Innovation commences with an idea, which serves as the impetus for potential industry transformation, life enhancement, or problem-solving. Transforming this idea into a tangible product demands prototyping, bridging the chasm between concept and reality. Prototyping is crucial for testing and refining designs prior to market release, regardless of the product type.
Traditional manufacturing techniques for prototyping can be costly and time-consuming, especially for iterative designs. 3D printing has emerged as a revolutionary alternative. Among the various 3D printing modalities, SLA (Stereolithography) is prominent. Renowned for its precision, versatility, and capacity to fabricate highly detailed models, SLA 3D printing has become a favored solution for innovators seeking efficiency and excellence.
What is SLA 3D Printing?
SLA 3D printing is a refined 3D printing technique. It operates by utilizing a high-powered UV laser to cure liquid photopolymer resin layer by layer, transforming it into solid objects.
Process Steps
- Liquid Resin Tank: The process initiates with a vat filled with liquid photopolymer resin that is sensitive to UV light.
- Laser Exposure: A precisely directed UV laser beam follows a pre-programmed pattern to polymerize the resin, forming the first layer of the object.
- Layer-by-Layer Printing: Once a layer solidifies, the build platform shifts marginally, and the laser proceeds to create the subsequent layer until the object is complete.
- Post-Processing: After printing, the object is extracted from the resin tank and undergoes procedures such as cleaning, curing, and surface finishing to augment its strength and appearance.
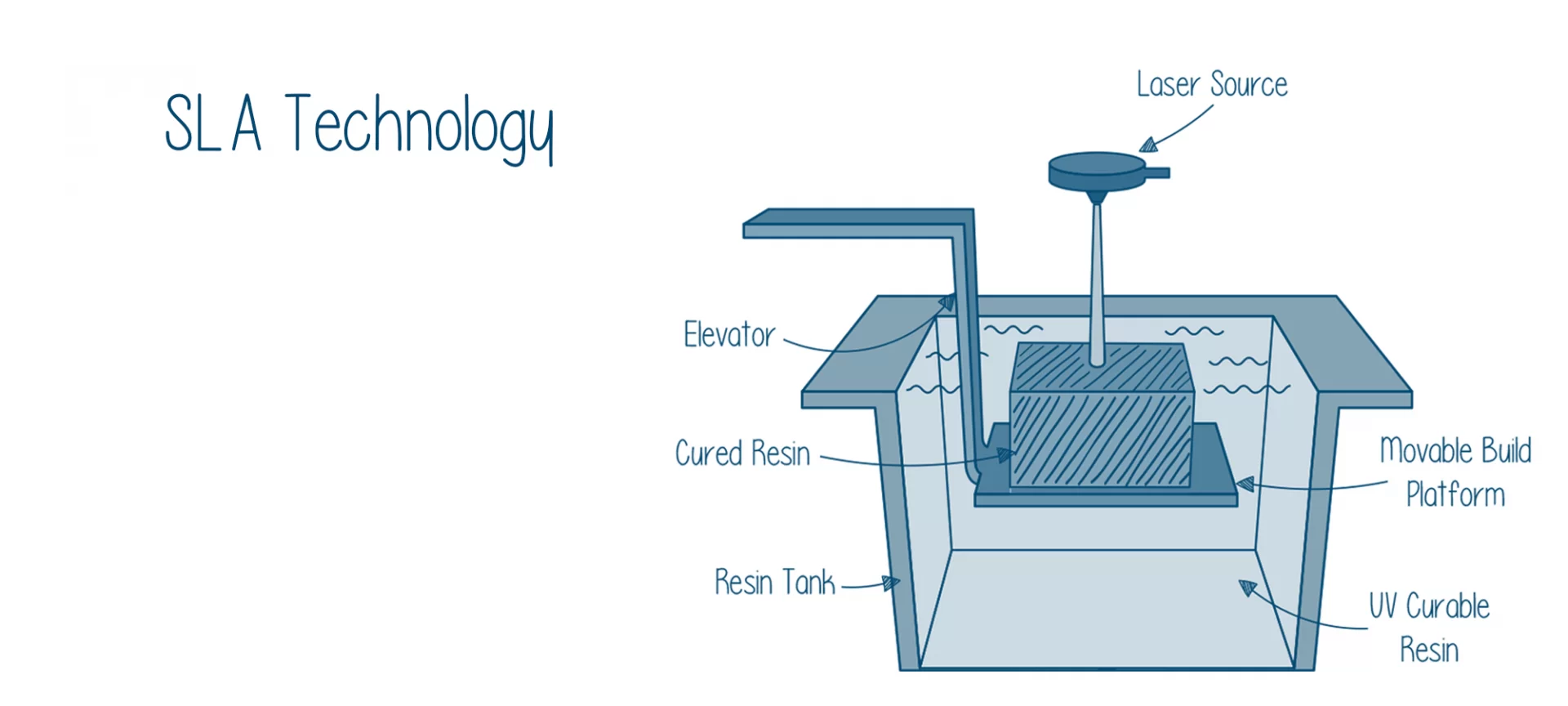
Key Features
- High Resolution: SLA can achieve layer thicknesses as diminutive as 25 microns (0.025 mm), facilitating the creation of intricate designs.
