwear soles and midsoles.
Industrial Manufacturing Tools and Fixtures
In industrial manufacturing, nylon is essential for creating durable, precise, and cost-effective tools and fixtures. Applications include jigs and fixtures for assembly lines, molds for design testing, and components for robotics.
Fashion and Art
Nylon’s ability to create intricate designs and smooth finishes has opened up new creative possibilities in fashion and art. It is used for jewelry, custom apparel, and art installations.
Research and Education
Nylon’s affordability and ease of use make it suitable for research labs and educational institutions. It is used for functional prototypes, student projects, and testing new designs.
Challenges and Limitations of Nylon in SLS 3D Printing and Solutions
Hygroscopic Nature and Moisture Absorption
Nylon is hygroscopic and absorbs moisture from the air. This can lead to inconsistent sintering and defects in printed parts. To address this, proper storage in airtight containers with desiccants, pre-drying the powder before use, and controlling the humidity of the printing environment are recommended.
Powder Degradation Over Time
Repeated exposure to heat during printing can cause nylon powder to degrade, reducing its mechanical properties and sintering quality. Following the recommended refreshing ratios of mixing used powder with fresh powder, tracking powder usage, and using high-quality powders can help overcome this issue.
Surface Finish and Porosity
SLS-printed nylon parts often have a rough surface texture and porosity. Post-processing techniques such as bead blasting, polishing, dyeing, or coating can improve the surface finish and reduce porosity. Design considerations like incorporating larger wall thicknesses or sealant coatings can also be applied.
Limited Color Options Without Post-Processing
Raw nylon powder typically has neutral colors. To obtain vibrant colors, post-processing steps like dyeing or painting are necessary. Using quality dyes or professional coatings and considering pre-colored powders are possible solutions.
Initial Material and Equipment Costs
The cost of premium nylon powders and SLS printers can be a barrier. However, focusing on the long-term savings due to nylon’s reusability, using service bureaus for occasional projects, or starting with smaller printers can help mitigate this challenge.
Design Constraints for Maximum Efficiency
Certain design rules need to be followed when using nylon in SLS to ensure strength and performance. Optimizing wall thickness, adding fillets and rounds to avoid sharp edges, and avoiding overly thin features can improve the quality of printed parts.
How to Get the Best Results with Nylon in SLS 3D Printing
Design Optimization
- Wall Thickness: Ensure the wall thickness of functional parts is 1.5 – 2 mm or more, while decorative parts can be as thin as 0.8 – 1 mm depending on design complexity. This helps prevent warping or overheating during sintering.
- Avoid Sharp Edges: Add fillets or rounded edges to improve structural integrity and sintering quality by reducing stress points.
- Hollow Out Large Parts: Use hollow structures with appropriately sized escape holes to remove unfused powder and reduce material use and internal stresses.
- Interlocking and Moving Parts: Maintain a gap of at least 0.5 mm between moving parts to prevent sintering overlap.
Printer Configuration
- Laser Power and Speed: Follow the manufacturer’s guidelines for nylon powder and optimize the laser settings to balance precision and bonding strength.
- Layer Thickness: Use a layer thickness of 100 – 120 microns (0.1 – 0.12 mm) for nylon to achieve a good balance of detail and durability.
- Powder Bed Temperature: Preheat the powder bed to just below nylon’s melting point (typically 170 – 180°C) to ensure uniform sintering and prevent warping.
Powder Management
- Storage: Store nylon powder in airtight containers with desiccants in a low-humidity environment (below 40%) to prevent moisture absorption.
- Recycling and Refreshing Powder: Mix recycled powder with fresh powder according to the recommended ratio (usually 30 – 50% fresh powder) and use aged powder for non-critical parts.
- Sifting and Sieving: Sift the powder through a fine sieve (300 microns or finer) before loading it into the printer to remove clumps and contaminants.
Post-Processing
- Removing Excess Powder: Use compressed air or bead blasting to remove unfused powder from the printed part.
- Polishing: Polish the part using a tumbling machine or manual polishing tools to improve the surface finish.
- Dyeing and Painting: Dye the nylon part using fabric dye in a hot water bath or apply industrial-grade paints for color customization.
- Surface Coatings: Apply sealants or coatings to reduce porosity, enhance water resistance, or add a glossy finish.
Testing and Iteration
Print small-scale prototypes to validate the design, material behavior, and printer settings. Perform mechanical testing to ensure the parts meet performance requirements. Document the process to learn from successes and failures and refine the printing process over time.