- Smooth Surface Finish: It produces parts with exceptionally smooth surfaces, minimizing the need for additional sanding or finishing.
- Versatility: Capable of fabricating both small, detailed components and larger prototypes with high precision.
Materials Used in SLA Printing
SLA printing employs photopolymer resins, which solidify upon exposure to UV light. These resins are available in diverse formulations, each tailored to specific applications.
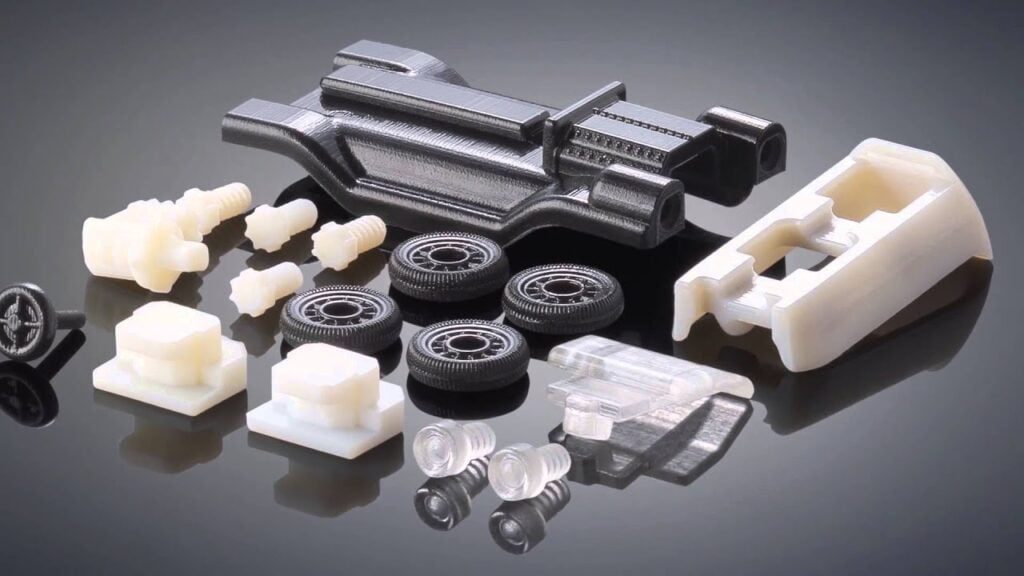
Resin Type | Properties | Common Applications |
Standard Resin | Smooth finish, high detail | Visual prototypes, concept models |
Tough Resin | Durable, impact-resistant | Functional prototypes, mechanical parts |
Flexible Resin | Elastic, bendable | Wearables, soft-touch parts |
High-Temperature Resin | Heat-resistant, thermally stable | Automotive components, molds |
Transparent Resin | Clear, optical-quality finish | Lenses, fluid flow testing |
Dental/Medical Resin | Biocompatible, sterilizable | Dental aligners, surgical guides |
The variety of resins enables SLA 3D printing to accommodate different industries, from aerospace and automotive to medical devices and consumer products.
Comparison with Other 3D Printing Technologies
In the realm of 3D printing, SLA is not the sole option. Alternatives include FDM (Fused Deposition Modeling), SLS (Selective Laser Sintering), and DLP (Digital Light Processing).
Feature | SLA | FDM | SLS | DLP |
Resolution | High | Low to Medium | Medium | High |
Surface Finish | Smooth | Rough | Grainy | Smooth |
Material Options | Wide variety of resins | Limited to thermoplastics | Limited to powders | Similar to SLA |
Cost | Moderate to High | Low | High | Moderate to High |
Build Speed | Moderate | Fast | Moderate | Fast |
Best For | Detailed prototypes, smooth surfaces | Simple parts, larger models | Durable parts, functional testing | Similar to SLA, smaller parts |
SLA outperforms FDM in resolution and surface quality. While SLS is stronger for functional testing, SLA excels in visual prototyping and intricate designs. SLA and DLP are similar in quality, but DLP is faster for smaller parts.
Popularity of SLA Printing
SLA 3D printing is favored in industries demanding precision, aesthetics, and versatility. Its popularity stems from the following aspects:
- Unmatched Detail: It can reproduce fine details that other methods struggle to achieve, applicable in jewelry and medical device prototyping.
- Prototyping Speed: It strikes a balance between speed and quality, suitable for iterative designs.
- Wide Applicability: Its material versatility allows it to handle a broad spectrum of applications, from engineering to artistic creations.
- Professional Results: Printed prototypes often have a polished and professional appearance.
Why is SLA 3D Printing Ideal for Prototyping?
Key Advantages
- Precision and Accuracy
- SLA’s high resolution makes it the preferred choice for prototypes requiring intricate details and dimensional precision. Many prototypes in aerospace, medical devices, and automotive industries need to meet tight tolerances. SLA can handle complex geometries and produce layers as thin as 25 microns, resulting in smooth and detailed prototypes. For example, a designer can use SLA to print a watch prototype with tiny engravings and complex internal components accurately.
- Superior Surface Finish
- SLA is known for its smooth surface finish, reducing the need for extensive post-processing. This is beneficial for applications where appearance matters, such as presentations or functional testing involving moving parts. In contrast, other 3D printing technologies like FDM leave visible layer lines and require more post-processing.
- Material Versatility
- SLA’s compatibility with various photopolymer resins caters to diverse prototyping needs. Different resins offer properties like strength, flexibility, heat resistance, and clarity. This allows for creating prototypes that mimic the final product’s behavior, ensuring accurate testing and validation.
- Faster Iterative Design Cycles
- Prototyping is iterative, and SLA enables quick design iterations. It can produce high-quality prototypes in hours, facilitating design tweaks by simply modifying the CAD file. Multiple design iterations can be tested simultaneously, saving time and resources.
- Cost-Effectiveness for Low-Volume Production
- For low-volume prototyping, SLA is a more affordable option than traditional manufacturing processes like injection molding or CNC machining. It eliminates the need for expensive tooling, uses resin efficiently, and allows for on-demand production.
Real-World Applications
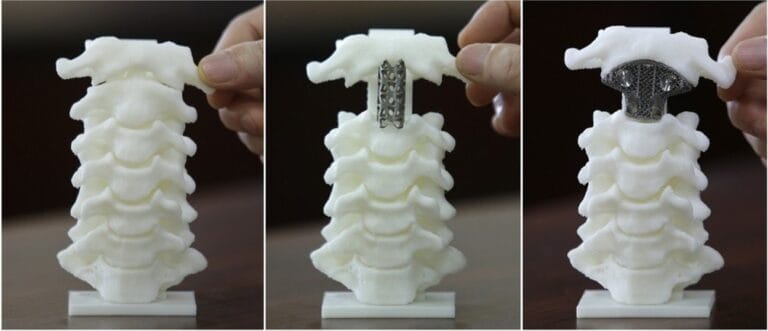
- Healthcare and Medical Devices
- Used for prototyping surgical tools, custom implants, and creating patient-specific anatomical models for pre-surgery planning. Dental labs also use it for orthodontic models and crowns.
- Consumer Electronics
- Helps in designing sleek prototypes for smartphones, earbuds, wearables, and testing ergonomic designs. It ensures accurate dimensions for casings and enclosures.
- Automotive and Aerospace
- Develops lightweight, complex components for functional testing and creates aerodynamic models for wind tunnel testing. Engine parts and interior components can also be prototyped.