Case Studies
(A) Lightweight Brackets in Aerospace Applications
An aerospace company used SLS 3D printing with nylon to redesign brackets. By leveraging nylon’s high strength-to-weight ratio, the new brackets were 50% lighter than aluminum ones, yet equally durable. They were manufactured in a single piece, reducing production time and costs. This led to a 15% improvement in fuel efficiency.
(B) Custom Prosthetics in Healthcare
A medical equipment manufacturer utilized SLS printing with nylon to produce patient-specific prosthetics. Nylon’s flexibility and biocompatibility allowed for lightweight, durable, and custom-fit prosthetics with complex geometries. Production time was reduced by 50% compared to traditional methods, improving patient outcomes and reducing costs.
(C) Durable End-Use Parts for Automotive Applications
An automotive manufacturer turned to SLS printing with nylon 12 to develop an intake manifold. This enabled quick testing of multiple designs without tooling costs and small production runs of end-use parts. The manifold could withstand high temperatures and exposure to fuel and oil, resulting in a 66% reduction in lead time and significant cost savings.
(D) Custom Manufacturing Tools for Assembly Lines
A factory adopted SLS printing with glass-filled nylon to produce custom jigs and fixtures. These tools were lightweight yet robust, tailored to specific tasks, and could be produced 75% faster than traditional machining. Downtime was reduced by 40%, and costs were saved by 30 – 50% per tool.
(E) High-End Consumer Goods
A luxury eyewear brand used SLS printing with nylon to create customized frames. Nylon’s strength and flexibility allowed for intricate designs, and post-printing dyeing offered a wide range of colors. Production time was reduced while maintaining high quality, leading to a successful product line.
(F) Artistic and Architectural Projects
An artist used SLS printing with nylon to create large, intricate sculptures for an architectural project. Nylon’s ability to produce complex geometries, its lightweight nature, and durability made it suitable for the project. The sculptures were completed on time and within budget, receiving acclaim for their design.
The Future of Nylon in SLS 3D Printing
Emerging Innovations
- Advanced Nylon Composites: Carbon-fiber-reinforced nylon offers enhanced stiffness and strength for aerospace and automotive applications. Glass-filled nylon provides rigidity and thermal stability for industrial tools. Metal-filled nylon combines the properties of nylon and metals for increased durability and conductivity.
- Bio-Based and Biodegradable Nylons: Bio-based nylon derived from renewable resources reduces reliance on fossil fuels. Biodegradable nylon addresses environmental concerns related to waste.
- High-Temperature and High-Performance Nylons: High-temperature nylons can withstand extreme heat for aerospace and automotive components. Electrically conductive nylons are useful in electronics and robotics.
Sustainability Efforts
- Increased Recyclability: Research is focused on developing nylon powders with higher refresh rates and advanced recycling technologies to reduce waste.
- Circular Manufacturing Ecosystem: A closed-loop system for recycling nylon parts and powder is being developed to create a sustainable manufacturing model.
- Energy Efficiency: Energy-efficient SLS printers are being developed to reduce electricity consumption during printing.
Expanding Applications
- Clean Energy Solutions: Nylon is being explored for use in wind turbines (such as lightweight internal gears and covers) and solar energy systems (like mounting and enclosures for photovoltaic panels).
- Space Exploration: Nylon composites are under testing for satellite, rover, and spacecraft components. New high-performance nylons may enable in-space manufacturing for long-duration missions.
- Construction and Infrastructure: SLS-printed nylon parts are being investigated for modular housing, custom plumbing fixtures, and durable construction tools.
- Wearable Technology: Flexible and durable nylons are being utilized to create custom-fit components for wearable devices like fitness trackers, medical monitors, and augmented reality headsets.
Challenges Ahead
Despite the promising future, there are still hurdles. The cost of advanced nylon formulations and specialty powders remains high, potentially limiting their accessibility. Developing new materials that meet industry standards takes time. Scaling sustainable practices, such as circular recycling systems, requires supply chain collaboration. However, as the technology advances and adoption grows, these challenges are expected to be gradually overcome.
Conclusion
Nylon has established itself as a key material in SLS 3D printing, offering a unique combination of properties that make it highly suitable for a wide range of applications. Its compatibility with the SLS process, mechanical strength, thermal stability, chemical resistance, and design flexibility have driven innovation across multiple industries. While there are challenges associated with its use, ongoing research and development efforts are focused on enhancing its performance, improving sustainability, and expanding its applications. As SLS technology and material science continue to evolve, nylon is expected to play an even more significant role in the future of additive manufacturing, enabling the creation of more complex, efficient, and sustainable products.