- Jewelry and Creative Industries
- Ideal for producing intricate prototypes for jewelry and artistic creations, such as rings, bracelets, and sculptures.
Challenges and Solutions
- Material Fragility
- SLA prototypes may lack the durability of parts made from certain materials. To address this, tough or engineering-grade resins can be used for functional testing.
- Post-Processing Requirements
- SLA parts need cleaning, curing, and sometimes sanding. Adequate time should be allocated for post-processing in the project timeline, and automated curing stations can be utilized.
- Environmental Concerns
- Photopolymer resins may pose environmental issues. Resin waste should be disposed of properly, and the exploration of bio-based resins is advisable.
Applications of SLA 3D Printing in Prototyping
SLA 3D printing is a potent tool for prototyping across industries. Its key advantages include high precision, smooth surface finish, material versatility, speed, and cost-effectiveness for low-volume production.
Industry Applications
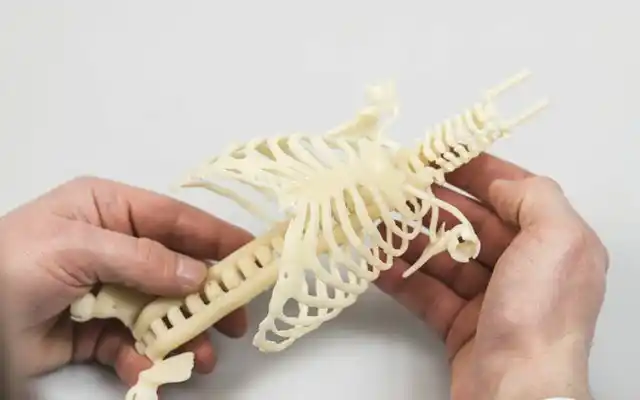
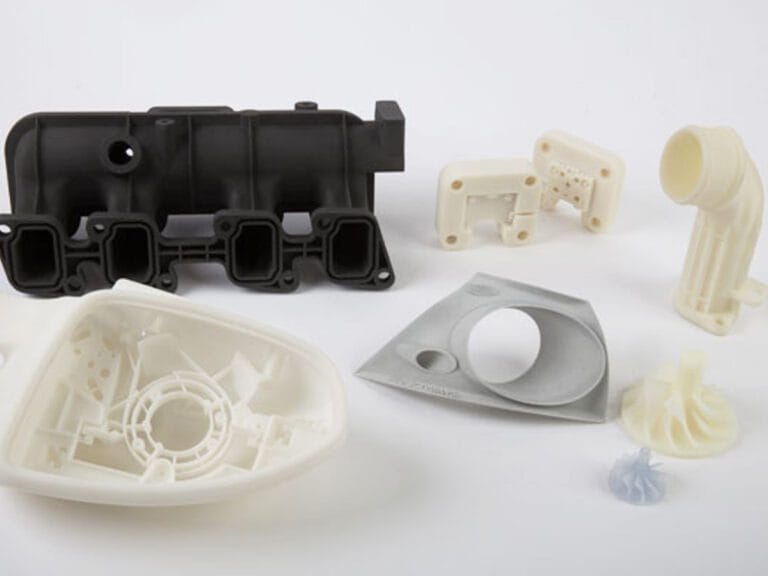
- Healthcare and Medical Devices
- Enables the creation of detailed and customized prototypes for medical devices and anatomical models. Surgical tool prototypes benefit from high precision for ergonomic testing, and anatomical models accurately replicate human anatomy for surgery planning. Dental applications use biocompatible resins.
- Consumer Electronics
- Helps manufacturers prototype devices with aesthetic appeal and functional accuracy. Wearables and gadgets can be prototyped with fine details, and ergonomic testing is facilitated. Housing and enclosures can be precisely fabricated.
- Automotive and Aerospace
- Used for creating aerodynamic models, interior components, and engine part mockups. Its high resolution and material options are valuable for meeting complex geometries and performance requirements.
- Jewelry and Creative Industries
- Unmatched in producing intricate designs for jewelry and artistic prototypes. Custom jewelry can be prototyped with fine engravings, and artists can bring their concepts to life.
- Industrial Manufacturing
- Creates functional mockups, tooling, and packaging prototypes that mirror the final product’s functionality and appearance.
Types of Prototypes
- Visual Prototypes
- Intended to showcase the design, shape, and aesthetics of a product. SLA’s high resolution and smooth surfaces make them resemble final products.
- Functional Prototypes
- Used to test the functionality and mechanical performance of a design. Tough and heat-resistant resins support rigorous testing.
- Concept Models
- Communicate an idea or explore different design directions. SLA’s fast production and cost-effectiveness are advantageous for early-stage exploration.
Real-World Case Studies
- Medical Device Prototyping
- A medical device company used SLA to prototype a handheld surgical tool. The high precision allowed for ergonomic testing and design refinement based on surgeon feedback. Biocompatible resins enabled early-stage testing.
- Consumer ElectronicsStartup
- A startup developing a wearable fitness tracker used SLA to prototype the device’s housing. SLA facilitated quick iterations, ensuring a compact and stylish design that fit the internal electronics.
Key Considerations for Using SLA 3D Printing
Understanding Limitations
- Material Fragility
- SLA resins are generally brittle compared to some other materials. This restricts their use in high-impact or load-bearing applications. Tough or engineering-grade resins can be used to mitigate this issue.
- Post-Processing Requirements
- SLA requires extensive post-processing, including cleaning, curing, and support removal. Sufficient time should be planned, and automated equipment can be used.
- Build Volume Constraints
- SLA printers typically have smaller build volumes. Designs may need to be modularized for larger prototypes.
- Resin Handling and Waste
- Photopolymer resins are liquid and require careful handling. Unused resin must be filtered and stored properly, and waste resin should be disposed of following guidelines.
Design Guidelines
- Wall Thickness
- A minimum wall thickness of 0.6 mm is recommended to ensure structural integrity.
- Overhangs and Supports
- SLA can handle complex overhangs, but supports may be needed. Orienting the model to minimize support requirements can improve surface finish.
- Detail Size
- SLA can reproduce details as small as 0.1 mm, but larger features print more reliably. Avoid overly intricate designs that may be affected during post-processing.
- Hollow Parts
- Hollowing out large parts can save material, but drain holes (at least 3-4 mm in diameter) should be included to allow uncured resin to escape.
- Part Orientation
- The orientation affects print quality, support placement, and post-processing ease. Optimize orientation to balance detail quality and minimize supports on visible surfaces.
Post-Processing Steps
- Part Removal
- Carefully remove the printed part from the build platform using a scraper.
- Cleaning
- Wash the part in isopropyl alcohol (IPA) to remove uncured resin. Two-stage cleaning is recommended for better results.
- Curing
- Expose the part to UV light to fully cure the resin. The curing time typically ranges from 10 to 30 minutes depending on the resin and thickness.
- Support Removal
- Carefully remove supports using clippers or a knife and sand any remaining nubs.
- Surface Finishing
- Sanding, polishing, or painting can be done to enhance the appearance. SLA parts are well-suited for painting due to their smooth surface finish.
Environmental Impact and Sustainability
- Resin Waste
- Unused or uncured resin cannot be disposed of in regular waste streams. It should be properly cured before disposal.
- Energy Usage
- SLA printers and curing stations consume energy. Using energy-efficient equipment and optimizing settings can reduce consumption.
- Recycling Limitations
- SLA resins are not recyclable. Minimize resin use and explore sustainable resin options.
How to Get Started with SLA 3D Printing for Prototyping
Choosing the Right SLA Printer
- Understanding Needs
- Evaluate requirements such as budget, size of prototypes, and desired precision before purchasing an SLA printer. Consider the type of prototypes to be created, budget constraints, material compatibility, and available space.
- Popular Printers
- Some popular SLA printers include Formlabs Form 3, Kings3dprinter – SLA400, Zongheng3D – Supermaker SLA400. Consider factors like build volume, resolution, price, software, and consumable costs when choosing.
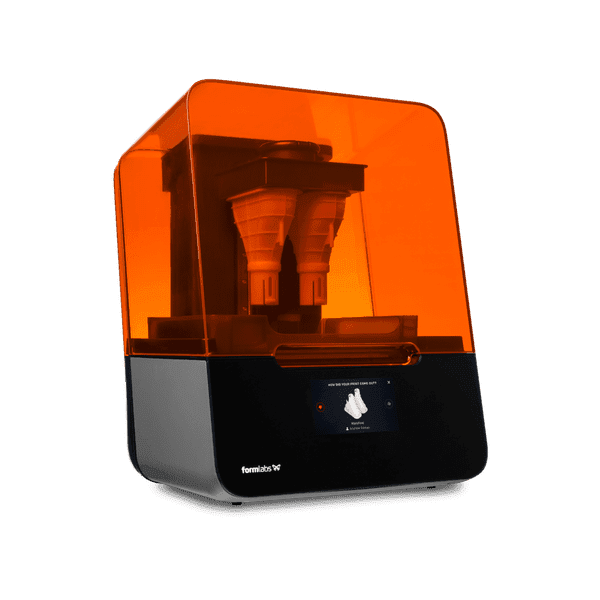
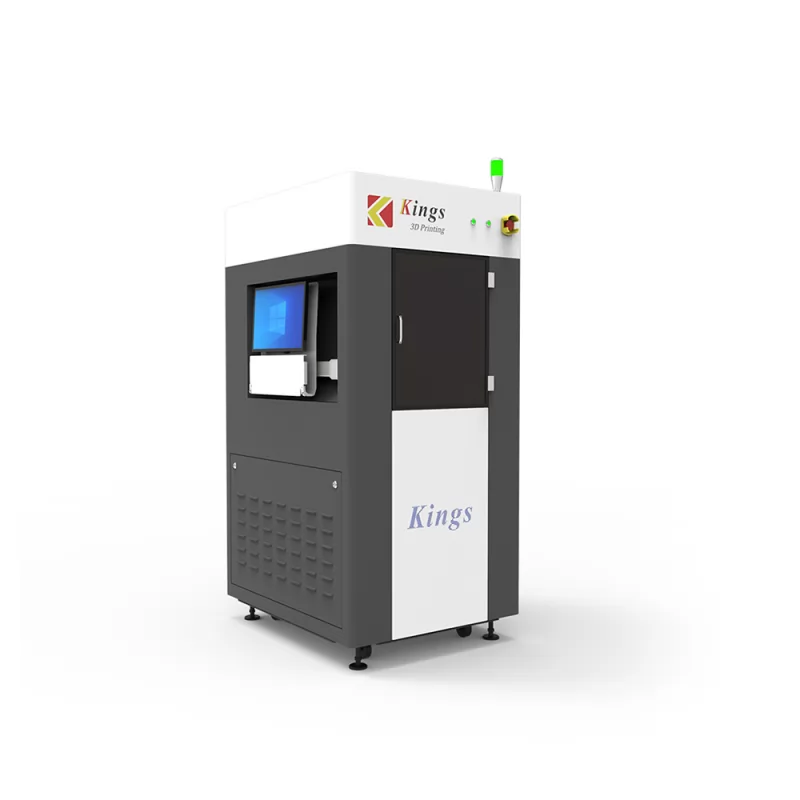
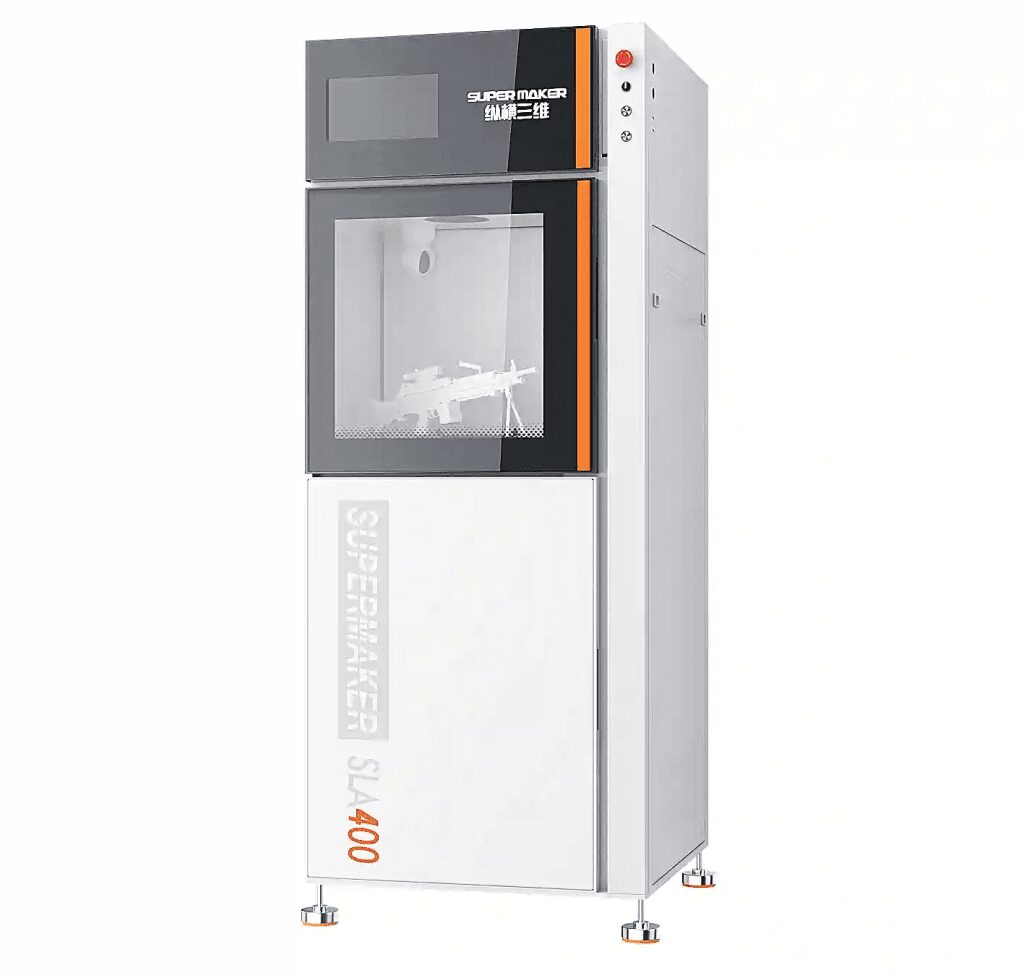
Selecting the Right Resin
- Types of Resins
- Different SLA resins have specific properties and applications. Standard resin is suitable for visual prototypes, while tough resin is for functional testing. Choose the resin based on the prototype’s purpose, environmental conditions, and biocompatibility requirements.
- Questions for Selection
- Determine the purpose of the prototype, the environmental conditions it will face, and if biocompatibility is needed.
In-House Printing vs. Outsourcing
- In-House Printing
- Benefits include control over the workflow, cost savings over time for frequent printing, and faster iterations. Downsides are the high initial investment, learning curve, and space requirements.
- Outsourcing
- Advantages are low startup costs, access to professional expertise, and flexibility for one-off projects. Disadvantages are longer turnaround times, higher costs for frequent use, and limited control.
- When to Choose Each Option
- Frequent prototyping with tight timelines is better suited for in-house printing. Occasional prototyping or one-off projects, the need for large industrial-grade parts, or limited budget for initial investment are reasons to outsource.
Cost Breakdown
- In-House Printing Costs
- Include the cost of the printer (ranging from $300 to $5,000), resins ($50 – $200 per liter), post-processing equipment ($200 – $1,000), and consumables.
- Outsourcing Costs
- Comprise the cost per print ($50 – $500), shipping fees ($10 – $50 per order), and lead time (2 – 7 days).
Tips for Getting Started
- Start Small
- Begin with an affordable printer and standard resin to familiarize with the process.
- Practice Post-Processing
- Dedicate time to master cleaning, curing, and finishing techniques.
- Experiment with Resins
- Test different resin types to understand their properties.
- Leverage Online Communities
- Join forums and connect with other users to learn and troubleshoot.
- Iterate Often
- Utilize SLA’s rapid prototyping capabilities to refine designs.
Conclusion
SLA 3D printing is a highly effective technology for prototyping. Its unique advantages such as precision, surface quality, material versatility, rapid iteration, cost-effectiveness, and broad industry applications make it the preferred choice.
Despite challenges like post-processing requirements, material fragility, and environmental concerns, these can be managed through proper planning and best practices.
Businesses can benefit from SLA 3D printing by accelerating time to market, reducing costs, improving design validation, and enhancing stakeholder confidence. It is a valuable tool for turning ideas into reality in the product development process.